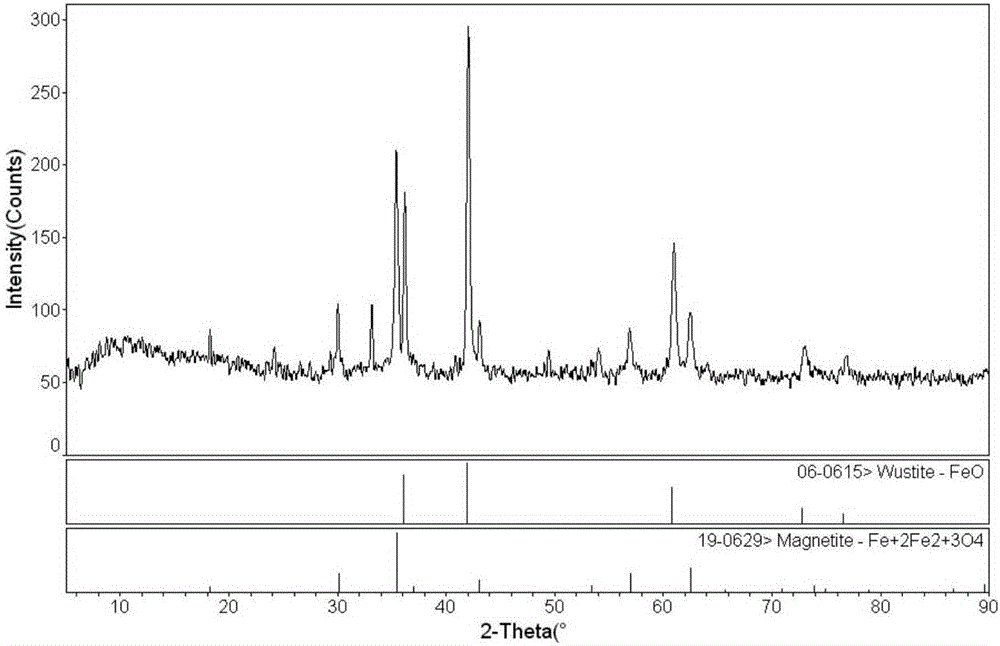
本发明属于化工和钢铁冶金
技术领域:
,特别是钢厂污泥和低热值高炉煤气资源化利用领域,涉及一种钢厂高含油含铁污泥超临界水气化资源化处理方法及装置。
背景技术:
:在轧钢生产过程中,需要大量直接冷却水,冲洗钢材和设备,会产生大量的废水,废水中主要含有喷淋冷却轧机轧辊辊道和轧制钢材的表面产生的氧化铁,机械设备上的油类物质,固体杂质等废弃物及污泥等,主要污染物是大量的粒度不同的氧化铁、润滑油类及乳化液,其中冷轧废水中的乳化液的油脂浓度高、乳化浓度高,普遍含表面活性剂。据统计,我国钢厂平均每轧制1吨钢板约排出废水30-40m3。废水中含氧化铁皮约5000mg/L,悬浮物100-1250mg/L,残渣800-1500mg/L,油类50-500mg/L。钢铁行业很多都采用简单的混凝沉淀处理工艺对钢厂废水进行处理,处理后产生的高含油含铁污泥脱水后进行焚烧或者填埋处理。但是对于高含水量的污泥,焚烧法处理设施的投入和运营成本较高,增加了钢铁的生产成本。此外,高温焚烧容易产生二噁英、氮氧化物等有毒物质,造成二次污染。填埋法占地面积大,而且污泥稳定性差,会腐烂变质产生臭气体,污泥中的水分渗漏易污染地下水。此外,钢厂污泥含高浓度氧化铁,直接填埋会造成资源浪费,填埋处理费也逐年增加,这在钢铁行业去产能的大背景下,无疑增加了钢厂的生存压力。因此很多学者一直寻求一些新技术、新工艺对污泥进行资源化利用。超临界水气化技术是利用超临界水的特性,在温度、压力高于水的临界温度和压力(374℃,22.1MPa)条件下,水的密度、粘度和介电常数快速下降,导致超临界水可以与有机物和气体以任意比例混合,强化传质。加之在超临界状态下,水的离子积远小于10-14,水中的化学反应主要以自由基反应为主,污泥中的有机物可以被快速的分解为二氧化碳、水和氮气等物质,氧化铁转化为带有磁性的四氧化三铁,可以通过磁选分离回收利用,或者直接返回炼钢炉重复利用。然而作为一种新兴的污泥处理技术,超临界水气化技术很少应用在钢厂污泥处理中,而且以往的研究发现,为达到良好的污泥处理效果,系统温度必须提高,这无疑增加了能源的消耗。钢铁企业炼钢生产中产生的副产能源高炉煤气,由于热值较低,含尘含水量大,压力波动大等因素在钢铁企业中难以适应生产需要,大部分钢铁厂出高炉热风炉、焦炉以及部分与焦炉煤气混合使用外,剩余的煤气被白白地放散掉,造成资源的浪费。而这部分煤气可以用于超临界水气化系统的供热,因此有必要根据钢铁企业自身优势和资源,研究开发钢厂污泥处理处理处置的新工艺。技术实现要素:有鉴于此,本发明的目的在于提供一种钢厂高含油含铁污泥超临界水气化资源化处理方法及装置,该方法和装置利用超临界水气化技术回收利用钢厂高含铁污泥,并充分利用钢厂低热值高炉煤气作为加热器燃料,通过超临界水气化技术将污泥中的油脂转化为高热值甲烷和氢气燃气。为达到上述目的,本发明提供如下技术方案:一种钢厂高含油含铁污泥超临界水气化资源化处理方法,该方法包括以下步骤:S1:将钢厂高含油含铁生产污泥在预处理池中进行调质预处理;S2:将步骤S1中预处理后的污泥,通过柱塞泵输送到加热器,在加热器中进行预加热,预加热后的污泥输入超临界水气化反应器;S3:经过步骤S2处理后,将超临界水气化反应后的泥浆通过换热器进行降温和热交换处理;S4:降温后的泥浆进入气液分离器,使气体混合物从泥浆中充分分离出来,经分离处理后,得到甲烷和氢气的混合燃气;而渣水混合物进入排水池中,在排水池中加入絮凝剂,静置30-60min后,上清液排放到钢厂污水处理厂继续处理,池底污泥进行压滤,将压滤后的污泥通过换热器传下来的余热进行脱水烘干,烘干后的污泥直接送入炼钢炉,作为炼钢原料。进一步,在步骤S1中,经过调质处理后,水/泥质量比为5:1,pH值为6-10。进一步,在步骤S2中,加热器所用燃料为钢厂产生的低热值高炉煤气。进一步,在步骤S2中,反应器的温度控制在600-700℃,压力控制在25-30MPa,停留时间为10-20min。在步骤S4中,气液分离处理后,产生的混合气经分离处理,产生的高热值的甲烷和氢气混合燃气可以作为炼钢高炉燃气;超临界气化反将污泥中所有铁质转化为四氧化三铁,可以直接作为炼钢原料;超临界水气化处理后的水直接排入钢厂污水处理厂,无需进一步处理。本发明还提供了一种钢厂高含油含铁污泥超临界水气化资源化处理装置,该装置包括依次相连的钢厂污泥池1、污泥调质池2、柱塞泵3、加热器4、超临界气化反应器5、换热器6、气液分离器7;钢厂污泥池1中的高含油含铁生产污泥通过污泥调质池2进行调质预处理后通过柱塞泵3输送到加热器4,在加热器4中进行预加热后的污泥输入超临界气化反应器5,经过超临界水气化反应后的泥浆通过换热器6进行降温和热交换处理;降温后的泥浆进入气液分离器7,使气体混合物从泥浆中充分分离出来;经分离处理后,得到甲烷和氢气的混合燃气,混合燃气随后进入储气柜8和气体分离系统9;渣水混合物进入排水池10中,在排水池10中加入絮凝剂,静置30-60min后,上清液排放到钢厂污水处理厂继续处理,池底污泥进行压滤,将压滤后的污泥送入废渣干燥系统11,通过换热器传下来的余热进行脱水烘干,烘干后的污泥直接送入炼钢炉,作为炼钢原料。本发明的有益效果在于:1)本发明充分利用钢厂高含油含铁污泥有机质含量高、热值高等特点,结合钢厂现有资源,如大量低热值煤气、钢厂自建污水处理厂、高温炼钢炉等,将钢厂低热值高炉煤气作为超临界水气化反应系统的加热燃气,含油含铁污泥经超临界水气化处理后,产生了高热值的甲烷和氢气的混合燃气,达到了利用低热值高炉煤气结合超临界水气化技术,产生高热值燃气的目的。2)本发明充分利用钢厂自建污水处理厂,将超临界水气化处理后的水直接排入钢厂污水处理厂,无需进一步处理,工艺简单,可操作性强。3)本发明充分利用超临界水的性质,含铁污泥在经超临界水气化处理后,其中的含铁物质完全转化为四氧化三铁,经简单的磁选后,废渣中的铁质返回炼钢炉,作为炼钢原料,达到了污泥资源化利用的目的。附图说明为了使本发明的目的、技术方案和有益效果更加清楚,本发明提供如下附图进行说明:图1为本发明所采用的系统结构示意图,其中:1-钢厂污泥池、2-污泥调质池、3-柱塞泵、4-加热器、5-超临界气化反应器、6-换热器、7-气液分离器、8-储气柜、9-气体分离系统、10-排水池、11-废渣干燥系统;图2为污泥原泥的XRD图谱;图3为污泥SCW反应后残渣XRD谱图。具体实施方式下面将结合附图,对本发明的优选实施例进行详细的描述。图1为本发明所采用的系统结构示意图,如图所示,该装置包括依次相连的钢厂污泥池1、污泥调质池2、柱塞泵3、加热器4、超临界气化反应器5、换热器6、气液分离器7;钢厂污泥池1中的高含油含铁生产污泥通过污泥调质池2进行调质预处理后通过柱塞泵3输送到加热器4,在加热器4中进行预加热后的污泥输入超临界气化反应器5,经过超临界水气化反应后的泥浆通过换热器6进行降温和热交换处理;降温后的泥浆进入气液分离器7,使气体混合物从泥浆中充分分离出来;经分离处理后,得到甲烷和氢气的混合燃气,混合燃气随后进入储气柜8和气体分离系统9;渣水混合物进入排水池10中,在排水池10中加入絮凝剂,静置30-60min后,上清液排放到钢厂污水处理厂继续处理,池底污泥进行压滤,将压滤后的污泥送入废渣干燥系统11,通过换热器传下来的余热进行脱水烘干,烘干后的污泥直接送入炼钢炉,作为炼钢原料。实施例1:钢厂高含油含铁污泥采集于某钢厂冷轧污泥池,污泥为黑色,有润滑油气味,含油量较高。污泥的工业分析和元素分析如表1所示,污泥的无机元素组成如表2所示,污泥的XRD晶相分析如图2所示:表1污泥工业分析和元素分析M-水分;A-灰分;V-挥发分,oil-油含量,溶剂萃取法测定。*收到基**差减计算表2污泥无机元素组成(wt.%,db)Fe2O3CaOMgOAl2O3SiO2SO3P2O5Na2OTiO297.000.89523ppm0.210.700.350.10--Cr2O3MnOCuOK2OMoO3Tb4O7ZnOCuONiO777ppm0.45472ppm--123ppm516ppm472ppm397ppm在水/污泥质量比为5,反应温度660℃,压力23.4±0.4MPa,停留时间20min条件下,添加不同质量的CaO,气体产物组成和收率如表3和表4所示。由于水煤气变换反应进行得较为完全,气体中CO含量极低,气相产物以氢气、二氧化碳、甲烷和乙烷为主,其中氢气和甲烷各占三分之一左右。表3气相产物组成(vol.%)表4气相产物收率(ml/g干污泥)和气化率反应后残渣元素分析结果列于表5,污泥中的碳转化率为94.7%,未添加CaO时气化率接近60%,添加CaO后气化率达到90%左右。表5超临界水中反应后残渣元素分析(wt%,db)样品CHNS碳转化率(%)2#污泥反应后0.5470.0430.0030.02194.7图3为反应后残渣的XRD谱图,反应后残渣几乎全部转化为磁铁矿,添加CaO的残渣中有碳酸钙,其中图3(a)为SCW反应残渣,图3(b)为SCW添加CaO反应残渣。污泥在超临界水中反应后,水中总有机碳(TOC)和化学需氧量(COD)列于表6。表6污泥反应后水质CaO/污泥质量比Ca/C摩尔比TOC(mg/L)COD(g/L)100307.50.6620.330.782656.09.0430.471.091264.05.18最后说明的是,以上优选实施例仅用以说明本发明的技术方案而非限制,尽管通过上述优选实施例已经对本发明进行了详细的描述,但本领域技术人员应当理解,可以在形式上和细节上对其做出各种各样的改变,而不偏离本发明权利要求书所限定的范围。当前第1页1 2 3