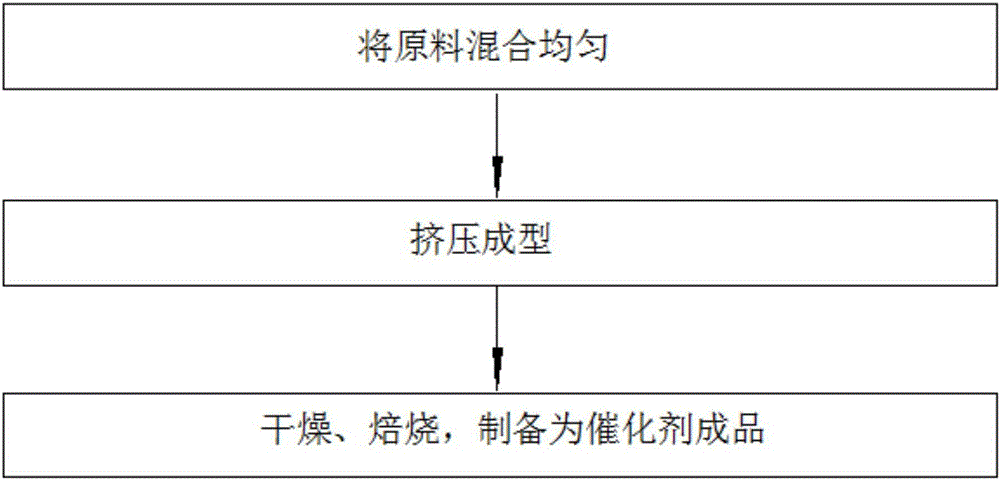
本发明涉及废烟气脱硝催化剂的回收和利用
技术领域:
,具体涉及一种废烟气脱硝催化剂的回收处理方法及催化剂的制备方法。
背景技术:
:SCR脱硝工艺因具有脱硝效率高、适应性强、可靠性高等优点而得到广泛应用。但经过多年的运行,积累了大量失效的废弃催化剂,由于这些失效的废弃催化剂中含有砷、矾等重金属污染物,如不进行有效处置,随意堆放将会成为新的污染源。目前国内的催化剂总体制造及使用水平不高,废弃催化剂的更换频率和数量均高于国外。因此这些有毒废弃催化剂的处理已成为亟待解决的问题。废烟气脱硝催化剂除了含有TiO2、V2O5、WO3外,还含有铬、铍、砷和汞等重金属,一方面,SCR催化剂中的V2O5作为有毒物质,对生态系统的危害主要体现在对人体的危害。另一方面,燃煤电厂废烟气脱硝催化剂的主要危险特性为浸出毒性,其中铍、铜、砷等重金属的浓度普遍高于新脱硝催化剂的浸出浓度。如不能妥善进行资源化、无害化处置,极易造成环境污染。作为危险废物,废SCR催化剂的综合利用,必须从资源利用和环境影响两方面考虑,既要有废催化剂资源利用的可行性,又要在经济成本和环境保护中找到最佳平衡点。国内外废SCR催化剂资源化利用的研究才处于起步阶段,处理方法和技术路线还还需要进一步的完善和优化,主要方法有:1)焚烧法;2)固化法;3)填埋法;4)重金属提纯法;5)作为钢铁原料;6)作为建筑、水泥及陶瓷等原料,加以资源化利用等。上述处理方法中显然没有得到资源的有效化利用,并且国内目前有部分SCR催化剂厂家将催化剂生产过程中产生的不合格催化剂或催化剂废料用于制备新鲜催化剂,有关专利如(CN201010589554.1),因其使用的催化剂未经过烟气冲刷,其组分与新催化剂相同,不含有其他重金属有害成分,因此在实验过程中参配比例较大。另外如专利(CN201310370818.8)采用废旧催化剂与新鲜原材料混合使用,制备得到新鲜催化剂,虽然有一定好评,但其对废旧催化剂的清洗时使用的化学原料较多,工段较多,耗时太长,并且在制备新鲜催化剂过程中所使用的原料也较多,成本负担过重,最后也没有实验证明新鲜催化剂的脱硝效果,有一定的技术缺陷。现在国外采用废催化剂制备新催化剂的方法有了一定的研究,但没有明确给出掺配比例的数据,因此需要进一步开发研究相应技术。技术实现要素:本发明的目的在于提供一种废烟气脱硝催化剂的回收处理方法及催化剂的制备方法。为实现上述发明目的之一,本发明采用如下技术方案:一种废烟气脱硝催化剂的回收处理方法,包括以下步骤;S1.将废旧催化剂进行物理清洗,以去除废旧催化剂表面附着物;S2.将废旧催化剂进行化学清洗,以去除废旧催化剂中积聚的中毒物质;S3.干燥,以脱去废旧催化剂中的水基;S4.将废旧催化剂粉碎、煅烧、研磨,即得到催化剂回收料粉体。作为本发明进一步改进的技术方案,步骤S2具体包括:一次药洗和二次药洗;其中,一次药洗所采用清洗液为柠檬酸钠、硫酸、硝酸中的一种或多种的水溶液,清洗时间为40-60分钟;二次药洗所采用清洗液为柠檬酸钠、硫酸、硝酸中的一种或多种、聚乙二醇、乳化剂、促进剂、粘泥剥离剂的水溶液,清洗时间为20-60分钟。作为本发明进一步改进的技术方案,二次药洗所采用的清洗液由以下质量比的原料与水混合后搅拌20-40分钟,静置2-5小时制得;所述原料的质量比为柠檬酸钠、硫酸、硝酸中的一种或多种1-2%、聚乙二醇5-10%、乳化剂1-2%、促进剂1-2%、粘泥剥离剂2-5%。作为本发明进一步改进的技术方案,步骤S1具体包括:使用吹灰器对废旧催化剂进行物理清灰;然后将废旧催化剂移入清洗槽中,采用双频超声震荡,频率选择为28/40kHz,超声震荡时间为20-40min。作为本发明进一步改进的技术方案,步骤S4具体包括:将废旧催化剂粉碎至200-400目;将废旧催化剂在400-600℃的条件下煅烧3-5小时,研磨至D50小于5μm。为实现上述另一发明目的,本发明采用如下技术方案:一种催化剂的制备方法,将原料混合均匀,挤压成型,干燥、焙烧,制备为催化剂成品;所述原料按质量份由以下组分构成:催化剂回收料粉体5-45份、二氧化钛50-80份、五氧化二钒0.6-1.2份、三氧化钨1-10份、羟乙基纤维素1-10份、乙二醇1-5份、占原料总质量5%-10%的粘合剂;其中,催化剂回收料粉体为上述废烟气脱硝催化剂的回收处理方法所制得。作为本发明进一步改进的技术方案,所述原料按质量份由以下组分构成:催化剂回收料粉体45份、二氧化钛55份、五氧化二钒1份、三氧化钨8份、羟乙基纤维素1份、乙二醇1份、占原料总质量5%的粘合剂。作为本发明进一步改进的技术方案,所述原料按质量份由以下组分构成:催化剂回收料粉体15份、二氧化钛75份、五氧化二钒1份、三氧化钨9份、羟乙基纤维素10份、乙二醇5份、占原料总质量8%的粘合剂。作为本发明进一步改进的技术方案,所述原料按质量份由以下组分构成:催化剂回收料粉体25份、二氧化钛65份、五氧化二钒1份、三氧化钨8.5份、羟乙基纤维素5份、乙二醇2份、占原料总质量5%的粘合剂。相对于现有技术,本发明的技术效果在于:采用上述方法新制备的催化剂有较良好的活性,同时所添加的成分物质对环境无污染,价格相对低廉,成本较低,同时采用了废旧脱硝催化剂回收料为主体,增强了活性点位,减少后续附着物质的添加,节约了成本,促进了催化剂的稳定性和拓展性。附图说明图1是本发明实施方式中一种废烟气脱硝催化剂的回收处理方法的流程示意图;图2是本发明实施方式一种催化剂的制备方法的流程示意图。具体实施方式以下将结合附图所示的具体实施方式对本发明进行详细描述。但这些实施方式并不限制本发明,本领域的普通技术人员根据这些实施方式所做出的结构、方法、或功能上的变换均包含在本发明的保护范围内。请参见图1,一种废烟气脱硝催化剂的回收处理方法,包括以下步骤;S1.将废旧催化剂进行物理清洗,以去除废旧催化剂表面附着物;S2.将废旧催化剂进行化学清洗,以去除废旧催化剂中积聚的中毒物质;S3.干燥,以脱去废旧催化剂中的水基;S4.将废旧催化剂粉碎、煅烧、研磨,即得到催化剂回收料粉体。进一步的,步骤S2具体包括:一次药洗和二次药洗;其中,一次药洗所采用清洗液为柠檬酸钠、硫酸、硝酸中的一种或多种的水溶液,清洗时间为40-60分钟;二次药洗所采用清洗液为柠檬酸钠、硫酸、硝酸中的一种或多种、聚乙二醇、乳化剂、促进剂、粘泥剥离剂的水溶液,清洗时间为20-60分钟。进一步的,二次药洗所采用的清洗液由以下质量比的原料与水混合后搅拌20-40分钟,静置2-5小时制得;所述原料的质量比为柠檬酸钠、硫酸、硝酸中的一种或多种1-2%、聚乙二醇5-10%、乳化剂1-2%、促进剂1-2%、粘泥剥离剂2-5%。进一步的,步骤S1具体包括:使用吹灰器对废旧催化剂进行物理清灰;然后将废旧催化剂移入清洗槽中,采用双频超声震荡,频率选择为28/40kHz,超声震荡时间为20-40min。进一步的,步骤S4具体包括:将废旧催化剂粉碎至200-400目;将废旧催化剂在400-600℃的条件下煅烧3-5小时,研磨至D50小于5μm。在以上废旧催化剂的处理过程中,利用独特的清洗液和清洗工艺,对各组分进行了物理和化学清洗,使得废旧催化剂中的有害物质逐步被清洗出来,而且保留了一部分脱硝催化剂的有效成分,充分满足了作为回收料制备新催化剂的条件。请参见图2,一种催化剂的制备方法,将原料混合均匀,挤压成型,干燥、焙烧,制备为催化剂成品;所述原料按质量份由以下组分构成:催化剂回收料粉体5-45份、二氧化钛50-80份、五氧化二钒0.6-1.2份、三氧化钨1-10份、羟乙基纤维素1-10份、乙二醇1-5份、占原料总质量5%-10%的粘合剂;其中,催化剂回收料粉体为上述废烟气脱硝催化剂的回收处理方法所制得。需要说明的是,粘合剂的质量计入原料总质量中。进一步的,所述原料按质量份由以下组分构成:催化剂回收料粉体45份、二氧化钛55份、五氧化二钒1份、三氧化钨8份、羟乙基纤维素1份、乙二醇1份、占原料总质量5%的粘合剂。进一步的,所述原料按质量份由以下组分构成:催化剂回收料粉体15份、二氧化钛75份、五氧化二钒1份、三氧化钨9份、羟乙基纤维素10份、乙二醇5份、占原料总质量8%的粘合剂。进一步的,所述原料按质量份由以下组分构成:催化剂回收料粉体25份、二氧化钛65份、五氧化二钒1份、三氧化钨8.5份、羟乙基纤维素5份、乙二醇2份、占原料总质量5%的粘合剂。采用废脱硝催化剂回收料制备的新鲜催化剂在成分组成上基本和现有工艺持平,而且不用额外的添加工艺,相对于传统新催化剂的制备过程中添加的贵重金属氧化物有所减少,降低了成本。制备的新鲜催化剂比表面积、孔容、抗压强度、活性、脱硝效率等性能,相对于传统制备方法制造的新催化剂没有降低。以下将结合几个本发明的实施例对本发明作进一步的说明。实施例1催化剂回收料粉体的制备首先,将废旧催化剂移入吹灰箱中,使用手持式吹灰器对废旧催化剂进行物理清灰,清除标准:表面没有堵孔的存在即可;进一步,将废旧催化剂移入清洗槽中,采用双频超声震荡,频率选择28/40kHz,超声时间约为20-40min;进一步,采用药洗(一次药洗),选取柠檬酸钠、硫酸、硝酸中的一种或多种对废旧催化剂进行清洗,去除中毒物质,清洗时间约为40-60min;进一步,对上一步药洗完成后的废旧催化剂进行水洗,去除酸和表面杂质,清洗时间约为20-40min;进一步,继续采用药洗(二次药洗),配制清洗液,具体为聚乙二醇10%、乳化剂2%、促进剂2%、柠檬酸、硫酸、硝酸中的一种或多种2%、粘泥剥离剂5%,机械搅拌20-40min,静置2-4h,浸泡时间约为20-60min;进一步,用水清洗废旧催化剂表面和孔道,清洗时间10-20min;接着,将处理好的废旧催化剂送进干燥间,在温度80-150℃间,干燥2-5h;进一步,将干燥好的废旧催化剂除去金属框架,将催化剂表面整理干净,送入粉碎机,粉碎至200-400目,得到催化剂回收料;进一步,将粉碎好的催化剂回收料送进煅烧炉,在温度400-600℃之间,煅烧3-5h后,脱去了粉体中的水基,送进研磨机内,研磨至D50小于5μm,得到催化剂回收料粉体。催化剂成品的制备将二氧化钛55份,五氧化二钒1份,三氧化钨8份,催化剂回收料粉体45份,羟乙基纤维素1份,乙二醇1份,粘合剂5%经混匀,挤压成型,干燥,焙烧后得到催化剂成品,其规格为150*150*700mm,18孔×18孔。性能参数测试经比表面积测试仪检测,测得催化剂成品比表面积为52m2/g;经抗压力测试仪器测试,其横向抗压强度和纵向抗压强度分别为0.8Mpa和2.4Mpa活性氨逃逸率测试表1烟气条件测试类型活性温度,℃380H2O,Vol%6O2,Vol%5入口SO2,ppm500入口NOX,ppm300层数2长度,mm700NH3/NOX摩尔比1.02表2参数设计值活性脱硝率(%)氨逃逸率(ppm)实际测试值39.590.231.88实施例2催化剂回收料粉体的制备首先,将废旧催化剂移入吹灰箱中,使用手持式吹灰器对废旧催化剂进行物理清灰,清除标准:表面没有堵孔的存在即可;进一步,将废旧催化剂移入清洗槽中,采用双频超声震荡,频率选择28/40kHz,超声时间约为20-40min;进一步,采用药洗(一次药洗),选取柠檬酸钠、硫酸、硝酸中的一种或多种对废旧催化剂进行清洗,去除中毒物质,清洗时间约为40-60min;进一步,对上一步药洗完成后的废旧催化剂进行水洗,去除酸和表面杂质,清洗时间约为20-40min;进一步,继续采用药洗(二次药洗),配制清洗液,具体为聚乙二醇5%、乳化剂1%、促进剂1%、柠檬酸、硫酸、硝酸中的一种或多种1%、粘泥剥离剂2%,机械搅拌20-40min,静置3-5h,浸泡时间约为20-60min;进一步,用水清洗废旧催化剂表面和孔道,清洗时间10-20min;接着,将处理好的废旧催化剂送进干燥间,在温度400-600℃间,干燥3-5h;进一步,将干燥好的废旧催化剂除去金属框架,将催化剂表面整理干净,送入粉碎机,粉碎至200-400目,得到催化剂回收料;进一步,将粉碎好的催化剂回收料送进煅烧炉,在温度400-600℃之间,煅烧3-5h后,脱去了粉体中的水基,送进研磨机内,研磨至D50小于5μm,得到催化剂回收料粉体。催化剂成品的制备将二氧化钛75份,五氧化二钒1份,三氧化钨9份,催化剂回收料粉体15份,羟乙基纤维素10份,乙二醇5份,粘合剂8%经混匀,挤压成型,干燥,焙烧后得到催化剂成品,其规格为150*150*700mm,18孔×18孔。性能参数测试经比表面积测试仪检测,测得催化剂成品比表面积为56m2/g;经抗压力测试仪器测试,其横向抗压强度和纵向抗压强度分别为0.8Mpa和2.6Mpa活性氨逃逸率测试表3烟气条件测试类型活性温度,℃380H2O,Vol%6O2,Vol%5入口SO2,ppm500入口NOX,ppm300层数2长度,mm700NH3/NOX摩尔比1.02表4参数设计值活性脱硝率(%)氨逃逸率(ppm)实际测试值40.191.21.36实施例3催化剂回收料粉体的制备首先,将废旧催化剂移入吹灰箱中,使用手持式吹灰器对废旧催化剂进行物理清灰,清除标准:表面没有堵孔的存在即可;进一步,将废旧催化剂移入清洗槽中,采用双频超声震荡,频率选择28/40kHz,超声时间约为20-40min;进一步,采用药洗(一次药洗),选取柠檬酸钠、硫酸、硝酸中的一种或多种对废旧催化剂进行清洗,去除中毒物质,清洗时间约为40-60min;进一步,对上一步药洗完成后的废旧催化剂进行水洗,去除酸和表面杂质,清洗时间约为20-40min;进一步,继续采用药洗(二次药洗),配制清洗液,具体为聚乙二醇8%、乳化剂1%、促进剂2%、柠檬酸、硫酸、硝酸中的一种或多种2%、粘泥剥离剂3%,机械搅拌20-40min,静置2-5h,浸泡时间约为20-60min;进一步,用水清洗废旧催化剂表面和孔道,清洗时间10-20min;接着,将处理好的废旧催化剂送进干燥间,在温度400-600℃间,干燥3-6h;进一步,将干燥好的废旧催化剂除去金属框架,将催化剂表面整理干净,送入粉碎机,粉碎至200-400目,得到催化剂回收料;进一步,将粉碎好的催化剂回收料送进煅烧炉,在温度400-600℃之间,煅烧3-5h后,脱去了粉体中的水基,送进研磨机内,研磨至D50小于5μm,得到催化剂回收料粉体。催化剂成品的制备将二氧化钛65份,五氧化二钒1份,三氧化钨8.5份,催化剂回收料粉体25份,羟乙基纤维素5份,乙二醇2份,粘合剂5%经混匀,挤压成型,干燥,焙烧后得到催化剂成品,其规格为150*150*700mm,18孔×18孔。性能参数测试经比表面积测试仪检测,测得催化剂成品比表面积为54m2/g;经抗压力测试仪器测试,其横向抗压强度和纵向抗压强度分别为0.8Mpa和2.5Mpa活性氨逃逸率测试表5烟气条件测试类型活性温度,℃380H2O,Vol%6O2,Vol%5入口SO2,ppm500入口NOX,ppm300层数2长度,mm700NH3/NOX摩尔比1.02表6参数设计值活性脱硝率(%)氨逃逸率(ppm)实际测试值39.890.561.38为了对比说明,以下给出一传统催化剂成品的制备方法,其原料中并不包括催化剂回收料粉体。将二氧化钛84份,五氧化二钒1份,三氧化钨9份,玻璃纤维5%,羟乙基纤维素5份,稀土氧化物3%,乙二醇2份,粘合剂5%经混匀,挤压成型,干燥,焙烧后得到脱硝催化剂组合物,其规格为150*150*700mm,18孔×18孔。性能参数测试经比表面积测试仪检测,测得脱硝催化剂比表面积为54m2/g;经抗压力测试仪器测试,其横向抗压强度和纵向抗压强度分别为0.8Mpa和2.6Mpa活性氨逃逸率测试表7烟气条件测试类型活性温度,℃380H2O,Vol%6O2,Vol%5入口SO2,ppm500入口NOX,ppm300层数2长度,mm700NH3/NOX摩尔比1.02表8参数设计值活性脱硝率(%)氨逃逸率(ppm)实际测试值40.391.51.32对比可知,采用本发明方法制造出的催化剂成品与采用传统方法制造的催化剂成品,性能参数接近。最后应说明的是:以上实施方式仅用以说明本发明的技术方案,而非对其限制;尽管参照前述实施方式对本发明进行了详细的说明,本领域的普通技术人员应当理解:其依然可以对前述各实施方式所记载的技术方案进行修改,或者对其中部分技术特征进行等同替换;而这些修改或者替换,并不使相应技术方案的本质脱离本发明各实施方式技术方案的精神和范围。当前第1页1 2 3