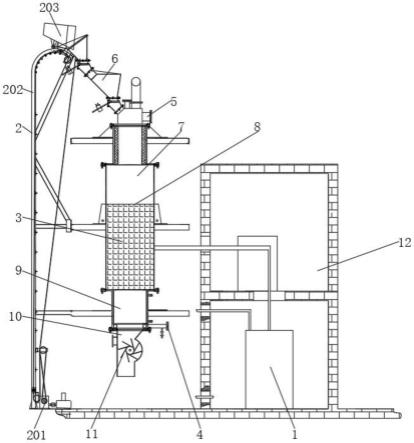
1.本发明涉及电治金还原技术领域,具体为一种可实现零碳排放的还原铁粉清洁生产方法与装置。
背景技术:2.钢铁工业既是国民经济发展的重大基础性行业,又是工业领域co2排放总量较大重点产业。究其根源就是钢铁工业一直以来把“碳”作为能源与还原剂的主体!从“零碳”排放的终极目标考虑,采用“清洁电”做能源并配合采用氢做冶金还原剂将是未来冶金工业实现绿色发展的唯一选择!因此研究、开发“清洁电”与氢在冶金领域的创新与协同应用,一旦技术取得突破,将会从源头推动传统“碳冶金”向新型“氢、电冶金”转变,使钢铁生产彻底摆脱对化石能源的绝对依赖,并带动其它相关行业协同实现可持续发展。
3.但是目前现有技术中用于还原铁粉生产的方法及其装置由于传统技术在清洁生产方面相对的不完善,已经无法满足未来发展的的需求,目前现有碳热炉窑及工艺生产存在还原铁能耗高、周期长、碳排放量大、炉料球团还原不均匀、高纯铁粉制备需要二次氢还原等技术的问题。所以我们提出了一种可实现零碳排放的还原铁粉清洁生产方法与装置,以便于解决上述中提出的问题。
技术实现要素:4.本发明的目的在于提供一种可实现零碳排放的还原铁粉清洁生产方法与装置,以解决上述背景技术提出的目前现有技术中用于还原铁粉生产的方法及其装置由于其技术在清洁生产方面相对的不完善,已经无法满足未来发展的需求,目前现有碳热炉窑及工艺生产还原铁能耗高、周期长、碳排放量大、炉料球团还原不均匀、高纯铁粉制备需要二次氢还原等技术的问题。
5.本技术方案采用氢气还原与“全电气化”模式作业运行,如实施水电、风电、光伏等方式供电及制氢,其整个冶金流程将完全实现清洁生产与零碳排放。
6.为实现上述目的,本发明提供如下技术方案:一种可实现零碳排放的还原铁粉清洁生产方法与装置,包括中频电控系统、出料装置和供氢及还原尾气氢回收系统,在竖炉冷却段下端外侧设有环形气室,环形气室通过周向设置的氢还原气喷口与炉体冷却段连通,氢还原气由竖炉环形气室通过周向设置的喷口正压进入炉体冷却段内部;
7.所述上料机构包括驱动机构、轨道和上料台车,所述上料机构开设有驱动机构,且驱动机构上传动连接有轨道,所述轨道上安装有上料台车;
8.所述感应竖炉包括石墨内衬、感应线圈、绝缘层、线圈间隙、炉料和炉衬隔热层,所述感应竖炉内壁上开设有石墨内衬,且感应竖炉外部盘绕有感应线圈,所述感应线圈上开设有绝缘层,所述感应线圈之间设置有线圈间隙,所述感应竖炉内部设置有炉料,所述石墨内衬外侧包裹有炉衬隔热层;
9.所述感应竖炉内部开设有石墨炉体加热还原段,且石墨炉体加热还原段上方设置
有炉体预热段,所述炉体预热段上方连接有富氢还原尾气回收单元接口,所述炉体预热段上方连接有储球料斗,且储球料斗侧面设置有上料机构,所述感应竖炉与中频电控系统之间的连接方式为电性连接,所述石墨炉体加热还原段下方设置有炉体金属球团冷却段,所述炉体金属球团冷却段底部设置有储氢供氢单元接口,且炉体金属球团冷却段下方开设有炉体冷储室,所述炉体冷储室下方安装有出料装置;
10.所述储氢供氢单元接口的输入端连接有供氢及还原尾气氢回收系统,所述储氢供氢单元接口输出端连接有炉体金属球团冷却段,所述富氢还原尾气回收单元接口的输出端设置有供氢及还原尾气氢回收系统。
11.优选的,所述中频电控系统的频率范围为100hz-1450h,所述感应线圈的所述线圈间隙间距为15mm~60mm,并且感应竖炉的功率控制在大于等于50kw。
12.炉体设计为常压、密闭、连续式生产作业,其冶金功能为“感应焙烧”,竖炉采用防磁泄露设计,操作采用手动或自动可切换控制。
13.优选的,所述感应竖炉呈中空圆柱形,所述感应竖炉中所述石墨内衬的壁厚为50mm~200mm,并且石墨内衬由石墨电极经机加工去芯制取。
14.其余炉段的炉衬由尖晶石等材质的浇注料整体按设计预制成型后配套使用。石墨炉衬的石墨材料是以优质石墨焦为主要原料,经煅烧、成型、焙烧、石墨化、机械加工而制成。竖炉石墨炉衬内径≥800mm可采用异形石墨砖环砌制成。
15.优选的,所述石墨内衬的高度可有单个或数个同等内径与壁厚的中空圆柱体链接构成或采用异形石墨砖环砌制成,且石墨内衬圆柱体的链接端面呈凹凸状设置。
16.一种可实现零碳排放的还原铁粉清洁生产方法,生产方法步骤如下:
17.s1:采用感应电加热、氢冶金还原的原理生产还原铁粉,同时在将炉料加入炉体之前将氧化铁质冷固球团与球径相当的石墨块均匀混合;混合完成后通过上料机构将混合的物料输送至上端的储球料斗等待备用,氧化铁质冷固球团采用高纯度氧化铁精矿、氧化铁磷粉粒或氧化铁颜料单一或混配构成,同时经少量配水润湿后,采用机械压制成冷固球团;石墨块与氧化铁质冷固球团按0~80%的比例均匀混配后入炉还原焙烧;
18.石墨块在本技术方案中有两种主要作用:作为竖炉的次热源配合石墨炉衬主热源建立氢还原反应热场,均匀加热氧化铁质冷固球团;作为竖炉高温还原反应的“隔离”材料,防止还原过程金属铁质类冶金球团在高温区形成烧结粘连,影响炉料的“连续”下行。
19.s2:将混合均匀的炉料经储球料斗中的滚筒阀分批次加入至炉体内部,并且通过中频电控系统启动设备,中频电炉利用中频电源经铜质感应线圈建立交变磁场,在石墨内衬与炉内石墨块同步产生感应电流、感应电流克服其内电阻产生焦耳热,其中由竖炉石墨炉衬形成的感应放热,构成石墨炉体加热还原段的主热源,由炉内石墨块形成的感应放热,构成石墨炉体加热还原段炉料均热的次热源,这两部分感应放热通过中频电控系统输出功率的调整在炉内协同建立起600~1100℃的炉料焙烧还原反应热场,并导致金属炉料尖端放电,产生特殊氢还原反应;炉料进入预热段之后按照工艺设定的下行速度连续下行进入还原段;
20.另外,本中频电热氢冶金竖炉,在炉料还原反应区的焙烧热场中将在已金属化的球团之间产生独特的尖端放电,其放电形成的高温电弧,将使电弧内的h2分子发生高温化学电离,激发出极高化学活性的单氢离子,形成与常规氢还原反应(fe2o3+3h2=2fe+3h2o)
不同的还原反应机制,可促进氢还原速率的有效提升;
21.s3:生产作业连续运行,炉料由炉顶储球料斗放入炉体预热段、靠重力下行与上行炉气逆流换热;采用氢气做还原气,氢气由炉体金属球团冷却段下部连续正压导入,经下行金属球团炉料逆流换热、得到梯次升温的热氢气,在炉体加热段与下行铁鳞热料球完成氧化铁至金属铁的脱氧还原反应;
22.竖炉预热段有两种工艺效果:将下行炉料与上行热还原炉气换热升温预热;
23.将上行热还原炉气与下行炉料换热降温至150~180℃,实现感应竖炉上部热能的梯次利用;
24.s4:在石墨炉体加热还原段生成的金属化球团靠重力下行,金属球团炉料经炉体金属球团冷却段降温下行进入炉体冷储室,继续冷却降温后排出炉体;反应后的氢还原炉气上行经炉体预热段换热降温后,其还原尾气由炉顶排出进入供氢及还原尾气氢回收系统中经过冷凝处理、干燥剂处理等方法进行脱水后增压返回感应竖炉再利用,且还原用氢气采用符合国标的工业的氢气或回收脱水再生氢气或以液氨为原料催化分解制得的氢气;
25.氢气具有两种冶金作用:做清洁还原气体、做强制冷剂,通过在球料间的迷宫式穿行,对下行的金属化热球团进行换热冷却,氢气的导热系数是空气的6.69倍,散热能力是空气的8倍,自身被预热到600~1000℃;另外,氢还原是吸热反应,其对下行金属化热球团的深度还原,可对热金属球团进一步形成化学降温作用,使其得到强化冷却;
26.对于本步骤中还原尾气的主要成分为h2o和h2,而供氢及还原尾气氢回收系统所采用的干燥方法,本领域技术人员可根据实际工况进行干燥方法和干燥剂的选用,同时液氨制氢的催化原理已为目前公开技术,因此在此不再进行详细的赘述。
27.将氢还原气由竖炉冷却段下端外侧设置环形气室,通过周向设置的喷口正压进入冷却段内部,与炉内下行的热金属球团换热至600~1000℃后进入炉内反应区与炉料球团发生还原反应fe2o3+3h2=2fe+3h2o;反应后的还原炉气上行进入炉体上部的炉料球团预热段,在与预热段的冷炉料换热降温后,其尾气由炉顶排出进入尾气氢回收系统回收利用;
28.s5:出炉的金属球团需先将混配在其中的石墨块分拣出之后,再衔接球磨工艺,完成高纯、低磷、低硫还原铁粉产品的制备。
29.本技术方案可将金属化率≥98%的金属化球团在非氧化性气体的保护下直接球磨制备出高纯、低磷、低硫、致密的还原铁粉产品,而不需要再经过传统的二次还原纯化,同时分拣出的石墨块返回系统循环使用。
30.优选的,氧化铁质冷固球团直径控制在10mm~60mm,且氧化铁质冷固球团入炉时水分小于1%,并且石墨块的直径控制在15mm~100mm。
31.优选的,采用液氨催化分解制成的含氮混合氢气其还原尾气不再回收利用,且氢气气压控制在大于等于0.2mpa。
32.优选的,所述炉料在高温反应区的还原时间60~360分钟,且还原尾气在出炉时温度控制在120℃~150℃,并且出炉的还原尾气经供氢及还原尾气氢回收系统洗涤、脱水净化后方可循环利用,所述净化后的气体h2o含量小于等于4%。
33.与现有技术相比,本发明的有益效果是:该可实现零碳排放的还原铁粉清洁生产方法与装置:
34.实现电气化操控,更易实现全系统的自动化与智能化;中频电热氢冶金竖炉,采用
感应电流加热模式,经竖炉中频电源形成交变磁场,在石墨炉衬及炉料石墨块中产生感应电流,形成电阻热,可对炉内整个反应区料柱由内到外均匀、快速加热配合感应电流在炉内形成的尖端放电效应,可使反应区内的炉料高效还原,可显著提升本装置的生产作业效率。
35.中频电热氢冶金竖炉为连续作业,通过炉料与还原氢气的逆流热交换,使装置内的热能得到了梯次利用,显著提升了竖炉流程的能源效率。中频电热氢冶金竖炉,不经过传统的碳还原过程,不需配加焦丁、碳粉、煤等带杂质还原剂,也不用配加冶金石灰等脱硫剂,使还原铁产品纯度大为提升(氢还原反应还有附加脱硫、脱磷等效果),可一次还原直接制备出高纯、低磷、低硫、致密的还原铁产品,而不需要再经过传统的二次氢还原纯化加工,使流程更加高效、清洁。
36.中频电热氢冶金竖炉,因其在炉料中配加石墨块,可在高温还原反应区内对金属化球团产生隔离作用,可有效防止常规竖炉在≥700℃时发生炉料高温粘结状况,保障竖炉可在生产条件下连续高效运行。
37.采用氢气还原及“全电气化”模式作业运行,如实施水电、风电、光伏等方式供电及制氢,其整个冶金流程将完全实现绿色生产与零碳排放。
附图说明
38.图1为本发明一种可实现零碳排放的还原铁粉清洁生产装置主体结构示意图;
39.图2为本发明一种可实现零碳排放的还原铁粉清洁生产装置感应竖炉剖视结构示意图;
40.图3为本发明一种可实现零碳排放的还原铁粉清洁生产方法流程示意图;
41.图4为本发明一种可实现零碳排放的还原铁粉清洁生产装置炉内各反应区参数示意图。
42.图中:1、中频电控系统;2、上料机构;201、驱动机构;202、轨道;203、上料台车;3、感应竖炉;301、石墨内衬;302、感应线圈;303、线圈间隙;304、绝缘层;305、炉料;306、炉衬隔热层;4、储氢供氢单元接口;5、富氢还原尾气回收单元接口;6、储球料斗;7、炉体预热段;8、石墨炉体加热还原段;9、炉体金属球团冷却段;10、炉体冷储室;11、出料装置;12、供氢及还原尾气氢回收系统。
具体实施方式
43.下面将结合本发明实施例中的附图,对本发明实施例中的技术方案进行清楚、完整地描述,显然,所描述的实施例仅仅是本发明一部分实施例,而不是全部的实施例。基于本发明中的实施例,本领域普通技术人员在没有做出创造性劳动前提下所获得的所有其他实施例,都属于本发明保护的范围。
44.实施例所采用的中频电热氢冶金竖炉装置参数如下:
[0045][0046][0047]
实施例中所使用的氢气,为工业氢气,含量为≥99.0%;
[0048]
中频电热氢冶金竖炉在首次开炉式时,炉体冷却段全部采用石墨块填充,在炉体“涡流感应”加热还原段及其上部炉体采用氧化铁质料球与石墨块混合填充;炉体、炉内各部位温度测量均采用红外测温装置在线实时监测;冷固球团的入炉水分<1%。
[0049]
实施例一
[0050]
请参阅图1-4,本发明提供一种技术方案:一种可实现零碳排放的还原铁粉清洁生产方法与装置:
[0051]
所使用的氧化铁质原料为工业氧化铁红,其化学成分如下:
[0052]
tfe%fe2o3%fe
2+
h2o%cl-%原料粒径mm球团粒径mm
68.8198.350093.611.74≤0.01910~25
[0053]
表1原料氧化铁红成分与粒度
[0054]
将中频电热氢冶金竖炉试验装置用表1中的氧化铁红冷固球团与体积比35%~40%的石墨块(粒径25mm~50mm)混合后从竖炉顶部储球料斗6装填入炉,每次开炉时,混合炉料305只装填至石墨炉体加热还原段8上部料线,装料后启动中频电控系统1并调整功率实施升温,在石墨炉体加热还原段8炉料305升温≤500℃之前,不向炉内通入氢气,待该段料温度升至>500℃之后,继续升温,并开始将0.3mpa~0.4mpa的氢气由炉体金属球团冷却段9下端外侧设置环形气室,通过周向设置的喷口正压进入炉体金属球团冷却段9内部(出炉尾气由炉顶负压吸入供氢及还原尾气氢回收系统12),同时开启炉顶旋转进料阀向炉内匀速布料,控制布料速度使炉体预热段7顶部料面温度始终保持≥150℃,待石墨炉体加热还原段8炉料305升温至850℃时,开启炉体金属球团冷却段9下部的旋转卸料阀向炉体冷储室10卸料,同时调整竖炉加热功率及控制卸料速度,使石墨炉体加热还原段8炉料305温度始终保持在840℃~860℃范围之内,在石墨炉体加热还原段8生成的金属化球团靠重力下行,直通进入竖炉下部的炉体金属球团冷却段9,该高温金属球团炉料305在炉体金属球团冷却段9由入炉氢气换热降温至≤200℃后,下行进入炉体冷储室10,继续自然冷却降温至≤100℃后排出炉体,氢气具有两种冶金作用:做清洁还原气体、做强制冷剂,通过在球料间的迷宫式穿行,对下行的金属化热球团进行换热冷却,自身被预热到840~860℃并在还原段将氧化铁质球团还原为金属化球团,该还原反应是吸热反应,还可对下行到炉体金属球团冷却段9的金属化热球团的进行深度还原,可对热金属球团进一步产生化学降温作用,使其得到强化冷却,还原h2气通用量控制在吨铁900nm3/t~1400nm3/t,炉料305在石墨炉体加热还原段8的停留时间100~180min,还原铁产量170kg/h~300kg/h,吨铁综合电耗530~960kwh,还原后的金属球团全铁tfe=97.84%~99.04%,磨细后的铁粉(细磨过程通入n2保护)最终获得的粉末冶金铁粉质量如下:松装密度2.51g/cm3,流动性34s/50g,压缩性6.49/cm3。
[0055]
实施例二
[0056]
请参阅图1-4,本发明提供一种技术方案:一种可实现零碳排放的还原铁粉清洁生产方法与装置:
[0057]
所使用的铁精矿为磁铁精矿,其化学成分如下:
[0058][0059]
表2原料高纯磁铁精矿成分与粒度
[0060]
将中频电热氢冶金竖炉试验装置用表2中的磁铁精矿冷固球团与体积比40%~45%的石墨块(粒径30mm~50mm)混合后从竖炉顶部储球料斗6装填入炉,每次开炉时,混合炉料305只装填至石墨炉体加热还原段8上部料线,装料后启动中频电控系统1并调整功率实施升温,在石墨炉体加热还原段8炉料305升温≤600℃之前,不向炉内通入氢气,待该段料温度升至>600℃之后,继续升温,并开始将0.3mpa~0.4mpa的氢气由炉体金属球团冷却
段9下端外侧设置环形气室,通过周向设置的喷口正压进入炉体金属球团冷却段9内部(出炉尾气由炉顶负压吸入供氢及还原尾气氢回收系统12),同时开启炉顶旋转进料阀向炉内匀速布料,控制布料速度使炉体预热段7顶部料面温度始终保持≥150℃,待石墨炉体加热还原段8炉料305升温至950℃时,开启炉体金属球团冷却段9下部的旋转卸料阀向炉体冷储室10卸料,同时调整竖炉加热功率及控制卸料速度,使石墨炉体加热还原段8炉料305温度始终保持在940℃~960℃范围之内,在石墨炉体加热还原段8生成的金属化球团靠重力下行,直通进入竖炉下部的炉体金属球团冷却段9,该高温金属球团炉料305在炉体金属球团冷却段9由入炉氢气换热降温至≤200℃后,下行进入炉体冷储室10,继续自然冷却降温至≤100℃后排出炉体,氢气具有两种冶金作用:做清洁还原气体、做强制冷剂,通过在球料间的迷宫式穿行,对下行的金属化热球团进行换热冷却,自身被预热到940~960℃并在石墨炉体加热还原段8将磁铁精矿球团还原为金属化球团,该还原反应是吸热反应,还可对下行到冷却段的金属化热球团的进行深度还原,可对热金属球团进一步产生化学降温作用,使其得到强化冷却,还原h2气通用量控制在吨铁900nm3/t~1300nm3/t,炉料305在石墨炉体加热还原段8的停留时间120~210min,还原铁产量150kg/h~270kg/h,吨铁综合电耗610~1070kwh,还原后的金属球团全铁tfe=97.61%~98.87%,磨细后的铁粉(细磨过程通入n2保护)最终获得的粉末冶金铁粉质量如下:松装密度2.65g/cm3,流动性32s/50g,压缩性6.61/cm3。
[0061]
实施例三
[0062]
请参阅图1-4,本发明提供一种技术方案:一种可实现零碳排放的还原铁粉清洁生产方法与装置:
[0063]
所使用的氧化铁质原料为铁鳞(钢坯或者钢材轧制过程产生的氧化铁剥离层),其化学成分如下:
[0064]
tfe%feo%cao%mgo%sio2%s%原料粒径mm球团粒径mm72.4553.640.410.120.730.079≤0.3520~35
[0065]
表3原料铁鳞成分与粒度
[0066]
将中频电热氢冶金竖炉试验装置用表3中的磁铁精矿冷固球团与体积比40%~45%的石墨块(粒径30mm~60mm)混合后从竖炉顶部储球料斗6装填入炉,每次开炉时,混合炉料305只装填至石墨炉体加热还原段8上部料线,装料后启动中频电控系统1并调整功率实施升温,在石墨炉体加热还原段8炉料305升温≤550℃之前,不向炉内通入氢气,待该段料温度升至>550℃之后,继续升温,并开始将0.3mpa~0.4mpa的氢气由炉体金属球团冷却段9下端外侧设置环形气室,通过周向设置的喷口正压进入炉体金属球团冷却段9内部(出炉尾气由炉顶负压吸入供氢及还原尾气氢回收系统12),同时开启炉顶旋转进料阀向炉内匀速布料,控制布料速度使炉体预热段7顶部料面温度始终保持≥150℃,待石墨炉体加热还原段8炉料305升温至920℃时,开启炉体金属球团冷却段9下部的旋转卸料阀向炉体冷储室10卸料,同时调整竖炉加热功率及控制卸料速度,使石墨炉体加热还原段8炉料305温度始终保持在900℃~930℃范围之内,在石墨炉体加热还原段8生成的金属化球团靠重力下行,直通进入竖炉下部的炉体金属球团冷却段9,该高温金属球团炉料305在冷却段由入炉氢气换热降温至≤200℃后,下行进入炉体冷储室10,继续自然冷却降温至≤100℃后排出炉体,氢气具有两种冶金作用:做清洁还原气体、做强制冷剂,通过在球料间的迷宫式穿行,
对下行的金属化热球团进行换热冷却,自身被预热到940~960℃并在石墨炉体加热还原段8将磁铁精矿球团还原为金属化球团,该还原反应是吸热反应,还可对下行到冷却段的金属化热球团的进行深度还原,可对热金属球团进一步产生化学降温作用,使其得到强化冷却,还原h2气通用量控制在吨铁900nm3/t~1200nm3/t,炉料305在石墨炉体加热还原段8的停留时间120~200min,还原铁产量160kg/h~280kg/h,吨铁综合电耗570~1000kwh,还原后的金属球团全铁tfe=97.30%~98.74%,磨细后的铁粉(细磨过程通入n2保护)最终获得的粉末冶金铁粉质量如下:松装密度2.68g/cm3,流动性31s/50g,压缩性6.71/cm3。
[0067]
实施例四
[0068]
请参阅图1-4,本发明提供一种技术方案:一种可实现零碳排放的还原铁粉清洁生产装置,包括中频电控系统1、上料机构2、感应竖炉3、出料装置11和供氢及还原尾气氢回收系统12,上料机构2包括驱动机构201、轨道202和上料台车203,上料机构2开设有驱动机构201,且驱动机构201上传动连接有轨道202,轨道202上安装有上料台车203;
[0069]
感应竖炉3包括石墨内衬301、感应线圈302、线圈间隙303、绝缘层304、炉料305和炉衬隔热层306,感应竖炉3内壁上开设有石墨内衬301,且感应竖炉3外部盘绕有感应线圈302,感应线圈302上开设有绝缘层304,感应线圈302之间设置有线圈间隙303,感应竖炉3内部设置有炉料305,石墨内衬301外侧包裹有炉衬隔热层306;
[0070]
感应竖炉3内部开设有石墨炉体加热还原段8,且石墨炉体加热还原段8上方设置有炉体预热段7,炉体预热段7上方连接有富氢还原尾气回收单元接口5,炉体预热段7上方连接有储球料斗6,且储球料斗6侧面设置有上料机构2,感应竖炉3与中频电控系统1之间的连接方式为电性连接,石墨炉体加热还原段8下方设置有炉体金属球团冷却段9,炉体金属球团冷却段9底部设置有储氢供氢单元接口4,且炉体金属球团冷却段9下方开设有炉体冷储室10,炉体冷储室10下方安装有出料装置11;
[0071]
储氢供氢单元接口4的输入端连接有供氢及还原尾气氢回收系统12,储氢供氢单元接口4输出端连接有炉体金属球团冷却段9,富氢还原尾气回收单元接口5的输出端设置有供氢及还原尾气氢回收系统12。
[0072]
中频电控系统1的频率范围为100hz-1450h,感应线圈302的线圈间隙303间距为15mm~60mm,并且感应竖炉3的功率控制在大于等于50kw。
[0073]
感应竖炉3呈中空圆柱形,感应竖炉3中石墨内衬301的壁厚为50mm~200mm,并且石墨内衬301由石墨电极经机加工去芯制取。
[0074]
石墨内衬301的高度可有单个或数个同等内径与壁厚的中空圆柱体链接构成或采用异形石墨砖环砌制成,且石墨内衬301圆柱体的链接端面呈凹凸状设置。
[0075]
尽管参照前述实施例对本发明进行了详细的说明,对于本领域的技术人员来说,其依然可以对前述各实施例所记载的技术方案进行修改,或者对其中部分技术特征进行等同替换,凡在本发明的精神和原则之内,所作的任何修改、等同替换、改进等,均应包含在本发明的保护范围之内。