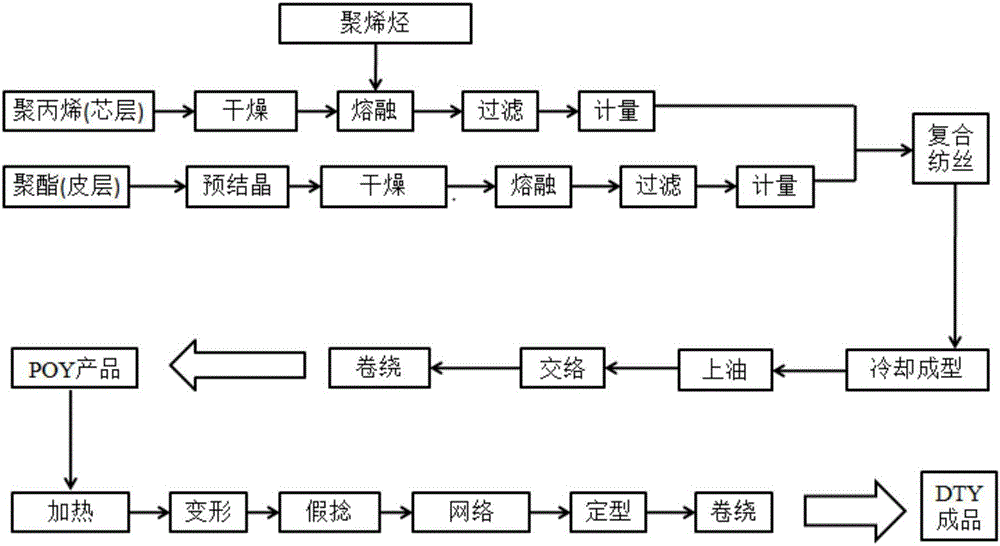
本发明涉及一种纤维及其制备方法,尤其是一种复合弹性纤维及其制备方法。
背景技术:
:聚丙烯纤维商品名为丙纶,聚丙烯比重轻,强度高,耐腐蚀耐磨抗污性和织造性好,且价格低廉,广泛地用于地毯基布和背衬材料,是世界地毯制造业的第二大原料,丙纶地毯占我国生产的化纤地毯为90﹪。但丙纶地毯档次不高,主要有三大缺点:一是不耐燃,二是静电强,三是耐倒伏性差。聚丙烯限氧指数LOI只有17.0~18.5,属易燃热塑性纤维,现有解决聚丙烯纤维及纺织品的阻燃方法是在生产过程中进行阻燃改性和阻燃整理;聚丙烯纤维的吸湿性和染色性在化学纤维中是最差的,几乎不吸湿,其回潮率小于0.03%,摩擦产生的静电大,现有生产技术是生产过程中添加抗静剂和抗静电整理;聚丙烯纤维耐倒伏性差是其初始模量只有27eN/dtex,且弹性差,现有生产技术从两个方面解决丙纶的耐倒伏性:一是提高丙纶的模量,使之不易变形,二是对丙纶进行改性提高其回弹性能。这些技术都是采用单组份纺丝技术,只能进行一种功能改性或进行单一功能的后整理,无法同时克服易燃、静电大、易倒伏三大缺点,且稳定性差。技术实现要素:基于此,本发明的目的在于克服上述现有技术的不足之处而提供一种同时具有阻燃、抗静电、抗倒伏三种性能的复合弹性纤维。为实现上述目的,本发明所采取的技术方案为:一种复合弹性纤维,所述复合弹性纤维包括芯层、包裹在所述芯层外表面的皮层;所述芯层采用聚丙烯和聚烯烃制备而成;所述皮层采用聚酯制备而成。本发明所述复合弹性纤维,兼有皮层和芯层材料的性能,所述皮层和芯层的选择,可以使该复合弹性纤维既有涤纶纤维强度高、悬垂性好及爽滑性,又有改性丙纶纤维弹性好及较强的芯吸作用。包裹的涤纶皮层模量高达132eN/dtex,聚丙烯分子加入聚烯烃变成弹性体;两方面共同作用,可以增加纤维的回弹性。优选地,所述皮层和芯层的质量比为1:1~7:3。本申请发明人经过大量尝试发现,上述比例的皮层和芯层,能更好的使复合弹性纤维充分发挥皮层和芯层材料的性能,使阻燃、抗静电、抗倒伏三种性能兼顾的更好。更优选地,所述芯层中,聚丙烯和聚烯烃的质量比为1:9~3:7。通过工艺筛选,此质量比范围内的聚丙烯和聚烯烃混合,能更好的使聚丙烯变成弹性性能较好的弹性体,可以更好的增加纤维的回弹性。优选地,所述芯层和皮层之间有缝隙,赋予复合纤维导湿性能和抗静电性。优选地,所述芯层的单丝纤度小于2dtex,纤维比表面积大,芯吸过程毫无阻碍,油污和水沿芯层与皮层的缝隙渗透极为容易,因此纤维织物具有极强的清洁功能和高吸水性。优选地,所述皮层的径向剖面为圆形,所述芯层的径向剖面为表面带翼形的圆环。有别于普通皮芯结构,本发明所述皮层表面设有翼形结构,翼形纤维结构具有更好的抗倒伏性能。同时,本发明还提供一种上述复合弹性纤维的制备方法,所述方法包括如下步骤:(1)将制成含水率小于30PPM的聚酯干切片,经第一螺杆挤出机挤出,进入纺丝箱体,得到皮层料;(2)将聚烯烃切片添加到聚丙烯切片中均匀混合,经第二螺杆挤出机挤出,进入纺丝箱体,得到芯层料;(3)将步骤(1)制备得到的皮层料和步骤(2)制备得到的芯层料均匀分配到翼形皮芯型复合组件中,挤出皮层初生丝和芯层初生丝,初生丝经过缓冷装置、侧吹风冷却、上油、牵伸卷绕,得到预取向丝束(POY)或全拉伸丝束(FDY);(4)将预取向丝束(POY)或全拉伸丝束(FDY)经过牵伸、加捻、定型、卷绕,得到网络丝,即为所述复合弹性纤维。优选地,所述步骤(1)中,按聚酯添加质量的50%~70%经第一螺杆挤出机挤出。优选地,所述步骤(1)中,聚酯切片的粘度范围为0.6~0.75dl/g,熔点为257~260℃;所述步骤(2)中,聚丙烯切片的熔融指数范围为25~30g/10min,熔点范围为167~170℃。优选地,所述步骤(2)中,按聚丙烯和聚烯烃混合物总质量的30%~50%经第二螺杆挤出机挤出。优选地,所述步骤(1)中,第一螺杆挤出机的设定温度为270℃~290℃,纺丝温度为270℃~295℃;所述步骤(2)中,第二螺杆挤出机的设定温度为200℃~240℃,纺丝温度为230℃~260℃。通过对上述温度的控制,使皮层先固化成型,芯层后固化成型,由于热胀冷缩的作用,芯组份和皮层之间形成永久间隙,赋予复合纤维导湿性能和抗静电性。优选地,所述步骤(3)中,所述皮层初生丝的冷却长度为15~50cm,所述芯层初生丝的冷却长度为15~100cm。优选地,所述步骤(3)中,聚酯组份和聚丙烯组份分别采用两组独立的联苯加热系统进行加热,保证各组分的熔体温度,通过计量泵、纺丝箱体和皮芯型喷丝板形成初生丝,侧吹风冷却的风速为0.4~1.0m/s,侧吹风冷却的温度为15~30℃,侧吹风冷却的相对湿度为60~90%。该复合弹性纤维之所以能产生较强的芯吸作用是复合纺丝过程采用缓冷技术路线:易冷却的皮层组份涤纶在纺丝侧吹风的冷却作用下首先冷却固化成型;被涤纶包裹在芯层的丙纶组分由230~260℃的熔体冷却至常温固化并收缩过程比皮层慢,形成永久间隙,芯组份丙纶混合体的单丝纤度小于2dtex,导湿性能大大提高。优选地,所述步骤(3)中,采用油嘴/油轮上油,纺丝速度为3000~4500m/min。优选地,所述步骤(3)中,牵伸倍数为2.5~3.8,第一热辊温度70~100℃,速度800~1600m/min;第二热辊温度110~140℃,速度3500~4500m/min;卷绕速度3400~4400m/min。优选地,所述步骤(4)中,牵伸温度110~140℃、牵伸倍数为1.3~1.7,定型温度120~150℃,卷绕速度400~700m/min。普通丙纶纺丝采用骤冷技术,涤丙复合纺丝采用缓冷技术:(1)丝束经过缓冷区不进行抽吸骤冷;(2)降低冷却风速、提高冷却风温、增大纺丝缓冷区域,涤纶皮层从喷丝板熔融挤出到固化成型为15~20CM,改性丙纶芯层固化区为30~50CM。翼形涤纶皮层先冷却成型,芯层丙纶组份后冷却成型,由于热胀冷缩的作用,芯组份和皮层之间形成永久的圆环型缝隙,赋予复合纤维导湿性能和抗静电性。此外,本发明还提供一种上述复合弹性纤维在地毯方面的应用。所述复合弹性纤维通过消光及加捻定型后能获得仿羊毛的效果,适合于生产机织地毯,其毯面酷似羊毛地毯,条干丰满、回弹性好,可广泛用于高档毛毯、地毯及滚筒刷等材料上。现有的丙纶地毯纤维生产技术采用单组份纺丝技术,纤维成份为丙纶,纤维的吸湿性和染色性在化学纤维中是最差的,其回潮率小于0.03%,单丝纤度为3~10dtex,几乎不吸湿。相对于现有技术,本发明的有益效果为:本发明所述复合弹性纤维兼具皮层材料和芯层材料的性能,翼形结构与现有的皮芯纤维相比具有更好的抗倒伏性能;制备过程采用双组份共厄复合纺丝生产线,使用翼形皮芯型组件,经过复合纺丝、牵伸制成翼形皮芯结构复合弹性纤维,复合纺丝过程使用缓冷纺丝技术,通过对冷却风速、冷却风温、缓冷区域的控制,使皮层先固化成型,芯层后固化成型,由于热胀冷缩的作用,芯层和皮层之间形成永久间隙,赋予复合纤维导湿性能和抗静电性。因此,所述复合弹性纤维同时具有阻燃、抗静电、抗倒伏三种性能,应用于地毯,可以大大提高地毯的性能和档次。附图说明图1为本发明所述复合弹性纤维结构的一种径向剖面图;图2为本发明所述复合弹性纤维的制备工艺流程图;其中,a为芯层,b为缝隙,c为皮层。具体实施方式为更好的说明本发明的目的、技术方案和优点,下面将结合具体实施例对本发明作进一步说明。实施例1本发明所述复合弹性纤维的一种实施例,本实施例所述复合弹性纤维结构的径向剖面图如附图1所示,所述复合弹性纤维包括芯层、包裹在所述芯层外表面的皮层,所述皮层为聚酯,所述芯层为聚丙烯和聚烯烃按质量比为1:4进行混合的混合体,皮层和芯层的质量比为5:3,所述芯层的单丝纤度小于2dtex,所述芯层的径向剖面为圆形,所述皮层的径向剖面为表面带翼形的圆环。本实施例所述复合弹性纤维的制备方法,包括如下步骤:(1)以用量为60%重量份聚酯切片(粘度范围为0.6~0.75dl/g,熔点为257~260℃)为第一原料A,进入结晶床和干燥塔,对物料进行连续结晶、干燥,制成含水率<30ppm的聚酯干切片,进入第一螺杆挤出机,第一螺杆挤出机的设定温度为280℃,熔融挤压成为可纺丝聚酯熔体,第一螺杆挤出机的熔融挤压过程设有五段加热区,各区的加热温度为283℃、285℃、287℃、289℃、287℃(五区螺杆),并将该聚酯熔体输送到纺丝箱体中(在第一螺杆挤出机至纺丝箱体之间聚酯熔体经过预过滤器,将聚酯熔体中的大颗粒杂质去除),纺丝温度为282℃,通计量泵进一步均匀分配到翼形皮芯型复合组件中去,为皮层组份。(2)以按一定比例添加聚烯烃切片到聚丙烯切片(熔融指数范围为25~30g/10min,熔点范围为167~170℃)中并均匀混合作为原料B,原料B按40%重量份通过第二螺杆挤出机的熔融挤压成为可纺丝的熔体,第二螺杆挤压机的熔融挤压过程设有五段加热区,各区的加热温度为170℃、200℃、210℃、220℃、225℃(五区螺杆),并通计量泵将该熔体输送到纺丝箱体中,并进一步均匀分配到翼形皮芯型复合组件中,为芯层组份,其中,第二螺杆挤出机的设定温度为220℃,纺丝温度为245℃。(3)将翼形皮芯型复合纺丝组件中成型的初生丝均匀挤出,经过缓冷装置、侧吹风冷却成型、上油系统上油,通过纺丝甬道,进入到油轮、导盘、卷绕,得到POY丝筒,其中,侧吹风冷却的风速为0.7m/s,侧吹风冷却的温度为22℃,侧吹风冷却的相对湿度为75%,纺丝速度为3200m/min。(4)将POY丝束依次通过集束架、导丝架、热箱牵伸、假捻,定型、网络、卷绕成DTY筒子。其中,牵伸温度125℃、牵伸倍数为1.5,定型温度135℃,卷绕速度500m/min。实施例2本发明所述复合弹性纤维的一种实施例,本实施例所述复合弹性纤维结构的径向剖面图如附图1所示,所述复合弹性纤维包括芯层、包裹在所述芯层外表面的皮层,所述皮层为聚酯,所述芯层为聚丙烯和聚烯烃按质量比为1:9进行混合的混合体,皮层和芯层的质量比为1:1,所述芯层的单丝纤度小于2dtex,所述芯层的径向剖面为圆形,所述皮层的径向剖面为表面带翼形的圆环。本实施例所述复合弹性纤维的制备方法,包括如下步骤:(1)以用量为50%重量份聚酯切片(粘度范围为0.6~0.75dl/g,熔点为257~260℃)为第一原料A,进入结晶床和干燥塔,对物料进行连续结晶、干燥,制成含水率<30ppm的聚酯干切片,进入第一螺杆挤出机,第一螺杆挤出机的设定温度为270℃,熔融挤压成为可纺丝聚酯熔体,第一螺杆挤出机的熔融挤压过程设有五段加热区,各区的加热温度为283℃、285℃、287℃、289℃、287℃(五区螺杆),并将该聚酯熔体输送到纺丝箱体中(在第一螺杆挤出机至纺丝箱体之间聚酯熔体经过预过滤器,将聚酯熔体中的大颗粒杂质去除),纺丝温度为295℃,通计量泵进一步均匀分配到翼形皮芯型复合组件中去,为皮层组份。(2)以按一定比例添加聚烯烃切片到聚丙烯切片(熔融指数范围为25~30g/10min,熔点范围为167~170℃)中并均匀混合作为原料B,原料B按50%重量份通过第二螺杆挤出机的熔融挤压成为可纺丝的熔体,第二螺杆挤压机的熔融挤压过程设有五段加热区,各区的加热温度为170℃、200℃、210℃、220℃、225℃(五区螺杆),并通计量泵将该熔体输送到纺丝箱体中,并进一步均匀分配到翼形皮芯型复合组件中,为芯层组份,其中,第二螺杆挤出机的设定温度为240℃,纺丝温度为230℃。(3)将翼形皮芯型复合纺丝组件中成型的初生丝均匀挤出,经过缓冷装置、侧吹风冷却成型、上油系统上油,通过纺丝甬道,进入到油轮、导盘、卷绕,得到POY丝筒,其中,侧吹风冷却的风速为0.4m/s,侧吹风冷却的温度为15℃,侧吹风冷却的相对湿度为60%,纺丝速度为3000m/min。(4)将POY丝束依次通过集束架、导丝架、热箱牵伸、假捻,定型、网络、卷绕成DTY筒子。其中,牵伸温度110℃、牵伸倍数为1.3,定型温度120℃,卷绕速度400m/min。实施例3本发明所述复合弹性纤维的一种实施例,本实施例所述复合弹性纤维结构的径向剖面图如附图1所示,所述复合弹性纤维包括芯层、包裹在所述芯层外表面的皮层,所述皮层为聚酯,所述芯层为聚丙烯和聚烯烃按质量比为3:7进行混合的混合体,皮层和芯层的质量比为7:3,所述芯层的单丝纤度小于2dtex,所述芯层的径向剖面为圆形,所述皮层的径向剖面为表面带翼形的圆环。本实施例所述复合弹性纤维的制备方法,包括如下步骤:(1)以用量为70%重量份聚酯切片(粘度范围为0.6~0.75dl/g,熔点为257~260℃)为第一原料A,进入结晶床和干燥塔,对物料进行连续结晶、干燥,制成含水率<30ppm的聚酯干切片,进入第一螺杆挤出机,第一螺杆挤出机的设定温度为290℃,熔融挤压成为可纺丝聚酯熔体,第一螺杆挤出机的熔融挤压过程设有五段加热区,各区的加热温度为283℃、285℃、287℃、289℃、287℃(五区螺杆),并将该聚酯熔体输送到纺丝箱体中(在第一螺杆挤出机至纺丝箱体之间聚酯熔体经过预过滤器,将聚酯熔体中的大颗粒杂质去除),纺丝温度为270℃,通计量泵进一步均匀分配到翼形皮芯型复合组件中去,为皮层组份。(2)以按一定比例添加聚烯烃切片到聚丙烯切片(熔融指数范围为25~30g/10min,熔点范围为167~170℃)中并均匀混合作为原料B,原料B按30%重量份通过第二螺杆挤出机的熔融挤压成为可纺丝的熔体,第二螺杆挤压机的熔融挤压过程设有五段加热区,各区的加热温度为170℃、200℃、210℃、220℃、225℃(五区螺杆),并通计量泵将该熔体输送到纺丝箱体中,并进一步均匀分配到翼形皮芯型复合组件中,为芯层组份,其中,第二螺杆挤出机的设定温度为200℃,纺丝温度为260℃。(3)将翼形皮芯型复合纺丝组件中成型的初生丝均匀挤出,经过缓冷装置、侧吹风冷却成型、上油系统上油,通过纺丝甬道,进入到油轮、导盘、卷绕,得到POY丝筒,其中,侧吹风冷却的风速为1m/s,侧吹风冷却的温度为30℃,侧吹风冷却的相对湿度为90%,纺丝速度为2800m/min。(4)将POY丝束依次通过集束架、导丝架、热箱牵伸、假捻,定型、网络、卷绕成DTY筒子。其中,牵伸温度130℃、牵伸倍数为1.6,定型温度140℃,卷绕速度550m/min。实施例4本发明所述复合弹性纤维的一种实施例,本实施例所述复合弹性纤维结构的径向剖面图如附图1所示,所述复合弹性纤维包括芯层、包裹在所述芯层外表面的皮层,所述皮层为聚酯,所述芯层为聚丙烯和聚烯烃按质量比为1:3进行混合的混合体,皮层和芯层的质量比为6:3,所述芯层的单丝纤度小于2dtex,所述芯层的径向剖面为圆形,所述皮层的径向剖面为表面带翼形的圆环。本实施例所述复合弹性纤维的制备方法,包括如下步骤:(1)以用量为55%重量份聚酯切片(粘度范围为0.6~0.75dl/g,熔点为257~260℃)为第一原料A,进入结晶床和干燥塔,对物料进行连续结晶、干燥,制成含水率<30ppm的聚酯干切片,进入第一螺杆挤出机,第一螺杆挤出机的设定温度为290℃,熔融挤压成为可纺丝聚酯熔体,第一螺杆挤出机的熔融挤压过程设有五段加热区,各区的加热温度为283℃、285℃、287℃、289℃、287℃(五区螺杆),并将该聚酯熔体输送到纺丝箱体中(在第一螺杆挤出机至纺丝箱体之间聚酯熔体经过预过滤器,将聚酯熔体中的大颗粒杂质去除),纺丝温度为285℃,通计量泵进一步均匀分配到翼形皮芯型复合组件中去,为皮层组份。(2)以按一定比例添加聚烯烃切片到聚丙烯切片(熔融指数范围为25~30g/10min,熔点范围为167~170℃)中并均匀混合作为原料B,原料B按35%重量份通过第二螺杆挤出机的熔融挤压成为可纺丝的熔体,第二螺杆挤压机的熔融挤压过程设有五段加热区,各区的加热温度为170℃、200℃、210℃、220℃、225℃(五区螺杆),并通计量泵将该熔体输送到纺丝箱体中,并进一步均匀分配到翼形皮芯型复合组件中,为芯层组份,其中,第二螺杆挤出机的设定温度为210℃,纺丝温度为235℃。(3)将翼形皮芯型复合纺丝组件中成型的初生丝均匀挤出,经过缓冷装置、侧吹风冷却成型、上油系统上油,通过纺丝甬道,进入到油轮、导盘、卷绕,得到POY丝筒,其中,侧吹风冷却的风速为0.6m/s,侧吹风冷却的温度为20℃,侧吹风冷却的相对湿度为70%,纺丝速度为3500m/min。(4)将POY丝束依次通过集束架、导丝架、热箱牵伸、假捻,定型、网络、卷绕成DTY筒子。其中,牵伸温度120℃、牵伸倍数为1.4,定型温度130℃,卷绕速度520m/min。实施例5本发明所述复合弹性纤维的一种实施例,本实施例所述复合弹性纤维结构的径向剖面图如附图1所示,所述复合弹性纤维包括芯层、包裹在所述芯层外表面的皮层,所述皮层为聚酯,所述芯层为聚丙烯和聚烯烃按质量比为3:17进行混合的混合体,皮层和芯层的质量比为4:3,所述芯层的单丝纤度小于2dtex,所述芯层的径向剖面为圆形,所述皮层的径向剖面为表面带翼形的圆环。本实施例所述复合弹性纤维的制备方法,包括如下步骤:(1)以用量为65%重量份聚酯切片(粘度范围为0.6~0.75dl/g,熔点为257~260℃)为第一原料A,进入结晶床和干燥塔,对物料进行连续结晶、干燥,制成含水率<30ppm的聚酯干切片,进入第一螺杆挤出机,第一螺杆挤出机的设定温度为280℃,熔融挤压成为可纺丝聚酯熔体,第一螺杆挤出机的熔融挤压过程设有五段加热区,各区的加热温度为283℃、285℃、287℃、289℃、287℃(五区螺杆),并将该聚酯熔体输送到纺丝箱体中(在第一螺杆挤出机至纺丝箱体之间聚酯熔体经过预过滤器,将聚酯熔体中的大颗粒杂质去除),纺丝温度为275℃,通计量泵进一步均匀分配到翼形皮芯型复合组件中去,为皮层组份。(2)以按一定比例添加聚烯烃切片到聚丙烯切片(熔融指数范围为25~30g/10min,熔点范围为167~170℃)中并均匀混合作为原料B,原料B按45%重量份通过第二螺杆挤出机的熔融挤压成为可纺丝的熔体,第二螺杆挤压机的熔融挤压过程设有五段加热区,各区的加热温度为170℃、200℃、210℃、220℃、225℃(五区螺杆),并通计量泵将该熔体输送到纺丝箱体中,并进一步均匀分配到翼形皮芯型复合组件中,为芯层组份,其中,第二螺杆挤出机的设定温度为230℃,纺丝温度为255℃。(3)将翼形皮芯型复合纺丝组件中成型的初生丝均匀挤出,经过缓冷装置、侧吹风冷却成型、上油系统上油,通过纺丝甬道,进入到油轮、导盘、卷绕,得到POY丝筒,其中,侧吹风冷却的风速为0.8m/s,侧吹风冷却的温度为25℃,侧吹风冷却的相对湿度为80%,纺丝速度为3600m/min。(4)将POY丝束依次通过集束架、导丝架、热箱牵伸、假捻,定型、网络、卷绕成DTY筒子。其中,牵伸温度130℃、牵伸倍数为1.35,定型温度145℃,卷绕速度570m/min。实施例6本实施例对实施例1~5中的复合弹性纤维的断裂强度、断裂伸长率、条干不匀率CV值进行了相关试验研究,研究结果如表1所示:表1实施例1~5中纤维的断裂强度、断裂伸长率、条干不匀率CV值断裂强度、断裂伸长率采用《化学纤维长丝拉伸性能试验方法》(GB/T14344-2008),测试仪器采用电子单纱强力仪,由莱州市电子仪器有限公司生产,型号为YG061;条干不匀率CV值采用常州二纺精密机械有限公司生产的YG800C条干均匀度测试仪。由以上性能测试结果可以看出,本发明所述复合弹性纤维的线密度、断裂强度、断裂伸长率均符合相应产品的使用需求。实施例7将实施例1~5中的复合弹性纤维产品DTY制成纤维织物,采用‘织物经反复压缩变形,恢复’这个过程前后绒毛高度改变的程度来测试纤维织物的抗倒伏性能,其高度变化量越大抗倒伏性能越差;研制的复合纤维织物(1#)和普通圆形丙纶纤维织物(2#)经上述方法分别进行测试,测试过程选取多组样品进行,测试的高度变化率取平均值,测试结果如表2所示:表21#和2#纤维织物的抗倒伏性能研究结果织物原绒毛高度CM测试后高度CM高度变化率﹪1#1513.8~14.1约7%2#1510~11.5约23%从表2中的数据可以看出,研制的复合纤维织物(1#)和普通圆形丙纶纤维织物(2#)经‘反复压缩变形,恢复’这个过程前后,1#织物比2#织物绒毛高度变化率小很多,说明研制的纤维抗倒伏性能改善很大。实施例8本实施例采用芯吸高度比较法来测量本发明所述复合弹性纤维的吸湿性能,即用粗细相同的纤维织成规格一致的袜带在装有水的容器上方一起放进水中,固定两条袜带并恒定30分钟,然后测定液面上方袜带湿润的高度,这个高度越大说明袜带纤维的吸湿性能越好;表3是研制的复合纤维袜带(1#)和普通圆形丙纶纤维袜带(2#)测试结果:表31#和2#纤维袜带的吸湿性能研究结果袜带湿润高度CM测试次数1#10.0~11.552#3.9~4.35从表3中可以看出,研制的复合纤维袜带(1#)的湿润高度比普通圆形丙纶纤维袜带(2#)的湿润高度大很多,说明研制的纤维吸湿性能改善很大。实施例9本实施例对本发明复合弹性纤维的阻燃性能和脆韧性进行研究分析。阻燃纤维的定义是:当纤维在中、小型火源点燃下,会发生小火焰燃烧,一旦火源撤走,火焰又能较快地自行燃灭,是不会蔓延成灾的纤维。纤维的阻燃性一般用常温极限氧指数(LOI)来衡量。因为空气中的含氧率为21%,纤维的LOI>21%,离开火焰后,在空气中才能继续燃烧,LOI=25~31%范围时,可认为基本不燃,如果纤维的LOI>20%,该纤维就具阻燃性。涤纶纤维的LOI为20.0~22.0%,具阻燃性;丙纶纤维的LOI为17.0~18.5%,不具阻燃性。本发明所述在丙纶纤维包一层具阻燃性的涤纶成复合纤维,复合纤维也具有阻燃性。丙纶材料冲击强度低、低温脆性的缺点尤为突出,使其应用受到限制,通过与弹性体共混来改善丙纶冲击性能是目前最广泛采用的方法,加入量一般为10%左右。聚烯烃以优异的性能以及与聚丙烯良好的亲和性,与聚丙烯组成的聚烯烃/聚丙烯体系,广泛应用于汽车工业。聚烯烃/聚丙烯共混物的相结构属于“海-岛”结构,海相(连续相)为聚丙烯,岛相(分散相)为聚烯烃。遵循橡塑共混原理,共混物中分散相的粒径大小对共混物的性能影响很大,在最佳粒径范围内,粒径小时,对共混物的物理性能有较好的贡献。聚烯烃的粒径小,且尺寸较均匀。塑料共混弹性体有几种增韧机理,聚烯烃对聚丙烯增韧改性符合银纹-剪切带机理;脆性基体内加入弹性体后,在外来冲击力作用下,弹性体可引发大量银纹,而基体则产生剪切屈服,主要靠银纹、剪切带吸收能量。具体过程为:产生银纹进一步发展并将终止于另一弹性体或剪切带;同时银纹与银纹、银纹与剪切带之间相互作用;如银纹与银纹相遇时,会使银纹转向或支化;银纹前峰处的应力集中,可以诱发新的剪切带。所有这些作用,都会大大缓解材料的冲击破坏过程,并增加破坏过程的能量,从而提高材料韧性。本发明所述复合弹性纤维中加入聚烯烃降低了聚丙烯纤维的结晶能力,赋予其良好的弹性。表4是本发明实施例1~5中的复合纤维与纯聚丙烯纤维韧性测量值:表4本发明所述复合纤维与纯聚丙烯纤维韧性测量值本发明复合纤维纯聚丙烯纤维韧性cn/dtex44~4620.4从表4中可以很明显的看出,本发明所述复合弹性纤维的韧性测量值比纯聚丙烯纤维大的多,这也进一步验证了上文的分析及本发明所述复合弹性纤维的进步性。此外,将实施例1~5中的复合弹性纤维产品DTY通过经编机织造、分割、剪绒、上浆,定型制成滚筒刷基布。其绒面胜过晴纶绒布,手感丰满、回弹性好,导水性好。其造价约为羊毛绒布的三分之一,约为晴纶绒布的三分之二。由于质量好、造价低,一经推出市场便深受消费者欢迎,已远消欧美市场。将实施例1~5中的复合弹性纤维产品DTY通过经编机织造、剪绒、上浆,定型制成地毯基布,其绒面酷似羊毛绒面,手感丰满、回弹性好,导水性好,抗污性好且防虫防蛀。最后所应当说明的是,以上实施例仅用以说明本发明的技术方案而非对本发明保护范围的限制,尽管参照较佳实施例对本发明作了详细说明,本领域的普通技术人员应当理解,可以对本发明的技术方案进行修改或者等同替换,而不脱离本发明技术方案的实质和范围。当前第1页1 2 3