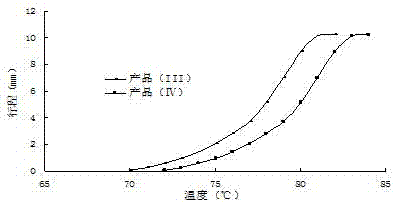
一种以F-T合成产物生产节温器用蜡介质的方法技术领域本发明属于特种蜡生产技术领域,特别是涉及一种以F-T合成产物生产节温器用蜡介质的方法。
背景技术:蜡质温控阀以蜡类物质作为感应温度变化的介质,当环境温度变化时,蜡类物质的体积产生变化,进而控制阀门开度,从而调节物流流量,达到调整、控制温度的目的。蜡质温控阀所用蜡类物质称作蜡介质。节温器又称调温器,其作用是根据冷却水温度的高低自动调节进入散热器的水量,改变水的循环范围,以调节冷却系统的散热能力,保证发动机在合适的温度范围内工作。常用的节温器是蜡式节温器,属蜡质温控阀。蜡式节温器一般采用套管式结构,控温范围10~12℃,根据发动机的最佳工作温度区域,又按标称温度分成70、72、76、80、82等规格,标称温度为70℃的节温器的控温区间为70℃~80℃。对节温器行程要求为:常温~标称温度+2℃的行程小于1mm,控温范围内(标称温度~标称温度+10℃或标称温度+12℃)行程大于8mm。蜡式节温器是依靠其所用的蜡介质随温度变化产生体积变化作为输出动作的原动力。当冷却水温度低于规定值时,节温器感温体内的蜡介质呈固态,节温器阀在弹簧的作用下关闭发动机与散热器之间的通道,冷却水经水泵返回发动机,进行发动机内小循环;当冷却水温度达到规定值后,蜡介质产生固→液相变,体积膨胀,并压迫橡胶管使其收缩。在橡胶管收缩的同时对推杆作用以向上的推力,推杆对阀门有向下的反推力使阀门开启。这时冷却水经由散热器和节温器阀,再经水泵流回发动机,进行大循环。这样蜡式节温器就能根据冷却水温度的变化自动调节进入散热器的水量,从而保证发动机在合适的温度范围内工作。从蜡式节温器的工作原理可以看出,蜡介质是其接收环境温度变化进而输出相应动作的主体,因而蜡介质的性质是蜡式节温器性能的决定因素。一般蜡介质处于液体状态时,其膨胀系数约为6.7×10-4,固态时的膨胀系数比液态时稍大,而在固←→液相变范围内膨胀系数远大于此值。对节温器用蜡介质的要求就是相变过程的体积膨胀应与节温器的控温范围一致,反映在推杆行程上就是要在节温器的控温范围内大于8mm,而在控温范围以外行程要很小。石油蜡是原油经过炼制加工后从含蜡馏分油中制得的各类蜡产品的总称,包括液体石蜡、石蜡和微晶蜡。商品石油蜡是多种碳数的正构烷烃、异构烷烃、环烷烃等的烃类混合物,其碳数分布较宽,正构烷烃含量较低。商品石油蜡直接用作节温器的蜡介质时,会导致大循环开启过早(常温~标称温度+2℃范围内推杆的行程大于1mm),使发动机预热时间延长;同时由于推杆行程较小(标称温度~标称温度+10℃或标称温度+12℃的行程小于8mm),会导致发动机正常工作时大循环的水量不足,引起发动机过热。所以商品石油蜡必须经分离提纯才能用作节温器的蜡介质。这些提纯过程工艺复杂,不仅生产成本高,而且对于节温器用蜡介质来说仍存在一定数量的非适宜组分,如油类等,这些非适宜组分的存在影响了使用性能。费-托(F-T)合成技术是1923年发明的,1936年在德国实现工业化。F-T合成技术主要包括高温合成技术和低温合成技术。二十世纪九十年代以来,F-T合成工艺及催化剂都取得了突破性的进展,F-T合成产品日益丰富,为生产节温器用蜡介质提供了新的原料。在石油蜡生产工艺方面,常用的分离加工手段主要有蒸馏、溶剂脱油、发汗脱油等。蒸馏是利用不同烃类的沸点不同达到分离提纯的目的,减小蒸馏的沸程可以有效降低产物碳分布的宽度,但对提高正构烷烃含量影响不大,并且由于蒸馏过程需要将石油蜡加热到沸点以上,消耗大量的能量。同时熔点在70℃以上的烃类的沸点在500℃(常压)以上,采用蒸馏进行分离时效率大大下降。溶剂脱油方法是利用正构烷烃与异构烷烃在溶剂中的溶解度不同达到分离提纯的目的,可以有效提高产物中的正构烷烃含量,但对碳分布宽窄的影响不大,同时溶剂脱油生产设备投资大;生产过程中需要大量使用溶剂,回收溶剂需要消耗大量的能量;溶剂中含有苯系物,会对环境造成影响;溶剂易燃,容易造成生产事故。发汗脱油方法是利用蜡中各种烃类组分熔点不同的性质进行分离提纯的。石油蜡中各种组分的分子量和结构的不同都会使其熔点不同。同为正构烷烃时,分子量较大的正构烷烃的熔点较高,而分子量较小的正构烷烃的熔点较低;分子量相同时,异构烷烃和环烷烃的熔点要低于正构烷烃,且异构程度越高熔点就越低。所以发汗脱油即能降低产物碳分布的宽度又能提高正构烷烃含量。与蒸馏分离方法相比,由于各种烃类的熔点温度远低于沸点温度,所以发汗分离过程的能耗远低于蒸馏分离,同时产物的熔点也可以提高;与溶剂分离方法相比,发汗分离过程不使用溶剂,所以发汗分离过程对环境无影响。而且发汗法即能降低产物碳分布的宽度又能提高正构烷烃含量,所以对生产节温器用蜡介质而言,发汗脱油分离过程在生产过程和产品性能两方面都有优势。普通的发汗脱油过程主要包括以下步骤:(1)准备工作:垫水,用水充满发汗装置皿板下部空间;(2)装料:原料加热至熔点以上呈液态时装入发汗装置;(3)降温结晶:将原料以不大于4℃/h的降温速率缓慢冷却到其熔点以下10~20℃。在冷却过程中,熔点最高的组分先以粗的纤维状晶体形态结晶出来,随着蜡层温度继续降低,其它组分按熔点由高到低的顺序依次结晶形成固体;(4)升温发汗:当蜡层温度达到预设的降温终止温度之后,放掉垫水;再将原料缓慢地加热到预设的发汗终止温度。在升温发汗过程中,各种组分按熔点由低到高的顺序先后熔化成液态并流出(蜡下),最后得到的蜡层剩余物(蜡上)就是高熔点、低含油的蜡;(5)粗产品收集:升温发汗过程结束后继续升高温度,以熔化取出蜡上,即为粗产品;(6)产品精制、成型、包装:精制过程通常采用白土精制:将粗产品熔化后升温至预定温度,加入白土并恒温搅拌至预定时间后过滤;再经成型、包装即为目的产品。普通发汗工艺可以生产熔点在40℃~60℃的皂蜡和低熔点石蜡,不适宜生产熔点在70℃以上的高熔点蜡产品。有试验表明,普通发汗脱油工艺生产熔点在70℃以上的高熔点蜡产品时,发汗后期蜡上的碳分布宽度和正构烷烃含量与收率无关,即蜡上的碳分布宽度不随收率的下降而下降,正构烷烃含量也不随收率的下降而提高,所以普通发汗分离工艺不适宜生产熔点在70℃以上的节温器用蜡介质。目前仅有部分厂家使用发汗脱油工艺生产皂蜡和低熔点的石蜡等普通产品。多年来,发汗脱油工艺在生产设备和工艺方面得到了一些发展,如CN89214332(立式方形多段隔板发汗罐)、CN98233254.8(石蜡发汗罐)、CN201320127680.4(管式石蜡脱油装置)等,在发汗脱油生产设备上作了改进;CN91206202(一种高效石蜡发汗罐)在发汗脱油工艺上作了改进。但这些改进仍不能生产熔点在70℃以上的节温器用蜡介质。现有技术中的蜡介质制备手段,有采用溶剂法的,如:DD241,829、DD241,830等专利介绍以溶剂萃取的方法制备80~90℃范围内控温的蜡介质。DD247,572、SU1,084,289、RU2,009,171、US5,223,122等专利介绍的制备方式,均以溶剂萃取为主。这些专利介绍的制备方式对环境有污染。现有技术中的蜡介质制备手段,也有采用(多段)发汗或(与蒸馏方法)组合发汗的,如:CN02109670.8(淋浴自动调温阀用蜡质感温介质)等专利的目的产品的熔点都在50℃以下;CN201110353409.8(一种控温阀用蜡质感温介质的制备方法)等专利的目的产品熔点也在50℃以下,且控温范围宽,不适合用作节温器用蜡介质。发汗工艺具有投资少、生产过程简单、操作费用低、处理量适中、产品质量指标易于调整等优点,更重要的是,发汗脱油工艺是目前已知用于工业规模生产石蜡产品的唯一无溶剂脱油方法,在提倡绿色低碳、环保节能的今天,采用发汗脱油工艺生产节温器用蜡介质的需求更加迫切。
技术实现要素:针对现有技术的不足,本发明提供一种以F-T合成产物生产节温器用蜡介质的方法,包括加氢转化、蒸馏、发汗三部分。具体地说是以适宜的F-T合成产物为原料,在催化剂作用下进行加氢转化,将其中的烯烃和含氧化合物转化为节温器用蜡介质的适宜组分;加氢产物经蒸馏制取适当馏程的组分;再采用发汗装置,在普通发汗方法的基础上,原料加热熔化后优选在压力条件下掺入低沸点液体;在冷却降温过程中的适当温度增加高温恒温阶段,并增加在冷却过程结束后的低温恒温阶段和升温发汗过程的恒温阶段;并在发汗过程中利用气流通过蜡层携带出液态组分以强制分离固态组分与液态组分,增强了分离效果并加快了分离速度。降温的低温恒温过程和升温及恒温的发汗过程中回收低沸点液体。本发明方法以F-T合成产物为原料使用发汗这种无溶剂分离方法生产出节温器用蜡介质。本发明的一种以F-T合成产物生产节温器用蜡介质的方法,包括以下内容:(一)加氢转化:F-T合成产物在催化剂作用下进行加氢转化,将其中的烯烃和含氧化合物转化为正构烷烃;(二)蒸馏:将上述经加氢转化所得产物在蒸馏装置中制取初馏点为450~500℃、终馏点为510~540℃的馏分;(三)发汗,包括以下过程:(1)在发汗装置中垫水;(2)以过程(二)蒸馏制取的馏分为原料,加热熔化后装入发汗装置;(3)以1.0℃/h~3.0℃/h的速率将蜡层降温至适当温度,高温恒温一段时间;再以0.5℃/h~2.5℃/h的速率降温至原料熔点以下5℃~20℃的预定温度,并低温恒温一段时间;(4)排出发汗装置中的垫水;然后以0.5℃/h~2.5℃/h的速率升温,蜡层达到预定温度后恒温一段时间,然后停止发汗;其中在发汗过程中强制气流通过蜡层;(5)产品精制和成型、包装后即得到节温器用蜡介质产品。本发明的方法中,所述的F-T合成产物,其正构烷烃重量含量要求大于等于85%,优选正构烷烃含量大于等于95%的F-T合成产物作为原料。本发明的方法中,其中过程(三)的步骤(2)中,通常将发汗原料加热至其熔点以上3℃~8℃,以使其尽快全部熔化。本发明的方法中,过程(一)所述的加氢转化过程采用本领域的常规技术。加氢转化操作条件为:反应压力3~10MPa、反应温度150~300℃、液时体积空速0.2~2.0h-1和氢液体积比100~1000:1,氢液体积比优选为300~800:1。加氢转化催化剂可以为Ni/Al2O3、W-Ni/Al2O3、Mo-Ni/Al2O3或W-Mo-Ni/Al2O3催化剂等。催化剂中活性金属组分以氧化物计的重量含量为20%~70%。加氢转化催化剂可以按本领域常规方法制备。催化剂使用时可以根据需要按本领域常规方法将活性金属氧化物还原或硫化,以提高催化剂活性。本发明的方法中,过程(二)中所述的蒸馏装置可以是具有接近2块理论塔板的减压蒸馏装置。本发明的方法中,优选在过程(三)的步骤(2)中原料(即过程(二)蒸馏制取的馏分)加热熔化后在压力条件下掺入低沸点液体。所述的压力(表压)为0.5~20.0个大气压,优选为1.0~10.0个大气压。所述的低沸点液体为有机物,其与原料有较好的互溶性,且在常压下的沸点低于冷却降温的预定温度,而在高压下的沸点高于加料过程的最高温度。所述的低沸点液体可以是烷烃、烯烃、炔烃、二烯烃、醇、醛、醚、酯、卤代烃等沸点适宜的有机物中的一种或几种,优选为烷烃、醇、酯等与原料有较好的互溶性、无特殊气味且无毒副作用的物质。所述的低沸点液体的加入量占原料蜡膏的0.1%~5.0%(重量),优选的比例为0.3%~2.0%。在降温的低温恒温过程和升温及恒温的发汗过程中可以回收低沸点液体。本发明的方法中,所述的发汗装置一般为发汗皿,并在蜡层以上增加可拆卸的密封系统及加压装置,以保证在加料和冷却过程中保持低沸点液体处于液体状态,所述的压力(表压)为0.5~20.0个大气压,优选为1.0~10.0个大气压。本发明的方法中,所述的发汗皿在蜡层以上增加加压装置和/或在蜡层以下增加真空装置。所述的强制气流通过蜡层采用在蜡层上方增加压力(气压)和/或在蜡层下方降低压力(气压),使蜡层上、下方形成压力差实现。所述的压力差一般为0.1~5.0个大气压,优选为0.2~1.5个大气压,以强制气流通过蜡层。本发明的方法中,步骤(3)中所述的降温过程在高温恒温段之前的降温速率优选1.5℃/h~2.5℃/h。本发明的方法中,步骤(3)中所述的降温过程的高温恒温段的适当温度为原料(过程(二)所得馏分)熔点-1.0℃~熔点+2.0℃,优选为原料熔点~熔点+1.0℃。冷却降温过程的高温恒温段的时间为0~4.0小时,优选为0.1~4.0小时,最优选为1.0~4.0小时。本发明的方法中,步骤(3)中所述的降温过程在高温恒温段之后的降温速率优选1.0℃/h~2.0℃/h。本发明的方法中,步骤(3)所述的预定温度(即降温终止温度)优选为原料熔点以下8℃~15℃。本发明的方法中,步骤(3)所述的冷却降温至预定温度后,增加低温恒温阶段以使固体结晶更充分,同时逐渐减低压力至常压。冷却降温过程的低温恒温阶段的时间为0~3.0小时,优选为0.1~3.0小时,最优选为1.0~3.0小时。本发明的方法中,步骤(4)中所述升温的速率优选1.0℃/h~2.0℃/h。所述升温的预定温度(即终止温度)为目的产品标称温度~标称温度+10℃。本发明的方法中,步骤(4)中升温发汗至制取产品的预定温度后,增加恒温阶段以使固态组分与液态组分分离更充分,恒温阶段的时间为0~5.0小时,优选为0.1~5.0小时,最优选为1.0~5.0小时。本发明的方法中,所述蜡层的升温速度和降温速度,可以通过空气浴、水浴、油浴或者其他可行的方式进行控制,优选采用水浴或油浴进行控制。采用水浴或油浴方式控制蜡层升温速率和降温速率时,可在发汗皿外增加夹套,夹套与可移动盘管及循环系统相连,循环系统具有程序降温/加热功能,以水或导热油等物质作为循环介质;增加盘管可使蜡层升/降温过程更快、蜡层温度更均匀。本发明的方法中,所述的强制气流通过蜡层可以在发汗过程任意阶段实施,优选在升温初期实施。本发明的方法中,所述的强制气流通过蜡层是采用在蜡层上方增加压力(气压)实现的,如在蜡层上方施加的压力为0.2~1.5个大气压(表压),而蜡层下方保持为常压。本发明的方法中,所述的强制气流通过蜡层是采用在蜡层下方降低压力(气压)实现的,如在蜡层上方保持常压,而在蜡层下方维持-0.2~-0.8个大气压(表压)的压力。本发明的方法中,所述的发汗装置连接回收系统,以回收低沸点液体。回收系统可以采用液体吸收或冷冻系统等多种可行的方式,优选为液体吸收系统。商品石油蜡直接用作节温器用蜡介质时,会导致大循环开启过早且控温范围内推杆行程较小,这是由商品石油蜡的化学组成引起的,即商品石油蜡的碳数分布较宽且含有较多的异构烷烃和环烷烃。由于商品石油蜡碳数分布较宽,即含有较多的低分子量的成分,低分子量成分的熔点低于节温器的控温范围,这些成分会提前熔化而产生体积膨胀,导致大循环开启过早;同时由于商品石油蜡含有较多的异构烷烃和环烷烃(一般异构烷烃和环烷烃的膨胀系数小于正构烷烃),这就会使在节温器控温范围内推杆的行程较小,导致大循环的水量不足。低温F-T合成产物的重组分主要为正构烷烃,但是还含有一定量的烯烃和含氧化合物,而且碳数分布比商品石油蜡还要宽很多,该产物本身不适宜直接作为节温器用蜡介质。所以商品石油蜡和F-T合成产物都必须经分离提纯才能用作节温器用蜡介质。普通发汗工艺是利用蜡和油熔点不同的性质进行分离生产蜡产品的,但是对于熔点在70℃左右的蜡产品,由于原料化学组成复杂,导致结晶时晶体结构更加细小致密,对液态组分的排出形成巨大的滤流阻力,这就造成仅靠重力自然分离的普通发汗过程中固态组分与液态组分难以完全分离。因此普通发汗脱油工艺不能生产熔点在70℃以上的节温器用蜡介质产品。本发明为了生产高性能的节温器用蜡介质,通过对节温器用蜡介质使用性能与其化学组成的关系和F-T合成产物的组成的深入研究,针对低温F-T合成产物含有一定量的烯烃和含氧化合物,且碳数分布非常宽是造成低温F-T合成产物不能满足节温器用蜡介质产品技术要求的原因,通过选择适当的催化剂和反应条件,将低温F-T合成产物中的烯烃和含氧化合物等非适宜组分转化为正构烷烃;并通过减压蒸馏对目的组分富集;再通过发汗降低碳数分布宽度以使产物的性能满足节温器用蜡介质的技术要求。本发明为了使发汗这种无溶剂分离方法可以生产熔点在70℃以上的节温器用蜡介质,针对普通发汗过程中固态组分与液态组分难以分离原因,通过在发汗过程中采用强制气流通过蜡层携带出液态组分的方法,同时还优选原料加热熔化后在压力条件下掺入低沸点液体,并在冷却降温过程中增加高温恒温阶段、降温过程的低温恒温阶段和升温发汗至预设温度后的恒温阶段等过程。这些措施有效地降低了产物碳分布的宽度并提高正构烷烃含量,使产物的性能能够满足节温器用蜡介质的技术要求。针对普通发汗过程的研究表明,在发汗过程中,液态组分是顺着结晶部分逐渐排出的,类似于液体在毛细管中流动的情况。由于熔点在70℃以上的蜡细小致密的结晶结构,会使对液态组分形成的滤流阻力急剧增大,这就导致仅靠重力自然分离过程的普通发汗过程不能生产熔点在70℃以上的节温器用蜡介质产品。在降温过程中增加高温恒温阶段可以使蜡的结晶更大,利于发汗过程中液态组分的排出。针对蜡结晶过程的研究表明,其化学组成是决定结晶形态的最主要因素,同时冷却过程的条件也会影响结晶形态,尤其是在熔点附近的温度下的冷却条件对结晶形态的影响最明显。熔点在70℃以上的蜡在冷却到熔点附近时,较大分子量的正构烷烃已形成结晶析出,这部分结晶体可以作为后续形成结晶的晶核,此时增加高温恒温阶段,可以使晶核能够充分增长,形成更大尺寸的晶体,这种更大尺寸的晶体虽然不如低熔点石蜡的结晶那样粗大,但这种增大的晶体结构对发汗阶段排出液态组分也是十分有利的。原料加热熔化后在压力条件下掺入低沸点液体,同时在发汗过程中强制气流通过蜡层也有利于发汗过程中液态组分的排出。原料加热熔化后掺入的低沸点液体,在压力条件下的沸点高于此时原料的温度而呈液体状态,并且由于与原料有较好的互溶性而均匀分散在原料中;保持压力下原料冷却至熔点以下8℃~15℃并恒温0.1~3.0h以使蜡层结晶更充分;同时在恒温过程中逐渐降低压力至常压,此时原料处于较软的固体状态,并且温度高于低沸点液体常压下的沸点(或泡点),低沸点液体随压力缓慢下降而逐渐汽化(或在其后的升温发汗过程中逐渐汽化),会在蜡层内形成均匀分散的微小气泡,这些微小气泡形成的空间在发汗过程中易于在蜡层中形成若干细小的通道,从而有利于发汗过程中液态组分的排出。同时在升温及恒温的发汗过程中利用气流通过蜡层携带出液态组分的方法强制液态组分与固态组分分离,增强了分离效果并加快了分离速度。再辅以冷却过程的低温恒温阶段使固体结晶更充分,以及发汗过程的恒温阶段使固态组分与液态组分分离更充分等方法,使得发汗工艺可以生产碳数分布范围窄且正构烷烃含量高的节温器用蜡介质。本发明的优点是:通过选择适当的催化剂和反应条件,将原料中的烯烃及含氧化合物通过加氢方法转化为节温器用蜡介质的适宜组分(正构烷烃),同时不产生其它杂质。然后通过蒸馏富集目的组分。在发汗过程中采用气流通过蜡层携带出液态组分的方法,增强了固态组分与液态组分的分离效果并加快了分离速度;而利用低沸点液体汽化在蜡层中形成均匀分散的微小气泡,更加有利于液态组分的快速排出。从而以F-T合成产物为原料采用发汗工艺可以生产碳数分布范围较窄且正构烷烃含量高的蜡产品,这些产品可以用作节温器用蜡介质。本发明方法装置投资低、生产过程无溶剂污染环境。附图说明图1是利用本发明实施例1制备的节温器用蜡介质(Ⅰ)、(Ⅱ)制备的节温器推杆的行程性能曲线。图2利用本发明实施例2制备的节温器用蜡介质(Ⅲ)、(Ⅳ)制备的节温器推杆的行程性能曲线。图中横坐标为温度,纵坐标为行程。具体实施方式本发明通过选用适宜的低温F-T合成产物为原料,经加氢转化、减压蒸馏、发汗等工艺过程生产熔点在70℃以上的节温器用蜡介质。具体为低温F-T合成产物在催化剂作用下进行加氢转化;加氢产物在蒸馏装置中制取适宜馏程的馏分;发汗皿上部连接可拆卸的密封装置并与加压缓冲罐和压缩机连接,和/或在发汗皿下部连接减压缓冲罐和真空泵;以水浴或油浴控制蜡层升、降温速度;发汗皿外增加夹套,夹套与可移动盘管和循环系统相连,循环系统具有程序降温/加热功能;以蒸馏制备的馏分为原料,加热熔化并优选在压力条件下掺入低沸点液体后装入发汗皿;保持压力下使蜡层温度降至原料熔点温度附近并高温恒温一段时间;继续降低蜡层温度至设定温度并低温恒温一段时间,恒温过程中逐渐降低原料蜡层以上的压力至常压;在发汗过程中,启动压缩机以在蜡层以上形成正压,和/或启动真空泵以在蜡层以下形成负压,用以强制气流通过蜡层;蜡层温度达到预设温度并恒温一段时间后停止发汗过程;蜡上经精制、成型、包装后即为节温器用蜡介质产品。以下通过实施例1-2具体说明本发明的以F-T合成产物生产节温器用蜡介质的方法。实施例1本实施例包括:(一)加氢转化、(二)蒸馏、(三)发汗三部分。(一)加氢转化以中国石油化工股份有限公司低温F-T合成实验装置的蜡油产物(正构烷烃重量含量为95.0%)为原料,在FHJ-2催化剂(一种Ni/Al2O3商业催化剂,抚顺石油化工研究院研制生产,以氧化物计活性金属镍含量为40%,催化剂在使用前进行常规还原处理)作用下在反应压力5.0MPa、反应温度200℃、体积空速1.0h-1和氢液体积比500:1的条件下进行加氢以转化其中的烯烃和含氧化合物,加氢产物中正构烷烃重量含量97.36%。(二)蒸馏将上述经加氢转化所得产物在接近2块理论塔板的减压蒸馏装置中,在13.3Pa~133Pa之间压力条件下,制备470℃~530℃的馏分。470℃~530℃馏分熔点71.1℃,收率8.03%(相对于蜡油原料),针入度(25℃)12(0.1mm)。(三)发汗本部分包括:(1)准备工作、(2)装料、(3)降温—高温恒温—降温—低温恒温结晶、(4)升温—恒温发汗、(5)发汗装置清理、(6)产品精制和成型、包装等过程。(1)准备工作将发汗皿夹套和可移动盘管与具有程序制冷/加热功能的循环系统连接,将盘管固定在发汗皿上;以水为介质;启动循环系统的加热功能,使循环水介质升温至75℃。发汗皿皿板下部垫水;发汗皿下部连接减压缓冲罐和真空泵。(2)装料以(二)部分蒸馏制备的470℃~530℃馏分为原料,加热至75℃熔化后加入发汗皿。安装发汗皿上部的密封系统并与加压缓冲罐和压缩机连接好;启动压缩机并保持加压缓冲罐内压力稳定在5.0~5.2个大气压(表压)。(3)降温—高温恒温—降温—低温恒温结晶启动循环系统的制冷功能,以2.0℃/h的降温速率使蜡层温度下降至72.0℃并恒温2.0小时进行高温恒温,以使结晶充分增长;再以1.5℃/h的降温速率使蜡层温度下降至60.0℃以使蜡层结晶形成固体,并恒温2.0小时进行低温恒温,以使结晶更充分。低温恒温阶段通过排空系统控制加压缓冲罐内压力逐渐降低至常压。关闭循环系统的制冷功能。(4)升温—恒温发汗排出发汗皿垫水。发汗皿出口连接蜡下储罐;启动压缩机并保持加压缓冲罐内压力稳定在1.0~1.2个大气压(表压),而在蜡层下方保持为常压;启动循环系统加热功能,以1.5℃/h的升温速率使蜡层温度升高到73.0℃并恒温4.0小时以使蜡层中的固态组分与液态组分充分分离。发汗皿出口换接粗产品储罐(Ⅰ),并保持缓冲罐内压力稳定在1.0~1.2个大气压(表压),发汗皿皿板下方保持常压;继续以1.0℃/h的升温速率使蜡层温度升高到75.0℃并恒温4.0小时以使蜡层中的固态组分与液态组分充分分离;停压缩机。发汗皿出口换接粗产品储罐(Ⅱ);开启真空泵并保持缓冲罐内压力稳定在-0.4~-0.6大气压(表压),蜡层上方保持常压;以1.0℃/h的升温速率使蜡层温度升高到77.0℃并恒温4.0小时以使蜡层中的固态组分与液态组分充分分离。停真空泵,终止发汗过程。(5)发汗装置清理发汗皿出口换接蜡上储罐;继续升高循环水的温度到90℃熔化取出蜡上,以清理发汗装置。(6)产品精制和成型、包装粗产品(Ⅰ)、(Ⅱ)分别经白土精制、成型和包装后即为节温器用蜡介质产品(Ⅰ)和产品(Ⅱ)。节温器用蜡介质产品(Ⅰ)性质:熔点74.4℃。节温器用蜡介质产品(Ⅰ)的收率为11.25%(相对于原料470℃~530℃馏分)。由节温器用蜡介质产品(Ⅰ)制备的节温器产品推杆的行程—温度关系如图1中曲线(Ⅰ)所示。从图1中曲线(Ⅰ)可以看出,节温器推杆行程在72℃时行程小于1mm,70℃~80℃间行程大于8mm,符合标称温度为70℃节温器的技术要求。节温器用蜡介质产品(Ⅱ)性质:熔点76.2℃。节温器用蜡介质产品(Ⅱ)的收率为12.28%(相对于原料470℃~530℃馏分)。由节温器用蜡介质产品(Ⅱ)制备的节温器产品推杆的行程—温度关系如图1中曲线(Ⅱ)所示。从图1中曲线(Ⅱ)可以看出,节温器推杆行程在74℃时行程小于1mm,72℃~82℃间行程大于8mm,符合标称温度为72℃节温器的技术要求。实施例2本实施例包括:(一)加氢转化、(二)蒸馏、(三)发汗三部分。(一)加氢转化同实施例1。(二)蒸馏同实施例1。(三)发汗本部分包括:(1)准备工作、(2)装料、(3)降温—高温恒温—降温—低温恒温结晶、(4)升温—恒温发汗、(5)发汗装置清理、(6)产品精制和成型、包装等过程。(1)准备工作将发汗皿夹套和可移动盘管与具有程序制冷/加热功能的循环系统连接,将盘管固定在发汗皿上;以水为介质;启动循环系统的加热功能,使循环水介质升温至75℃。发汗皿皿板下部垫水。安装发汗皿上部的密封系统并与加压缓冲罐和压缩机连接好,将加压缓冲罐排空系统和发汗皿下部排气口分别与回收系统连接好,以液体石蜡为吸收介质。在发汗皿下部连接减压缓冲罐和真空泵。(2)装料以实施例1中第(二)部分蒸馏制备的470℃~530℃馏分为原料,加热至75℃熔化后在5.0~5.2个大气压(表压)下掺入1.0%的甲酸乙酯,再加入发汗皿;保持加压缓冲罐内压力稳定在5.0~5.2个大气压(表压)。(3)降温—高温恒温—降温—低温恒温结晶启动循环系统的制冷功能,以2.0℃/h的降温速率使蜡层温度下降至72.0℃并恒温2.0小时进行高温恒温,以使结晶充分增长;再以1.5℃/h的降温速率使蜡层温度下降至60.0℃以使蜡层结晶形成固体,并恒温2.0小时进行低温恒温,以使结晶更充分。低温恒温阶段通过排空系统控制加压缓冲罐内压力逐渐降低至常压。排出的气体通过液体石蜡以回收低沸点液体甲酸乙酯。关闭循环系统的制冷功能。(4)升温—恒温发汗排出发汗皿垫水。发汗皿出口连接蜡下储罐;启动压缩机并保持加压缓冲罐内压力稳定在1.0~1.2个大气压(表压),而在蜡层下方保持为常压;启动循环系统加热功能,以1.5℃/h的升温速率使蜡层温度升高到73.0℃并恒温4.0小时以使蜡层中的固态组分与液态组分充分分离。发汗皿出口换接粗产品储罐(Ⅲ),并保持缓冲罐内压力稳定在1.0~1.2个大气压(表压),发汗皿皿板下方保持常压;继续以1.0℃/h的升温速率使蜡层温度升高到75.0℃并恒温4.0小时以使蜡层中的固态组分与液态组分充分分离;停压缩机。发汗皿出口换接粗产品储罐(Ⅳ);开启真空泵并保持缓冲罐内压力稳定在-0.4~-0.6大气压(表压),蜡层上方保持常压;以1.0℃/h的升温速率使蜡层温度升高到77.0℃并恒温4.0小时以使蜡层中的固态组分与液态组分充分分离。停真空泵,终止发汗过程。升温及恒温的发汗过程中排出的气体通过液体石蜡以回收低沸点液体甲酸乙酯。(5)发汗装置清理发汗皿出口换接蜡上储罐;继续升高循环水的温度到90℃熔化取出蜡上,以清理发汗装置。(6)产品精制和成型、包装。粗产品(Ⅲ)、(Ⅳ)分别经白土精制、成型和包装后即为节温器用蜡介质产品(Ⅲ)和产品(Ⅳ)。节温器用蜡介质产品(Ⅲ)性质:熔点74.6℃。节温器用蜡介质产品(Ⅲ)的收率为12.61%(相对于原料470℃~530℃馏分)。由节温器用蜡介质产品(Ⅲ)制备的节温器产品推杆的行程—温度关系如图2中曲线(Ⅲ)所示。从图2中曲线(Ⅲ)可以看出,节温器推杆行程在72℃时行程小于1mm,70℃~80℃间行程大于8mm,符合标称温度为70℃节温器的技术要求。节温器用蜡介质产品(Ⅳ)性质:熔点76.7℃。节温器用蜡介质产品(Ⅳ)的收率为13.15%(相对于原料470℃~530℃馏分)。由节温器用蜡介质产品(Ⅳ)制备的节温器产品推杆的行程—温度关系如图2中曲线(Ⅳ)所示。从图2中曲线(Ⅳ)可以看出,节温器推杆行程在74℃时行程小于1mm,72℃~82℃间行程大于8mm,符合标称温度为72℃节温器的技术要求。通过实施例1-2可以看出,本发明以F-T合成产物生产节温器用蜡介质的方法,通过选择适当的催化剂和反应条件,将原料中的烯烃及含氧化合物转化为节温器用蜡介质的适宜组分;再通过蒸馏富集目的组分;通过在发汗过程中采用气流通过蜡层携带出液态组分的方法强制液态组分与固态组分分离,增强了分离效果;利用低沸点液体汽化在蜡层中形成均匀分散的微小气泡也有利于液态组分的快速排出,从而以F-T合成产物为原料,使用发汗这种无溶剂分离方法生产出碳数分布范围较窄且正构烷烃含量较高的蜡产品,可以用作节温器用蜡介质。