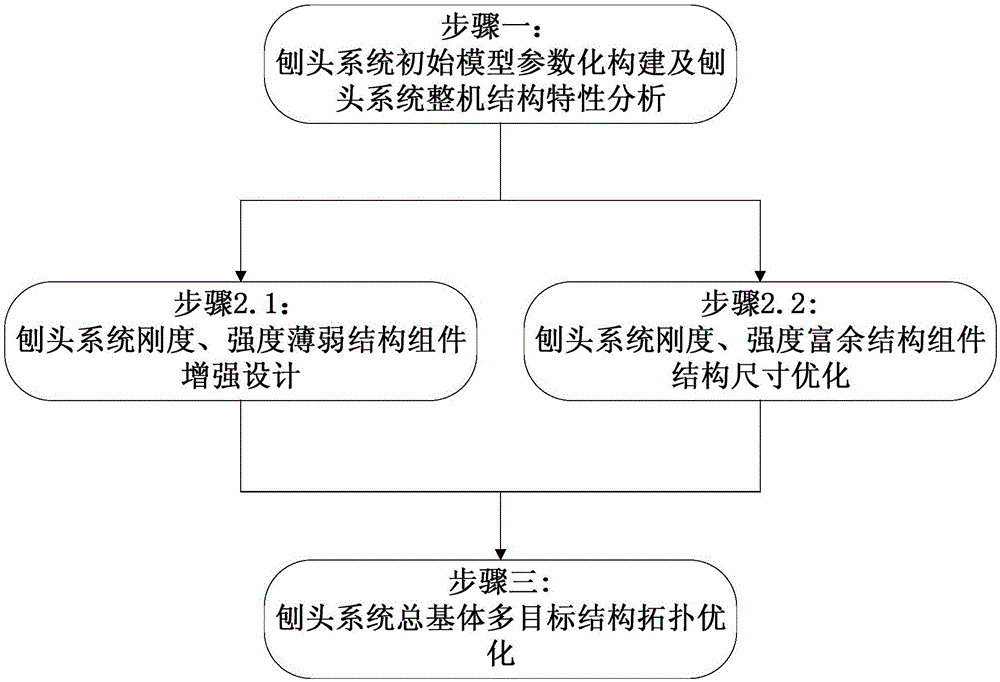
本发明涉及煤矿矿用开采设备的设计方法,特别是涉及一种刨煤机刨头结构综合优化方法。
背景技术:
:刨煤机采煤技术是实现薄与极薄煤层工作面、煤与瓦斯突出工作面机械化、自动化开采的重要技术手段。装有刨刀的刨头在刨链牵引下,沿采煤工作面刮板输送机的中部槽导轨刨削煤岩,实现煤岩的开采与运输。刨头系统是刨煤机的主要工作执行机构,通常由刨头基体、左右刨体、左右回转体、左右底刀架、左右顶刀架、盖板与刨刀等结构组件共同组成。在煤岩刨削过程中,刨头系统所受载荷复杂多变,工况恶劣,其结构设计的优劣将直接影响刨煤机整体工作性能。现有的刨头设计多结合设计者经验进行设计,往往通过盲目增加刨头系统质量与结构尺寸来实现结构强度的提升,从而保证其运行可靠性,这也导致所设计刨头系统在煤层厚度非常有限的开采空间内异常笨重,强度富余量大,整机能耗高。随着有限元技术、优化设计方法、拓扑设计方法的不断发展和应用,围绕刨煤机单体零部件开展的优化设计理论方法得到了一定的应用,但在含有多结构体的刨头整机系统结构拓扑综合优化设计方法应用领域仍未有成熟设计方法。刨头系统设计是一个多目标优化设计问题,要综合考虑刨头整机系统的刚度、振动特性、总体质量、稳定性等多方面的内容,如何在数量众多的设计参数和约束空间中实现刨头系统的综合多目标结构拓扑优化是刨煤机生产制造单位有待解决的重要议题。技术实现要素:针对现有技术存在的问题,本发明提供一种使刨头结构达到刚度最大、刨头受迫振动频率最大、刨头总体质量最轻、刨头屈曲稳定性最优目标的刨煤机刨头结构综合优化方法。为了实现上述目的,本发明采用如下技术方案:一种刨煤机刨头结构综合优化方法,以刨头结构刚度最大、刨头受迫振动频率最大、刨头总体质量最轻、刨头屈曲稳定性最优为多目标优化设计目标,以刨头基体、左右刨体、左右回转体、左右底刀架、左右顶刀架、盖板的结构参数化尺寸与空间拓扑结构形态为设计变量,以刨头结构强度、刨头屈曲特征值、刨头最大形变量、刨头整体结构长、宽、高尺寸及体积参数为约束条件,进行刨头结构的综合优化,包括以下步骤:步骤一:刨头系统初始模型参数化构建及刨头系统整机结构特性分析;建立刨头零部件的三维几何模型,基于参数化建模技术,构建盖板、刨头基体、左右刨体、左右回转体、左右底刀架、左右顶刀架的初始结构模型;建立刨头系统整体结构的结合面接触刚度模型,基于赫兹接触模型,建立刨头基体-左右刨体接触刚度等效模型、左右刨体-左右回转体接触刚度等效模型、左右刨体-左右顶刀架接触刚度等效模型、左右回转体-左右底刀架接触刚度等效模型,求解刨头系统在刨削载荷作用下的等效刚度参数值;对刨头系统建立有限元分析模型,对零部件进行结构的简化、装配,去除较小的过渡圆角、圆孔、凹孔与凸台,赋予各个零部件相应的材料弹性模量、泊松比、密度、屈服强度、抗拉强度,进行刨头系统的有限元网格划分,结合上述步骤中所建立的各结合面接触刚度模型,采用弹簧阻尼单元对结合面进行等效处理,输入已确定的各结合面特性等效参数,添加刨头有限元模型的载荷边界条件与约束条件,进行刨头系统整机有限元刚度特性分析与受迫振动频率分析,显示刨头系统结构等效应力、模态分析、谐响应分析结果,从而得到整机及组成零部件综合变形量与系统静、动刚度,固有频率、模态振型,获得刨头系统在动态刨削负载简谐力激振下的应力频谱,完成刨头系统刚度、强度薄弱结构组件和刚度、强度富余结构组件的分析;步骤二:刨头系统刚度、强度薄弱结构组件增强设计,及刨头系统刚度、强度富余结构组件结构尺寸优化;对需要进行增强的零部件进行设计结构域分割,其中各零部件装配结合面设定为不可设计结构域,其它区域为可设计结构域,根据步骤一中对刨头系统的有限元分析结果,确定刨头系统初始零部件负载最大区域,对零部件可设计结构域采取改变结构参数或增大安全系数或增加附属结构的方式完成刚度、强度薄弱结构组件的结构增强设计,并重复步骤一中的有限元分析过程,直至所有刚度、强度薄弱结构组件满足材料强度与结构刚度要求;对左右刨体滑靴搭接结合面尺寸参数进行优化,在有限元软件的结构优化设计模块中,设定左右刨体滑靴搭接结合面低阶固有频率高、挠度变形小为目标函数,设定各设计变量结构尺寸范围,设定相应约束值,建立优化分析试验各参数样本点,采用正交实验设计方法完成实验方案的设计,依据所设计的实验方案建立左右刨体滑靴搭接结合面的多目标结构尺寸参数优化设计模型并开展验算;对左右底刀架、左右顶刀架上的相邻刨刀座水平排距,相邻刨刀座位姿角参数进行优化,在有限元软件的结构优化设计模块中,设定左右底刀架、左右顶刀架低阶固有频率最高、屈曲稳定性最优为目标函数,设定各设计变量结构尺寸范围,设定相应约束值,建立优化分析试验各参数样本点,采用正交实验设计方法完成实验方案的设计,依据所设计的实验方案建立左右底刀架、左右顶刀架上相邻刨刀座水平排距,相邻刨刀座位姿角的多目标结构尺寸参数优化设计模型并开展验算;结合上述各步骤的参数优化结果,进一步修正刨头系统结构尺寸参数,完成刨头系统结构模型重建;步骤三:刨头系统总基体多目标结构拓扑优化;将步骤二所构建的新刨头模型的刨头盖板、刨头基体、左右刨体、左右底刀架、左右顶刀架之间结合面做固接绑定处理,构建除左右回转体的刨头结构总基体,基于参数化建模技术,对结构参数进行参数化驱动,对总基体进行设计域分割,确定刨头盖板、左右回转体、刨头基体、左右刨体、左右底刀架、左右顶刀架之间的装配结合面为不可设计结构域,其它区域为可设计结构域,建立以刨头系统总基体结构刚度最大、总基体低阶固有频率最高、总基体总体质量最轻、总基体屈曲稳定性最优为多目标的结构拓扑优化设计模型,去除伪密度值小于0.2的结构单元,结合优化设计参数,完成刨头系统总基体的结构拓扑再设计,重复进行步骤一,完成刨头结构优化方案的验证。进一步,步骤一中建立三维几何模型时需要参数化的几何尺寸包括:盖板厚度、长度、宽度,盖板下联接销直径;左右刨体高度、宽度,左右刨体滑靴搭接面厚度、宽度、长度尺寸参数;刨头基体联接销孔直径,刨头基体背板横向筋板厚度、纵向筋板厚度、竖向筋板厚度;左右顶刀架相邻刨刀座水平排距,左右顶刀架相邻刨刀座位姿角;左右底刀架相邻刨刀座水平排距,左右底刀架相邻刨刀座位姿角。进一步,步骤一中添加刨头有限元模型的载荷边界条件与约束条件,包括:刨头基体与刮板输送机中部槽导轨间摩擦力;左右刨体与刮板输送机中部槽导轨间摩擦力;沿煤壁走向迎煤一侧刨体牵引组件结构上的刨链拉力;作用于左右顶刀架、左右底刀架,左右回转体及左右刨体表面的煤岩挤压力;作用于迎煤一侧刨体装煤犁形槽与迎煤一侧底刀架上的挤压装煤力;作用于迎煤一侧刀架上的刨削阻力。进一步,步骤一中刨头系统在刨削载荷作用下的等效刚度参数计算为:刨头牵引力:T=X+F1+F2+Fk+Fr+To式中,X为作用在刨头X方向的合力;F1、F2、Fk、Fr为摩擦阻力,且Fk=μ1Gk、Fr=μ1Rn,μ为刨头与运输机之间的摩擦系数,一般为0.3,μ1为刨头与底板之间的摩擦系数,一般为0.3-0.6;为迎煤端刨头所受反作用力、为非迎煤端刨头所受反作用力;Gk为压在刨头滑靴搭接结合面中部槽的重量;Rn为底板反力,Rn=Gk+Gc+Z,Gc为刨头重量,Z为作用于刨头上Z方向的合力;To为松边刨链的摩擦力,To=μoqoLo,μo摩擦系数为0.4,qo为松边刨链每米重量;Lo为松边刨链长度;煤壁刨削阻力:式中,Zi为第i把刨刀所受刨削力,m为各种刨刀数量;刨头所受摩擦力:式中,Si为第i把刨刀刨削过程中所受摩擦力,m为各种刨刀数量;煤壁挤压力:式中,Ai为第i把刨刀所受煤壁挤压力,m为各种刨刀数量;装煤力:PΓ=P1+P2+P3+P4+P5,P1为刨头装载面插入煤堆中所需要的力,且P1=kbd,bd为刨头装载面宽度,k为刨头装载斜面单位宽度上的插入力,对于煤堆,k=2000-3000N/m;P2为煤堆从刨头装载斜面移动到装载高度所需的力,且G为位于刨头装载斜面上且低于装载高度煤堆的重力,f为煤与刨头装载斜面的摩擦系数,δ1为刨头装载斜面的倾斜角度,δ1≤60°。P3为刨头提升煤堆的力,且G'为位于装载表面且超过装载高度部分煤堆的重力,δ2为刨头装载斜面高位处的倾角,δ2≤75°。P4为煤堆被推送到输送机上所需的力,且G”为输送机移动煤堆的重力,f'为煤与煤之间的摩擦系数,ρ为输送机装煤斜面与工作面形成的角度,ρ≤60°。P5为煤堆内摩擦力,且Hn为装煤高度,bd为刨头装载面宽度,ψo为煤堆的抗截强度,ψo=0.0245-0.0274MPa,μ为煤的内摩擦系数,湿煤μ=0.5,干煤μ=0.85,γ为煤的密度,Hw为刨头前煤堆高度,δ1为刨头装载斜面的倾斜角度,θ为沿煤堆挤出楔滑移面与底板间夹角,δ1与θ之间满足下述关系:δ1/°3045607590θ/°6653485352等效刚度参数值计算公式为:且其中:K为接触结合面总刚度,Ki为第i个结合接触面等效刚度值,Pi为第i个结合接触面间压强,wi为第i个结合接触面间渗透量,i=1,2,3,...,V,V为设计变量的个数。进一步,步骤二对左右刨体滑靴搭接结合面尺寸参数优化时,在有限元软件的结构优化设计模块中设定的目标函数包括:低阶固有频率最高,即maxf(x);挠度变形最小,即minω(x);设计变量为:左右刨体滑靴搭接结构横截面的尺寸参数X=[x1,x2,...,xn]T,n为设计变量的个数;约束条件为:结构尺寸约束:令L为左右刨体滑靴搭接结构横截面尺寸下限值,U为左右刨体滑靴搭接结构横截面尺寸上限值,即L≤X≤U,且li≤xi≤ui,i=1,2,3,...,n,下限L=[l1,l2,...,ln]T,上限U=[u1,u2,...,un]T;最大等效应力约束:σmax≤[σ];最小屈曲特征值约束:λ1≥[λ]。进一步,步骤二中对左右底刀架、左右顶刀架上相邻刨刀座水平排距,相邻刨刀座位姿角参数进行优化时,在有限元软件的结构优化设计模块中设定的目标函数包括:低阶固有频率最高,即maxf(x);屈曲稳定性最优,即maxλ(x)。设计变量为:左右底刀架、左右顶刀架上相邻刨刀座水平排距参数T=[t1,t2,...,tq]T,q为设计变量个数;相邻刨刀座位姿角参数α=[α1,α2,...,αm]T,m为设计变量个数;约束条件为:结构尺寸约束:令L'为相邻刨刀座水平排距或相邻刨刀座位姿角参数下限值,U'为相邻刨刀座水平排距或相邻刨刀座位姿角参数上限值,即L'≤T||α≤U',且li'≤ti||αi≤ui',i=1,2,3,...,j,下限L'=[l1',l2',...,lj']T,上限U'=[u1',u2',...,uj']T,||为逻辑符号“或者”,j为设计变量个数,且j=q+m;相邻刨刀水平排距约束:令t为相邻刨刀水平排距,且50≤1.5h≤t≤2.3h≤110,b≤t,h为刨刀切煤深度,b为刨刀宽度;相邻刨刀位姿角约束:±5°≤α≤±55°;最大等效应力约束:σmax≤[σ];最小屈曲特征值约束:λ1≥[λ]。进一步,步骤三中建立以刨头系统总基体结构刚度最大、总基体低阶固有频率最高、总基体总体质量最轻、总基体屈曲稳定性最优为多目标的结构拓扑优化设计模型,设定的目标函数包括:总基体结构刚度最大,即maxK(x);总基体低阶固有频率最高,即maxf(x);总基体总体质量最轻,即minM(x);总基体屈曲稳定性最优,即maxλ(x);设计变量为:刨头总基体结构尺寸参数P=[p1,p2,...,pe]T,e为设计变量个数。约束条件为:刨头高度结构尺寸约束:Hn+4.8Hminhmax+Δc≤Hc≤75Hmax,其中Hc为刨头高度;Hn为装煤高度;Hmin为煤层最低高度;hmax为刨削下块状破碎煤屑最大厚度;Δc为刨刀超前量,20≤Δc≤50;Hmax为煤层最大厚度;其它结构尺寸约束:令L”为刨头总基体结构尺寸下限值,U”为刨头总基体结构尺寸上限值,即L”≤P≤U”,且li”≤pi≤ui”,i=1,2,3,...,e,下限L=[l1,l2,...,le]T,上限U=[u1,u2,...,ue]T;Vi/V0≤Ω,Vi优化后设计域有效体积数,V0优化前初始设计域体积数,Ω为体积比,且0.5≤Ω≤0.9;0≤ρr≤1,r=1,2,...,s,ρr为第r个单元的材料密度,s为设计变量的个数;f1≥85,f1为最低阶固有频率;最大等效应力约束:σmax≤[σ];最小屈曲特征值约束:λ1≥[λ]。本发明的有益效果:本发明先进行刨头系统初始模型参数化构建及特性分析,然后对系统刚度、强度薄弱结构组件进行增强设计,对系统刚度、强度富余结构组件进行尺寸优化设计,最后对刨头系统总基体进行多目标结构拓扑优化,从而使刨头总基体结构达到刨头结构刚度最大、刨头受迫振动频率最大、刨头总体质量最轻、刨头屈曲稳定性最优的目标。上述优化方法综合考虑多方面的参数影响,可设计出最合理、性能最优的刨煤机刨头结构。附图说明图1为本发明刨煤机刨头结构的结构示意图;图2为本发明刨煤机刨头结构综合优化方法的流程图;图3为图2的展开流程图;图4为本发明刨煤机刨头结构中滑靴搭接结构横截面的尺寸参数图;图5为本发明刨煤机刨头结构中右顶刀架相邻刨刀座水平排距图;图6为本发明刨煤机刨头结构中右顶刀架相邻刨刀座位姿角参数图;图7为本发明刨煤机刨头结构中右顶刀架销轴联接部结构强度增强设计图;图8为本发明刨煤机刨头结构拓扑优化后刨头基体结构示意图;图中,1—盖板、2-刨刀座、3-左刨体、4-右刨体、5-刨头基体、6—左底刀架、7-右底刀架、8—左顶刀架、9—右顶刀架、10-左回转体、11-右回转体。具体实施方式下面将结合本发明实施例中的附图,对本发明实施例中的技术方案进行清楚、完整地描述,显然,所描述的实施例仅仅是本发明的一部分实施例,而不是全部的实施例。基于本发明中的实施例,本领域普通技术人员在没有作出创造性劳动前提下所获得的所有其他实施例,都属于本发明保护的范围。如图1及图2,本发明提供一种刨煤机刨头结构综合优化方法,用于对刨头机构进行优化,刨头基本结构包括盖板1、刨刀座2、左刨体3、右刨体4、刨头基体5、左底刀架6、右底刀架7、左顶刀架8、右顶刀架9、左回转体10、右回转体11。由于左刨体3和右刨体4左右对称设置,其设计方法相同,故下面在优化方法中直接以左右刨体代指左刨体3和右刨体4,同样的,左底刀架6和右底刀架7左右对称,以左右底刀架代指左底刀架6和右底刀架7,左顶刀架8和右顶刀架9左右对称,以左右顶刀架代指左顶刀架8和右顶刀架9,左回转体10和右回转体11左右对称,以左右回转体代指左回转体10和右回转体11。如图2及图3,以刨头结构刚度最大、刨头受迫振动频率最大、刨头总体质量最轻、刨头屈曲稳定性最优为多目标优化设计目标,以刨头基体5、左右刨体、左右回转体、左右底刀架、左右顶刀架、盖板1的结构参数化尺寸与空间拓扑结构形态为设计变量,以刨头结构强度、刨头屈曲特征值、刨头最大形变量、刨头整体结构长、宽、高尺寸及体积参数为约束条件,进行刨头结构的综合优化,包括以下步骤:步骤一:刨头系统初始模型参数化构建及刨头系统整机结构特性分析,其具体过程为:(1)基于参数化建模技术,在UGNX三维建模软件中建立刨头零部件的三维几何模型,构建刨头系统的盖板1、刨头基体5、左右刨体、左右回转体、左右底刀架、左右顶刀架的初始结构模型。采用UG软件参数化驱动建模模块,设定盖板1的厚度长度宽度盖板1下联接销直径左右刨体高度宽度如图4,左右刨体滑靴搭接面上壁厚度宽度左右刨体滑靴搭接面侧壁厚度长度左右刨体滑靴搭接面上壁悬伸量左右刨体滑靴搭接面侧角γ;刨头基体5连接销孔直径刨头基体5背板横向筋板厚度纵向筋板厚度竖向筋板厚度如图5,左右顶刀架上相邻刨刀座2的水平排距tDing=ti,i=1,2,3,4,本实施例中令t1=t2=t3,如图6,左右顶刀架上相邻刨刀座2的位姿角αDing=αDingi,i=1,2,3,4;左右底刀架上相邻刨刀座2的水平排距tDi,在本实施例中左右底刀架上相邻刨刀座2水平排距tDi均相等,且记为tDi=tD,左右底刀架相邻刨刀座2的位姿角αDi,在本实施例中αD=αDi,i=1,2,3,上述尺寸为可参数化驱动结构参数,其初始赋值与尺寸约束空间如表1所示,设计负载功能结构面与装配结构面,在UG软件中完成刨头系统组成零部件的总体装配。表1刨头系统参数化结构尺寸初始设计值与尺寸约束空间(2)建立刨头系统整体结构的结合面接触刚度模型。基于赫兹接触模型,建立刨头基体-左右刨体接触刚度等效模型、左右刨体-左右回转体接触刚度等效模型、左右刨体-左右顶刀架接触刚度等效模型、左右回转体-左右底刀架接触刚度等效模型,在刨头系统刨削载荷作用下,分别计算刨头基体-左右刨体接触刚度等效值K1、左右刨体-左右回转体接触刚度等效值K2、左右刨体-左右顶刀架接触刚度等效值K3、左右回转体-左右底刀架接触刚度等效值K4。刨削载荷主要包括作用在刨头系统上的刨头牵引力,煤壁刨削阻力,刨头所受摩擦力,煤壁挤压力,及装煤力。其理论计算公式如下:刨头牵引力:T=X+F1+F2+Fk+Fr+To式中,X为作用在刨头X方向的合力;F1、F2、Fk、Fr为摩擦阻力,且Fk=μ1Gk、Fr=μ1Rn,μ为刨头与运输机之间的摩擦系数,一般为0.3,μ1为刨头与底板之间的摩擦系数,一般为0.3-0.6;为迎煤端刨头所受反作用力、为非迎煤端刨头所受反作用力;Gk为压在刨头滑靴搭接结合面中部槽的重量;Rn为底板反力,Rn=Gk+Gc+Z,Gc为刨头重量,Z为作用于刨头上Z方向的合力;To为松边刨链的摩擦力,To=μoqoLo,μo摩擦系数为0.4,qo为松边刨链每米重量;Lo为松边刨链长度。煤壁刨削阻力:式中,Zi为第i把刨刀所受刨削力,m为各种刨刀数量;刨头所受摩擦力:式中,Si为第i把刨刀刨削过程中所受摩擦力,m为各种刨刀数量;煤壁挤压力:式中,Ai为第i把刨刀所受煤壁挤压力,m为各种刨刀数量;装煤力:PΓ=P1+P2+P3+P4+P5,P1为刨头装载面插入煤堆中所需要的力,且P1=kbd,bd为刨头装载面宽度,k为刨头装载斜面单位宽度上的插入力,对于煤堆,k=2000-3000N/m;P2为煤堆从刨头装载斜面移动到装载高度所需的力,且G为位于刨头装载斜面上且低于装载高度煤堆的重力,f为煤与刨头装载斜面的摩擦系数,δ1为刨头装载斜面的倾斜角度,δ1≤60°。P3为刨头提升煤堆的力,且G'为位于装载表面且超过装载高度部分煤堆的重力,δ2为刨头装载斜面高位处的倾角,δ2≤75°。P4为煤堆被推送到输送机上所需的力,且G”为输送机移动煤堆的重力,f'为煤与煤之间的摩擦系数,ρ为输送机装煤斜面与工作面形成的角度,ρ≤60°。P5为煤堆内摩擦力,且Hn为装煤高度,bd为刨头装载面宽度,ψo为煤堆的抗截强度,ψo=0.0245-0.0274MPa,μ为煤的内摩擦系数,湿煤μ=0.5,干煤μ=0.85,γ为煤的密度,Hw为刨头前煤堆高度,δ1为刨头装载斜面的倾斜角度,θ为沿煤堆挤出楔滑移面与底板间夹角,δ1与θ之间满足下述关系:δ1/°3045607590θ/°6653485352则,等效刚度参数值计算公式为:且其中:K为接触结合面总刚度,Ki为第i个结合接触面等效刚度值,Pi为第i个结合接触面间压强,wi为第i个结合接触面间渗透量,i=1,2,3,...,V,V为设计变量的个数。在本实施例中,计算得到的刨头基体-左右刨体接触刚度等效值K1=9.87×109N/m,左右刨体-左右回转体接触刚度等效值K2=6.45×109N/m,左右刨体-左右顶刀架接触刚度等效值K3=8.36×109N/m,左右回转体-左右底刀架接触刚度等效值K4=6.11×109N/m。(3)对刨头系统建立有限元分析模型。对零部件进行结构的简化、装配,去除较小的过渡圆角、圆孔、凹孔与凸台,赋予各个零部件相应的材料弹性模量为216GPa、泊松比为0.3、密度7.84×103kg/m3、屈服强度324MPa、抗拉强度568MPa等属性。然后进行刨头系统的有限元网格划分,结合步骤一(2)中建立的各结合面接触刚度模型,采用弹簧阻尼单元对结合面进行等效处理,输入步骤一(2)中确定的各结合面特性等效参数。添加刨头有限元模型的载荷边界条件与约束条件,进行刨头系统整机有限元刚度特性分析与受迫振动频率分析,显示刨头系统结构等效应力、模态分析、谐响应分析结果。从而得到整机及组成零部件综合变形量与系统静、动刚度,固有频率、模态振型,获得刨头系统在动态刨削负载简谐力激振下的应力频谱,完成刨头系统刚度、强度薄弱结构组件和刚度、强度富余结构组件的分析。分析得到初始设计刨头系统前6阶固有频率与振型特征如表2所示。在本实施例中,添加刨头有限元模型的载荷边界条件与约束条件,主要包括:刨头基体5与刮板输送机中部槽导轨间摩擦力16KN;左右刨体与刮板输送机中部槽导轨间摩擦力14KN;沿煤壁走向迎煤一侧刨体牵引组件结构上的刨链拉力495KN;作用于左右顶刀架、左右底刀架,左右回转体及左右刨体表面的煤岩挤压力74KN;作用于迎煤一侧刨体装煤梨形槽与迎煤一侧底刀架上的挤压装煤力10KN;作用于迎煤一侧刀架上的刨削阻力405KN。表2刨头系统前6阶固有频率与振型步骤二:刨头系统刚度、强度薄弱结构组件增强设计,及刨头系统刚度、强度富余结构组件结构尺寸优化。步骤2.1刨头系统刚度、强度薄弱结构组件增强设计,具体设计过程为:(1)对要进行结构尺寸优化的零部件进行设计结构域分割,其中各零部件装配结合面设定为不可设计结构域,其他区域为可设计结构域。(2)根据步骤一(3)对刨头整机系统的有限元分析结果,确定刨头系统初始零部件负载最大区域,对零部件可设计结构域采取改变结构参数,增大安全系数,增加附属结构等方式完成该类组件的结构增强设计。然后重复步骤一(3),直至所有刚度、强度薄弱结构组件满足材料强度与结构刚度要求。在本实施例中,发现左右顶刀架与左右回转体之间存在强度薄弱区域,对该区域进行结构增强设计,采取的方式包括增大顶刀架与回转体联接销轴直径,由原有直径55mm增大到62mm,且在销轴结合面端部加工高度为3mm的辅助增强环形凸台,如图7所示。步骤2.2刨头系统刚度、强度富余结构组件结构尺寸优化,具体设计过程为:(1)对左右刨体滑靴搭接结合面尺寸参数进行优化。在有限元软件的结构优化设计模块中,设定左右刨体滑靴搭接结合面低阶固有频率高、挠度变形小为目标函数,设定各设计变量结构尺寸范围,设定相应约束值。建立优化分析试验各参数样本点,采用正交实验设计方法完成试验方案的设计,依据所设计的实验方案建立左右刨体滑靴搭接结合面的多目标结构尺寸参数优化设计模型并开展验算。对左右刨体滑靴搭接结合面尺寸参数优化时,在有限元软件的结构优化设计模块中设定的目标函数包括:低阶固有频率最高,即maxf(x);挠度变形最小,即minω(x);设计变量为:如图3,左右刨体滑靴搭接面上壁厚度宽度左右刨体滑靴搭接面侧壁厚度长度左右刨体滑靴搭接面上壁悬伸量左右刨体滑靴搭接面侧角γ,各设计变量初始值如表1所示,即n=6为设计变量个数。约束条件为:结构尺寸约束:令L为左右刨体滑靴搭接结构横截面尺寸下限值,U为左右刨体滑靴搭接结构横截面尺寸上限值,即L≤X≤U,且li≤xi≤ui,i=1,2,3,...,n,下限L=[l1,l2,...,ln]T,上限U=[u1,u2,...,un]T,各结构尺寸约束如表1所示,则L=[40,100,35,100,200,90]T,U=[65,150,65,150,320,145]T;最大等效应力约束:σmax≤[σ],[σ]为许用应力,即允许左右刨体滑靴承受的最大应力值;最小屈曲特征值约束:λ1≥[λ],[λ]为许用屈曲特征值。设计正交实验方案进行验算,因素集为γ,水平数为5,则所建立的实验方案如表3所示,共25组实验模型。表3左右刨体滑靴搭接结构横截面的尺寸参数优化设计实验方案(2)对左右底刀架、左右顶刀架上的相邻刨刀座2水平排距,相邻刨刀座2位姿角参数进行优化,在有限元软件的结构优化设计模块中,设定左右底刀架、左右顶刀架低阶固有频率最高、屈曲稳定性最优为目标函数,设定各设计变量结构尺寸范围,设定相应约束值,建立优化分析试验各参数样本点,采用正交实验设计方法完成试验方案的设计,依据所设计的实验方案建立左右底刀架、左右顶刀架上相邻刨刀座2水平排距,相邻刨刀座2位姿角的多目标结构尺寸参数优化设计模型并开展验算。对左右底刀架、左右顶刀架上相邻刨刀座2水平排距,相邻刨刀座2位姿角参数进行优化时,在有限元软件的结构优化设计模块中设定的目标函数包括:低阶固有频率最高,即maxf(x);屈曲稳定性最优,即maxλ(x)。设计变量为:左右底刀架、左右顶刀架上相邻刨刀座2的水平排距参数T=[t1,t2,...,tq]T,q为设计变量个数;相邻刨刀座2的位姿角参数α=[α1,α2,...,αm]T,m为设计变量个数;在本实施例中,左右底刀架、左右顶刀架上相邻刨刀座2水平排距参数分别为tD、tDing,各刨刀座2水平排距相等,其初始取值如表1所示,相邻刨刀座2位姿角参数分别为αDing1、αDing2、αDing3、αDing4,αD1、αD2、αD3与αD4,其初始取值如表1所示。约束条件为:结构尺寸约束:令L'为相邻刨刀座2水平排距或相邻刨刀座2位姿角参数下限值,U'为相邻刨刀座2水平排距或相邻刨刀座2位姿角参数上限值,即L'≤T||α≤U',且li'≤ti||αi≤ui',i=1,2,3,...,j,下限L'=[l1',l2',...,lj']T,上限U'=[u1',u2',...,uj']T,||为逻辑符号“或者”,j为设计变量个数,且j=q+m;相邻刨刀水平排距约束:令t为相邻刨刀水平排距,且50≤1.5h≤t≤2.3h≤110,b≤t,h为刨刀切煤深度,b为刨刀宽度;相邻刨刀位姿角约束:±5°≤α≤±55°,且根据设计要求,αDing4=10°,αD4=-5°;最大等效应力约束:σmax≤[σ];最小屈曲特征值约束:λ1≥[λ]。设计正交试验方案进行验算,因素集为tDing、αDing1、αDing2、αDing3、tD、αD1、αD2、αD3,水平数为4,则所建立的试验方案如表所示。表4相邻刨刀座水平排距、相邻刨刀座位姿角参数优化设计实验方案(3)进一步验算,依据表3实验方案,完成左右刨体滑靴搭接结合面尺寸参数优化设计,且以低阶固有频率最高、挠度变形最小为设计目标的最优设计值如表5所示;依据表4实验方案,完成左右底刀架、左右顶刀架相邻刨刀座2水平排距,相邻刨刀座2位姿角参数优化设计,且以低阶固有频率最高、屈曲稳定性最优为设计目标的最优设计值如表6所示。表5刨体滑靴搭接结合面尺寸参数优化结果表6刀架相邻刨刀座水平排距、相邻刨刀座位姿角参数优化结果(4)结合上述各步骤的参数优化结果,对左右刨体、左右顶刀架、左右底刀架结构进行重新建模设计,进一步修正刨头系统结构尺寸参数,完成刨头系统结构模型重建。其中,步骤2.1和步骤2.2可更换顺序。步骤三:刨头系统总基体多目标结构拓扑优化。(1)将步骤二所建立新刨头结构组件模型的盖板1、刨头基体5、左右刨体、左右底刀架、左右顶刀架之间结合面做固接绑定处理,构建除左右回转体的刨头结构总基体。基于参数化建模技术,对结构参数进行参数化驱动,参数化结构几何尺寸包括:盖板1的厚度长度宽度总基体高度宽度长度总基体背板横向筋板厚度纵向筋板厚度竖向筋板厚度(2)对总基体进行设计域分割,确定盖板1、左右回转体、刨头基体5、左右刨体、左右底刀架、左右顶刀架之间的装配结合面为不可设计结构域,其它区域为可设计结构域,(3)建立以刨头系统总基体结构刚度最大、总基体低阶固有频率最高、总基体总体质量最轻、总基体屈曲稳定性最优为多目标的结构拓扑优化设计模型。目标函数包括:总基体结构刚度最大,即maxK(x);总基体低阶固有频率最高,即maxf(x);总基体总体质量最轻,即minM(x);总基体屈曲稳定性最优,即maxλ(x);设计变量为:令刨头总基体结构尺寸参数P,P=[p1,p2,...,pe]T,e为设计变量个数,在本实施例中,约束条件为:刨头高度结构尺寸约束:Hn+4.8Hminhmax+Δc≤Hc≤75Hmax,其中Hc为刨头高度;Hn为装煤高度;Hmin为煤层最低高度;hmax为刨削下块状破碎煤屑最大厚度;Δc为刨刀超前量,20≤Δc≤50;Hmax为煤层最大厚度;刨头高度为刨头盖板厚度与总基体高度之和,即本实施例中675≤Hc≤950。其它结构尺寸约束:令L”为刨头总基体结构尺寸下限值,U”为刨头总基体结构尺寸上限值,即L”≤P≤U”,且li”≤pi≤ui”,i=1,2,3,...,e,下限L=[l1,l2,...,le]T,上限U=[u1,u2,...,ue]T。在本实施例中:Vi/V0≤Ω,Vi优化后设计域有效体积数,V0优化前初始设计域体积数,Ω为体积比,且0.5≤Ω≤0.9;0≤ρr≤1,r=1,2,...,s,ρr为第r个单元的材料密度,s为设计变量的个数;f1≥85,f1为最低阶固有频率;最大等效应力约束:σmax≤[σ];最小屈曲特征值约束:λ1≥[λ]。(4)去除伪密度值小于0.2的结构单元,结合优化设计参数,完成刨头系统总基体的结构拓扑再设计,如图8为结构拓扑优化后的刨头基体5的结构图,设计了减重孔,在应力集中区域进行圆角化处理。重复进行步骤一,完成刨头结构优化方案的验证。本发明刨煤机刨头结构综合优化方法先进行刨头系统初始模型参数化构建及特性分析,然后对系统刚度、强度薄弱结构组件进行增强设计,对系统刚度、强度富余结构组件进行尺寸优化设计,最后对刨头系统总基体进行多目标结构拓扑优化,从而使刨头系统达到刨头结构刚度最大、刨头受迫振动频率最大、刨头总体质量最轻、刨头屈曲稳定性最优的目标。以上实施例仅用以说明本发明的技术方案而非限制,尽管参照较佳实施例对本发明进行了详细说明,本领域技术人员应当理解,可以对本发明的技术方案进行修改或者等同替换,而不脱离本技术方案的宗旨和范围,其均应涵盖在本发明的权利要求范围内。当前第1页1 2 3