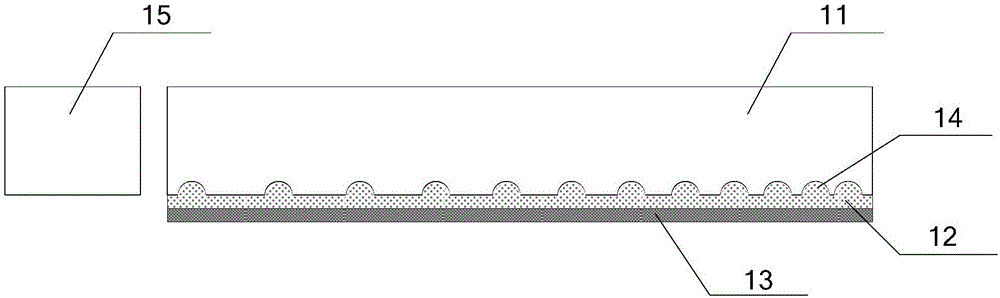
本发明涉及显示装置
技术领域:
,尤其涉及一种侧入式背光模组及显示装置。
背景技术:
:随着科学技术的不断发展,人们对液晶显示装置的厚度要求越来越高,液晶显示装置的薄形化已经成为人们追求的热点。液晶显示装置一般包括液晶面板及背光模组,由于液晶面板本身不发光,需要借由背光模组提供的光源来正常显示影像,因此,背光模组成为了液晶显示装置的关键组件之一。背光模组按照光源入射位置的不同分成侧入式背光模组与直下式背光模组两种。图1为现有技术中的侧入式背光模组的结构示意图,参考图1所示,所述侧入式背光模组包括胶框01、设于胶框01内侧的导光板02,导光板02下方设置有反射片03,反射片03与导光板02之间存在间隙04,导光板02上方设置有光学膜片05,光学膜片05远离导光板02的一侧设置有遮光胶带06。从图1可知,侧入式背光模组的整体厚度包括反射片03及间隙04的厚度、导光板02的厚度、光学膜片05的厚度和遮光胶带06的厚度。由于现有技术中的反射片03一般是通过在基材上涂覆反光材料制作而成,而基材一般厚度较大,因而导致反射片的厚度较大,进而导致侧入式背光模组的整体厚度较大,这样不利于侧入式背光模组的薄形化设计。技术实现要素:本发明的实施例提供一种侧入式背光模组及显示装置,能够减小侧入式背光模组的厚度,有利于侧入式背光模组的薄形化设计。为达到上述目的,本发明的实施例采用如下技术方案:一方面,本发明实施例提供一种侧入式背光模组,包括导光板,所述导光板包括用于出光的上表面,和与所述上表面相对的下表面,所述下表面设置有折射镀层,所述折射镀层的折射率小于所述导光板的折射率;所述折射镀层远离所述导光板的表面设置有反射镀层,所述反射镀层用于反射照射在其上的光线。可选的,所述折射镀层的材质为氟化物或硅化物。可选的,所述折射镀层的材质为氟化钙。可选的,所述反射镀层和所述折射镀层均通过蒸镀工艺制作而成。可选的,所述上表面形成有V型割槽结构。可选的,所述反射镀层的材料为铝或银。可选的,所述反射镀层的厚度为3um~5um。可选的,所述下表面形成有网点结构,所述网点结构用于将照射在其上的光线反射出所述导光板。可选的,所述网点结构为凸起或凹槽。另一方面,本发明实施例提供一种显示装置,包括上述任意一种所述的侧入式背光模组。本发明实施例提供的侧入式背光模组及显示装置,所述侧入式背光模组包括导光板,导光板包括用于出光的上表面,和与上表面相对的下表面,下表面设置有折射镀层,折射镀层的折射率小于导光板的折射率;折射镀层远离导光板的表面设置有反射镀层,反射镀层用于反射照射在其上的光线。相较于现有技术,本发明实施例在导光板的下表面设置折射镀层,然后在折射镀层远离导光板的表面设置反射镀层,由于折射镀层位于导光板和反射镀层之间,由于折射镀层的存在,使得光从导光板入射到折射镀层时,光在导光板和折射镀层的界面发生全反射,减少光线进入反射镀层的机会,从而减少反射镀层对光线的吸收,进而保证了导光板的出光亮度;同时,在导光板的下表面设置折射镀层和反射镀层,即为在导光板的下表面通过镀膜工艺先设置一层低折射材料,然后再设置一层反光材料,由于导光板充当了反射片中反光材料的基材的作用,因而不需要额外设置基材,这样反射镀层的厚度远小于现有技术中反射片的厚度,通过所述反射镀层代替现有技术中的反射片,减小了侧入式背光模组的整体厚度,有利于侧入式背光模组的薄形化设计;另外,由于反射镀层是通过镀膜工艺设置在导光板的下表面的折射镀层上,所述反射镀层不会发生褶皱,因而避免现有技术中由于反射片褶皱而造成的背光模组出光侧亮暗不均匀的问题,即提高了背光模组的亮度均匀性。附图说明为了更清楚地说明本发明实施例或现有技术中的技术方案,下面将对实施例或现有技术描述中所需要使用的附图作简单地介绍,显而易见地,下面描述中的附图仅仅是本发明的一些实施例,对于本领域普通技术人员来讲,在不付出创造性劳动的前提下,还可以根据这些附图获得其他的附图。图1为现有技术提供的一种侧入式背光模组结构示意图一;图2为本发明实施例提供的一种侧入式背光模组结构示意图;图3为现有技术提供的一种侧入式背光模组结构示意图二;图4为现有技术提供的一种侧入式背光模组结构示意图三;图5为本发明实施例提供的一种导光板出光面亮度分布示意图。具体实施方式下面将结合本发明实施例中的附图,对本发明实施例中的技术方案进行清楚、完整地描述,显然,所描述的实施例仅仅是本发明一部分实施例,而不是全部的实施例。基于本发明中的实施例,本领域普通技术人员在没有做出创造性劳动前提下所获得的所有其他实施例,都属于本发明保护的范围。本发明实施例提供一种侧入式背光模组,如图2所示,所述侧入式背光模组包括导光板11,导光板11包括用于出光的上表面,和与所述上表面相对的下表面,所述下表面设置有折射镀层12,折射镀层12的折射率小于导光板11的折射率;折射镀层12远离导光板11的表面设置有反射镀层13,反射镀层13用于反射照射在其上的光线。参考图3和图4所示,图3中反射片03与导光板02的下表面紧贴。由于反射片03中反射材料的反射率无法达到100%,一般会存在较高的光吸收率,示例的,铝的反射率为85%,其光吸收率为15%;银的反射率为90%,其光吸收率为10%。因而当光线从灯条04出来后,由于反射片03与导光板02的下表面紧贴,光线在靠近灯条04端不断反射接触反射片03,这样许多光线会被反射片03吸收,无法保证足够量的全反射,导致导光板02远离灯条04端的光线较少,并且使得导光板02的总出光量减少。而图4中,导光板02与反射片03之间存在间隙04,间隙04处充满的是空气,其折射率接近1,由于间隙04的折射率小于导光板02的折射率,因而光线在导光板02中的全反射较多,这样使得整个导光板02的出光比较均匀;并且减少了光线直接照射到反射片03的次数,即减少了反射片03对于光线的吸收,这样保证了整个导光板02的出光量。基于同样的原理,本发明实施例在反射镀层13和导光板11之间设置折射镀层12,同样可以达到保证导光板11的出光亮度的目的。需要说明的是,本发明实施例对于折射镀层12和反射镀层13的具体材料均不做限定,本领域技术人员可以根据实际情况进行选取。这样一来,相较于现有技术,本发明实施例在导光板的下表面设置折射镀层,然后在折射镀层远离导光板的表面设置反射镀层,由于折射镀层位于导光板和反射镀层之间,使得光从导光板入射到折射镀层时,光在导光板和折射镀层的界面发生全反射,减少光线进入反射镀层的机会,从而减少反射镀层对光线的吸收,进而保证了导光板的出光亮度;同时,在导光板的下表面设置折射镀层和反射镀层,即为在导光板的下表面通过镀膜工艺先设置一层低折射材料,然后再设置一层反光材料,由于导光板充当了反射片中反光材料的基材的作用,因而不需要额外设置基材,这样反射镀层的厚度远小于现有技术中反射片的厚度,通过所述反射镀层代替现有技术中的反射片,减小了侧入式背光模组的整体厚度,有利于侧入式背光模组的薄形化设计;另外,由于反射镀层是通过镀膜工艺设置在导光板的下表面的折射镀层上,所述反射镀层不会发生褶皱,因而避免现有技术中由于反射片褶皱而造成的背光模组出光侧亮暗不均匀的问题,即提高了背光模组的亮度均匀性。由于折射镀层12和导光板11之间的折射率差异越大,具体地,折射镀层12的折射率应远小于导光板材料的折射率,这样越有利于光线在导光板11内进行全反射,就越能提高导光板11的出光亮度和出光均匀性,因而选取的折射镀层12的折射率越小越好。而在实际应用中,氟化物或硅化物的折射率一般较小,比较适合作为折射镀层12的材料,因而一般选用氟化物或硅化物作为折射镀层12的材质。较佳的,折射镀层12的材质为氟化钙。由于现有技术中导光板11的材质一般为有机玻璃PMMA,其折射率为1.49,而氟化钙的折射率可达到1.35,两者折射率相差较大,这样使得导光板11的亮度提升越明显。在实际应用中,反射镀层13和折射镀层12可以通过多种镀膜工艺设置到导光板11的下表面上,示例的,可以通过蒸镀工艺设置,也可以通过溅射工艺设置,或者也可以通过其它镀膜工艺设置,本发明实施例对此不做限定。其中,反射镀层13的厚度一般控制在3um~5um,折射镀层12一般控制在5um~50um。由于蒸镀工艺能够精确的控制镀膜厚度,因而较佳的,反射镀层13和折射镀层12均通过蒸镀工艺制作而成。进一步的,导光板11的上表面形成有V型割槽结构。所述V型割槽结构即为V-cut结构,其设置在导光板11的上表面可以提高导光板的出光亮度。在实际应用中,所述V型割槽结构一般沿导光板11的长边方向设置。由于铝或银具有较高的反射率,且较易获取,因而较佳的,反射镀层13的材料为铝或银。进一步的,参考图2所示,所述下表面形成有网点结构14,网点结构14用于将照射在其上的光线反射出导光板11。如果从灯条15出来的较多光线在导光板11内一直发生全反射,这些光线就不能从导光板11射出,这样导光板11的出光量就会减少。因而为了保证导光板11有足够的出光量,导光板11中的全反射就不能太多,所述网点结构能够破坏导光板11下表面上的部分全反射,将导光板11内的全反射保持在一定范围内,这样不但保证了导光板11的出光均匀性,同时也保证了导光板11有足够的出光量。由于凸起或凹槽对光线全反射的破坏性能较好,且较易制作,因而较佳的,网点结构14一般为凸起或凹槽。参考图5所示,图5为通过光学模拟软件SPEOS对导光板11的出光面的出光亮度进行模拟实验的图像。整个画面代表的是导光板11的出光面,X轴代表导光板11的短边,Y轴代表导光板11的长边,图像中亮点越多代表出光量越多,出光亮度越高。图5(a)为导光板11的下表面只设置一层反射镀层13的情况;图5(b)为导光板11的下表面先设置一层折射镀层12,再设置一层反射镀层13的情况。其中,导光板11的折射率为1.49;反射镀膜13的反射率为85%,折射镀层12的折射率为1.35。表1为通过光学模拟软件SPEOS对导光板11的出光亮度进行模拟后得到的实验数据。表1参数反射镀层反射镀层+折射镀层射出光通量(lm)6.1034.35正视角平均亮度(nits)304.061244.82结合表1和图5可知,在导光板11和反射镀层13之间设置折射镀层12,可以使得导光板11的射出光通量(即出光量)由6.10lm(流明)提升到34.35lm(流明),即提高了将近6倍;并且使得正视角平均亮度由304.06nits提升到1244.82nits,提高了4倍多。由此可知,通过在导光板11和反射镀层13之间设置折射镀层12,可以很好地保证导光板11的出光量和出光均匀性。本发明实施例提供的侧入式背光模组,包括导光板,导光板包括用于出光的上表面,和与上表面相对的下表面,下表面设置有折射镀层,折射镀层的折射率小于导光板的折射率;折射镀层远离导光板的表面设置有反射镀层,反射镀层用于反射照射在其上的光线。相较于现有技术,本发明实施例在导光板的下表面设置折射镀层,然后在折射镀层远离导光板的表面设置反射镀层,由于折射镀层位于导光板和反射镀层之间,由于折射镀层的存在,使得光从导光板入射到折射镀层时,光在导光板和折射镀层的界面发生全反射,减少光线进入反射镀层的机会,从而减少反射镀层对光线的吸收,进而保证了导光板的出光亮度;同时,在导光板的下表面设置折射镀层和反射镀层,即为在导光板的下表面通过镀膜工艺先设置一层低折射材料,然后再设置一层反光材料,由于导光板充当了反射片中反光材料的基材的作用,因而不需要额外设置基材,这样反射镀层的厚度远小于现有技术中反射片的厚度,通过所述反射镀层代替现有技术中的反射片,减小了侧入式背光模组的整体厚度,有利于侧入式背光模组的薄形化设计;另外,由于反射镀层是通过镀膜工艺设置在导光板的下表面的折射镀层上,所述反射镀层不会发生褶皱,因而避免现有技术中由于反射片褶皱而造成的背光模组出光侧亮暗不均匀的问题,即提高了背光模组的亮度均匀性。另一方面,本发明实施例提供一种显示装置,所述显示装置包括上述任意一种所述的侧入式背光模组。所述侧入式背光模组在导光板的下表面设置折射镀层,然后在折射镀层远离导光板的表面设置反射镀层,由于折射镀层位于导光板和反射镀层之间,由于折射镀层的存在,使得光从导光板入射到折射镀层时,光在导光板和折射镀层的界面发生全反射,减少光线进入反射镀层的机会,从而减少反射镀层对光线的吸收,进而保证了导光板的出光亮度;同时,在导光板的下表面设置折射镀层和反射镀层,即为在导光板的下表面通过镀膜工艺先设置一层低折射材料,然后再设置一层反光材料,由于导光板充当了反射片中反光材料的基材的作用,因而不需要额外设置基材,这样反射镀层的厚度远小于现有技术中反射片的厚度,通过所述反射镀层代替现有技术中的反射片,减小了侧入式背光模组的整体厚度,有利于侧入式背光模组的薄形化设计;另外,由于反射镀层是通过镀膜工艺设置在导光板的下表面的折射镀层上,所述反射镀层不会发生褶皱,因而避免现有技术中由于反射片褶皱而造成的背光模组出光侧亮暗不均匀的问题,即提高了背光模组的亮度均匀性。以上所述,仅为本发明的具体实施方式,但本发明的保护范围并不局限于此,任何熟悉本
技术领域:
的技术人员在本发明揭露的技术范围内,可轻易想到变化或替换,都应涵盖在本发明的保护范围之内。因此,本发明的保护范围应以所述权利要求的保护范围为准。当前第1页1 2 3