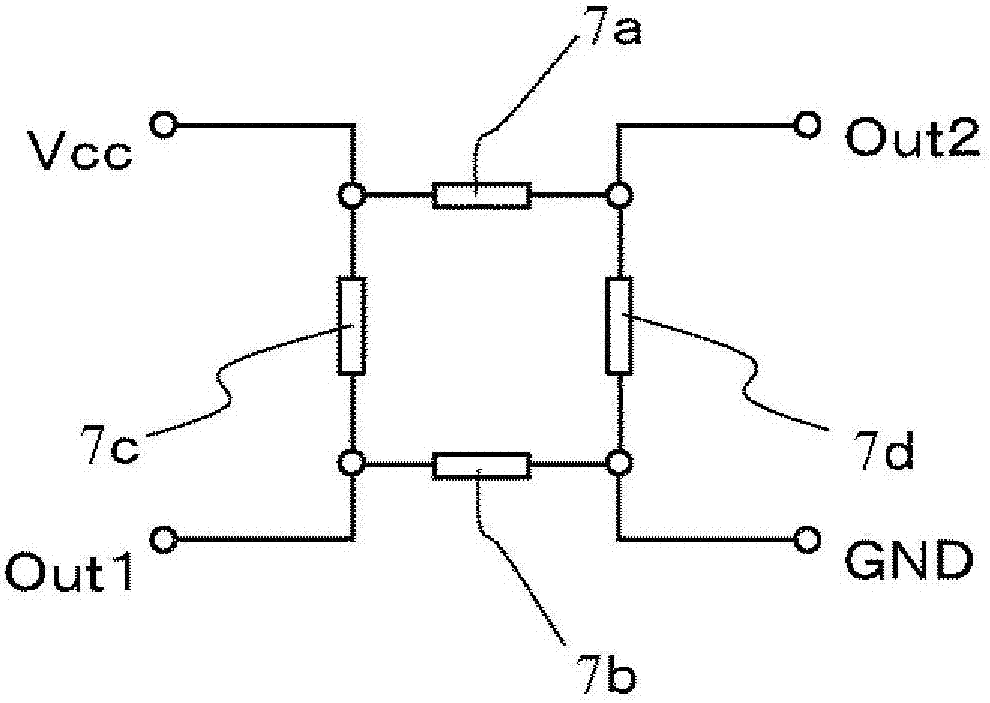
本发明涉及利用受到压力的膜片的变形来进行检测的压力传感器。
背景技术:在膜片上形成有应变片的结构的压力传感器众所周知。该压力传感器利用压力所致的膜片的变形而导致应变片的电阻发生变化来检测压力。一般来说,由四个应变片构成电桥电路,通过从该电桥电路得到与压力成比例的差分电压输出来检测压力。此处,电桥电路主要用于温度补偿目的。这是因为,只要四个应变片的变化相同,则即使应变片具有温度特性电桥电路的输出也不发生变化。当用于1MPa程度以下的低压时,通常使用利用对硅基板进行加工而形成了膜片的硅膜片的结构的压力传感器。专利文献1公开了从硅基板的背面进行蚀刻来形成薄的膜片,在膜片上形成多晶硅制的应变片的技术。根据专利文献1,四个应变片中两个配置在膜片周边部,另外两个配置在膜片中央部,由此,因压力施加而在应变片中产生的应力分别称为压缩应力和拉伸应力。还公开了:通过将膜片设成长方形,在配置于膜片中央的应变片中,能够减少对传感器灵敏度起负面作用的垂直方向的应力。在用于1MPa程度以上的高压时或者需要耐蚀性而不能露出硅的用途等之中,使用利用不锈钢制的膜片在膜片上贴上半导体应变片或者贴上形成有半导体应变片的传感器芯片的结构的压力传感器。专利文献2公开了在圆形的金属制膜片之上接合形成有应变片的单晶半导体制的传感器芯片的技术。其中,传感器芯片的尺寸大于膜片的尺寸,以传感器芯片上的应变片配置在膜片周边部上的方式接合传感器芯片。根据专利文献2,四个应变片中两个朝向圆周方向配置,另外两个朝向半径方向配置,由此因压力施加而在应变片中产生的应力分别成为压缩应力和拉伸应力,得到传感器灵敏度。还公开了:通过将传感器芯片的形状做成尽量接近圆形的多边形,能够尽量排除传感器芯片与膜片的线膨胀系数差所致的热应力的不良影响。现有技术文献专利文献专利文献1:日本专利第2615887号公报专利文献2:日本专利第4161410号公报
技术实现要素:发明想要解决的技术问题在如上所述的现有的压力传感器中,四个应变片中至少两个配置在膜片的外周部。此处,对应于压力施加的膜片的应力分布在外周部与中央部相比,其变化更为急剧。因此,应变片的位置偏移所致的检测误差与内周部相比较大。特别是,在如专利文献2那样将传感器芯片与金属制膜片接合的结构的压力传感器中,由于传感器芯片的接合位置偏移,导致传感器芯片上的应变片的位置相对于膜片的边缘的位置偏移时,存在传感器特性容易变化的问题。另外,在接合有传感器芯片的结构的压力传感器中,硅等半导体制的传感器芯片与金属制的膜片的线膨胀系数不同,所以因温度变化产生热变形,因此该热变形所致的传感器输出变化也是问题。本发明的目的在于,实现一种加工误差、组装误差等所致的传感器特性的不均较小且随温度变化的传感器输出的变化小的压力传感器。用于解决技术问题的技术方案为了解决上述技术问题,本发明的压力传感器在具有长边和短边的膜片上配置形成有构成电桥电路的特性相等的四个应变片的半导体制成的传感器芯片,由电桥电路检测与施加于膜片的压力成比例的电压输出,上述压力传感器的特征在于,四个应变片中两个沿着短边,另外两个沿着长边,靠近膜片的中央附近配置,从传感器芯片看在长边方向上具有膜片的厚度较薄的部分。发明效果根据本发明,能够实现一种加工误差、组装误差等所致的传感器特性的偏差较小且随温度变化的传感器输出的变化小的压力传感器。附图说明图1是本发明的第一实施例的(a)平面图、(b)截面图、(c)截面图。图2是示出电桥电路的例子的说明图。图3是本发明的第一实施例的变形例的(a)平面图、(b)截面图、(c)截面图。图4是表示本发明的第二实施例的概略图。图5是本发明的第三实施例的(a)平面图、(b)截面图、(c)截面图。图6是本发明的第三实施例的变形例的平面图。图7是本发明的第四实施例的(a)平面图、(b)截面图、(c)截面图。图8是本发明的第四实施例的变形例的(a)平面图、(b)截面图、(c)截面图。图9是本发明的第五实施例的截面图。图10是表示使用了基于分析的验证的模型形状的概要的立体图。图11是表示使用了基于分析的验证的三个模型的尺寸的立体图。图12是表示针对各模型的温度变化的分析结果的曲线图。具体实施方式图1(a)至(c)表示本发明的压力传感器的第一实施例的平面图和截面图。在图1(a)中,令沿着X轴的中心线为X中心线10,沿Y轴的中心线为Y中心线11,图1(b)表示X中心线10的截面图,图1(c)表示Y中心线11的截面图。压力传感器1是在形成有膜片2的金属制的传感器壳体3上通过接合层5接合方形的传感器芯片4的结构。图1(a)中,用虚线表示膜片2的外形。在传感器芯片4中,在不与膜片2接合的一侧的表面的中央部设有测量(gauge)区域6,在测量区域6内设有第一~第四应变片7a~7d。第一~第四应变片7a~7d利用未图示的配线相连,构成图2所示的惠斯通电桥电路。膜片2是具有短边和长边的各向异性形状,令短边方向为X轴,长边方向为Y轴。测量区域6配置在膜片2的中央部上。第一应变片7a和第二应变片7b配置成使得膜片2的短边方向(X轴方向)成为电流方向,第三应变片7c和第四应变片7d配置成使得膜片2的长边方向(Y轴方向)成为电流方向。在传感器壳体3的接合传感器芯片4的一侧的面形成有第一槽8a和第二槽8b。第一槽8a和第二槽8b与传感器芯片4相比在长边方向侧形成,形成在传感器芯片的两侧,以使得传感器芯片4位于第一槽8a和第二槽8b之间。通过槽8a、8b,与膜片2的传感器芯片4相比在Y轴侧上分别形成比搭载有传感器芯片4的部分薄的部分。在压力传感器1中,对应于施加在膜片2的与传感器4接合面相反一侧的面上的压力,膜片2发生变形,由此各应变片7a~7d的应力发生变化,随此各应变片7a~7d的电阻发生变化。将电阻值的变化作为电桥电路的差分输出,得到与压力成比例的输出。包括膜片2的传感器壳体3以不锈钢等金属为材质。传感器壳体3呈圆筒形,从一面对中央部进行加工,剩下的薄的部分成为膜片2。加工方法能够使用切削、放电加工或者压力加工等。膜片2的被加工侧的面的端部形成有R形状,具有缓和施加压力时在端部产生的应力集中的作用。传感器芯片4以单晶硅基板为材料制作。各应变片7a~7d是通过杂质扩散制作的P型硅的压电型电阻计。硅基板使用晶面(100)的基板,使X轴和Y轴与硅晶轴的<110>一致。因此,第一~第四应变片7a~7d全部都是p型硅<110>方向的压电型电阻计。接合层5使用Au/Sn焊料。接合的工艺是,例如在传感器芯片4的接合面通过溅射形成Ni/Au膜,在膜片2的传感器芯片4接合区域通过镀膜形成Sn膜,夹着颗粒状的Au/Sn进行对位,加热融化Au/Sn来接合。在第一实施例的压力传感器中,特征在于,第一~第四应变片7a~7d全部靠近位于膜片2的中央部上的测量区域6内配置。当施加压力时,在膜片2的表面产生的应力分布在膜片2的中央部比在膜片2的端部附近缓和。因此,即使传感器芯片4的接合位置发生偏移等,发生各应变片7a~7d相对于膜片2的相对位置偏移,在应变片7中产生的应力也难以变化。即,能够减小相对于位置偏移的传感器灵敏度的变化。另外,第一实施例的压力传感器1的特征在于,膜片2做成具有长边和短边的各向异性形状,第一~第四应变片中两个沿着长边方向(Y轴),另外两个沿着短边方向(X轴)配置。在图2所示的惠斯通电桥电路中,在第一应变片7a与第二应变片7b的组和第三应变片7c与第四应变片7d的组中,两者之间产生应力差,由此中点电位产生差,得到输出。因此,第一~第四应变片7a~7d中产生的应力全都相同时无法得到输出,传感器灵敏度为零。四个应变片7配置在膜片2的中央时,例如膜片2为圆形或正方形时,膜片2的中央部的应力在X轴方向和Y轴方向相等,所以传感器灵敏度为零。在第一实施例中,将膜片2做成Y轴方向上长的各向异性形状,所以在膜片2的中央部产生的应力在X轴方向上比在Y轴方向上大。因此,电流方向与X轴方向一致的第一应变片7a和第二应变片7b和电流方向与Y轴方向一致的第三应变片7c和第四应变片7d之间产生的应力不同,与应力变化相应的电阻变化量不同,所以能够获得传感器灵敏度。第一实施例的压力传感器1具有减小相对于温度变化的传感器输出的变化的效果。如上所述,第一~第四应变片7a~7d通过用于半导体制造的杂质扩散制作,通过高度管理的工艺得到均匀的特性的应变片。由此,初始电阻、压电型电阻率、压电型电阻率的温度依赖性等的特性均匀,相对于温度变化的变化也均匀。这样的均匀的变化利用惠斯通电桥电路来抵消,所以第一实施例的压力传感器很难相对于温度变化而发生输出变化。另外,第一实施例中,第一~第四应变片7a~7d靠近配置。在传感器芯片4内发生温差时,各应变片的位置彼此远离时,各应变片的电阻变化可能发生差异。第一实施例的压力传感器中,第一~第四应变片7a~7b靠近配置,所以各应变片之间难以产生温差,结果是应变片输出难以变化。而且,第一~第四应变片7a~7d全部配置在传感器芯片4的中央部。通过温度变化,膜片2和传感器芯片4的热膨胀系数差导致发生热应力,但该热应力除了传感器芯片4的端部附近外大致是各向同性的。因此,应变片中一部分靠近传感器芯片4的端部配置时,容易根据热应力的差而发生输出变化。另一方面,第一实施例的压力传感器中,第一~第四应变片7a~7b全部配置在传感器芯片4的中央部,所以各应变片的应力大致相等,热应力难以出现差异。因此,传感器输出难以发生变化。此处,膜片2的形状具有各向异性导致热应力在X轴方向和Y轴方向产生差异。因此,发生膜片2的各向异性导致的传感器输出的变化。此处,在膜片2的中央部,热应力的分布与端部相比较缓和。因此,在膜片2的中央部附近与膜片2的端部相比,膜片2的各向异性形状所致的传感器输出的变化较小,但还有改善的余地。为了进一步降低膜片2的各向异性形状导致的传感器输出的变化,在第一实施例中,在传感器壳体3形成第一槽8a和第二槽8b。通过相对于传感器芯片4靠近膜片的长边方向(Y轴方向)配置槽8a、8b,具有使Y轴方向的热应力与X轴方向热应力接近的效果。因此,能够进一步降低各应变片之间的热应力差,能够进一步降低膜片2的各向异性形状所致的传感器输出的变化。本发明人对相对于温度变化的压力传感器的热变形行为进行详细研究后,导出了槽8a、8b的效果。本发明人在存在应变片7a~7b的传感器芯片4的中央,详细研究了相对于温度变化的X轴方向和Y轴方向的应力发生差异的原因。考虑到温度上升的情况,线膨胀系数较大的传感器壳体3与传感器芯片4相比膨胀更多,所以传感器芯片4对整体产生拉伸应力。同时,在厚度较薄的膜片2和传感器芯片4接合的部分,还发生面外方向的弯曲变形。该弯曲变形是膜片侧凸出的变形,在存在应变片7的传感器芯片4表面侧产生压缩应力,但该压缩应力相对于作用在传感器芯片4整体上的拉伸应力来说较小。然而,因为膜片2的各向异性形状,作为短边方向的X轴方向与作为长边方向的Y轴方向相比弯曲曲率较小,X轴方向的压缩应力大于Y轴方向的压缩应力。因为从拉伸应力减去的压缩应力的大小在X轴方向更大,所以结果是,拉伸应力在Y轴方向更大,发生X轴方向和Y轴方向的应力差。于是,相对于膜片2的传感器芯片4的搭载部在Y轴方向上形成槽8a、8b,由此降低Y轴方向的传感器壳体3的刚性,降低施加于传感器芯片4的Y轴方向的热应力。结果是,能够使Y轴方向的热应力接近X轴方向的热应力,能够减少X轴方向和Y轴方向的应力差。槽8a、8b的位置靠近传感器芯片4时,降低施加于传感器芯片4的应力的效果更高,予以优选。因此,也可以使传感器芯片4的端部和槽8a、8b的端部一致,但考虑到传感器芯片4的接合位置偏移,优选例如在离开0.1mm左右的一定距离的位置形成槽8a、8b。槽8a、8b的形状能够做成各种各样的形状。如图1所示,X轴方向的长度比传感器芯片4的长度长时,容易降低施加在传感器芯片4的应力,予以优选。不过,比传感器芯片4短也能够得到一定的效果,不限于此。另外,如图3所示,第一槽8a和第二槽8b也可以做成在宽广的区域形成的台阶那样,使得第一槽8a和第二槽8b到达传感器壳体3的端部。能够增大膜片2的薄的部分的区域,降低Y轴方向的应力的效果好。另外,传感器壳体3的结构变简单,容易制造。膜片2和传感器芯片4的位置关系,优选为如第一实施例那样,在X轴方向上看时(YZ截面处),传感器芯片4的尺寸大于膜片2的尺寸。在上述结构中,在X轴方向上,传感器芯片4的端部位于膜片2的外侧,所以在传感器芯片4的接合端部难以产生高的应力,能够降低传感器特性的变化。而且,当在Y轴方向看时(XZ截面处),优选传感器芯片4的尺寸小于膜片2的尺寸。过于增大传感器芯片4时,传感器芯片4的制造成本变高,而且传感器芯片4和膜片2的热膨胀系数差可能导致在传感器芯片4的接合部产生的热应力升高等。对于有限尺寸的传感器芯片4,膜片2全部配置在传感器芯片4的内部时,膜片2的尺寸变小。这样,膜片2的应力分布的变化也变急剧,能够配置应变片7的区域有限之外,还存在应变片7的位置偏移的影响也变大的问题。通过使膜片2的尺寸在短边方向小于传感器芯片4且在长边方向大于传感器芯片4,防止膜片2的尺寸变小,并且还能够减小传感器芯片4的接合部的边缘发生的应力。在传感器芯片4上不仅能够制作电桥电路,还能够制作输出放大器、电流源、A/D转换器、输出校正电路、保存校正值的存储器、温度传感器等外围电路。由于在传感器芯片4内设有如上所述的信号处理电路,能够进行输出信号的放大、温度校正、零点校正等,能够提高输出信号的精度。在温度校正中,应变片7和温度传感器能够形成在相同的传感器芯片4上,所以能够准确地测量应变片7的温度,能够高精度进行温度校正。在第一实施例中,受到压力的膜片2和传感器壳体3是耐力性优异的不锈钢制,所以容易构成能够测量高压力范围的传感器。另外,在作为测定对象的液体或气体的腐蚀性高时,也能够使用。不锈钢的种类在重视耐力时选择SUS630等析出硬化型的不锈钢,在重视耐蚀性的情况下,选择SUS316等耐蚀性高的不锈钢等,能够选择各种材质。另外,材质不限于不锈钢,考虑耐力和耐蚀性、与硅之间的热膨胀系数差等,能够选择各种材料。另外,关于接合层5的材质和接合工艺,也不限于上述的材质和工艺。作为接合层5,例如使用Au/Ge焊料、Au/Si焊料,由此能够进一步减小接合层5的蠕变变形。另外,虽然容易蠕变变形,但如果是允许这种情况的用途,那么能够使用各种粘接剂。接合工艺除了使用上述的Au/Su颗粒(pellet)的方法以外,还有直接将Au/Sn镀在膜片或传感器芯片背面等而形成的方法等。利用图4,对本发明的第二实施例进行说明。其中,与第一实施例一样的结构,省略说明。第一~第四应变片7a~7d采用串联连接多个压电型电阻的结构。图4(a)表示测量区域6内的应变片7的配置,图4(b)表示电桥电路的结构。是构成第一~第四应变片7a~7d的每一个压电型电阻的组在测量区域内配置有四组的结构。分为四个的第一应变片7a以未图示的配线串联连接在一起。第二~第四应变片7b~7d也一样。这样,如图4(b)所示,将被分为四个的应变片统一起来,构成与图2所示的电桥电路等价的电桥电路。像这样,分割应变片而分散配置在测量区域6内,由此具有将应力的平均值均匀化的效果。例如,在测量区域6内应力分布不均匀,在Y方向上存在梯度时,第一应变片7a在测量区域6内的Y轴的正的区域被分开配置,第二应变片7b在Y轴的负的区域分开配置时,两者间产生压力差,出现输出。通过第二实施例的结构,分割应变片而分散配置在测量区域6内,由此能够使应变片7间的压力差变小。利用图5,对本发明的第三实施例进行说明。另外,与第一实施例同样的结构省略说明。图5(a)~(c)表示本发明的压力传感器1的第三实施例的平面图和截面图。图5(a)中,令沿着X轴的中心线为X中心线10,沿Y轴的中心线为Y中心线11,图5(b)表示X中心线10的截面图,图5(c)表示Y中心线11的截面图。膜片2采用设置从长边方向的中央至端部的区域处的短边方向的尺寸比长边方向中央附近处的短边方向的尺寸大的部分的结构,采用中央部变细的葫芦似的形状。即,X中心线10上的膜片2的尺寸采用膜片中央尺寸12时,比X中心线10更向Y轴方向偏离的膜片2的长边方向端部附近处的X轴方向的尺寸(膜片端部尺寸13)大于上述膜片中央尺寸12。在膜片2的中央部变细的第三实施例中,与没有变细的情况相比,膜片2的中央部的短边方向和长边方向的应力差能够扩大。由于传感器灵敏度成比例于上述应力差,所以提高了相对于传感器灵敏度的应力利用效率(对于在应变片中产生的最大应力得到的传感器灵敏度的比例)。另外,膜片2的中央部附近的应力分布的变化变小,能够进一步减小位置偏移的影响。在第三实施例中,也在传感器壳体3形成有槽8a、8b。通过将槽8a、8b相对于传感器芯片4靠近膜片2的长边方向(Y轴方向)配置,具有Y轴方向应力接近X轴方向应力的效果,减少应力差,降低输出变化。在膜片2采用葫芦状的第三实施例中,在配置槽8的位置,膜片2的X轴方向长度变宽,所以通过形成槽能够减薄膜片2的厚度的区域比第一实施例更广。因此,容易得到降低Y轴方向的应力的效果,具有容易降低输出变化的效果。槽8a、8b如图5所示,X轴方向的长度形成为比膜片2的长度长,能够形成为膜片2在X轴方向上被完全横穿。另外,如图6的平面图所示,槽8a、8b也能够形成为收敛在比膜片2的外形靠内侧的区域。这样,能够在膜片2的端部确保槽形成前的厚度。当受到压力时在膜片2产生的应力在膜片2的端部变高,所以通过确保端部的厚度,在膜片2产生的最大应力减小,能够使塑性变形难以发生。槽8a、8b的X轴方向的长度优选比传感器芯片4的长度长,但比传感器芯片4短也能够得到一定的效果,并不限于此。另外,如第一实施例的图3所示的变形例所示,也可以将槽8a、8b做成形成在宽广区域的台阶那样,以到达传感器壳体3的端部。膜片2的薄的部分的区域增大,Y轴方向的应力的降低效果升高。另外,传感器壳体3的结构变简单,制造容易。作为上述的第三实施例应变片的结构,也能够采用第二实施例记载的结构。由此,能够获得与第二实施例中记载的效果一样的效果。利用图7说明本发明的第四实施例。另外,与第一实施例一样的结构省略说明。图7(a)~(c)表示本发明的压力传感器1的第四实施例的平面图和截面图。图7(a)中,令沿着X轴的中心线为X中心线10,沿Y轴的中心线为Y中心线11,图7(b)表示X中心线10的截面图,图7(c)表示Y中心线11的截面图。在第四实施例中,槽8(第一槽8a和第二槽8b)形成在膜片2的接合传感器芯片4的面的相反的面一侧。在本结构中,从传感器4看,也在长边方向形成膜片2的厚度薄的部分,所以具有降低传感器芯片4中央的Y轴方向应力的效果,能够降低相对于温度变化的输出变化。在第四实施例的结构中,在传感器壳体3形成膜片2和槽8时,具有可以从一个方向加工的优点。图8(a)~(c)表示第四实施例的变形例。图8(a)中,令沿着X轴的中心线为X中心线10,沿Y轴的中心线为Y中心线11,图8(b)表示X中心线10的截面图,图8(c)表示Y中心线11的截面图。如本变形例所示,形成在膜片2的槽8a、8b可以到达膜片2的端部。另外,因为是传感器芯片4接合面的相反的面一侧,所以槽8也可以到达比传感器芯片4的外形靠内侧的位置。无论是何种情况,均能够增大膜片2的薄的部分的区域,Y轴方向应力的降低效果好。另外,虽未图示,但如图5所示的第三实施例那样利用葫芦状的膜片的情况下,也能够如第四实施例那样在传感器芯片4接合面侧相反的面一侧形成槽8a、8b。另外,作为第四实施例的应变片的结构,也能够采用第二实施例记载的结构。由此,能够获得与第二实施例中记载的效果一样的效果。利用图9说明本发明的第五实施例。另外,与第一实施例一样的结构省略说明。图9表示本发明的压力传感器的第五实施例的截面图。第五实施例表示将第一~第四实施例中记载的压力传感器组装成产品形态的压力传感器组件21的构成例。传感器壳体3除了第一~第四实施例中记载的结构之外,还具有将外周部以圆筒状向下方伸长的圆筒部22,一体形成为在外侧面设置凸缘部23和螺纹部24的形状。螺纹部24为外螺纹,在作为测量对象的配管侧准备内螺纹的接头(未图示)安装。上述圆筒部22的内部形成压力到入口25,经由该压力导入口25将作为测量对象的液体或气体导入到膜片2的表面。在传感器壳体3的上表面,与传感器芯片4相邻地配置有配线基板26。配线基板26利用粘接剂27粘接保持在传感器壳体3的上表面。传感器芯片4和配线基板26的电极焊盘间利用导线28电连接。为了保护传感器芯片4的表面及其周边部,圆筒形的罩29与传感器壳体3的凸缘部23连接设置。在罩29的上端设置有多个外部电极销30,以使其贯通罩29。外部电极销30和配线基板26经由柔性配线基板31电连接。传感器芯片4经由导线28、配线基板26、柔性配线基板31、外部电极销30向外部发送信号。通过第五实施例的结构,能够获得能够容易安装在测量对象的装置的配管且容易进行用于对传感器供电和信号取出的配线的压力传感器组件21。在如第五实施例所示的压力传感器组件21中,在测定对象的配管螺纹固定时对传感器组件21施力时,变形传递到传感器壳体3,传感器芯片4中央的应力发生变化,从而传感器输出发生变化,有时这成为问题。上述的力的施加方法应该相对于X轴和Y轴是各向同性的,但因为膜片2的形状为各向异性的,所以与相对温度变化的行为一样,上述应力也产生各向异性。在本发明的压力传感器中,通过在膜片2的长边方向形成槽8a、8b,对于上述的螺纹固定的力的影响,也具有使在传感器芯片4中央发生的X轴方向应力和Y轴方向应力接近的效果,能够降低传感器输出的变化。以下,表示由本发明得到的效果进行验证的结果为了确认本发明的通过形成槽8a、8b降低相对于温度变化的输出变化的效果,进行了利用有限元法(FEM)的数值分析。图10是表示用于分析的模型形状的立体图。采用在圆板状的传感器壳体的中央设置有方形的传感器芯片的形状的模型,省略了接合层。为了研究相对于温度变化的输出变化,实施使温度上升1℃的分析。传感器芯片的材料采用硅,且使线膨胀系数为2.5×10-6/℃。传感器壳体的材料采用不锈钢,且使线膨胀系数为10.8×10-6。当升高温度时,线膨胀系数大的传感器壳体更膨胀,所以传感器芯片整体产生拉伸应力。图11表示比较研究的分析模型形状。关于X轴和Y轴对称,所以利用XY对称的1/4模型实施了分析,图11也表示1/4形状。图11(a)所示的模型1是传感器壳体采用形成有膜片的圆板的情况,在传感器芯片中在X轴方向上以及Y轴方向上都有同样的应力起作用。图11(b)所示的模型2是形成有将X轴方向为短边,将Y轴方向为长边的长方形的膜片的情况。图11(c)所示的模型3是在模型2的形状中追加槽的情况。从传感器芯片看,槽在长边方向靠近传感器芯片配置,槽的短边方向的长度比传感器芯片长。槽的深度为膜片的厚度的一半。图12是分析结果的应力分布的曲线图。表示应变片形成的传感器芯片表面的应力分布。如图12中所示,从传感器芯片的中心沿着X轴划的线上的X轴方向应力设为X线应力,从传感器芯片的中心沿着Y轴划的线上的Y轴方向应力设为Y线应力。图12的曲线图中示出了关于模型1~3的分析结果的X线应力和Y线应力。曲线的横轴以传感器芯片端部为1归一化示出距传感器芯片中心的距离,曲线的纵轴的应力以模型1的传感器芯片中央的应力为1归一化示出。在没有膜片的模型1中,X线应力与Y线应力的分布一致,在传感器芯片中央,产生拉伸应力。形成有长方形膜片的模型2中,与模型1相比,传感器芯片中央的应力下降,X线应力小于Y线应力。与模型1相比,膜片的部分变薄,所以传感器壳体的刚性下降,拉伸传感器芯片的力减弱,所以应力下降。另外,薄的膜片和传感器芯片的层叠结构中,通过两者的热膨胀差,还产生弯曲变形(面外弯曲变形),弯曲所致的应力在传感器芯片表面为压缩方向,所以作用为稍微缓和拉伸应力。此时,X轴方向上膜片较短,所以弯曲变形的曲率较小,传感器芯片中央的拉伸应力的缓和量比Y轴方向大。因此,可以认为在具有应变片的传感器芯片中央,X轴方向应力小于Y轴方向应力,产生XY应力差,输出发生变化。当观察形成有槽的模型3的结果时,X线应力的分布与模型2几乎不变,但Y线应力的分布与X模型2相比下降。从传感器芯片看,在Y轴方向形成槽,由此传感器壳体的刚性下降,仅在Y轴方向,拉伸传感器芯片的力下降,能够仅降低Y轴方向应力。结果是,Y轴方向应力与X轴方向应力接近,XY应力差减少,能够减小输出变化。在本分析的结果中,传感器芯片中央处的XY应力差,在模型2中为0.092,在模型3中为0.034。假定传感器输出与传感器芯片中央的XY应力差成比例时,能够将相对于温度变化的传感器输出变化(即温度特性)通过追加槽进一步降低约63%。附图标记说明1压力传感器2膜片3传感器壳体4传感器芯片5接合层6测量区域7a第一应变片7b第二应变片7c第三应变片7d第四应变片8a第一槽8b第二槽10X中心线11Y中心线12膜片中央尺寸13膜片端部尺寸21压力传感器组件22圆筒部23凸缘部24螺纹部25压力导入口26配线基板27粘接剂28导线29罩30外部电极销31柔性配线板。