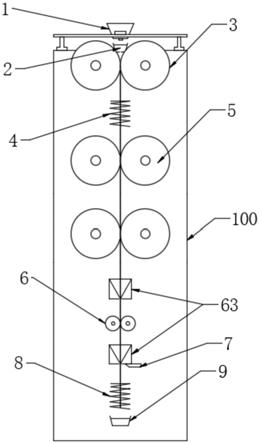
[0001]
本实用新型属于黄金生产提纯设备技术领域,具体是涉及到一种黄金连续铸锭设备。
背景技术:[0002]
黄金是国际通用结算货币,属硬通货,保值性强,供交割用的金条由交易所指定厂家生产,正面为会员标识,背面带有交易所标识和生产厂家标识,铸有唯一编号。金条延用黄金国标gb/t4134-2003,金条,单条重量为200克和500克,纯度不低于99.99%,生产含金99.99%及以上的高纯金越来越受到人们的关注,由于其良好的市场前景,各企业争相研究高纯金生产工艺。
[0003]
传统的黄金铸锭,需要先将99.99%金进行熔炼,再通过造粒机将黄金变成直径为2mm-4mm的金粒,接下来通过烘干设备将金粒进行烘干,然后通过人工进行手工配重,将配重好的金粒倒入石墨模具进行熔铸成金锭,这种铸锭方式存在以下问题:
[0004]
1、黄金熔体的凝固是从结晶器的内壁开始,垂直于冷却面的方向向黄金熔体内部扩展,所以铸造组织具有明显的方向性,随着黄金熔体凝固层的增厚,传热系数减小,内外晶核的形成和长大的不一致导致晶粒的形状、位向和大小也随之变化,凝固时造成的偏析现象,晶粒四周和晶体内浓度的差异扩大了再结晶温度区间,降低了生核率,铸造时金锭内部产生不同程度的缩孔和疏松组织,导致金锭的重量达不到要求。
[0005]
2、配重时人工的进行金粒的粗配重,然后通过人手工增减金粒达到配重要求,配重的精度要求高,所以配重环节需要消耗大量的人工成本和时间成本。
[0006]
3、国外的自动配重设备也是首先进行金粒的粗配重,然后通过剪切细金丝进行配重,虽然实现了自动化配重,但是其对金粒和细金丝的要求比较高,需要质地均匀而且干燥程度要求高,传统的轧制机生产的金丝不均匀,经过多次的挤压后才能达到均匀目的,轧制过程造成大量的金损耗和能耗的浪费,其次是消耗金粒和细金丝两种原料,工艺周期长,铸造成本高。
技术实现要素:[0007]
本实用新型要解决的技术问题是提供一种自动化程度高、工艺周期短、配重精准,能降低人工成本、大幅提升生产效率的黄金连续铸锭设备。
[0008]
为了达到上述目的,本实用新型的技术方案如下,一种黄金连续铸锭设备,包括机箱,所述机箱内自上而下依次设有熔炼炉、线模、牵引轮、中频线圈、轧制轮、长度计量器、切割刀、高频线圈和模盒,所述熔炼炉的下方设有用于承接黄金熔体的线模,线模用于承接熔炼炉中的黄金熔体,并将黄金熔体浇铸成铸条,铸条经牵引轮引导穿过中频线圈,并由轧制轮挤压成金线,所述长度计量器测量金线的长度,且上方和下方均设有导向筒,所述切割刀设于长度计量器下方的导向筒上,用于切断金线,所述模盒承接高频线圈加热熔化的黄金,冷却形成金锭。
[0009]
优选的,所述轧制轮上挤压槽的截面形状为半圆形,所述半圆形圆弧的直径为20-35mm。
[0010]
优选的,所述轧制轮为中空结构,轧制轮的一个端面与旋转轴连接,另一个端面与旋转接头连接,所述旋转接头上设有进水口和出水口。
[0011]
优选的,所述轧制轮至少为两对,且每个轧制轮上均设有温度传感器。
[0012]
优选的,所述长度计量器的精度为
±
0.001mm。
[0013]
优选的,所述长度计量器包括导线轮和计量轮,两个所述导线轮沿金线水平的径向方向设置,所述计量轮沿金线竖直的径向方向设置。
[0014]
优选的,所述黄金连续铸锭设备还包括风冷机构,所述风冷机构向机箱内通入氮气。
[0015]
优选的,所述机箱内通入氮气的压力为3-6bar。
[0016]
优选的,所述熔炼炉的进料口设有高温纤维幕帘。
[0017]
优选的,所述导向筒的进线口不小于出线口。
[0018]
本实用新型的有益效果是,将熔炼到铸锭整个流程集成在一台设备上完成自动一体化,黄金原料经熔炼炉加热熔解进入线模,线模将黄金熔体浇铸成铸条,压丝过程增加中频线圈来进行二次加热均匀化处理,铸条由牵引轮导向从中频线圈中穿过,二次加热后由轧制轮进行热轧、挤压,能使金线不均匀状态得到很大改善,轧制轮挤压得到均匀的金线,然后通过长度计量器精准测量金线长度,导向筒的中心轴线与长度计量器上金线的中心轴线高度相平齐,能够最大限度的减少对金线的磨损,防止金线跳变的问题,保证长度测量精度,由切割刀进行剪切,切断后的金线通过高频线圈加热后,以溶液状态进入模盒,冷却后形成金锭,设备仅需进行距离测量就能快速的完成配重,自动化程度高,配重精准,能缩短整个工艺的时间周期,降低人力和时间成本,避免金粒均匀、干燥、金丝消耗、第二次精准配重问题对金锭品质的影响,无二次金污染,高频线圈加热速度快,总的能耗低,能降低铸锭成本。
附图说明
[0019]
图1为本实用新型其中一实施例的结构示意图;
[0020]
图2为图1所示的轧制轮的结构示意图;
[0021]
图3为图2所示的轧制轮另一视角的结构示意图;
[0022]
图4为图1所示的长度计量器的结构示意图;
[0023]
图5为导向筒的结构示意图;
[0024]
图6为图5所示的导向筒另一视角的结构示意图。
[0025]
在图中,100-机箱;1-熔炼炉;2-线模;3-牵引轮;4-中频线圈;5-轧制轮;6-长度计量器;7-切割刀;8-高频线圈;9-模盒;51-挤压槽;52-旋转轴;53-旋转接头;531-进水口;532-出水口;61-导线轮;62-计量轮;63-导向筒。
具体实施方式
[0026]
下面结合附图和具体实施例,对本实用新型的技术方案作进一步具体的说明:
[0027]
请一并参阅图1-6,本实施例提供一种黄金连续铸锭设备,包括机箱100,所述机箱
100内自上而下依次设有熔炼炉1、线模2、牵引轮3、中频线圈4、轧制轮5、长度计量器6、切割刀7、高频线圈8和模盒9,所述熔炼炉1的下方设有用于承接黄金熔体的线模2,线模2用于承接熔炼炉1中的黄金熔体,并将黄金熔体浇铸成铸条,铸条经牵引轮3引导穿过中频线圈4,并由轧制轮5挤压成金线,所述长度计量器6测量金线的长度,所述切割刀7由气缸或者电机驱动,用于切断金线,所述模盒9承接高频线圈8加热熔化的黄金,冷却形成金锭。
[0028]
使用时,黄金原料经熔炼炉1加热熔解进入线模2,线模2将黄金熔体浇铸成铸条,压丝过程增加中频线圈4来进行二次加热均匀化处理,铸条由牵引轮3导向从中频线圈4中穿过,二次加热后由轧制轮5进行热轧、挤压,能使金线不均匀状态得到很大改善,轧制轮5挤压得到均匀的金线,然后通过长度计量器6精准测量金线长度,由切割刀7进行剪切,切断后的金线通过高频线圈8加热后,以熔液状态进入模盒9,冷却后形成金锭;将熔炼到铸锭整个流程集成在一台设备上完成自动一体化,设备仅需进行距离测量就能快速的完成配重,自动化程度高,配重精准,能缩短整个工艺的时间周期,降低人力和时间成本,避免金粒均匀、干燥、金丝消耗、第二次精准配重问题对金锭品质的影响,无二次金污染,高频线圈加热速度快,总的能耗低,能降低铸锭成本。
[0029]
所述轧制轮5上挤压槽51的截面形状为半圆形,能增加金线与轧制轮5的接触面积,提高热传递的效率,所述半圆形圆弧的直径为20-35mm,两个轧制轮5挤压时,产生直径为20-35mm的金线。
[0030]
所述轧制轮5为中空结构,轧制轮5的一个端面与旋转轴52连接,另一个端面与旋转接头53连接,所述旋转接头53上设有进水口531和出水口532,进水口531、出水口532通过旋转接头53与轧制轮5连接,并形成一个冷却回路,便于轧制轮5的冷却,提高了金线冷却、结晶的效率。
[0031]
在本实施例中,所述轧制轮5为两对,且每对轧制轮5上均设有温度传感器,温度传感器测量金线的表面温度,设备根据金线的表面温度信息控制循环水的冷却速度和轧制轮5的转动速度;靠近中频炉的轧制轮5通入压力不小于3.5bar、温度为23-26℃的冷却水;另一对轧制轮5通入压力不小于3.5bar、温度为19-23℃的冷却水;滚轮采用中空形式,冷却水通过轧制轮5与金线接触达到降温的目的,两对轧制轮5通入两级不同温度冷却水对金线进行分级降温处理,减小或消除冷却不均匀的影响,从而达到金线均匀化的目的。为了进一步改善金线的热轧、挤压的性能,使金线均匀化,以达到提高热加工后产品质量和档次的目的,轧制轮5还可以为三对、四对或者更多,将冷却水的温度划分为相应数量的等级,采用多级不同温度冷却进行进行分级降温处理,减小或消除冷却不均匀的影响。
[0032]
所述长度计量器6的精度为
±
0.001mm,能将金锭每千克的误差控制在
±
0.005g,保证金锭品质和档次,以满足交割要求。
[0033]
所述长度计量器6包括导线轮61和计量轮62,两个所述导线轮61沿金线水平的径向方向设置,所述计量轮62沿金线竖直的径向方向设置,采用三个面的滚轮带动并测量所需精准长度,有效验长度的功能,形成实时反馈,保证精准度;导线轮61和计量轮62均具有凹形槽外圆周,能降低金线卡槽和脱落的风险。
[0034]
长度计量器6的上方和下方均设有有导向筒63,所述切割刀7设于长度计量器6下方的导向筒63上,用于切断金线;所述导向筒63的中心轴线与长度计量器6上的金线高度相平齐,能够最大限度的减少对金线的磨损,防止金线跳变的问题,提高生产效率。
[0035]
黄金连续铸锭设备还包括风冷机构,所述风冷机构向机箱100内通入氮气,一方面能提升冷却速度,另一方面通入氮气作为保护气体。
[0036]
所述机箱100内通入氮气的压力为3-6bar。
[0037]
所述熔炼炉1为中频炉,中频炉的石墨坩埚的进料口设有高温纤维幕帘,用以封闭机箱100内部的保护气体;石墨坩埚要求纯度高,同时避免熔炼过程有石墨粉进入到黄金熔液中。
[0038]
所述导向筒63的进线口不小于出线口,较大的进线口便于金线伸入,较小的出线口用于限定金线的位置。
[0039]
一种黄金连续铸锭方法,包括以下步骤:
[0040]
熔炼:机箱100内通入压力为3-6bar的氮气,将纯度不小于99.99%的金原料放入熔炼炉1内,熔炼炉1的加热温度为1150-1250℃(溶金温度1064℃),黄金熔解后,开启熔炼炉1底部的孔塞,使黄金熔体进入线模2;
[0041]
铸条:线模2将黄金熔体浇铸成铸条;
[0042]
二次加热:牵引轮3引导铸条穿过中频线圈4,中频线圈4加热的温度为300-600℃;
[0043]
压丝:轧制轮5将中频线圈4加热后的铸条挤压成金线,轧制轮5内通入压力不小于3.5bar、温度为19-26℃的冷却水,轧制轮5上的温度传感器测量金线的表面温度,设备根据金线的表面温度信息控制循环水的冷却速度和轧制轮5的转动速度;
[0044]
剪切配重:长度计量器6测量金线长度,由切割刀7进行剪切配重;
[0045]
铸锭:高频线圈8的加热温度为1200-1250℃,剪切好的金线进入高频线圈8后快速熔解,由模盒9承接,冷却模盒9后形成金锭。
[0046]
本方法提供的黄金连续铸锭方法在压丝过程增加中频线圈4来进行二次加热均匀化处理,二次加热后的铸条由轧制轮5进行热轧、挤压,能使金线不均匀状态得到很大改善,轧制轮5挤压得到均匀的金线,避免多次轧制、挤压带来的黄金损耗和能量损耗等问题;在配重时,无需像传统流程进入中转容器和称量容器进行称重,仅需进行金线长度测量、剪切即可快速的完成配重,精准配重好的金线通过高频线圈8进行加热,直接熔解进入石英模盒9中,高频线圈8将石英模盒9包裹,当剪切好的金线进入高频线圈8后快速熔解,然后冷却模盒9后形成能交割的金锭,整个流程自动化程度高、工艺周期短、配重精准,能降低人工成本、大幅提升生产效率。
[0047]
以上实施例仅用于说明本实用新型的技术方案,而非对其限制;尽管参照前述实施例对本实用新型进行了详细的说明,本领域的普通技术人员应当理解:其依然可以对前述各实施例所记载的技术方案进行修改,或者对其中部分技术特征进行等同替换;而这些修改或者替换,并不使相应技术方案的本质脱离本实用新型各实施例技术方案的精神和范围。