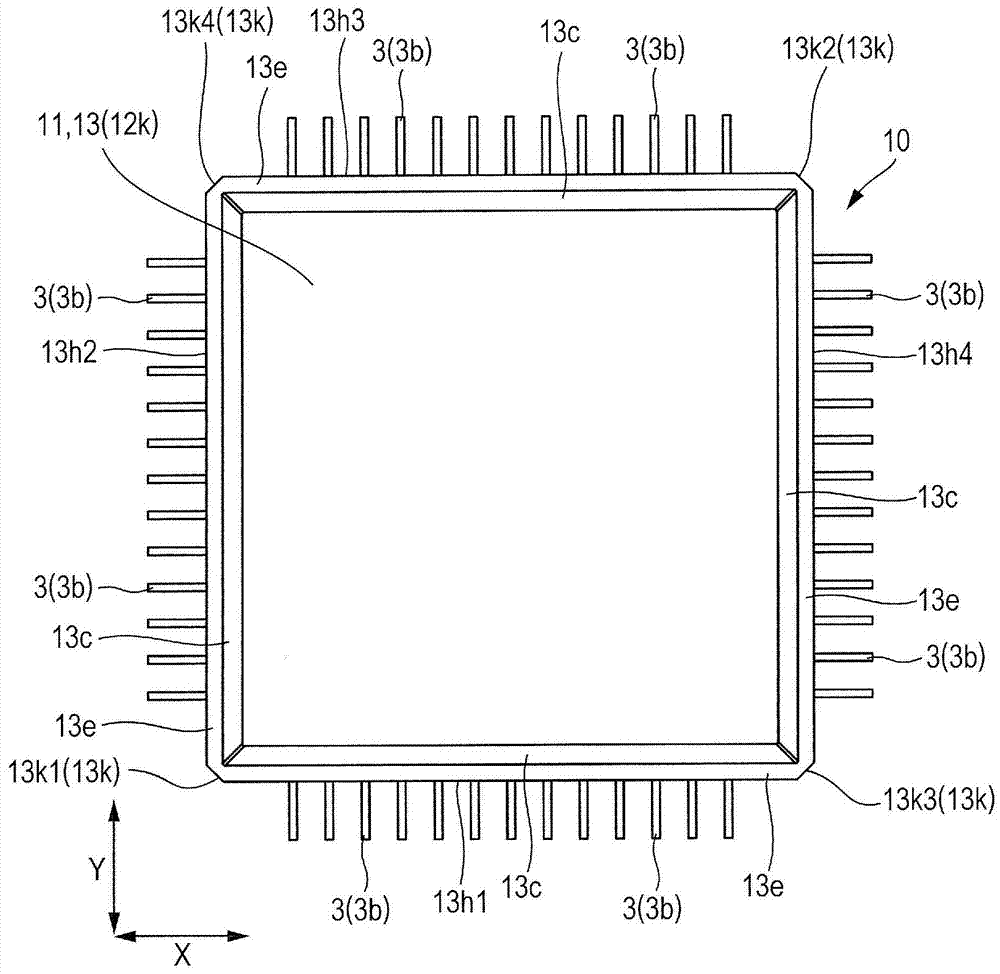
半导体器件的制造方法和半导体器件相关申请的交叉引用2012年3月2日提交的日本专利申请No.2012-046329的公开,包含说明书、附图和摘要,以其整体作为参考并入本文中。技术领域本发明涉及半导体器件及其制造技术,并且更具体地,涉及有效应用于具有利用由橡胶制成的密封体覆盖的半导体芯片的半导体器件的技术。
背景技术:日本未审查专利公布No.平4(1992)-157757(专利文献1)公开了:利用铝帽覆盖安装在印刷基板上的半导体器件,然后从帽的中心充入树脂。日本未审查专利公布No.2010-80931(专利文献2)公开了:电子组件布置在由热沉和盖形成的内部空间中,然后在内部空间中填充树脂。[相关技术文献][专利文献][专利文献1]日本未审查专利公布No.平4(1992)-157757[专利文献2]日本未审查专利公布No.2010-80931
技术实现要素:本申请的发明人研究了包括利用树脂密封的半导体芯片的所谓树脂密封半导体器件(半导体封装),并发现了如下问题。也就是,当树脂密封半导体器件暴露于高温气氛(例如,在约175至250℃的温度下)中时,由树脂制成的树脂密封体表面老化,这降低了半导体器件的可靠性。已经鉴于前述问题提出了在本申请中公开的发明的优选实施例,并且本发明的目的是提供一种用于提高半导体器件可靠性的技术。由本申请的描述和附图,本发明要解决的其它问题和本发明的新特征将变得更明显。下面将简要描述本申请中公开的本发明的典型实施例的概要。也就是,在根据本申请的一个方面的半导体器件制造方法中,在定位盖以便覆盖半导体芯片和导线之后,将树脂供应到由该盖形成的空间中,使得形成密封体,以覆盖半导体芯片和导线。在形成密封体的步骤中,在平面图中树脂是从盖的中心供应的。在根据本申请的另一方面的半导体器件的制造方法中,在形成用于密封半导体芯片和导线的密封体之后,布置盖以覆盖密封体。该盖包括第一盖部件和第二盖部件,该第二盖部件通过叠加在第一盖部件上方,形成用于在其中容纳密封体的空间。在平面图中,布置在第一盖部件和第二盖部件外围上的接合部分在其整个外围上被密封。如下将简要描述在本申请中公开的发明的典型实施例造成的效果。本申请中公开的本发明的典型实施例能够提高半导体器件的可靠性。附图说明图1是示出根据本发明的一个实施例的半导体器件的上表面的平面图;图2是示出图1中所示的半导体器件的下表面的平面图;图3是图1所示半导体器件的侧面图;图4是沿着图1的线A-A的截面图;图5是沿着图1的线B-B的截面图;图6是通过图1示出的半导体器件的上帽示出内部结构的透视平面图;图7是示出图6中所示结构的一部分的放大平面图;图8是示出图4或5中所示的帽的截面图;图9是沿着图6的线A-A的截面图;图10是示出图1中所示的半导体器件的组装流程图的说明图;图11是图10中示出的引线框设置步骤中设置的引线框的整个结构的平面图;图12是图11中示出的多个产品形成区中的一个和其周围的放大平面图;图13是沿着图12的线A-A的放大截面图;图14是示出在图12中所示的管芯垫上经由粘合剂安装的半导体芯片的状态的放大平面图;图15是沿着图14的线A-A的放大截面图;图16是示出在图14中示出的半导体芯片上经由粘合剂安装另一个半导体芯片的状态的放大平面图;图17是沿着图16的线A-A的放大截面图;图18是示出图16中示出的半导体芯片经由导线电连接到多个引脚的状态的平面图;图19是沿着图18的线A-A的放大截面图;图20是示出在图18所示的引脚上接合和固定帽的状态的放大平面图;图21是沿着图20的线A-A的放大截面图;图22是示出图20中所示的引线框的顶部和底部翻转的状态的放大平面图;图23是沿着图22的线A-A的放大截面图;图24是示出在图18所示的帽和引脚上涂覆密封剂的状态的放大平面图;图25是沿着图24的线A-A的放大截面图;图26是示出在安装表面侧上的帽经由图24中示出的密封剂接合并固定的状态的放大平面图;图27是沿着图26的线A-A的放大截面图;图28是沿着图26的线B-B的放大截面图;图29是示出密封体形成在图20中示出的引线框的产品形成区中的状态的放大平面图;图30是沿着图29的线A-A的放大截面图;图31是沿着图29的线B-B的截面图中所示的、示出将用于密封的树脂供应到由帽形成的空间的状态的放大截面图;图32是示出切割图29中示出外引脚以使产片形成区成形的状态的放大平面图;图33是示出将图32中所示的产品形成区与引线框的框架部分分离并形成为单体的状态的放大平面图;图34是示出作为图2的修改实例的半导体器件的下表面的平面图;图35是作为图4的修改实例的半导体器件的截面图;图36是作为图5的修改实例的半导体器件的截面图;图37是作为图6的修改实例的半导体器件的透视平面图;图38是示出作为图10的修改实例的半导体器件的组装流程图的说明图;图39是示出作为图12的修改实例的引线框的放大平面图;图40是示出作为图13的修改实例的引线框的放大截面图;图41是示出图27的修改实例的放大截面图;图42是示出作为图10的另一个修改实例的半导体器件的组装流程图的说明图;图43是作为图4的另一个修改实例的半导体器件的截面图;图44是作为图5的另一个修改实例的半导体器件的截面图;图45是作为图43的修改实例的半导体器件的截面图;图46是示出在图42所示的密封主体形成步骤中在图18中示出的引线框上形成密封剂的状态的放大平面图;图47是示出图1的修改实例的平面图;和图48是示出图31的修改实例的放大截面图。具体实施方式(本申请中的描述格式、基本术语和用法的说明)在本申请中,在下面,如果需要,为了方便,通过分成多个章节等来描述下面的优选实施例,除非另行规定,这些章节不是相互独立的。不管这些章节的描述顺序,这些章节指示单个实例中的各个部分。替代地,这些章节中的一个可以是其它章节的一部分的细节,或者是其它章节的一部分或全部的修改实例。原则上,具有相同功能的部分将不再重复描述。除了当在原理上限制组件的数目时之外,以及除了当根据上下文认为绝对不是这样时之外,除非另外指定,优选实施例的各个组件都不是必需的。同样,在实施例的描述中,除非另外指定,以及除了从上下文认为绝对不是这样时之外,关于材料、成分等的术语“由A形成X”等,并不排除除了元素“A”之外的元素。例如,对于成分,上述术语的意思是“X包含A作为主要成分”。例如,术语“硅部件”并不限于纯硅,并且显然可以包括SiGe(硅-锗)合金、或者包含硅作为主要成分的多种成分的合金,以及另外的添加物。除非另外指定,术语“金镀层”、“铜层”或“镍镀层”并不限于纯的,而包括包含金、铜或镍作为主要成分的部件。除了当在理论上限定为该特定数值时,并且除了当从上下文认为绝对不是这样时之外,除非另外指定,即使当涉及特定数值或数量时,元件的数目等可以大于或小于该特定数值。在实施例的每个图中,相同或相似的部分用相同或相似的附图标记或数字指示,并且原则上将不再重复它们的描述。在附图中,在如果剖面线可能使截面图复杂或者当容易区分空腔或孔时的一些情况下,即使截面图也可以省略剖面线。在该上下文中,当通过描述等看起来清晰时,关于背景可以省略以平面方式封闭的孔的轮廓线。此外,为了表示不是腔或孔的部分,或者为了清楚表示区域之间的边界,即使当图不是截面图时,有时也会给出阴影线或点图案。第一实施例<半导体器件的结构>首先,下面将描述本实施例中的半导体器件的结构。图1示出了本实施例中的半导体器件的上表面的平面图。图2示出图1中所示半导体器件的下表面的平面图。图3是图1中所示的半导体器件的侧面图。图4是沿着图1的线A-A的截面图。图5是沿着图1的线B-B的截面图。图6是通过图1中所示的半导体器件的上帽示出内部结构的透视平面图。图7示出了图6中所示结构的一部分的放大平面图。图8示出了图4或5中所示的结构的截面图。图9是沿着图6的线A-A的截面图。本实施例的半导体器件10是引线框型半导体封装,具有安装在用作基座的引线框的芯片安装部件上方的半导体芯片。在本实施例中,如图1和2所示,将通过引线框型半导体器件的实例来描述四方扁平封装(QFP)半导体器件10。在平面图中半导体器件10的封装具有四方形外观,并且具有布置在其四边上的多个引脚。<外观>首先,下面将描述半导体器件10的外观。图1中所示的在上表面侧上的上帽(盖)12具有外表面(上表面)12a和围绕外表面12a布置的侧面12c,由此在平面图中具有四角形(四边形)。上帽12在其外围处包括将要在后面描述的四个边(四个主边)。也就是,上帽12包括在X方向上延伸的边(主边)12h1、在Y方向上延伸且与边12h1相交(垂直)的边(主边)12h2、与边12h1相对的边(主边)12h3和与边(主边)12h2相对的边12h4。上帽12具有四个角12k,其定位在边12h1、12h2、12h3和12h4的相邻边彼此相交的区域中。具体地,上帽12具有定位在边12h1与边12h2相交的区域中的角12k1。上帽12具有定位在边12h3与边12h4相交的区域中的角12k2。上帽12具有定位在边12h1与边12h4相交的区域中的角12k3。上帽12具有定位在边12h2与边12h3相交的区域中的角12k4。上帽12的角12k中的每一个覆盖上帽12的四个边(四个主边)中两个任意相交边(两个主边)的交叉点和它们的周围。确切地,如图1所示,上帽12的每个角12k的一部分被削角,由此两个主边的交叉定位在上帽12的相应角12k的外部。然而,削角部分与主边的长度相比足够小。在本申请中,削角部分的中心认为是描述中的上帽12的角。也就是,在本申请中,当上帽12的四个边(四个主边)中任意两个边(两个主边)交叉的区域被削角时,削角部分对应于角12k。当该区域没有削角时,任意两个(两个主边)的交叉对应于角12K。本申请中使用的术语“帽的角”用于具有与上述相同的意思和内容,特别的是除了当指定该术语具有不同的意思和内容时之外。如图2所示,下表面(安装表面)侧上的下帽(盖)13具有外表面(下表面)13b和围绕外表面13b布置的边13c,并且由此在平面图中为四角形(四边形)。下帽13在其外围处具有后面将要描述的四个边(四个主边)。也就是,下帽13包括在X方向上延伸的边(主边)13h1、在Y方向上延伸且与边13h1相交(垂直)的边(主边)13h2、与边13h1相对的边(主边)13h3和与边(主边)13h2相对的边13h4。下帽13具有四个角13k,其定位在边13h1、13h2、13h3和13h4的相邻边彼此相交的区域中。具体地,下帽13具有定位在边13h1与边13h2相交的区域中的角13k1。下帽13具有定位在边13h3与边13h4相交的区域中的角13k2。下帽13具有定位在边13h1与边13h4相交的区域中的角13k3。下帽13具有定位在边13h2与边13h3相交的区域中的角13k4。下帽13的角13K的定义与关于上帽12的角12k的描述相同,由此将不再重复描述。如图3所示,上帽12的边12c和下帽13的边13c分别是倾斜表面。上帽12和下帽13具有从边12c和13c向外部突出(向着边12c和13c的外围突出)的凸缘(凸部,接合区)12e和13e。如图1和图2所示,凸缘12e和13e分别形成在上帽12和下帽13的外围上,使其围绕边12c和13c。在半导体器件10中,上帽12的凸缘12e的内表面(下表面,或者图4中示出的接合表面12f)与下帽13的凸缘13e的内表面(上表面,或者图4中示出的接合表面13f)相对,并且各个凸缘12e和13e经由密封剂14与引脚3接合,这形成覆盖密封体7的帽(盖、部件)11。如图1和2所示,在半导体器件1中,多个引脚3沿着帽11的每个边(每个主边)布置。具体地,引脚3(一组引脚)沿着图1中所示的上帽12的边12h1、12h2、12h3和12h4中的每一个布置。换句话说,引脚3(一组引脚)沿着图2中所示的下帽13的边13h1、13h2、13h3和13h4中的每一个布置。如图3所示,悬置引脚8布置在沿着每个边布置的引脚组的每个端部处。引脚3(和悬置引脚8)由金属制成。在本实施例中,例如,引脚和悬置引脚中的每一个包括层叠金属膜,该层叠金属膜包括形成在由铜(Cu)或铜合金制成的衬底的表面上的镍(Ni)或镍-钯的金属膜(未示出)。这里使用的术语“镍-钯”指的是由镍(Ni)和钯(Pd)的合金制成的金属膜。在下文中,镍和钯的合金定义为“镍-钯或者Ni/Pd”,并且由镍-钯制成的金属膜(镀膜)定义为镍-钯膜。如图4所示,引脚3从上帽12和下帽13之间向外突出,以从帽11暴露。引脚3的暴露部分(外引脚3b)以向着下帽13的鸥翅形状形成(弯曲)在帽11的外部。每个引脚3的下端的位置位于比下帽13的外表面13b的位置低的水平处。引脚3的从帽11暴露的部分(外引脚3b)设置有金属膜MM,以覆盖上述衬底的下表面。金属膜MM例如是提高焊料的可湿性的金属膜,该焊料在引脚3与在安装衬底侧上的端子(未示出)接合时用作接合材料。金属膜MM包括上述镍(Ni)或镍-钯(Ni/Pd)。镍膜或镍-钯膜用作用于提高在密封体7和管芯垫2、引脚3或帽11之间的粘合的粘合提高膜。为此,不需要将镍膜或镍-钯膜形成为直到引脚3的从帽11暴露的部分(外引脚3b)。然而,为了提高焊料的可湿性,需要在每个引脚3的外引脚3b处额外形成金属膜(外部镀膜)MM。<内部结构>接下来,下面将描述半导体器件10的内部结构。如图4所示,半导体器件10包括:半导体芯片1、半导体芯片6、管芯垫(芯片安装部件)2和围绕管芯垫2布置的引脚3。半导体器件10包括多个用于电连接半导体芯片1与引脚3的导线5。半导体器件10还包括:用于密封半导体芯片1和6以及导线5的密封体7,和覆盖密封体7的帽(盖)11。如图4所示,半导体芯片1具有前表面(主表面、上表面)1a、与前表面1a相反的后表面(主表面、下表面)1b、和定位在前表面1a和后表面1b之间的侧面1c。用作半导体芯片1的电极的多个焊垫(电极,接合焊垫)1p形成在前表面1a上。焊垫1p电连接到形成在半导体衬底(未示出)的主表面(半导体元件形成表面)上的多个半导体元件(未示出),由此形成了电路(未示出)。半导体芯片6具有前表面(主表面、上表面)6a、与前表面6a相反的后表面(主表面、下表面)6b、和定位在前表面6a和后表面6b之间的侧面6c。用作半导体芯片6的电极的多个焊垫6p形成在前表面6a上。焊垫6p电连接到形成在半导体衬底(未示出)的主表面(半导体元件形成表面)上的多个半导体元件(未示出)上,由此形成了电路(未示出)。在图4至7中所示的实例中,半导体器件10具有半导体芯片(半导体芯片1和6),并且半导体芯片1安装在半导体芯片6的前表面6a上。换句话说,半导体器件10是具有被层叠并安装的多个半导体芯片的半导体器件。半导体芯片6经由粘合剂(管芯接合材料)S1安装在管芯垫2上。半导体芯片1经由另一粘合剂(管芯接合材料)S2安装在半导体芯片6的前表面6a上。如图4所示,半导体芯片6通过所谓的面向上安装(faceupmounting)来安装,以便后表面6b与管芯垫2的上表面2a相对。半导体芯片1通过所谓的面向上安装来安装,以便后表面1b与半导体芯片6的前表面6a相对。粘合剂S1没有限制于指定的一种,只要它能够将半导体芯片6固定在管芯垫2的上表面2a上。在本实施例中,例如,半导体芯片6通过采用由热固性环氧树脂制成的糊状树脂粘合剂来接合,然后被热固以固定。粘合剂S2是用于在半导体芯片6上固定半导体芯片1的部件。粘合剂S2的一部分可能会贴附到半导体芯片6的焊垫6p,这使得在后面要描述的导线接合步骤中很难连接导线5与焊垫6p。为了防止这些,粘合剂S2优选地是膜状粘合剂。因为与糊状粘合剂相比,膜状粘合剂不会从膜状粘合剂位于的位置向外扩展,所以膜状粘合剂由于其弹性差而是优选的。例如,膜状粘合剂包括形成在衬底上的粘合剂层,并且称为“管芯贴膜(DAF)”。可以使用通常用于将一个半导体芯片层叠在另一个半导体芯片上的粘合剂膜。通过这种方式,具有安装在一个封装(半导体器件)中的多个半导体芯片的结构的实例是称为系统级封装(SIP)的半导体器件。在具有SIP结构的半导体器件中,半导体芯片电连接在一起以形成系统。例如,存储器电路形成在图6所示的半导体芯片1中,并且用于控制半导体芯片1的存储电路的控制电路形成在半导体芯片6中。通过这种方式,将半导体芯片安装在一个封装中以形成系统,这样可以减小安装面积。半导体芯片的数目并不限于两个。在一个修改实例中,例如,这些可以应用于安装一个半导体芯片(未示出)的情况,或者安装三个或更多个半导体芯片(未示出)的情况。其上安装有半导体芯片6的管芯垫2是由与引脚3(和悬置引脚8)相同的金属制成的。在本实施例中,管芯垫2是由层叠金属膜制成的,该层叠金属膜例如,包括形成在由铜(Cu)或铜合金制成的衬底的前表面上的镍(Ni)或镍-钯的金属膜(未示出)。如图6所示,管芯垫2用作芯片安装表面的上表面2a在平面图中具有圆形形状,其面积比半导体芯片6的前表面6a的面积小。由此,如图4所示,半导体芯片6的后表面6b的一部分从管芯垫2暴露出,以粘合到密封体7上。从而,半导体芯片6的一部分后表面6b粘合到密封体7上,这样可以提高密封体7与半导体芯片6的接合强度。管芯垫2的芯片安装表面的面积和形状并不限于上述条件。替代地,管芯垫2的芯片安装表面可以形成为四方平面形状,以具有比半导体芯片6的后表面6b大的面积。管芯垫2通过悬置引脚8支撑。如图5所示,悬置引脚8具有连接到管芯垫2的一端,并且向着角12k和13k延伸。在本实施例中,如图6所示,每个悬置引脚8在角12k和管芯垫2之间分支成多个部分(例如,图6中为两个)。在上帽12(见图1)的各个边12h1、12h2、12h3和12h4中,引脚8的各个分支端从帽11暴露出(见图3)。换句话说,悬置引脚8从管芯垫2向着角12k延伸,但是被定位为避开上帽12的对应角12k。此外,简言之,悬置引脚8从在角12k和引脚3之间的帽11暴露。每个悬置引脚8在角12k和管芯垫2之间分支成多个部分,并且由此用作用于抑制裂缝发展的阻止件(stopper),这将在后面详细描述。悬置引脚8不定位在角12k处,这在半导体器件10的制造过程中可以有效地从角12k(具体地,图5中所示的角12k1和13k1之间开口)供应树脂。如图4所示,半导体芯片1经由多条导线(导电部件,金属线)5电连接到引脚3。具体地,导线5b的一端与半导体芯片6的焊垫6b接合,并且其另一端与引脚3接合。由此,半导体芯片6经由导线5电连接到引脚3。上级上的半导体芯片1经由导线5电连接到下级上的半导体芯片6。具体地,导线5a的一端连接到半导体芯片6的焊垫6p,并且导线5a的另一端连接到半导体芯片1的焊垫1p。由此,半导体芯片1经由导线5a电连接到半导体芯片6。换句话说,半导体芯片1经由半导体芯片6电连接到引脚3。在图6的修改实例中,这可以适用于半导体芯片1和引脚3经由导线5电连接在一起的情况。如图4所示,利用由橡胶制成的密封体7密封半导体芯片1和6以及导线5。利用密封体7密封导线5,这可以保护导线5,并且还可以防止或抑制由氧化或变形造成的电特性劣化。利用密封体7密封导线5,这可以防止或抑制相邻导线5之间的接触。用于密封体7的材料没有具体限制,但可以是树脂密封材料,包含具有向其中加入了诸如硅土的填充材料(颗粒)的热固性环氧树脂。形成密封体7可以在没有形成图4中所示的帽11的情况下保护导线5。然而,本申请的发明人已经发现:在没有形成帽11时,在一些情况下,例如在约175至250℃的高温环境下,在密封体7中可能产生裂缝。具体地,本申请的发明人已经通过将没有形成如图4所示的帽11的半导体器件放在约175℃、200℃和250℃的高温环境下,来评估高温耐用性。结果,发现在密封体7的前表面上产生裂缝。确认的是,裂缝将从其在密封体7前表面处产生的位置开始,向着密封体7内部发展。也就是,取决于产生裂缝的位置和裂缝的发展程度,裂缝可能会达到导线5、在导线5与焊垫1p和6p之间的接合部分或者半导体芯片1和6,从而降低了半导体器件的可靠性(电特性)。假设上述现象通过下面的机制产生。也就是,当密封体7的前表面的温度变高时,由于氧化,破坏了在密封体7前表面处的聚合作用。在破坏聚合作用的同时,产生了解聚作用。当在密封体7前表面处非均匀产生解聚作用时,在前表面处产生畸变,由此造成裂缝。近年来,树脂密封半导体器件被用于各种应用,并且例如,在一些情况下作为安装在车辆上的半导体器件。对于用作车载半导体器件,在一些情况下,与安装在移动电话上的半导体相比,该半导体器件的使用环境温度变高。从而,在约175至250℃温度的上述高温环境下,要求该技术来确保树脂密封半导体器件的可靠性。对于产生的裂缝,提出了一种防止裂缝到达导线5、在导线5与焊垫1p和6p之间的接合部分以及半导体芯片1和6的方法。该方法包括加厚密封体7,以加长从前表面到导线5的距离。然而,要求半导体器件变薄,这趋向降低从密封体7的前表面到导线5的距离。具体地,在包括像本实施例的半导体芯片1和6的层叠的半导体器件中,在密封体7的前表面和连接到在上层上的半导体芯片1的导线5之间的距离变得更短。基于上述发现,本申请的发明人已经进行了进一步研究,并且发现了如图4所示的利用帽11覆盖密封体7的结构。帽11包括布置在半导体器件10的安装表面侧上的下帽(安装表面侧盖、部件或帽)13和布置在与半导体器件10的安装表面相对侧上的上帽(上表面侧盖、部件或帽)12。上帽12的外围经由密封剂14接合并固定到下帽13的外围,由此形成包含用于在其中容纳密封体7的空间的帽11。如图8所示,上帽12具有外表面(上表面,暴露表面)12a、定位为与外表面12a相反的内表面(下表面)12b和围绕外表面12a布置的侧面(外表面)12c。上帽12具有布置在内表面(下表面)12b的基本中心上的凹进部(空间形成部)12d。上帽12包括围绕凹进部12d布置的凸缘(凸部,接合区)12e。凸缘12e的下表面侧用作用于接合如图4所示的密封剂14的接合表面12f。下帽13具有外表面(下表面、暴露表面、安装表面)13b、定位为与外表面13b相反的内表面(上表面)13a和围绕外表面13b布置的侧面(外表面)13c。下帽13具有布置在内表面(下表面)13a的基本中心处的凹进部(空间形成部)13d。下帽13包括围绕凹进部13d布置的凸缘(凸部,接合区)13e。凸缘13e的上表面侧用作用于接合如图4所示的密封剂14的接合表面13f。如图8所示,上帽12和下帽13中的每一个的形状(成形为具有凹进部12d和13d和凸缘12e和13e)可以通过冲压可塑性形变金属板形成。如图4所示,通过使上帽12的接合表面12f与下帽13的接合表面13f相对,并通过经由密封剂14使接合表面12f和13f与引脚3接合,帽11将半导体芯片1和6以及导线5容纳在由凹进12d和13d形成的空间中。由凹进部12d和13d形成的空间在其中容纳密封体7。围绕上帽12的凹进12d设置凸缘12e,并且围绕下帽13的凹进13d设置凸缘13e,这能够扩大密封剂14的接合区面积。由此,可以提高在上帽12和下帽13之间的接合强度。通过帽11覆盖密封体7,帽11可以用作散热器(热沉),以抑制密封体7前表面的温度增加。也就是,当图4中示出的半导体器件10暴露在约175至250℃的高温环境下时,帽11的温度增加。帽11是由具有比密封体7高的辐射效率的材料制成,以便帽11中包含的热量的一部分作为辐射热量从帽11的前表面向外耗散。密封体7粘合到帽11,以便热量从密封体7传递到帽11。结果,这种布置能够抑制密封体7前表面的温度增加。抑制了密封体7前表面的温度增加,能够抑制出现畸变来防止产生裂缝。也就是,半导体器件10使热量经由帽11从密封体7向半导体器件10的外部耗散,这可以防止产生裂缝,以提高器件的可靠性。为了使帽11用作散热器,利用具有比密封体7高的辐射系数的帽11的结构相比没有帽11的结构能够提高热耗散。具有比由树脂制成的密封体7高的辐射系数的材料包括金属、陶瓷等。为了在制造步骤中容易处理,帽11优选地由金属形成。为了提高从与密封体7的接触界面的热传导,帽11也优选地由金属制成。为了提高热传导和辐射系数(也就是,热耗散特性),更优选地,帽11例如由铜或铜合金形成。当密封体7粘合到帽11时,像半导体器件10,为了抑制由于线性膨胀系数区别而产生的畸变,密封体7优选地具有与帽11相同的线性膨胀系数。如上所述,诸如硅土(silica)的填充材料被加入到密封体7中,这造成半导体芯片1和6之间的线性膨胀系数区别很小。由此,用于帽11的材料具有与半导体芯片1和6相同的线性膨胀系数,使得密封体7的线性膨胀系数可以设置为与帽11相同。例如,在本实施例中,半导体芯片1和6的半导体衬底包括硅(Si),并且帽11(上帽12和下帽13)包括科瓦尔合金(kovar)(向其中加入了镍和钴的铁合金),其具有类似于硅(Si)的线性膨胀系数。例如,包括镍或镍-钯的金属膜(镀膜)形成在包括科瓦尔合金的衬底的前表面上。包括镍或镍-钯的镀膜(镍膜或镍-钯膜)用作用于防止帽11氧化的氧化防止膜。此外,形成在帽11的内表面(上帽12的内表面12b和下帽13的内表面13a)上的金属膜(镍膜或镍-钯膜)用作用于提高密封体7和帽11之间的界面的粘合的粘合提高膜。密封体7和帽11之间粘合提高,增加了热传递效率,由此提高了热耗散。密封剂14布置在上帽12和下帽13之间(凸缘12e和13e之间)的接合部分处。为了提高帽内部的密封性,密封剂14优选地具有高密封特性(相邻引脚3之间的嵌入性质,直到密封剂14在涂覆后接合并固定为止的形状保持性质,和接合界面的粘合性质)。为了减小相邻引脚3之间产生的间隙,与像膜状(带状)粘合剂的用于以固态接合的材料相比,优选地使用在固化之前具有糊状性质的材料。直到密封剂14在涂覆后固化为止,需要保持涂覆的形状。由此,密封剂14优选地具有一定程度的粘度。例如,具有与水相同的粘度的密封剂不能保持涂覆或涂布的形状。相反,具有非常高粘度的密封剂可能造成相邻引脚3之间的间隙。如本实施例,当上帽12和下帽13由金属(例如,科瓦尔合金,铜,或铜合金)制成时,引脚3和上帽12或下帽13之间的意外接触,会造成引脚3之间的短路。如图9所示,为了防止与引脚3接触,作为绝缘体的密封剂14需要确保介于上帽12和引脚3之间,以及下帽13和引脚3之间。虽然密封剂14被涂覆并固化来固定上帽12和下帽13的接合表面12f和13f,但密封剂14的粘度优选地较低,只要它能够保持涂敷或涂布时的形状。例如,在本实施例中,粘合剂S1是使用包括向其中混合了填充物(颗粒)的热固性环氧树脂的粘合剂形成的。然而,密封剂14固化前的粘度低于粘合剂S1固化前的粘度。通过控制加入到粘合剂中的填充物的形状、填充物的颗粒直径、诸如用于调节粘度的粘结剂的添加物与粘合剂主要材料的配比等,可以执行这种粘度调节。在固化密封剂14之后,与上帽12、下帽13和引脚3中的每一个的接合界面需要被接合并固定到密封剂14。在本实施例中,分别在上帽12和下帽13的接合表面12f和13f以及引脚3的前表面上形成包括相同金属(例如,镍或镍-钯)的镀膜。镀膜可以容易地提高与在接合表面12f和13f之间的接合部分中布置的每个组件的粘合。当首先将上帽12和下帽13中的一个(例如,上帽12)接合到引脚3,并且然后将另一个接合到引脚3时,可以使用不同类型的密封剂14用于接合。例如,如随后将详细描述的,在第一次接合(例如,到上帽12的接合表面12f)时,预先贴附膜状密封剂14(未示出)。接着,在接合(例如,下帽13)时,可以将糊状密封剂14涂覆到引脚3或下帽13的接合表面13f。在使用由金属制成的下帽13时,当在安装衬底(未示出)上安装半导体器件时,可以经由诸如焊料的金属接合材料将定位在安装衬底上的散热端子连接至下帽13的外表面13b。也就是,下帽13可以用作用于使热量从帽11的内部朝着半导体器件10的外部耗散的散热器(放热器)。在这种情况下,除了取决于从帽11辐射的散热路径,还可以增加另一散热路径(通过下帽13和金属接合材料(未示出)的散热路径),这样可以进一步提高散热效率。在本实施例中为了使密封体7粘合到帽11的内表面,由帽11覆盖半导体芯片1和6与导线5,并且接着充入树脂,从而形成密封体7(如将在下面详细描述的)。在以这种方式在形成帽11之后形成密封体7时,用于树脂的供应口是有必要的。为了防止在密封体7的内部或者密封体7和帽11之间形成空隙(气泡),形成密封体7时优选地设置用于排出帽11中的气体的排出口。为此,如图6所示,沿着上帽12的外围的每个边,具体地,在上帽12的边12h1、12h2、12h3和12h4中的每一个处布置密封剂14(见图1)。然而,没有在上帽12的角12k中的每一个处设置密封剂14。换句话说,将密封剂布置为避开上帽12的每个角12k。因此,在形成图5中所示的密封体7时,四个角12k中的一个或一些可以用作用于供应树脂的门,并且其它的角可以用作用于排出帽11中的气体的排放孔。如上所述,在形成帽11之后,将树脂供应到帽11中以形成密封体7。在这种情况下,使用于树脂的供应口和用于气体的排出口打开,以便在角12k和角13k之间暴露出密封体7的一部分,如图5所示。当在高温环境下留下具有密封体7的一部分被暴露的半导体器件10时,在暴露部分处可能产生裂缝。也就是,取决于密封体7的暴露部分的位置(产生裂缝的位置),在一些情况下,裂缝可能到达导线5、导线5与焊垫1p和6p之间的接合部分、或者半导体芯片1和6之间(见图4)。在相关技术中,例如,当在图4中所示的导线5上方暴露出密封体7的上表面7a的一部分时,裂缝更可能到达导线5。相反,在本实施例中,如上所述在角12k和13k之间暴露出密封体7。然而,即使在密封体7的暴露部分中产生裂缝,也远离导线5产生裂缝。因此,可以减少到达导线5的裂缝的可能性。此外,密封体7的整个上表面7a被上帽12覆盖,这可以防止裂缝产生。考虑到裂缝的发展,不必过多地加厚密封体7。换句话说,密封体7的厚度仅必须具有覆盖导线5所需的厚度,这可以导致半导体器件10的厚度减小。在本实施例中,如图6所示,悬置引脚8在角12k和管芯垫2之间被分支成多个部分(图6中为两个部分)。每个分支端在上帽12(见图1)的边12h1、12h2、12h3和12h4中的每一个处从帽11暴露出(见图3)。即使在图5中所示的密封体7的暴露表面处产生了裂缝,也可以将悬置引脚8放置在裂缝发展的方向上以在裂缝到达悬置引脚8之前阻止裂缝发展。也就是,由于每个悬置引脚8在平面图上在角12k和管芯垫2之间被分支成多个部分,所以悬置引脚8可以用作阻止件,用于中断裂缝的发展。该布置可以确保防止裂缝到达导线5或引脚3。<半导体器件的制造工序>接下来,下面将描述图5至9中所示的半导体器件的制造工序。根据图10中所示的组装流程图制造半导体器件10。图10示出了本实施例中的半导体器件的组装流程图的说明图。下面将利用图11至33描述各个步骤的细节。1.引线框制备步骤:图11示出了图10中所示的引线框设置步骤中设置的引线框的整个结构的平面图。图12是图11中所示的多个产品形成区中的一个及其周围的放大平面图。图13示出了沿着图12的线A-A的放大截面图。在图10所示的引线框设置步骤中,如图11所示设置了引线框20。在本实施例中使用的引线框20包括在外框(框体)20b内部的多个产品形成区20a。产品形成区20a被布置成列。框架部分20c布置在相邻的产品形成区20a之间。框架部分20c连接至每个产品形成区20a的组件(例如,图12中所示的引脚3和管芯垫2)以支撑它们。在随后将要描述的密封体形成步骤中,框架部分20c用作用于定位流道(runner)(未示出)的区域(流道布置区)(runnerarrangementregion),该流道作为用于将用于密封的树脂供应到布置在每个产品形成区20a中的帽中的供应路径。如作为图11的部分放大图的图12所示,每个产品形成区20a具有在X方向上延伸的边(主边)20h1、在Y方向上延伸的且与边20h1相交(垂直)的边(主边)20h2、与边20h1相对的边(主边)20h3和与边(主边)20h2相对的边20h4。产品形成区20a具有四个角20k,其定位在四个边20h中的相邻边相交的区域中。具体地,产品形成区20a在边20h1与边20h2相交的区域中具有角20k1。产品形成区20a在边20h3与边20h4相交的区域中具有角20k2。产品形成区20a在边20h1与边20h4相交的区域中具有角20k3。产品形成区20a在边20h2与边20h3相交的区域中具有角20k4。在每个产品形成区20a中,用作芯片安装部件的管芯垫2布置在产品形成区20a的中心处。多个引脚3围绕管芯垫2布置以包围管芯垫2。在产品形成区20a中,沿着产品形成区20a的四个边中的每一个布置引脚3。管芯垫2被事先弯曲,并经由悬置引脚8由框架部分20c支撑,每个悬置引脚8都具有倾斜部。因此,如图13所示,管芯垫2的上表面2a定为在比引脚3的上表面低的水平处。也就是说,在引线框设置步骤中设置的引线框20事先经受下置处理(down-settingprocessing)(偏移处理)。悬置引脚8中的每一个都具有连接至管芯垫2的一端,并且向着产品形成区20a的相应角20k延伸。在本实施例中,如图12所示,悬置引脚8被分成在角20k和管芯垫2之间的多个部分(图6中为两个)。每个分支端连接至引脚3和角20k之间的框架部分20c。换句话说,悬置引脚8从管芯垫2向着角20k延伸,并且被布置为避开角20k。如图4所示,引脚3中的每一个都包括在完成制造时利用密封体7和密封剂14密封的内引脚3a,和从帽11暴露的外引脚3b。如图13所示,内引脚3a包括从引脚3的内端侧按顺序布置的接合区3c、密封区3d和密封粘合区3e。接合区3c定位在引脚3的内端。接合区3c是导线接合步骤(见图10)中用于接合导线5(见图4)的区域。密封区3d定位在接合区3c和密封粘合区3e之间。密封区3d是在密封体形成步骤(见图10)中被密封体7(见图4)密封的区域。密封粘合区3e布置在密封区3d和外引脚3b之间。密封粘合区3e是在帽接合步骤(见图10)中通过在帽11(见图4)的凸缘12e和13e(见图4)之间的密封剂14(见图4)经受密封粘合(或密封)的区域。外引脚3b定位在引脚3的外端。外引脚3b是在引脚形成步骤(见图10)中被弯曲成如图6所示的鸥翼形的区域,并且该区域连接至安装衬底(未示出)上的端部。管芯垫2和引脚3与引线框20的框架部分20c一体形成,并且如图13所示,例如,包括由铜(Cu)制成的衬底21、和事先形成在衬底21的前表面上且由例如镍(Ni)或镍-钯(Ni-Pd)制成的金属膜(镀膜)MM。金属膜MM不必是以上述的方式形成在引脚3中的每一个的整个表面上。当金属膜MM没有形成在整个表面上时,如利用图4描述的,例如,在引脚3的从帽11暴露的外引脚3b的前表面(上表面、下表面和侧面)上通过镀的方法由焊料(包含无铅焊料)形成金属膜(外镀膜)MM。相反,当金属膜MM预先形成在包括外引脚3b的整个引脚3上时,可以省略图4中所示的形成金属膜MM的步骤。如图12所示,引脚3分别连接至框架部分20c,并且经由框架部分20c相互一体化,但在框架部分20c内没有连接。如下面将详细描述的,在本实施例中,在密封体形成步骤中(见图10),将树脂供应到由帽11(见图4)和密封剂14(见图4)密封的空间中,从而形成了密封体7(见图4)。引脚3在框架部分20c处连接在一起,并且因此可以在除了框架部分20c之外的其它区域中相互隔离。2.半导体芯片安装步骤:图14是示出在图12中所示的管芯垫上经由粘合剂安装的半导体的状态的放大平面图。图15是沿着图14的线A-A的放大截面图。图16是示出在图14中所示的半导体芯片上经由粘合剂安装另一半导体芯片的状态的放大平面图。图17是沿着图16的线A-A的放大截面图。然后,在图10所示的半导体芯片安装步骤中,如图14至17所示,半导体芯片6和半导体芯片1按顺序安装在管芯垫2上方。首先,在本步骤中,设置多个半导体芯片(半导体芯片1和半导体芯片6)。例如,在下面的步骤中,可以获得半导体芯片1和6。例如,设置由硅制成的半导体晶片(未示出),然后在其上方形成集成电路。集成电路包括半导体元件、连接至半导体元件的布线层和连接至布线层的外部端子(焊垫1p或焊垫6p)。其后,沿着半导体晶片的分割线移动分割刀片(旋转切割器)(未示出)以将晶片分离成多种类型的半导体芯片,每种类型都包括芯片。具体地,每个半导体晶片都被制作成单体以提供半导体芯片1和半导体芯片6。由于在本实施例中,半导体芯片1经由例如所谓DAF的膜状粘合剂S2而被安装在半导体芯片6的前表面6a上方,所以在该步骤中获得的半导体芯片1中的每一个都具有贴附到其后表面1b的粘合剂S2。接着,如图14和15所示,首先,经由粘合剂S1将要被定位为下层的半导体芯片6事先安装在管芯垫2的上表面2a上方。如图15所示,半导体芯片6利用其与管芯垫2的上表面2a相对的后表面6b来安装,也就是,通过所谓的面朝上安装。在本实施例中,半导体芯片6经由粘合剂S1安装,粘合剂S1例如是热固性环氧树脂。粘合剂S1是在固化(热固性)之前具有足够柔性的糊。在以这种方式使用这种糊作为粘合剂S1时,首先,将糊状粘合剂S1涂覆到管芯垫2的上表面2a上。接着,例如,通过将挤压模具(pressingjig)30向半导体芯片6的前表面6a挤压,将半导体芯片6的后表面6b推向管芯垫2的上表面2a,从而使得粘合剂S1在半导体芯片6的整个后表面6b上扩散,从而将半导体芯片6接合到管芯垫2上。接合之后,粘合剂S1被固化(例如,通过热处理)。结果,如图14和15所示,半导体芯片6经由粘合剂S1被固定到管芯垫2上。在修改实例中,粘合剂S1可以是膜状粘合剂。此外,为了提高朝向管芯垫2的散热,可以使用包含高热传导性的导电颗粒的粘合剂。然而,为了提高与包括金属(例如,镍或镍-钯)的管芯垫2的上表面2a的接合强度,优选的是糊状粘合剂。接着,如图16和17所示,经由粘合剂S2将半导体芯片1安装在半导体芯片6的前表面上。在该步骤中,利用半导体芯片1与半导体芯片6的前表面6a相对的后表面1b(涂覆了粘合剂S2的表面),将半导体芯片1定位在半导体芯片6的前表面6a上。例如,通过将图17中所示的挤压模具31向半导体芯片6的前表面6a挤压以将芯片1的后表面1b推向芯片6的前表面6a并与其接合,来安装半导体芯片1。由于半导体芯片1具有预先贴附到其后表面1b的膜状粘合剂S2,所以相比安装半导体芯片6的情况,可以通过小的挤压力安装半导体芯片1。因此,可以抑制可能会在该步骤中导致的对半导体芯片1的损伤。如图17所示,膜状粘合剂S2没有从半导体芯片1的后表面1b的外边缘向外突出,这可以防止粘合剂的一部分粘合到(污染)半导体芯片6的焊垫6p。接着,使粘合剂S2的接合层固化以将半导体芯片1固定在半导体芯片6的前表面6a上。3.导线接合步骤图18是示出图16所示的半导体芯片经由导线电连接至多个引脚的状态的平面图。图19是沿着图18的线A-A的放大截面图。接着,在图10所示的导线接合步骤中,如图18和19所示,经由导线5将半导体芯片的焊垫和引脚3相互电连接。在该步骤中,经由导线5a将半导体芯片1的焊垫1p电连接至半导体芯片6的焊垫6p。此外,经由导线5b将半导体芯片6的焊垫6p电连接至引脚3的接合区3c(见图19)。4.帽接合步骤:图20是示出在图18所示的引脚上接合并固定帽的状态的放大平面图。图21是沿着图20的线A-A的放大截面图。图22是示出图20所示的引线框的顶部和底部翻转的状态的放大平面图。图23是沿着图22的线A-A的放大截面图。图24是示出在图18所示的帽和引脚上涂覆密封剂的状态的放大平面图。图25是沿着图24的线A-A的放大截面图。图26是示出在安装表面上经由图24所示的密封剂接合并固定帽的状态的放大平面图。图27是沿着图26的线A-A的放大截面图。图28是沿着图26的线B-B的放大截面图。接着,在图10所示的帽接合步骤中,如图27所示,帽11被布置成覆盖半导体芯片1和6以及导线5,并经由密封剂14接合到引脚3。在该步骤中,如图27所示,设置了上帽12和下帽13。接着,在半导体芯片1的前表面1a侧上安装上帽12,并且在半导体芯片1的后表面1b侧上安装下帽13。在本实施例的帽接合步骤中,安装上帽12和下帽13的顺序并不限于上面提到的顺序。然而,为了安装下帽13同时保护连接至芯片1和6的导线5,首先在前表面1a侧上安装上帽12,并且然后在后表面1b上安装下帽13。具体地,如图21所示,设置了包括凹入部(凹进部)32a的台阶(支撑台)32和围绕凹入部32a布置的引脚架32b。随后,将引线框20放置在台阶32上使得引脚3位于引脚架32b上并且管芯垫2的下表面2b位于凹入部32a上。接着,上帽12被布置为覆盖半导体芯片1和6以及导线5并且经由密封剂14被接合到引脚3。如图21所示,上帽12包括外表面12a、与外表面12a相反的内表面(下表面)12b、和定位在外表面12a与内表面12b之间的侧面12c。上帽12具有朝向外表面12a凹进的形状,并且在主表面12b侧上包括凹进部(空间形成部、凹入部或芯片容纳部)12d、和围绕凹进部12d布置的凸缘(接合部)12e。上帽12是由例如通过挤压由科瓦尔合金(koval)制成的平板而形成凹进部12d和凸缘12e来获得的。用于形成上帽12的方法并不限于此,并且凹进部12d和凸缘12e(从平板的底部突出的部分)可以通过移除(切割掉)一个厚平板的一部分(中心)来形成。从所使用的材料的量或重量减少的角度看,优选地如本实施例成形平板。凹进部12具有可以在其中保持半导体芯片1和6、导线5和部分引脚3(图13中所示的接合区3c)的这种平面尺寸。因此,在该步骤中,利用上帽12覆盖半导体芯片1和6、导线5和部分引脚3(接合区3c)。换句话说,在该步骤中,将上帽12接合并固定到引脚3以覆盖半导体芯片1和6、导线5和部分引脚3(接合区3c)。引脚3中的每一个都包括共同一体形成的内引脚3a和外引脚3b,并且在平面图中从上帽12的凹进部12d的内侧朝着凹进部12d的外部延伸。在该步骤中,为了将密封剂14嵌入在相邻的引脚3之间,优选地使用糊状树脂。然而,在本实施例中,上帽12和下帽13(见图27)按顺序接合并固定,从而在接合随后将要被固定的帽(例如,下帽13)时使用糊状树脂可以利用密封剂14填充相邻引脚3之间的间隙。因此,首先要被固定的帽(例如,上帽12)可以经由膜状(带状)密封剂14a接合并固定,如图21所示。在该情况下,例如,预先将膜状(带状)密封剂14a的一个接合表面接合到上帽12的接合表面12f。然后,将上帽12利用与其接合的密封剂14a接合到引脚3的密封粘合区3e。因此,上帽12可以被容易地接合并固定到引脚3。图10中所示的密封剂涂覆步骤包括将膜状(带状)密封剂14a接合到接合表面12f。密封剂14并不限于上面的膜状密封剂14a。可以使用糊状树脂作为密封剂14,如用于接合随后将要描述的下帽13的密封剂。在这种情况下,在引脚3的密封区3e上涂覆糊状密封剂14b。在管芯垫2的上方布置上帽12使得涂覆了密封剂14的区域(密封粘合区3e)与上帽12的凸缘12e的接合表面12f相对。此时,半导体芯片1和6、导线5、引脚3的接合区3c(见图19)和管芯垫2被容纳在上帽12的凹进部12d中。通过挤压模具(未示出)从外表面12a向着台阶32挤压上帽而将凸缘12e的接合表面12f推向台阶32,以便使密封剂14扩散来填充相邻引脚3之间的间隙,这经由密封剂14将每个引脚3的密封粘合区3e接合到凸缘12e的接合表面12f。涂覆糊状密封剂14的细节与随后将要描述的接合下帽13的工艺相同,因而下面将省略其重复描述。接着,如图22和23所示,使引线框20的顶部和底部(前面和背面)翻转。也就是,如图23所示,将引线框20布置为使得管芯垫2定位在半导体芯片1和6上方。如图22所示,在本实施例中,密封剂14没有布置在角20k处。在每个角20k处,暴露了上帽12的凸缘12e的接合表面12f。这是因为角20k用作树脂的供应口(门)或者用于在随后将要描述的密封体形成步骤中的气体的排出口(排放孔)。接着,如图24和25所示,在引脚3(见图25)的密封粘合区3e上,换句话说,在上帽12(见图25)的凸缘12e的接合表面12f上,涂覆糊状密封剂14b。随后,如图27所示,下帽13被布置为覆盖半导体芯片1和6以及导线5,并且经由密封剂14被接合到引脚3。如图28所示,布置下帽13使得凸缘13e与上帽12的凸缘12e相对,并且接着通过挤压模具(未示出)将下帽13挤压向上帽12而被接合。如上面提到的,糊状密封剂14b具有可以保持涂覆形状(例如,图25中所示的形状)的这种粘度。因此,可以在涂覆了密封剂14b之后防止密封剂14b直至接合下帽13之前在涂覆区的周围上扩散。将引脚3定位在要涂覆密封剂14b的区域(接合区)中,因此与上帽12的接合表面12f相比,该区域具有粗糙波状表面。因此,如图25所示,在涂覆了密封剂14b的台阶中,在一些情况下在密封剂14b、上帽12和相邻的引脚3间形成了间隙。然而,如图28所示,可以挤压下帽13以扩散糊状密封剂14b,由此密封剂14可以嵌入在相邻的引脚3之间的间隙中。具体地,使用具有比图15中所示的糊状粘合剂S1的粘度低的密封剂14b改善了嵌入性质,这样可以有效地防止产生没有由密封剂14b填充的间隙。如图24所示,密封剂14b没有被涂覆到产品形成区20a中的角20k上。例如,如图25所示,当悬置引脚8定位在平行布置的一组引脚3的一端附近时,连续地涂覆密封剂14b以覆盖引脚3的密封区3e,但在密封剂重叠在悬置引脚8上的位置处停止涂覆密封剂14b。如图28所示,当下帽13的凸缘13e挤压向上帽12的凸缘12e时,相邻的引脚3之间的间隙填充有密封剂14b,这样可以防止密封剂14b在每个角20k上扩散。因此,密封剂14被嵌入在相邻引脚3之间的间隙以及悬置引脚8和引脚3之间的间隙中,结果在产品形成区20a(见图26)的每个角20k处形成了开口。接着,当糊状密封剂14b被加热并固化时,上帽12的凸缘12e的接合表面12f和下帽13的凸缘13e的接合表面13f被接合并固定到固化的密封剂14上。在本实施例中,例如,密封剂14b包含热固性环氧树脂,并由此可以被加热以被固化。参考图24和25,上面已经描述了用于涂覆密封剂14的方法的一个实例。然而,如图28所示,只要密封剂14嵌入在相邻的引脚3之间并且在上帽12接合到下帽13的台阶中的每个角20处形成了开口,则该涂覆方法不受具体限制。例如,以图24和25所示的形式,糊状密封剂14b沿着管芯垫2的上表面2a的外围布置成带状。在修改实例中,糊状密封剂14不连续地布置在引脚3的密封粘合区3e的多个位置中,也就是,可以采用所谓的多点涂布。即使在多点涂布中,也挤压下帽13以扩散糊状密封剂14b,使得密封剂14b可以嵌入在引脚3之间的间隙中。例如,参考图24和25,上面已经说明了在引脚3上涂覆糊状密封剂14b。涂覆密封剂14b的部件并不限于引脚3。例如,密封剂14b可以涂覆到下帽13的凸缘13e的接合表面13f。替代地,例如,密封剂14b可以涂覆到下帽13的接合表面13f和引脚3的密封粘合区3e。通过上述步骤,上帽12和下帽13利用彼此相对的凹进部12d和13d接合并固定到一起。在接合并固定下帽13之后,如图27所示,半导体芯片1和6、导线5和部分引脚3(接合区3c)定位在由在下帽13的凹进部13d上重叠上帽12的凹进部12d所形成的空间TK内。在该步骤中,由金属制成的上帽12和下帽13经由由绝缘材料制成的密封剂14接合并固定在一起,使得不与引脚3接触。5.密封部件形成步骤图29是示出密封体形成在图20中所示的引线框的产品形成区中的状态的放大平面图。图30是沿着图29的线A-A的放大截面图。图31是示出将用于密封的树脂供应到由帽形成的空间的状态的并且沿着图29的线B-B的放大截面图。接着,在图10所示的密封体形成步骤中,如图29和31所示,树脂7p被供应到由上帽12和下帽13形成的空间TK(见图31)中,使得利用树脂7p密封导线5(见图30)以及半导体芯片1和6(见图30和31)。本实施例中的密封体7是通过所谓的传递模塑法形成的。也就是,如图31所示,引线框20被固定在模塑模具40的上模具41和下模具42之间。随后,软化的(变成塑性的)热固性树脂(树脂7p)被供应(挤压)进要被模塑的上帽12和下帽13之间的空间TK中,并且然后被加热并固化。在本实施例中使用的热固性树脂(树脂7p)包含树脂和混合到树脂中的填充物(颗粒)。传递模塑法在有效制造方面是优选的,因为可以通过一次操作将密封体7形成在产品形成区20a中。在传递模塑法中,软化的树脂7p被供应到空间TK中,使得树脂7p能够容易地粘合到上帽12的下表面(内表面)和下帽13的上表面(内表面)。也就是,如图30所示,密封体7粘合到帽11,这样可以将热量从密封体7有效地传递到帽11。在该步骤中,首先,如图30和31所示设置模塑模具40。模塑模具40包括覆盖引线框20的上表面(安装有半导体芯片的表面)侧的上模具(第一模具)41和覆盖引线框20的下表面(与安装有半导体芯片的表面相反的表面)的下模具(第一模具)42。上模具41包括腔(凹入部、帽挤压部、盖挤压部)43。下模具42包括腔(凹入部、帽挤压部、盖挤压部)44。腔43和腔44彼此相对并且重叠在彼此上方,从而形成了用于在其中容纳帽11的空间。腔43和44具有与上帽12和下帽13类似的形状。树脂膜45沿着内表面41a和42a中的每一个的形状被贴附到上模具41的内表面(下表面)41a和下模具42的内表面(上表面)42a中的每一个。换句话说,树脂膜45被布置在腔43和上帽12之间,以及腔44和下帽13之间。树脂膜45比模塑模具40和帽11软。换句话说,树脂膜45具有比模塑模具40和帽11中的每一个高的弹性。因此,当帽11被夹(夹持)在上模具41和下模具42之间时,树脂膜45进入间隙11,这样可以防止树脂7p的泄漏。也就是,树脂79可以供应到空间TK中。现在,利用树脂膜45的模塑方法是所谓的“层叠模塑法”。在本实施例中,供应树脂7p同时例如通过模塑模具40挤压上帽12的整个周围和下帽13的整个周围。树脂7p供应到的区域已被上帽12和下帽13覆盖,并且上帽12和下帽13之间的接合部分通过硬化的密封剂14固定在一起。因此,至少通过挤压树脂7p的供应口可以将树脂7p供应到空间TK中。将经平衡的力(夹持力)施加到整个帽11上。为了稳定地供应树脂7p,优选地如本实施例,在通过模塑模具40挤压上帽12和整个周围和下帽13的整个周围的情况下供应树脂7p。如图30所示,模具表面(夹持表面)41b围绕上模具41的腔43布置。模具表面(夹持表面)42b围绕与模具表面41b相对的下模具42的腔44布置。通过在彼此相对的模具表面41b和42b之间挤压并夹住引线框,模塑模具40将引线框20固定在上模具41和下模具42之间。如图31所示,模塑模具40包括用作用于树脂7p的供应口的门40G,和用作空间TK中的气体(空气)、或者多余树脂7p的排出口的排放孔40B。在本实施例中,图29中所示的产品形成区20a具有四个角20k。在一个角20k1处布置了门40G(见图31),并且在剩余的三个角20k2、20k3和20k4处布置了排放孔40B(见图31)。换句话说,从产品形成区的四个角之中的角20k1供应树脂7a,并且从其它的角20k2、20k3和20k4排出气体。因此,从角20k排出气体,这很难在空间TK中留下气泡(空隙)。如描述帽接合步骤时使用的图28所示,密封剂14嵌入在相邻的引脚3之间以及在悬置引脚8和引脚3之间,并且在产品形成区20a的每个角20k处形成了开口(见图26)。该步骤使用在没有密封剂14的角20k处形成的开口,作为用于供应树脂7p的供应口(开口)和用于排出气体的排出口(开口)。换句话说,在本实施例中,将树脂7p供应(挤压)到图31所示的在角12k1和角13k1之间形成的开口中。在该步骤中,从除角12k1之外的角12k处和除角13k1之外的角13k处形成的开口排出帽11中的气体。如图31所示,具有布置在腔43侧的门40G的系统是所谓的侧门系统。在传递模塑系统中,树脂7p被从门40G供应到图31中所示的空间TK中。在空间TK中,树脂在管芯垫2和半导体芯片1和6的周围扩散以密封空间TK内的全部组件。空间TK中的气体(空气)通过树脂7p的供应压力而被挤压以从排放孔40B排出。如图12所示从管芯垫2朝着角20k1延伸的悬置引脚8在角12k和管芯垫2之间分支成多个片(两个),以避开上帽12的角12k。因此,图31所示的角12k1和13k1之间的开口的面积可以被加宽,从而从开口有效地供应树脂7p。通常,当利用模塑模具通过传递模塑法形成密封体时,设置了用于连接相邻引脚3的部件,其被称为阻挡条(dambar)(分歧器(diver))。在应用传递模塑法时,设置阻挡条用于防止树脂7p从相邻的引脚3之间的间隙泄漏。然而,在本实施例中,在帽接合步骤中,密封剂14嵌入在相邻的引脚3之间。在应用传递模塑法时密封剂14具有防止树脂7p泄漏的作用。换句话说,在密封体形成步骤中,相邻的引脚3经由由绝缘材料组成的密封剂14连接在一起。因此,在密封体形成步骤之后,移除阻挡(密封剂14)的步骤(阻挡移除步骤中)不是必须的。也就是,本实施例可以削减一部分制造步骤,从而提高制造效率。为了将热量从密封体7有效地传递到帽11,优选地减少帽11内剩余的气泡(空隙)。从减少气泡的角度,由于在图31中所示的空间TK被填充树脂7p之后,树脂7p中剩余的气泡(空隙)被强制排出,所以优选地将比供应压力(空隙移除压力)高的压力施加到空间TK的内部。用于移除气泡的方法不限于上面的。可以应用所谓的减压模塑法,其包括,例如,在减压室(未示出)(真空室等)布置引线框20,和将树脂7p供应到空间TK中。在这种情况下,甚至在树脂7p的供应压力设置为低时,也可以防止气泡剩余,这样可以减少对密封剂14的应力。将比上述供应压力高的压力(空隙移除压力)应用到空间TK的上述方法是有利的,在于与减压模塑法相比,可以在不使用减压室等的情况下移除气泡。如上面提到的,在利用树脂7p填充空间TK以移除气泡(空隙)之后,树脂7p被加热以被固化,其形成图30所示的密封体7。在加热步骤(烘焙步骤)中,例如,树脂7p被暂时固化在模塑模具40中(即使在从模塑模具40移除之后,整个树脂7p也在保持其形状的情况下没有被固化)。之后,引线框20被从模塑模具40取出,并且被传递到加热炉(未示出),并且然后树脂7p被完全固化(其使整个树脂7p硬化)。在上面的步骤中形成的密封体7使其上表面7a粘合到上帽12的内表面12b,如图30所示。密封体7的下表面7b粘合到下帽13的内表面(上表面)13a。如图29所示,密封体7在产品形成区20a的角20k处的从帽11暴露,用作树脂7p的供应口,或气体的排出口。然而,密封体7的暴露部分布置在角12k处,这可以使密封体7的暴露部分与导线5分离(见图30)。甚至当在密封体7的暴露部分中产生裂缝时,也可以减少裂缝到达导线5的可能性。密封体7的上表面7a被上帽12覆盖,这可以防止裂缝的产生。6.引脚形成步骤图32是示出形成产品形成区的状态的放大平面图,其中从该产品形成区切割了图29中所示的外引脚。沿着图32中所示的线A-A的放大截面图与图4中的相同,因此此处将省略。现在,下面将参考图4描述引脚形成步骤。接下来,在图10所示的引脚形成步骤中,如图32所示,从引线框架部分20c切割引脚3的外引脚3b。之后,引脚3的外引脚3b中的每一个都形成为鸥翼状。切割引脚3的外引脚3b的方式包括将冲压机(切割刀片)(未示出)定位在引线框20的上表面侧并将模具(支撑夹具)(未示出)定位在其下表面侧上,并且通过将冲压机挤压向该模具来切割外引脚3b。使引脚3的外引脚3b成形的方式可以包括利用用于成形的冲压机和模具挤压外引脚。在该步骤中,使引脚3分别分离为单独的部件。在该步骤中,使引脚3与引线框20分离。因此,除非产品形成区20a内的每个组件都由引线框20的框架部分20c支撑,否则成形会变难。在本实施例中,悬置引脚8布置在没有布置引脚3的区域中。例如,如图7所示,利用密封体7密封悬置引脚8。因此,直至完成如随后将要描述的片隔离步骤,产品形成区20a都经由悬置引脚8连接至引线框20的框架部分20c并由其支撑。7.单体化步骤:图33是示出将图32中所示的产品形成区从引线框的框架部分分离并形成为单体的状态的放大平面图。然后,在图10所示的片分离步骤中,如图33所示,从引线框20的框架部分20c分离产品形成区20a以便执行单体化。在该步骤中,用作使产品形成区20a与框架部分20c连接的连接部分的悬置引脚8是通过例如利用冲压机(切割刀片)和模具(支撑模具)(未示出)挤压来切割的。此时,分别通过冲压机移除形成在门部分40G中的门树脂和形成在排放孔40B中的排放孔树脂。在上面的各个步骤中,获得了图1至9中所示的半导体器件10。本实施例使用具有如图11所示的产品形成区20a的引线框20,以便可以从一片引线框20获得多个半导体器件10。其后,对每个半导体器件进行必要的检查和测试,诸如外观检查和电测试,该半导体器件然后被出货或安装在安装衬底(未示出)上。如在引线框设置步骤的描述中使用的图13所示,在本实施例的引线框20中,由例如镍(Ni)或镍-钯(Ni/Pd)制成的金属膜(镀膜)MM被预先形成在由铜(Cu)制成的衬底21的整个前表面(上表面、下表面和侧面)上方。也就是,当如图4所示在安装衬底(未示出)上安装半导体器件10时,利用由镍(Ni)或镍-钯(Ni/Pd)制成的金属膜MM覆盖连接至安装衬底侧上的端子的外引脚3b。金属膜MM具有提高焊料的可湿性的作用,该焊料用作在安装衬底上安装半导体器件10时的接合部件。在图10中,可以省略括弧中表示的镀膜步骤。在修改实例中,当在外引脚3b上没有形成由镍-钯(Ni/Pd)制成的金属膜(镀膜)MM时,如图10的括弧中所示,在密封体形成步骤之后进行镀的步骤。在图10所示的镀的步骤中,例如,在从密封体7暴露的引脚3(外引脚3)上形成由焊料制成的金属膜(外镀膜)。在该步骤中,将要被镀的物体的引线框20布置在填充有镀液(未示出)的镀槽(未示出)中,镀液通过电解电镀形成外镀膜。电解电镀方法可以通过一次操作在从密封体7暴露的区域中形成外镀膜。该外镀膜形成在外引脚3b中的每一个的上表面、下表面和侧面中的每一个上。如上所述,由绝缘材料制成的密封剂14介于帽12和13以及引脚3中的每一个之间。因此,在利用引线框20作为电极时,上帽12和下帽13没有通电,并且外镀膜没有形成在帽11处。为了防止帽11的氧化,优选地,在将帽11接合到引脚3之前预先在帽11的前表面上形成金属膜(镀膜)。第二实施例作为在第一实施例中描述的半导体器件10的修改实例,本实施例将描述在没有在布置于半导体芯片的后表面侧上的帽中形成腔的情况下,利用由平板制成的帽的封装结构。本实施例将描述与第一实施例中描述的半导体器件及其制造方法的区别,并且下面将省略对这些实施例共同部分的描述。关于附图,根据需要示出了用于说明与第一实施例的区别所需的附图,并且在一些情况下,引用了用于第一实施例的描述的附图用于下面说明。<结构上与第一实施例的区别>图34是示出作为图2的修改实例的半导体器件的下表面侧的平面图。图35是作为图4的修改实例的半导体器件的截面图。图36是作为图5的修改实例的半导体器件的截面图。图37是作为图6的修改实例的半导体器件的透视平面图。图34中所示的半导体器件的顶视图与第一实施例中描述的图1相同,并且下面将省略其说明。图34至37中所示的半导体器件50与第一实施例中描述的半导体器件10的不同之处在于,由平板制成的下帽(盖)15被接合在与上帽12相对的位置。如图34所示,布置在半导体器件50的下表面(安装表面)侧上的下帽(盖)15具有外表面(下表面、暴露的表面、安装表面)15b,并且在平面图中具有四角形(四边形)。下帽15的平面尺寸与上帽12相同(见图1)。下帽15被接合并固定到上帽12,使得上帽(凸缘12e)的外围重叠在下帽15的外围上。下帽15具有由例如镍或镍-钯制成的并且形成在由科瓦尔合金制成的衬底前表面上的金属膜(镀膜)MM(见图35),与第一实施例中描述的下帽13类似。通过这种方式,金属膜MM形成在布置于安装表面侧上的下帽15的下表面(安装表面)上方,这提高了下帽15的外表面15b处的可湿性(焊料的可湿性)。结果,当在安装衬底(未示出)上安装半导体器件50时,将下帽15的外表面(下表面)15b连接至安装衬底侧上的端子,这可以提高散热。下帽15在其外围处包括以下四个边(四个主边)。也就是,下帽15在其外围处具有在X方向上延伸的边(主边)15h1、在Y方向上延伸并与边15h1相交(垂直)的边(主边)15h2、与边15h1相对的边(主边)15h3和与边(主边)15h2相对的边15h4。下帽15具有定位在边15h1、15h2、15h3和15h4中的相邻边相互相交的区域中的四个角15k。具体地,下帽15具有定位在边15h1与边15h2相交的区域中的角15k1。下帽15具有定位在边15h3与边15h4相交的区域中的角15k2。下帽15具有定位在边15h1与边15h4相交的区域中的角15k3。下帽15具有在边15h2与边15h3相交的区域中的角15k4。下帽15的角15k的限定与上述的上帽12的上述角12k相同,并且由此将省略重复描述。密封体7的上表面7a没有暴露,并且在上帽12的角12k和下帽15的角15k之间暴露密封体7。这与前述实施例中描述的半导体器件10相同。如图35所示,下帽15在截面图中具有平坦板(平板)状,而没有上帽12的凹进部12d和凸缘12e。在半导体器件50中,密封体7覆盖有具有平板状的下帽15,以便下帽15可以用作用于安装半导体器件1和6的芯片安装部件。换句话说,半导体器件50与第一实施例中描述的半导体器件10不同之处在于,没有布置图1中所示的管芯垫2并且半导体芯片6安装在下帽15的内表面15a上。具体地,半导体芯片6经由粘合剂S1安装在作为芯片安装部件的下帽15的内表面15a上。并且,半导体芯片1经由粘合剂S2安装在半导体芯片6的前表面6a上。下帽15用作芯片安装部件而没有设置管芯垫2(见图4),这样可以减小半导体器件的厚度。替代地,下帽15用作芯片安装部件,这样可以增加下帽15的厚度(从内表面15a到外表面15b的距离),从而提高了下帽15的散热。在图35和36所示的实例中,例如,下帽15的厚度比上帽12的厚度厚(大),上帽12的厚度也就是从外表面12a到内表面(下表面)12b的距离。当下帽15用作芯片安装部件时,在修改实例中,不能设置悬置引脚8。然而,如用于描述第一实施例的引脚形成步骤所使用的图32所示,除非在切割引脚3的外引脚3b之后,在产品形成区20a内的每个组件通过引线框20的框架部分20c支撑,否则引脚3很难形成或成形。如图35所示,在本实施例中,为了通过弯曲容易地形成引脚3,设置了悬置引脚8。如图37所示,在平面图中,悬置引脚8分别布置在下帽15的四个角15k和半导体芯片6的四个角之间。每个悬置引脚8在半导体芯片6和下帽15的每个角之间被分支为多个部分。每个暴露端在下帽15的边15h1、15h2、15h3和15h4中的每一个处从帽11(见图35)暴露。<在制造方法上与第一实施例的区别>现在,下面将描述图34至37中所示的半导体器件50的制造方法。而且在这一章节中,在下面将主要描述与第一实施例的半导体器件的制造方法的区别,并且下面将省略与这些实施例共同的部分的描述。图38是示出图10的修改实例中的半导体器件的组装流程图的说明图。本实施例的半导体器件的制造方法在引线框设置步骤和帽接合步骤方面与第一实施例不同。详细地,本实施例与第一实施例的不同之处在于,在半导体芯片安装步骤中,下帽15的一部分(布置在其中心的芯片安装区)用作芯片安装部件。在本实施例中,在应用时在第一实施例中描述的管芯垫2可以由下帽15替代,除内表面(上表面)15a的平面面积比半导体芯片6大的事实之外,并由此下面将省略其描述和说明。在引线框设置步骤中,首先,如图39和40中所示设置引线框20。图39是示出图12的修改实例中的引线框的放大平面图。图40是示出图13的另一修改实例中的引线框的放大截面图。因为在本实施例中,在半导体芯片安装步骤(见图38)中,半导体芯片6(见图35)安装在下帽15上,所以必须在半导体芯片安装步骤之前将下帽15接合到引线框。因此,如图39所示,下帽15定位在产品形成区20a的中心处。下帽15与引线框20分离地形成,并且经由密封剂14接合并固定到引脚(以及悬置引脚8)。此时在本步骤中,没有必要将密封剂14嵌入在相邻的引脚3之间。可以利用第一实施例中描述的膜状密封剂14a或糊状密封剂14b中的任何一个来接合下帽。密封剂14与引脚3和下帽15中的每一个之间的接合界面具有由镍或镍-钯形成的金属膜MM,这样可以提高与密封剂的粘合。在该步骤中,如图39所示,设置了引线框20,其具有接合并固定到下帽15的引脚3。引脚3围绕下帽15的芯片安装区(将要安装半导体芯片6的区域;芯片安装部件)布置。每个引脚3都包括由密封体7密封的内引脚3a和在图35中所示在完成时从密封体7暴露出的外引脚3b。如图40所示,内引脚3a具有从引脚3的内端部按顺序布置的接合区3c、密封区3d和密封粘合区3e。在本实施例中,下帽15形成为打开形状,以便在整个内引脚3a上,下帽15位于靠近内引脚3a。为了防止在引脚3和下帽15之间的接触,使密封剂14布置在接合区3c和下帽15之间、密封区3d和下帽15之间、以及密封粘合区3e和下帽15之间。如在第一实施例中描述的帽接合步骤,在产品形成区20a的角20k处没有布置密封剂14。因此,在密封体形成步骤中,可以从每个角20k(具体地,从角12k1和角15k1之间的开口,如图36所示)供应树脂。从其他的角20k,可以排出气体或多余的树脂。如第一实施例,从帽11暴露密封体的位置可以设置在帽11的角处(具体地,图36中所示的角12k和角15k之间)。换句话说,可以由密封体7覆盖密封体7的整个上表面7a。接着,在图38所示的帽接合步骤中,已经接合了下帽15。通过接合并固定上帽12,如图41所示,上帽12和下帽15利用上帽12的凹进部12d接合并固定在一起,该凹进部12d与下帽15的内表面15a相对,由此形成了空间TK。在该步骤中,上帽和下帽接合在一起,使得上帽12的外围重叠在下帽15的外围上。图41是图27的修改实例的放大截面图。在该步骤中,设置了上帽(盖)12,其包括凹进部12d和围绕凹进部12d布置的凸缘(突出部)12e。并且,上帽12被定位为使得下帽15的外围重叠在上帽12的外围上,并且然后经由密封剂14b被接合到引脚3。在本实施例的帽接合步骤中,安装上帽12。因此,优选地将密封剂14嵌入在相邻的引脚3之间。优选地使用本实施例中描述的糊状密封剂14b。在本实施例中,尽管没有示出,下帽15由平板制成,并且因此相比在第一实施例中描述的下帽13,在密封体形成步骤中下帽15更可能粘合到模塑模具40(见图31)。例如,即使树脂膜45(见图31)不介于下帽15和模塑模具40之间,该结构也可以防止树脂7p的泄露(见图31)。也就是,在制造步骤中可以减少昂贵材料的使用量。除上述区别之外,本实施例中的半导体器件及其制造方法与第一实施例中描述的半导体器件的制造方法相同。因此,下面将省略其重复的描述,并且除了上述区别之外,在本实施例中可以应用本发明中的第一实施例的方面。第三实施例作为在第一实施例中描述的半导体器件10的修改实例,下面将描述第三实施例,其中在形成密封体之后,将帽设置为覆盖密封体。而且在本实施例中,在下面将主要描述半导体器件的制造方法和结构与第一实施例的区别,并且下面将省略对这些实施例共同部分的说明。关于附图,将示出说明与第一实施例的区别所需的附图,并且如果需要,则引用用于第一实施例中的描述的附图用于说明。<与第一实施例的区别>首先,将在下面描述本实施例中的半导体器件的制造方法。图42是示出作为图10的修改实例的半导体器件的组装流程图的说明图。图43是作为图4的另一修改实例的半导体器件的截面图,并且图44是作为图5的另一修改实例的半导体器件的截面图。图45是作为图43的修改实例的半导体器件的截面图。如图42所示,本实施例的半导体器件52的制造方法与第一实施例中描述的半导体器件10的制造方法的不同之处在于,在密封体形成步骤之后执行帽接合步骤。如图43和44所示,上帽12重叠在下帽13上以形成用于在其中容纳密封体7的空间TK。密封剂14被定位在布置于上帽12和下帽13的外围处的接合部分处(凸缘12e和13e之间),以使(密封)其中容纳密封体7的空间成为气密状态。当预先形成密封体7(见图43)时,如本实施例,在密封体形成步骤中不需要用于供应用于密封的树脂的开口。也就是,密封剂14可以被布置在上帽12的角12k和下帽13的角13k之间。换句话说,上帽12和下帽之间的接合表面可以在其外围上密封。结果,密封体7没有直接暴露于外部环境,这可以抑制密封体7的温度增加。在形成密封体7的情况下,上帽12与下帽13被接合并固定在一起,这使得难以在密封体7的上表面7a和上帽12的内表面(下表面)12b之间、以及密封体7的下表面7b和下帽13的内表面(下表面)13a之间建立粘合。换句话说,如图43所示,可能会在帽11和密封体7之间形成间隙SK。在存在间隙SK的情况下,与如在第一和第二实施例中描述的、帽11粘合到密封体7的上表面7a的情况相比,从密封体7到帽11的热传递率降低了。来自帽11的热量不仅在半导体器件51的向外方向上辐射,而且在半导体器件51的向内方向(朝着密封体7的内部的方向)上辐射,使得辐射的热量倾向于存储在帽11内部的空间TK中。结果,取决于环境温度或辐射条件,密封体7的上表面7a的温度变得比半导体器件10的温度高。为了抑制密封体7的温度增加,如图45中所示的半导体器件53,密封体7的上表面7a优选地经由粘合剂16连接至上帽12的内表面12b。例如,粘合剂16是由含有多个(大量)金属颗粒的热固性环氧树脂制成的糊状树脂粘合剂。粘合剂16是具有热传导率比仅由树脂制成的粘合剂的热传导率高的热传导率的热传导粘合剂。粘合剂16介于导线5附近的密封体7的上表面7a和上帽12的内表面12b之间,以便密封体7的上表面7a粘合于上帽12的内表面12b,这可能降低上表面7a的温度。粘合剂16更优选地布置为覆盖整个上表面7a。如图45所示,优选地,粘合剂16更优选地布置在密封体7的下表面7b和下帽13的内表面13a之间。尽管密封体7的下表面7b与上表面7a相比更远离导线5,但粘合剂16也布置在下表面7b侧上,这可以降低整个密封体7的温度。此外,从减小间隙SK的角度来看,粘合剂16优选地设置在密封体7的侧面7c处。然而,如上所述由于粘合剂16包含金属颗粒,所以粘合剂16不应当优选地布置在密封体7的侧面7c上,以防止引脚3和金属颗粒之间的接触。由于在本实施例中预先形成了密封体7,如图46所示,阻挡条(阻挡部)22必须设置在引线框20中以防止树脂7p泄露。图46是示出在图42所示的密封形成步骤中在图18所示的引线框中形成密封体7的放大平面图。图46中所示的阻挡条(阻挡部)22与引脚3一体形成以连接相邻的引脚3,并且布置成围绕密封体7。在图42所示的密封体形成步骤中,阻挡条22阻止了树脂7p的泄露。由于密封体7必须存储在帽11中,所以阻挡条22必须设置在密封粘合区3e(见图13)的内侧上(在图13中所示的接合区3c侧上)。阻挡条22是用于连接引脚3的金属部件。为了分离相邻的引脚3,阻挡条22必须在帽接合步骤(见图42)之前切割。也就是,如图42所示,阻挡切割步骤必须在密封体形成步骤之后和帽接合步骤之前执行。在阻挡切割步骤中,切割了布置在相邻的引脚3之间的每个阻挡条22。切割阻挡条的方式并没有具体地限定,但阻挡条可以通过利用冲压机和模具(未示出)挤压来切割。在第一和第二实施例中描述的半导体器件10和50的制造方法中,密封剂14用作阻挡部,并且因此可以省略阻挡切割步骤,这是优选的。本实施例的半导体器件及其制造方法与第一实施例的相同,除了上述的区别之外。因此,将省略其重复描述,并且除了上述区别之外,本实施例可以应用第一实施例中描述的本发明的方面。已描述了本实施例作为第一实施例中描述的半导体10及其制造方法的修改实例,并且应用时本实施例也可以与第二实施例中描述的修改实例结合。<其它修改实例>已经基于实施例具体描述了由本发明人提出的本发明,但本发明并不限于公开的实施例。很显然,可以在不脱离本发明的范围的情况下进行各种修改和变形。例如,第一至第三实施例已经描述了安装在一个封装(半导体器件)中的两个半导体芯片1和6。然而,半导体芯片的数量不限于两个,并且本发明可以应用于具有一个半导体芯片的半导体器件或者具有三个或更多个半导体芯片的半导体器件。例如,如图4所示,在具有在其上层叠的半导体芯片1和6的半导体器件10中,导线5靠近密封体7的上表面7a。当在密封体7的上表面7a处造成裂缝时,裂缝很可能到达导线5。然而,应用上述实施例中描述的技术可以有效地提高半导体器件的可靠性。例如,在上述的第一至第三实施例的描述中,凸缘12e和13e不仅设置在沿着上帽12和下帽13的各个侧面的部分处,而且设置在角12k和13k处。然而,在作为图47中的修改实例示出的半导体器件54中,凸缘12e没有设置在密封体形成步骤中用作用于树脂的供应口的角处(在图47中所示的角12k1处)。图47示出了图1的修改实例的平面图,以及图48示出了图31的修改实例的放大截面图。如图48所示,凸缘12e和13e没有设置在布置了模塑模具40的门40G的角20k1、12k1、13k1处,这便于供应树脂7p。在布置了排放孔40B的其他角20k、12k和13k处,设置凸缘12e和13e以增加静压力,这样可以减小树脂7p的泄漏量。设置凸缘12e和13e可以增加密封剂14的接合表面的面积,从而提高了上帽12和下帽13之间的接合强度。例如,上述修改实例可以与第二实施例和/或第三实施例中描述的技术组合应用。本发明可以应用于树脂密封的半导体器件。