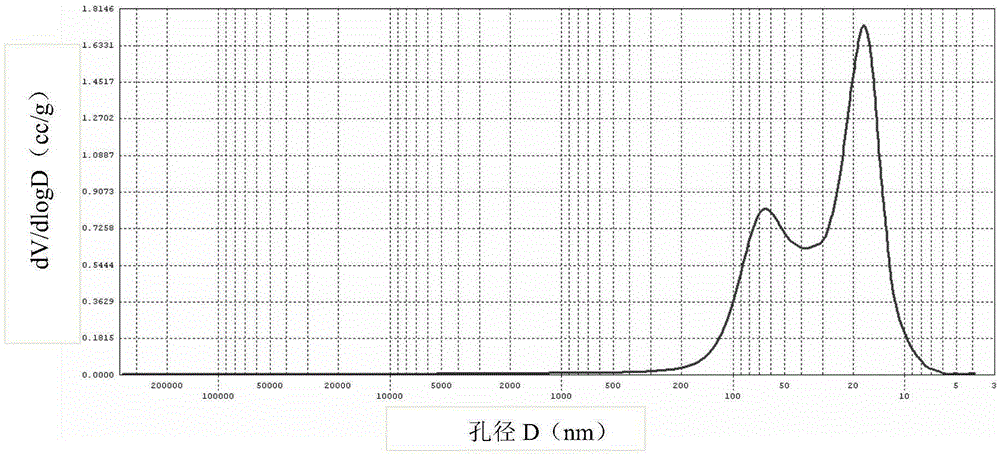
本发明涉及催化剂领域,具体地,涉及一种炔烃及二烯烃选择加氢催化剂和一种炔烃及二烯烃选择加氢方法。
背景技术:
:催化裂化、蒸汽裂解产生的碳四馏分中含有数量不等的炔烃、丁二烯、丁烯、丁烷等。烯烃是石油化工的基本原料,在烯烃加工过程中二烯烃、炔烃会引发副反应或在催化剂上聚合,易导致催化剂失活。因此在对碳四烯烃进一步加工之前,需要脱除其中的炔烃及二烯烃,选择加氢是最经济有效的手段。在选择性除炔烃、二烯烃领域,主要以Pd催化剂为主。Pd催化剂成本高,抗硫性能差,在含硫的原料中极易失活,增添了原料预处理的难度,增加了操作成本;使用铜和镍催化剂很少,只有UOP公司的KLP技术使用Cu为主活性组分,其代表申请是US4101451,其内容主要是对混合碳四馏分选择加氢除碳四炔烃,丁二烯不参加加氢反应,Cu催化剂的主要问题是单次运行周期短,需频繁再生。中国石油大学(刘建军,黄星亮;Ag助剂对C4烃选择加氢Ni基催化剂的影响,石油化工,2011,40(8),p825-830)研制了Ni-Ag催化剂用于催化裂化碳四馏分原料选择加氢过程,选择加氢仅运行59小时,催化剂活性就下降,而且催化剂积碳含量达1.6%。综上可见,由现有技术提供的炔烃及二烯烃加氢催化剂选择性略微提高,但催化剂在使用过程中存在易流失、单次运转周期短的缺陷。技术实现要素:针对现有技术炔烃及二烯烃选择加氢催化剂在使用过程中存在易失活、活性不高、单次运转周期短的缺陷,本发明提供一种新的炔烃及二烯烃选择加氢催化剂和一种新的炔烃及二烯烃选择加氢方法,由本发明提供的催化剂不仅有效脱除了碳四馏分中的炔烃及二烯烃,催化剂活性有所提高,而且催化剂的使用寿命也得以明显改善。本发明的发明人发现,上述由现有技术制备的选择加氢催化剂的载体多使用氧化铝,但在催化剂使用过程中,氧化铝表面的酸中心易引发不饱和烃齐聚生成“绿油”,导致催化剂的活性、选择性和稳定性下降。本发明的发明人通过研究进一步发现,对氧化铝载体进行炭包覆改性,不但可以保留原有载体的组织机构、机械性能和热稳定性等优点,而且载体表面覆炭后改变了氧化铝的孔结构,有利于炔烃及二烯烃选择加氢催化剂活性和稳定性的提高。因此,该技术可有效解决常规炔烃及二烯烃选择加氢催化剂的技术缺陷。由此,本发明提供一种新的炔烃及二烯烃选择加氢催化剂,该催化剂包括载体和负载在该载体上的活性组分,所述载体为覆炭氧化铝,所述活性组分包括Cu元素和Ni元素,以载体的重量为基准,所述Cu元素的含量为2-20重量%,所述Ni元素的含量为2-20重量%。本发明还提供了一种新的炔烃及二烯烃选择加氢的方法,该方法包括:在选择加氢条件下,将碳四馏分与本发明所提供的炔烃及二烯烃选择加氢催化剂接触。本发明所提供的炔烃及二烯烃选择加氢催化剂兼具良好分散性和结构稳定性,而且具有明显较高的活性及抗硫中毒能力。例如实施例6和对比例1的评价结果显示,反应40小时后,使用催化剂S6时,反应产物中剩余丁二烯9.8ppm,剩余炔烃3.1ppm,而使用催化剂D1时,反应产物中剩余丁二烯389.7ppm,剩余炔烃117.6ppm;反应666小时后,使用催化剂S6时,反 应产物中剩余丁二烯12.3ppm,剩余炔烃9.4ppm,而使用催化剂D1时,反应产物中剩余丁二烯871ppm,剩余炔烃409ppm;反应666小时后,催化剂S6积碳量只有2.4%,而催化剂D1积碳量高达19.8%,严重影响了催化剂的活性。上述结果显示,本发明提供的催化剂具有较高的活性和较好的稳定性,延长反应时间催化剂的活性变化较小,而对比例提供的催化剂反应初期活性较低,反应666小时后催化剂积碳严重,活性下降较快。本发明所提供的炔烃及二烯烃选择加氢方法能够有效脱除碳四馏分中的炔烃及二烯烃,具有较好的工业应用前景。本发明的其它特征和优点将在随后的具体实施方式部分予以详细说明。附图说明附图是用来提供对本发明的进一步理解,并且构成说明书的一部分,与下面的具体实施方式一起用于解释本发明,但并不构成对本发明的限制。在附图中:图1是实施例1所提供的覆炭氧化铝载体的孔径分布图;图2是现有技术所使用的常规氧化铝载体孔径分布图。具体实施方式以下对本发明的具体实施方式进行详细说明。应当理解的是,此处所描述的具体实施方式仅用于说明和解释本发明,并不用于限制本发明。本发明提供了一种炔烃及二烯烃选择加氢催化剂,该催化剂包括载体和负载在该载体上的活性组分,所述载体为覆炭氧化铝,所述活性组分包括Cu元素和Ni元素,以载体的重量为基准,所述Cu元素的含量为2-20重量%,所述Ni元素的含量为2-20重量%。本发明中,炔烃及二烯烃选择加氢催化剂指的是用于炔烃和/或二烯烃 选择加氢的催化剂。根据本发明,优选地,以载体的重量为基准,所述Cu元素的含量为2-12重量%,进一步优选为3-8重量%,所述Ni元素的含量为2-12重量%,进一步优选为3-5重量%。采用该优选的含量,能够进一步提高催化剂的活性和稳定性。根据本发明,优选地,该催化剂还含有金属助剂,所述金属助剂元素选自第VIII族金属元素、第IIA族金属元素和第IB族金属元素中的一种或多种,优选为铁元素、镁元素和银元素中的一种或多种。根据本发明,优选地,以载体的重量为基准,所述金属助剂元素的含量为0.5-5重量%,优选为0.5-1.5重量%。根据本发明,优选地,所述覆炭氧化铝中,炭含量为2-20重量%,进一步优选为5-17重量%。采用这种优选方式不仅有利于保留原有氧化铝的组织机构、机械性能和热稳定性等优点,而且有利于覆炭对氧化铝孔结构的改变。根据本发明,优选地,所述覆炭氧化铝的比表面积为80-190m2/g,进一步优选为130-150m2/g。采用该优选的比表面积,能够进一步提高催化剂的活性及稳定性。根据本发明,优选地,所述覆炭氧化铝的制备步骤包括:在惰性气体气氛下,将含有含碳化合物与氧化铝的混合物进行热处理。根据本发明,制备含有含碳化合物与氧化铝的混合物没有特别的要求,可以是将含碳化合物与水配成溶液,浸渍氧化铝然后进行干燥得到所述混合物;也可以是在覆炭装置内,汽化后的含碳化合物由惰性气体带入与氧化铝接触。根据本发明,优选地,在覆炭装置内,汽化后的含碳化合物与惰性气体的体积比为1:2-20。根据本发明,优选地,所述惰性气体选自氮气、氦气、氖气、氩气、氪 气和氙气中的一种或多种,优选为氮气、氦气和氩气中的一种或多种,更优选为氮气。根据本发明,优选地,所述热处理的条件包括:热处理温度为400-1200℃,优选为700-1000℃。根据本发明,优选地,所述热处理的条件包括:热处理时间为0.5-12h,优选为3-6h。根据本发明,所述含碳化合物的种类可选范围较宽,通过热处理能够分解沉积的化合物均可用于本发明,针对本发明,优选所述含碳化合物选自可溶性糖、C5-C10的烷烃、C5-C10的烯烃、C2-C7的有机酸、C2-C6的多元醇和C2-C7的有机胺中的一种或多种。在本发明中,所述可溶性糖包括葡萄糖、果糖、麦芽糖、蔗糖和可溶性淀粉中的一种或多种。所述C2-C7的有机酸可以为乙酸、马来酸、草酸、氨基三乙酸、1,2-环己烷二胺四乙酸、柠檬酸、酒石酸和苹果酸中的一种或多种。所述C2-C6的多元醇可以为乙二醇、丙三醇、二乙二醇和丁二醇中的一种或多种。在本发明中,所述含碳化合物特别优选选自可溶性淀粉、蔗糖、葡萄糖、柠檬酸和乙二胺中的一种或多种。本发明中,对于金属活性组分Cu和Ni负载到载体的方式没有特别的限制,优选为浸渍法。所述浸渍法可以为共浸渍法,也可以为分步浸渍法,优选为共浸渍法。当采用共浸渍法时,可以先将各活性组分配制为混合溶液,然后共同浸渍于载体上。当采用分步浸渍法时,可以在载体浸渍一种活性组分后并干燥后,再依次浸渍其他活性组分。本发明中,对于金属助剂的引入方式没有特别的限制,优选为浸渍法。本发明中,金属助剂可以与活性组分中的一种或多种共同浸渍在载体 上,也可以在活性组分引入前或引入后,单独浸渍在载体上,优选为金属助剂与活性组分共同浸渍在载体上。本发明还提供一种炔烃和二烯烃选择加氢方法,该方法包括:在选择加氢条件下,将碳四馏分与本发明提供的催化剂接触。在本发明中,所述炔烃及二烯烃选择加氢方法的选择加氢条件例如可以包括:入口温度为20-70℃,反应压力为0.8-2.0MPa,碳四馏分原料液相空速为1-20h-1。在本发明中,所述碳四馏分物料可以为常规的碳四馏分物料,通常含有正丁烷、异丁烷、正丁烯、异丁烯、1,2-丁二烯、1,3-丁二烯、1-丁烯、2-丁烯(顺式2-丁烯、反式2-丁烯)。以下通过具体实施例详细说明本发明的实施过程和所产生的有益效果,旨在帮助阅读者更清楚地了解本发明的精神实质所在,但不能对本发明的实施范围构成任何限定。以下实施例中,覆炭载体中炭含量采用元素分析仪测定;载体比表面积和孔径分布采用比表面及孔径分布测定仪通过BET低温氮吸附法测定;采用日本理学电机工业株式会社3271E型X射线荧光光谱仪,对催化剂中各元素的含量进行分析测定;催化剂上的积碳量通过热重分析测得,热重在NETZSCH公司STA449CJupiter型热分析仪上进行,工作条件为样品重量50mg,升温速率10K/min,升温至1073K,流动气氛为空气。实施例1将150g氧化铝载体(孔径分布图如图2所示)浸渍于含有36g蔗糖和125ml去离子水的溶液中,浸渍时间2h,自然风干后,于100℃干燥8h,然后在氮气气氛下,在820℃下热处理6h,其中,氮气流速为40ml/min,冷却至室温,得到Z1载体。Z1载体的比表面积和炭含量列于表1,载体Z1的 孔径分布图如图1所示。由图1和图2可以看出,向氧化铝载体覆炭后明显改变了载体的孔径分布。称取100gZ1载体浸渍于含有19gCu(NO3)2·3H2O、24.7gNi(NO3)2·6H2O、3.6gFe(NO3)3·9H2O和80ml去离子水的溶液中,浸渍时间为12h,自然风干后,于110℃干燥8小时,在氮气气氛下,400℃焙烧4h,制得催化剂S1。催化剂S1的组成列于表2。实施例2将150g氧化铝载体装入覆炭装置内,将汽化后的环己烯与氮气制成混合气(汽化后的环己烯与氮气的体积比为10:90)通入覆炭装置与氧化铝载体在700℃、常压下热处理4h,混合气流速为40ml/min,反应完成后,得到载体Z2。Z2载体的比表面积和炭含量列于表1。称取100gZ2载体浸渍于含有19gCu(NO3)2·3H2O、24.7gNi(NO3)2·6H2O、3.6gFe(NO3)3·9H2O和80ml去离子水的溶液中,浸渍时间为12h,自然风干后,于110℃干燥8小时,在氮气气氛下,400℃焙烧4h,制得催化剂S2。催化剂S2的组成列于表2。实施例3将150g氧化铝载体浸渍于含有57.1g可溶性淀粉和115ml去离子水的溶液中,浸渍时间1h,自然风干后,于90℃干燥8h,然后在氮气气氛下,在1000℃下热处理6h,其中,氮气流速为40ml/min,冷却至室温,得到Z3载体。Z3载体的比表面积和炭含量列于表1。称取100gZ3载体浸渍于含有30.4gCu(NO3)2·3H2O、19.8gNi(NO3)2·6H2O、21.3gMg(NO3)2·6H2O和75ml去离子水的溶液中,浸渍时间为6h,自然风干后,于110℃干燥8小时,在氮气气氛下,400℃焙烧4h, 制得催化剂S3。催化剂S3的组成列于表2。实施例4称取100g实施例1所述Z1载体浸渍于含有12gCu(NO3)2·3H2O、16gNi(NO3)2·6H2O、1.9gAgNO3和72ml去离子水的溶液中,浸渍时间为6h,自然风干后,于110℃干燥8小时,在氮气气氛下,450℃热处理4h,制得催化剂S4。催化剂S4的组成列于表2。实施例5按照实施例1的方法,所不同的是,使用的蔗糖的量为75g,热处理的时间为12h。制得Z5载体的比表面积和炭含量列于表1,制得催化剂S5的组成列于表2。实施例6按照实施例1的方法,所不同的是,催化剂制备过程中,溶液中不含有Fe(NO3)3·9H2O。制得的催化剂记为S6。催化剂S6的组成列于表2。对比例1按照实施例6的方法,所不同的是,所使用的载体为实施例1所述氧化铝,具体过程为:称取100g氧化铝载体浸渍于含有19gCu(NO3)2·3H2O、24.7gNi(NO3)2·6H2O和80ml去离子水的溶液中,浸渍时间为12h,自然风干后,于110℃干燥8小时,在氮气气氛下,400℃焙烧4h,制得催化剂D1。催化剂D1的组成列于表2。对比例2按照实施例1的方法,所不同的是,所使用的载体为实施例1所述氧化铝,具体过程为:称取100g氧化铝载体浸渍于含有19gCu(NO3)2·3H2O、24.7gNi(NO3)2·6H2O、3.6gFe(NO3)3·9H2O和80ml去离子水的溶液中,浸渍时间为12h,自然风干后,于110℃干燥8小时,在氮气气氛下,400℃焙烧4h,制得催化剂D2。催化剂D2的组成列于表2。对比例3按照实施例1的方法,所不同的是,所使用的载体为活性炭,具体过程为:称取100g活性炭浸渍于含有19gCu(NO3)2·3H2O、24.7gNi(NO3)2·6H2O、3.6gFe(NO3)3·9H2O和80ml去离子水的溶液中,浸渍时间为12h,自然风干后,于110℃干燥8小时,在氮气气氛下,400℃焙烧4h,制得催化剂D3。催化剂D3的组成列于表2。表1载体比表面积(m2/g)含炭量(wt%)实施例1Z11389.7实施例2Z213516.9实施例3Z31425.8实施例4Z11389.7实施例5Z513120实施例6Z11389.7对比例1氧化铝1470对比例2氧化铝1470对比例3活性炭800100表2催化剂Cu(wt%)Ni(wt%)助剂(wt%)实施例1S15.05.0Fe(0.5)实施例2S24.94.8Fe(0.5)实施例3S38.13.9Mg(1.5)实施例4S43.43.5Ag(1.2)实施例5S54.85.1Fe(0.6)实施例6S65.05.0-对比例1D15.15.0-对比例2D25.15.1Fe(0.5)对比例3D35.05.2Fe(0.5)实施例7-12和对比例4-6实施例7-12和对比例4-6用于说明本发明的炔烃及二烯烃选择加氢催化剂在碳四馏分选择加氢除炔烃及二烯烃中的应用和碳四馏分选择加氢除炔及二烯烃的方法。分别在实施例1-6和对比例1-3所制备的催化剂S1、S2、S3、S4、S5、S6、D1、D2和D3的存在下(分别对应实施例1-6和对比例1-3),在两段固定床反应器中对碳四馏分进行加氢除炔及二烯烃处理,用反应40小时所得反应产物中丁二烯和炔烃的剩余量(采用气相色谱仪分析测得)来表示催化剂的活性,反应40小时所得反应产物中丁二烯和炔烃的剩余量越少,代表催化剂的活性越高,催化剂的活性评价结果列于表4。对比使用催化剂S6和D1反应666小时后,反应产物中丁二烯和炔烃的剩余量及催化剂上的积 碳量来评价催化剂的稳定性,结果列于表5。实验条件控制如下:每段固定床反应器中催化剂的装填量为50ml,催化剂使用前,用氮气置换反应器后,在400℃,常压下氢气还原4h,加氢反应过程中,反应压力为2.0MPa,空速为3h-1,催化剂床层入口温度为35℃,氢气与炔烃和二烯烃的摩尔比为5,碳四馏分组成见表3。表3组分原料含量(wt%)异丁烷30.57正丁烷14.27反-2-丁烯13.22正丁烯21.21异丁烯2.26顺-2-丁烯9.001,2-丁二烯0.081,3-丁二烯3.08丙烯0.79乙烯基乙炔3.341-丁炔1.18正丙硫醇0.0011表4催化剂剩余丁二烯,ppm剩余炔烃,ppm实施例7S15.96.6实施例8S24.40实施例9S32.70实施例10S42.40实施例11S54912实施例12S69.83.1对比例4D1389.7117.6对比例5D2110.153.4对比例6D389005600表5反应666小时后催化剂评价结果及积碳量催化剂积碳量(wt%)剩余丁二烯,ppm剩余炔烃,ppm实施例12S62.412.39.4对比例4D119.8871409由表4可以看出,在相同反应条件下,催化剂S1、S2、S3、S4、S5和S6的活性明显优于催化剂D1、D2和D3。将表4和表5结合起来可以看出,在延长反应时间至666小时后,催化剂S6的活性的下降要远远低于催化剂D1,从催化剂积碳情况来看,实施例12中催化剂S6只有少量积碳,而对比例4中催化剂D1积碳严重。综上所述,本发明提供的催化剂不仅有效提高了催化剂的活性,并且提高了催化剂的稳定性。以上详细描述了本发明的优选实施方式,但是,本发明并不限于上述实施方式中的具体细节,在本发明的技术构思范围内,可以对本发明的技术方案进行多种简单变型,这些简单变型均属于本发明的保护范围。另外需要说明的是,在上述具体实施方式中所描述的各个具体技术特征,在不矛盾的情况下,可以通过任何合适的方式进行组合,为了避免不必要的重复,本发明对各种可能的组合方式不再另行说明。此外,本发明的各种不同的实施方式 之间也可以进行任意组合,只要其不违背本发明的思想,其同样应当视为本发明所公开的内容。当前第1页1 2 3