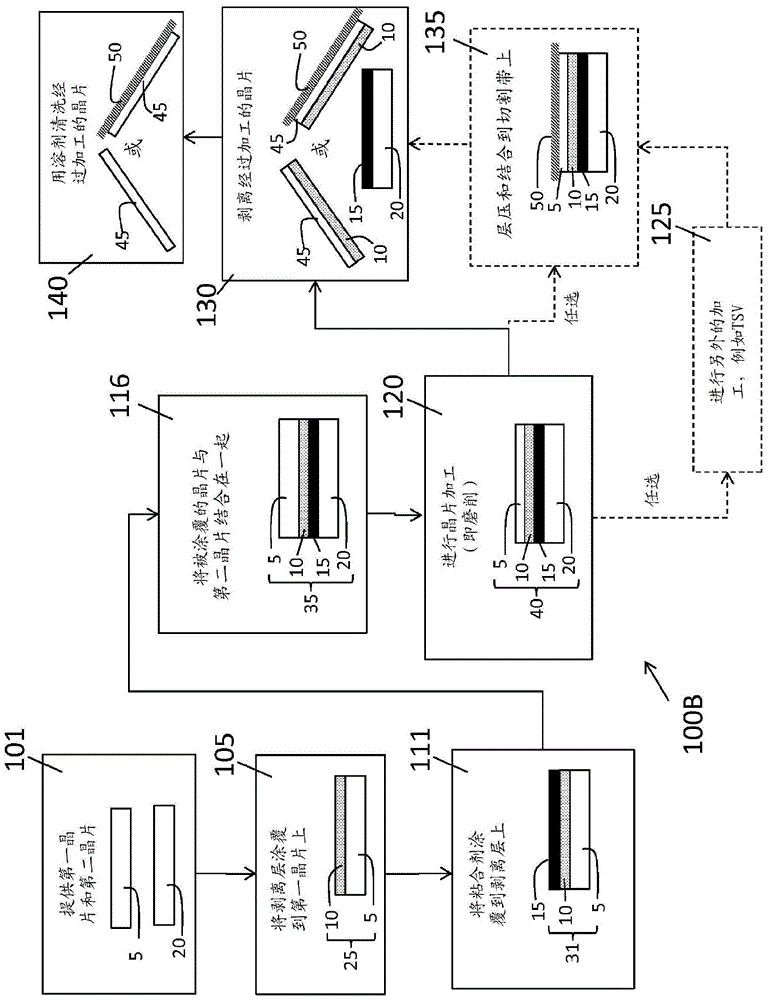
本发明整体涉及处理用于生产半导体产品的晶片的材料和工艺。更具体地讲,本发明涉及粘合剂和剥离层组合物的制备以及它们作为暂时性晶片结合材料的用途。
背景技术:微电子行业在制造要求高水平数据处理速度的半导体器件中使用非常薄的图案化晶片(如<50微米),从而要求具备高水平的晶片封装,并能够进行穿透硅通孔(TSV)加工和/或经受晶片磨削。这些半导体器件用于多种不同应用,例如三维封装和发光二极管(LED)。然而,由于图案化晶片非常薄,因此它也往往易碎。因此,在生产半导体器件过程中对这些晶片进行处理时,要求工艺和材料经过特殊设计,以免晶片发生损坏。在这方面,已出现暂时性晶片结合和剥离方法,成为制造工艺中的关键步骤。当前,微电子行业在生产半导体器件过程中采用单层和双层方法完成暂时性晶片结合和剥离。对于暂时性晶片结合的基本要求包括:(i)能够经受在至少180℃下的暴露;(ii)磨削后还能够存在;(iii)容易剥离和清洗;(iv)高通量(20-30晶片/小时);以及(v)耐受半导体行业中使用的多种典型化学品(溶剂、酸、碱等)。预计可使用旋涂法将材料涂覆到晶片上,因为可实现厚度控制、简单且快速操作。要求膜厚度最多为100微米,且厚度偏差小于1%。单层方法采用如美国专利公布No.2008/0173970中所述的热滑动机理。更具体地讲,使用交联噁唑啉将图案化晶片结合到载体晶片上。完成晶片磨削和TSV处理后,将晶片暴露于高温(285℃)下,然后机械滑动使晶片分开,从而分离晶片。由于结合和剥离需要在高温下操作且需要苛刻溶剂清洗以除去任何残留物,因此该方法可导致低收率和低生产率。双层方法使用附加层来帮助载体晶片首先从图案化薄晶片上剥离,如美国专利公布No.2009/0115075中所述。在该方法中,玻璃载体晶片涂覆有热敏材料的薄层,如光热转换(LTHC)材料。粘合剂被夹在涂覆有LTHC的玻璃晶片与图案化晶片之间,并通过紫外线辐照穿过玻璃晶片来固化。在进行晶片薄化和TSV加工后,激光辐照层叠件穿过玻璃晶片,以帮助剥离玻璃晶片。然后将粘合剂从图案化晶片上剥离下来。与该方法相关的若干缺点包括紫外线和激光源的同时使用,与玻璃载体晶片相关的有限寿命和热问题,以及与从图案化晶片上除去粘合剂相关的困难。美国专利公布No.2010/0330788描述了一种薄晶片处理结构,该结构包括半导体晶片、剥离层、粘合剂层和载体晶片。该结构被结合到一起,然后进行结合后工艺。然后对剥离层施加紫外线或激光形式的能量,将载体晶片与半导体晶片分离开来。最后通过化学浸泡操作除去半导体晶片上的粘合剂。与该方法相关的一个缺点涉及到在进行结合后工艺之后与使用紫外线或激光源剥离晶片相关的成本和困难。美国专利No.7,482,249描述了将硅基材料薄层(约1000埃)涂覆到图案化晶片上以及将无溶剂有机硅材料(大约100微米)涂覆到载体晶片上。被涂覆的图案化晶片采用等离子体处理以对其表面性质进行改性,从而在结合步骤之前改善剥离层材料与有机硅粘合剂材料的相容性。将结合晶片加热至高温,以便使粘合剂固化。晶片加工之后,将图案化薄晶片附接到切片型上,并利用剥离层的各向异性粘附力特性将图案化薄晶片从粘合剂去除。在该方法中,被涂覆的材料在施涂于晶片之后仍保持为液态,使其在后续加工过程中难以操纵或处理。此外,材料需要经过等离子体处理,使得该工艺变得复杂且成本高效益低。
技术实现要素:为克服列举的缺点和相关领域的其他限制,本发明总体上提供了一种处理半导体晶片表面以提高晶片在后续加工操作中的处理的方法。根据本发明的一个方面,该方法包括如下步骤:将剥离层施涂到第一晶片表面以形成涂覆有剥离层的晶片;将粘合剂施涂到第二晶片表面以形成涂覆有粘合剂的晶片;将涂覆有剥离层的晶片与涂覆有粘合剂的晶片结合到一起以形成结合晶片系统;在第一晶片和第二晶片中的一者上进行至少一次晶片加工操作(如晶片磨削等)以形成经过加工的晶片系统;通过引发剥离层和粘合剂之间的分离来剥离经过加工的晶片系统,从而获得经过加工的薄晶片;以及使用能够溶解剥离层或其任何残留物的有机溶剂对经过加工的薄晶片的表面进行清洗。此类有机溶剂的若干例子包括丙二醇单甲醚醋酸酯(PGMEA)、乙酸丁酯、甲苯、二甲苯和均三甲苯。根据本发明的另一个方面,该方法包括如下步骤:将剥离层施涂于第一晶片表面以形成涂覆有剥离层的晶片,然后将粘合剂施涂于涂覆有剥离层的晶片的表面以形成涂覆有粘合剂/剥离层的晶片。然后将涂覆有粘合剂/剥离层的晶片与第二载体晶片结合以形成结合晶片系统。可以对结合晶片系统中第一晶片和第二载体晶片中的一者进行至少一次晶片加工操作(如晶片磨削等)以形成经过加工的晶片系统。然后可通过引发剥离层和粘合剂之间的分离来剥离经过加工的晶片系统,从而获得经过加工的薄晶片。最后,使用能够溶解剥离层或其任何残留物的有机溶剂对经过加工的薄晶片的表面进行清洗。根据本发明的另一个方面,该方法包括如下步骤:将剥离层施涂于第一晶片与第二晶片的表面以形成涂覆有剥离层的第一晶片和涂覆有剥离层的第二晶片。将粘合剂施涂于涂覆有剥离层的第一晶片或涂覆有剥离层的第二晶片中的至少一者的表面,以形成涂覆有粘合剂/剥离层的晶片。然后将涂覆有粘合剂/剥离层的晶片与剩下的涂覆有剥离层的晶片结合以形成结合晶片系统。可以对第一晶片和第二载体晶片中的一者进行至少一次晶片加工操作(如晶片磨削等)以形成经过加工的晶片系统。可通过引发剥离层中的一层和粘合剂之间的分离来剥离经过加工的晶片系统,从而获得经过加工的薄晶片。如果在粘合剂与邻近经过加工的薄晶片的剥离层之间发生分离,可使用能够溶解剥离层或其任何残留物的有机溶剂对经过加工的薄晶片的表面进行清洗。如果在粘合剂与邻近载体晶片的剥离层之间发生分离,那么在清洗经过加工的晶片的表面之前,可采用剥落或本领域内技术人员所知的任何其他机械手段将粘合剂层从邻近经过加工的晶片的剥离层除去。剥离层包含倍半硅氧烷基树脂或热塑性树脂,且能够承受暴露于最高约180℃而不发生大量交联。粘合剂为聚硅氧烷基组合物,其包含乙烯基官能化低聚树脂、Si-H官能化低聚树脂、催化剂和任选的抑制剂。剥离层与粘合剂不混溶。该方法还可包括如下步骤:在约90℃至约110℃之间的温度下预焙烧涂覆有粘合剂的晶片。根据本发明的另一个方面,提供了一种结合系统,该系统可用于暂时性地将载体晶片结合到半导体晶片上以有利于晶片加工操作。该结合系统一般包括第一晶片和第二晶片;施涂于第一晶片表面的剥离层,其中剥离层能够溶解于有机溶剂中;以及施涂于第二晶片表面的粘合剂。尽管粘合剂与剥离层不混溶,但粘合剂与剥离层能够暂时性结合到一起,然后剥离。结合系统中的粘合剂包含乙烯基官能化的低聚树脂、Si-H官能化的低聚树脂和催化剂。乙烯基官能化的树脂包含根据式E(C1)a(C2)b(C3)cE的三种硅氧烷组分C1、C2和C3中的至少一种,其中E代表封端基团,并且a、b和c表示树脂中每种组分的摩尔百分比,且a处于约0.025至1.0之间的范围内;b大于0.0,最多至约0.95,或者b可以为0.0;并且c大于0.0,最多至约0.60,或者c可以为0.0。乙烯基官能化树脂中的封端基团E和硅氧烷组分C1、C2和C3进一步通过下式限定:其中R1、R2、R3、R4、R5、R15和R16为独立选择的有机基团,并且R2、R3、R4、R15和R16中的至少一者为包括乙烯基官能团的脂族或芳族基团;R6为氢原子或具有1至4个碳原子的烃基;下标v处于0至1的范围内,而下标u处于0至2的范围内;并且每种组分的聚合度m、n和o预定为整数,其经选择使得相应的组分表现出足以在粘合剂组合物中发挥功能所需的性质。或者,选择的R2、R3、R4、R15和R16基团中的至少一者为氟化部分。本领域的技术人员应当理解,组分C3在需要时可为官能化的二氧化硅粒子。Si-H官能化树脂由下式限定:其中下标v处于0至1的范围内,下标u处于0至2的范围内,且下标z处于0至1的范围内;并且R1、R2、R3、R7、R8、R9和R10为有机基团,其可任选地包括氟化官能团,且当(u+v+z)之和为0时,R9、R10和R11中的至少一者为氢原子。聚合度p预定为整数,其经选择使得Si-H官能化树脂表现出足以在粘合剂组合物中发挥功能所需的性质。催化剂可以为能够促进硅氢加成反应的任何热活化或光活化催化剂。结合系统中的剥离层包含热塑性树脂或具有根据式(U1)d(U2)e(U3)f的三种硅氧烷单元中的至少一者的树脂,其中d、e和f表示树脂中每种组分的摩尔百分比,且d处于约0.025至1.0之间的范围内;e大于0.0,最多至约0.95,或者e为0.0;并且f大于0.0,最多至约0.30,或者f为0.0。树脂中的单元U1、U2和U3由下式限定:其中R11、R13和R14为有机基团;R12为选择为氢原子或含有1至4个碳原子之间的烃基中一种的基团;x值为0、1或2;并且每个单元的聚合度值q、r和s预定为整数,其经选择使得相应的单元表现出足以在剥离层中发挥功能所需的性质。结合系统中的催化剂为选自下列的一种:氯铂酸、由氯铂酸或二氯化铂与脂族不饱和有机硅化合物反应得到的含铂催化剂、铂(0)-1,3-二乙烯基-1,1,3,3-四甲基二硅氧烷复合物、乙酰丙酮铂以及硅氢加成反应所用的任何其他过渡金属催化剂。根据本发明的另一个方面,结合系统中的粘合剂还可包含抑制剂,所述抑制剂能够与催化剂发生相互作用以延缓催化反应的引发。抑制剂可选择为下列组中一种:马来酸二烯丙酯、乙炔基环己醇、双-2-甲氧基-1-甲基乙基马来酸酯和N,N,N’,N’-四甲基乙二胺。根据本文所提供的说明书,更多适用领域将变得显而易见的。应当理解,说明书和具体实例仅旨在用于举例说明目的,而不旨在限制本发明的范围。附图说明本文所述的附图仅用于举例说明目的,而不旨在以任何方式限制本发明的范围。图1为根据本发明的一个方面的结合系统和用于处理半导体晶片表面以提高后续加工操作过程中晶片的处理的方法的示意图;图2为根据本发明的另一个方面的结合系统和用于处理半导体晶片表面以提高后续加工操作过程中晶片的处理的方法的示意图;以及图3为根据本发明的又一个方面的结合系统和用于处理半导体晶片表面以提高后续加工操作过程中晶片的处理的方法的示意图。具体实施方式下列说明实质上仅为示例性的,绝非旨在限制本发明或其应用或用途。应当理解,在整个说明和附图中,相应的参考数字指示类似或相应的部件或特征。本发明总体上提供了处理用于生产半导体产品的晶片的材料和工艺。更具体地讲,本发明涉及粘合剂和剥离层组合物的制备及在用作结合系统一部分时其在形成暂时性结合的用途。暂时性粘合剂组合物为有机硅基热固性材料,并且剥离层组合物为倍半硅氧烷基材料或热塑性材料。有机硅基粘合剂和倍半硅氧烷基或热塑性基剥离层可通过使用常规涂覆技术(例如,旋涂、喷涂、流涂等)施涂于半导体晶片或载体晶片的表面。引发粘合剂与剥离层之间的暂时性粘合,以有利于通过后续的晶片磨削、TSV或其他加工步骤对半导体晶片进行处理。完成所需的加工之后,可通过粘合剂与剥离层之间发生剥离,使半导体晶片与载体晶片分离开来。就使用倍半硅氧烷基剥离层而言,该剥离步骤涉及将倍半硅氧烷材料溶解于有机溶剂中。使用本发明的教导内容的结合工艺等等的一个例子涉及将暂时性粘合剂涂覆到载体晶片上,然后在预定温度下对被涂覆晶片进行预焙烧,该温度低于粘合剂组合物的固化温度。将倍半硅氧烷基或热塑性基剥离材料涂覆到半导体晶片的图案化表面上。随后,通过在一定温度下焙烧足以固化粘合剂的时长使得两种晶片结合到一起。完成任何所需的加工步骤(如晶片磨削、TSV等)之后,可通过引发剥离层与粘合剂之间的分离使结合晶片剥离。还可将剥离层暴露于能够溶解剥离层的有机溶剂中对晶片进行清洗。本发明的结合和剥离工艺以及粘合剂和剥离层的组合物在用于制造结合薄晶片技术的半导体器件时提供多个优势。粘合剂和剥离层的组合物,使用常规技术将粘合剂和剥离层涂覆到晶片上的能力,使用热活化或紫外线活化固化的简单结合工艺,简单机械剥离工艺,以及将晶片表面暴露于有机溶剂的清洗过程,实现了总体更低的制造成本和停机时间,以及提高的工艺通量、收率和生产率。根据本发明的一个方面,提供了一种结合系统,该系统可用于暂时性地将载体晶片结合到半导体晶片上以有利于晶片加工操作。该结合系统一般包括第一晶片和第二晶片;与第一晶片表面相邻位置处的剥离层;以及与第二晶片表面相邻位置处的有机硅基粘合剂,使得这些剥离层与粘合剂被夹在两个晶片之间。粘合剂与剥离层能够暂时性结合到一起并剥离。尽管剥离层可溶于有机溶剂中,但剥离层与粘合剂彼此不混溶。根据本发明的另一个方面,结合系统可包括第一晶片和第二晶片;与第一晶片相邻位置处的剥离层;以及与第二晶片相邻位置处的第二剥离层;剥离层可溶于有机溶剂中。有机硅基粘合剂位于剥离层之间;粘合剂与剥离层不混溶。粘合剂与剥离层能够暂时性结合到一起并剥离。有机硅基粘合剂一般包含乙烯基官能化的聚硅氧烷低聚树脂、Si-H官能化的聚硅氧烷低聚树脂和催化剂。催化剂可为热活化的或紫外线活化的。任选地,有机硅基粘合剂还可包含抑制剂,该抑制剂可与催化剂相互作用,以延缓催化反应的引发。根据需要,粘合剂可分散于溶剂中以便控制施涂到晶片表面的粘合剂层的厚度。可使用的典型溶剂包括本领域中技术人员已知的可溶解聚二甲基硅氧烷的任何溶剂,包括但不限于二硅氧烷和三硅氧烷溶剂以及脂族或芳族溶剂。乙烯基官能化聚硅氧烷低聚树脂包含根据式E(C1)a(C2)b(C3)cE所述的三种硅氧烷组分C1、C2和C3中的至少一种,其中E表示封端基团,并且a、b和c表示树脂中每种组分的摩尔百分比。a值可处于约0.025至1.0的范围内;b值可大于0.0,最多至约0.95,或者b值可以为0.0;并且c值可大于0.0,最多至约0.60,或者c值可以为0.0。乙烯基官能化树脂中的封端基团E和硅氧烷组分C1、C2和C3进一步通过下式限定:其中每个R1、R2、R3、R4、R15和R16表示独立地选择为下列中一种的有机基团:甲基、乙基、丙基、己基、环己基、苯基、乙烯基、己烯基、甲基丙烯酰氧基丙基、丙烯酰氧基丙基以及任何其他有机基团,所述任何其他有机基团任选地包括具有1至8个碳原子的氟化部分。然而,R2、R3、R4、R15和R16中的至少一者为包括乙烯基官能团的脂族或芳族基团。或者,R2、R3、R4、R15和R16中的至少一者为氟化部分。氟化部分的若干例子包括但不限于三氟丙基、五氟丁基和九氟己基等等。在组分C1中,下标v为0与1之间范围的任何数字,而下标u为0与2之间范围的任何数字。在组分C2和C3中,下标x具有0、1或2的值。下标u和v用于描述组分C1主链中存在的(R2R3SiO2/2)与(R1R1SiO2/2)部分之间的比率。或者下标u和v可用关系式0≤(u+v)≤3来描述。R5表示有机基团,例如甲基、乙基、乙烯基、苯基或者另一个具有1至12个碳的脂族或芳族基团或它们的组合。R6表示氢原子或具有1至4个碳原子的烃基。每种组分的聚合度m、n和o的值预定为整数且m大于零,并且每个整数经选择使得组分C1、C2和C3表现出足以在根据本发明教导内容的粘合剂组合物中发挥功能所需的性质。在本发明的某些实施例中,组分C2和C3中至少一者表现出聚合度n和/或o具有大于零的值。Si-H官能化聚硅氧烷低聚树脂(SiHR)还可由以下示出的式限定,其中下标v为0与1之间范围的任何数字,下标u为0与2之间范围的任何数字,并且下标z为0与1之间范围的任何数字。下标u、v和z用于描述聚硅氧烷低聚树脂主链中存在的(HR7SiO2/2)(R2R3SiO2/2)与(R1R1SiO2/2)部分之间的比率。或者下标u、v和z可用关系式0≤u≤2、0≤v≤1和0≤z≤1来描述。R1为如上所述的有机基团。R2、R3和R7表示独立地选择为下列中一种的有机基团:氢原子、甲基、乙基、丙基、己基、环己基、苯基以及其他不含乙烯基的、包含具有1至8个碳原子的氟化部分的有机基团。或者,R2、R3和R7中的至少一者为氟化部分。R8、R9和R10表示独立地选择为下列中一种的有机基团:氢原子、甲基、乙基、丙基、己基、环己基、苯基以及其他不含乙烯基的、包含具有1至8个碳原子的氟化部分的有机基团,并且当下标u+v+z之和为0时,R8、R9和R10基团中的至少一者包含氢原子(即,Si-H键)。聚合度p值预定为非零整数,其经选择使得Si-H官能化低聚树脂表现出足以在根据本发明教导内容的粘合剂组合物中发挥功能所需的性质。粘合剂中存在的乙烯基官能化和Si-H官能化聚硅氧烷低聚树脂的量可根据配方中存在的乙烯基官能化树脂与Si-H官能化树脂的摩尔比来限定。通常,粘合剂中存在的乙烯基:Si-H树脂的摩尔比处于约0.1至约4.0之间,或者根据需要使用约0.5至约2.5的比率。热活化或紫外线活化催化剂可包括本领域中技术人员已知的可用于催化硅氢加成反应的任何催化剂。催化剂可以为包含过渡金属族的催化剂。按照定义,过渡金属包括但不限于钌、铑、钯、锇、铱和铂金属以及它们的任何混合物或复合物。过渡金属催化剂可包括实心或中空颗粒,沉积到载体(例如硅胶或粉末木炭)上的金属层,或者含过渡金属的有机金属化合物或复合物。含过渡金属的催化剂的若干例子包括六水合物形态或无水形态的氯铂酸、由氯铂酸或二氯化铂与脂族不饱和有机硅化合物反应得到的含铂催化剂、铂(0)-1,3-二乙烯基-1,1,3,3-四甲基二硅氧烷复合物以及乙酰丙酮铂。粘合剂中所用的催化剂的合适量根据使用的具体催化剂的选择进行预定。铂催化剂以足够的量存在以在粘合剂中提供至少2份每一百万份(ppm)的铂。或者,粘合剂中存在的催化剂的量接近约5ppm至约2000ppm。可将催化剂作为单一催化剂物质或作为两种或更多种不同物质的混合物添加。抑制剂可以为本领域中技术人员已知的能够抑制催化剂活性的任何材料。换句话讲,抑制剂为妨碍或阻止催化剂发挥催化剂功能的材料。根据本发明的一个方面,抑制剂可以在室温下阻碍催化剂活性,但在高温下将不会干扰催化剂的性质。抑制剂可包括但不限于烯键式或芳族不饱和酰胺、乙炔化合物、甲硅烷基化乙炔化合物、烯键式不饱和异氰酸酯、烯属硅氧烷、不饱和烃单酯和二酯、氢过氧化物、腈和二氮丙啶。抑制剂的多个例子中的若干具体例子包括马来酸二烯丙酯、乙炔基环己醇、双-2-甲氧基-1-甲基乙基马来酸酯和N,N,N’,N’-四甲基乙二胺。一般来讲,抑制剂将被添加到粘合剂中,使得催化剂:抑制剂的摩尔比在约1至约200之间,或者根据需要使用约7至约11的比率。根据本发明的另一个方面,剥离层作为结合系统的一部分提供,其中该层由选自倍半硅氧烷基树脂和热塑性材料中的一种形成。包含热塑性材料的剥离层组合物的若干例子包括聚砜、聚酰亚胺和聚醚酮等等,其能够溶解于常见的溶剂例如N-甲基吡咯烷酮和N,N-二甲基乙酰胺中。包含倍半硅氧烷基树脂的剥离层组合物包含根据式(U1)id(U2)e(U3)f所述的三个硅氧烷单元U1、U2和U3中的至少一者,其中d、e和f表示树脂中每种组分的摩尔百分比。d值可处于约0.025至1.0的范围内;e值大于0.0,最多至约0.95,或者e为0.0;并且f大于0.0,最多至约0.30,或者f为0.0。剥离涂层树脂中的单元U1、U2和U3由下式限定:其中R11表示选择为下列中一种的有机基团:氢原子、甲基、乙基、丙基、苯基、三氟甲基、任何其他含有1至20个碳原子的有机基团(包括氟化有机基团)以及它们的任何组合。R12表示选择为氢原子或含有1至4个碳原子之间的烃基中一种的基团。R13和R14表示独立地选择为下列中一种的有机基团:氢原子、甲基、乙基、丙基、己基、环己基、苯基、乙烯基、己烯基、甲基丙烯酰氧基丙基、丙烯酰氧基丙基以及任何其他有机基团,所述任何其他有机基团包括具有1至8个碳原子的氟化部分。x的值可以为0、1或2,而每个单元的聚合度q、r和s值预定为整数,其中q大于零并且每个整数经选择使得硅氧烷单元U1、U2和U3表现出足以在根据本发明教导内容的剥离层中发挥功能所需的性质。在本发明的某些实施例中,单元U2和U3中的至少一者表现出聚合度r和/或s具有大于零的值。根据本发明的另一个方面,如图1所示提供了方法100A,该方法包括使用粘合剂和剥离层在第一与第二晶片之间提供暂时性结合以便于执行至少一次加工操作从而形成经过加工的晶片,剥离晶片以及随后清洗经过加工的晶片。该方法一般包括在步骤101中提供第一晶片5和第二晶片20以进行后续涂覆。在步骤105中将剥离层10涂覆到第一晶片5的表面上以形成涂覆有剥离层的晶片25。在步骤105中可使用本领域中的技术人员已知的常规技术(包括但不限于旋涂、喷涂、流涂等)涂覆剥离层10。相似地,在步骤110中可使用常规技术将粘合剂15涂覆到第二晶片20的表面上,以形成涂覆有粘合剂的晶片30。本领域中的技术人员应当理解,第一晶片5和第二晶片20可选择为下列组中的一种:载体晶片或可在其上进行后续加工的晶片例如图案化晶片。第一晶片5和第二晶片20彼此不同。涂覆有粘合剂的晶片30可在约70至约140℃范围的温度下进行预焙烧以热固化粘合剂。或者可根据需要使用90至110℃的温度范围。涂覆有剥离层的晶片25可在约80至约140℃范围的温度下进行预焙烧,或者根据需要使用约100至约120℃的温度范围。然后在步骤115中将粘合剂放置在与剥离层接触的位置,使涂覆有粘合剂的晶片30与涂覆有剥离层的晶片25结合到一起,从而形成结合晶片系统35。被涂覆的晶片25、30可通过如下方式结合:在真空烘箱内在预定的减压和温度水平下或者当粘合剂中的催化剂为热活化的时在常规烘箱内在较高温度下进行固化。如果粘合剂中的催化剂为光活化的,则被涂覆的晶片25、30可在暴露于紫外线(UV)辐射后结合并且可在暴露于高温下后进行进一步固化。在这种情况下,晶片中的至少一者为玻璃晶片或透过紫外线的晶片以便紫外固化粘合剂。在结合晶片系统35中,载体晶片对图案化晶片提供了必要的支撑,以便于进行后续操作或加工,例如晶片磨削等等。继续参见图1,对图案化晶片进行晶片加工120以形成经过加工的晶片系统40,仅出于举例说明目的将该图案化晶片标识为第一晶片5。一旦图案化晶片被加工为非常薄的晶片,就可任选地根据需要对经过加工的晶片系统40进行另外的加工125,例如穿透硅通孔(TSV)。在步骤130中,可使用尖刀(例如剃刀刀片)在剥离层10与粘合剂15之间的界面边缘开出缺口,使经过加工的晶片系统40机械剥离。将剥离层从粘合剂分离,从而形成经过加工的薄晶片45。在结合晶片系统35中,使用粘合剂层15支撑图案化晶片。在磨削及任何后续加工完成之时剥离层10用于促进经过加工的晶片系统40的剥离。任选地,为在剥离和清洗之后处理并使用经过加工的薄晶片45,在步骤135中可以将经过加工的晶片45的背侧面层压或永久性结合到切割带50上。经过加工的晶片45的背侧面定义为未与剥离层10或粘合剂15相接触的晶片侧面。可以在将经过加工的晶片系统40暴露于剥离130和清洗140步骤之前,进行层压或结合到切割带50上。然后在步骤140中可将经过加工的晶片45暴露于有机溶剂中,该有机溶剂将充当表面清洁剂。可通过将溶剂喷洒到晶片上或通过将晶片浸泡于可溶解剥离层的有机溶剂中,将剥离层10或其任何残留物从经过加工的晶片45上除去。有机溶剂还清洗其上涂覆有剥离层的晶片10的表面。可采用任何有机溶剂清洗经过加工的晶片45,前提条件是该溶剂能够溶解剥离层10并可满足任何必要的法规要求。有机溶剂的若干例子包括但不限于甲苯、二甲苯、均三甲苯、丙二醇甲醚醋酸酯(PGMEA)和乙酸丁酯。本领域中的技术人员应当理解,方法100A可进行修改,以允许在结合到第二未经涂覆的晶片或另一个涂覆有剥离层的晶片之前,将粘合剂施涂于涂覆有剥离层的晶片上,如图2和图3所示。现在参见图2,以方法100B的形式展示了方法100A(见图1)的此类变型。方法100B与方法100A的差别在于,在步骤111中将粘合剂15施涂于第一晶片5上的剥离层10的表面,形成涂覆有粘合剂/剥离层的晶片31。然后在步骤116中将第二晶片20与涂覆有粘合剂/剥离层的晶片31结合在一起以形成结合晶片系统35。可按照与方法100A中先前所述类似的方式对结合晶片系统35进行后续加工120、剥离120和清洗140步骤,以及任选包括与步骤125中执行其他加工操作及将经过加工的晶片层压/结合到切割带上相关的步骤。现在参见图3,以方法100C的形式提供了方法100B的变型的例子。该方法一般包括在步骤101中提供第一晶片5和第二晶片20;晶片5、20未经涂覆。在步骤105中将剥离层10涂覆到第一晶片5,并在步骤106中将第二剥离层10涂覆到第二晶片20上,形成两个涂覆有剥离层的晶片25、26。然后在步骤111中将粘合剂15施涂于涂覆有剥离层的晶片25、26中的一者上,形成涂覆有粘合剂/剥离层的晶片31、32。在步骤117中,将涂覆有粘合剂/剥离层的晶片31、32暂时性结合到剩余的涂覆有剥离层的晶片25、26上,形成结合晶片系统36。在步骤120中,可对结合晶片系统36中的晶片5、20中的一者进行晶片加工操作例如磨削以形成经过加工的晶片系统41。仍参见图3,完成该经晶片加工120和任何后续可选的加工(例如在步骤125中执行额外的加工(即TSV)和将经过加工的晶片系统41层压/结合到切割带上)之后,可在步骤130中通过将剥离层10中的一层从粘合剂15分离,使晶片5、20剥离。在步骤140中可将经过加工的晶片45暴露于有机溶剂中,该有机溶剂将充当表面清洁剂。可通过将溶剂喷洒到晶片上或通过将晶片浸泡于可溶解剥离层的有机溶剂中,将剥离层10或其任何残留物从经过加工的晶片45上除去。本领域中的技术人员应当理解,如果将粘合剂15从邻近载体晶片的剥离层分离(如图3所示),可在执行溶剂清洗140之前在步骤137中将粘合剂从邻近经过加工的晶片45的剥离层机械去除。给出了下列具体实例来说明本发明,并且不应将其理解为限制本发明的范围。本领域的技术人员根据本发明应当理解,可以在不背离或超出本发明的精神和范围的情况下,在本文所公开的具体实施例中做出许多改变且仍获得相同或类似的结果。实例1–用催化剂制备Si-H官能化树脂该实例说明了根据本发明的教导内容的Si-H官能化聚硅氧烷低聚树脂的制备,其中还分散了催化剂。将总共244毫克的N,N,N’,N’-四甲基乙二胺与硅氧烷溶剂中的87毫克铂(0)-1,3-二乙烯基-1,1,3,3-四甲基二硅氧烷复合物溶液(22毫克Pt)在室温下混合一小时。然后,向上述铂催化剂溶液中加入130.35克聚甲基氢硅氧烷-共-聚二甲基硅氧烷共聚物(F1-3546聚合物,密歇根州米德兰的道康宁公司(DowCorningCompany(Midland,MI))和79.8克另一种聚甲基氢硅氧烷-共-聚二甲基硅氧烷共聚物(6-3570聚合物,道康宁公司(DowCorningCorp.))。将混合物在室温下搅拌24小时。实例2–粘合剂组合物的制备该实例说明了根据本发明的教导内容的粘合剂组合物的制备。将总共16.30克保存的实例1的混合物加入到配有机械搅拌轴和氮气入口/出口的250ml三颈圆底烧瓶中。然后向烧瓶中缓慢加入100克乙烯基封端的聚二甲基硅氧烷低聚物(SFD-119,道康宁公司(DowCorningCorporation))与乙烯基官能化二氧化硅(6-3444,道康宁公司(DowCorningCorporation))的混合物,同时进行搅拌。对混合物搅拌2小时,然后将其转移到塑料瓶中供将来使用。实例3–粘合剂组合物的第二制备该实例说明了根据本发明的教导内容的第二粘合剂组合物的制备。将总共2.314克保存的实例1的混合物加入到配有机械搅拌轴和氮气入口/出口的250ml三颈圆底烧瓶中。然后向烧瓶中缓慢加入100克乙烯基封端的聚二甲基硅氧烷低聚物(SFD-120,道康宁公司(DowCorningCorporation)),同时进行搅拌。对混合物搅拌2小时,然后将其转移到塑料瓶中供将来使用。实例4–甲基倍半硅氧烷剥离层的制备该实例说明了根据本发明的教导内容的倍半硅氧烷基剥离层的制备。将总共316克浓HCl(HCl:H2O的摩尔比为3.12mol/11.2mol)、689克甲苯和2克辛基硫酸钠加入到配有机械搅拌轴、冷凝器以及氮气入口和出口的3L夹套圆底烧瓶中,形成含水HCl/甲苯悬浮液。在600rpm下对含水HCl/甲苯悬浮液进行搅拌,使辛基硫酸钠表面活性剂溶解,同时使反应温度保持在20℃。以每分钟1.46克的速率将总共200克甲苯(2.17mol)和149.5克甲基三氯硅烷(1.0mol)一起加入到另一个圆底烧瓶中。在氮气气氛下,在4小时的时间内将甲基三氯硅烷/甲苯溶液加入到HCl/甲苯悬浮液中。然后,停止机械搅拌,以允许相分离发生。约2分钟内发生相分离。包含粗制甲基倍半硅氧烷相的上层有机甲苯层与下层浓HCl层分离开。移去HCl层。在300rpm的搅拌速率下使用200ml去离子水对有机甲苯层清洗1分钟。停止机械搅拌5分钟,并移去包含残留HCl和表面活性剂的水层。重复该清洗过程5次,直至洗后的水pH值为约4。随后,将80克(1.7摩尔)乙醇添加至有机甲苯层中同时进行搅拌,使该层变澄清。对溶液搅拌约5分钟。最后,将半透明溶液转移至梨形烧瓶中,并使用旋转蒸发仪在40℃下将甲苯溶剂、乙醇和残留HCl汽提馏出,仅剩下粗制甲基倍半硅氧烷树脂。进一步使粗制树脂真空干燥过夜。然后将粗制树脂以约7重量%溶解于乙酸丁酯中,过滤并保存供将来使用。实例5–苯基倍半硅氧烷剥离层的制备该实例说明了根据本发明的教导内容的另一种倍半硅氧烷基剥离层的制备。将总共503.4克(2.54摩尔)苯基三甲氧基硅烷和0.36克三氟甲磺酸(三氟利克酸)加入到配有机械搅拌轴、温度计、迪安-斯塔克分离器、冷凝器以及氮气入口和出口的1升三颈圆底烧瓶中。在200rpm下对混合物进行搅拌时,将总共137.2g(7.62摩尔)水在15分钟内缓慢加入,确保反应混合物温度不超过50℃。然后,在75℃下对反应混合物回流90分钟。通过迪安-斯塔克分离器除去甲醇和一些水。在温度升至80℃后,除去约233克液体。随后,将反应混合物冷却至约60℃,并单独加入317克甲苯和1.54克50重量%的KOH水溶液。对反应混合物进行回流,通过迪安-斯塔克分离器除去水。在温度升至113℃后,除去约300克液体。对混合物再回流2小时后,将反应混合物冷却至90℃,并向混合物中加入0.83克乙酸。然后对反应混合物再冷却30分钟,通过玻璃纤维/布氏漏斗对形成的盐进行过滤,以分离和收集盐。然后使用旋转蒸发仪除去溶剂,收集到剥离层树脂。树脂的分子量为约12,600kg/mol,其重均分子量与数均分子量之比(Mw:Mn)的测定值为约3.08。将树脂以约10重量%溶解于乙酸丁酯中,过滤并保存供将来使用。实例6–晶片结合、剥离和清洗过程将实例2或实例3中制备的约5ml粘合剂放到4"清洁硅晶片的表面,该硅晶片布置在Karl-Suss旋涂仪上。根据涂覆涂层所用的旋转速率不同,所得涂层的厚度可处于约30至约100微米之间的范围内。晶片在90℃下预焙烧约1分钟。将实例4或实例5中制备的约2ml剥离层树脂放到4"清洁硅或玻璃晶片的表面,该硅或玻璃晶片布置在Karl-Suss旋涂仪上。根据涂覆涂层所用的旋转速率不同,所得涂层的厚度可处于约150至约300纳米之间的范围内。晶片在110℃下预焙烧约1分钟。在约50毫巴的真空下,将涂覆有粘合剂的晶片结合到涂覆有剥离涂层的晶片上。然后将结合晶片置于烘箱中,并在130至150℃下焙烧约2分钟。根据加工要求不同,可以在约150℃至约250℃范围的多种温度下对晶片进一步处理1小时,以形成结合晶片系统。实例7–在剥离和清洗方面对结合晶片系统进行测试对实例6的方法独立执行十次,以形成根据本发明教导内容的结合晶片系统(运行编号1-10)。通过将剃刀刀片插入到晶片中引起剥离,对每种结合晶片系统进行剥离测试。完成剥离后,使用乙酸丁酯或丙二醇甲醚乙酸酯(PGMEA)清洗晶片,对涂覆有剥离层树脂的晶片进行溶剂溶解度测试。在运行编号1-10中用于形成结合晶片系统的工艺参数以及所进行的剥离和溶解度测试的结果提供于表1中。该实例说明了根据本发明教导内容制备的结合晶片系统可通过本文所述的简单机械方法剥离(运行编号1、3和5-9)。剥离后,可将晶片表面暴露于有机溶剂中对晶片表面进行清洗(运行编号1、3、5-9)。结合后温度应当保持足够低,以防止剥离层和粘合剂中发生大量固化和交联。例如,来自实例4的剥离层若与实例2的粘合剂(运行编号1-2)或与实例3的粘合剂(运行编号3-4)配合使用,则在结合后温度暴露为150℃时(运行编号1和3)成功剥离,但在结合后温度升至200℃时(运行编号2和4)不是如此。然而,当实例5的剥离层与实例2的粘合剂配合使用(运行编号5-7)时,结合晶片系统可在暴露于150℃(运行编号5)至250℃(运行编号7)之间的结合后温度之后剥离。表1所示的结果表明,若正确选择了粘合剂和剥离层,结合晶片可在经过薄晶片加工操作之后剥离。表1本领域中的技术人员应当认识到,所述的测量结果为标准测量结果,其可以通过多种不同的测试方法获得。实例中所述的测试方法仅代表获得各种所需测量结果的一种可用方法。本发明多个实施例的上述说明仅出于举例说明和描述目的而示出。并非意图详尽列举或将本发明限制在所公开的确切实施例。按照上述教导内容,许多修改形式或变型形式均是可行的。所论述的实施例被选择和描述成提供本发明及其实际应用所包含的原理的最佳例证,从而使本领域中的普通技术人员能够利用多个实施例中的本发明教导内容,并且可设想适用于特定应用的多种修改形式。当根据其公平、合法和公正享有的广度进行解释时,所有此类修改形式和变型形式均处于所附权利要求书所确定的本发明的范围内。