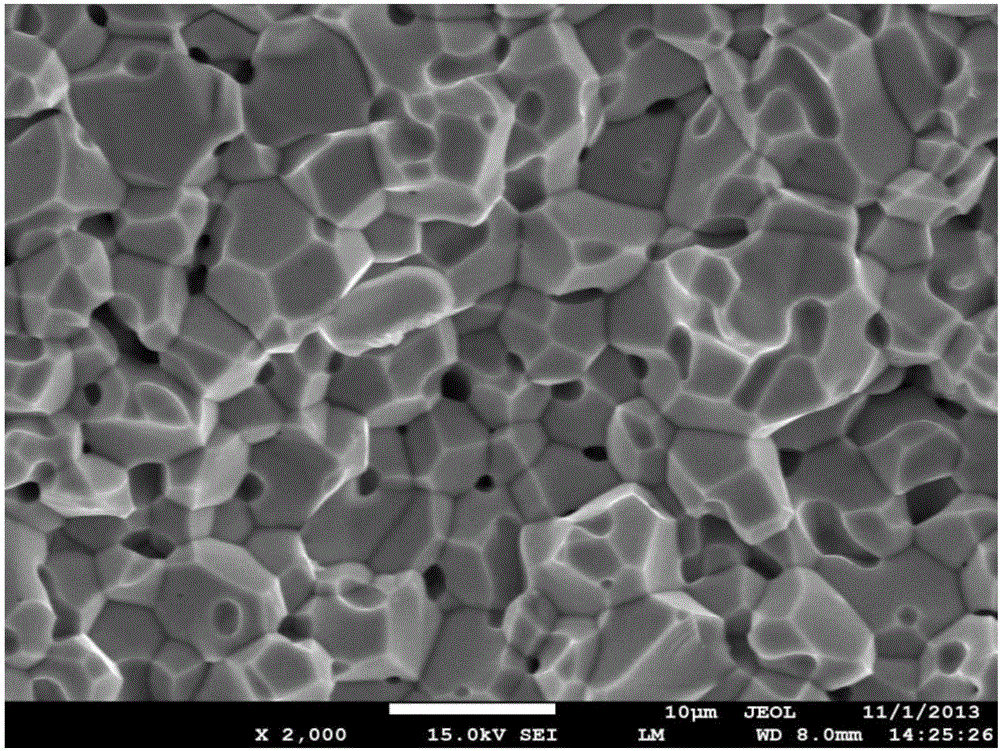
本发明属于高性能软磁铁氧体材料先进制备与应用领域,涉及一种宽温(25℃~140℃)低功耗锰锌功率铁氧体材料及其基于Na掺杂微观结构调控的制备工艺。
背景技术:
:锰锌铁氧体是一类广泛应用于通讯、新能源、汽车电子、电磁兼容、IT、家电、绿色照明以及国防科技等领域中的氧化物软磁材料。在新能源汽车车载充电机、充电站/桩、移动通信基站等户外电子设备中,变压器、电感器、扼流圈等磁性元器件通常在很宽的环境温度范围内工作。许多输出功率变化的开关电源,变压器的温升亦会随着负载的轻重而显著变化,传统的锰锌低功耗铁氧体材料的功耗随温度的变化很大,仅能在很窄的温度范围内实现低功耗。为了追求高效率、低温升、高功率密度和高可靠性,希望使用的磁性元器件在很宽的工作温度范围内能够保持低功耗。近十多年来,以TDK公司PC95材料为代表的国内外一系列宽温低功耗铁氧体材料获得了广泛的应用,但是对于部分特殊应用而言,这一代材料在更高(120~140℃)、更低(室温及以下)的温度区间功耗仍然偏高。市场迫切需要具有更平坦的功耗~温度特性曲线的新一代宽温低功耗铁氧体材料。对于软磁材料制备厂商而言,也希望开发更多的工艺调控手段,来比较容易而稳定地制备高性能的铁氧体材料。研究表明,铁氧体材料各项磁性能参数存在着复杂的相互制约关系,强烈地依赖于材料的化学组成及微观结构,这些又取决于材料的配方及制备工艺。锰锌铁氧体通过化学组成、微量添加剂掺杂及微观结构的调控可实现宽温低功耗,同时兼顾较高的的起始磁导率和饱和磁通密度的要求。由于受到磁晶各向异性常数K1强温度依赖特性的影响,MnZn铁氧体材料仅能在磁晶各向异性常数K1补偿为零的温度点附近实现低磁滞损耗和高磁导率。CN102693802A发明公开了一种宽温MnZn功率铁氧体材料及其制备方法,由主成分和辅助成分组成,其中主成分及含量以氧化物计算为:Fe2O3为52.1~52.6mol%、ZnO为9~11.5mol%、MnO为余量;辅助成分为CaCO3、ZrO2、Nb2O5、SnO2和Co2O3。该材料温度在25~140℃范围损耗比较低,但饱和磁通密度偏低,且缺乏Na作为微量添加物对微观结构的调控作用。CN103588472A发明公开了一种宽温MnZn功率铁氧体材料及其制备方法,由主成分和辅助成分组成,其中所述主成分的各组分的摩尔百分比为:Fe2O3为52.45~52.6mol%,ZnO为9.2~9.7mol%,MnO为余量;按占主成分总重量计,辅助成分各组分含量为:CaCO3:0.05~0.06%,ZrO2:0.02~0.03%,Nb2O5:0.03~0.04%,Co2O3:0.35~0.4%。该材料在25~140℃温度范围内损耗较低,但缺乏Na作为微量添加物对微观结构的调控作用。CN102693803A发明公开了一种宽温低损耗MnZn功率铁氧体材料及其制备方法。由主成分和辅助成分组成,其中主成分及含量以氧化物计算为:Fe2O3:51~54mol%、MnO:35~38mol%、ZnO:9~13mol%;按主成分总重量计的辅助成分为:CaCO3:0.03~0.1wt%、SnO2:0.02~0.1wt%、Nb2O5:0.01~0.04wt%、ZrO2:0.01~0.05wt%、Co2O3:0.1~0.5wt%中的四种以上。该材料缺乏120℃以上的损耗信息,且缺乏Na作为微量添加物对微观结构的调控作用。技术实现要素:本发明目的是提出一种高性能宽温低功耗锰锌铁氧体材料及其制备工艺。本发明的技术方案是,一种宽温低功耗锰锌铁氧体材料,其主成分的各组分的摩尔百分比为:Fe2O3为52.7~53.5mol%,ZnO为8.6~9.6mol%,MnO为余量;按占主成分总重量计,其辅助成分各组分含量为:CaCO3为0.03~0.04%,Nb2O5为0.02~0.03%,Co2O3为0.4~0.5%,SnO2为0.05~0.15%,NaO2为0.0074~0.022%(以碳酸氢钠的形式添加)。进一步,Na以易溶于水的碳酸氢钠(NaHCO3)的形式进行添加。添加量按占主成分总重量计为0.01~0.03%。本发明中,称取主成分各组分,砂磨混合后进行喷雾干燥,再在回转窑内进行预烧,向预烧料中加入辅助成分各组分,进行砂磨粉碎,再进行喷雾干燥造粒,然后压制成坯件,把坯件在氮气保护气氛下烧结后获得铁氧体磁心;所述烧结过程包括升温阶段、恒温阶段和降温阶段;烧结升温温度为1200±10℃,然后降温,氧含量控制在0.8~1.0%,保温45~75分钟;再降温至920℃以下时,控制氧含量在0.005%以下,直到降至室温。烧结升温温度为1200±10℃,保持时间为200~280分钟,氧含量控制在3~5%。上述成份的材料在烧结降温阶段的1200℃进行控制气氛的保温处理。本发明的铁氧体材料在25~140℃温度范围内有很低的功耗,同时兼有较高的饱和磁通密度和磁导率。所述宽温低功耗锰锌铁氧体材料在25~140℃温度范围内,尤其是在100~140℃高温区内,功耗较现有大多数低功耗锰锌铁氧体材料更低。在100kHz、200mT条件下的功耗Pcv为:25℃Pcv≤320kW/m360℃Pcv≤310kW/m3100℃Pcv≤300kW/m3120℃Pcv≤320kW/m3140℃Pcv≤380kW/m3在1194A/m、50Hz条件下的饱和磁通密度Bs为:25℃Bs≥540mT100℃Bs≥420mT在25℃下的起始磁导率μi为3300±20%。所述的宽温低功耗锰锌铁氧体材料的制备方法为:称取主成分各组分,其摩尔百分比为:Fe2O3为52.7~53.5mol%,ZnO为8.6~9.6mol%,MnO为余量;经砂磨混合后进行喷雾干燥,再在回转窑内进行预烧,预烧温度为900±30℃,时间为120±30分钟;在预烧料中加入按主成分总重量计的辅助成分,其含量为:CaCO3为0.03~0.04%,Nb2O5为0.02~0.03%,Co2O3为0.4~0.5%,SnO2为0.05~0.15%,NaO2为0.0074~0.022%(以碳酸氢钠的形式添加);进行砂磨粉碎,时间为120±30分钟,砂磨料平均粒径约为0.9μm;对此砂磨料进行喷雾造粒,用成型机压制成坯件;把坯件在氮气保护气氛下烧结,烧结过程包括升温阶段、恒温阶段和降温阶段。恒温阶段烧结温度为1280±20℃,时间为200~280分钟,氧含量控制在3~5%;降温至1200±10℃时的氧含量控制在0.8~1.0%,并保温45~75分钟;再降温至920℃以下时,控制氧含量在0.005%以下,直到降至室温。预烧的条件是,Fe2O3、ZnO、MnO经砂磨混合和喷雾干燥后预烧,预烧温度为900±30℃,时间为120±30分钟;在预烧料中加入按比例称取的辅助成分原料,按主成分总重量计的辅助成分含量为CaCO3:0.04%,Nb2O5:0.03%,Co2O3:0.4%,SnO2:0.1%,NaHCO3:0.02%,进行砂磨粉碎,时间为120±30分钟,砂磨料平均粒径为0.9μm;然后对此砂磨料进行喷雾造粒,用成型机压制试样;制备MnZn铁氧体。由于受到磁晶各向异性常数K1强温度依赖特性的影响,锰锌铁氧体材料仅能在K1补偿为零的温度点附近实现低磁滞损耗和高磁导率。本发明基于深入研究影响磁晶各异性常数K1温度依赖特性的机理和其它各种影响因素,通过对材料化学组成、微量添加剂掺杂、烧结工艺及微观结构的深入研究,创新性的地将磁晶各向异性常数K1补偿为零的温度由通常单一温度点分成高、低两个温度点,从而大大降低了材料磁晶各向异性对温度的依赖性,使锰锌铁氧体材料在较宽的温度范围内具有平坦的功耗~温度特性。软磁铁氧体材料功耗Pcv由磁滞损耗Ph、涡流损耗Pe和剩余损耗Pr三部分构成。通常认为在500kHz以下频段,Pr可以忽略,所以有Pcv=Ph+Pe。本发明基于大量研究表明,锰锌铁氧体材料功耗与多晶材料的微观结构有密切的关系。经烧结产生均匀、细密的晶粒,气孔较少且分布在晶界,磁心密度较高,这样的微观结构不仅有利于在外加磁场作用下的畴壁位移和磁畴转动,减少了磁化所需能量,即减少了磁滞损耗,同时也减少了交变磁场在晶粒内感生出的涡流,从而减少了涡流损耗。但是,形成均匀而细密的晶粒和实现高密度在烧结工艺上往往是矛盾的。通过掺加有助于细化晶粒的微量添加剂,如Na等,易于得到均匀、细密且密度较高的微观结构,从而低磁滞损耗及涡流损耗。另外,通过烧结不同阶段气氛中氧分压(氧含量)的适当控制,特别是在降温阶段特定温度下进行控制气氛中氧含量的保温处理,有利于高电阻物质如CaSiO3等在晶界处偏析,从而提高晶界电阻率,降低材料的涡流损耗。本发明的有益效果,该宽温低功耗锰锌铁氧体材料尤其适用于车载、户外等环境温度变化很大的应用场合,如新能源汽车车载充电机、充电站/桩、车载DC-DC变换器、移动通信基站、屋顶光伏微型逆变器等。该材料也适用于高功率密度模块式开关电源,对器件的小型化与高密度集成具有重要的应用价值。在制备技术上,本发明利用微量添加物Na对烧结形成的材料微观结构的调控作用,得到细密、均匀且密度较高的微观结构,降低了材料的磁滞损耗及涡流损耗,同时提高了饱和磁通密度;通过在降温阶段特定温度下进行控制气氛中氧含量的保温处理,提高了材料的电阻率,从而降低了涡流损耗。本发明能够解决宽温低功耗铁氧体材料制备和应用方面的部分现有技术问题,当然预料处理工艺也有所不同,对最终产品性能也有着意义。附图说明图1未掺加Na试样的微观结构;图2本发明掺加0.02%NaHCO3试样的微观结构;图3实施例2和比较例2样品功耗Pcv与温度的关系(功耗随温度变化的曲线);图4实施例2试样磁滞损耗Ph、涡流损耗Pe与温度的关系;图5实施例3和比较例3样品涡流损耗Pe与温度的关系。具体实施方式实施例1:按下述主成分含量称取主成分原料:Fe2O3含量为53.1mol%、ZnO含量为9.2mol%、MnO含量为37.7mol%,经砂磨混合和喷雾干燥后预烧,预烧温度为900℃,时间为120分钟。在预烧料中加入按比例称取的辅助成分原料。按主成分总重量计的辅助成分含量为:CaCO3:0.04%,Nb2O5:0.03%,Co2O3:0.4%,SnO2:0.1%,NaHCO3:0.02%,进行砂磨粉碎,时间为120分钟,砂磨料平均粒径为0.9μm。然后对此砂磨料进行喷雾造粒,用成型机压制H25/15/10环形试样。比较例1:按下述主成分含量称取主成分原料:Fe2O3含量为53.1mol%、ZnO含量为9.2mol%、MnO含量为37.7mol%,经砂磨混合和喷雾干燥后预烧,预烧温度为900℃,时间为120分钟。在预烧料中加入按比例称取的辅助成分原料。按主成分总重量计的辅助成分含量为CaCO3:0.04%,Nb2O5:0.03%,Co2O3:0.4%,SnO2:0.1%,进行砂磨粉碎,时间为120分钟,砂磨料平均粒径为0.9μm。然后对此砂磨料进行喷雾造粒,用成型机压制H25/15/10环形试样。将实施例1和比较例1中的环形试样在相同条件下烧结,烧结温度为1280℃,时间为240分钟,氧含量控制在4%,然后降温。降温至1200℃时的氧含量控制在0.8~1.0%,并保温60分钟,再降温至920℃以下,控制氧含量在0.005%以下直到降至室温。如此得到的铁氧体环形磁心样品特性比较结果见表1。表1从表1可以看出,通过加入Na,材料的功耗明显降低,同时饱和磁通密度明显增高,其主要原因是在烧结过程中Na离子可以改善材料的微观结构,均匀化及细化晶粒,可以在较低的烧结温度下得到较高的烧结密度,有效地降低了材料的涡流损耗,其微观结构比较如图1及图2。实施例2:按下述主成分含量称取主成分原料:Fe2O3含量为53.1mol%、ZnO含量为9.2mol%、MnO含量为37.7mol%,经砂磨混合和喷雾干燥后预烧,预烧温度为900℃,时间为120分钟;在预烧料中加入按比例称取的辅助成分原料,按主成分总重量计的辅助成分含量为CaCO3:0.04%,Nb2O5:0.03%,Co2O3:0.4%,SnO2:0.1%,NaHCO3:0.02%,进行砂磨粉碎,时间为120分钟,砂磨料平均粒径为0.9μm。然后对此砂磨料进行喷雾造粒,用成型机压制H25/15/10环形试样。比较例2:按下述主成分含量称取主成分原料:Fe2O3含量为53.1mol%、ZnO含量为9.2mol%、MnO含量为37.7mol%,经砂磨混合和喷雾干燥后预烧,预烧温度为900℃,时间为120分钟;在预烧料中加入按比例称取的辅助成分原料(按主成分总重量计的辅助成分含量为:CaCO3:0.04%,Nb2O5:0.03%,Co2O3:0.4%,NaHCO3:0.02%,进行砂磨粉碎,时间为120分钟,砂磨料平均粒径为0.9μm,然后对此砂磨料进行喷雾造粒,用成型机压制H25*15*10环形试样。将实施例2和比较例2中的环形试样在相同条件下烧结,烧结温度为1280℃,时间为240分钟,氧含量控制在4%。然后降温,降温至1200℃时的氧含量控制在0.8~1.0%,并保温60分钟,再降温至920℃以下,控制氧含量在0.005%以下直到降至室温。如此得到的铁氧体环形磁心样品特性比较结果见表2。表2功耗随温度变化的曲线见图3。图3实施例2和比较例2样品功耗Pcv与温度的关系。从表2及图3可以看出,通过加入0.1%的SnO2,材料功耗与温度关系曲线形状有所改变,低温及高温的功耗同时降低。通过对实施例2试样的功耗构成进行分离分析,结果如图4。图4实施例2试样磁滞损耗Ph、涡流损耗Pe与温度的关系;从图4可以看出,材料的磁滞损耗Ph呈现相对平坦的温度特性,并出现高、低温两个功耗最低点,这对应K1的两个补偿零点。实施例的涡流损耗Pe也比较低。实施例3:按下述主成分含量称取主成分原料:Fe2O3含量为53.1mol%、ZnO含量为9.2mol%、MnO含量为37.7mol%,经砂磨混合和喷雾干燥后预烧,预烧温度为900℃,时间为120分钟;在预烧料中加入按比例称取的辅助成分原料(按主成分总重量计的辅助成分含量为:CaCO3:0.04%,Nb2O5:0.03%,Co2O3:0.4%,SnO2:0.1%,NaHCO3:0.02%,进行砂磨粉碎,时间为120分钟,砂磨料平均粒径为0.9μm。然后对此砂磨料进行喷雾造粒,用成型机压制H25/15/10环形试样,烧结降温至1200℃时保温60分钟。比较例3:按下述主成分含量称取主成分原料:Fe2O3含量为53.1mol%、ZnO含量为9.2mol%、MnO含量为37.7mol%,经砂磨混合和喷雾干燥后预烧,预烧温度为900℃,时间为120分钟;在预烧料中加入按比例称取的辅助成分原料(按主成分总重量计的辅助成分含量为:CaCO3:0.04%,Nb2O5:0.03%,Co2O3:0.4%,SnO2:0.1%,NaHCO3:0.02%,进行砂磨粉碎,时间为120分钟,砂磨料平均粒径为0.9μm。然后对此砂磨料进行喷雾造粒,用成型机压制H25/15/10环形试样,烧结降温至1200℃时不做保温处理。试样电阻率测量结果表明,在1200℃保温60分钟可提高材料电阻率,从而降低涡流损耗,结果如表3。表3电阻率(Ω·m)实施例36.7比较例35.0实施例3和比较例3样品的涡流损耗比较如图5。当前第1页1 2 3