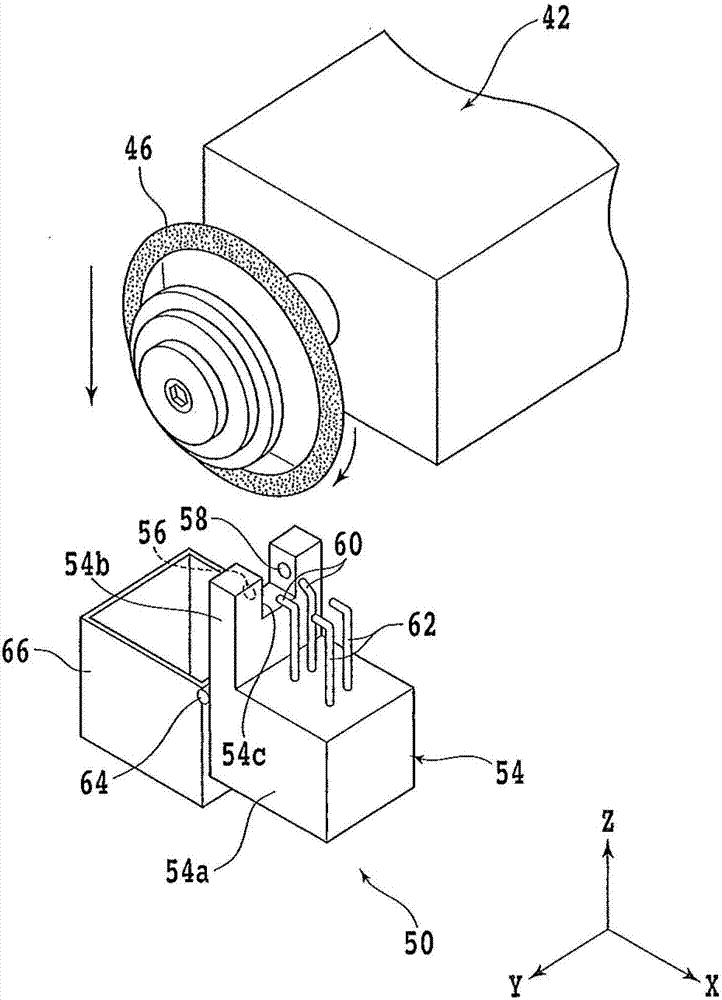
本发明涉及切削装置的设置方法,对安装有切削刀具的切削单元的位置进行调整。
背景技术:
:在对以半导体晶片为代表的板状的被加工物进行切削时,例如,使用安装有环状的切削刀具的切削装置。一边使该切削刀具旋转并切入被加工物,一边使被加工物与切削刀具相对地移动,由此,能够对被加工物进行切削。但是,当通过上述那样的切削装置对被加工物进行切削时,随着切削刀具的磨损进展其直径逐渐变小。当继续使用直径因磨损而变小的切削刀具时,切削刀具相对于被加工物的切入变浅,无法合适地切削被加工物。因此,实用化了如下的设置方法:在任意的时机对切削刀具的前端(下端)的位置进行检测,并以该前端的位置为基准对切削刀具的切入深度进行控制(例如,参照专利文献1、2)。在该设置方法中,例如,使旋转的切削刀具相对于位于切削刀具的下方的光学式的传感器下降,通过切削刀具来遮挡传感器内的光路从而对切削刀具的前端的位置进行检测。专利文献1:日本特开2001-298001号公报专利文献2:日本特开2013-251457号公报但是,在上述的设置方法中,例如,当使切削刀具下降而侵入传感器内时,由于切削刀具的旋转和传感器的形状等相互作用而导致切削刀具的周围的气流改变。其结果是,有时随着切削刀具而旋转的切削液会落下并附着在传感器上,无法准确地对切削刀具的前端的位置进行检测。技术实现要素:本发明是鉴于该点而完成的,其目的在于,提供切削装置的设置方法,能够降低切削液的影响而准确地对安装有切削刀具的切削单元的位置进行检测。根据本发明的一方式,提供切削装置的设置方法,使用切削装置对切削刀具的前端的位置进行检测,该切削装置具有:卡盘工作台,其将被加工物保持在保持面上;切削单元,在该切削单元中安装有该切削刀具,该切削刀具对该卡盘工作台所保持的被加工物进行切削;切削液提供单元,其向该切削刀具提供切削液;移动机构,其使该切削单元在与该保持面垂直的切入进给方向上移动;刃尖位置检测单元,其具有夹着供该切削刀具侵入的刀具侵入部而对置的发光部和受光部,该刃尖位置检测单元对该切入进给方向上的该切削刀具的前端的位置进行检测;以及控制单元,其对各构成要素进行控制,该切削装置的设置方法的特征在于,具有如下的步骤:提供停止步骤,停止向该切削刀具提供切削液;除水步骤,在实施了该提供停止步骤之后,使该切削单元在该切入进给方向上移动,在使旋转的该切削刀具侵入到该刀具侵入部中之后,使该切削刀具从该刀具侵入部退避,由此,使该切削刀具的周围的气流变化,使随着该切削刀具而旋转的切削液向周围飞散;以及位置检测步骤,在实施了该除水步骤之后,使旋转的该切削刀具再次侵入到该刀具侵入部中,对该受光部的受光量成为规定的光量时的该切削单元的位置进行检测。在本发明的一方式中,优选该刃尖位置检测单元具有向该受光部和该发光部的端面提供空气的空气提供部,在该除水步骤中从该空气提供部提供空气。在本发明的一方式的切削装置的设置方法中,由于在对切削单元的位置进行检测的位置检测步骤之前实施使随着切削刀具而旋转的切削液向周围飞散的除水步骤,所以在实施位置检测步骤时,切削液很难附着在刃尖位置检测单元的发光部和受光部上。因此,能够降低切削液的影响而准确地检测切削单元的位置。附图说明图1是示意性示出切削装置的结构例的立体图。图2是对刃尖位置检测单元进行放大的立体图。图3是示出设置方法的概要的示意图。图4是示出除水步骤的侧视图。图5是示出位置检测步骤的侧视图。图6是示出切削单元的动向的例子的图表。图7是示出以往的设置方法的侧视图。标号说明11:被加工物;13:带;15:框架;21:切削液;23:光;2:切削装置;4:基台;6:x轴移动机构;8:x轴导轨;10:x轴移动工作台;12:x轴滚珠丝杠;14:x轴脉冲电动机;16:工作台基座;18:卡盘工作台;18a:夹具;18b:保持面;20:水箱;22:支承构造;24:切削单元移动机构(移动机构、移动构件);26:y轴导轨;28:y轴移动板;30:y轴滚珠丝杠;32:y轴脉冲电动机;34:z轴导轨;36:z轴移动板;38:z轴滚珠丝杠;40:z轴脉冲电动机;42:切削单元(切削构件);44:照相机(拍摄单元、拍摄构件);46:切削刀具;48:切削液提供喷嘴(切削液提供单元、切削液提供构件);50:刃尖位置检测单元(刃尖位置检测构件);52:控制单元(控制构件);52a:电压比较部;52b:前端位置检测部;52c:计算部;52d:位置校正部;54:基座;54a:支承部;54b:检测部;54c:刀具侵入部;56:发光部;58:受光部;60:空气提供喷嘴(空气提供部);62:液体提供喷嘴(液体提供部);64:连结件;66:罩;68:光源;70:光电转换部。具体实施方式参照附图对本发明的一方式的实施方式进行说明。本实施方式的切削装置的设置方法包含提供停止步骤、除水步骤(参照图4)和位置检测步骤(参照图5)。在提供停止步骤中,停止切削液向切削刀具的提供。在除水步骤中,通过使切削刀具的周围的气流变化而使随着切削刀具旋转的切削液飞散。在位置检测步骤中,使用刃尖位置检测单元对切削单元的位置进行检测。以下,对本实施方式的切削装置的设置方法进行详述。首先,对在本实施方式中使用的切削装置的例子进行说明。图1是示意性示出本实施方式的切削装置的结构例的立体图。如图1所示,切削装置2具有搭载有各构成要素的基台4。在基台4的上表面上设置有x轴移动机构6。x轴移动机构6具有与x轴方向(加工进给方向、前后方向)平行的一对x轴导轨8,在x轴导轨8上以能够滑动的方式安装有x轴移动工作台10。在x轴移动工作台10的下表面(背面)侧安装有螺母(未图示),与x轴导轨8平行的x轴滚珠丝杠12与该螺母螺合。x轴滚珠丝杠12的一端部与x轴脉冲电动机14连结。通过x轴脉冲电动机14来使x轴滚珠丝杠12旋转,由此,x轴移动工作台10沿着x轴导轨8在x轴方向上移动。在该x轴移动机构6上设置有对x轴移动工作台10的x轴方向的位置进行测定的x轴测定单元(未图示)。在x轴移动工作台10的上表面侧(正面侧)设置有工作台基座16。在工作台基座16的上部配置有用于对被加工物11进行保持的卡盘工作台18。在卡盘工作台18的周围配置有4个夹具18a,该4个夹具18a从四周对支承被加工物11的环状的框架15进行固定。被加工物11例如是由硅等半导体构成的圆形的晶片,其上表面(正面)侧分为中央的器件区域和围绕器件区域的外周剩余区域。器件区域被呈格子状排列的分割预定线(间隔道)进一步划分成多个区域,在各区域内形成有ic、lsi等器件。在被加工物11的下表面(背面)侧粘贴有比被加工物11的直径大的带13。带13的外周部分被环状的框架15固定。即,被加工物11借助带13而支承在框架15上。另外,在本实施方式中,将由硅等半导体构成的圆形的晶片作为被加工物11,但被加工物11的材质、形状等并没有限制。例如,也能够使用由陶瓷、树脂、金属等材料构成的任意的形状的基板来作为被加工物11。卡盘工作台18与电动机(旋转驱动源)(未图示)等连结,绕与z轴方向(切入进给方向、上下方向)大致平行的旋转轴进行旋转。并且,如果通过上述的x轴移动机构6使x轴移动工作台10在x轴方向上移动,则使卡盘工作台18在x轴方向上进行加工进给。卡盘工作台18的上表面成为用于对被加工物11进行保持的保持面18b。该保持面18b相对于x轴方向和y轴方向(分度进给方向、左右方向)大致平行地形成,通过形成于卡盘工作台18和工作台基座16的内部的流路(未图示)等而与吸引源(未图示)连接。另外,在使卡盘工作台18相对于工作台基座16固定时也使用该吸引源的负压。在与卡盘工作台18接近的位置处设置有将被加工物11搬送到卡盘工作台18上的搬送机构(未图示)。并且,在x轴移动工作台10的附近设置有水箱20,该水箱20对在切削时使用的纯水等切削液的废液进行暂时贮存。贮存在水箱20内的废液通过排水管(未图示)等排出到切削装置2的外部。在基台4的上表面上配置有横跨x轴移动机构6的门型的支承构造22。在支承构造22的前表面上部设置有两组切削单元移动机构(移动机构、移动构件)24。各切削单元移动机构24配置在支承构造22的前表面上并且共同具有与y轴方向大致平行的一对y轴导轨26。在y轴导轨26上以能够滑动的方式安装有构成各切削单元移动机构24的y轴移动板28。在各y轴移动板28的背面侧设置有螺母(未图示),与y轴导轨26平行的y轴滚珠丝杠30分别与该螺母螺合。各y轴滚珠丝杠30的一端部与y轴脉冲电动机32连结。如果通过y轴脉冲电动机32使y轴滚珠丝杠30旋转,则y轴移动板28沿着y轴导轨26在y轴方向上移动。在各y轴移动板28的前表面(正面)上设置有与z轴方向大致平行的一对z轴导轨34。在z轴导轨34上以能够滑动的方式安装有z轴移动板36。在各z轴移动板36的背面侧设置有螺母(未图示),与z轴导轨34平行的z轴滚珠丝杠38分别与该螺母螺合。各z轴滚珠丝杠38的一端部与z轴脉冲电动机40连结。如果通过z轴脉冲电动机40使z轴滚珠丝杠38旋转,则z轴移动板36沿着z轴导轨34在z轴方向上移动。在各切削单元移动机构24上设置有对y轴移动板28的y轴方向的位置进行测定的y轴测定单元(未图示)。并且,在各切削单元移动机构24上设置有对z轴移动板36的z轴方向的位置进行测定的z轴测定单元(未图示)。在各z轴移动板36的下部设置有用于对被加工物11进行切削的切削单元(切削构件)42。并且,在与切削单元42相邻的位置处设置有用于对被加工物11进行拍摄的照相机(拍摄单元、拍摄构件)44。如果通过各切削单元移动机构24使y轴移动板28在y轴方向上移动,则对切削单元42和照相机44进行分度进给,如果使z轴移动板36在z轴方向上移动,则切削单元42和照相机44升降。另外,通过上述的x轴测定单元对切削单元42和照相机44相对于卡盘工作台18等的x轴方向上的位置进行测定。并且,通过上述的y轴测定单元对切削单元42和照相机44相对于卡盘工作台18等的y轴方向上的位置进行测定。进而,通过上述的z轴测定单元对切削单元42和照相机44相对于卡盘工作台18等的z轴方向上的位置进行测定。切削单元42具有大致与y轴方向平行的作为旋转轴的主轴(未图示)。在主轴的一端侧安装有环状的切削刀具46。主轴的另一端侧与电动机(旋转驱动源)(未图示)等连结,切削刀具46通过经由主轴传递的电动机的转矩而进行旋转。并且,在切削刀具46的附近设置有对被加工物11、切削刀具46等提供纯水等切削液的切削液提供喷嘴(切削液提供单元、切削液提供构件)48。在切削刀具46的下方配置有刃尖位置检测单元(刃尖位置检测构件)50,该刃尖位置检测单元50对切削刀具46的前端(下端)在z轴方向上的位置进行检测。x轴移动机构6、卡盘工作台18、搬送机构、切削单元移动机构24、切削单元42、照相机44以及刃尖位置检测单元50等构成要素分别与控制单元(控制构件)52连接。该控制单元52按照被加工物11的加工条件等对上述的各构成要素进行控制。图2是对刃尖位置检测单元50进行放大的立体图。如图2所示,刃尖位置检测单元50具有搭载各构成要素的基座54。基座54包含大致长方体状的支承部54a和竖立在支承部54a的后端侧(x轴方向的一侧)的检测部54b。在检测部54b的上端部,形成有按照能够供切削刀具46侵入的方式进行了切口的刀具侵入部54c。刀具侵入部54c具有在y轴方向上对置的一对内侧面,在该一对内侧面上分别配置有发光部56和受光部58,该发光部56和受光部58构成光学式的传感器。即,发光部56与受光部58夹着刀具侵入部54c而对置。在位于检测部54b的前方侧(x轴方向的另一侧)的支承部54a的上表面上设置有两根用于向发光部56和受光部58提供空气的空气提供喷嘴(空气提供部)60。并且,在与空气提供喷嘴60相邻的位置处设置有两根用于向发光部56和受光部58提供水等液体的液体提供喷嘴(液体提供部)62。例如在利用来自液体提供喷嘴62的液体对发光部56和受光部58进行清洗之后,利用来自空气提供喷嘴60的空气进行干燥。长方体状的罩66借助由铰链等构成的连结件64而安装在基座54的后端面上。该罩66的内部是空洞。因此,例如,通过使罩66以连结件64为中心旋转至关闭位置,能够将检测部54b、空气提供喷嘴60、液体提供喷嘴62等收纳在罩66的内部。另一方面,在通过刃尖位置检测单元50对切削刀具46的前端的位置进行检测时,通过使罩66旋转至图2所示的打开位置而使检测部54b、空气提供喷嘴60以及液体提供喷嘴62等露出。由此,能够使切削刀具46侵入到刀具侵入部54c中而对切削刀具46的前端的位置进行检测。接着,对通过该切削装置2实施的设置方法的概要进行说明。图3是示出设置方法的概要的示意图。首先,从经由光纤等与发光部56连接的光源68产生光,从发光部56向受光部58照射该光。照射在受光部58上的光通过光纤等被发送给光电转换部70。光电转换部70例如由1个或多个光电转换元件构成,将从受光部58发送的光转换成电压而输出。与从光电转换部70输出的电压有关的信息例如被发送给控制单元52内的电压比较部52a。电压比较部52a对从光电转换部70输出的电压与任意的基准电压(阈值电压)进行比较而将该结果输出给前端位置检测部52b。前端位置检测部52b根据电压比较部52a的输出和来自切削单元移动机构24(z轴测定单元)的信号对切削刀具46的前端(下端)的位置进行检测。具体来说,例如,前端位置检测部52b检测从光电转换部70输出的电压达到了上述的基准电压(基准电压以下)时的切削单元42的z轴方向的位置作为切削刀具46的前端(下端)的位置。与前端位置检测部52b检测出的切削刀具46的前端(下端)的位置有关的信息被发送给计算部52c。计算部52c根据从前端位置检测部52b通知的切削刀具46的前端的位置对z轴方向上的切削刀具46(切削单元42)的位置的校正量进行计算。另外,该计算部52c也可以根据切削刀具46的前端的位置的变化等对切削刀具46的磨损量进行计算。将计算部52c计算出的z轴方向上的切削刀具46(切削单元42)的位置的校正量(或磨损量)通知给位置校正部52d。位置校正部52d根据从计算部52c通知的校正量(或磨损量)对切削刀具46(切削单元42)的z轴方向的位置进行校正。接着,对本实施方式的切削装置的设置方法进行详述。在本实施方式的切削装置的设置方法中,例如,在被加工物11的加工前、加工中或加工后的任意的时机实施提供如下的停止步骤:停止向旋转的切削刀具46提供切削液。由此,不向切削刀具46提供新的切削液。但是,在实施了提供停止步骤之后切削刀具46仍继续旋转。因此,在实施提供停止步骤之前提供给切削刀具46的切削液的一部分在附着于切削刀具46的状态下与切削刀具46一同(随着切削刀具46)继续旋转。在提供停止步骤之后实施如下的除水步骤:使切削刀具46的周围的气流变化(混乱)从而使与切削刀具46一同旋转的切削液飞散。图4是示出除水步骤的侧视图。在该除水步骤中,首先,将切削刀具46定位在刀具侵入部54c的上方,该刀具侵入部54c设置在刀尖位置检测单元50上。接着,通过切削单元移动机构24使切削单元42下降,使旋转的切削刀具46侵入到刃尖位置检测单元50的刀具侵入部54c中。由此,由于切削刀具46的周围的气流因刃尖位置检测单元50而变化(混乱),所以与切削刀具46一同旋转的切削液21向周围飞散。接着,使切削刀具46退避到刀具侵入部54c的上方。另外,优选一边从空气提供喷嘴60对发光部56和受光部58提供空气一边实施该除水步骤。由此,从切削刀具46飞散并落下的切削液21很难附着在发光部56和受光部58上。在除水步骤之后实施位置检测步骤,使用刃尖位置检测单元50对切削单元42的位置进行检测。图5是示出位置检测步骤的侧视图。如图5所示,在该位置检测步骤中,一边从发光部56向受光部58照射光23一边使切削单元42下降,使旋转的状态下的切削刀具46再次侵入到刀具侵入部54c中。由此,如图5所示,从发光部56照射到受光部58的光23被切削刀具46局部遮挡,受光部58的受光量达到规定的阈值(成为规定的阈值以下)。在电压比较部52a中作为阈值使用的基准电压与该受光量的阈值对应地设定。因此,当受光部58的受光量达到规定的阈值(成为规定的阈值以下)时,从光电转换部70输出的电压也达到基准电压(成为基准电压以下)。并且,检测此时的切削单元42的z轴方向的位置作为切削刀具46的前端(下端)的位置。另外,实施该位置检测步骤的次数并没有限制。例如,可以在除水步骤之后仅实施1次位置检测步骤,也可以在除水步骤之后连续或断续地实施好几次位置检测步骤。图6是示出设置方法中的切削单元42的动向的例子的图表。另外,在图6中,横轴表示时间(t),纵轴表示切削单元的z轴方向上的位置(z)。并且,时间段t0~t1与除水步骤对应,时间段t1~t2、时间段t2~t3、时间段t3~t4分别与位置检测步骤对应。即,在图6所示的例子中,在除水步骤之后连续地实施3次位置检测步骤。由于除水步骤的目的是使随着切削刀具46旋转的切削液21向周围飞散,所以在该除水步骤中,如图6所示,可以使切削单元24以比位置检测步骤中的速度快的速度进行移动。由此,能够缩短设置所需的时间。并且,在除水步骤中,不需要如位置检测步骤那样使切削单元42下降至受光部58的受光量达到规定的阈值(成为所定的阈值以下)位置z2。例如,在图6所示的例中,使切削单元42下降至切削刀具46稍微侵入到刀具侵入部54c中的位置z1。另外,位置z0是切削单元42的零点(作为基准的位置)。这样,在本实施方式的切削装置的设置方法中,由于在对切削单元42的位置进行检测的位置检测步骤之前实施除水步骤,使随着切削刀具46旋转的切削液21向周围飞散,所以在实施位置检测步骤时,切削液21很难附着在刃尖位置检测单元50的发光部56和受光部58上。因此,能够降低切削液21的影响而对切削单元42的位置进行准确地检测。图7是示出以往的设置方法的侧视图。如图7所示,在以往的设置方法中,由于不实施本实施方式那样的除水步骤,所以从切削刀具46飞散并落下的切削液21容易附着在发光部56和受光部58上,无法准确地检测切削单元42的位置的可能性较高。与此相对,在本实施方式中,由于在位置检测步骤之前实施除水步骤,所以与以往的设置方法相比容易准确地检测切削单元42的位置。接着,对为了确认本实施方式的切削装置的设置方法的效果而进行的实验进行说明。在该实验中,分别多次试验了本实施方式的设置方法和以往的设置方法,在各试验的前后在受光部的受光量中产生规定的差的情况(也就是说,在发光部或受光部上附着有规定的分量的切削液的情况)下进行重试(再试验),并对其次数进行了确认。实验的结果如表1所示。另外,在表1中,将检测到的前端的位置的偏差精度(3σ)一并示出。【表1】实施方式的方法以往的方法总次数199次324次重试次数2次135次重试发生率1%42%偏差精度(3σ)0.57μm0.97μm如表1所示,在以往的设置方法的情况下,重试的发生率为42%,而在上述实施方式的设置方法的情况下,重试的发生率大幅改善至1%。并且,偏差精度(3σ)也从0.97μm改善至0.57μm。认为偏差精度(3σ)的改善也是由于切削液很难附着在发光部和受光部上。另外,上述实施方式的构造、方法等在不脱离本发明目的的范围内能够实施适当变更。当前第1页12