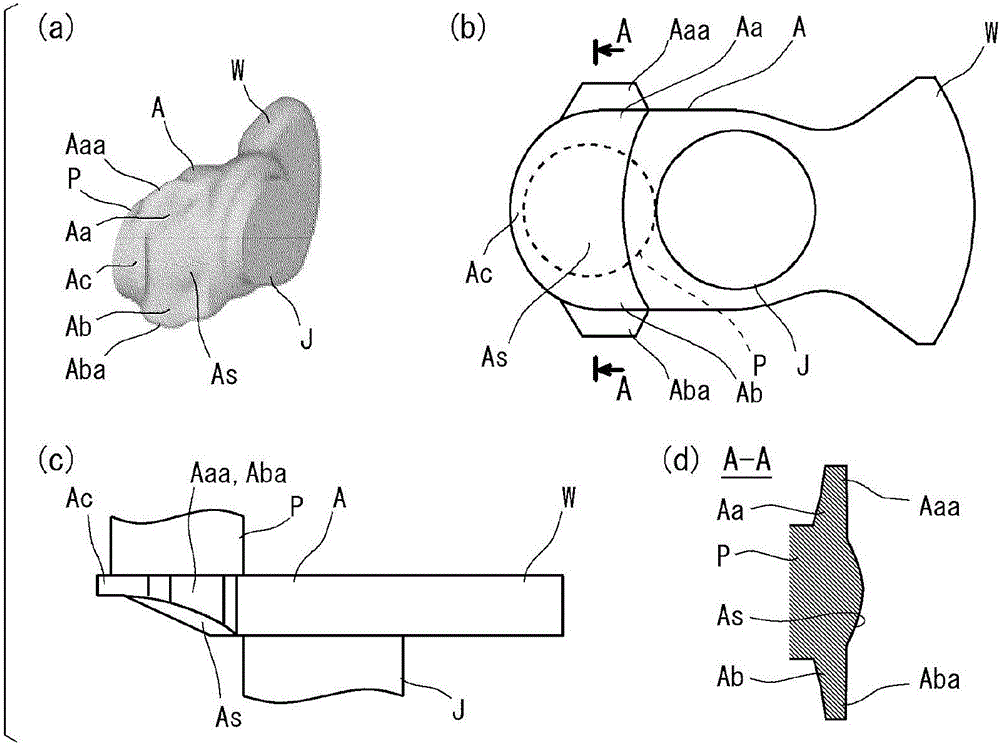
本发明涉及一种利用热锻来制造曲轴的方法。
背景技术:对于汽车、摩托车、农业机械、船舶等的往复式发动机来说,为了将活塞的往复运动转换为旋转运动而输出动力,曲轴是必不可少的。曲轴被大致区分为利用模锻制造的曲轴和利用铸造制造的曲轴。特别是,在被要求高强度和高刚度的情况下,多数使用强度和刚度优异的前者的锻造曲轴。通常,锻造曲轴以截面呈圆形或方形且在整个长度上截面积恒定的钢坯为原材料,依次经过预成形、模锻、去除飞边以及整形各工序而制造。通常,预成形工序包括辊轧成形和弯曲锻造各工序,模锻工序包括粗锻和精锻各工序。图1是用于对以往的通常的锻造曲轴的制造工序进行说明的示意图。图1所例示的曲轴1(参照图1(f))搭载于四缸发动机,包括五个轴颈部J1~J5、四个销部P1~P4、前端部Fr、法兰部Fl以及分别将轴颈部J1~轴颈部J5和销部P1~销部P4相连的八片曲臂部(以下,也简称为“臂部”)A1~A8。该曲轴1是在八个臂部A1~A8均一体地具有平衡块部(日文:カウンターウエイト部)(以下也简称为“平衡块部(日文:ウエイト部)”)W1~W8,该曲轴1被称作四缸-八平衡块的曲轴。以下,在对轴颈部J1~J5、销部P1~P4、臂部A1~A8以及平衡块部W1~W8分别进行统称时,也将轴颈部的附图标记记为“J”,将销部的附图标记记为“P”,将臂部的附图标记记为“A”,将平衡块部的附图标记记为“W”。将销部P以及与该销部P相连的一组臂部A(包括平衡块部W)统一简称为“曲拐”。在图1所示的制造方法中,如以下那样制造锻造曲轴1。首先,在利用感应加热炉、气体气氛加热炉对预先已切割为预定长度的图1(a)所示的钢坯2进行加热之后,进行辊轧成形。在辊轧成形工序中,利用例如孔型轧辊轧制钢坯2而使钢坯2缩径并且将其体积分配在长度方向上,从而使作为中间坯料的辊轧坯件3成形(参照图1(b))。接下来,在弯曲锻造工序中,对利用辊轧成形而获得的辊轧坯件3从与长度方向成直角的方向局部冲压下压而将该辊轧坯件3的体积分配,使作为进一步的中间坯料的弯曲坯件4成形(参照图1(c))。接下来,在粗锻工序中,使用一对模具对通过弯曲锻造而获得的弯曲坯件4进行上下锻压,使被造形成曲轴(最终产品)的大致的形状的锻造件5成形(参照图1(d))。然后,在精锻工序中,被提供通过粗锻而获得的粗锻件5,使用一对模具对粗锻件5进行上下锻压,使被造形成与最终产品的曲轴相一致的形状的锻件6成形(参照图1(e))。在进行该粗锻和精锻时,剩余材料作为飞边自互相相对的模具的分型面之间流出。因此,粗锻件5、精锻件6在已被造形的曲轴的周围分别带有较大的飞边5a、6a。在去除飞边工序中,利用模具从上下对由精锻而获得的带有飞边6a的精锻件6进行保持,并且利用刀具类模具将飞边6a冲切去除。由此,如图1(f)所示,获得锻造曲轴1。在整形工序中,对去除了飞边的锻造曲轴1的重要部位例如轴颈部J、销部P、前端部Fr、法兰部Fl等这样的轴部利用模具自上下略微冲压下压,进一步对臂部A以及平衡块部W利用模具自上下略微冲压下压,而矫正为最终产品的尺寸形状。如此,制造锻造曲轴1。图1所示的制造工序并不限定于例示的四缸-八平衡块的曲轴,即使是在八个臂部A中的一部分臂部具有平衡块部W的曲轴,制造工序也相同。例如在搭载于四缸发动机的曲轴中,有时在开头的第一臂部A1、最末尾的第8臂部A8以及中央的两个第4臂部A4、第5臂部A5设有平衡块部W。该曲轴被称作四缸-四平衡块的曲轴。另外,即使是搭载于三缸发动机、直列六缸发动机、V型六缸发动机、八缸发动机等的曲轴,制造工序也相同。另外,在需要调整销部的配置角度的情况下,在去除飞边工序之后,追加扭转工序。近年来,特别是对于用于汽车的往复式发动机来说,为了改善油耗而追求轻量化。因此,针对作为往复式发动机的主要零部件的曲轴,轻量化的要求也变得日益显著。作为实现锻造曲轴的轻量化的现有技术,存在下述技术。在日本特开2012-7726号公报(专利文献1)以及日本特开2010-230027号公报(专利文献2)中记载了一种臂部,在臂部的轴颈部侧的表面,在将轴颈部的轴心与销部的轴心连接的直线(以下,也称为“臂部中心线”)上,形成有朝向销部去又大又深地凹陷的孔部,还记载了一种具有该臂部的曲轴的制造方法。上述专利文献1以及2所记载的臂部减轻了与孔部的体积相对应的重量。臂部的轻量化关系到与臂部成对的平衡块部的重量减轻,进而关系到锻造曲轴整体的轻量化。另外,对于上述专利文献1以及2所公开的臂部来说,在中间隔着臂部中心线的销部附近的两个侧部处将厚度维持得较厚,因而还确保了刚度(扭曲刚度以及弯曲刚度)。如此,如果在较厚地维持臂部的两个侧部的厚度的同时使臂部的轴颈部侧的表面具有凹部,则能够同时实现轻量化和确保刚度。但是,在以往的制造方法中制造具有上述独特的形状的臂部的锻造曲轴比较困难。其原因在于,在模锻工序中,若想在臂部表面形成凹部,则模具的该凹部部位的脱模斜度变成反坡,从而发生已被成形的锻件不能从模具拔出的状况。为了应对这样的状况,专利文献1和专利文献2所记载的制造方法为,在模锻工序中不在臂部表面形成凹部,而是将臂部成形得较小,在去除飞边工序之后,将冲头压入臂部的表面,利用该冲头的痕迹而形成凹部。现有技术文献专利文献专利文献1:日本特开2012-7726号公报专利文献2:日本特开2010-230027号公报
技术实现要素:发明要解决的问题根据所述专利文献1和专利文献2所记载的制造方法,能够在较厚地维持臂部的两个侧部的厚度的同时,在臂部的轴颈部侧的表面形成凹部,从而能够制造同时实现了轻量化和确保刚度的锻造曲轴。然而,在该制造方法中,为了在臂部表面形成凹部,将冲头用力地按压在臂部表面而使臂部整体变形,因而在压入冲头时需要很大的力量。因此,需要用于对冲头施加很大的力量的特别的设备结构,关于冲头的耐久性也必须考虑到。本发明的目的在于提供一种能够简便地获得同时实现了轻量化和确保刚度的锻造曲轴的锻造曲轴的制造方法。用于解决问题的方案基于本发明的实施方式的锻造曲轴的制造方法,其中,该锻造曲轴具有:作为旋转中心的轴颈部、相对于该轴颈部偏心的销部以及用于连接所述轴颈部和所述销部的曲臂部。该制造方法包括模锻工序、去除飞边工序和余料部弯折工序。在模锻工序中,成形带有飞边的精锻件,该精锻件被造形成在所述曲臂部的所述销部附近的两个侧部的各自的外周具有自该外周突出的余料部的曲轴的形状。在去除飞边工序中,从在所述模锻工序中成形了的所述精锻件去除飞边。在余料部弯折工序中,通过对在所述去除飞边工序中去除飞边而成的曲轴自所述销部的偏心方向插入U字形的第一模具,而将所述曲臂部的所述余料部朝向所述曲臂部的所述轴颈部侧的表面弯折。在上述制造方法中,能够构成为,在所述余料部弯折工序中,利用第二模具的推压而保持所述曲臂部的所述轴颈部侧的表面中的除了至少所述两个侧部的区域以外的表面。在上述制造方法中,能够构成为,通过所述模锻工序成形的所述精锻件的所述余料部从自所述曲臂部的所述两个侧部至所述销部的偏心方向的顶部的范围的外周突出。另外,在上述制造方法中,能够构成为,所述余料部弯折工序在通过使用模具的冲压下压而矫正曲轴的形状的整形工序中实施。另外,在上述制造方法中,能够构成为,在所述余料部弯折工序中,在所述曲臂部的所述轴颈部侧的表面中的所述曲臂部的两个侧部的内侧形成凹部。发明的效果根据本发明,在臂部的两个侧部的外周形成局部突出的余料部,利用自销部的偏心方向插入U字形的第一模具来弯折该局部突出的余料部。由此,能够将臂部的两个侧部的厚度维持得较厚的同时,在臂部的轴颈部侧的表面形成凹部,从而能够制造同时实现了轻量化和确保刚度的锻造曲轴。在制造时,只是通过自销部的偏心方向插入U字形的第一模具而弯折该局部地突出的余料部就足矣,因此,不需要很大的力量就能简便地进行制造。附图说明图1是用于对以往的通常的锻造曲轴的制造工序进行说明的示意图。图2是示意性表示基于本发明第一实施方式的制造方法的整形前的曲轴的臂部形状的图,图2(a)表示立体图,图2(b)表示从轴颈部侧观察时的平面图,图2(c)表示侧视图,图2(d)表示图2(b)的A-A剖面图。图3是示意性表示基于本发明第一实施方式的制造方法的整形后的曲轴的臂部形状的图,图3(a)表示立体图,图3(b)表示从轴颈部侧观察时的平面图,图3(c)表示侧视图,图3(d)表示图3(b)的B-B剖面图。图4是用于对基于本发明第一实施方式的制造方法的整形工序的状况进行说明的示意图,且是从轴颈部侧观察臂部时的平面图,图4(a)表示整形前的状态,图4(b)表示整形后的状态。图5是用于对基于本发明第一实施方式的制造方法的整形工序的状况进行说明的示意图,且是臂部的侧视图,图5(a)表示整形前的状态,图5(b)表示整形后的状态。图6是表示在基于本发明第一实施方式的制造方法的整形工序中使用的U字形的第一模具的图,图6(a)是表示U字形的第一模具的外观的俯视图,图6(b)表示从前端面侧观察时的平面图,图6(c)是表示图6(a)的C-C剖视图,图6(d)是表示图6(a)的D-D剖视图。图7是示意性表示基于本发明第二实施方式的制造方法的整形前的曲轴的臂部形状的图,图7(a)表示从轴颈部侧观察时的平面图,图7(b)表示侧视图。图8是示意性表示基于本发明第二实施方式的制造方法的整形后的曲轴的臂部形状的图,图8(a)表示从轴颈部侧观察时的平面图,图8(b)表示侧视图。图9是用于对基于本发明第二实施方式的制造方法的整形工序的状况进行说明的示意图,且是从轴颈部侧观察臂部时的平面图,图9(a)表示整形前的状态,图9(b)表示整形后的状态。图10是用于对基于本发明第二实施方式的制造方法的整形工序的状况进行说明的示意图,且是臂部的侧视图,图10(a)表示整形前的状态,图10(b)表示整形后的状态。具体实施方式以下,关于本发明的锻造曲轴的制造方法,对其实施方式进行详述。[第一实施方式]作为第一实施方式,在本发明的锻造曲轴的制造方法中采用所述图1所示的制造工序。即,基于本实施方式的制造方法包括以下各工序:在热状态下进行的预成形(辊轧成形和弯曲锻造)、在热状态下进行的模锻(粗锻和精锻)、在热状态下进行的去除飞边以及在热状态下进行的整形。特别是,在基于本实施方式的制造方法中,与所述图1所示的以往的制造方法相比,其较大的特征在于模锻工序以及整形工序的方式。1.曲轴的臂部的形状图2是示意性表示基于本发明第一实施方式的制造方法的整形前的曲轴的臂部形状的图。图3是示意性表示基于本发明第一实施方式的制造方法的整形后的曲轴的臂部形状的图。图2和图3均是代表性地抽选出一个曲轴的臂部(包括平衡块部)来进行表示,图2(a)和图3(a)表示立体图,图2(b)和图3(b)表示从轴颈部侧观察时的平面图,图2(c)和图3(c)表示侧视图。图2(d)表示图2(b)的A-A剖面图,图3(d)表示图3(b)的B-B剖面图。如图3所示,作为本实施方式的最终产品的锻造曲轴的臂部形状即整形后的臂部形状为:臂部A的销部P附近的两个侧部Aa、Ab朝向轴颈部J侧鼓出,上述两个侧部Aa、Ab的厚度较厚。而且,该臂部形状为使臂部A的轴颈部J侧的表面中的两个侧部Aa、Ab的内侧的区域As具有凹部的形状。更加具体而言,如图3(d)所示,臂部A的两个侧部Aa、Ab增厚,两个侧部Aa、Ab的内侧由于凹部而减薄厚度,该凹部的内侧增厚。简而言之,整形后的臂部形状为:将臂部A的两个侧部Aa、Ab的厚度维持得较厚,并且在臂部A的轴颈部J侧的表面形成有凹部。具有这样的形状的臂部的锻造曲轴能够利用臂部A表面的凹部而实现轻量化,与此同时能够利用维持臂部A的两个侧部Aa、Ab的厚度而实现确保刚度。相对与此,如图2所示,整形前的臂部形状为使臂部A的轴颈部J侧的表面中的两个侧部Aa、Ab的内侧的区域As具有与整形后的最终产品形状相一致的凹部的形状。该凹部平滑地扩展至臂部A的两个侧部Aa、Ab区域。由此,该臂部形状为两个侧部Aa、Ab的厚度比整形后的最终产品的两个侧部Aa、Ab的厚度薄。而且,在臂部A的两个侧部Aa、Ab的外周分别形成有自该外周突出的余料部Aaa、Aba。该余料部Aaa、Aba为沿着臂部A的两个侧部Aa、Ab的外周延伸的板状,并且该余料部Aaa、Aba的厚度等于或小于臂部A的两个侧部Aa、Ab的厚度。这样的整形前的臂部形状是利用模锻工序的精锻来最终造形的,并通过去除飞边来维持该形状。2.锻造曲轴的制造方法如上所述,本实施方式的制造方法包括:预成形、模锻、去除飞边以及整形各工序,所有的工序均在热状态下接连进行。另外,在需要调整销部的配置角度的情况下,在去除飞边工序之后整形工序之前追加扭转工序。在本实施方式的制造方法中,与所述图1所示的以往的制造方法同样地,通过经过预成形工序来使弯曲坯件成形。接下来,经过模锻工序(粗锻和精锻),由此自上述弯曲坯件成形被造形成具有所述图2所示的臂部形状的曲轴的形状的、带有飞边的精锻件。粗锻和精锻的任一模锻均是通过使用一对模具的上下锻压进行的。在此,如上所述,被造形成精锻件的曲轴的形状为:在臂部A的轴颈部J侧的表面形成有凹部,并在臂部A的两个侧部Aa、Ab的外周形成有板状的余料部Aaa、Aba。该凹部平滑地扩展至臂部A的两个侧部Aa、Ab区域,余料部Aaa、Aba的厚度等于或小于两个侧部Aa、Ab的厚度。在模锻所使用的模具中刻入有反映了上述形状的模具雕刻部,在与臂部表面的凹部相对应的部位以及与臂部外周的余料部Aaa、Aba相对应的部位中的任一部位,脱模坡度均不会变成反坡。因此能够无障碍地进行模锻。接下来,经过去除飞边工序,由此自带有飞边的精锻件冲切去除飞边而获得锻造曲轴。经过去除飞边工序而获得的曲轴具有所述图2所示的臂部形状,在臂部A的两个侧部Aa、Ab的外周形成有余料部Aaa、Aba。然后,进行到整形工序。图4和图5是用于对基于本发明第一实施方式的制造方法的整形工序的状况进行说明的示意图,图4(a)和图5(a)表示整形前的状态,图4(b)和图5(b)表示整形后的状态。上述图中,图4表示从轴颈部侧观察臂部时的平面图,图5表示臂部的侧视图。另外,图5的侧视图中的剖面线部表示本实施方式中使用的专用的模具(第一模具、第二模具)的臂部中心线上的剖面。图6是表示在基于本发明第一实施方式的制造方法的整形工序中使用的U字形的第一模具的图,图6(a)是表示外观的俯视图,图6(b)表示从前端面侧观察时的平面图,图6(c)表示图6(a)的C-C剖视图,图6(d)表示图6(a)的D-D剖视图。在整形工序中,与以往的通常的整形工序同样地使用上下一对模具。在图4和图5中,省略该整形用模具的图示。在本实施方式的整形用模具中,刻入有反映了所述图3所示的曲轴的最终产品形状中的除了臂部A以外的部分(例如轴颈部J、销部P)的形状的模具雕刻部。为了收纳后述的第一模具,该整形用模具的与臂部A相对应的部位在销部P的偏心方向上大幅度开放。而且,为了收纳后述的第二模具,整形用模具的与臂部A的轴颈部J侧的表面的凹部相对应的部位开放。特别是,在本实施方式的整形工序中,如图4~图6所示,在整形用模具之外还使用第一模具10和第二模具20。第一模具10以及第二模具20都分别独立于整形用模具,并被收纳在整形用模具的开放的部分。第一模具10是夹着曲轴的臂部A的臂部中心线呈对称形状的U字形。该第一模具10能够沿着曲轴的臂部A的臂部中心线(销部P的偏心方向)进退移动。第一模具10的进退移动是利用连结于第一模具10的液压缸等进行的。在第一模具10的基部11的内表面11a、11b、11c刻入有所述图3所示的曲轴的臂部A的外周形状,即从臂部A的两个侧部Aa、Ab到销部P的偏心方向的顶部(以下,也称为“销顶部”)Ac的范围的外周形状。自第一模具10的基部11突出的两端部12A、12B的内表面12Aa、12Ba平滑地连接于基部11的内表面11a、11b,该内表面12Aa、12Ba以越靠轴颈部J侧开口越大的方式形成为扭转的面。另一方面,在第二模具20刻入有与臂部表面的凹部相对应的形状的模具雕刻部。第二模具20能够以相对于臂部表面的凹部接触或离开的方式进退移动。第二模具20的进退移动是利用连结于第二模具20的液压缸等进行的。使用了这样的整形用模具、第一模具10以及第二模具20的本实施方式的整形工序如下进行。首先,将去除飞边之后的曲轴收纳在下侧的整形用模具的模具雕刻部。此时,第一模具10以及第二模具20均处于从曲轴离开了的退避状态,如图4(a)所示,臂部A包括臂部外周的余料部Aaa、Aba,并且完全不受模具约束。自该状态使上侧的整形用模具朝向下侧的整形用模具移动。由此,对曲轴的轴部(例如轴颈部J、销部P、前端部Fr、法兰部Fl)轻微地冲压下压,进一步对平衡块部W轻微地冲压下压,而矫正为最终产品的尺寸形状。利用整形用模具进行冲压下压之后,如图5(a)所示,使第二模具20行进,并将第二模具20按压到臂部A的轴颈部J侧的表面。此时,第二模具20被按压到臂部A的轴颈部J侧的表面中的至少除了两个侧部Aa、Ab区域以外的凹部区域As的表面。接下来,使第一模具10行进,并将第一模具10自曲轴的销部P的偏心方向插入臂部A。随着第一模具10的插入,首先,第一模具10的两端部12A、12B的内表面12Aa、12Ba分别与臂部A的两个侧部Aa、Ab的外周的余料部Aaa、Aba相接触。利用分别与余料部Aaa、Aba相接触的第一模具10的两端部12A、12B的内表面12Aa、12Ba,而将各余料部Aaa、Aba逐渐地弯向轴颈部J侧的表面。然后,如图4(b)以及图5(b)所示,利用继续与余料部Aaa、Aba接触的第一模具10的基部11的内表面11a、11b,而将各余料部Aaa、Aba最终弯向轴颈部J侧的表面。由此,臂部A的两个侧部Aa、Ab朝向轴颈部J侧的表面凸出与各自的余料部Aaa、Aba的体积相对应的量。如此地,如所述图3所示,能够获得臂部A的两个侧部Aa、Ab的厚度较厚且在臂部A的轴颈部J侧的表面形成有凹部的曲轴。另外,在插入第一模具10时,臂部A通过第二模具20被推压到该臂部A的轴颈部J侧的表面的凹部区域As而被约束着,因此臂部A的凹部区域As的形状稳定。而且,利用第一模具10的插入而使臂部A的两个侧部Aa、Ab朝向轴颈部J侧凸出,该凸出形状利用第二模具20而精密成形。完成第一模具10的插入之后,使第一模具10以及第二模具20后退从而自臂部A退避,然后,使上侧的整形用模具上升以取出曲轴。根据本实施方式的制造方法,能够在将臂部A的两个侧部Aa、Ab的厚度维持得较厚的同时,在臂部A的轴颈部J侧的表面形成凹部,从而能够制造同时实现了轻量化和确保刚度的锻造曲轴。在该制造方法中,在臂部A的两个侧部Aa、Ab的外周形成有局部突出的余料部Aaa、Aba,只是通过自销部的偏心方向插入U字形的第一模具弯折该局部突出的余料部Aaa、Aba就足矣。因此,不需要很大的力量就能简便地进行本实施方式的曲轴的制造。特别是,在本实施方式中,将第二模具20按压到臂部A的表面,而不再将该第二模具20进一步按压,因此用于保持第二模具20的力较小即可。另外,在本实施方式中,在对臂部A的最终的形状进行造形时只是弯折余料部Aaa、Aba而已,因此,其变形很少会对轴颈部等其他的部分产生影响。另外,在本实施方式中,在整形工序中实施臂部外周的余料部Aaa、Aba的弯折,因此无需改变以往的制造工序。当然,臂部外周的余料部Aaa、Aba的弯折只要是在去除飞边工序之后进行即可,即使在整形工序以外的其他工序进行也是可以的。[第二实施方式]第二实施方式以上述第一实施方式为基础,改变了锻造曲轴的臂部形状。1.曲轴的臂部的形状图7是示意性表示基于本发明第二实施方式的制造方法的整形前的曲轴的臂部形状的图。图8是示意性表示基于本发明第二实施方式的制造方法的整形后的曲轴的臂部形状的图。图7和图8均是代表性地抽选出一个曲轴的臂部(包括平衡块部)来进行表示,图7(a)和图8(a)表示从轴颈部侧观察时的平面图,图7(b)和图8(b)表示侧视图。如图8所示,作为本实施方式的最终产品的锻造曲轴的臂部形状,即整形后的臂部形状,与上述第一实施方式相同地,将臂部A的两个侧部Aa、Ab的厚度形成得较厚,并且使在臂部A的轴颈部J侧表面的区域As具有凹部。而且,本实施方式的整形后的臂部形状为:除了将臂部A的两个侧部Aa、Ab的厚度形成得较厚以外,还将在自该两个侧部Aa、Ab至销顶部Ac的连续的范围内的厚度形成得较厚。简而言之,整形后的臂部形状为:自臂部A的两个侧部Aa、Ab至销顶部Ac的范围的厚度连续地维持得较厚,并且在臂部A的轴颈部J侧的表面形成有凹部。具有这样形状的臂部的锻造曲轴能够利用臂部A表面的凹部而实现轻量化,与此同时,能够利用维持臂部A的两个侧部Aa、Ab的厚度而实现确保刚度。在此,由于作为销部P和臂部A的接缝的销焊角(日文:フィレット)部是易于产生应力集中的部分,因此,为了提高疲劳强度,大多会实施基于高频感应加热所进行的淬火。此时,由于臂部A的销顶部Ac与被实施淬火的销焊角部相邻,因此若不确保一定程度的厚度,则存在产生淬裂的隐患。针对这样的情况,本实施方式的臂部A的销顶部Ac厚度较厚,因此抗淬裂性优异。相对与此,如图7所示,本实施方式的整形前的臂部形状为:使臂部A的轴颈部J侧的表面中的两个侧部Aa、Ab以及销顶部Ac的内侧的区域As具有与整形后的最终产品形状相一致的凹部。该凹部平滑地扩展至臂部A的两个侧部Aa、Ab以及销顶部Ac的区域。由此,该臂部形状为两个侧部Aa、Ab以及销顶部Ac的厚度比整形后的最终产品的厚度薄。而且,在自臂部A的两个侧部Aa、Ab至销顶部Ac的范围内,在该范围的外周形成自该外周突出的余料部Aaa、Aba、Aca。该余料部Aaa、Aba、Aca为沿着自臂部A的两个侧部Aa、Ab至销顶部Ac的范围的外周延伸的板状,该余料部Aaa、Aba、Aca的厚度分别等于或小于臂部A的两个侧部Aa、Ab的厚度以及销顶部Ac的厚度。与上述第一实施方式相同地,这样的整形前的臂部形状利用模锻工序的精锻而最终造形,并通过去除飞边维持其形状。2.锻造曲轴的制造方法本实施方式的制造方法与上述第一实施方式相同。即,经过模锻工序和去除飞边工序,由此获得具有所述图7所示的臂部形状的曲轴。用该曲轴来经过整形工序,由此获得具有所述图8所示的臂部形状的最终产品的曲轴。图9和图10是用于对基于本发明的第二实施方式的制造方法的整形工序的状况进行说明的示意图,图9(a)和图10(a)都表示整形前的状态,图9(b)和图10(b)都表示整形后的状态。图9和图10中,图9表示从轴颈部侧观察臂部时的平面图,图10表示臂部的侧视图。在整形工序中,使用上述第一实施方式所使用的整形用模具、第一模具10以及第二模具20。与上述第一实施方式相同地,利用整形用模具进行冲压下压之后,如图10(a)所示,使第二模具20行进,并将第二模具20按压到臂部A的轴颈部J侧的表面。接下来,与上述第一实施方式相同地,自图9(a)所示的状态,使第一模具10行进,并将第一模具10自曲轴的销部P的偏心方向插入臂部A。随着第一模具10的插入,首先,利用与臂部A的两个侧部Aa、Ab的余料部Aaa、Aba分别接触的第一模具10的两端部12A、12B的内表面12Aa、12Ba,而将余料部Aaa、Aba逐渐地弯向轴颈部J侧的表面。然后,如图9(b)和图10(b)所示,利用与臂部A的两个侧部Aa、Ab的各余料部Aaa、Aba继续接触的第一模具10的基部11的内表面11a、11b,而将余料部Aaa、Aba最终弯向轴颈部J侧的表面。与此同时,利用与臂部A的销顶部Ac的余料部Aca接触的第一模具10的基部11的内表面11c,而将余料部Aca最终弯向轴颈部J侧的表面。由此,将臂部A的两个侧部Aa、Ab以及销顶部Ac的余料部Aca朝向轴颈部J侧的表面凸出与各自的余料部Aaa、Aba、Aca的体积相对应的量。如此地,如所述图8所示,能够获得将自臂部A的两个侧部Aa、Ab至销顶部Ac的连续的范围的厚度形成得较厚并在臂部A的轴颈部J侧的表面形成有凹部的曲轴。根据本实施方式的制造方法,能够在将自臂部A的两个侧部Aa、Ab至销顶部Ac的范围的厚度连续地维持得较厚的同时,在臂部A的轴颈部J侧的表面形成凹部。因此,能够制造同时实现轻量化和确保刚度且抗淬裂性优异的锻造曲轴。该制造方法只是在臂部A的两个侧部Aa、Ab以及销顶部Ac的外周形成局部突出的余料部Aaa、Aba、Aca,并通过自销部的偏心方向插入U字形的第一模具而弯折该局部突出的余料部Aaa、Aba、Aca就足矣。因此,本实施方式的曲轴的制造不需要很大的力量就能简便地进行。当然,本实施方式的制造方法能够达到与上述第一实施方式相同的效果。另外,本发明并不限定于上述各实施方式,在不脱离本发明的主旨的范围内,能够进行各种改变。例如,并不是一定需要第二模具20。因为如果不要求臂部A具有精密的尺寸精度,即使没有第二模具20,通过利用第一模具10来弯折臂部外周的余料部Aaa、Aba,也能够在将臂部A的两个侧部Aa、Ab的厚度维持得较厚的同时,在臂部A的轴颈部J侧的表面形成凹部。本实施方式的制造方法不仅用于制造搭载于四缸发动机的曲轴,还能适用于制造搭载于三缸发动机、直列六缸发动机、V型六缸发动机等的曲轴(以下,称为“三缸等的曲轴”)。在制造三缸等的曲轴的情况下,销部的围绕旋转轴(轴颈部)的配置角度以120°或60°等间隔地切换。因此,在三缸等的曲轴的制造工序中,根据平衡块部的形状,在去除飞边工序之后整形工序之前,追加扭转工序。在制造三缸等的曲轴时适用本实施方式的制造方法的情况下,也可以自销部的偏心方向进行上述余料部弯折工序中的第一模具的插入。产业上的可利用性本发明能够有效地用于制造搭载于所有的往复式发动机的锻造曲轴。附图标记说明1:锻造曲轴,J、J1~J5:轴颈部,P、P1~P4:销部,Fr:前端部,Fl:法兰部,A、A1~A8:曲臂部,W、W1~W8:平衡块部,Aa、Ab:臂部的侧部,Ac:臂部的销顶部,As:臂部的轴颈部侧表面的两个侧部的内侧区域,Aaa、Aba、Aca:余料部,10:第一模具,11:第一模具的基部,11a、11b、11c:第一模具的基部的内表面,12A、12B:第一模具的端部,12Aa、12Ba:第一模具的端部的内表面,20:第二模具