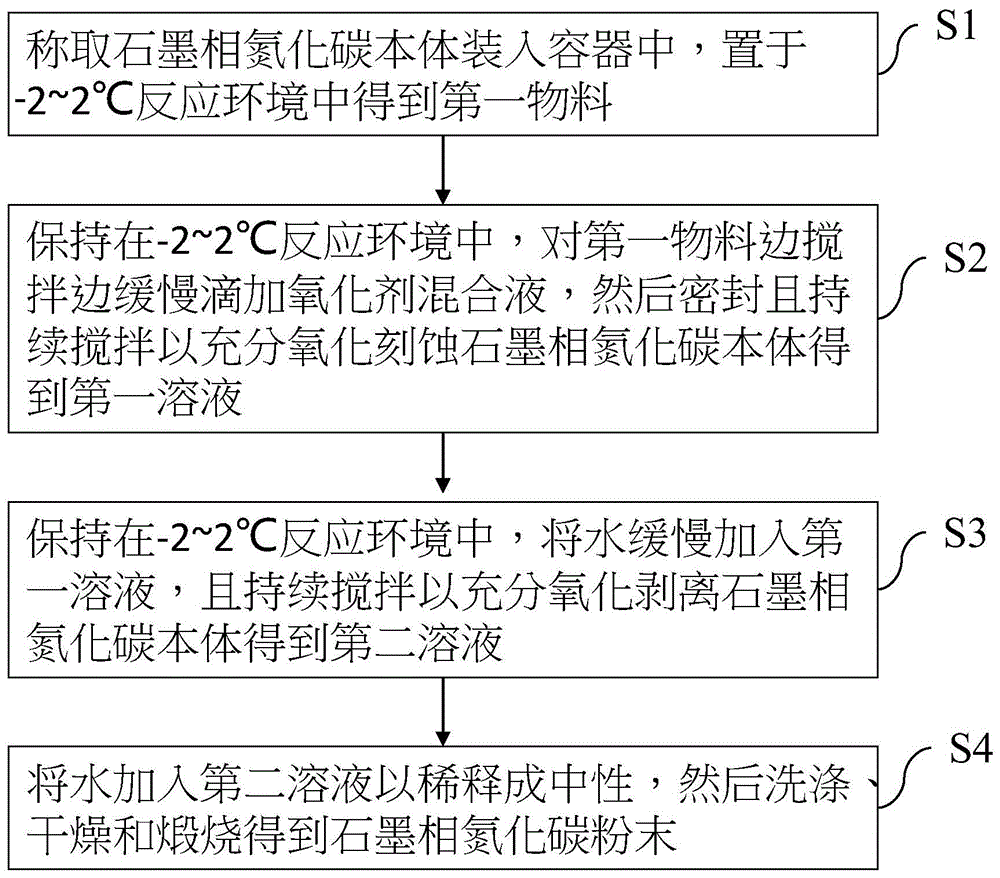
本发明涉及材料
技术领域:
,特别是指一种石墨相氮化碳的制备方法。
背景技术:
:本部分旨在为权利要求书中陈述的本发明的实施方式提供背景或上下文。此处的描述不因为包括在本部分中就承认是现有技术。石墨相氮化碳(cn)作为一种易于制备、分子结构可调、可见光响应且不含金属的光催化剂在光催化水裂解产氢、二氧化碳还原及有机污染物降解等领域受到研究者的广泛关注,本体的cn具有类石墨相的二维层状结构,由于层状堆积cn比表面积较小,反应活性位点少,催化活性低;不同于石墨烯的п电子共轭体系,cn的基本结构组成单元三嗪环或者七嗪环中,氮原子对称替代了碳六边形中的碳,导致cn为缺п电子共轭体系,材料电导率低,光催化反应过程中载流子复合率较高,光生载流子迁移及利用率差。技术实现要素:鉴于以上内容,有必要提供解决上述问题的一种石墨相氮化碳的制备方法。本发明提供的技术方案为:一种石墨相氮化碳的制备方法,包括以下步骤:称取石墨相氮化碳本体装入容器中,置于-2~2℃反应环境中得到第一物料;及保持在-2~2℃反应环境中,对第一物料边搅拌边缓慢滴加氧化剂混合液,然后密封且持续搅拌以充分氧化刻蚀石墨相氮化碳本体得到第一溶液;将水缓慢加入第一溶液,且持续搅拌以充分氧化剥离石墨相氮化碳本体得到第二溶液;将水加入第二溶液以稀释成中性,然后洗涤、干燥和煅烧得到石墨相氮化碳粉末。进一步地,所述氧化剂混合液包括双氧水与硝酸的混合液。进一步地,所述双氧水与所述硝酸的体积比为10:1。进一步地,所述石墨相氮化碳本体用量为500mg,所述氧化剂混合液用量范围为2.5-12.5ml。进一步地,所述对第一物料边搅拌边缓慢滴加氧化剂混合液,然后密封且持续搅拌以充分氧化刻蚀石墨相氮化碳本体得到第一溶液的步骤包括:每毫升所述氧化剂混合液的滴加时长不少于24分钟;所述持续搅拌的时长为12小时。进一步地,所述将水缓慢加入第一溶液,且持续搅拌以充分氧化剥离石墨相氮化碳本体得到第二溶液的步骤包括:所述水与所述氧化剂混合液的体积比为1:1,每毫升所述水的滴加时长不少于24分钟;所述持续搅拌的时长为12小时。进一步地,所述称取石墨相氮化碳本体装入容器中,置于-2~2℃反应环境中得到第一物料的步骤包括:置于-2~2℃反应环境中静置预设时长,得到第一物料,其中预设时长不少于30min。进一步地,在所述然后洗涤、干燥和煅烧得到石墨相氮化碳粉末的步骤中,所述洗涤采用去离子水进行若干次清洗。进一步地,在所述然后洗涤、干燥和煅烧得到石墨相氮化碳粉末的步骤中,所述干燥包括在温度为45℃的真空环境下处理。进一步地,在所述然后洗涤、干燥和煅烧得到石墨相氮化碳粉末的步骤中,所述煅烧的过程中升温速率为2-10℃/min,煅烧温度为520℃,煅烧保温时长为4小时。与现有技术相比,本发明提供一种操作简便、低温缓慢氧化刻蚀与剥离协同的制备方法,cn氧化刻蚀、剥离过程维持在低温(-2~2℃)环境中,能够有效调节cn的氧化速率,增大其比表面积,增加参与光催化反应的活性位点;低温环境中加水且搅拌,使得水力剪切力促进cn层状结构的剥离,改性后的cn由于氧化刻蚀剥离的协同作用,孔道结构增多,比表面积增大,层数减少,电阻率显著降低,有助于光生载流子的分离,光催化活性显著提高。附图说明下面结合附图和具体实施方式对本发明作进一步详细的说明。图1为本发明一较佳实施方式中石墨相氮化碳的制备流程图。图2为本发明实施例中cn本体的扫描电子显微镜(sem)图。图3为本发明实施例得到的低温氧化改性后cn的sem图。图4是本发明实施例的cn本体和改性后cn的n2吸附脱附等温曲线。图5a是本发明实施例的改性后cn的孔径分布曲线。图5b是本发明实施例的cn本体的孔径分布曲线。图6是本发明实施例的cn本体和改性后cn的光催化降解罗丹明b(rhb)的性能。附图标记说明:无。如下具体实施方式将结合上述附图进一步说明本发明实施例。具体实施方式为了能够更清楚地理解本发明实施例的上述目的、特征和优点,下面结合附图和具体实施方式对本发明进行详细描述。需要说明的是,在不冲突的情况下,本申请的实施方式中的特征可以相互组合。在下面的描述中阐述了很多具体细节以便于充分理解本发明实施例,所描述的实施方式仅是本发明一部分实施方式,而不是全部的实施方式。基于本发明中的实施方式,本领域普通技术人员在没有做出创造性劳动前提下所获得的所有其他实施方式,都属于本发明实施例保护的范围。本文中“氧化刻蚀”:是指cn本体在强酸混合液中,在强氧化剂存在条件下,部分c,n原子被氧化成氧化物,导致cn的分子结构中部分c,n原子缺失,形成缺陷及孔结构。本文中“氧化剥离”:是指在强氧化剂存在条件下,磁力搅拌提供的水力剪切力有助于二维cn层状结构的剥离。除非另有定义,本文所使用的所有的技术和科学术语与属于本发明实施例的
技术领域:
的技术人员通常理解的含义相同。本文中在本发明的说明书中所使用的术语只是为了描述具体的实施方式的目的,不是旨在于限制本发明实施例。请参阅图1,为本发明较佳实施方式中石墨相氮化碳的制备流程,具体如下:步骤s1:称取石墨相氮化碳本体装入容器中,置于-2~2℃反应环境中得到第一物料。本实施方式中,本步骤还包括:置于-2~2℃反应环境中静置预设时长,得到第一物料,其中预设时长不少于30min。该预置30min是为了让烧杯容器和样品(cn本体)的温度降低,不预置对氧化刻蚀效果有影响,预置更长时间也可以,采用其他快速降温方式短时间达到降温至预设温度范围也可以,本发明对此不作限定。其中,-2~2℃反应环境可以采用冰水浴,用于减小浓酸及强氧化剂对cn本体的氧化刻蚀速率,温度在-2~2℃范围内变化影响不大。本实施方式中,cn本体为三聚氰胺热聚合得到。在其他实施方式中也可以由其他原料得到cn本体,如氰胺,二氰二胺,尿素等,在此不作限定。步骤s2:保持在-2~2℃反应环境中,对第一物料边搅拌边缓慢滴加氧化剂混合液,然后密封且持续搅拌以充分氧化刻蚀石墨相氮化碳本体得到第一溶液。本实施方式中,所述氧化剂混合液包括双氧水与硝酸的混合液;所述双氧水与所述硝酸的体积比为10:1,所述石墨相氮化碳本体用量为500mg,所述氧化剂混合液用量范围为2.5-12.5ml。本实施方式中,每毫升所述氧化剂混合液的滴加时长不少于24分钟。该步骤中,当cn本体为500mg时,优选持续搅拌的时长为12小时,若搅拌时间过短cn本体被氧化的不够充分,若搅拌时间过长会导致处理后的材料缺陷过多,光催化活性反而降低。如此控制的原因在于缓慢低温氧化刻蚀,有助于增大比表面积,形成三维孔洞结构,活性位点增加。其中,密封步骤作用在于保证反应体系不受污染。步骤s3:保持在-2~2℃反应环境中,将水缓慢加入第一溶液,且持续搅拌以充分氧化剥离石墨相氮化碳本体得到第二溶液。本实施方式中,所述水包括去离子水,所述水与所述氧化剂混合液的体积比为1:1,每毫升所述水的滴加时长不少于24分钟;本实施方式中,当cn本体为500mg时,优选的持续搅拌时间为12小时,与上一步骤类似,时间过短剥离会不够充分,时间过长对光催化活性不利。本发明在缓慢低温氧化12小时并缓慢加水稀释,cn本体除在低温强氧化作用下被氧化刻蚀,强氧化剂条件下搅拌过程水力剪切力还能实现层状结构的有效剥离,cn本体在层数减小之后材料电阻率显著下降,改性后材料的光催化活性显著提高。在其他实施方式中,水还可以是蒸馏水、纯水等。步骤s4:将水加入第二溶液以稀释成中性,然后洗涤、干燥和煅烧得到石墨相氮化碳粉末。本步骤中第二溶液加入大量去离子水后得到白色粉末均匀分散的溶液,也是一种澄清白色溶液;水洗去除上层清液可以得到白色沉淀;洗涤的作用是去除体系中过量的酸,直至上层清液ph为中性。在其他实施方式中,水还可以是蒸馏水、纯水等。本实施方式中,所述洗涤采用去离子水进行若干次清洗;所述干燥包括在温度为45℃的真空环境下处理,在其他实施方式中,也可以是普通烘箱干燥;所述然后洗涤、干燥和煅烧得到石墨相氮化碳粉末的步骤中,所述煅烧的过程中升温速率为2-10℃/min,煅烧温度为520℃,煅烧保温时长为4小时。上述方法提供一种操作简便、低温缓慢氧化刻蚀剥离的策略,有效提高材料的比表面积,显著降低材料电阻率,得到光催化性能极大提高的改性cn。下面举例对本发明的石墨相氮化碳粉末的制备过程进行说明,并就得到的产物进行性能检测。实验原料:环境温度25℃,1个大气压;水,密度1.00g/ml,分子量18g/mol;三聚氰胺,熔点250℃,密度1.574g/ml,溶解度3.1g/l,分子量126g/mol;h2o2,密度1.13g/ml,分子量34.01g/mol;hno3,密度1.42g/ml,分子量63.01g/mol。实施例1:称量500mgcn(本体)倒入50ml烧杯中,置于冰水浴中30min,开启磁力搅拌(300转/min),向烧杯中缓慢滴加2.5mlh2o2与hno3的混合溶液(滴加过程持续1h),密封后冰水浴中搅拌12h,得到白色粘稠溶液。向混合溶液缓慢滴加2.5ml去离子水(滴加过程持续1h),冰水浴中磁力搅拌12h,得到澄清白色溶液。向体系中加入大量去离子水至体系ph为中性,去离子水洗涤离心3次后置于45℃真空烘箱干燥,得到白色粉末固体。将样品转移至25ml的带盖坩埚中煅烧样品,升温速率2℃/min至520℃保温4小时,自然冷却后得到浅棕色固体粉末,充分研磨后水洗干燥后得到改性的cn样品。本实施例中cn本体及改性后的cn的sem图分别如图2和图3所示,可以看出,改性后的cn仍为层状堆积结构,由于氧化刻蚀样品表面形成多孔结构。图4示出了cn本体及改性后的cn的n2吸附脱附等温曲线,可见,cn本体的n2吸附脱附等温曲线始端偏向横坐标轴(指相对压力),表明cn本体与氮作用力弱,而改性后的cn的n2吸附脱附等温曲线始端偏向纵坐标轴(指吸附量),表明改性后cn与氮有较强的作用力,这是由于改性形成的较多微孔内强吸附势使得材料在低压端(相对压力0.0-0.1)出现氮气的强吸附。而且改性后cn的吸附量明显高于cn本体的;越靠近高压端,吸附量的差距越大,如此可见,氧化刻蚀剥离协同形成的微孔结构改进有效改善了cn的吸附能力。从图5a和图5b分别示出的cn本体及改性后的cn的孔径分布曲线可以看出,本发明的cn材料相比cn本体在同一孔径下吸(脱)附量要大3倍以上,换言之,本发明的cn材料相比cn本体的比表面积大,吸(脱)附能力强。实施例2:称量500mgcn倒入50ml烧杯中,置于冰水浴中30min,开启磁力搅拌(300转/min),向烧杯中缓慢滴加5mlh2o2与hno3的混合溶液(滴加过程持续2h),密封后冰水浴中搅拌12h,得到白色粘稠溶液。向混合溶液缓慢滴加5ml去离子水(滴加过程持续2h),冰水浴中磁力搅拌12h,得到澄清白色溶液。向体系中加入大量去离子水至体系ph为中性,去离子水洗涤离心3次后置于45℃真空烘箱干燥,得到白色粉末固体。将样品转移至25ml的带盖坩埚中煅烧样品,升温速率2℃/min至520℃保温4小时,自然冷却后得到浅棕色固体粉末,充分研磨后水洗干燥后得到改性的cn样品。实施例3:称量500mgcn倒入50ml烧杯中,置于冰水浴中30min,开启磁力搅拌(300转/min),向烧杯中缓慢滴加7.5mlh2o2与hno3的混合溶液(滴加过程持续3h),密封后冰水浴中搅拌12h,得到白色粘稠溶液。向混合溶液缓慢滴加7.5ml去离子水(滴加过程持续3h),冰水浴中磁力搅拌12h,得到澄清白色溶液。向体系中加入大量去离子水至体系ph为中性,去离子水洗涤离心3次后置于45℃真空烘箱干燥,得到白色粉末固体。将样品转移至25ml的带盖坩埚中煅烧样品,升温速率2℃/min至520℃保温4小时,自然冷却后得到浅棕色固体粉末,充分研磨后水洗干燥后得到改性的cn样品。实施例4:称量500mgcn倒入50ml烧杯中,置于冰水浴中30min,开启磁力搅拌(300转/min),向烧杯中缓慢滴加10mlh2o2与hno3的混合溶液(滴加过程持续4h),密封后冰水浴中搅拌12h,得到白色粘稠溶液。向混合溶液缓慢滴加10ml去离子水(滴加过程持续4h),冰水浴中磁力搅拌12h,得到澄清白色溶液。向体系中加入大量去离子水至体系ph为中性,去离子水洗涤离心3次后置于45℃真空烘箱干燥,得到白色粉末固体。将样品转移至25ml的带盖坩埚中煅烧样品,升温速率2℃/min至520℃保温4小时,自然冷却后得到浅棕色固体粉末,充分研磨后水洗干燥后得到改性的cn样品。实施例5:称量500mgcn倒入50ml烧杯中,置于冰水浴中30min,开启磁力搅拌(300转/min),向烧杯中缓慢滴加12.5mlh2o2与hno3的混合溶液(滴加过程持续5h),密封后冰水浴中搅拌12h,得到白色粘稠溶液。向混合溶液缓慢滴加12.5ml去离子水(滴加过程持续5h),冰水浴中磁力搅拌12h,得到澄清白色溶液。向体系中加入大量去离子水至体系ph为中性,去离子水洗涤离心3次后置于45℃真空烘箱干燥,得到白色粉末固体。将样品转移至25ml的带盖坩埚中煅烧样品,升温速率2℃/min至520℃保温4小时,自然冷却后得到浅棕色固体粉末,充分研磨后水洗干燥后得到改性的cn样品。实施例6:称量500mgcn倒入50ml烧杯中,置于冰水浴中30min,开启磁力搅拌(300转/min),向烧杯中缓慢滴加5mlh2o2与hno3的混合溶液(滴加过程持续2h),密封后冰水浴中搅拌12h,得到白色粘稠溶液。向混合溶液缓慢滴加5ml去离子水(滴加过程持续2h),冰水浴中磁力搅拌12h,得到澄清白色溶液。向体系中加入大量去离子水至体系ph为中性,去离子水洗涤离心3次后置于45℃真空烘箱干燥,得到白色粉末固体。将样品转移至25ml的带盖坩埚中煅烧样品,升温速率5℃/min至520℃保温4小时,自然冷却后得到浅棕色固体粉末,充分研磨后水洗干燥后得到改性的cn样品。实施例7:称量500mgcn倒入50ml烧杯中,置于冰水浴中30min,开启磁力搅拌(300转/min),向烧杯中缓慢滴加5mlh2o2与hno3的混合溶液(滴加过程持续2h),密封后冰水浴中搅拌12h,得到白色粘稠溶液。向混合溶液缓慢滴加5ml去离子水(滴加过程持续2h),冰水浴中磁力搅拌12h,得到澄清白色溶液。向体系中加入大量去离子水至体系ph为中性,去离子水洗涤离心3次后置于45℃真空烘箱干燥,得到白色粉末固体。将样品转移至25ml的带盖坩埚中煅烧样品,升温速率10℃/min至520℃保温4小时,自然冷却后得到浅棕色固体粉末,充分研磨后水洗干燥后得到改性的cn样品。在其他实施方式中,以上步骤的顺序不可颠倒,氧化剂混合液的滴加时长,与cn的配比,去离子水的用量,洗涤次数等等不限定为以上实施例。可以理解,cn本体用量变化,相应的滴加或搅拌时长,以及氧化剂和水的用量均会相应改变,不限定为以上实施例。另外,对上述实施例中得到的cn样品和cn本体进行光催化降解rhb性能的测试,如图6所示。结果显示相同时间下,本发明cn样品对rhb的降解效果明显,历时90min左右可实现完全降解,而cn本体在100min左右可降解约80%的rhb,且时间的增长,无法对剩余的20%rhb进一步分解。因此,本发明的方法增加了cn参与光催化反应的活性位点,表现出很高的光催化降解有机染料活性。对上述采用本发明得到的cn样品和cn本体的霍尔效应测试数据如下表所示,从表可以看出,本发明的cn样品电阻率明显降低,载流子迁移率增大,表明氧化剥离过程能有效降低材料的电阻率,改善的电学性质有利于光生载流子的分离和迁移,改性方法简便有效。样品电阻率(ohm·cm)载流子迁移率(cm2·v-1·s-1)本体cn1.469e81.123e4改性cn2.633e62.498e5综上,本发明的方法通过采用氧化剂混合液在低温下缓慢氧化刻蚀cn本体,随后在氧化条件下协同以水力剪切力剥离二维cn层状结构,得到最终产物,步骤简单易操作,成效显著,改性后的cn产品比表面积增大,吸(脱)附能力强,同时对材料的电学性质进行改性,降低材料的电阻率,减小载流子在材料表面迁移阻力,促进光生载流子的分离和迁移,可有效提高cn在光催化反应中的活性和光电转换效率,使其有望在工业生产中大规模应用。以上实施方式仅用以说明本发明实施例的技术方案而非限制,尽管参照以上较佳实施方式对本发明实施例进行了详细说明,本领域的普通技术人员应当理解,可以对本发明实施例的技术方案进行修改或等同替换都不应脱离本发明实施例的技术方案的精神和范围。当前第1页12