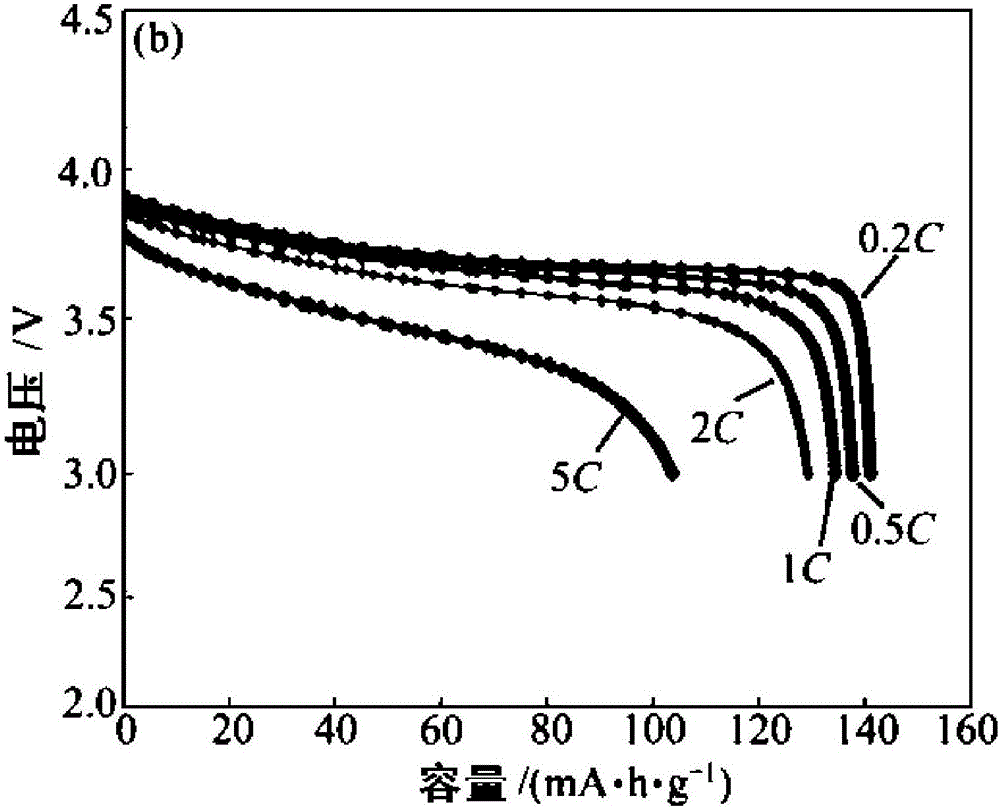
本发明锂离子电池
技术领域:
,具体涉及一种高功率密度锂离子电池。
背景技术:
:目前锂离子电池以高能量密度、循环寿命长、自放电小、无记忆效应、环境友好等优点,迅速成为多数电子类产品不可或缺的一部分。如,手机,笔记本,数码相机等。但锂离子电池的功率密度较低,大倍率电流放电正极材料克容量发挥低,同时循环性能差。限制了锂离子电池在很多方面的应用,如新能源汽车、太阳能、风能等领域。人们为了解决上述问题,提高了正极中导电剂的质量百分比,但这种方法会降低锂离子电池的能量密度。因此,寻找其他的解决途径,在不降低能量密度的前提下,提高了锂离子电池的功率密度非常有必要。目前,锂离子电池行业提高功率的主要方法:(1)通过正极材料掺杂金属元素或颗粒表面改性等达到提高正极材料的导电率,公开号CN103296249A公开了“掺杂改性锂镍钴锰、制备方法及锂离子电池”,通过掺杂改性锂镍钴锰的二次颗粒由一次颗粒组成,二次颗粒为球状或类球状,一次颗粒的表面非均匀掺杂有纳米金属氧化物层;制备方法是在锂镍钴锰的前驱体合成阶段对其掺杂纳米金属氧化物而进行掺杂改性。采用本发明掺杂改性锂镍钴锰作为正极活性材料的锂离子电池,在充放电条件下,具有良好的循环性和热稳定性,可以有效满足锂离子电池的高能量密度、高功率密度;(2)提高负极材料导电率,公开号CN103178243A公开了“锂离子电池用石墨烯/金属复合负极材料及其制备方法”,通过化学刻蚀制备得到光栅结构的金属电极及氧化还原化学法制备得到石墨烯/二氧化钛复合粒子,并采用电化学沉积法在光栅结构的金属电极上沉积石墨烯/二氧化钛复合粒子,进一步热处理获得石墨烯/金属复合负极材料。本发明利用纳米二氧化钛粒子用作石墨烯堆叠的改性,金属光栅结构作为石墨烯载体,使之垂直于集流体排成阵列,这种结构既减小了锂离子在石墨烯片层之间的扩散距离,同时也使锂离子在石墨烯片层间的嵌入、脱出更加快速,因而所得复合材料作为锂离子电池负极时,具有高的比容量,优异的循环稳定性和倍率性能,有望用于高能量密度、高功率密度的锂离子电池负极材料;实际正负极材料本身容量问题很小,也有能达到实际的功率效果潜力,但生产或制作电池的过程中,却往往材料的后处理及工艺工序确实人们最容易忽略的,其对材料容量发挥的影响也是非常大的,因此会造成本身材料性能良好,而在实际电池生产制作过程中容量发挥不正常,进而影响电池的整体性能,造成电池容量低,内阻大,功率密度低等情况。技术实现要素:本发明的发明目的在于:为解决上述存在的问题,本发明的目的在于提供一种高功率密度锂离子电池,通过正负极片对应的铜箔和铝箔的处理和增加导电膜,提高了锂离子电池的导电率,进而提升了电池的大倍率放电性能,同时使用低分子量的正极粘结剂PVDF,使正负极片的厚度反弹更小,降低了极片厚度对离子传递产生的阻碍,减小了电池内阻,进一步提高了电池容量的发挥,促进了电池功率密度的提升。为了实现上述目的,本发明采用的技术方案如下:本发明一种高功率密度锂离子电池,包括正极片和负极片;所述正极片包括铝箔、正极导电剂和正极粘结剂;所述负极片包括铜箔和负极导电剂;所述正极粘结剂为PVDF,且分子量为30~70万;所述铜箔和所述铝箔在制作极片前先进行表面处理,然后在铝箔和铜箔表面附着一层导电膜,所述导电膜的厚度为1~5μm。正极粘结剂目前市面上使用的PVDF的分子量均为70万分子量以上的,正极材料涂布成正极片再经过滚压,PVDF固化后,极片厚度反弹较大,而且PVDF的分子量越大,极片厚度滚压后和充放电后反弹值也越大,;而使用低分子量的PVDF,可以有效地减小正极片滚压后的反弹,也能减小电池充放电后极片的厚度反弹,从而减小极片厚度对锂离子迁移或电子传递的距离,较好的降低了电池的内阻,也减少了电池的发热量,提高了电池能量的利用率。本发明的正极片在涂布正负极极片前,先在铝箔或铜箔上附着一层导电膜,该导电膜可以由重量比95~98:2~5的石墨烯和所述PVDF组成,且用静电喷涂货丝网印刷在铝箔上;也可以由石墨烯组成,且导电膜利用气相沉积法附着在铝箔上。因石墨烯的导电能力非常强,使用石墨烯作为导电膜,可以增加正极片的电导率,降低内阻,提高正极材料容量的发挥,进而达到提升电池容量的效果。在附着导电膜之前,本发明对铜箔和铝箔的表面处理,处理方法包括以下步骤:(1)除油:将铝箔或铜箔先放入0.5~2mol/L的碱溶液中浸泡10~30min,然后用去离子水冲洗;(2)除锈:将除油水洗后的铝箔或铜箔放入1.0~5.0mol/L酸溶液中浸泡3~10min,然后用去离子水冲洗;本发明所述碱溶液中的碱为氢氧化钠、氢氧化钾、氢氧化钙或碳酸氢钠一种或几种的混合物;而酸溶液中的酸为硫酸、盐酸或硝酸中的一种或几种混合物;铜箔或铝箔使用碱溶液和酸溶液进行处理,可以快速达到出去表面油渍和氧化物的目的,可以使铜箔或铝箔中的铜或铝充分与导电剂接触,降低了接触电阻,提高了极片的导电率。综上所述,由于采用了上述技术方案,本发明的有益效果是:本发明采用用低分子量的PVDF作为正极粘结剂减小正极片厚度的反弹率,从而减小极片厚度对锂离子迁移或电子传递的距离,较好的降低了电池的内阻,也减少了电池的发热量,提高了电池能量的利用率;同时,通过正负极片对应的铜箔和铝箔的处理和增加导电膜,提高了锂离子电池的导电率,进而提升了电池的大倍率放电性能,同时使用低分子量的正极粘结剂PVDF,使正负极片的厚度反弹更小,降低了极片厚度对离子传递产生的阻碍,减小了电池内阻,进一步提高了电池容量的发挥,促进了电池功率密度的提升。【附图说明】图1是本发明实施例1的电池铜箔和铝箔未进行处理的不同电流的放电比容量曲线。图2是本发明对照组1的电池铜箔和铝箔已进行处理的不同电流的放电比容量曲线。【具体实施方式】以下通过具体实施例及附图及数据表对本发明作进一步详述。实施例1一种高功率密度锂离子电池,包括正极片和负极片;所述正极片包括铝箔、正极导电剂和正极粘结剂;所述负极片包括铜箔和负极导电剂;所述正极粘结剂为PVDF,且分子量为30~50万;所述铜箔和所述铝箔在制作极片前先进行表面处理,然后在铝箔和铜箔表面附着一层导电膜,所述导电膜的厚度为1μm。正极片在涂布正负极极片前,先在铝箔或铜箔上附着一层导电膜,该导电膜可以由重量比95:5的石墨烯和所述PVDF组成,且用静电喷涂货丝网印刷在铝箔上;也可以由石墨烯组成,且导电膜利用气相沉积法附着在铝箔上。因石墨烯的导电能力非常强,使用石墨烯作为导电膜,可以增加正极片的电导率,降低内阻,提高正极材料容量的发挥,进而达到提升电池容量的效果。在附着导电膜之前,本发明对铜箔和铝箔的表面处理,处理方法包括以下步骤:(1)除油:将铝箔或铜箔先放入0.5mol/L的碱溶液中浸泡10min,然后用去离子水冲洗;(2)除锈:将除油水洗后的铝箔或铜箔放入1.0mol/L酸溶液中浸泡3min,然后用去离子水冲洗;其中,碱溶液中的碱为氢氧化钠;而酸溶液中的酸为硫酸。实施例2一种高功率密度锂离子电池,包括正极片和负极片;所述正极片包括铝箔、正极导电剂和正极粘结剂;所述负极片包括铜箔和负极导电剂;所述正极粘结剂为PVDF,且分子量为50~70万;所述铜箔和所述铝箔在制作极片前先进行表面处理,然后在铝箔和铜箔表面附着一层导电膜,所述导电膜的厚度为5μm。正极片在涂布正负极极片前,先在铝箔或铜箔上附着一层导电膜,该导电膜可以由重量比98:2的石墨烯和所述PVDF组成,且用静电喷涂货丝网印刷在铝箔上;也可以由石墨烯组成,且导电膜利用气相沉积法附着在铝箔上。因石墨烯的导电能力非常强,使用石墨烯作为导电膜,可以增加正极片的电导率,降低内阻,提高正极材料容量的发挥,进而达到提升电池容量的效果。在附着导电膜之前,本发明对铜箔和铝箔的表面处理,处理方法包括以下步骤:(1)除油:将铝箔或铜箔先放入2mol/L的碱溶液中浸泡30min,然后用去离子水冲洗;(2)除锈:将除油水洗后的铝箔或铜箔放入5.0mol/L酸溶液中浸泡10min,然后用去离子水冲洗;其中,碱溶液中的碱为氢氧化钾;而酸溶液中的酸为盐酸。实施例3一种高功率密度锂离子电池,包括正极片和负极片;所述正极片包括铝箔、正极导电剂和正极粘结剂;所述负极片包括铜箔和负极导电剂;所述正极粘结剂为PVDF,且分子量为50~70万;所述铜箔和所述铝箔在制作极片前先进行表面处理,然后在铝箔和铜箔表面附着一层导电膜,所述导电膜的厚度为3μm。正极片在涂布正负极极片前,先在铝箔或铜箔上附着一层导电膜,该导电膜可以由重量比96:4的石墨烯和所述PVDF组成,且用静电喷涂货丝网印刷在铝箔上;也可以由石墨烯组成,且导电膜利用气相沉积法附着在铝箔上。因石墨烯的导电能力非常强,使用石墨烯作为导电膜,可以增加正极片的电导率,降低内阻,提高正极材料容量的发挥,进而达到提升电池容量的效果。在附着导电膜之前,本发明对铜箔和铝箔的表面处理,处理方法包括以下步骤:(1)除油:将铝箔或铜箔先放入1.2mol/L的碱溶液中浸泡20min,然后用去离子水冲洗;(2)除锈:将除油水洗后的铝箔或铜箔放入3.5mol/L酸溶液中浸泡7min,然后用去离子水冲洗;其中,碱溶液中的碱为氢氧化钙和碳酸氢钠1:1的混合物;而酸溶液中的酸为硝酸。效果验证:以容量为3700mAh的856068型号锂离子电池为例。电池电芯的标准尺寸为厚度7.6mm,宽度50.0mm,长度68.0mm,本发明用磷酸锰铁锂的正极材料对应电池的标准体积能量密度为426.7Wh/L。实验组:实验组采用实施例1~3的材料及其组成进行组装电池进行试验,电池的组装工艺如下:(1)正极的制备:钴酸锂为正极活性物质,超级导电碳黑(SP)为导电剂,聚偏氟乙烯(PVDF)为粘结剂,N-二甲基吡咯烷酮(NMP)为溶剂。制备浆料粘度控制为2000~8500mPa·s。本实施例所用质量百分比为钴酸锂:SP:PVDF=97:1.4:1.6。首先将PVDF充分溶于NMP中制成胶液,继续添加SP搅拌均匀,最后加入钴酸锂持续搅拌均匀后抽真空,除去浆料中的气泡。最后将所得浆料双面均匀的涂敷在12μm厚度的铝箔上。经干燥,辊压,裁片后进行极耳焊接,极耳厚度为0.1mm。完成正极片制作。(2)负极的制备:以石墨为负极活性物质,导电剂为高电导率的乙炔黑,粘结剂为水性丁苯橡胶乳SBR和羧甲基纤维素钠CMC的组合物,水为溶剂。制备浆料粘度控制为1000~4500mPa·s。本实施例所用质量百分比为石墨:AB:CMC:SBR=96.5:1:1:1.5。首先将CMC充分溶于水中制成胶液,继续添加AB搅拌均匀,在加入石墨持续搅拌均匀后加入SBR搅拌1.5h,抽真空,除去浆料中的气泡。最后将所得浆料双面均匀的涂敷在8μm厚度铜箔上。经干燥,辊压,裁片后进行极耳焊接,极耳厚度为0.1mm。完成负极片制作。(3)电池组装:隔膜采用厚度为12μm的微孔聚乙烯膜。铝塑膜厚度为113μm。将制备好的正、负极片和隔膜卷绕成卷芯,进行一次封装、注液并进行封装,在经化成、二次封装完成电池制作。对照组:以与实验组同型号的电池进行组装测试。对照组的材料为与实验组相同的钴酸锂和石墨,正极片制作时,正极粘结剂的分子量分别为70~100万和100~120万的PVDF,材料的配比及用量与实验组相同,而且铝箔不先附着任何导电膜按常规工艺直接涂布正极材料,并按照实验组进行电池的组装。为方便对比,对照组的其他参数均与实验组相同,具体结果见表1和2所示:表1正极片滚压后的厚度与极片卷绕前反弹的厚度滚压后正极极片厚度/mm卷绕前正极片厚度/mm正极片反弹率实施例10.1940.2013.61%实施例20.1950.2055.13%实施例30.1940.2034.64%对照组10.1950.2107.69%对照组20.1950.22314.36%表2对照组和实验组的电池参数对比从表1和表2可以看出:正极粘结剂PVDF的分子量越大,正极片的反弹率更大,导致极片更厚,影响电池的整体厚度,进而降低了电池的体积能量密度;而负极片的厚度也随着高锰酸钾与石墨化中间相碳微球的重量比的增加而减小。使用纳米碳片/石墨化中间相碳微球复合材料比使用石墨化中间相碳微球制得的电池体积能量密度更高,而且需要的负极材料更好,负极极片厚度更薄;另外,铝箔上增加导电膜,可以降低电池内阻。再选择实施例1和对照组2所制作的电池用不同倍率的电流进行放电,具体见附图1和附图2所示。从附图1和2中可以看出:随着放电电流的增大,铜箔和铝箔进行处理且增加了导电膜的电池放电性能比铜箔和铝箔未进行处理且无导电膜倍率性能更好,说明本发明通过铜箔铝箔的除油去氧化层,以及在铜箔铝箔上附着导电膜可以较好的提高电池的放电倍率性能,提高电池的功率密度。当前第1页1 2 3