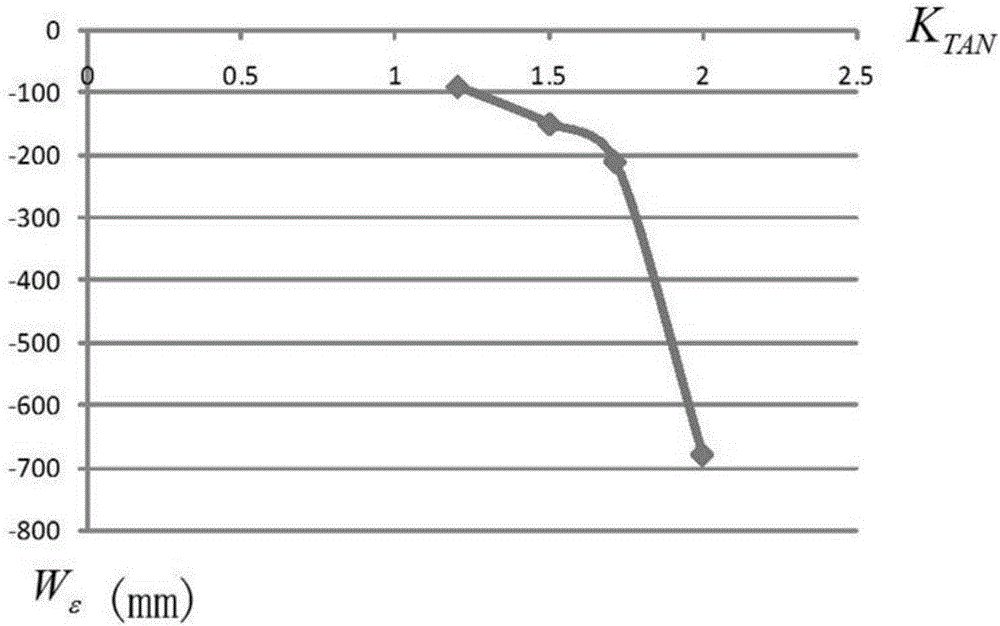
本发明涉及一种剪板机的剪程控制方法,具体说是一种基于板宽的剪板机剪程控制方法。
背景技术:
:剪板机借助于运动的上刀片和固定的下刀片,按照板材所需要的尺寸将板材剪切断裂分离。剪板机常用来剪裁直线边缘的板料毛坯,主要用于金属加工行业,属于锻压机械中的一种。剪程过短会因剪切不完全而造成板材报废;剪程过长会降低工作效率,增加能源消耗。因此对于剪程的精确控制是十分必要的。目前剪板机的剪程控制主要为上下限位开关控制、时间继电器控制、电位计控制三种方法。上下限位开关控制方法主要通过机床提供的上下限位开关信号对剪程进行控制,当检测到下限位开关信号时即判定刀架运行至下限位,停止剪切动作。这样的设计,每次刀架在剪切时都会从上限位运行至下限位,增加了不必要的能源消耗。时间继电器控制方法主要通过控制刀架执行剪切动作的时间来控制剪程,相对于上下限位控制剪程已经有了很大的进步,已经可以根据设置时间的长短来控制剪切行程的大小。但是由于时间受人的主观影响较大,在调试和使用中会带来一定的误差,难以达到很高的控制精度。电位计控制方法中,刀架位置会通过电位计反馈成电压值。根据实时监测电压值的变化,计算出当前刀架所在的位置,以此来控制刀架到达指定位置。此种控制方式有一定的局限性,因为电位计只可以反馈出垂直方向的刀架行程,如果刀架的剪切角改变时,系统不会自动调整板料宽度和电位计反馈值的对应关系,所以剪切精度就不能保证,剪切同样板宽的板料会出现不能完全切断或是切断板料后又下行过长距离的情况,为保证剪切精度,用户需要再一次标定板料宽度和电位计反馈值的对应关系,这种方法严重影响剪切效率,也提高了机床厂家后期的维护成本。目前业内在剪程方面的研究以上下限位开关控制、时间继电器控制为主,电位计控制用的很少,主要是因为板宽控制精度无法满足用户要求。技术实现要素:本发明的目的是针对现有技术的不足,提供一种能够根据板材宽度,精确控制剪程的方法。本发明方法的基本原理。剪板机中,运动控制部件控制剪板机刀架垂直运动,其剪程测量部件测量刀架运动距离。当剪板机执行剪切动作时,剪程测量部件实时测量当前剪程,并通过算法将当前剪程转化为当前剪切板宽,直到测量出当前剪切板宽等于目标板宽时,通过运动控制部件停止剪切动作。计算标定角度下的当前剪切板宽:根据三角函数,刀架在标定角度αnorm下执行剪切动作,垂直方向的剪程S与水平方向的剪切板宽W满足线性关系:W=Stan(αnorm)---(1-1).]]>根据电位计特性,刀架运动位置S与电位计反馈来的电压值V也满足线性关系:V=S×Kp(1-2)其中:KP为电位计系数。调试阶段,在标定角度下执行剪切动作,测量并记录出最大剪切板宽和最小剪切板宽以及与之对应的监测电位计采集到的电压值:(W1,V1)、(W0,V0)。由于反馈电压与标定角度下的剪切板宽成线性关系,可以将这两组数据拟合一元函数,推导出在标定角度下监测电位计采集到的电压值与当前剪切板宽的对应关系:W=Knorm×V+Bnorm(1-3),式中:乘常数加常数Bnorm=W0-Knorm×V0。为了提高算法精度,增加测量数据,可以将该公式用于多组数据对W和V进行分段的线性拟合。即:将剪板机剪切角度调节至标定角度αnorm,在该标定角度下执行剪切动作。按照设定的间隔,记录下实际剪切板宽W(W={wi|i=0,1,……,n})和与之对应的监测电位计采集到的电压值V(V={vi|i=0,1,……,n})。至少记录两组以上数据(n≥1),优选,数据中包含最大剪切板宽和最小剪切板宽以及对应的电压值。多组数据对W和V进行分段线性拟合,得到:乘常数Knorm,加常数Bnorm。从而确定由监测电位计采集到的电压值计算对应剪切板宽的数学模型W=Knorm×V+Bnorm。剪切角与剪切板宽关联计算:根据标定角度下的数据建立参数表1:表1剪程电压参数表剪切板宽标定角度αnorm电压值当前角度α电压值(映射值)最小剪切板宽时W0V0Vm0最大剪切板宽时W1V1Vm1根据图1,可以看出:1)在剪切板材宽度为最大值时,电位器行程固定,所以不论剪切角α为何值,满足:V0=Vm0(1-4)2)根据参数表以及三角变换,映射出任何角度下,剪切板宽W1对应的电压值Vm1。推导算法如下:a)V0=S0×Kpb)V1=(S0+ΔS)×Kpc)Vm1=(S0+ΔSm)×Kpd)ΔS=(W0-W1)×tan(αnorm)e)ΔSm=(W0-W1)×tan(α)式中:S0--标定角度下,最小剪切板宽时对应的剪程位置;ΔS--标定角度下,从最小剪切板宽运动到最大剪切板宽时的剪程距离;ΔSm--任意角度下,从最小剪切板宽运动到最大剪切板宽时的剪程距离。根据公式a)、b)、c)、d)、e)推导出最大剪切板宽的电压值Vm1:Vm1=V0+tan(α)×(V1-V0)tan(αnorm)---(1-5)]]>根据表1以及式(1-3)可以推导出在任何剪切角度α下当前剪切板宽的计算公式W=Kα×V+Bα其中:乘常数加常数Bα=W0-Kα×Vm0;结合式(1-4)和式(1-5),最终可计算出任何剪切角度α下的剪切板宽W:W=W0+tan(αnorm)tan(α)Knorm×(V-V0)---(1-6)]]>为提高精度,该算法可以适用于多段标定,参数表中数据不局限为2组。剪切角与提前停止剪切板宽关联计算:当刀架运行至提前停止剪切板宽范围之内时,运动控制部件停止剪切动作,刀架依靠惯性继续向目标剪切板宽运动。根据式(1-1),可以得出:Wstopαnorm=Sstopαnormtan(αnorm)---(1-7)]]>Wstopα=Sstopαtan(α)---(1-8)]]>式中:--标定角度αnorm下刀架垂直方向上的提前停止剪程;--标定角度αnorm下刀架水平方向上的提前停止剪切板宽;--设定的剪切角度α下刀架垂直方向上的提前停止剪程;--设定的剪切角度α下刀架水平方向上的提前停止剪切板宽。同一台机床,刀架在垂直方向的运动惯性在各个剪切角度下都一致,可以根据标定角度下的提前停止距离推算出设定的剪切角度α下的提前停止剪切板宽Wstopα=Wstopαnorm×Ktan;Ktan=tan(αnorm)tan(α)---(1-9)]]>式中:Ktan--设定的剪切角度α下的提前停止剪切板宽修正系数。在调试机床阶段,在标定角度下实际剪切板宽与目标剪切板宽之差即为标定角度下的提前停止剪切板宽,将该值记录下来并存入参数表中。在剪切过程中,可以根据当前设定的剪切角度α与标定角度αnorm以及标定角度下的提前停止剪切板宽根据式(1-9),计算出当前设定的剪切角度α下的提前停止剪切板宽提前停止剪切板宽修正:根据式(1-9)计算出当前角度下的提前停止剪切板宽,在执行剪切动作过程中,记录下实际剪切板宽Wact,计算剪切板宽误差Wε(Wε=实际剪切板宽Wact-目标剪切板宽Wtarget)。实验结果如图2,图3,可以明显发现剪切板宽误差Wε与式(1-9)中的Ktan密切相关。从图2,图3可以看出,当前角度α大于标定角度时(Ktan小于1),Knat与误差Wε类似于线性关系;当前角度α小于标定角度时(Ktan大于1),Knat与误差Wε类似于二阶函数。为提高精度,减小剪切板宽误差Wε,可以构造提前停止剪切板宽补偿函数,计算补偿后的提前停止剪切板宽Wstopα-=Wstopαnorm×Ktan+(Ktan-1)×Wstopαnorm×C1(Ktan<1)Wstopαnorm×Ktan+(Ktan-1)×Wstopαnorm×C2+(Ktan-1)2×Wstopαnorm×C3(Ktan>1)---(1-10)]]>式中:C1、C2、C3--提前停止剪切板宽补偿系数,需要在机床调试阶段确定合适的数值,并进行保存。基于上述技术原理,本发明为实现发明目的所提出的基于板宽的剪板机剪程控制方法,其步骤:包括调整数学模型阶段和剪切阶段。所述调整数学模型阶段:首先测量当前剪切角度将其设置为标定角度αnorm。手动调节剪板机剪切角度,记录下最大剪切板宽W1和最小剪切板宽W0以及对应的监测电位计采集到的电压值(V1、V0),即(W1,V1)、(W0,V0)。将记录的数据输入剪板机中的剪程电压参数表。剪切板宽W计算模型:W=Knorm×V+Bnorm(1-3)其中:乘常数加常数Bnorm=W0-Knorm×V0。在标定角度αnorm下执行剪切动作,记录下多个实际剪切板宽Wact和对应的电位计采集到的电压值Vact,用公式1-3计算出与之对应的目标剪切板宽Wtarget。计算剪切板宽误差Wε:Wε=Wact-Wtarget多个Wε取平均,该平均差值即为标定角度下的提前停止剪切板宽将剪切角度α调整至大于标定角度αnorm,此时提前停止剪切板宽修正系数在此剪切角度α下执行剪切动作,记录下实际剪切板宽Wact和对应的电位计采集到的电压值Vact并计算与之对应的目标剪切板宽Wtarget,计算剪切板宽误差Wε;校验调整提前停止剪切板宽计算公式1-10提前停止剪切板宽补偿系数:当实际剪切板宽Wact大于目标板宽Wtarget时,减小提前停止剪切板宽补偿系数C1值,反之增加提前停止剪切板宽补偿系数C1值;多次调节提前停止剪切板宽补偿系数C1大小,直到剪切板宽误差Wε≤设定的限值。将剪切角度α调整至小于标定角度αnorm,此时Ktan>1,在此剪切角度α下执行剪切动作,记录下实际剪切板宽Wact和对应的电位计采集到的电压值Vact并计算与之对应的目标剪切板宽Wtarget,计算剪切板宽误差Wε。校验调整提前停止剪切板宽计算公式1-10提前停止剪切板宽补偿系数:当实际剪切板宽Wact大于目标板宽Wtarget时,首先增大提前停止剪切板宽补偿系数C2,在增大C2无法减小实际剪切板宽和目标剪切板宽之间的误差时可增大补偿系数C3,反之减小提前停止剪切板宽补偿系数(C2,C3)。通过调节提前停止剪切板宽补偿系数(C2,C3)大小,达到剪切板宽误差Wε≤设定的限值。当提前停止剪切板宽补偿系数C、C2和、C3调整完毕,得到提前停止剪切板宽数学模型:Wstopα-=Wstopαnorm×Ktan+(Ktan-1)×Wstopαnorm×C1(Ktan<1)Wstopαnorm×Ktan+(Ktan-1)×Wstopαnorm×C2+(Ktan-1)2×Wstopαnorm×C3(Ktan>1)---(1-10)]]>进入所述剪切阶段。所述剪切阶段:首先测定剪板机当前的剪切角度α的值。按照公式1-10,计算出当前剪切角度下的提前停止剪切板宽同时实时监测电位计采集到的电压值,根据式(1-6)计算出当前剪切板宽W。当刀架运行至提前停止剪切板宽区域时,运动控制部件停止剪切动作,刀架依靠惯性运行至目标剪切板宽。本发明方法,通过电位计采集电压,将刀架在垂直方向的剪程映射为水平方向的剪切板宽。根据标定剪切角度下的剪切板宽与反馈电压对应参数表,在任意剪切角度下,可以由电位计反馈电压推导出当前剪切板宽。设置提前停止剪切板宽,用于补偿刀架运动的惯性对于剪程控制的影响。根据当前剪切角度对提前停止剪切板宽进行修正,在任意剪切角度下都能保证剪切板宽的精度。因此,本发明方法具有如下有益效果:在标定的剪切角度下,剪切板宽误差在0~50mm范围内,通过本发明中的算法修正后,在任意剪切角度下,剪切板宽误差也能到达与标定剪切角度下的误差一样的剪切精度,满足用户的使用需求,误差范围为正值确保不会出现因剪程过短而造成板材报废的情况,同时提高了剪切效率,降低了能源消耗,由于用户不需要再对剪切板宽和角度进行重复标定,也方便用户使用,提高了工作效率。附图说明:图1不同角度下剪切板宽与剪程的关系示意图。图2Ktan与剪切板宽误差曲线(Ktan>1)。图3Ktan与剪切板宽误差曲线(Ktan<1)。图4本发明控制的剪板机的结构图。具体实施方式下面结合实施例和附图,对本发明方法做进一步的详细说明。首先确定机床的最大剪切角度和最小剪切角度,设定剪切角度范围是0.5°-2.0°,选取标定角度αnorm=1.2°。已知机床最大剪程为3200mm。将刀架的剪切角度调整为1.2°,执行剪切动作,记录下剪切板宽为0mm时的反馈电压值和剪切板宽为3200mm时的反馈电压值。将数据录入剪程电压参数表,具体如表2。表2标定角度下的参数表剪切板宽(mm)电压值(V)3200408设置目标剪切板宽Wtarget为2000mm,执行剪切动作,经过测量发现实际剪切板宽Wact为2300mm。经过多组调试,发现实际剪切板宽与目标剪切板宽之间的差值保持在300mm左右,标定角度αnorm下刀架水平方向上的提前停止剪切板宽设置为300mm,以补偿实际剪切板宽和目标剪切板宽之间的差值。在不同的剪切角度下执行剪切动作,调试提前停止剪切板宽补偿系数C1、C2、C3。系数C1需满足:当剪切角度大于标定角度1.2°时,剪切板宽误差Wε控制在100mm以下;系数C2、C3需满足:当剪切角度小于标定角度1.2°时,剪切板宽误差Wε控制在300mm以下。设定C1=0.1,C2=0.3,C3=0.4。设置目标剪切板宽Wtarget为2000mm,剪板机当前的剪切角度α为1.6°。已知TAN(1.2)=0.020947,TAN(1.6)=0.027933,得出Ktan=0.749902,可以计算出当前剪切角度下的剪程电压参数表,具体如表3。表3当前角度下的参数表剪切板宽(mm)电压值(V)3200409.33将C1、C2、C3带入式(1-9),计算出当前剪切角度下的提前停止剪切板宽为217mm。剪板机刀架执行剪切动作时,运动控制模块实时将采集到的反馈电压值转化为当前剪切板宽,当检测到当前反馈电压值为6.36V时,推算出当前剪切板宽为1783mm,由于之前目标剪切板宽设置为2000mm,此时刀架已经运行至提前停止剪切板宽区域。运动控制模块停止剪切动作,刀架依靠惯性运动至目标位置。剪切动作完成。当前第1页1 2 3