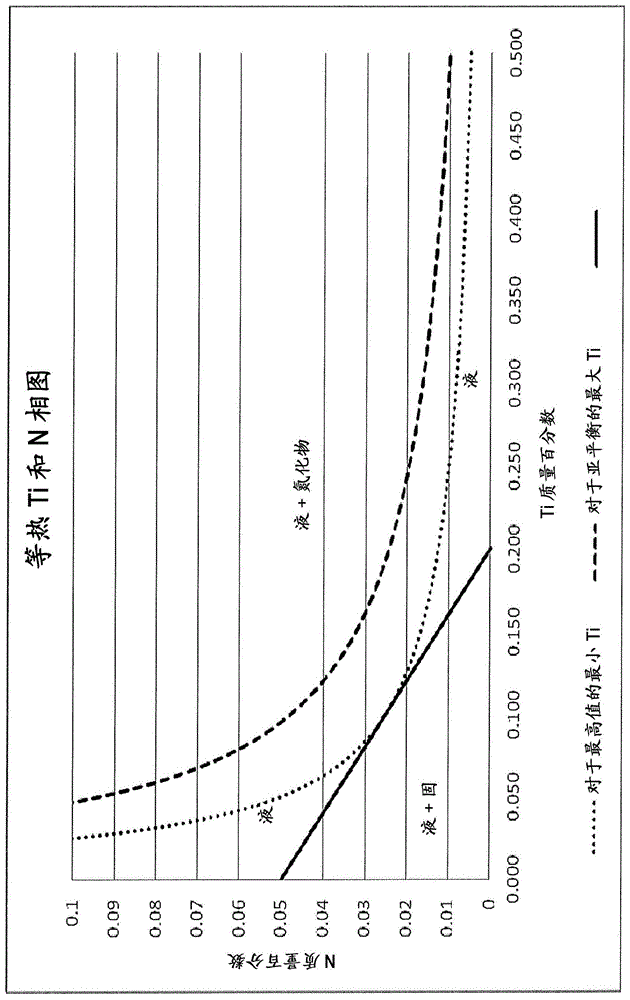
本申请是非临时专利申请,要求了于2012年4月2日提交的名称为“21%cr铁素体不锈钢”的61/619,048号临时申请的优先权。61/619,048号申请的公开通过引用合并于此。发明概要需要生产一种耐腐蚀性能与astm304类型不锈钢相当的铁素体不锈钢,这种不锈钢基本上不含镍,通过钛和铌双稳定化以防止晶间腐蚀,以及包含铬、铜和钼以提供耐点蚀性,而不牺牲耐应力腐蚀裂纹性。这种钢尤其可用于通用钢板,其通常见于商业厨房用品、建筑构件和汽车应用,汽车应用包括但不限于商用和客运车辆排气和选择性催化还原(scr)部件。附图说明图1是铁素体不锈钢的实施方案中液相线温度下钛和氮元素的相图。图2是描绘腐蚀速率作为在还原性酸性氯化物环境(诸如盐酸)中的钢组成的函数的图。图3是描绘腐蚀速率作为在富含硫酸盐的还原酸中的钢组成的函数的图。图4是描绘电化学阳极溶解电流密度作为钢组成的函数的图。图5是描绘电化学击穿电位作为钢组成的函数的图。图6是描绘电化学击穿电位作为钢组成的函数的图。图7是描绘电化学再钝化电位作为钢组成的函数的图。图8是描绘电化学再钝化电位作为钢组成的函数的图。图9是描绘铁素体不锈钢和比较钢的比较恒电位行为的图。图10是描绘铁素体不锈钢和比较钢的比较恒电位行为的图。发明详述在铁素体不锈钢中,控制钛、铌、碳和氮的相互关系及用量以获得亚平衡的表面质量,基本上为铸态等轴晶结构,完全耐晶间腐蚀。并且控制铬、铜和钼的相互关系以优化耐腐蚀性能。亚平衡熔体被定义为钛和氮的含量非常低以致在合金熔体中不形成氮化钛的组合物。这种氮化钛析出物在热轧或冷轧过程中会形成缺陷,如表面纵裂缺陷或层裂。这些缺陷会降低可成形性,耐蚀性以及外观。图1是从在铁素体不锈钢的一种实施方案的液相温度下热力学模拟钛和氮元素产生的示例相图得到的。为了基本不含氮化钛以及被认为是亚平衡,在铁素体不锈钢中的钛和氮的含量应落在图1中显示的溶解度曲线的左侧或下侧。如图1中所示,氮化钛的溶解度曲线可以表示为如下数学方程式:方程1timax=0.0044(n-1.027)式中,timax是钛的最大重量百分比浓度,n是氮的重量百分比浓度。除非另有指明,这里所有的浓度均为重量百分比浓度。根据方程式1,如果在一个实施方式中氮的含量等于或低于0.020%,那么所述实施方式中的钛的浓度应该保持在或低于0.25%。如果钛的浓度超过0.25%,就会导致在熔融合金中形成氮化钛析出物。然而,图1还显示,如果氮的含量小于0.02%,那么即使钛的含量高于0.25%也是可以接受的。铁素体不锈钢的实施方式显示铸态和轧态和退火态等轴晶结构,在板坯中没有大的柱状晶粒或在冷轧板中没有带状晶粒。这种精细的晶粒结构能够提高可成形性和韧性。为了获得这种晶粒结构,应具有足够的钛、氮和氧的含量以称为固化板坯的晶种,并提供等轴晶初始形成的位点。在这样的实施方式中,最小的钛和氮的含量示于图1中,并通过以下方程式表示:方程式2:timin=0.0025/n式中,timin是钛的最小重量百分比浓度,以及n是氮的重量百分比浓度。利用方程式2,如果在一个实施方式中氮的含量等于或低于0.020%,那么最小钛浓度是0.125%。图1中的抛物线表明如果总的钛浓度降低,那么在氮浓度高于0.02%时可以得到等轴晶结构。预期钛和氮的含量在方程式2所代表的曲线的右侧或上方时,可获得等轴晶结构。亚平衡状态与得到等轴晶结构的钛和氮含量之间的关系如图1所示。其中,最小钛含量方程式(方程式2)标会在图1的液相线相图上。两个抛物线之间的区域是这些实施方式中的钛和氮的含量范围。铁素体不锈钢的完全稳定化熔体必须具有足够的钛和铌,以与钢中存在的可溶解碳和氮相结合。这有助于防止因碳化铬和氮化铬的形成而降低耐晶间腐蚀性能。导致完全稳定化所需的最小钛和碳含量可用下式表示:方程式3:ti+cbmin=0.2%+4(c+n)式中,ti是钛的重量百分数,cbmin是铌的最小重量百分数,c是碳的重量百分数,n是氮的重量百分数。在上述的实施方式中,当最大氮含量为0.02%时,确定了等轴晶结构和亚平衡条件所必要的钛含量。如上所述,由式1和2分别得到了最小的钛含量是0.125%,最大的钛含量是0.25%。在该实施方式中,利用最大碳含量0.025%和应用式3,对于最小和最大的钛含量,需要的最小铌含量分别是0.25%和0.13%。在一些这样的实施方式中,铌浓度的目标是0.25%。在某些实施方式中,在由约21%cr和0.25%mo构成的基体中保持铜的浓度在0.40-0.80%之间,即可得到与市场上销售的304l相当(如果不比其更好)的整体耐腐蚀性。当有强酸性的还原氯化物(如盐酸)存在时除外。加铜的合金在硫酸中显示出改进的性能。当铜的含量维持在0.4-0.8%时,阳极溶解速率降低,电化学击穿电位在中性氯化物环境中最大。在某些实施方式中,最佳的cr、mo和cu的含量(以重量百分数表示)满足以下两个方程式:方程式4:20.5<cr+3.3mo方程式5:0.6<cu+mo<1.4当cumax<0.80所述铁素体不锈钢的实施方式可包含约0.020重量百分比或更低的碳。所述铁素体不锈钢的实施方式可包含0.40重量百分比或更低的锰。所述铁素体不锈钢的实施方式可包含约0.030重量百分比或更低的磷。所述铁素体不锈钢的实施方式可包含约0.010重量百分比或更低的硫。所述铁素体不锈钢的实施方式可包含约0.30-0.50重量百分比的硅。一些实施方式可包含约0.40%的硅。所述铁素体不锈钢的实施方式可包含约20.0-23.0重量百分比的铬。一些实施方式可包含约21.5-22重量百分比得铬,以及一些实施方式可包含约21.75%的铬。所述铁素体不锈钢的实施方式可包含约0.40重量百分比或更少的镍。所述铁素体不锈钢的实施方式可包含约0.020重量百分比或更少的氮。所述铁素体不锈钢的实施方式可包含约0.4-0.8重量百分比的铜。一些实施方式可包含约0.45-0.75重量百分比的铜,以及一些实施方式可包含约0.60%的铜。所述铁素体不锈钢的实施方式可包含约0.20-0.60重量百分比的钼。一些实施方式可包含约0.30-0.5重量百分比的钼,以及一些实施方式可包含约0.40%的钼。所述铁素体不锈钢的实施方式可包含约0.10-0.25重量百分比的钛。一些实施方式可包含约0.17-0.25重量百分比的钛,以及一些实施方式可包含约0.21%的钛。所述铁素体不锈钢的实施方式可包含约0.20-0.30重量百分比的铌。一些实施方式可包含约0.25%的铌。所述铁素体不锈钢的实施方式可包含约0.010重量百分比或更少的铝。所述铁素体不锈钢利用本领域已知的用于制造铁素体不锈钢的工艺条件,如记载在美国专利6,855,213和5,868,875中的工艺条件生产。在一些实施方式中,所述铁素体不锈钢也可包含炼钢领域已知的或者是故意添加或者是残留元素的其他元素,如炼钢过程中的杂质。在熔化炉(如电弧炉)中提供铁素体不锈钢的含铁熔体。这种含铁的熔体可由固体含铁废料、碳钢废料、不锈钢废料、含铁固体材料,包括氧化铁、碳化铁、直接还原铁、热压块铁,在熔化炉中形成,或者所述熔体也可在高炉中或在任何能够提供含铁熔体的其他熔铁单元内形成。然后,含铁熔体在熔化炉中精炼,或被移至精炼容器中,如氩氧脱碳容器或真空氧脱碳容器,然后是修整站,如钢包冶金炉或喂丝站。在一些实施方式中,含有足够钛和氮和限定量的铝(用于形成小的氧化钛夹杂物以提供形成铸态等轴晶结构必需的核心)的熔体被铸造成钢,使得用这样的钢生产的退火板也有增强的起垄特性。在一些实施方式中,铸造之前将钛添加到熔体中以达到脱氧的目的。用钛来对熔体脱氧形成小的氧化钛夹杂物,这些夹杂物提供铸态等轴晶结构必需的核心。为了使生成的氧化铝夹杂物,如三氧化二铝al2o3的量最少,可不将铝作为脱氧剂加入到这种精炼的熔体中。在一些实施方式中,钛和氮可存在于铸造之前的熔体中,以便产品中钛和氮除以残留铝的比至少为0.14。如果钢需要稳定化,则可添加超过脱氧所需量的钛,用于与熔体中的碳和氮结合,但最好小于与氮饱和(即亚平衡的量)所需量,由此可以避免或至少最小化在固化之前大的氮化钛夹杂物的析出。将铸钢热加工为钢板。对于本公开,术语“板”指的是包括连续带或从连续带切割的一段,以及术语“热加工”是指铸钢会被再加热,此后如果必要的话,如通过热轧将铸钢减薄到预定的厚度。如果进行热轧,板坯被再加热至2000到2350°f(1093-1288℃),热轧终了温度是1500-1800°f(816-982℃),并在1000-1400°f(538-760℃)的温度卷取。热轧钢板也被称为“热带”。在一些实施方式中,热带可在金属峰值温度1700-2100°f(926-1149℃)被退火。在一些实施方式中,热带可被除鳞并冷轧减薄至少40%达到需要的最终板厚。在其他实施方式中,热带可被除鳞并冷轧减薄至少50%达到需要的最终板厚。其后,冷轧板在金属峰值温度1700-2100°f(927-1149℃)被退火。铁素体不锈钢可以由通过很多方法制造的热加工钢板生产。该钢板可以由锭坯或连铸坯形成的厚度为50-200mm的板坯经再加热至2000-2350°f(1093-1288℃),然后进行热轧,以得到厚度为1-7mm的初始热加工板来生产,或者该钢板由连铸带钢热加工为厚度2-26mm。本工艺适用于通过其中将连铸坯或锭坯直接提供到有或没有显著再加热的热轧机中的方法生产的板,或者适用于热减薄为具有足以在有或没有进一步再加热下被热轧成钢板的板坯的锭坯。实施例1为制备导致其整体耐腐蚀性与304l奥氏体不锈钢相当的铁素体不锈钢组合物,进行了一系列实验室炉次(heats)的熔化,并分析了耐局部腐蚀性。利用大气熔化能力在实验室熔化了第一组炉次。该系列大气熔化的目的是更好地了解铬、钼和铜在铁素体基体里的作用和与304l钢的腐蚀行为进行比较,了解组成的变化如何影响腐蚀性能。这个研究中,在所研究的大气熔化中使用的实施方式的组成如下表1所示。表1对以上表1中涉及到的化学物质进行三氯化铁浸泡实验和电化学评价实验,并与304l钢的性能进行对比。根据astmg48中描述的三氯化铁点蚀试验方法a,样品在50℃,暴露在6%的三氯化铁溶液中24小时后,评价其质量损失。该暴露试验评价当暴露于酸性,强氧化或氯化物环境中时基本的耐点蚀性能。筛选实验表明,加入少量铜的高铬铁素体合金将会形成在该系列中最耐腐蚀的组成。具有最高铜含量(1%)的组成不会像其他化学物质那样耐腐蚀。然而,这种行为可能是由于熔化过程产生的不理想的表面质量造成的。用电化学技术对钝化膜强度和再钝化行为进行了详细研究,使用的电化学技术包括腐蚀曲线(cbd)和在脱气的、稀释的、中性的氯化物环境下的循环极化。在这组空气熔化物上观察到的电化学行为表明大约21%cr、0.5%cu和少量的mo的组合能够实现在三个方面对304l钢的主要改善。首先,铜的加入似乎降低了表面上初始阳极溶解速率;第二,铜和少量钼存在于21%cr化学物质中有助于强钝化膜的形成;第三,钼和高含量的铬有助于改善再钝化性能。在21cr+残留mo的熔体中铜的含量确实出现一个“最佳”值,加入1%铜将导致性能下降。这一点证实了在三氯化铁点蚀实验中观察到的性能。对于希望生产清洁钢样品的真空熔炼提出了其他熔体化学并确定最佳铜添加量以获得最好的整体耐蚀性能。实施例2对于真空熔体工艺提出了表2中的第2组熔体化学物质。这个研究中的组成如下表所示。表2idcmnpssicrnicumoncbti020.0150.300.0270.00260.3620.820.250.240.250.0140.200.15510.0140.300.0260.00260.3620.760.240.940.250.0140.200.17910.0160.290.0280.00260.3520.720.250.480.250.0140.200.17920.0160.290.0280.00260.3620.840.250.740.250.0140.200.15上述加热体主要在铜含量上变化,为进行比较,表3所示的组成的其他真空热也被熔化。用于比较的304l是可商购的钢板。表3表3的化学物质被真空熔化成为锭,在2250f(1232℃)热轧,除鳞并冷轧减薄60%。冷轧减薄的材料在1825f(996℃)进行最终退火,然后进行最终除鳞。实施例3在上述提到的实施例2(用它们的id号识别)的真空熔体上进行的比较研究是在盐酸、硫酸、次氯酸钠和醋酸中的化学浸泡试验。1%盐酸。如图2所示,化学浸泡评价显示在还原酸性氯化物环境中(如盐酸)镍的有益效果。在该环境下,304l钢优于所有研究的化学物质。铬的加入导致很低的整体腐蚀速率,而铜和钼的存在显示进一步降低了腐蚀速率,但铜单独的效果非常小,如图2中标注fe21crxcu0.25mo的线所示。这种表现支持了镍的加入对于作用条件是有利的,如下所述。5%硫酸。如图3所示,在富含硫酸盐的还原酸中的浸泡实验中,铬含量在18-21%的合金表现类似。钼和铜的加入显著降低了总体腐蚀速率。在评价铜单独对腐蚀速率的影响(如图3中标记为fe21crxcu0.25mo的线所示)时,似乎是有一个直接的关系,即铜含量越高,腐蚀速率越低。在铜含量为0.75%时,总体腐蚀速率开始稳定,在304l的2mm/yr之内。钼的含量在0.25%时,对在硫酸中的腐蚀速率影响很大。然而,腐蚀速率的急剧降低也归因于铜的加入。尽管实施例2中的合金的腐蚀速率没有低于304l钢,但他们确实在还原的硫酸条件下显示出提高的、相当的耐腐蚀性能。醋酸和次氯酸钠。在由醋酸和5%次氯酸钠构成的酸浸泡中腐蚀行为和304钢l相当。腐蚀速率非常低,并且加入铜后在腐蚀行为上没有观察到真正的趋势。实施例2中所有研究的含铬高于20%的化学物质均在304l钢的lmm/yr之内。实施例4进行包括腐蚀曲线图(cbd)和循环极化研究的电化学评价,并与304l钢的行为进行比较。为研究铜对阳极溶解行为的影响,汇总了实施例2中的真空热化学物质和可商购的304l在3.5%次氯酸钠溶液中的腐蚀行为曲线。阳极端代表在达到钝化状态之前在材料的表面发生的电化学溶解。如图4所示,至少0.25%的钼和最少约为0.40%的铜的加入降低了在阳极溶解过程中的电流密度到低于304l钢的测定值。同时,也注意到使阳极电流密度保持在低于304l钢的测定值的铜的最大加入量大约在0.85%左右,如图4中标注为fe21crxcu.25mo的线所示。这表明在21%cr和0.25%钼存在下同时加入少量的可控制量的铜确实可以降低在稀氯化物中的阳极溶解速率,且为保证溶解速率低于304l钢的显示值有一个最适宜的铜含量。汇总了实施例2中的实验化学物质和可商购的304l钢在3.5%次氯酸钠溶液中的循环极化图。这些循环极化图通过阳极活性溶解、钝化区、超钝化区和钝化的击穿来说明铁素体不锈钢的阳极行为。并且,将这些极化图像反过来可以确定再钝化电位。上述循环极化图中显示的击穿电位如图5和图6所示,该值被用来考察加入铜的影响,如果有影响的话。击穿电位确定为是电流开始连续流过击穿的钝化层,且开始出现活性小坑时的电位。与阳极溶解速率非常相似,如图5和图6中标记为fe21crxcu.25mo的线所示,铜的加入似乎强化了钝化层,且说明在小坑的形成方面,为使铜的有利方面最大化,存在一个最佳的铜加入量。在0.25%钼和21%cr存在下,达到最大的钝化层强度时,铜的含量在0.5-0.75%。这种趋势在上述讨论的阳极溶解研究中得到的腐蚀曲线上得到证实,尽管由于扫描速率的差异,使数值往更小方向移动。评价实施例2的真空熔化化学物质的再钝化行为时表明,铬的含量为21%,并加入少量的钼能使再钝化反应最大化。铜与再钝化电位之间的关系似乎随着铜含量的增加而变得不利,如图7和图8中标记为fe21crxcu.25mo的线所示。只要铬的含量约为21%,和少量的钼存在,实施例2中所研究的化学物质就能达到高于304l钢的再钝化电位,如图7和图8所示。实施例5将具有下表4中(id92,实施例2)所示组成的铁素体不锈钢与具有表4中所示组成的304l钢进行比较。表4合金ccrnisiticb(nb)其他id920.01620.840.250.360.150.200.74cu,0.25mo304l0.0218.258.500.50....1.50mn根据astm标准试验测定时两种材料具有如表5表示出的力学性能。表5与304l钢相比,实施例2的材料中,id92显示出更好的抗电化学性能,更高的击穿电位和更高的再钝化电位,如图9和图10所示。应了解在不背离本发明的精神和范围的情况下可以对本发明进行各种改进。因此,本发明的范围应由所附的权利要求确定。当前第1页12