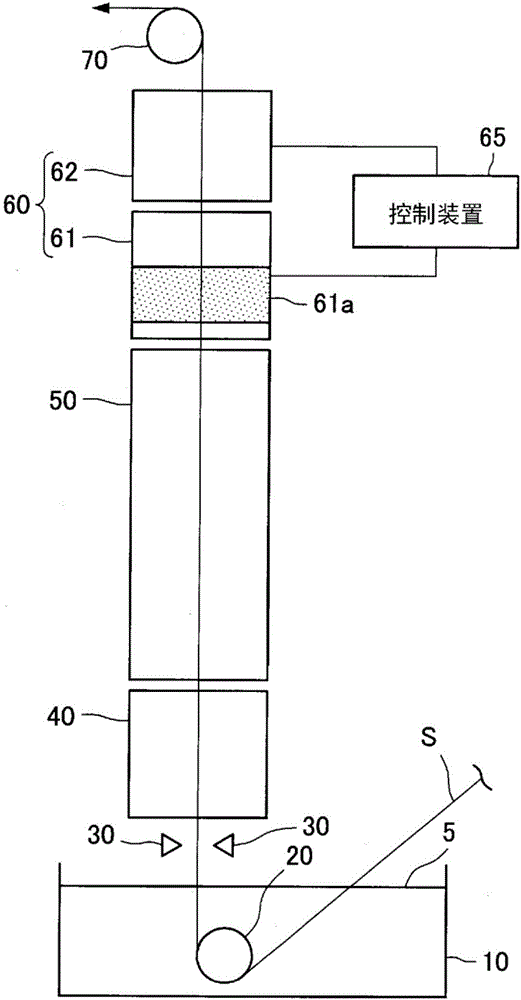
本发明涉及热镀锌的合金化炉中的钢带的冷却方法和冷却设备。
背景技术:
:在钢带的热镀锌处理工序中,钢带在通过脱脂、清洗等预处理槽之后,通过退火炉、放入有熔融锌的锌锅,被铅垂地提起。在合金化炉中对被提起来的钢带进行合金化处理。对于合金化炉而言,在钢带的提起方向上,自上游侧起配置有加热区域、冷却区域。即,合金化炉的冷却区域配置于加热区域的铅垂上方。因此,对于冷却区域中的钢带的冷却而言,为了不给配置于冷却区域的铅垂下方的设备带来滴水等影响而使用气体冷却、喷雾冷却。尤其是,为了提高生产能力,应用冷却能力较高的喷雾冷却(气水冷却)的做法很有效果。但是,若使用喷雾冷却,则在为了对钢带进行强冷却而以大水量进行喷雾的情况下,会在钢带的宽度方向上产生温度不均。该温度不均导致产生皱疤、合金卷曲(日文:合金巻き)等品质不良。针对这样的问题,例如,在专利文献1中,公开了一种合金化炉输出侧气水冷却方法,在该气水冷却方法中,通过调整钢带的冷却模式来抑制过冷所导致的宽度方向上的温度偏差。在专利文献1中,以改变冷却区域的前段与后段之间的冷却比而对后段进行缓冷的方式来冷却钢带,以抑制滴水所导致的冷却偏差并使其成为折断极限温度不均以下。另外,在专利文献2中,公开了一种合金化处理过程的冷却方法,在该冷却方法中,通过根据冷却负荷而相应地分开使用气体冷却和气水冷却,从而避免过渡沸腾并抑制宽度方向上的温度偏差。并且,在专利文献3中,公开了一种密集地配置钢带的宽度方向中央部的喷嘴并设置用于遮挡喷嘴的闸门的技术。另外,在下述专利文献4中,公开了如下一种技术:为了使冷却区域的输出侧温度为240℃以下以防止在气水冷却设备的输出侧产生颈缩、钢板的弯曲,根据预定的关系式对张力值和温度不均进行控制。另外,在下述专利文献5中,公开了如下一种技术:为了使镀层中的Fe浓度量为适当的量,针对每个区域分开使用气水冷却和利用气体进行的冷却,以使得不进入会产生冷却偏差的过渡沸腾区域。现有技术文献专利文献专利文献1:日本特开2006-111945号公报专利文献2:日本特开平11-43758号公报专利文献3:日本特公平7-65153号公报专利文献4:日本特开平9-268358号公报专利文献5:日本特开2000-256818号公报技术实现要素:发明要解决的问题但是,在上述专利文献1所记载的冷却方法中,由于是利用对前段进行高负荷冷却并对后段进行缓慢冷却的冷却模式来消除温度不均的方法,因此,在兼顾冷却区域的冷却能力确保和温度不均的消除这两方面时存在极限。另外,在上述专利文献2所记载的冷却方法中,分开使用了气体冷却和气水冷却,但是可明确的是,在该情况下也是,在气体冷却时冷却区域的冷却能力降低。即,不管在上述专利文献1和专利文献2中的哪一种方法中,对于消除高速通板条件下的温度不均而言效果都受到限制,其结果,不能以高速进行通板,从而生产率降低。另外,在使用上述专利文献3所公开的技术的情况下,闸门会妨碍雾沫的流动或引起滴水,因此无法应用。另外,密集地配置于中央部的喷嘴会使中央部的水流量密度在骤冷点附近增加,使骤冷点温度上升而导致宽度方向上的冷却不均。并且,上述专利文献4所公开的技术是以钢板的张力值为基础对能够容许的温度不均进行设定的技术,但由于无法极端地改变钢板的张力值,因此无法应用于实际的操作。另外,即使使用上述专利文献5所公开的技术,也难以完全抑制因滴水的影响而产生冷却不均。因此,本发明是鉴于上述问题而做出的,本发明的目的在于,提供能够在合金化炉的冷却区域中对钢带进行喷雾冷却并能够兼顾生产率和品质的、新的且改良了的钢带的冷却方法和冷却设备。用于解决问题的方案为了解决上述问题,根据本发明的某一观点,提供一种钢带的冷却方法,在该冷却方法中,利用合金化炉的冷却设备中的喷雾冷却来冷却钢带,该合金化炉用于对被热镀锌了的钢带进行合金化处理。在该冷却方法中,利用被设在冷却设备的通板方向上游侧的冷却调整设备,以对通过该冷却设备的钢带喷射的雾沫喷射量成为钢带的宽度方向上的边缘部的雾沫喷射量小于中心部的雾沫喷射量的方式对通过冷却设备的钢带喷射雾沫,利用至少设于冷却设备的通板方向下游侧的雾沫抽吸设备来对向钢带喷射出的雾沫的至少一部分进行抽吸,以如下通板速度来冷却所述钢带,在该通板速度下,在自钢带的冷却开始直到冷却结束为止的期间,钢带的温度在膜态沸腾温度范围内,且在所述冷却设备的总冷却长度中的至少自通板方向上游侧起的该总冷却长度的2/3以上的范围内,钢带的宽度方向上的边缘部的温度为中心部的温度以上。也可以是,相对于冷却调整设备的设备长度L(m),钢带的速度被设定为利用下述式(a)算出的上限速度Vmax(m/s)以下,Vmax=(L×(Tin-β’)^m×(Tin-γ’))/(α’×th)...(a)其中,Tin(℃)是冷却设备的入口处的钢带的中心部的温度,th(m)是钢带的厚度,α’、β’、γ’、m是常数,是根据热镀锌设备而设定的。常数也可以分别为,α’=1870000、β’=330、γ’=45、m=0.6。另外,为了解决上述问题,根据本发明的另一观点,提供一种冷却设备,其是利用合金化炉的喷雾冷却来进行冷却的冷却设备,该合金化炉用于对被热镀锌了的钢带进行合金化处理。该冷却设备包括:冷却调整设备,其设于冷却设备的通板方向上游侧,能够对向通过该冷却设备的钢带喷射的雾沫喷射量在钢带的宽度方向上进行调整;以及雾沫抽吸设备,其至少设于冷却设备的通板方向下游侧,用于对向钢带喷射出的雾沫的至少一部分进行抽吸,冷却调整设备对向通过该冷却设备的钢带喷射的雾沫喷射量进行调整,使得钢带的宽度方向上的边缘部的雾沫喷射量小于中心部的雾沫喷射量,该冷却调整设备具有如下那样的钢带的通板方向上的设备长度,使得在自钢带的冷却开始直到冷却结束为止的期间,使钢带的温度在膜态沸腾温度范围内,且在冷却设备的总冷却长度中的至少自通板方向上游侧起的该总冷却长度的2/3以上的范围内,使钢带的宽度方向上的边缘部的温度为中心部的温度以上。也可以是,冷却调整设备以使该冷却调整设备在钢带的通板方向上的设备长度L(m)满足下述式(b)的方式设置,L≥(α×V×th)/((Tin-β)^m)×(Tin-γ))...(b)其中,Tin(℃)是冷却设备的入口处的钢带的中心部的温度,V(m/s)是钢带的速度,th(m)是钢带的厚度,α、β、γ、m是常数,是根据热镀锌设备而设定的。常数也可以分别为,α=1700000、β=330、γ=45、m=0.6。另外,也可以是,冷却调整设备在通板方向上包括多个集管,该集管由沿着宽度方向配置的多个喷嘴形成,各集管以在钢带的宽度方向边缘部不对钢带喷射雾沫的方式构成。也可以是,冷却调整设备的各所述集管以在钢带的宽度方向中心部对钢带喷射雾沫的喷嘴的数量自通板方向上游朝向下游去增加的方式的构成。发明的效果如以上说明那样,采用本发明,能够提供能在合金化炉的冷却区域中对钢带进行喷雾冷却并兼顾生产率和品质的钢带的冷却方法和冷却设备。附图说明图1是表示设有本发明的实施方式的冷却设备的热镀锌设备的概略结构的概略说明图。图2是表示正通过冷却区域的钢带的宽度方向和长度方向上的板温分布的说明图。图3是表示利用该实施方式的合金化炉的冷却区域进行板温控制的概略的说明图。图4是表示冷却水量与骤冷温度之间的关系和冷却水量与钢带的中心部的温度之间的关系的图表。图5是表示冷却水量与宽度方向上的温度分布的改善效果之间的关系的图表。图6是表示本实施方式的冷却区域60的一结构例的说明图。图7是表示具有该实施方式的冷却调整设备的冷却区域前段部的一结构例的说明图。图8是表示气水集管的一结构例的说明图。图9是对冷却调整设备由一级气水集管构成时的冷却调整设备的设备长度进行说明的说明图。图10是作为比较例6而表示自冷却区域的最终段侧设有冷却调整设备的情况下的、正通过冷却区域的钢带的宽度方向和长度方向上的板温分布的说明图。具体实施方式下面,参照附图来详细说明本发明的优选实施方式。此外,在本说明书和附图中,对于实质上具有相同功能结构的构成要件,通过标注相同的附图标记而省略重复说明。<1.热镀锌设备的概要>首先,参照图1说明设有本发明的实施方式的冷却设备的热镀锌设备的概略结构。图1是表示设有本实施方式的冷却设备的热镀锌设备的概略结构的概略说明图。作为利用本实施方式的热镀锌设备进行处理的钢种,存在例如极低碳钢、高张力钢板等。通常,对厚度0.4mm~3.2mm、宽度600mm~1900mm的钢材进行处理。如图1所示,热镀锌设备包括放入有用于对钢带S的表面进行镀层处理的熔融锌5的锌锅10、用于对附着于钢带S的镀层的量进行调整的一对气体喷嘴30、以及由加热区域40、保热区域50和冷却区域60组成的合金化炉。此外,虽然本实施方式的热镀锌设备包括保热区域50,但本发明并不限定于该例子,也能够应用不包括保热区域50的热镀锌设备。在热镀锌设备中,使钢带S进入放入有熔融锌5的锌锅10,利用被浸渍于熔融锌5的沉没辊20将钢带S铅垂地提起。对于被提起来的钢带S,利用自气体喷嘴30喷射的擦拭气体(日文:ワイピングガス)将附着于钢带S的表面的镀层的量调整为预定量。之后,一边将钢带S进一步铅垂地提起,一边利用合金化炉对钢带S进行合金化处理。在合金化炉中,首先,利用加热区域40加热至钢带S的板温达到大致均匀,之后利用保热区域50确保合金化时间而产生合金层。之后,利用冷却区域60对钢带S进行冷却,并利用上辊(日文:トップロール)70将钢带S向接下来的工序输送。本实施方式的合金化炉的冷却区域60包括设于钢带S的通板方向上游侧(即铅垂下方侧(锌锅10侧))的冷却区域前段部61和相对于冷却区域前段部61设于钢带S的通板方向下游侧(即铅垂上方侧)的冷却区域后段部62。在冷却区域前段部61和冷却区域后段部62中分别配置有多级气水集管(图8、图9的附图标记63)。在各气水集管上设有多个以雾沫状喷射冷却水的气水喷射嘴(图9的附图标记64)。自气水喷射嘴喷射出的雾沫被吹送到钢带S的表面。向各气水集管供给的冷却水量受控制装置65控制。另外,在冷却区域60至少设有一对以与钢带S的宽度方向上的边缘部相对的方式配置的雾沫抽吸设备(图6的附图标记67)。雾沫抽吸设备至少设于冷却区域60的通板方向下游侧,用于抽吸向钢带S喷射出的雾沫的至少一部分。<2.喷雾冷却的机理>以往,为了提高生产能力,使用冷却能力较高的喷雾冷却,但在喷雾冷却中,当为了对钢带S进行强冷却而以大水量进行喷雾时,在钢带S的宽度方向上产生温度不均,从而成为引起品质不良的原因。在图2中表示正通过冷却区域60的钢带S的宽度方向和长度方向上的板温分布。在图2的长度方向上的温度分布中,示出了应用本申请之前的中心部的温度Cb和边缘部的温度Eb以及应用本申请之后的中心部的温度Ca和边缘部的温度Ea。另外,在图2的宽度方向上的温度分布中,示出了长度方向上的位置A、B、C处的、应用本申请之前的温度分布和应用本申请之后的温度分布。位置A是利用冷却区域60冷却钢带S的冷却开始位置,位置B是冷却区域前段部61与冷却区域后段部62之间的位置,位置C是利用冷却区域60冷却钢带S的冷却结束位置。在此,将钢带S的宽度方向上的中央部分作为中心部,将钢带S的宽度方向两端侧作为边缘部。对于边缘部而言,将自钢带S的宽度方向端部起到距离为100mm的交界位置为止的范围作为边缘部。在应用本申请之前,对于钢带S的长度方向上的温度而言,如图2所示,边缘部的温度Eb低于中心部的温度Cb。随着自冷却区域前段部61向冷却区域后段部62移动,钢带S的中心部的温度和边缘部的温度均逐渐降低,且中心部的温度和边缘部的温度的温度差逐渐变大。即,当观察宽度方向上的温度分布时,随着输送钢带S,与中心部的温度相比,边缘部的温度变低,在冷却区域60输出侧即位置C,温度分布成为向上凸起的形状。作为在宽度方向上产生温度分布的原因之一,可列举出在冷却区域内部朝向板端部方向去的气体流动。在来自配置于板宽度方向中央附近的喷嘴的气体朝向排气口去时,产生经由冷却区域60的宽度方向端部的流动,该气体流动使附着在钢带S的表面上的雾沫朝向钢带S的两端流动,因此钢带S的边缘部的板温降低。对于钢带S的温度较高的部分而言,钢带表面的镀层附着于上辊70而成为品质不良的原因,另一方面,对于钢带S的温度较低的部分而言,温度低于水的膜态沸腾区域与过渡沸腾区域之间的交界温度即骤冷温度而成为局部的过冷却,从而产生皱疤。因此,需要最终使钢带S的宽度方向上的温度分布均匀。在本实施方式中,为了提高生产能力,作为冷却区域60中的冷却方法,也采用喷雾冷却。为了通过采用喷雾冷却来提高生产能力并且不产生品质不良,本申请发明人进行了认真研究的结果,完成了能够抑制钢带S的边缘部的过冷却且最终使钢带S的宽度方向上的温度分布均匀并避免冷却不稳定的冷却设备。即,在本实施方式的合金化炉的冷却区域60中,为了将钢带S稳定地冷却,在冷却区域60中,维持使附着于钢带S的雾沫进行膜态沸腾的板温。随着液体在沸腾状态下温度升高,液体的形态从核态沸腾变化至过渡沸腾,进而变化至膜态沸腾。通常,在合金化炉的冷却区域60的输入侧,钢带S的温度处于水进行膜态沸腾的温度区域。之后,当随着钢带S的温度的降低而在钢带S的表面上局部地产生水自膜态沸腾变成过渡沸腾的区域时,成为不稳定的冷却,在钢带S上产生温度不均。因此,在本实施方式中,在冷却区域60中,以维持使附着于钢带S的雾沫进行膜态沸腾的板温的方式进行冷却。并且,为了抑制钢带S的边缘部的过冷却,在通板方向上游侧,对向钢带S喷射的雾沫喷射量进行调整,使得钢带S的宽度方向上的边缘部的雾沫喷射量少于钢带S的宽度方向上的中心部的雾沫喷射量。若在钢带S的整个宽度方向上以相同的雾沫喷射量来冷却钢带S,则如所述那样钢带S的边缘部的温度大大降低,边缘部与中心部之间的温度偏差变大。因此,在通板方向上游侧,对向钢带S喷射的雾沫进行调整而抑制钢带S的边缘部的冷却,且排除钢带S的边缘部的过量的雾沫而防止通板过程中的钢带S的边缘部的板温降低。由此,防止边缘部的过冷却,如图2所示,在利用冷却区域60开始冷却直到冷却结束为止的期间,钢带S的温度在膜态沸腾温度范围内且钢带S的边缘部的温度为中心部的温度以上。当观察钢带S的宽度方向上的温度分布时,例如位置B处的状态那样,成为钢带S的宽度方向边缘部的温度比钢带S的宽度方向中心部的温度高的温度曲线。然后,随着钢带S的输送,如图2的钢带S的长度方向上的分布所示,边缘部的温度Ea与中心部的温度Ca之间的温度偏差变小,最终能够使冷却区域60的输出侧的钢带S的宽度方向上的温度分布大致均匀。即,在利用冷却区域60开始冷却直到冷却结束为止的期间,使钢带S的温度在膜态沸腾温度范围内且使钢带S的边缘部的温度为中心部的温度以上,由此避免钢带S的边缘部的不稳定的过渡沸腾状态,防止钢带S的品质不良。此外,并非需要在利用冷却区域60开始冷却直到冷却结束为止的整个范围内使钢带S的边缘部的温度均为中心部的温度以上。只要在冷却区域60的通板方向上的总冷却长度中的至少自通板方向上游侧起的该总冷却长度的2/3以上的范围内使钢带S的边缘部的温度为中心部的温度以上即可。只要在该范围内使钢带S的边缘部的温度为中心部的温度以上,就能够将钢带S的品质保持在容许范围内。如图2所示最终温度差为零是理想的,在现实中,在产生皱疤的温度上限与产生合金卷曲的温度下限之间存在富余,该富余温度通常为40℃左右。因而,只要在自通板方向上游侧起的总冷却长度的2/3以上的范围内使钢带S的边缘部的温度为中心部的温度以上,就能够将最终温度偏差保持在能够避免皱疤和合金卷曲的温度范围内。此外,本见解是根据在实际生产线中对钢带S的温度偏差的产生量进行了调查的结果而研究出的。此时,在总冷却长度的冷却中间位置处,钢带S的边缘部的温度期望比中心部的温度高20℃以上。即,通过在总冷却长度的冷却中间位置处如图2的位置B那样成为钢带S的宽度方向边缘部的温度高于钢带S的宽度方向中心部的温度的温度曲线,能够最终使冷却区域60的输出侧的钢带S的宽度方向上的温度分布大致均匀。<3.利用冷却区域的冷却设备进行的钢带冷却>(3-1.钢带的冷却方法)在图3中表示利用本实施方式的合金化炉的冷却区域60进行板温控制的概略。如图3所示,钢带S通过冷却区域60而被冷却到目标终点温度。通常,在热镀锌处理中,钢带S在合金化炉的冷却区域60的输入侧的温度为大约450℃~600℃,终点温度为300℃~400℃左右。另外,图3所示的骤冷温度Tq是水的膜态沸腾区域与过渡沸腾区域之间的交界温度。比骤冷温度Tq高的温度范围是水在钢带S的表面上发生膜态沸腾的膜态沸腾温度范围。骤冷温度Tq因冷却条件而变化,当以大水量对钢带S进行强冷却时,骤冷温度Tq存在上升的倾向。如图3所示,终点温度与骤冷温度Tq之间的温度差小于冷却区域60的输入侧的板温与骤冷温度Tq之间的温度差。因而,当在冷却区域后段部62对钢带S进行强冷却时,骤冷温度Tq上升,终点温度与骤冷温度Tq之间的温度差变得更小。这样一来,雾沫在冷却区域后段部62发生过渡沸腾的可能性变高,有可能使钢带S产生温度不均。在本实施方式的冷却区域60中,在冷却区域60的通板方向上游侧以大水量积极地冷却钢带S,并使板温始终不会成为骤冷温度Tq以下。具体而言,在冷却区域前段部61的通板方向上游侧设有冷却调整设备61a,该冷却调整设备61a用于对向通过冷却区域60的钢带S喷射的雾沫的喷射量在钢带S的宽度方向上进行调整。冷却调整设备61a进行调整,使得对钢带S的宽度方向上的中心部积极地进行冷却并抑制边缘部的冷却。通过设置冷却调整设备61a,从而使钢带S的温度不会成为水自膜态沸腾变成过渡沸腾的骤冷温度以下,且不使钢带S的宽度方向上的温度分布变得剧烈。将冷却调整设备61a设于冷却区域前段部61的通板方向上游侧的理由在于,如所述那样,与将冷却调整设备61a设于冷却区域60的通板方向下游侧相比,在钢带S的温度控制幅度上具有富余。由于钢带S的目标终点温度处于水的骤冷温度附近,因此,为了使钢带S的温度不会成为骤冷温度以下,要求控制装置65具有较高的控制精度。因此,期望的是,在冷却区域前段部61的通板方向上游侧设置冷却调整设备61a,以大水量来积极地冷却钢带S。另外,在本实施方式的冷却区域60中,为了使骤冷点的位置变化的影响最小化而设有雾沫抽吸设备67,其对向钢带S喷射出的雾沫的至少一部分连同存在于冷却区域60内的空气一起进行抽吸。由此,能够对导致滴水的剩余的雾沫进行抽吸,从而能够防止剩余的雾沫作为滴水而挂在钢带S上。该雾沫抽吸设备67优选至少设于冷却区域60中的与钢带S的边缘部相对的部分的附近。通过将雾沫抽吸设备67设于该位置,能够更有效地对在边缘部会导致滴水的剩余的雾沫进行抽吸。另外,该雾沫抽吸设备67优选至少设于冷却区域60的通板方向下游侧。在钢带S的温度处于更低的状态的通板方向上的下游侧,因滴水而产生骤冷点位置的变化、沸腾状态自膜态沸腾状态向过渡沸腾状态转变的可能性较高。因而,通过将雾沫抽吸设备67重点地设于冷却区域60的通板方向下游侧,能够更有效地抑制滴水所引起的温度偏差。此外,对于设于冷却区域60的雾沫抽吸设备67的个数,并没有特别限定,只要根据冷却区域60的大小、应当自冷却区域60抽吸的雾沫的量等适当设定即可。利用雾沫抽吸设备67抽吸剩余雾沫的抽吸量受控制装置65控制。控制装置65通过对冷却调整设备61a和雾沫抽吸设备67这两者进行控制,能够更高效地对钢带S的冷却状态实施管理。在此,当被雾沫抽吸设备67抽吸的雾沫的量过少时,会产生残留的剩余雾沫所引起的滴水,当被抽吸的雾沫的量过多时,不能对钢带S充分地进行冷却。因此,优选的是,在控制装置65的控制下使雾沫抽吸设备67所抽吸的雾沫的量在能够防止产生滴水且能够对钢带S充分地进行冷却的、预定的范围内。能够通过公知的方法对利用雾沫抽吸设备67所抽吸的、排出空气和雾沫的量进行控制,例如,能够利用在雾沫抽吸设备67的雾沫吸入口附近设置的压力计(图6的附图标记69)的值来进行控制。即,只要利用设于雾沫抽吸口附近的压力计对雾沫抽吸口附近的钢带S的中心部的压力值进行测量并以使测得的压力值成为负压的方式对设于雾沫抽吸设备67的排气风机的风门开度进行调整即可。另外,为了利用冷却调整设备61a在通板方向上的有限的设备长度对宽度方向上的温度分布进行调整,需要以大水量来使用冷却调整设备61a。另一方面,在膜态沸腾区域中使用冷却调整设备61a时,为了避免骤冷温度Tq的上升,期望以小水量来使用冷却调整设备61a。这样,在仅设置冷却调整设备61a的情况下,用于实现宽度方向上的温度分布的调整的条件和用于实现膜态沸腾区域中的稳定冷却的条件成为相反的要件而不容易兼顾。不必要地延长冷却调整设备61a的设备长度的做法导致如下问题:设备变得复杂而设置成本变高这样的问题、在不需要调整宽度方向上的温度分布的对象材料的情况下反而使边缘部的温度变高这样的问题。因此,本申请发明人对用于实现抑制宽度方向上的温度分布和维持膜态沸腾条件的设备进行了研究,结果发现,只要使冷却调整设备61a的设备长度L(m)满足以下的式(1)即可。L≥(α×V×th)/((Tin-β)^m)×(Tin-γ))...(1)其中,将冷却区域60的入口处的钢带S的中心部的温度设为Tin(℃),将钢带S的速度设为V(m/s),将钢带的厚度设为th(m)。另外,α、β、γ、m是常数,是根据热镀锌设备而设定的。本申请发明人在各种操作条件下对与冷却调整设备61a的水量相对应的宽度方向上的温度分布调整能力和冷却稳定性进行了调查。结果发现,在能够维持膜态沸腾区域的条件之中,存在使宽度方向上的温度分布变为最平缓的水量。另外,发现了,该水量与冷却区域60的入口处的钢带S的温度、钢带S的速度、钢带S的厚度、以及冷却调整设备61a的设备长度L有关。因此,利用该关系导出了上述式(1),上述式(1)用于对为了获得宽度方向上的温度分布调整效果而所需的冷却调整设备61a的设备长度L进行限定。式(1)是如以下那样导出的。首先,如上述那样,当以大水量对钢带S进行强冷却时,骤冷温度Tq存在上升的倾向。该关系能够通过使用模拟实际设备的试验设备来评价钢带的冷却特性而得到。例如图4所示,骤冷温度Tq利用下述式(1-1)那样的冷却水量Q的一次函数来表示。在式(1-1)中,a、b是常数。Tq=aQ+b...(1-1)另外,如图4所示,在将冷却调整设备61a的中心部(宽度方向上的中心)处的钢带S的输入侧的温度Tin、钢带S的厚度th、钢带S的速度V以及冷却调整设备61a的设备长度L设为恒定时,如图4所示,对于冷却水量Q和钢带S的中心部的温度T,存在冷却水量Q越大则钢带S的中心部的温度T越低那样的关系。在此,利用冷却调整设备61a来改善钢带S的中心部与边缘部之间的温度差的改善效果ΔT同钢带S的中心部的输入侧的温度Tin与冷却调整设备61a内的任意的通板方向位置的温度T1之差存在正比关系。即,宽度方向上的温度分布的改善效果ΔT利用下述式(1-2)来表示。在式(1-2)中,α是常数。ΔT=α(Tin-T1)...(1-2)另一方面,为了使钢带S的温度不会冷却到小于骤冷温度Tq,能够利用冷却调整设备61a进行调整的、宽度方向上的温度分布存在上限。即,如图5所示,在自点PA起到表示成为骤冷温度Tq的位置的点PB之间,冷却水量Q越增加,宽度方向上的温度分布的改善效果ΔT越高。但是,当钢带S的温度T小于骤冷温度Tq时,钢带S成为局部地过冷却的状态,如图5所示,自点PB朝向点PC去,宽度方向上的温度分布的改善效果ΔT急剧地降低。因而,能够利用冷却调整设备61a进行调整的、宽度方向上的温度分布成为钢带S的温度为骤冷温度Tq以上的膜态沸腾温度范围(点PA~点PB的范围)。因此,当将骤冷温度Tq下的宽度方向上的温度分布的改善效果设为ΔTmax时,根据式(1-2),能够利用下述式(1-3)来表示。ΔTmax=α(Tin-Tq)...(1-3)并且,根据需要进行调整的温度分布偏差,决定冷却调整设备61a的设备长度L。在此,如下述式(1-4)那样,上述的能够调整的温度分布的改善效果的上限ΔTmax也能够利用钢带S的输入侧的中心部的温度Tin、钢带S的厚度th和钢带S的速度V、以及冷却调整设备61a的设备长度L来表示。ΔTmax=(α·2·h·L·(Tave-Tw))/(ρ·Cp·V·th)...(1-4)其中,Tave是平均板温,其利用例如钢带S的输入侧的中心部的温度Tin与骤冷温度Tq之间的平均值来表示。另外,Tw是冷却水温,ρ是钢材密度,Cp是钢材比热。当对该式(1-4)的关系、上述式(1-1)、式(1-3)、以及表示冷却水量Q(l/m2·min)与热传递系数h(W/m2·℃)之间的关系的式(1-5)进行整理时,能够得到上述式(1)。在式(1-5)中,k是常数。h=kQm...(1-5)此外,此时,上述式(1)的常数α、β、γ如下。α=20280×am/k...(1-7)β=33+b...(1-8)γ=45...(1-9)常数α、β、γ能够利用使用模拟实际设备的试验设备来对钢带的冷却特性进行评价而得到的结果来设定,能够设为,例如α=1700000、β=330、γ=45、m=0.6。此外,冷却区域60的入口处的钢带S的温度T、钢带S的速度V、钢带S的厚度th是由钢种、生产量、预订尺寸决定的值,因此,利用式(1)算出的L的值不会成为固定的值。因而,冷却调整设备61a的设备长度L是例如以代表性的操作条件为前提而决定的。另外,在冷却调整设备61a的设备长度L为恒定时,根据上述式(1)的关系,也可以是,以自下述式(2)算出的钢带S的上限速度Vmax以下的速度来生产钢带S。α’、β’、γ’、m是常数,是根据热镀锌设备而设定的。能够设为,例如α’=1700000、β’=330、γ’=45、m=0.6。钢带S的速度V因通板对象不同而变化,这些常数是考虑过渡状态而设定的。Vmax=(L×(Tin-β’)^m×(Tin-γ’))/(α’×th)...(2)这样,在不能改变冷却调整设备61a的设备长度L的情况下,通过根据钢种、生产量、预订尺寸来改变钢带S的上限速度Vmax并以上限速度Vmax以下的速度V来生产钢带S,也能够避免冷却不均所引起的品质不良并能够获得较高的生产率。能够使用例如向导系统将钢带S的速度V通知给操作者,进行更改。另外,对于钢带S的宽度方向上的温度分布,期望没有温度分布,但只要保持在预定的温度范围内,就不会对品质产生较大的影响。例如,预定的温度范围为30℃左右。此外,对于冷却区域60的输出侧的终点温度,如上述那样终点温度为300℃~400℃左右,当终点温度高于该范围时,钢带S的表面的镀层有可能卷绕在上辊70上。因而,进行控制,使得冷却区域60的输出侧的钢带S的宽度方向上的温度中的最高温度不高于300℃~400℃。[3-2.冷却调整设备的结构例]根据图6~图9来说明冷却调整设备61a的一结构。图6是表示本实施方式的冷却区域60的一结构例的说明图。图7是表示具有本实施方式的冷却调整设备61a的冷却区域前段部61的一结构例的说明图。图8是表示气水集管63的一结构例的说明图。图9是对冷却调整设备61a由一级气水集管63构成时的冷却调整设备61a的设备长度进行说明的说明图。本实施方式的冷却区域60是通过将图8所示那样的、沿着钢带S的宽度方向排列有多个气水喷射嘴64的气水集管63在长度方向上配置多个而构成的。在冷却区域前段部61和冷却区域后段部62中,气水集管63分别设有多级(例如大约30级)。图7所示那样的冷却区域60隔着钢带S的通板方向对称地配置。由此,自表面和背面冷却钢带S。来自气水喷射嘴64的雾沫喷射量(即,气水集管63的水量)能够通过图8所示的阀66a、66b的开闭来进行调节。能够利用控制装置65针对每级来调整阀66a、66b的开闭。冷却调整设备61a能够通过如下方式构成:例如利用罩将排列于各气水集管63的气水喷射嘴64中的、靠钢带S的宽度方向上的边缘部侧的气水喷射嘴64堵塞而使该边缘部侧的气水喷射嘴64不喷射雾沫。在图7的例子中,位于冷却区域前段部61的通板方向上游侧的第1级~第n级的气水集管63的边缘部被罩堵塞而形成了未喷射区域63b。因而,在钢带S通过冷却调整设备61a的期间,钢带S的与喷射区域63a相对应的中心部被积极地冷却,而钢带S的两边缘部的冷却受到抑制。此外,构成冷却调整设备61a的气水集管63的数量n根据利用上述式(1)设定的冷却调整设备61a的设备长度L或预先设定的冷却调整设备61a的恒定的设备长度L来进行设定。具体而言,冷却调整设备61a的设备长度L利用下述式(3)来表示。在此,在冷却调整设备61a由一级气水集管63构成时(即,n=1时),如图9所示,将自气水喷射嘴64向钢带S的表面以相对于垂直的方向呈上下45°的角度θ喷射雾沫的范围作为冷却调整设备61a的设备长度L。数学式1在此,p表示在通板方向上相邻的气水集管63的间距,d表示钢带S与气水集管63之间的距离。能够根据上述式(3)来决定构成冷却调整设备61a的气水集管63的数量n、设置位置。例如图7所示,也可以是,在通板方向上游侧利用罩将冷却调整设备61a的、与钢带S的两边缘部对应的气水喷射嘴64较多地堵塞而增大未喷射区域63b,并随着朝向下游侧去而自中心部侧减少被罩堵塞的气水喷射嘴64的数量而使未喷射区域63b变小。即,使利用气水集管63的气水喷射嘴64向钢带S的表面喷射雾沫的喷射区域63a自通板方向上游朝向下游去增大。例如,在钢带S的厚度为0.6mm、冷却区域60的入口的钢带温度为500℃时所需的冷却调整设备61a的设备长度L如以下的表1那样进行设定。钢带S的速度V越大,需要越长的冷却调整设备61a。表1钢带的速度(m/分钟)冷却调整设备的所需长度(m)1200.211500.261800.312500.433000.51由此,能在冷却开始时有效地抑制钢带S的边缘部的过冷却并在之后逐渐扩大钢带S的冷却范围而全面地进行冷却。尤其是,通过在冷却开始阶段集中地冷却钢带S的中心部并停止边缘部的冷却,如图2所示,在通过冷却区域60的过程中,能够使钢带S的边缘部的温度为中心部的温度以上。因而,在冷却区域60中的冷却结束时,钢带S的宽度方向上的温度分布不会变得剧烈,能够大致均匀地进行冷却。对于冷却区域60中的、比冷却调整设备61a靠通板方向下游侧的气水集管63、即冷却区域前段部61的第n+1级之后的气水集管63和冷却区域后段部62的所有的气水集管63而言,自所有的气水喷射嘴64喷射雾沫。此外,如图6所示,并不是必须从冷却区域60的通板方向最上游的第1根气水集管63起设置冷却调整设备61a,但为了享受本发明的效果,期望尽量在上游侧、可能的话自第1根起设置冷却调整设备61a。另外,如图6和图7所示,雾沫抽吸设备67以与钢带S的边缘部相对的方式设于冷却区域前段部61的下游侧和冷却区域后段部62的下游侧。根据利用压力计69测得的压力值,利用该雾沫抽吸设备67,以使中心部的压力值成为负压的方式对自气水集管63喷射出的雾沫抽吸预定量。由此,在冷却区域前段部61的内部存在能够在防止产生滴水的同时对钢带充分地进行冷却的雾沫,能够防止因滴水而产生冷却不均。图6和图7所示的冷却调整设备61a的结构是一个例子,本实施方式的冷却区域60的冷却调整设备61a的结构并不限定于该例子。也可以是,例如,在图6和图7中,起初就不设置被罩65堵塞的气水喷射嘴64,使边缘部的冷却停止。或者也可以是,不使边缘部的冷却完全停止,以比中心部的水量低的水量对边缘部进行喷雾。另外,图6和图7的冷却调整设备61a以自通板方向上游朝向下游去钢带S的中心部的冷却范围增大的方式构成,但利用冷却调整设备61a对中心部进行冷却的冷却范围也可以为恒定。以上,说明了本实施方式的热镀锌处理设备中的合金化炉的冷却区域60。本实施方式的合金化炉的冷却区域60在冷却区域前段部61的通板方向上游侧包括用于在钢带S的宽度方向上对向通过冷却区域60的钢带S喷射的雾沫的喷射量进行调整的冷却调整设备61a。在冷却调整设备61a中,积极地冷却钢带S的中心部,另一方面,停止边缘部的冷却或以低水量对边缘部进行喷射。另外,至少在冷却区域60中的与钢带S的边缘部相对的部分的附近设有一对雾沫抽吸设备67。此时,通过将冷却调整设备61a的设备长度L设定为能够在防止出现钢带S的宽度方向上的温度偏差变大而产生温度不均的情况的同时、以钢带S的板温不会变为骤冷温度Tq以下的方式进行冷却的长度,能够稳定地冷却钢带S。在本实施方式的合金化炉的冷却区域60中,能够利用喷雾冷却来稳定地冷却钢带,因此,能够使钢带高速地通过并对钢带进行处理,从而能够提高生产率。另外,通过将雾沫抽吸设备67设于上述位置,能够对可能在边缘部成为滴水的原因的剩余的雾沫更有效地进行抽吸。实施例作为实施例,在热镀锌处理设备的合金化炉的冷却区域中,使冷却调整设备的使用集管数变化而改变冷却调整设备的设备长度L,对冷却了热镀锌钢带时的、冷却后的钢带的宽度方向上的温度分布和产品的外观品位进行了调查。冷却区域的结构与图6相同,包括36级气水集管。其中,第1级~第9级的气水集管构成冷却调整设备。在本例子中,冷却调整设备的边缘部的水量为零,仅对中心部进行了雾沫喷射。将结果表示在表2中。此外,在表2中,对于冷却区域中间位置处的温度差而言,示出了在冷却区域前段部61与冷却区域后段部62之间的位置处的、自边缘部的温度减去中心部的温度而得到的值。冷却区域输出侧处的温度差也示出了自边缘部的温度减去中心部的温度而得到的值。边缘部的温度为距钢带的宽度方向端部的距离为100mm的位置处的表面温度,中心部的温度为钢带的宽度方向中心位置处的表面温度。表2◎:无(良好),△:略有(劣),×:有(劣)比较例0是不使用作为冷却调整设备的第1级~第9级的气水集管的情况、即对钢带的整个宽度方向进行喷雾冷却的情况。在比较例0中,也未使用雾沫抽吸设备。此时,与钢带的宽度方向上的中心部相比,边缘部的板温大大降低。钢带表面的镀锌附着于上辊,还产生了皱疤。比较例1是在比较例0的状态的基础上设置雾沫抽吸设备的情况。在该情况下,未产生皱疤,但看到钢带表面的镀锌附着于上辊。实施例1~实施例3是使用了作为冷却调整设备的第1级~第9级的气水集管的情况。实施例1~实施例3的冷却调整设备的长度以满足上述式(1)的方式被设定为比该长度的下限值长。在实施例1~实施例3的情况下,在利用冷却调整设备来积极地冷却钢带的宽度方向上的中心部之后,利用比冷却调整设备靠下游侧的气水集管来对钢带的整个宽度方向进行喷雾冷却,由此,与比较例0和比较例1相比,减轻了边缘部温度降低程度。既不会出现钢带表面的镀锌附着于上辊的情况,也不会产生皱疤。比较例2是使用了作为冷却调整设备的第1级~第9级的气水集管的情况,是虽然冷却调整设备的长度满足上述式(1)、但未设置雾沫抽吸设备的情况。在该情况下,与比较例0同样地,与钢带的宽度方向上的中心部相比,边缘部的板温大大降低,钢带表面的镀锌附着在上辊,且还产生了皱疤。比较例3~比较例5是减少作为冷却调整设备的第1级~第9级的气水集管的使用根数的情况。在比较例3~比较例5中,冷却调整设备的长度均不满足上述式(1),冷却调整设备的长度被设定为短于该长度的下限值。此外,对于比较例3,由于不满足上述式(1)的关系,因此,镀锌少量地附着在上辊的钢带表面上。能想到其原因在于,在冷却过程中,钢带的温度未低于骤冷温度,但由于冷却区域中间位置处的钢带的宽度方向上的中心部的温度为比边缘部的温度略高的程度,因此,在冷却区域输出侧的温度差变大。对于比较例4和比较例5,它们是如下那样的情况:减少了冷却调整设备的气水集管的使用根数,其结果,为了抑制中心部与边缘部之间的温度差消除量变少所带来的影响,增多向冷却调整设备的各气水集管供给的水量而想要减少冷却区域输出侧的中心部与边缘部之间的温度差。在比较例4中,冷却区域输出侧的中心部与边缘部之间的温度差变小,但由于在冷却过程中钢带的温度低于骤冷温度,因此产生了皱疤。在比较例5中,即使增多向冷却调整设备的各气水集管供给的水量,也不能充分地减少中心部与边缘部之间的温度差。其结果,冷却区域出口处的钢带的宽度方向上的中心部的温度变高。另一方面,钢带的宽度方向上的边缘部的温度降低并低于骤冷温度。其结果,在比较例5中,钢带表面的镀锌附着在上辊上,还产生了皱疤。比较例6是将冷却调整设备设于冷却区域的最终段侧的情况。在比较例6中,冷却调整设备的长度满足上述式(1),还设置了雾沫抽吸设备。即,如图10所示,在冷却区域中,以与钢带S的宽度方向上的边缘部相对的方式配置的一对雾沫抽吸设备67设于冷却区域60的通板方向中间位置和输出侧,用于对向钢带S喷射出的雾沫的至少一部分进行抽吸。另外,自冷却区域输出侧朝向通板方向上游侧去构成了冷却调整设备。冷却调整设备通过利用罩将钢带S的宽度方向上的边缘部侧的气水喷射嘴堵塞、使该边缘部侧的气水喷射嘴不喷射雾沫而构成。此时,随着自冷却区域输出侧朝向通板方向上游侧去,未喷射区域63c变小。在比较例6中,在冷却区域前段部61,钢带S的宽度方向全部被冷却,因此,在冷却区域的中间位置,钢带的宽度方向上的边缘部的温度低于中心部的温度。其结果,在冷却区域后段部62,即使抑制了边缘部的冷却,也不能避免边缘部的不稳定的过渡沸腾,钢带表面的镀锌附着于上辊,还产生了皱疤。由本实施例可知,在将冷却调整设备设于冷却设备的通板方向上游侧时,通过满足上述式(1),能够减轻钢带的宽度方向上的边缘部的温度降低程度而抑制产生温度不均,从而能够制造没有皱疤的良好的产品。另外,示出了还能够消除钢带表面的镀锌附着于上辊的情况。以上,参照附图详细地说明了本发明的优选实施方式,但本发明并不限定于该例子。很明显的,只要是具有本发明所属的
技术领域:
中的通常的知识的人,就能够在权利要求书中记载的技术思想的范畴内想到各种变更例或修改例,所述变更例或修改例当然也被认为属于本发明的保护范围。例如,在上述实施方式中,作为用于冷却钢带的冷却设备而使用了喷射雾沫的气水喷嘴(双组分喷嘴),但本发明并不限定于该例子。例如,也可以利用喷射水的单组分喷嘴来构成冷却设备。此外,从水质管理的观点考虑,与水质管理较困难的单组分喷嘴相比,优选使用双组分喷嘴。附图标记说明5、熔融锌;10、锌锅;20、沉没辊;30、气体喷嘴;40、加热区域;50、保热区域;60、冷却区域;61、冷却区域前段部;62、冷却区域后段部;63、气水集管;63a、喷射区域;63b、未喷射区域;64、气水喷射嘴;65、控制装置;70、上辊;S、钢带。当前第1页1 2 3