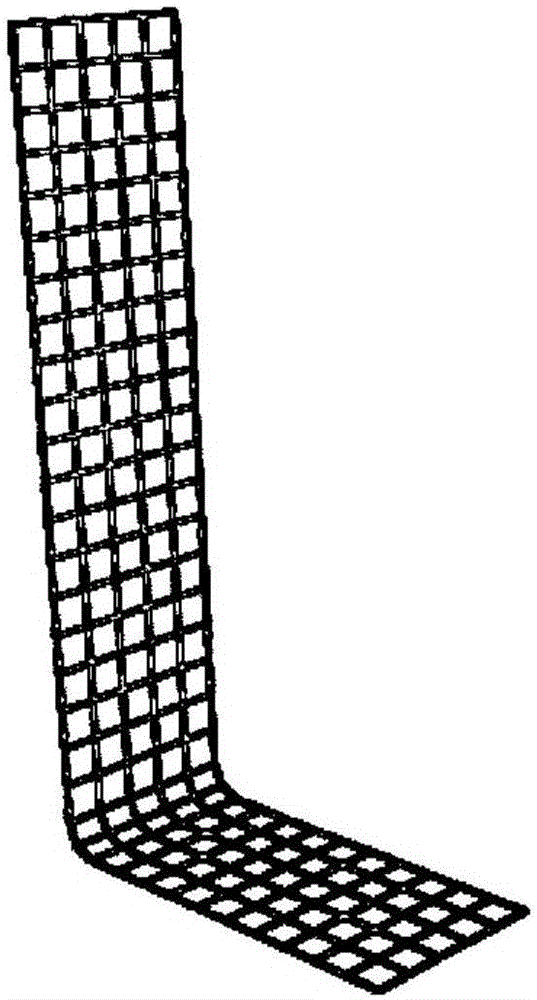
本发明涉及复合材料构件领域,尤其涉及复合材料构件热校形工艺的仿真模拟方法。
背景技术:
:碳纤维增强树脂基复合材料是以树脂为基体、碳纤维为增强体,采用先进复合材料的成型加工方法制备的一系列高性能复合材料。复合材料结构在经历高温固化及冷却成型过程后,受热应力的作用、基体树脂的化学反应收缩效应,以及复合材料与成型模具的相互作用,复合材料在室温下的自由形状与预期的理想形状之间会产生一定程度的不一致,通常将这种不一致状态称为构件的固化变形。固化变形会影响构件的外形精度。我们尝试通过热校形工艺对发生固化变形的复合材料零件进行再加工,修正复合材料的形状,降低废品率,方便零件装配。热校形工艺过程:零件在外力的作用下贴覆到校形模具表面,在高温下保持载荷一段时间后卸载,修正零件的外形轮廓。影响热校形效果的因素包括热校形温度、热校形时间和热校形载荷。不同的校形时间和校形载荷,热校形后零件形状不同,因此需要建立一套复合材料热校形工艺的有限元模拟方法,用模拟替代重复的试错性实验。对给定的复合材料结构,给出优化的热校形工艺参数。缩短热校形工艺参数确定的周期,节约生产成本。技术实现要素:本发明要解决的技术问题是为了克服现有技术难以准确模拟复合材料的热校形工艺过程的缺陷,提出一种复合材料构件热校形工艺的仿真模拟方法。本发明是通过下述技术方案来解决上述技术问题的:本发明提供了一种复合材料构件热校形工艺的仿真模拟方法,其特点在于,包括以下步骤:步骤一、建立复合材料的L形构件模型,所述L形构件模型包括短腹板和长腹板,输入复合材料在若干方向上的力学参数和热膨胀参数;步骤二、采用有限元软件中的壳单元对所述L形构件模型进行网格划分,建立L形构件的有限元模型;步骤三、将所述L形构件的有限元模型中的短腹板的三点简支约束作为边界条件,对所述有限元模型施加温度载荷ΔT,通过如下公式计算所述L形构件的固化变形,公式中,aI、aT分别表示复合材料的面内热膨胀系数、厚度方向热膨胀系数,ΔT表示材料成型降温过程中的温度变化,Δθ表示所述L形构件的角度的变化量,θmoId表示热校形工艺中所用的成型模具的角度;步骤四、对所述L形构件的有限元模型施加校形载荷,其约束条件为所述短腹板水平横放,使所述长腹板旋转预设的旋转角度;步骤五、对所述L形构件的有限元模型模拟应力松弛过程,所述应力松弛过程近似为面内剪切应力的应力松弛,并且在所述应力松弛过程中,保持所述校形载荷的约束条件不变;步骤六、模拟脱模过程,其中去掉所述校形载荷,恢复约束条件为三点简支约束,以得到所述L形构件模型最终的残余应力和变形状态。较佳地,步骤一中输入复合材料在所述L形构件的面内方向和厚度方向上的力学参数和热膨胀参数。较佳地,所述面内方向由面内纵向和面内横向构成。较佳地,所述力学参数包括弹性模量和剪切模量。较佳地,步骤四中的所述旋转角度大于3°且小于10°。较佳地,所述复合材料为织物增强热固性复合材料。较佳地,所述复合材料为碳纤维增强树脂基复合材料。较佳地,所述有限元软件为abaqus软件。较佳地,所述壳单元为S4R单元,即线性缩减积分壳单元。较佳地,步骤五中采用abaqus软件的子程序UMAT模拟应力松弛过程。在符合本领域常识的基础上,上述各优选条件,可任意组合,即得本发明各较佳实例。本发明的积极进步效果在于:本发明的复合材料构件热校形工艺的仿真模拟方法,能够预报复合材料的固化变形和其在校形载荷下的应力松弛行为,准确模拟复合材料的热校形工艺过程,尤其是碳纤维增强树脂基复合材料的热校形工艺过程。附图说明图1为本发明一较佳实施例的仿真模拟方法中建立的L形构件模型的示意图。图2为本发明一较佳实施例中对图1中的L形构件模型进行网格划分后得到的有限元模型的示意图。图3为本发明一较佳实施例中的L形构件在热校形前的形状示意图。图4为本发明一较佳实施例中的L形构件在热校形后的形状示意图。具体实施方式下面结合说明书附图,进一步对本发明的优选实施例进行详细描述,以下的描述为示例性的,并非对本发明的限制,任何的其他类似情形也都落入本发明的保护范围之中。在以下的具体描述中,方向性的术语,例如“左”、“右”、“上”、“下”、“前”、“后”、等,参考附图中描述的方向使用。本发明的实施例的部件可被置于多种不同的方向,方向性的术语是用于示例的目的而非限制性的。参考图1所示,本发明一较佳实施例的复合材料构件热校形工艺的仿真模拟方法,包括以下步骤:步骤一、建立复合材料的L形构件模型,所述L形构件模型包括短腹板和长腹板,输入复合材料在若干方向上的力学参数和热膨胀参数;步骤二、采用有限元软件中的壳单元对所述L形构件模型进行网格划分,建立L形构件的有限元模型;步骤三、将所述L形构件的有限元模型中的短腹板的三点简支约束作为边界条件,对所述有限元模型施加温度载荷ΔT,通过如下公式计算所述L形构件的固化变形,公式中,aI、aT分别表示复合材料的面内热膨胀系数、厚度方向热膨胀系数,ΔT表示材料成型降温过程中的温度变化,Δθ表示所述L形构件的角度的变化量,θmold表示热校形工艺中所用的成型模具的角度,其中,热校形前复合材料的L形构件的形状,可参考图3所示;步骤四、对所述L形构件的有限元模型施加校形载荷,其约束条件为所述短腹板水平横放,使所述长腹板旋转预设的一旋转角度;步骤五、对所述L形构件的有限元模型模拟应力松弛过程,所述应力松弛过程近似为面内剪切应力的应力松弛,并且在所述应力松弛过程中,保持所述校形载荷的约束条件不变;步骤六、模拟脱模过程,其中去掉所述校形载荷,恢复约束条件为三点简支约束,以得到所述L形构件模型最终的残余应力和变形状态,其中,热校形前复合材料的L形构件的形状可参考图4所述。在如图3、4中示出的这一例子中,L形构件在热校形前后,其长腹板和短腹板间的夹角可由图3所示的88.9°变为图4所示的89.8°。具体来说,本实施例中,选取T300碳纤维织物增强环氧树脂基复合材料的L形构件作为研究对象,在abaqus环境下建立如图1所示的L形构件模型,其由短腹板、长腹板、拐角三部分组成。对图1所示的L形构件模型,采用S4R单元进行网格划分,建立起有限元分析模型,如图2所示。容易理解的是,尽管本发明针对L形构件进行说明,但容易将本发明推广到形状结构更复杂的构件中。在本发明的仿真模拟方法中,为了简化模拟过程,本发明的建模建立在以下假设的基础上。即,复合材料中为连续纤维且纤维在树脂中均匀分布,在模拟固化变形时可以认为复合材料近似是弹性的。本实施例中,输入的复合材料在不同方向上的力学参数和热膨胀参数,如下表1所示。表1密度(g/cm3)1.154面内纵向模量EX(Pa)6.0E+10面内横向模量EY(Pa)6.0E+10泊松比PRXY0.042剪切模量GXY(Pa)3.36E+9剪切模量GXZ(Pa)3.47E+9轴向热膨胀系数ALPX(T-1)1.67E-06面内横向热膨胀系数ALPY(T-1)1.67E-06法向热膨胀系数ALPZ(T-1)79.66E-6在网格划分建立L形构件的有限元模型后,计算复合材料的固化变形及残余应力分布情况。在如上计算了构件的固化变形后,进行应力松弛的模拟,具体如下。首先对L形构件的有限元模型施加校形载荷,边界条件为约束短腹板水平横放,对L形构件长腹板旋转一定角度,在本实施例中旋转6°。然后,模拟应力松弛过程,在此过程中保持校形载荷约束条件不变,并采用具有粘弹性特征的复合材料本构关系,通过abaqus自定义子程序UMAT实现。应力松弛过程的模拟,基于以下假设或是近似,即材料的经向和纬向不发生应力松弛,并满足层合板理论,因而材料的应力松弛可近似为面内剪切应力的应力松弛。本实施例的复合材料的L形构件的面内剪切应力松弛规律接近于四元件模型,可由以下公式(1)表示:其中表示松弛过程中t时刻的面内剪切应力、表示初始状态的面内剪切应力,t表示热校形时间。A、B、C、n、a66为系数。本实施例中,公式(1)中的系数分别可测得为,A=19.18、B=0.85、C=-21.03MPa、n=0.00048s-1、a66=1。通过UMAT子程序,计算得到材料经历应力松弛后的应力状态。以下对表示上述面内剪切应力松弛规律的公式作进一步说明。经典的四元件模型描述的是各向同性材料的应力松弛行为,可以表示如下:σt=(σ0-σ∞)e-′/τ+σ∞(2)公式(2)中σ′表示材料在t时刻的应力,σ0表示应力松弛前材料的应力,σ∞表示松弛时间无穷大时材料的应力。t为时间,τ为应力松弛时间。对于本实施例的织物增强复合材料,在模拟过程中,假设经纬向不发生应力松弛,则复合材料的应力松弛主要是面内剪切应力的松弛,在本实施例中得到面内剪切应力松弛规律由公式(1)所示。可以看到,本实施例中的松弛规律(即公式1)与经典的四元件模型的公式形式(公式2)类似,应力同样按指数函数衰减,但σ∞项变为其为与初始应力有关的一函数。对于公式(1),本领域技术人员可根据上述思路参照现有技术中的相关文献进行推导,在此不再赘述。复合材料具有各向异性,复合材料构件在热压罐工艺过程中经历复杂的物理、化学变化,往往产生严重的固化变形问题。并且,复合材料构件在经历热压罐工艺后往往具有严重的残余应力,残余应力与校形载荷使得构件产生的内应力一样,都会在高温下发生松弛。因此,准确分析、预报构件的固化变形和残余应力是实现热校形工艺预报分析的最重要的基础。另一方面,复合材料构件在高温下的应力松弛行为,是指材料在位移不变的情况下,应力随时间发生衰减的行为,是热校形工艺的原理和物理本质。本发明的仿真模拟方法能够准确预报复合材料构件经历热压罐工艺后的固化变形和残余应力分布,并基于有效应力-应变理论,通过有限元分析软件,将粘弹性模型嵌入计算,形成对复合材料构件应力松弛行为的有限元模拟办法,尤其适用于碳纤维增强树脂基复合材料的热校形工艺过程的模拟。虽然以上描述了本发明的具体实施方式,但是本领域的技术人员应当理解,这些仅是举例说明,本发明的保护范围是由所附权利要求书限定的。本领域的技术人员在不背离本发明的原理和实质的前提下,可以对这些实施方式做出多种变更或修改,但这些变更和修改均落入本发明的保护范围。当前第1页1 2 3