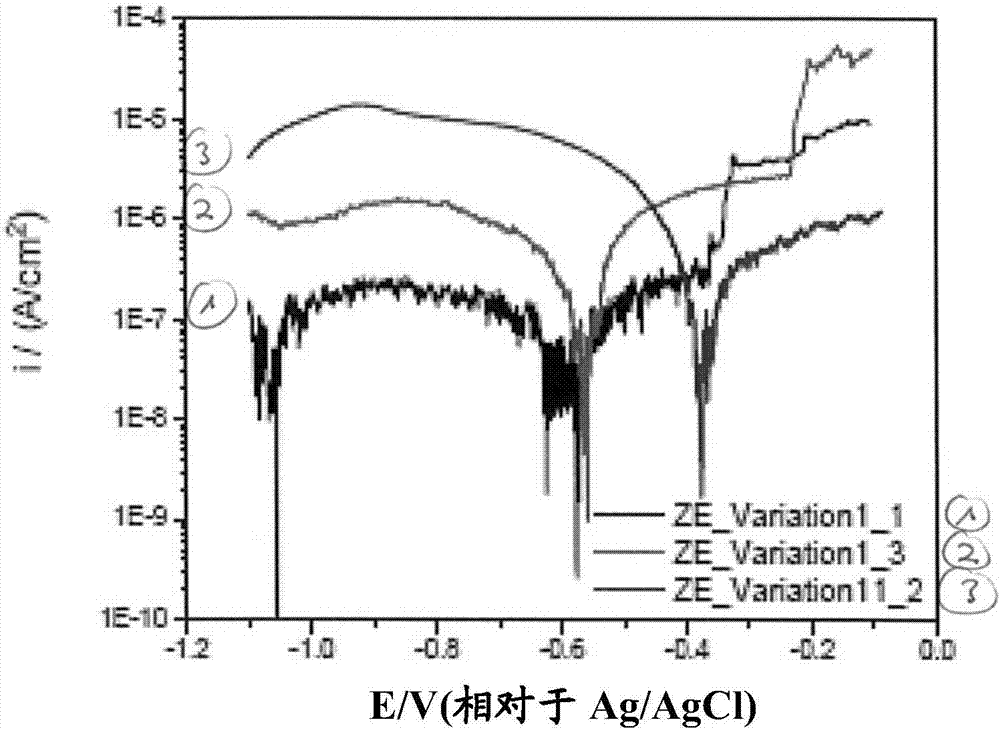
本发明涉及一种基本上无镍磷化金属表面的方法、相应的磷化组合物以及相应的磷酸盐涂覆的金属表面。现有技术已知金属表面上的磷酸盐涂层。该类涂层用于防止金属表面腐蚀,此外还用作后续涂膜的粘合增进剂。该类磷酸盐涂层特别用于汽车工业以及一般工业领域中。后续涂膜以及粉末涂料和湿漆特别为阴极沉积的电涂材料(cec)。由于cec的沉积需要在金属表面和处理浴之间存在电流,因此重要的是在磷酸盐涂层中设定确定的电导率以确保有效且均匀的沉积。因此,磷酸盐涂层通常使用含镍的磷化溶液施加。在该过程中沉积的镍(呈元素形式或者作为合金成分例如zn/ni)在随后的电涂过程中为涂层提供了合适的电导率。然而,由于其高毒性和环境危害,镍离子不再是处理溶液的理想成分,因此应尽可能避免或至少减少其用量。原则上,使用无镍或低镍磷化溶液的确是已知的。然而,其限于特定的基材,例如钢。此外,由于非理想的基材表面,所述的无镍或低镍体系在常用的cec沉积条件下可能导致差的腐蚀值和涂层粘合性值。因此,本发明的目的是提供一种方法,借此可对金属表面进行基本上无镍的磷化处理,其中这些表面在其电化学性质方面与用含镍磷化溶液处理的金属表面相当或基本上相当;更特别地,借此避免了上文所述的现有技术缺点。该目的通过权利要求1的方法、权利要求21的磷化组合物和权利要求23的磷酸盐涂覆的金属表面实现。在本发明的基本上无镍磷化金属表面的方法中,在任选清洁和/或活化后,首先用含有锌离子、锰离子和磷酸根离子的酸性含水磷化组合物处理金属表面,并任选冲洗和/或干燥,然后用包含至少一种选自钼、铜、银、金、钯、锡、铂、锑、钛、锆和铪的离子的金属离子和/或至少一种选自聚胺、聚乙烯胺、聚苯胺、聚亚胺、聚乙烯亚胺、聚噻吩和聚吡咯及其混合物和共聚物的聚合物类别的含水后冲洗组合物处理,其中所述磷化组合物和后冲洗组合物基本不含镍。定义:本发明的方法可用于处理未涂覆的金属表面或已涂覆有转化涂层的金属表面。因此,下文提及的“金属表面”总是视为也包括已涂覆有转化涂层的金属表面。就本发明而言,“含水组合物”为包含至少一部分,优选主要的水作为其溶剂的组合物。除了溶解的成分之外,其还可包含分散的—即乳化和/或悬浮的—成分。就本发明而言,“磷酸根离子”还指代磷酸氢根、磷酸二氢根和磷酸。此外,意欲包括焦磷酸和多磷酸及其部分和完全脱质子化的全部形式。就本发明而言,“金属离子”可选地为金属阳离子,络合金属阳离子或络合金属阴离子。就本发明而言,当组合物含有小于0.3g/l的镍离子时,认为其是“基本上无镍的”。金属表面优选包括钢、热浸镀锌体系、电解镀锌体系、铝或其合金,例如zn/fe或zn/mg。在热浸镀锌体系和电解镀锌体系的情况下,其在每种情况下更特别地为钢上的这种体系。金属表面更特别地为至少部分镀锌的。本发明的方法尤其适于多金属涂覆。如果要涂覆金属表面并且不是新鲜的热浸镀锌体系,则有利的是在用所述磷化组合物处理之前,首先在含水清洁组合物中清洁金属表面,更特别地脱脂。为此,尤其可使用酸性、中性、碱性或强碱性的清洁组合物,然而也可任选额外使用酸性或中性酸洗组合物。此处,已证明碱性或强碱性清洁组合物是特别有利的。除至少一种表面活性剂之外,所述含水清洁组合物还可任选包含清洁剂助洗剂和/或其他添加剂如络合剂。还可使用活化清洁剂。在清洁/酸洗之后,有利的是用水冲洗金属表面至少一次,在这种情况下,还可任选在水中加入溶于水中的添加剂,例如亚硝酸盐或表面活性剂。在用磷化组合物处理金属表面之前,有利的是用活化组合物处理金属表面。活化组合物的目的是在金属表面上沉积多种超细磷酸盐颗粒作为晶种。这些晶体有助于在随后的方法步骤中与磷化组合物接触(优选期间不进行冲洗)时形成磷酸盐层,更特别地具有极高数量的致密排列的细磷酸盐晶体的结晶磷酸盐层,或基本上不透的磷酸盐层。设想的活化组合物特别包括基于磷酸钛或磷酸锌的酸性或碱性组合物。然而,还可有利地向清洁组合物中加入活化剂,尤其是磷酸钛或磷酸锌,换言之,清洁和活化在一个步骤中实施。所述酸性含水磷化组合物包含锌离子、锰离子和磷酸根离子。此处,所述磷化组合物可由浓缩物通过用合适的溶剂,优选用水稀释1-100倍,优选5-50倍,并且需要的话,添加ph调节物质而获得。所述磷化组合物优选以下列优选和更优选的浓度范围包含下列组分:然而,就锰离子而言,已证明0.3-2.5g/l的浓度是有利的;且就游离氟离子而言,10-250mg/l的浓度是有利的。络合氟离子优选包含四氟硼酸根(bf4–)和/或六氟硅酸根(sif62–)。特别是在处理铝和/或镀锌材料时,在磷化组合物中存在络合氟离子以及简单的氟化物,例如氟化钠是有利的。磷化体系中的al3+是一种浴毒物,且可通过与氟离子络合(例如以冰晶石的形式)而从体系中移除。将络合氟离子作为“氟离子缓冲剂”加入到浴中,因为否则的话氟离子含量将快速地降低且涂覆不再发生。然后,氟离子辅助形成磷酸盐层,因此间接导致涂层粘合性以及腐蚀控制改善。此外,在镀锌材料上,络合氟离子有助于防止缺陷如斑点。特别是在铝处理中,也有利的是磷化组合物包含fe(iii)。在这种情况下,优选fe(iii)含量为0.001-0.2g/l,更优选为0.005-0.1g/l,非常优选为0.01-0.05g/l。所述磷化组合物进一步优选以下列优选和更优选的浓度范围包含至少一种选自下列化合物的促进剂:硝基胍0.2-3.0g/l0.2-1.55g/lh2o210-100mg/l15-50mg/l硝基胍/h2o20.2-2.0g/l/10-50mg/l0.2-1.5g/l/15-30mg/l亚硝酸盐30-300mg/l90-150mg/l羟胺0.1-5g/l0.4-3g/l然而,就硝基胍而言,已证明0.1-3.0g/l的浓度是有利的;就h2o2而言,5-200mg/l的浓度是有利的。非常优选地,所述至少一种促进剂为h2o2。然而,优选所述磷化组合物包含小于1g/l,更优选小于0.5g/l,非常优选小于0.1g/l,尤其优选小于0.01g/l的硝酸根。其原因在于,特别是在镀锌表面的情况下,磷化组合物中的硝酸根导致成层反应额外加速,从而导致较低的涂层重量,但特别地减少了引入晶体中的锰。然而,如果磷酸盐涂层的锰含量太低,则其耐碱性受损。耐碱性在随后的阴极电涂沉积中又起到关键作用。在该过程中,在基材表面上发生水的电离:形成氢氧根离子。因此,基材界面处的ph升高。实际上只有这样,电涂材料才能凝聚并沉积。然而,升高的ph也可能损害结晶磷酸盐层。所述磷化组合物优选具有30-55℃的温度。此外,所述磷化组合物的特征可在于下列优选和更优选的参数范围:fa0.3-2.00.7-1.6fa(dil.)0.5-81-6taf12-2822-26ta12-4518-35a值0.01-0.20.03-0.15温度,℃30-50℃35-45℃然而,就fa参数而言,已证明0.2-2.5的值是有利的;且就温度的值而言,30-55℃的值是有利的。在该列表中,“fa”表示游离酸,“fa(dil.)”表示游离酸(稀释),“taf”表示fischer总酸,“ta”表示总酸,“a值”表示酸值。这些参数如下确定:游离酸(fa):为了测定游离酸,将10ml磷化组合物移液至合适的容器如300ml锥形瓶中。如果磷化组合物含有络合氟离子,则再在样品中加入2-3g氯化钾。随后,使用ph计和电极用0.1mnaoh滴定至ph值为3.6。该滴定中消耗的0.1mnaoh的量(以ml/10ml磷化组合物计)给出了游离酸(fa)值的点数。游离酸(稀释)(fa(dil.)):为了测定游离酸(稀释),将10ml磷化组合物移液至合适的容器如300ml锥形瓶中。然后加入150ml去离子水。使用ph计和电极用0.1mnaoh滴定至ph值为4.7。该滴定中消耗的0.1mnaoh的量(以ml/10ml稀磷化组合物计)给出了游离酸(稀释)(fa(dil.))值的点数。由相对于游离酸(fa)的差可确定络合氟离子的量。如果将该差值乘以0.36的系数,则获得以sif62–计(g/l)的络合氟离子的量。fischer总酸(taf):在测定游离酸(稀释)后,在加入草酸钾溶液后,用ph计和电极使用0.1mnaoh将稀磷化组合物滴定至ph值为8.9。在该程序中,以ml/10ml稀磷化组合物计的0.1mnaoh的消耗量给出了fischer总酸(taf)的点数。如果将该数值乘以0.71,结果是以p2o5计的磷酸根离子总量(参见w.rausch:“diephosphatierungvonmetallen”,eugeng.leuze-verlag2005,第3版,第332页及随后各页)。总酸(ta):总酸(ta)是存在的二价阳离子以及游离和结合的磷酸(后者为磷酸盐)的总和。其通过使用ph计和电极由0.1mnaoh的消耗量测定。为此,将10ml磷化组合物移液至合适的容器如300ml锥形瓶中,并用25ml去离子水稀释。此后用0.1mnaoh滴定至ph为9。在该程序中以ml/10ml稀磷化组合物计的消耗量对应于总酸(ta)的点数。酸值(a值):酸值(a值)表示比值fa:taf,并且通过将游离酸(fa)的值除以fischer总酸(taf)的值得到。由于将酸值设定为0.03-0.065,更特别地为0.04-0.06,涂层粘合性的进一步改善(尤其是在热浸镀锌表面上)是令人惊讶的。令人惊讶地发现,特别是在使用钢或热浸镀锌体系作为金属表面的情况下,低于45℃,优选35-45℃的磷化组合物温度导致腐蚀和涂层粘合值进一步改善。所述磷化组合物基本不含镍。其包含优选小于0.1g/l,更优选小于0.01g/l的镍离子。用所述磷化组合物处理金属表面优选达30-480秒,更优选60-300秒,非常优选90-240秒,优选通过浸涂或喷涂处理。取决于处理的表面,用磷化组合物处理金属表面在金属表面上产生下列优选和特别优选的磷酸锌涂层重量(通过x射线荧光分析(xrf)测定):在用磷化组合物处理之后,优选冲洗金属表面,更优选用完全去离子水或自来水冲洗金属表面。在用后冲洗组合物处理之前,任选将金属表面干燥。根据本发明的方法,进一步用含水后冲洗组合物处理已用磷化组合物处理(即已涂覆磷酸)的金属表面。所述后冲洗组合物可由浓缩物通过用合适的溶剂,优选用水稀释1-1000倍,优选5-500倍,并且需要的话,加入ph调节物质而获得。根据一个实施方案,所述后冲洗组合物以下列优选、更优选和尤其优选的浓度范围包含至少一种选自下列金属的离子的金属离子(全部以所述金属计):mo1-1000mg/l10-500mg/l20-225mg/lcu1-1000mg/l100-500mg/l150-225mg/lag1-500mg/l5-300mg/l20-150mg/lau1-500mg/l10-300mg/l20-200mg/lpd1-200mg/l5-100mg/l15-60mg/lsn1-500mg/l2-200mg/l3-100mg/lsb1-500mg/l2-200mg/l3-100mg/lti20-500mg/l50-300mg/l50-150mg/lzr20-500mg/l50-300mg/l50-150mg/lhf20-500mg/l50-300mg/l50-150mg/l存在于所述后冲洗溶液中的金属离子以含有所述金属(例如钼或锡)阳离子的盐的形式,优选以至少两种氧化态—更特别地以氧化物氢氧化物、氢氧化物、尖晶石或缺陷尖晶石的形式—或者以元素形式沉积在处理表面(例如铜、银、金或钯)上。根据一个优选的实施方案,所述金属离子为钼离子。它们优选以钼酸盐,更优选七钼酸铵,非常优选七钼酸铵×7h2o的形式加入所述后冲洗组合物中。钼离子也可以以钼酸钠的形式加入。可选地,钼离子也可以以例如至少一种含有钼阳离子的盐,例如氯化钼的形式加入所述后冲洗组合物中,然后借助合适的氧化剂,例如借助稍上文稍早描述的促进剂将其氧化成钼酸盐。在这种情况下,所述后冲洗组合物本身包含相应的氧化剂。进一步优选地,所述后冲洗组合物包含与铜离子、锡离子或锆离子组合的钼离子。特别优选地,其包含与锆离子以及任选的聚合物或共聚物组合的钼离子,所述聚合物或共聚物更特别地选自聚胺、聚乙烯胺、聚苯胺、聚亚胺、聚乙烯亚胺、聚噻吩和聚吡咯及其混合物和共聚物以及聚丙烯酸的聚合物类别,其中钼离子和锆离子的量在每种情况下为10-500mg/l(以金属计)。此处,钼离子的量优选为20-225mg/l,更优选为50-225mg/l,非常优选为100-225mg/l,锆离子的量优选为50-300mg/l,更优选为50-150mg/l。根据另一优选实施方案,所述金属离子为铜离子。在这种情况下,所述后冲洗溶液优选含有浓度为100-500mg/l,更优选150-225mg/l的这些离子。根据另一实施方案,本发明的后冲洗组合物包含至少一种选自聚胺、聚乙烯胺、聚苯胺、聚亚胺、聚乙烯亚胺、聚噻吩和聚吡咯及其混合物和共聚物的聚合物类别的聚合物。所述至少一种聚合物优选以0.1-5g/l,更优选0.1-3g/l,更优选0.3-2g/l,非常优选0.5-1.5g/l的浓度存在(以纯聚合物计)。所用的聚合物优选为阳离子聚合物,特别为聚胺、聚乙烯胺、聚亚胺和/或聚乙烯亚胺。特别优选使用聚胺和/或聚亚胺,非常优选聚胺。根据第三实施方案,本发明的后冲洗组合物在每种情况下以下列优选、更优选和尤其优选的浓度范围(聚合物以纯聚合物计,金属离子以所述金属计)包含至少一种选自钼、铜、银、金、钯、锡、锑、钛、锆和铪的离子的金属离子和至少一种选自聚胺、聚乙烯胺、聚苯胺、聚亚胺、聚乙烯亚胺、聚噻吩和聚吡咯及其混合物和共聚物的聚合物类别的聚合物。mo1-1000mg/l10-500mg/l20-225mg/lcu1-1000mg/l100-500mg/l150-225mg/lag1-500mg/l5-300mg/l20-150mg/lau1-500mg/l10-300mg/l20-200mg/lpd1-200mg/l5-100mg/l15-60mg/lsn1-500mg/l2-200mg/l3-100mg/lsb1-500mg/l2-200mg/l3-100mg/lti20-500mg/l50-300mg/l50-150mg/lzr20-500mg/l50-300mg/l50-150mg/lhf20-500mg/l50-300mg/l50-150mg/l聚合物0.1-3g/l0.3g/l-2g/l0.5-1.5g/l根据一个优选的实施方案,所述至少一种聚合物为阳离子聚合物,更特别为聚胺和/或聚亚胺,并且所述金属离子为铜离子、钼离子和/或锆离子,在每种情况下以下列优选、更优选的和尤其优选的浓度范围包含(聚合物以纯聚合物计,金属离子以所述金属计)。mo1-1000mg/l10-500mg/l20-225mg/lcu1-1000mg/l100-500mg/l150-225mg/lzr20-500mg/l50-300mg/l50-150mg/l阳离子聚合物0.1-3g/l0.3-2g/l0.5-1.5g/l所述后冲洗组合物—尤其是如果所述金属表面为铝或铝合金—优选额外包含20-500mg/l,更优选50-300mg/l,非常优选50-150mg/l呈络合形式的ti、zr和/或hf(以金属计)。所述络合物优选为氟络合物。此外,所述后冲洗组合物优选包含10-500mg/l,更优选15-100mg/l,非常优选15-50mg/l的游离氟离子。特别优选地,所述后冲洗组合物包含呈络合形式的zr(以金属计)和至少一种选自钼、铜、银、金、钯、锡和锑,优选钼的离子的金属离子。包含呈络合形式的ti、zr和/或hf的后冲洗组合物优选进一步包含至少一种有机硅烷和/或其至少一种水解产物(换言之,有机硅烷醇)和/或其至少一种缩合产物(换言之,有机硅氧烷/聚有机硅氧烷),其浓度为5-200mg/l,更优选为10-100mg/l,非常优选为20-80mg/l(以si计)。所述至少一种有机硅烷优选含有至少一个氨基。更优选地,所述有机硅烷为可水解成氨基丙基硅烷醇和/或2-氨基乙基-3-氨基丙基硅烷醇的有机硅烷,和/或其为双(三甲氧基甲硅烷基丙基)胺。所述后冲洗组合物的ph值优选处于酸性范围内,更优选为3-5,非常优选为3.5-5。令人惊讶地发现,降低ph值能促进钼离子在磷酸盐涂覆的金属表面上的沉积。因此,在后冲洗溶液包含钼离子的情况下,ph值优选为3.5-4.5,更优选为3.5-4.0。所述后冲洗组合物基本不含镍。其含有优选小于0.1g/l,更优选小于0.01g/l的镍离子。所述后冲洗组合物优选具有15-40℃的温度。用所述后冲洗组合物处理金属表面优选达10-180秒,更优选20-150秒,尤其优选30-120秒,优选通过浸渍或喷洒。本发明进一步涉及一种可通过本发明的方法获得的磷酸盐涂覆的金属表面。本发明的方法允许通过在磷酸盐层中产生确定的孔而以特定的方式调节磷酸盐涂覆的金属表面的电导率。在这种情况下,电导率可以可选地大于、等于或小于提供有含镍磷酸盐涂层的相应金属表面的电导率。用本发明方法调节的磷酸盐涂覆的金属表面的电导率可通过改变后冲洗溶液中给定金属离子和/或聚合物的浓度而影响。然后,可在涂覆有磷酸盐的金属表面—也用后冲洗组合物处理—上沉积阴极电涂材料,且施加涂层体系。在这种情况下,在用所述后冲洗组合物处理后,任选首先对金属表面进行冲洗,优选用去离子水冲洗,且任选干燥。在下文中,意图是通过不应理解为施加任何限制的实施例和对比实施例来阐述本发明。对比实施例1在53℃下使用含有1.3g/lzn、1g/lmn、13g/lpo43–(以p2o5计)、3g/lno3-以及1g/l镍的磷化溶液涂覆由电解镀锌钢(ze)制成的测试板。不进行后冲洗。然后相对于施加在银/氯化银(ag/agcl)电极上的电压e(以v计)测量电流密度i(以a/cm2计)(参见图1:ze_variation11_2:曲线3)。测量通过线性扫描伏安法进行(电位范围:-1.1至-0.2vref;扫描速率:1mv/s)。在所有本发明实施例和对比实施例中,测得的电流密度i取决于转化涂层的电导率。规则如下:测得的电流密度i越高,转化涂层的电导率也越高。在转化涂层的情况下,不能像在液体介质中那样直接测量电导率(μs/cm)。因此,目前对含镍转化涂层测得的电流密度i总是用作与给定转化涂层的电导率相关的描述的参考点。图1-4中的标记“1e”总是表示“10”。因此,例如,“1e-4”意指“10-4”。对比实施例2在53℃下使用含有1.3g/lzn、1g/lmn、16g/lpo43–(以p2o5计)和2g/lno3–的无镍磷化溶液涂覆如对比实施例1的测试板,不进行后冲洗,然后如对比实施例1那样相对于电压e测量电流密度i(参见图1,ze_variation1_1:曲线1;ze_variation1_3:曲线2)。从图1可以看出,无镍体系(对比实施例2)相对于含镍体系(对比实施例1)的静止电位向左移动。电导率也较低:曲线1和曲线2的“臂”在每种情况下位于曲线3下方,即朝向较低的电流密度。对比实施例3使用如对比实施例2的无镍磷化溶液涂覆如对比实施例1的测试板。随后用含有约120mg/lzrf62–(以zr计)且具有约4的ph的后冲洗溶液处理如此涂覆的测试板。如对比实施例1那样相对于电压e测量电流密度i(参见图2:ze_variation6_1:曲线1;ze_variation6_2:曲线2)。与对比实施例1(图2:ze_variation11_2:曲线3)进行比较。从图2可以看出,当使用含zrf62–的后冲洗溶液(对比实施例3)时,无镍体系的静止电位相对于含镍体系(对比实施例1)向左偏移。所述无镍体系的电导率也较低(参见关于对比实施例2的观察结果)。实施例1使用如对比实施例2的无镍磷化溶液涂覆如对比实施例1的测试板。随后用含有约220mg/l铜离子且具有约4的ph的后冲洗溶液处理由此涂覆的测试板。如对比实施例1那样相对于电压e测量电流密度i(参见图3:ze_variation2_1:曲线1;ze_variation2_2:曲线2)。与对比实施例1(图3:ze_variation11_2:曲线3)进行比较。从图3可以看出,当使用含铜离子的后冲洗溶液(实施例1)时,无镍体系的静止电位对应于含镍体系(对比实施例1)的静止电位。这种无镍体系的电导率相对于含镍体系的电导率略有增加。实施例2使用如对比实施例2的无镍磷化溶液涂覆如对比实施例1的测试板。随后用含有约1g/l(基于纯聚合物计算)导电聚胺(9030,生产商basf)且具有约4的ph的后冲洗溶液处理由此涂覆的测试板。如对比实施例1那样相对于电压e测量电流密度i(参见图4,ze_variation3_1:曲线1;ze_variation3_2:曲线2)。与对比实施例1(图4:ze_variation11_2:曲线3)进行比较。从图4可以看出,当使用含导电聚合物的后冲洗溶液(实施例2)时,无镍体系的静止电位对应于含镍体系(对比实施例1)的静止电位。此时,无镍体系的电导率相对于其含镍对应体系的电导率稍微降低。对比实施例4使用如对比实施例1的含有1g/l镍的磷化溶液涂覆由热浸镀锌钢(ea)制成的测试板。随后用含有约120mg/lzrf62–(以zr计)且具有约4的ph的后冲洗溶液处理如此涂覆的测试板,然后相对于施加在银/氯化银(ag/agcl)电极上的电压e(以v计)测量电流密度i(以a/cm2计)(参见图5:ea173:曲线1)。测量使用线性扫描伏安法进行。对比实施例5在35℃下使用包含1.2g/lzn、1g/lmn和16g/lpo43–(以p2o5计)的无镍且无硝酸根的磷化溶液涂覆如对比实施例4的测试板,而不进行后冲洗,然后如对比实施例3那样相对于电压e测定电流密度i(参见图5:ea167:曲线3;ea1672:曲线2)。从图5可以看出,无镍体系(对比实施例5)的静止电位相对于含镍体系(对比实施例4)的静止电位右移。所述含镍体系情况下的电导率要低得多,这可归因于含zrf62–的后冲洗溶液的钝化作用。实施例3使用如对比实施例2的无镍磷化溶液涂覆如对比实施例4的测试板。随后用含有约120mg/lzrf62–(以zr计)和220mg/l的钼离子且具有约4的ph的后冲洗溶液处理如此涂覆的测试板。如对比实施例1那样相对于电压e测量电流密度i(参见图6,ea178:曲线3;ea1782:曲线2)。与对比实施例3(图6:ea173:曲线1)进行比较。从图6可以看出,当使用含zrf62–和钼离子的后冲洗溶液(实施例3)时,无镍体系的静止电位对应于含镍体系(对比实施例4)的静止电位。通过在含zrf62–的后冲洗溶液(对比实施例4)中添加钼离子(实施例3),可显著提高基材表面的电导率。在磷化后,用阴极电涂材料以及标准汽车涂料体系(填料、底漆、清漆)涂覆对比实施例1-3(ce1-ce3)以及实施例1和2(e1和e2)的测试板,然后进行dineniso2409划格法测试。在每种情况下测试3块金属板,在暴露于冷凝水240小时(dineniso6270-2ch)之前和之后进行。相应的结果参见表1。在这些结果中,0的划格法结果是最好的,5的结果是最差的结果。此处,0和1的结果具有相当的质量。表1表1显示了ce2,尤其是ce3在每种情况下在暴露后的不良结果,而e1(铜离子)和e2(导电聚胺)提供了良好的结果,其至少与ce1(含镍磷化)相当。对比实施例6在53℃下且在亚硝酸盐(约90mg/l亚硝酸盐)促进下,使用含有1.1g/lzn、1g/lmn、13.5g/lpo43–(以p2o5计)、3g/lno3–以及1g/l镍的磷化溶液涂覆由热浸镀锌钢制成的测试板。随后用含有约120mg/lzrf62–(以zr计)且具有约4的ph值的后冲洗溶液处理如此涂覆的测试板。对比实施例7在35℃下且在亚硝酸盐(约90mg/l亚硝酸盐)促进下,使用含有1.1g/lzn、1g/lmn、17g/lpo43–(以p2o5计)和0.5gno3–的无镍磷化溶液涂覆如对比实施例6的测试板。随后用含有约120mg/lzrf62–(以zr计)和220mg/l钼离子且具有约4的ph值的后冲洗溶液处理如此涂覆的测试板。实施例4在35℃下且在亚硝酸盐(约90mg/l亚硝酸盐)促进下,使用含有1.1g/lzn、1g/lmn和17g/lpo43–(以p2o5计)的无镍且无硝酸根的磷化溶液涂覆如对比实施例6的测试板。随后用含有约120mg/lzrf62–(以zr计)和220mg/l钼离子且具有约4的ph值的后冲洗溶液处理如此涂覆的测试板。对比实施例8在35℃下且在过氧化物(约80mg/lh2o2)促进下,使用含有1.1g/lzn、1g/lmn、17g/lpo43–(以p2o5计)和0.5g/lno3–的无镍磷化溶液涂覆如对比实施例6的测试板。随后用含有约120mg/lzrf62–(以zr计)和220mg/l钼离子且具有约4的ph值的后冲洗溶液处理如此涂覆的测试板。实施例5在35℃下且在过氧化物(约80mg/lh2o2)促进下,使用含有1.1g/lzn、1g/lmn和17g/lpo43–(以p2o5计)的无镍且无硝酸根的磷化溶液涂覆如对比实施例6的测试板。随后用含有约120mg/lzrf62–(以zr计)和220mg/l钼离子且具有约4的ph值的后冲洗溶液处理如此涂覆的测试板。在磷化后,用阴极电涂材料以及标准汽车涂料体系(填料、底漆、清漆)涂覆对比实施例6-8(ce6-ce8)以及实施例4和5(e4和e5)的测试板,然后进行dineniso2409划格法测试。在每种情况下测试3块金属板,在暴露于冷凝水240小时(dineniso6270-2ch)之前和之后进行。相应的结果参见表2。表2表2显示了与ce6相比,ce7(亚硝酸盐促进)以及ce8(过氧化物促进)的不良结果,而e4(亚硝酸盐促进)和e5(过氧化物促进)给出了良好的结果—与ce6的那些相当(含镍磷化)。对比实施例9在53℃下且在亚硝酸盐(约90mg/l亚硝酸盐)促进下,使用含有1.1g/lzn、1g/lmn、13.5g/lpo43–(以p2o5计)、3g/lno3–以及1g/l镍的磷化溶液涂覆由热浸镀锌钢(ea)制成的测试板。随后用含有约120mg/lzrf62–(以zr计)具有约4的ph值的后冲洗溶液处理如此涂覆的测试板。实施例6在35℃下且在过氧化物(约80mg/lh2o2)促进下,使用含有1.1g/lzn、1g/lmn和17g/lpo43–(以p2o5计)的无镍且无硝酸根的磷化溶液涂覆如对比实施例9的测试板。随后用含有约120mg/lzrf62–(以zr计)和220mg/l钼离子且具有约4的ph值的后冲洗溶液处理如此涂覆的测试板。对比实施例10在53℃下且在亚硝酸盐(约90mg/l亚硝酸盐)促进下,使用含有1.1g/lzn、1g/lmn、13.5g/lpo43–(以p2o5计)、3g/lno3–以及1g/l镍的磷化溶液涂覆由光亮钢制成的测试板。随后用含有约120mg/lzrf62–(以zr计)且具有约4的ph值的后冲洗溶液处理如此涂覆的测试板。实施例7在35℃下且在过氧化物(约80mg/lh2o2)促进下,使用含有1.1g/lzn、1g/lmn和17g/lpo43–(以p2o5计)的无镍且无硝酸根的磷化溶液涂覆如对比实施例10的测试板。随后用含有约120mg/lzrf62–(以zr计)和220mg/l钼离子且具有约4的ph值的后冲洗溶液处理如此涂覆的测试板。对比实施例11在53℃下且在亚硝酸盐(约90mg/l亚硝酸盐)促进下,使用含有1.1g/lzn、1g/lmn、13.5g/lpo43–(以p2o5计)、3g/lno3–以及1g/l镍的磷化溶液涂覆由电解镀锌钢(ze)制成的测试板。随后用含有约120mg/lzrf62–(以zr计)且具有约4的ph值的后冲洗溶液处理如此涂覆的测试板。实施例8在35℃下且在过氧化物(约80mg/lh2o2)促进下,使用含有1.1g/lzn、1g/lmn和17g/lpo43–(以p2o5计)的无镍且无硝酸根的磷化溶液涂覆如对比实施例11的测试板。随后用含有约120mg/lzrf62–(以zr计)和220mg/l钼离子且具有约4的ph值的后冲洗溶液处理如此涂覆的测试板。在磷化后,用阴极电涂材料以及标准汽车涂料体系(填料、底漆、清漆)涂覆对比实施例9-11(ce9-ce11)以及实施例6-8(e6-e8)的测试板,然后如上文稍早对ce6-ce8、e4和e5所述那样进行划格法测试。结果汇总在表3中。此外,对所述测试板进行vda测试(vda621-415),其测定了涂层破坏(u,以mm计)以及石击后的涂层剥离(dineniso20567-1,方法c)。此处,石击后0的结果是最好的,5的结果是最差的。至多1.5的数值被视为是良好的。结果同样汇总在表3中。表3表3显示了可用本发明的无镍方法在热浸镀锌钢(e6)和光亮钢(e7)以及电解镀锌钢(e8)上可以获得的良好结果。这些结果在每种情况下与含镍方法相当(参见e6和ce9,e7和ce10,以及e8和ce11)。对比实施例12在53℃下且在亚硝酸盐(约90mg/l亚硝酸盐)促进下,使用含有1.1g/lzn、1g/lmn、13.5g/lpo43–(以p2o5计)、3g/lno3–以及1g/l镍的磷化溶液涂覆由热浸镀锌钢(ea)制成的测试板。随后用含有约120mg/lzrf62–(以zr计)且具有约4的ph值的后冲洗溶液处理如此涂覆的测试板。实施例9在35℃下且在过氧化物(约80mg/lh2o2)促进下,使用含有1.1g/lzn、1g/lmn和17g/lpo43–(以p2o5计)的无镍且无硝酸根的磷化溶液涂覆如对比实施例12的测试板。随后用含有约120mg/lzrf62–(以zr计)和220mg/l钼离子且具有约4的ph值的后冲洗溶液处理如此涂覆的测试板。实施例10在45℃下且在过氧化物(约50mg/lh2o2)促进下,使用含有1.2g/lzn、1g/lmn和13g/lpo43–(以p2o5计)的无镍且无硝酸根的磷化溶液涂覆如对比实施例12的测试板。随后用含有约120mg/lzrf62–(以zr计)和220mg/l钼离子且具有约4的ph值的后冲洗溶液处理如此涂覆的测试板。对比实施例13在亚硝酸盐促进(约90mg/l的亚硝酸盐)下,使用如对比实施例12的磷化溶液涂覆由光亮钢制成的测试板。随后用含有约120mg/lzrf62–(以zr计)且具有约4的ph值的后冲洗溶液处理如此涂覆的测试板。实施例11在过氧化物促进(约80mg/lh2o2)下,使用如实施例9的磷化溶液涂覆如对比实施例13的测试板。随后用含有约120mg/lzrf62–(以zr计)和220mg/l钼离子且具有约4的ph值的后冲洗溶液处理如此涂覆的测试板。实施例12在过氧化物促进(约50mg/lh2o2)下,使用如实施例10的磷化溶液涂覆如对比实施例13的测试板。随后用含有约120mg/lzrf62–(以zr计)和220mg/l钼离子且具有约4的ph值的后冲洗溶液处理如此涂覆的测试板。对比实施例14在亚硝酸盐促进(约90mg/l亚硝酸盐)下,使用如对比实施例12的磷酸化溶液涂覆由aa6014s制成的测试板。随后用含有约120mg/lzrf62–(以zr计)且具有约4的ph值的后冲洗溶液处理如此涂覆的测试板。实施例13在过氧化物促进(约80mg/lh2o2)下,使用如实施例9的磷化溶液涂覆如对比实施例14的测试板。随后用含有约120mg/lzrf62–(以zr计)和220mg/l钼离子且具有约4的ph值的后冲洗溶液处理如此涂覆的测试板。实施例14在过氧化物促进(约50mg/lh2o2)下,使用如实施例10的磷化溶液涂覆如对比实施例14的测试板。随后用含有约120mg/lzrf62–(以zr计)和220mg/l钼离子且具有约4的ph值的后冲洗溶液处理如此涂覆的测试板。在磷化后,用阴极电涂材料以及标准汽车涂料体系(填料、底漆、清漆)涂覆对比实施例12-14(ce12-ce14)以及实施例9-14(e9-e14)的测试板。对对比实施例12和13(ce12和ce13)以及实施例9-12(e9-e12)的测试板进行上文稍早所述的vda测试。结果总结在表4中。相反,根据dineniso9227对对比实施例14(ce14)以及实施例13和14(e13和e14)的测试板进行240小时的cass测试。结果总结在表5中。表4表5实施例15在35℃下且在过氧化物(约80mg/lh2o2)促进下,使用含有1.1g/lzn、1g/lmn和17g/lpo43–(以p2o5计)的无镍且无硝酸根的磷化溶液涂覆由热浸镀锌钢(ea)制成的测试板。将磷化溶液的酸值调节至0.07。随后用含有约120mg/lzrf62–(以zr计)和220mg/l钼离子且具有约4的ph值的后冲洗溶液处理如此涂覆的测试板。实施例16在35℃下且在过氧化物(约80mg/lh2o2)促进下,使用含有1.1g/lzn、1g/lmn和17g/lpo43–(以p2o5计)的无镍且无硝酸根的磷化溶液涂覆由热浸镀锌钢(ea)制成的测试板。将磷化溶液的酸值调节至0.05。随后用含有约120mg/lzrf62–(以zr计)和220mg/l钼离子且具有约4的ph值的后冲洗溶液处理如此涂覆的测试板。在磷化后,用阴极电涂材料以及标准汽车涂料体系(填料、底漆、清漆)涂覆实施例15和16(e15和e16)的测试板,然后在暴露于冷凝水240小时之前和之后进行划格法测试(如上文稍早所述)。结果汇总在表6中。从表6中可以看出,通过降低酸值(e16)可以显著改善暴露于冷凝水后的划格法结果。当前第1页12