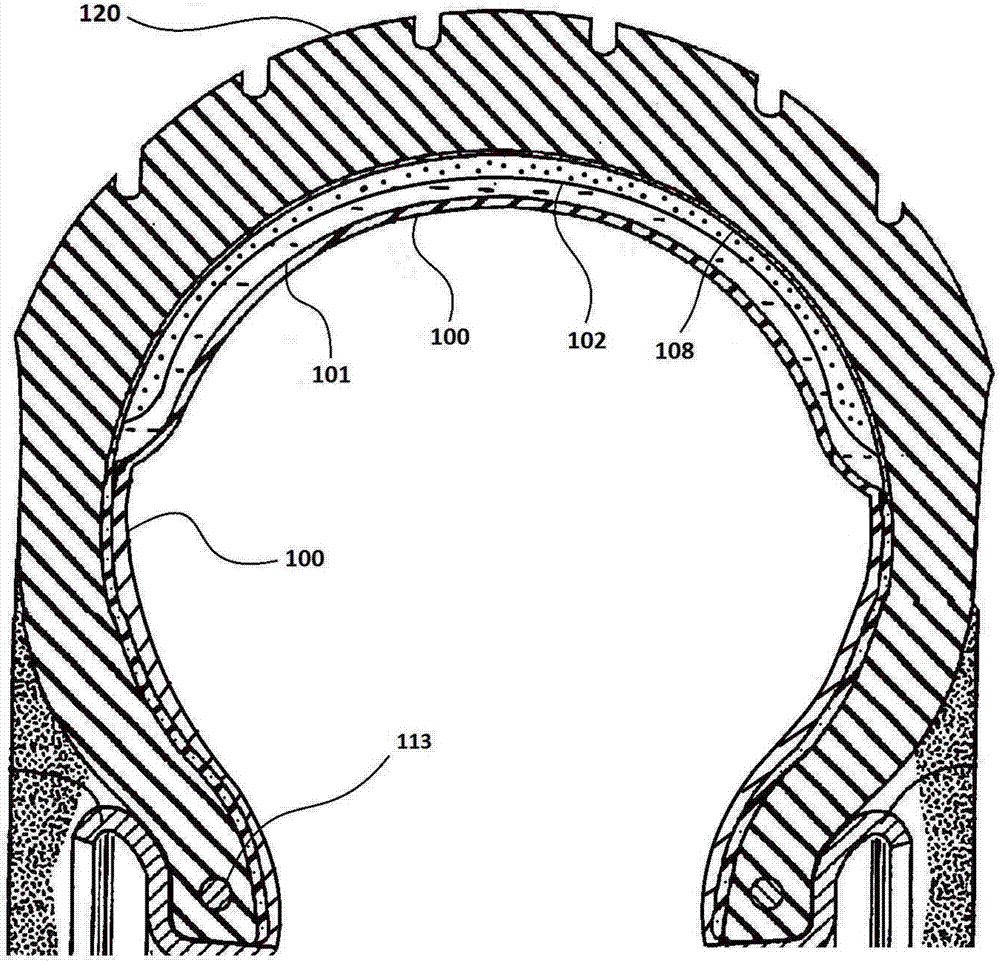
本发明涉及一种带有内部密封胶层的轮胎,尤其涉及一种带有多个内置密封胶层的轮胎,其中,所述密封胶层中至少有一层由密封胶前体层构成。
背景技术:
:轮胎刺破是橡胶轮胎的一个固有问题。针对该问题,已经研究出了密封胶,并置于内胎中,可最大程度降低轮胎刺破的影响。此外,在任何温度条件下均有可能发生刺破。在低温条件下,使用单层低粘度密封胶即可,但在高温条件下,密封胶的粘度会非常低,导致密封胶在使用时会流出轮胎外。在轮胎密封胶用尽之后,轮胎则不具有刺破自封性能。同样,在高温条件下,使用单层高粘度密封胶即可,但在较低温度条件下,高粘度密封胶几乎固化,无法在较低温度条件下流动,从而不能堵住轮胎中的刺孔。现有技术中已存在带有内置密封胶层的轮胎。通常情况下,轮胎密封胶为包含过氧化物的丁基橡胶基密封胶前体层,例如,美国专利4,895,610;6,962,181;7,073,550;7,674,344;8,293.049;美国专利公开2005/0113502和2005/021568,均引用结合到本文中。密封胶层可能为黑色或其他颜色,且可能包含聚酯或聚氨酯纤维等短纤维和其他填充聚合体,帮助堵塞钉刺孔。采用多个密封胶层的轮胎已经面世,如美国专利8,387,672(majumdar),其中采用了多个密封胶层,每个密封胶层均以聚氨酯密封胶前体为基础,在前体层中含有一个非织物层。重点是使用该非织物材料来防止聚氨酯密封胶泄漏,堵住刺孔。技术实现要素:一种带有内置密封胶层的轮胎,包括支撑轮胎胎体,由一个或多个帘布层、外周向胎面和径向内层组成;一对胎圈;胎侧,从胎面部分轴向外边缘径向向内延伸,连接相应的胎圈;密封胶,包括外层密封胶和内层密封胶,外层密封胶和内层密封胶从所述轮胎胎体内层向内布置;其中,所述内层和外层密封胶的粘度不同,所述密封胶具有轮胎刺破自封性能。附图说明本发明的上述和其他特征与优点对本领域的技术人员显而易见,在参考相关附图时需阅读下列说明,其中:图1所示为密封胶层和密封胶覆盖层的横截面图;图2所示为使用本发明的轮胎的横截面图;图3所示为显示本发明备选实施例的轮胎的横截面视图;图4所示为显示本发明备选实施例的轮胎的横截面视图;图5所示为已刺破轮胎和说明现有技术的部分横截面视图;图5a所示为已刺破轮胎和说明现有技术的部分横截面视图;图6所示为使用本发明的已刺破轮胎的部分横截面视图;图7所示为显示本发明备选实施例的轮胎的横截面视图;图8所示为显示本发明另一种备选实施例的轮胎的横截面视图。具体实施方式本发明涉及一种带有多个内置密封胶层的轮胎。所述轮胎包括支撑轮胎胎体,由一个或多个帘布层、外周向胎面和径向内层组成;一对胎圈;胎侧,从胎面部分轴向外边缘径向向内延伸,连接相应的胎圈;密封胶层,包括气密层、两个或多个密封胶层和布置在所述支撑轮胎胎体最内层的覆盖层,其中,所述气密层附着在所述轮胎胎体的最内层,所述两个或多个密封胶层位于所述气密层和所述覆盖层之间,所述两个或多个密封胶层包括内层和外层,内外层密封胶的粘度不同,所述密封胶层具有轮胎刺破自封性能。轮胎剖面结构的从外到里层次顺序包括:最外层为胎面层,然后依次为是传统的轮胎胎体(包括帘布层和带束层)、气密层、密封胶外层、密封胶内层,最内层是防护覆盖层。在气密层和轮胎胎体的最内层之间可选择布置气体渗透层。气密层永久性附着、接合或连接到轮胎胎体的内表面上。在彼此相对位置布置了密封胶内层和外层,所述密封胶内层和外层为轮胎内部结构的一部分,即密封胶外层并不位于或部分位于轮胎的外部/外侧。本发明使用了一种密封胶,包括多个内置刺穿密封胶层,所述刺穿密封胶层以密封胶外层和密封胶内层构成。与一个等总厚度的密封胶层相比,使用多个密封胶层可以为轮胎提供更好的性能。利用本发明,当密封胶外层为高粘度密封胶层而密封胶内层为低粘度密封胶层时(即高粘度密封胶层位于轮胎外胎面外表面的较近位置,而低粘度密封胶层则位于轮胎/轮胎旋转轴中心的最近位置),可获得更好的刺穿自封效果。密封胶内层和外层主要包括降解的异丁橡胶。本文中所用术语“密封胶前体”是指本身不是密封胶,但在制造轮胎的高温轮胎硫化步骤中通过热降解可转化为密封胶的一种化合物。所述“前体层”为密封胶前体层。所述前体层可以是100%的丁基橡胶或以丁基橡胶为主要成分,丁基橡胶占80%-90%,二烯基弹性体最多为5%左右。在高温条件下进行轮胎硫化期间,丁基橡胶降解,形成低分子量粘性密封胶。可从内部到轮胎气密层之间布置多个密封胶层,其中,需要采用密封胶防护层来防止轮胎硫化胶囊污染。轮胎气密层和轮胎胎体之间可布置多个密封胶层,其中,由于轮胎气密层会防止轮胎硫化胶囊污染,因此无需采用密封胶防护层。但是,需要在帘布层和密封胶层之间布置橡胶刮扫层,防止密封胶在帘子线和帘布层之间流动。橡胶刮扫层可使用任何橡胶基成分,如天然橡胶、丁二烯橡胶以及丁苯橡胶基成分。为了方便起见,橡胶刮扫层的成分可与气密层的成分相同,但是,由于无需具有阻隔性能,因此橡胶刮扫层的厚度可相对较小。通常情况下,橡胶刮扫层的厚度应大于0.5mm小于1mm。对于乘用车轮胎,传统卤化丁基胶橡胶基气密层厚度应约为1.5mm,对于卡车轮胎等较大的轮胎,传统卤化丁基胶橡胶基气密层厚度可达4mm。低粘度/密封胶内层的储能模量(g’)非常低,在轮胎成型期间无法压延或方便地直接应用。为了弥补这一缺陷,轮胎成型开始时,使用高g’密封胶前体层,在轮胎硫化期间利用适当的过氧化物(下文讨论)催化,前体层会原位降解,从而形成低g’密封胶层。同样,高粘度/密封胶外层可由密封胶前体层原位成型。但是,高粘度密封胶层的g’足够高,在轮胎成型期间可直接应用,无需通过过氧化物进行热降解。更改或抑制过氧化物的数量,粘度会随之变化。一种阻挡层,可以为气密层(见图2)或橡胶刮扫层(见图3),用于防止密封胶被加固轮胎胎面的纤维材料吸收。虽然该阻挡层是需要的,但其并不是关键性部分。可使用任何商用丁基橡胶作为密封胶前体层。可使用不饱和级别为0.90–2.25mol%并且门尼粘度(ml(1+8)125℃)处于33–51mu(门尼单位)范围内的各种丁基橡胶,如德国朗盛(lanxess)的丁基橡胶。在存在过氧化物催化剂的情况下加热,丁基橡胶会降解成门尼粘度(ml(1+8)125℃)较低的橡胶,门尼粘度处于5-25mu范围之间。除了丁基橡胶之外,还可使用通过过氧化物降解的其他橡胶单独或与丁基橡胶组合作为密封胶前体。例如,可使用溴化的异丁烯-异戊二烯共聚物,如德国朗盛(lanxess)的x_butyltmi4565p。此种共聚物的门尼粘度(ml(1+8)125℃)处于52–60mu范围内。在存在过氧化物催化剂的情况下加热,x_butyltmi4565p橡胶会降解成门尼粘度(ml(1+8)125℃)较低的橡胶,门尼粘度处于10-35mu范围之间。高粘度密封胶层主要由丁基橡胶、溴化的异丁烯-异戊二烯共聚物和两者的组合组成。所述高粘度密封胶层的门尼粘度(ml(1+8)125℃)处于25–60mu范围内,此种密封胶层的粘度高于低粘度密封胶层。(例如,若高粘度密封胶层的粘度为25mu,低粘度密封胶层的粘度则应为24mu或更低。)本发明采用了一种标准的轮胎成型工艺。在生胎(未硫化)成型后,可选择在所述最内层的顶部应用一层可选保护膜。所述保护膜的宽度应稍大于密封胶层(宽出密封胶层两侧约2英寸以上)。若最内层密封胶覆盖层在模具中破裂或撕裂,该保护膜可保护轮胎硫化胶囊并保持硫化胶囊清洁。此类保护膜在现有技术中已经存在。一种此类薄膜为2密尔的未拉开尼龙6,6,如coverishighperformancepackaging公司的c900。在轮胎硫化后,薄膜端部应重叠大约1”(英寸),可作为一个拉带,便于简单拆除。美国专利7,332,047(majumdar、logan和lukich)中描述了此类系统,本文参考引用了该专利。该保护膜还可作为轮胎成型鼓中的第一层膜。为了方便起见,优先采用涂覆压敏胶(psa)的可热成型薄膜覆盖在该薄膜的两个边缘上。美国专利7,419,557(majumdar和page)中说明了该系统,本文参考引用了该专利。虽然该薄膜并不是关键性部分,但由于动态硫化合金(dva)的应变模量明显降低,受到较小的力即可延伸,因此,在轮胎成型鼓中的尼纶-6,6薄膜上优先选用动态硫化合金薄膜。美国专利8,776,851(majumdar)中说明了此类材料,本文参考引用了该专利。此外,美国专利8,021,730和8,158,721中说明了其他示例。在密封胶成分中可添加一种有机过氧化物活化剂,用于加速降解。美国专利7,674,344(d’sidockyet等人)中说明了该方法,本文参考引用了该专利。本发明包括气密层和密封胶前体。所述气密层包括溴化丁基橡胶、炭黑、环烷油、硬脂酸、酚醛树脂增粘剂、黑色芳烃类树脂混合物(存在于美国struktol公司制造的40ms树脂中)、mgo、zno、硫和2,2’-二硫基(苯并噻唑)(销售名为mtbs)。所述密封胶前体包括第一个非生产性(np)混合步骤中的丁基橡胶、溴丁基、聚丁二烯、石蜡油、二氧化硅、黏土、二氧化钛、滑石粉、酞色/苯胺色浓缩染料/颜料(如akrochem公司制造的e2295绿色)、橙色颜料(如akrochem公司制造的e6615橙色)、脂肪酸衍生物加工助剂混合物(如美国struktol公司制造的hps11加工助剂)。在最后生产(pr)步骤中可添加有机过氧化物,如正丁基4,4-二(叔丁基-过氧)戊酸盐(如akzonobel制造的17-40b-gr)。优选通过以下方式来制造本发明的轮胎:1.一种密封胶覆盖层,按表1所示配方,混合并压延至厚度为1mm,宽度与气密层的宽度相等。2.一种低粘度前体,按表2所示配方,混合并压延至厚度为3mm,宽度比胎面宽度少15mm(即胎面宽度减去15mm)。3.然后,一种高粘度前体,按表2所示配方,混合并压延至厚度为3mm,宽度与胎面宽度相等。4.在轮胎成型鼓中应用密封胶覆盖层(上述第1条)。5.在轮胎成型鼓中应用低粘度前体(上述第2条)。6.在轮胎成型鼓中应用高粘度前体(上述第3条)。7.在典型轮胎成型过程中,在轮胎成型鼓中应用气密层,然后在普通轮胎成型过程中采用其他层。一个备选实施例包括上述步骤,但对这些步骤进行了修改,用三个或三个以上中等粘度的中间层来代替低粘度和高粘度密封胶层。表1密封胶覆盖层表2两种密封胶前体为便于说明,有些附图中忽略了一些轮胎内部材料,如带束层和帘布层,但成品轮胎中仍然存在。图1所示为密封胶层和密封胶覆盖层的简化说明,其中值得注意的是,所示为各个层的顺序,未按照比例显示各个层,且各层的宽度和厚度均不是具体的数值。所述宽度范围为从整个轮胎宽度到沿着轮胎中心的小条宽度。图中以一般形式显示了第一密封胶前体层101’和第二密封胶前体层或直接密封胶层102’和密封胶覆盖层100’。在优选实施例中,密封胶前体内层101’的粘度低于密封胶前体外层102’的粘度。刺破期间,密封胶101和/或102(见图6)流入刺孔中,填充该刺孔。根据内部温度和刺孔的直径,所述覆盖层100可能会从轮胎内侧延伸覆盖/堵塞刺孔。图2所示为图1给出的轮胎内部密封胶层。从内部到气密层108之间(即距离轮胎中心较近的位置)布置低粘度密封胶内层101和高粘度密封胶外层102(如图1所示,分别由前体层101’和102’形成),此外,还需要一个密封胶覆盖层100。覆盖层100将轮胎的宽度延伸到胎圈113处。最外层为胎面120。从内部到密封胶覆盖层之间可选择地布置一个尼龙薄膜(未显示),覆盖密封胶覆盖层下面的密封胶层。所述尼龙薄膜用于在密封胶覆盖层破裂时,防止密封胶泄漏。轮胎硫化后,需拆掉所述尼龙薄膜。图3所示为图2中轮胎的备选实施例。在此实施例中,气密层108位于密封胶层101和102之间。如上述讨论内容,此种布置需要一个橡胶刮扫层109。图4所示为本发明的一个备选实施例,其中,在轮胎中嵌入所述密封胶层101和102,使所述覆盖层100与轮胎内部齐平。所述密封胶由丁基橡胶构成,丁基橡胶还是一种良好的屏障,因此无需在密封胶下面额外布置一个气密层。此种布置可节省材料并降低轮胎的重量。低温条件下使用单层低粘度密封胶即可,但在高温条件下,低粘度密封胶可能会泄漏,如图5所示。高温会降低密封胶层301的粘度,从而导致密封胶通过轮胎刺破孔300泄漏302,最终导致使用期间密封胶从轮胎中流出,从而削弱钉孔自封能力。此种情况还会污染路面。同样,高温条件下使用单层高粘度密封胶即可,但在低温条件下,高粘度密封胶几乎固化,无法在低温条件下流动堵住轮胎中的刺孔,如图5a所示。低温会增加密封胶层301的粘度,此种情况下,密封胶不会流动或者只会轻微流动,导致密封胶膨胀303程度最低,留出气隙,导致无法密封轮胎刺破孔300。在固特异轮胎等典型的刺破自封轮胎中,如us4,895,610、us4359078、us6,962,181、uspp2005/0113502、2005/0215684,密封胶层位于厚气密层和外胎之间。此种情况下,气密层会非常厚,从而无法延伸堵塞刺孔。如图6所示,在本发明的一个实施例中,从内部到气密层108之间采用了一个密封胶层并用低模薄密封胶覆盖层100保护。出现刺破时,高粘度层102和低粘度层101的密封胶会流入刺孔300中。这会产生一个密封胶塞202,防止轮胎放气。此外,根据温度和刺孔的直径,防护层100可延伸并永久性堵塞较大的轮胎刺孔。图7所示为本发明的一个备选实施例,其中,密封胶层101和102处于两个单独的隔室内,此种布置可在轮胎使用期间减少密封胶流动。换言之,将密封胶分为两个或多个平行的圆周带。同样,密封胶层也可处于四个隔室中,如图8所示,其中,图7所示的两个或多个平行的圆周带包括四个带。通常情况下,钉子通过胎面凹槽处刺入轮胎,而密封胶覆盖层或气密层应附着在胎面凸起花纹的下面。此种布置可减少轮胎中所需密封胶的总量。下列示例对本发明以及本发明与市面上相似轮胎的关系进行了说明。实施例1密封胶轮胎成型的优选方法成型215/17r17.5尺寸的卡车客车子午线轮胎。首先在轮胎成型鼓上应用与气密层同等宽度的密封胶覆盖层,然后是两层低粘度密封胶前体b和两层高粘度密封胶前体4c014a。密封胶前体层的宽度大约与胎面宽度相同。然后依次应用全宽度的气密层和其他常规层。生胎成型后,在覆盖密封胶前体的密封胶覆盖层顶部应用一层2mm的dartekc917薄膜,然后进行硫化。硫化后,在测试前拆掉dartekc917薄膜。在将轮胎从压力机上取出时,密封胶覆盖层初次膨胀,但在轮胎冷却后,膨胀处恢复原样。均匀性测试轮胎均匀性测试期间采用kokusai的fdbrc-6142td-r。带有密封胶层轮胎的均匀性为a。钉孔密封胶测试将轮胎充气到116psi时进行测试。该轮胎通过了12d和16d钉子的钉孔密封胶测试,但未通过20d钉子的钉孔密封胶测试。12d、16d和20d钉子对应的直径分别为0.148、0.162和0.192英寸或3.8、4.1和4.9毫米。硫化轮胎的密封胶厚度切开该轮胎,确定轮胎的密封胶厚度为4mm。实施例2带有单层密封胶轮胎与带有双层密封胶轮胎的钉孔自封性能对比如表3所示,采用相同组合厚度的单密封胶层和双密封胶层成型215/75r17.5tbr轮胎。表3中1a和1b显示了总厚度为4.8mm的两种不同密封胶层(4c014a和4c014b)组合的刺破自封性能。在将该种密封胶层组合应用到胎面凸起花纹上时,20d的钉子会刺破其上的两种密封孔。1a未能成功密封胎面凹槽中的20d钉子孔,而1b则成功地密封了胎面凹槽中的20d钉子孔。这表明在高粘度密封胶层内优选使用一个低粘度密封胶层。这还表明了低粘度密封胶有助于将高粘度密封胶推进到钉子孔中,从而堵塞钉子孔,高粘度密封胶不会露出胎面外表面。表3中的1c和1d具有总厚度为4.8mm的粘度密封胶(如固特异duraseal轮胎和其他轮胎,参考1-11)。与总厚度相同的1a和1b两种粘度密封胶层组合相比,1c和1d两种密封胶的钉刺孔自封能力较差。表3带有密封胶层的215/75r17.5tr685tbr轮胎刺破测试实施例3密封胶覆盖层如表4所示,利用不同密封胶覆盖层制造相同的轮胎。表5所示为使用4c013a密封胶覆盖层时密封胶流出胎面。使用90biir/10csm密封胶覆盖层时,密封胶不会流出胎面,其中,biir为溴化丁基橡胶,csm为氯磺化聚乙烯。除了用90biir和10csm替换了100biir之外,90biir/10csm的成分与表1中所示的成分相似。切开的轮胎显示,使用90biir/10csm时密封胶覆盖层会延伸堵塞钉孔。由于m100的粘度非常高(2.99mpa),使用4c013a密封胶覆盖层时,其需要很大的力才能够延伸,所以密封胶覆盖层不会延伸堵塞钉子孔。如表7和8所示,在不使用丁基橡胶或卤化丁基胶的情况下,利用传统橡胶也可合成低粘度m100密封胶覆盖层。目前商用duraseal轮胎采用的气密层非常厚,导致密封胶无法延伸堵塞钉孔。本发明中使用了一种密封胶覆盖层,其拥有1.6mpa(范围为0.5-2.5mpa,优选1.2-1.9mpa)的100%模量。表4两种不同密封胶覆盖层的性能a3tid4c013a90biir/10csm拉伸强度(mpa)17.09.3e(%)446642m100(mpa)2.991.6m300(mpa)8.654.3表5带有两种不同密封胶覆盖层的315/80r22.5轮胎刺破测试表6刺破测试后315/80r22.5轮胎的气密层检查表7两个红色最里层密封胶覆盖层的混合表8表7的红胶化合物性能实施例4密封胶rpa测量值橡胶工业中广泛使用了橡胶加工分析仪(rpa)。可从alphatechnologies公司购买rpa-2000。该型号的rpa能够在硫化前、硫化期间和硫化后测量橡胶的性能。下列为4种密封胶和一个密封胶覆盖层的rpa测试条件,表9和表10中分别记录了其结果。步骤1-温度为80℃、应变为5%、频率为1hz,确定储能模量步骤2-在温度为170℃、应变为5%、频率为1hz的条件下加热样品12分钟步骤3-将样品冷却到80℃,重复步骤1步骤4-将样品冷却到35℃,重复步骤1储能模量(g’)与材料的粘度相关。表9所示为加热前密封胶前体的g'值以及加热后密封胶前体的g'值。在35℃条件下,四种密封胶的g'值处于0.056–0.406mpa范围内。在80℃条件下,四种密封胶的g'值处于0.01–0.194mpa范围内。若g'值处于0.3–0.41mpa范围内对密封钉孔最有利,则如果在35℃条件下发生刺破,最好选用rc4c014密封胶,若在80℃条件下发生刺破,最好选用4c021b密封胶。数据表明,若在不同温度条件下发生刺破,两层不同粘度的密封胶性能优于一种粘度的密封胶。在80℃条件下,加热前的一种密封胶覆盖层g’值(表10)低于加热后高粘度密封胶层的g’值(0.144mpavs0.194mpa)(表9)。这表明无需任何过氧化物或硫化剂即可构成高粘度密封胶层。如表7所示,4c022a的np1即为此种高粘度密封胶层的一个示例,无需使用硫化剂。表9热分解后,在温度为35℃时,按升序排序的四个密封胶层rpa表10密封胶覆盖层的rpa结果实施例5高粘度和低粘度密封胶的储能模量范围表11和12所示为采用不同范围高粘度和低粘度密封胶的轮胎测试。加热后,g’与密封胶的粘度相关。表11和12中给出了八个测试。对于高粘度密封胶,g’值处于0.405–0.134mpa范围内,而低粘度密封胶的g’处于0.196-0.056mpa范围内。如表中所示,温度为35℃时,高粘度密封胶的g’值处于0.5–0.1mpa范围内。无需使用任何过氧化物或硫化剂即可制造出此种材料。温度为35℃时,低粘度密封胶的g’值处于0.3–0.02mpa范围内。另外,由于此种材料采用其他方式难以加工,因此只能使用过氧化物由前体生成。使用过氧化物催化剂可将丁基橡胶降解成低分子量橡胶。但所用催化剂必须能够在室温条件下保持稳定。此种催化剂应能够在150℃的轮胎硫化温度下进行降解。换言之,我们可以使用一种或多种在50–140℃温度范围内具有自加速分解温度(sadt)的过氧化物催化剂。以下为此类催化剂的几个示例:表13和14所示为密封胶前体成分。表11315/80r22.5轮胎中从内部到轮胎气密层之间的密封胶层和密封胶覆盖层。轮胎充气到0.83mpa(120psi)标准值时,轮胎通过用20d钉子刺破的刺孔测试表12从内部到轮胎气密层之间的密封胶层和密封胶覆盖层,密封由20d钉子刺破的刺孔表13两种密封胶前体的成分表144种其他密封胶前体的成分r4c014cr4c014dr4c014er4014f丁基301100100100100溴丁基5-5-丁二烯橡胶(br900)-5-5石蜡油13131313二氧化硅17520202020黏土10101010绿色1-1-黄色-1-1三角17-40b-gr1262414总计161155173163表中数据表明,本发明是对美国专利8,387,672(majumdar)等轮胎刺破密封技术的一种改进。相比之下,本发明不采用或不需要非织物纤维层作为密封胶的“载体”。相反,可使用纯净的密封胶层,无需使用非织物载体层。本发明的上述实施例仅供解释和说明。这些说明和实施例不旨在详述或限制本发明为披露的精确形式,根据上述披露,可能会明显存在很多变形和变体。为更好地说明本发明的原理及其实际应用,我们选择并说明了这些实施例,从而使本领域其他技术人员能够更好地将本发明应用到各个实施例中,并经过各种修改以适用于预期的特殊目的。当前第1页12