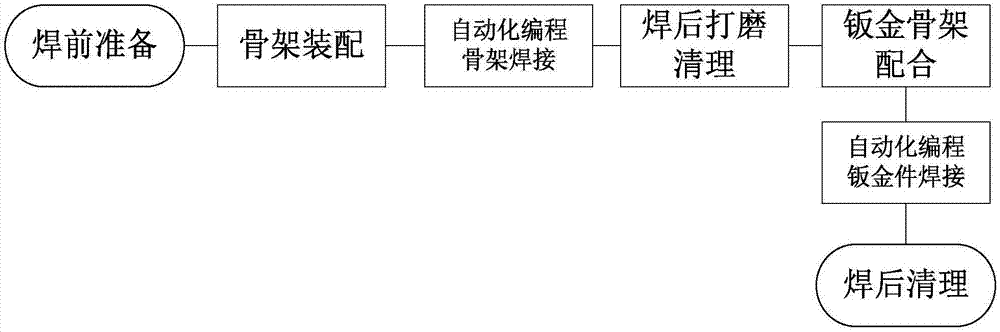
本发明属于轻量化汽车焊接
技术领域:
,涉及一种铝合金轻量车身自动化焊接工艺。
背景技术:
:焊接工艺是使工件的材质达到原子间结合而形成永久性连接的工艺过程。汽车的很多零部件以及整个汽车车身都是以焊接的形式连接起来的,伴随着汽车轻量化的发展,由于铝合金材质轻,所以对铝合金在汽车行业的发展越来越明显,汽车用铝合金焊接工艺也成为一个热题。而汽车用铝合金焊接特点主要有:1、铝合金的热导系数和比热容等都很大;2、铝合金的热裂纹倾向性大;3、异种型号、不同板厚铝合金焊接难度大。因此轻量化汽车铝合金的焊接工艺难度相对较高。目前汽车用铝合金常见的是5系与6系铝合金,不同系列以及不同板厚铝合金焊接难点在于:1、异种系列铝合金连接难度大;2、厚铝合金板焊接过程中熔深不足,焊接质量差;3、薄铝合金板与厚铝合金板焊接过程中,薄铝合金板易咬边、烧穿,而厚铝合金板不能熔合;4、铝合金薄板焊接变形严重。技术实现要素:有鉴于此,本发明为了解决上述不同系列以及不同板厚铝合金板材焊接过程中所存在的问题,提供一种铝合金轻量车身自动化焊接工艺。为达到上述目的,本发明提供一种铝合金轻量车身自动化焊接工艺,主要包括内型材件焊接和外附钣金件焊接,其中内型材件焊接的焊接工艺为:a、焊前准备:将焊缝附近25~50mm的范围内打磨除去内型材件表面氧化膜后用丙酮或乙醇清洗内型材件表面油污,其中内型材件为3mm厚的6系铝合金;b、装配组对:利用夹紧工装将焊缝两侧内型材件压紧,保证内型材件焊缝间隙为0.5~1.0mm,焊缝两侧内型材件的错边量为0.1~0.3mm;c、焊接:根据实际内型材件的匹配性编辑焊缝程序,焊缝程序编程过程中需要考虑变位机以及夹紧工装的状态,防止出现撞枪,同时依据各内型材件之间的装配状态进行焊枪姿态调整,其中焊接工艺采用cmt焊接的dp模式,焊接速度为70~78cm/min,焊接电流为110~130a,焊接电压为18~22v,干伸长度12~18mm;d、焊后清理及检验:内型材件焊接完成后,对焊缝表面进行擦灰清理,按内型材件焊缝质量要求进行检验;外附钣金件焊接的焊接工艺为:e、焊前准备:将钣金件和待焊接内型材件焊缝附近25~50mm的范围内打磨除去钣金件和内型材件表面氧化膜后用丙酮或乙醇清洗钣金件表面油污,其中钣金件为1mm厚的5系铝合金,待焊接内型材件为3mm厚的6系铝合金;f、装配组对:利用夹紧工装将焊缝两侧的钣金件和内型材件压紧,保证钣金件和内型材件焊缝间隙为0.1~0.7mm;g、焊接:根据实际钣金件与内型材件的匹配性编辑焊缝程序,焊缝程序编程过程中需要考虑变位机以及夹紧工装的状态,防止出现撞枪,同时依据钣金件与内型材件的装配状态进行焊枪姿态调整,其中焊接工艺采用cmt焊接的pc模式和cmt模式,焊接速度为48~60cm/min,焊接电流为60~80a,焊接电压为17~19v,干伸长度12~18mm;h、焊后清理及检验:钣金件与内型材件焊接完成后,对焊道周围进行擦灰清理,按钣金件与内型材件的焊缝质量要求进行检验。进一步,步骤a和步骤e打磨所使用的打磨工具均为钢丝碗刷。进一步,步骤b和步骤f夹紧工装均为液压式压臂。进一步,步骤b和步骤f夹紧工装均匀相错排列。进一步,步骤c和步骤g中焊接环境温度≥18℃,湿度≤60%,风速小于2m/s。进一步,步骤c和步骤g焊接采用tps4000-福尼斯焊机,焊接保护气为99.99%ar。本发明的有益效果在于:1、本发明所公开的铝合金轻量车身自动化焊接工艺,通过分析不同系列(5系与6系)不同板厚铝合金以及轻量化汽车的焊接特点,根据实际内型材件的匹配性以及实际钣金件与内型材件的匹配性进行焊缝程序的编辑,焊接机器人系统通过编程可以在焊接过程中切换不同焊接模式以及工艺参数,保证了焊接工艺与零件状态的匹配性,克服了铝合金异种板厚异种型号在焊接过程中出现的厚板不熔,薄板易咬边等问题。2、本发明所公开的铝合金轻量车身自动化焊接工艺,为保证轻量化汽车焊接过程中焊缝的稳定性,使用焊接机器人系统进行焊接,代替了手工焊接,焊缝美观,焊接缺陷较少,保证了焊缝质量和钣金件小变形量,无需矫形,飞溅小,同时减少了焊接与返工工作量,大大增加了轻量化汽车的合格率,提高了铝合金车身的生产效率。附图说明为了使本发明的目的、技术方案和有益效果更加清楚,本发明提供如下附图进行说明:图1为本发明铝合金轻量车身自动化焊接工艺的流程图。具体实施方式下面将对本发明的优选实施例进行详细的描述。实施例中的cmt焊接为冷金属过渡焊接技术。实施例1如图1所示的一种铝合金轻量车身自动化焊接工艺,主要包括内型材件焊接和外附钣金件焊接,其中内型材件焊接的焊接工艺为:a、焊前准备:将焊缝附近30mm的范围内用钢丝碗刷打磨除去内型材件表面氧化膜,用无纺布蘸取丙酮或乙醇清洗内型材件表面油污,以防止缺陷产生,其中内型材件为3mm厚的6系铝合金;b、装配组对:利用夹紧工装将焊缝两侧内型材件压紧,保证内型材件焊缝间隙为0.5mm,焊缝两侧内型材件的错边量为0.1mm,其中夹紧工装为液压式压臂,夹紧工装均匀相错排列,内型材件压紧后检查内型材件与夹紧工装的匹配性,如焊接间隙,错位等现象是否存在;c、焊接:根据实际内型材件的匹配性编辑焊缝程序,焊缝程序编程过程中需要考虑变位机以及夹紧工装的状态,防止出现撞枪,同时依据各内型材件之间的装配状态进行焊枪姿态调整,其中焊接工艺采用cmt焊接的dp模式,焊接速度为70cm/min,焊接电流为110a,焊接电压为22v,干伸长度12mm,根据焊接位置不同对焊接参数可以进行略微调整,以适应热量分布不同状态的件,采用适当的起收弧参数保证了足够的焊接熔深,提高了焊接质量。焊接环境温度为18℃,湿度为60%,风速为2m/s,焊接采用tps4000-福尼斯焊机,焊接机器人状态良好,焊机焊枪无严重飞溅,送丝管、送丝机内无大量铝屑,焊接保护气为99.99%ar;d、焊后清理及检验:内型材件焊接完成后,对焊缝表面用碗刷进行擦灰清理,旋转锉打磨蒙皮干涉点,按内型材件焊缝质量要求进行检验;外附钣金件焊接的焊接工艺为:e、焊前准备:将钣金件和待焊接内型材件焊缝附近25mm的范围内用钢丝碗刷打磨除去钣金件和内型材件表面氧化膜,用无纺布蘸取丙酮或乙醇清洗钣金件表面油污,以防止缺陷产生,其中钣金件为1mm厚的5系铝合金,待焊接内型材件为3mm厚的6系铝合金;f、装配组对:利用夹紧工装将焊缝两侧的钣金件和内型材件压紧,保证钣金件和内型材件焊缝间隙为0.1mm,其中夹紧工装为液压式压臂,夹紧工装均匀相错排列,钣金件和内型材件压紧后检查钣金件、内型材件压紧与夹紧工装的匹配性,如否存在较大间隙,钣金件变形等现象;g、焊接:根据实际钣金件与内型材件的匹配性编辑焊缝程序,焊缝程序编程过程中需要考虑变位机以及夹紧工装的状态,防止出现撞枪,同时依据钣金件与内型材件的装配状态进行焊枪姿态调整,其中焊接工艺采用cmt焊接的pc模式和cmt模式,焊接速度为48cm/min,焊接电流为60a,焊接电压为17v,干伸长度12mm,焊接环境温度为18℃,湿度为50%,风速为2m/s,焊接采用tps4000-福尼斯焊机,焊接机器人状态良好,焊机焊枪无严重飞溅,送丝管、送丝机内无大量铝屑,焊接保护气为99.99%ar;h、焊后清理及检验:钣金件与内型材件焊接完成后,对焊道周围进行擦灰清理,按钣金件与内型材件的焊缝质量要求进行检验。实施例2一种铝合金轻量车身自动化焊接工艺,主要包括内型材件焊接和外附钣金件焊接,其中内型材件焊接的焊接工艺为:a、焊前准备:将焊缝附近40mm的范围内用钢丝碗刷打磨除去内型材件表面氧化膜,用无纺布蘸取丙酮或乙醇清洗内型材件表面油污,以防止缺陷产生,其中内型材件为3mm厚的6系铝合金;b、装配组对:利用夹紧工装将焊缝两侧内型材件压紧,保证内型材件焊缝间隙为1.0mm,焊缝两侧内型材件的错边量为0.3mm,其中夹紧工装为液压式压臂,夹紧工装均匀相错排列,内型材件压紧后检查内型材件与夹紧工装的匹配性,如焊接间隙,错位等现象是否存在;c、焊接:根据实际内型材件的匹配性编辑焊缝程序,焊缝程序编程过程中需要考虑变位机以及夹紧工装的状态,防止出现撞枪,同时依据各内型材件之间的装配状态进行焊枪姿态调整,其中焊接工艺采用cmt焊接的dp模式,焊接速度为78cm/min,焊接电流为130a,焊接电压为18v,干伸长度18mm,根据焊接位置不同对焊接参数可以进行略微调整,以适应热量分布不同状态的件,采用适当的起收弧参数保证了足够的焊接熔深,提高了焊接质量。焊接环境温度为20℃,湿度为50%,风速为1.5m/s,焊接采用tps4000-福尼斯焊机,焊接机器人状态良好,焊机焊枪无严重飞溅,送丝管、送丝机内无大量铝屑,焊接保护气为99.99%ar;d、焊后清理及检验:内型材件焊接完成后,对焊缝表面用碗刷进行擦灰清理,旋转锉打磨蒙皮干涉点,按内型材件焊缝质量要求进行检验;外附钣金件焊接的焊接工艺为:e、焊前准备:将钣金件和待焊接内型材件焊缝附近40mm的范围内用钢丝碗刷打磨除去钣金件和内型材件表面氧化膜,用无纺布蘸取丙酮或乙醇清洗钣金件表面油污,以防止缺陷产生,其中钣金件为1mm厚的5系铝合金,待焊接内型材件为3mm厚的6系铝合金;f、装配组对:利用夹紧工装将焊缝两侧的钣金件和内型材件压紧,保证钣金件和内型材件焊缝间隙为0.2mm,其中夹紧工装为液压式压臂,夹紧工装均匀相错排列,钣金件和内型材件压紧后检查钣金件、内型材件压紧与夹紧工装的匹配性,如否存在较大间隙,钣金件变形等现象;g、焊接:根据实际钣金件与内型材件的匹配性编辑焊缝程序,焊缝程序编程过程中需要考虑变位机以及夹紧工装的状态,防止出现撞枪,同时依据钣金件与内型材件的装配状态进行焊枪姿态调整,其中焊接工艺采用cmt焊接的pc模式和cmt模式,焊接速度为60cm/min,焊接电流为80a,焊接电压为19v,干伸长度18mm,焊接环境温度为20℃,湿度为60%,风速为1.5m/s,焊接采用tps4000-福尼斯焊机,焊接机器人状态良好,焊机焊枪无严重飞溅,送丝管、送丝机内无大量铝屑,焊接保护气为99.99%ar;h、焊后清理及检验:钣金件与内型材件焊接完成后,对焊道周围进行擦灰清理,按钣金件与内型材件的焊缝质量要求进行检验。实施例3一种铝合金轻量车身自动化焊接工艺,主要包括内型材件焊接和外附钣金件焊接,其中内型材件焊接的焊接工艺为:a、焊前准备:将焊缝附近50mm的范围内用钢丝碗刷打磨除去内型材件表面氧化膜,用无纺布蘸取丙酮或乙醇清洗内型材件表面油污,以防止缺陷产生,其中内型材件为3mm厚的6系铝合金;b、装配组对:利用夹紧工装将焊缝两侧内型材件压紧,保证内型材件焊缝间隙为0.8mm,焊缝两侧内型材件的错边量为0.2mm,其中夹紧工装为液压式压臂,夹紧工装均匀相错排列,内型材件压紧后检查内型材件与夹紧工装的匹配性,如焊接间隙,错位等现象是否存在;c、焊接:根据实际内型材件的匹配性编辑焊缝程序,焊缝程序编程过程中需要考虑变位机以及夹紧工装的状态,防止出现撞枪,同时依据各内型材件之间的装配状态进行焊枪姿态调整,其中焊接工艺采用cmt焊接的dp模式,焊接速度为78cm/min,焊接电流为120a,焊接电压为20v,干伸长度15mm,根据焊接位置不同对焊接参数可以进行略微调整,以适应热量分布不同状态的件,采用适当的起收弧参数保证了足够的焊接熔深,提高了焊接质量。焊接环境温度为25℃,湿度为50%,风速为1.5m/s,焊接采用tps4000-福尼斯焊机,焊接机器人状态良好,焊机焊枪无严重飞溅,送丝管、送丝机内无大量铝屑,焊接保护气为99.99%ar;cmt焊接的dp模式就是传统焊机的双脉冲模式,一路是正向脉冲,一路是反向脉冲,由两种脉冲交替变化的焊接方式。d、焊后清理及检验:内型材件焊接完成后,对焊缝表面用碗刷进行擦灰清理,旋转锉打磨蒙皮干涉点,按内型材件焊缝质量要求进行检验;外附钣金件焊接的焊接工艺为:e、焊前准备:将钣金件和待焊接内型材件焊缝附近40mm的范围内用钢丝碗刷打磨除去钣金件和内型材件表面氧化膜,用无纺布蘸取丙酮或乙醇清洗钣金件表面油污,以防止缺陷产生,其中钣金件为1mm厚的5系铝合金,待焊接内型材件为3mm厚的6系铝合金;f、装配组对:利用夹紧工装将焊缝两侧的钣金件和内型材件压紧,保证钣金件和内型材件焊缝间隙为0.3mm,其中夹紧工装为液压式压臂,夹紧工装均匀相错排列,钣金件和内型材件压紧后检查钣金件、内型材件压紧与夹紧工装的匹配性,如否存在较大间隙,钣金件变形等现象;g、焊接:根据实际钣金件与内型材件的匹配性编辑焊缝程序,焊缝程序编程过程中需要考虑变位机以及夹紧工装的状态,防止出现撞枪,同时依据钣金件与内型材件的装配状态进行焊枪姿态调整,其中焊接工艺采用cmt焊接的pc模式和cmt模式,焊接速度为50cm/min,焊接电流为70a,焊接电压为18v,干伸长度15mm,焊接环境温度为25℃,湿度为50%,风速为1.5m/s,焊接采用tps4000-福尼斯焊机,焊接机器人状态良好,焊机焊枪无严重飞溅,送丝管、送丝机内无大量铝屑,焊接保护气为99.99%ar;由于铝的熔点比较低,但是铝型材表面的氧化膜熔点很高,经常会出现起弧电流打开后焊接烧穿,或者密集焊接的时候,工件加热了,起弧直接烧穿了,因此采用采用pc模式,pc模式的优点在于,打开电弧后切换成cmt,能量输入稳定,焊薄板时候成型更好,进而能避免未熔及烧穿问题,调试简单,稳定性高。h、焊后清理及检验:钣金件与内型材件焊接完成后,对焊道周围进行擦灰清理,按钣金件与内型材件的焊缝质量要求进行检验。实施例1~3所制备的铝合金轻量车身合格率和生产效率见表一:表一实施例1实施例2实施例3合格率(%)99.399.299.5生产效率(s/件)175173174通过本发明所公开的铝合金轻量车身自动化焊接工艺制备的铝合金轻量车身,合格率达到99%,高于现有技术的96%,生产效率达到175s/件,高于现有技术的210s/件。最后说明的是,以上优选实施例仅用以说明本发明的技术方案而非限制,尽管通过上述优选实施例已经对本发明进行了详细的描述,但本领域技术人员应当理解,可以在形式上和细节上对其作出各种各样的改变,而不偏离本发明权利要求书所限定的范围。当前第1页12