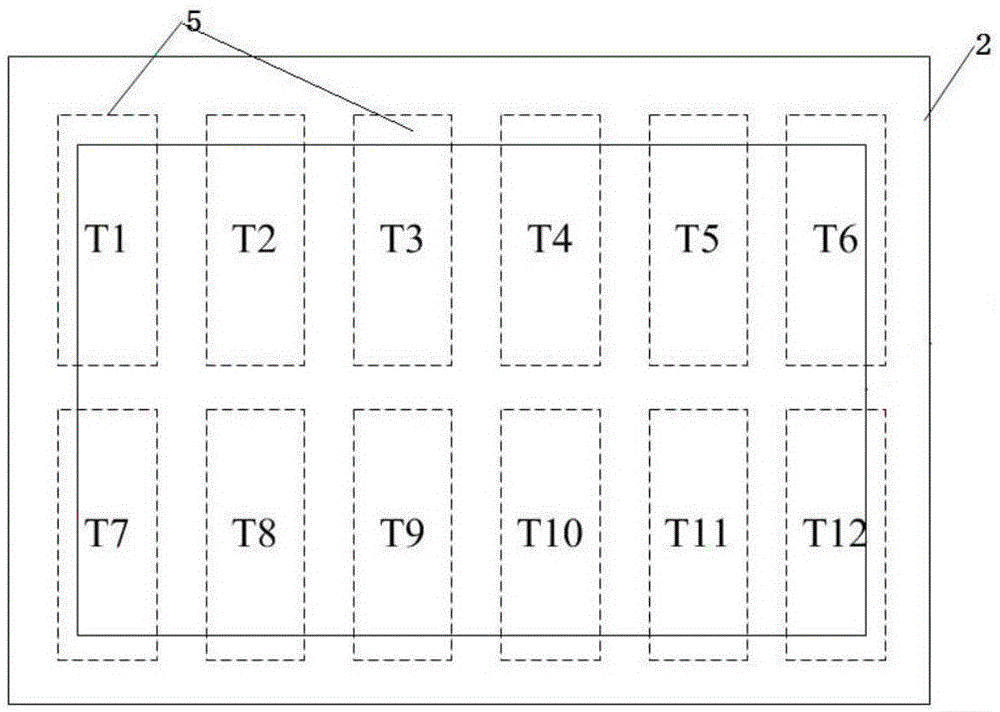
本发明涉及选择性催化还原催化剂的再生
技术领域:
,具体涉及一种失活脱硝催化剂的清洗装置和方法。
背景技术:
:氮氧化物(NOx)是大气的主要污染物之一。在我国,燃煤电厂是NOx的重要排放源。近年来,随着选择性催化还原(SCR)技术的普及和应用,我国燃煤电厂的NOx减排成效明显。然而,也同时带来了一系列问题。作为SCR脱硝技术的核心,脱硝催化剂按形式可分为蜂窝式、板式和波纹板式三种类型,一般在运行24000h后就会失活,届时为满足NOx排放指标,需要更换失活催化剂。若直接填埋,不仅会造成资源的极大浪费,更会带来二次污染。因此,对催化剂进行再生,使其脱硝效率恢复至新鲜样品水平,对燃煤电厂的节能降耗意义重大。脱硝催化剂的再生方法包括热再生、湿法清洗再生、热还原再生等。其中,工业应用最为广泛的是湿法清洗再生,主要流程为:除灰-清洗液清洗-水洗-干燥-焙烧。清洗液可根据催化剂的具体失活原因,选择碱性、酸性等多种配方,目前已有多种技术在本领域公开,如CN104492507A、CN103949291A、CN104209148A、CN103551209A、CN102059156A、CN104162456A等。一般而言,酸性清洗液用以去除催化剂上的碱性金属如K、Na、Ca等,碱性清洗液则可以去除催化剂上的As、S等元素。为增强再生效果,超声技术也逐渐被应用于脱硝催化剂的清洗过程中,这是利用了超声波在液体中的空化作用,去除催化剂表面和孔道中的污染物颗粒。发明专利CN104069900A公开了一种用于废弃脱硝催化剂再生的清洗方法和装置。其超声清洗装置,包括清洗箱体、模块旋转箱、减速电机、超声振板、沉降池、多级过滤装置等。再生流程为:用高压水枪对催化剂模块进行冲洗;曝气管通蒸汽加热清洗箱体中的水;曝气管通压缩空气进行水气清洗操作;超声清洗;再次高压水枪冲洗。发明专利CN103464221A公开了SCR脱硝系统催化剂再生设备及再生工艺方法。其再生设备包括空气压缩机、清洗槽、超声波振动器、加热器、热风炉等。超声波振动器位于清洗槽底层。该再生设备可以完成吹扫、清洗、干燥处理,催化剂的再生处理效率较高。发明专利CN104801182A公开了一种脱硝催化剂的再生方法。该方法在清洗过程中,清洗液温度约为30℃,清洗时间30min,超声波功率为6KW,超声频率40Hz。发明专利CN104722206A公开了一种失活SCR脱硝催化剂的再生方法。该方法中,催化剂在进行酸液处理和碱液处理时,采用的超声波功率为200-500W,处理时间20-40min。然而,尽管超声处理可以有效增强失活脱硝催化剂的清洗效果,但同时也会对催化剂的物理性能,如磨损强度、机械强度等产生较大的影响。清洗过程中,催化剂活性组分V2O5的流失量也会受超声处理影响而增加。此外,不同形式的脱硝催化剂,其物理化学性能也各有差异;失活催化剂的中毒原因、积灰状况也不同。因此,在超声处理之前,需要针对不同催化剂的具体情况,制定不同的超声清洗方案。但上述技术均没有涉及这方面的问题,且目前本领域所公开的超声清洗技术,清洗过程也多采用固定的超声技术方案。技术实现要素:发明目的:针对现有技术中的上述缺陷,本发明提供一种失活脱硝催化剂的超声清洗装置和方法。技术方案:本发明所述的一种失活脱硝催化剂的超声清洗装置,包括清洗槽、第一超声系统和第二超声系统,第一超声系统和第二超声系统均包含若干个超声振板;其中,第一超声系统固定在清洗槽的底部,第二超声系统活动连接在清洗槽的上部。本发明的失活脱硝催化剂的超声清洗装置设置有上下两个超声系统,位于底部的是固定式的,位于上部的是投入式的;再者,两个超声系统均由数个超声振板构成,更便于灵活使用,实现针对性的定向超声清洗,和全面的清洗效果。优选的,所述第一超声系统包含8-24块均匀、有序排列的超声振板;所述第二超声系统包含4-16块均匀、有序排列的超声振板;所述超声振板的频率独立控制,单独投用。通过将超声系统分为数个可以单独开启的超声振板、并且进行了均匀的排列之后,实现了对残余积灰较多区域的定向超声清洗。优选的,所述的清洗装置还包括恒温加热装置。以便于实现清洗液的恒温设置,更利于超声清洗的进行。利用上述装置清洗失活脱硝催化剂的方法,包括以下步骤:(1)预处理:将失活脱硝催化剂进行表面除灰,并确定残余积灰较多的区域;(2)定向低频粗洗:将经过步骤(1)预处理之后的失活脱硝催化剂放入清洗槽内,加入清洗液,然后将第二超声系统浸入清洗液中,位于失活脱硝催化剂上方,开启失活脱硝催化剂残余积灰较多的区域对应的第一超声系统和第二超声系统的超声振板,进行粗洗;(3)高频精洗:步骤(2)粗洗完成后开启所有超声振板,同时切换超声振板频率,进行高频精洗,精洗完成后关闭超声系统,将催化剂取出,烘干。优选的,步骤(1)中,所述确定残余积灰较多的区域是指通过肉眼观察即可实现。优选的,步骤(2)中,所述清洗液为去离子水、酸性清洗液或碱性清洗液。进一步的,所述酸性清洗液为H2SO4、HCl、HNO3、HF、草酸、甲酸、乙酸、柠檬酸、酒石酸、氨基磺酸、甲磺酸、抗坏血酸中的一种或几种的水溶液。其中,溶质浓度为0.1-5wt%。进一步的,所述碱性清洗液为NaOH、KOH中的一种或两种的水溶液,还包含烷基酚聚氧乙烯醚作为表面活性剂。其中,碱性溶质和烷基酚聚氧乙烯醚的浓度分别为0.5-5wt%和0.01-0.5wt%。优选的,步骤(2)中,所述超声振板的频率为15-50kHz,粗洗时间15-45min,清洗液温度25-50℃;步骤(3)中,高频精洗时,超声振板的频率为50-120kHz,精洗时间15-60min,清洗液温度50-90℃。优选的,步骤(3)中所述高频精洗用如下方式替换:步骤(2)粗洗完成后,依然保持只打开与步骤(2)中相同的超声振板,但切换频率为50-120kHz,继续进行定向高频精洗,精洗时间15-60min,清洗液温度50-90℃,精洗完成后关闭超声系统,将催化剂取出,烘干。优选的,针对蜂窝式脱硝催化剂,步骤(2)粗洗过程中,超声振板的频率为30-50kHz,粗洗时间30-45min,清洗液温度25-50℃;步骤(3)精洗过程中,超声振板的频率为80-120kHz,精洗时间40-60min,清洗液温度50-90℃。进一步优选的,针对蜂窝式脱硝催化剂,步骤(2)粗洗过程中,超声振板的频率为40kHz,粗洗时间35min,清洗液温度35℃;步骤(3)精洗过程中,超声振板的频率为120kHz,精洗时间60min,清洗液温度60℃。优选的,针对板式脱硝催化剂,步骤(2)粗洗过程中,超声振板的频率为20-40kHz,粗洗时间20-30min,清洗液温度25-50℃;步骤(3)精洗过程中,超声振板的频率为60-100kHz,精洗时间30-60min,清洗液温度50-90℃。进一步优选的,针对板式脱硝催化剂,步骤(2)粗洗过程中,超声振板的频率为30kHz,粗洗时间25min,清洗液温度50℃;步骤(3)精洗过程中,超声振板的频率为80kHz,精洗时间45min,清洗液温度60℃。优选的,针对波纹板式脱硝催化剂,步骤(2)粗洗过程中,超声振板的频率为15-30kHz,粗洗时间15-25min,清洗液温度25-50℃;步骤(3)精洗过程中,超声振板的频率为50-80kHz,精洗时间15-40min,清洗液温度50-90℃。进一步优选的,针对波纹板式脱硝催化剂,步骤(2)粗洗过程中,超声振板的频率为20kHz,粗洗时间20min,清洗液温度30℃;步骤(3)精洗过程中,超声振板的频率为80kHz,精洗时间30min,清洗液温度50℃。本发明方法包含低频定向清洗和高频精洗,并且根据催化剂的形式、表面状况来确定具体超声清洗参数,可以有效去除失活脱硝催化剂表面和孔道中的积灰和有毒物质,同时减少催化剂活性组分流失和物理性能下降。所述脱硝催化剂为钒钛系催化剂。所述清洗槽、超声系统、连接管道均为防腐材质。有益效果:相比较于现有技术,本发明的超声清洗装置,包含两套超声系统,分别位于清洗槽的底部和顶部;底部的超声系统固定于清洗槽底部,顶部的超声系统为活动连接的投入式,可以浸入清洗液中,位于脱硝催化剂模块上端,两套超声系统配合使用,清洗效果较好,整体清洗过程能耗低。本发明的超声清洗方法,分为低频定向粗洗和高频精洗两个阶段;首先低频定向粗洗针对催化剂模块中残余积灰较多的区域,可以在保证清洗效果的同时,降低超声对整体催化剂物理性质的负面影响,同时减少催化剂活性组分的流失量;高频精洗用于除去催化剂孔道中积灰和有毒物质,提升清洗效果。本发明的超声清洗方法,是根据催化剂的形式制定清洗工艺,可以在高效清洗的同时,进一步降低超声对脱硝催化剂物理性质的负面影响。附图说明图1是失活脱硝催化剂的超声清洗装置结构示意图;图2是图1的仰视图;图3是图1的俯视图。其中:1清洗槽;2第一超声系统;3第二超声系统;4连接件;5超声振板。具体实施方式以下实施例是对本发明的进一步说明。酸性清洗液为H2SO4与草酸的混合水溶液,其中,H2SO4与草酸的浓度分别为0.5wt%和0.1wt%。碱性清洗液为NaOH和壬基酚聚氧乙烯醚混合水溶液,其中,NaOH和壬基酚聚氧乙烯醚的浓度分别为1.2wt%和0.2wt%。实施例1失活脱硝催化剂的超声清洗装置。如图1所示的一种失活脱硝催化剂的超声清洗装置,包括清洗槽1、第一超声系统2和第二超声系统3,第一超声系统2固定在清洗槽1的底部,第二超声系统3通过连接件4活动连接在清洗槽1的上部,连接件4具体为履带;如图2所示,第一超声系统2包含12块超声振板5,分别为T1-T12,分两排对称有序排列;如图3所示,第二超声系统3包含8块超声振板5,分别为A1-A8,分两排对称有序排列;所有超声振板5的频率均可以独立控制,单独投用。实施例2利用实施例1的清洗装置清洗失活脱硝催化剂的方法。失活脱硝催化剂选用国内某燃煤电厂运行24000h后的V2O5-WO3/TiO2蜂窝式脱硝催化剂。包括以下步骤:将失活脱硝催化剂模块除灰后,检查除灰后催化剂的表面状况,确定残余积灰相对较多的区域,分别为T2、T11和A2、A8;将催化剂置于清洗槽中,加入酸性清洗液,打开超声振板T2、T11和A2、A8,进行定向粗洗,超声振板的频率为40kHz,粗洗时间35min,清洗液温度35℃;粗洗完成后,投用所有超声振板,切换频率为120kHz,进行高频精洗,精洗时间60min,清洗液温度60℃。然后关闭超声系统,将催化剂取出,80℃烘干。对比例1失活脱硝催化剂、催化剂清洗装置和酸性清洗液同实施例2。不同之处在于:将失活脱硝催化剂模块除灰后,置于清洗槽中,加入酸性清洗液,浸泡35min,清洗液温度35℃;然后将清洗液温度升至60℃,继续浸泡60min;完成后,将催化剂取出,80℃烘干。对比例2失活脱硝催化剂、催化剂清洗装置和酸性清洗液同实施例2。具体步骤包括:将失活脱硝催化剂模块除灰后,置于清洗槽中,加入酸性清洗液,打开底部和顶部超声系统,进行低频粗洗,超声振板的频率为40kHz,粗洗时间35min,清洗液温度35℃;然后将清洗液温度升至60℃,继续清洗60min;完成后,关闭超声系统,将催化剂取出,80℃烘干。相比较于实施例2,该对比例使用同一的频率进行清洗,并且没有对催化剂残余积灰较多的区域进行定向粗洗。对比例3失活脱硝催化剂、催化剂清洗装置和酸性清洗液同实施例2。具体步骤包括:将失活脱硝催化剂模块除灰后,置于清洗槽中,加入酸性清洗液,打开底部和顶部超声系统,进行低频粗洗,超声振板的频率为40kHz,粗洗时间35min,清洗液温度35℃;然后将清洗液温度升至60℃,切换超声振板频率为120kHz,进行高频精洗60min;然后关闭超声系统,将催化剂取出,80℃烘干。相比较于实施例2,该对比例没有对催化剂残余积灰较多的区域进行定向粗洗。对比例4该对比例除了定向粗洗和精洗的参数外,均同实施例2。定向粗洗和精洗的参数为:进行定向粗洗时,超声振板的频率为30kHz,粗洗时间45min,清洗液温度50℃;粗洗完成后,投用所有超声振板,切换频率为80kHz,精洗高频精洗,精洗时间40min,清洗液温度50℃。然后关闭超声系统,将催化剂取出,80℃烘干。对比例5该对比例除了定向粗洗和精洗的参数外,均同实施例2。定向粗洗和精洗的参数为:进行定向粗洗时,超声振板的频率为50kHz,粗洗时间30min,清洗液温度25℃;粗洗完成后,投用所有超声振板,切换频率为100kHz,精洗高频精洗,精洗时间50min,清洗液温度90℃。然后关闭超声系统,将催化剂取出,80℃烘干。对实施例2、对比例1到5清洗后的催化剂进行XRF分析和氮吸附脱附分析,结果如表1和表2所示。表1不同催化剂的XRF分析数据表2不同催化剂的物理性质数据此外,采用磨损测试设备测定对比例1、对比例2、对比例3、实施例2、对比例4和对比例5中清洗后催化剂的磨损值,结果分别为清洗前的失活脱硝催化剂的97.1%、78.1%、80.3%、92.8%、88.7%和92.9%。由对比例1和实施例2的分析数据可知,单纯的酸液浸泡也可以达到一定的除去失活催化剂表面有毒元素的作用,但是总体清洗效果不佳。由对比例1、对比例2、对比例3和实施例2的分析数据可知,清洗过程中采用超声处理可以有效增强清洗效果。然而,也会同时带来催化剂的磨损强度下降,活性组分V2O5流失的问题。由对比例2和对比例3的分析数据可知,采用低频粗洗和高频精洗结合的超声清洗方式,清洗效果较好,对于催化剂的磨损强度和活性组分V2O5的影响也较小。由对比例3和实施例2的分析数据可知,采用低频定向粗细和高频精洗结合的超声清洗方式,可以在保证催化剂清洗效果的同时,对催化剂的磨损强度的影响更小,催化剂活性组分V2O5流失量也更低。由实施例2、对比例4和对比例5的分析数据可知,综合考虑催化剂的清洗效果、清洗后催化剂的物理性能以及活性组分V2O5的流失程度,实施例2中的超声清洗参数为优选方案。实施例3利用实施例1的清洗装置清洗失活脱硝催化剂的方法。失活脱硝催化剂选用国内某燃煤电厂运行23000h后的V2O5-MoO3/TiO2平板式脱硝催化剂。将失活脱硝催化剂模块除灰后,检查除灰后催化剂的表面状况,确定残余积灰相对较多的区域,分别为T3、T9和A2、A6,将催化剂置于清洗槽中,加入碱性清洗液,打开超声振板T3、T9和A2、A6,进行定向粗洗,超声振板的频率为30kHz,粗洗时间25min,清洗液温度50℃;粗洗完成后,投用所有超声振板,切换超声振板频率为80kHz,进行高频精洗,精洗时间45min,清洗液温度60℃。然后关闭超声系统,将催化剂取出,80℃烘干。对比例6该对比例除了定向粗洗和精洗的参数外,均同实施例3。定向粗洗和精洗的参数为:进行定向粗洗时,超声振板的频率为20kHz,粗洗时间20min,清洗液温度25℃;粗洗完成后,投用所有超声振板,切换超声振板频率为100kHz,进行高频精洗,精洗时间30min,清洗液温度50℃。然后关闭超声系统,将催化剂取出,80℃烘干。对比例7该对比例除了定向粗洗和精洗的参数外,均同实施例3。定向粗洗和精洗的参数为:进行定向粗洗时,超声振板的频率为40kHz,粗洗时间30min,清洗液温度40℃;粗洗完成后,投用所有超声振板,切换超声振板频率为60kHz,进行高频精洗,精洗时间60min,清洗液温度90℃。然后关闭超声系统,将催化剂取出,80℃烘干。实施例4利用实施例1的清洗装置清洗失活脱硝催化剂的方法。失活脱硝催化剂选用国内某燃煤电厂运行23000h后的V2O5-MoO3/TiO2平板式脱硝催化剂。将失活脱硝催化剂模块除灰后,检查除灰后催化剂的表面状况,确定残余积灰相对较多的区域,分别为T3、T9和A2、A6,将催化剂置于清洗槽中,加入碱性清洗液,打开超声振板T3、T9和A2、A6,进行定向粗洗,超声振板的频率为30kHz,粗洗时间25min,清洗液温度50℃;粗洗完成后,依然保持只打开超声振板T3、T9和A2、A6,切换超声振板频率为80kHz,进行定向高频精洗,精洗时间45min,清洗液温度60℃。然后关闭超声系统,将催化剂取出,80℃烘干。对实施例3、对比例6、对比例7和实施例4清洗后的催化剂进行XRF分析和氮吸附脱附分析,结果如表3和表4所示。表3不同催化剂的XRF分析数据单位失活催化剂实施例3对比例6对比例7实施例4V2O5%0.950.780.790.800.84SiO2%6.754.435.014.834.44SO3%1.920.250.650.470.25As%1.560.110.630.570.11表4不同催化剂的孔结构分析数据单位失活催化剂实施例3对比例6对比例7实施例4比表面积m2/g5475646674孔容cm3/g0.250.380.280.290.37此外,采用磨损测试设备测得实施例3、对比例6、对比例7和实施例4中清洗后催化剂的磨损值分别为清洗前的失活脱硝催化剂的93.3%、88.2%、90.2%和94.2%。由实施例3、对比例6、对比例7的分析数据可知,综合考虑催化剂的清洗效果、清洗后催化剂的物理性能以及活性组分V2O5的流失程度,实施例3中的超声清洗参数为优选方案。由实施例3和实施例4的分析数据可知,实施例4中所采用的定向粗洗加定向精洗的清洗工艺,可以在保证清洗效果的同时,进一步减少催化剂活性组分V2O5的流失量,以及催化剂的磨损强度的下降程度。实施例5利用实施例1的清洗装置清洗失活脱硝催化剂的方法。失活脱硝催化剂选用国内某燃煤电厂运行22000h后的V2O5-WO3/TiO2波纹板式脱硝催化剂。将失活脱硝催化剂模块除灰后,检查除灰后催化剂的表面状况,确定残余积灰相对较多的区域,分别为T6、T12和A4、A8。将催化剂置于清洗槽中,加入碱性清洗液,打开超声振板T6、T12和A4、A8,进行定向粗洗,超声振板频率为20kHz,粗洗时间20min,清洗液温度30℃;粗洗完成后,投用所有超声振板,切换振板频率为80kHz,进行高频精洗,精洗时间30min,清洗液温度50℃。然后关闭超声系统,将催化剂取出,80℃烘干。对比例8该对比例除了定向粗洗和精洗的参数外,均同实施例5。定向粗洗和精洗的参数为:进行定向粗洗时,超声振板频率为15kHz,粗洗时间25min,清洗液温度50℃;粗洗完成后,投用所有超声振板,切换振板频率为50kHz,进行高频精洗,精洗时间40min,清洗液温度60℃。然后关闭超声系统,将催化剂取出,80℃烘干。对比例9该对比例除了定向粗洗和精洗的参数外,均同实施例5。定向粗洗和精洗的参数为:进行定向粗洗时,超声振板频率为30kHz,粗洗时间15min,清洗液温度45℃;粗洗完成后,投用所有超声振板,切换振板频率为60kHz,进行高频精洗,精洗时间15min,清洗液温度90℃。然后关闭超声系统,将催化剂取出,80℃烘干。实施例6利用实施例1的清洗装置清洗失活脱硝催化剂的方法。失活脱硝催化剂选用国内某燃煤电厂运行22000h后的V2O5-WO3/TiO2波纹板式脱硝催化剂。将失活脱硝催化剂模块除灰后,检查除灰后催化剂的表面状况,确定残余积灰相对较多的区域,分别为T6、T12和A4、A8。将催化剂置于清洗槽中,加入碱性清洗液,打开超声振板T6、T12和A4、A8,进行定向粗洗,超声振板频率为20kHz,粗洗时间20min,清洗液温度30℃;粗洗完成后,依然保持只打开超声振板T6、T12和A4、A8,切换超声振板频率为80kHz,进行定向高频精洗,精洗时间30min,清洗液温度50℃。然后关闭超声系统,将催化剂取出,80℃烘干。对实施例5、对比例8、对比例9和实施例6清洗后的催化剂进行XRF分析和氮吸附脱附分析,结果如表5和表6所示。表5不同催化剂的XRF分析数据单位失活催化剂实施例5对比例8对比例9实施例6V2O5%0.350.270.280.280.30Al2O3%1.790.210.460.450.21MgO%0.770.080.180.190.08CaO%0.890.280.570.550.29Fe2O3%1.040.090.140.140.10Na2O%0.520.010.010.010.01K2O%0.230.010.010.010.01表6不同催化剂的孔结构分析数据单位失活催化剂实施例5对比例8对比例9实施例6比表面积m2/g4762585761孔容cm3/g0.160.260.210.200.25此外,采用磨损测试设备测得实施例5、对比例8、对比例9和实施例6中清洗后催化剂的磨损值分别为清洗前的失活脱硝催化剂的93.4%、82.2%、91.1%和95.0%。由实施例5、对比例8、对比例9的分析数据可知,综合考虑催化剂的清洗效果、清洗后催化剂的物理性能以及活性组分V2O5的流失程度,实施例5中的超声清洗参数为优选方案。由实施例5和实施例6的分析数据可知,实施例6中所采用的定向粗洗加定向精洗的清洗工艺,可以在保证清洗效果的同时,进一步减少催化剂活性组分V2O5的流失量,以及催化剂的磨损强度的下降程度。当前第1页1 2 3