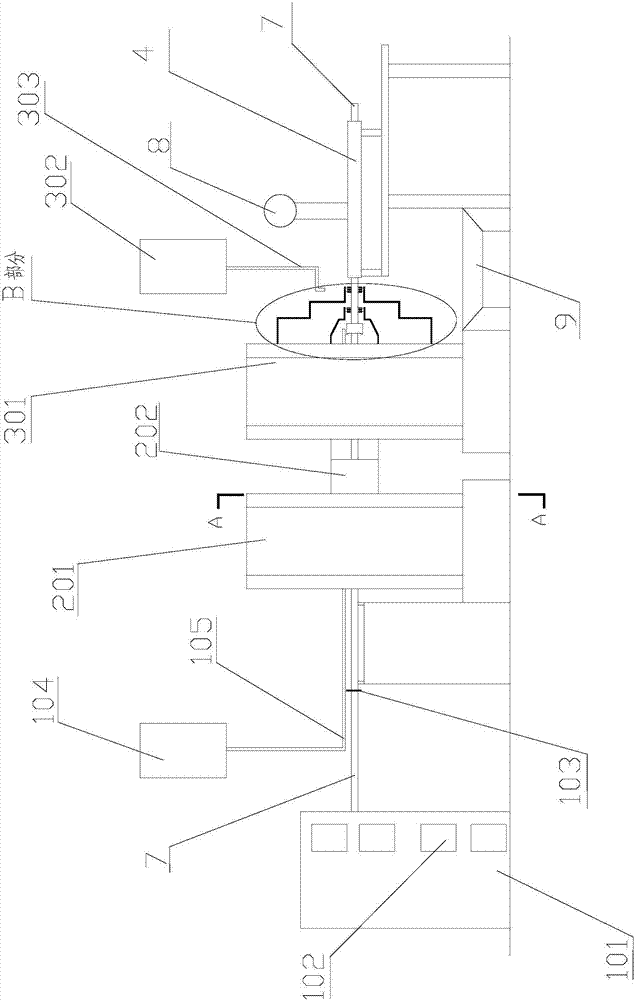
本发明涉及一种玻璃钢管的生产设备。
背景技术:
:中国发明专利文献cn105014986a公开了一种挤拉带缠绕式玻璃钢管及其制作方法,包括如下步骤:(1)工具和材料准备:准备管状内模具和外模具、第一分纱装置、第二分纱装置、正缠绕装置、反缠绕装置、浸胶装置、刷胶装置、包裹装置、加热装置、牵拉装置和切割机,所述内模具的外径小于外模具的内径,还准备玻璃纤维纱、缝编毡和不饱和聚酯树脂为材料,其中,不饱和聚酯树脂中需要加入内脱模剂和高温固化剂;其中正缠绕和反缠绕的玻璃纤维纱的纱卷装置在纱轮上,纱轮在支架上绕中轴旋转而释放玻璃纤维纱用于玻璃钢管制作;直拉层直接从纱卷上抽取玻璃纤维纱。(2)走底纱:将步骤(1)中的玻璃纤维纱通过第一分纱装置均匀分布在内模具外围,然后通过牵拉装置将玻璃纤维纱顺着内模具向第二分纱装置牵拉,穿过第二分纱装置后,玻璃纤维纱均匀的覆盖在内模具上形成玻璃纤维直拉层,然后通过浸胶装置将玻璃纤维直拉层均匀浸透不饱和聚酯树脂,在走底纱的同时,通过牵拉装置对玻璃纤维直拉层施加一定张力,使其与内模具外围紧贴并顺着内模具轴向拉动;(3)正向缠绕:通过正缠绕装置的周向运动,在玻璃纤维直拉层上缠绕覆盖玻璃纤维正绕层,同时通过浸胶装置将玻璃纤维正绕层均匀浸透不饱和聚酯树脂,同时,通过牵拉装置对玻璃纤维直拉层和玻璃纤维正绕层施加一定张力,使其与内模具外围紧贴,一边顺着内模具轴向拉动,一边旋转缠绕;(4)反向缠绕:完成步骤(3)后,通过反缠绕装置的周向运动,在玻璃纤维正绕层上按与缠绕玻璃纤维正绕层相反的方向旋转缠绕玻璃纤维反绕层,同时通过刷胶装置将玻璃纤维反绕层周向均匀涂刷不饱和聚酯树脂,同时,通过牵拉装置对玻璃纤维直拉层、玻璃纤维正绕层和玻璃纤维反绕层施加一定张力,使其与内模具外围紧贴,一边顺着内模具轴向拉动,一边旋转缠绕,所述玻璃纤维直拉层的厚度小于玻璃纤维正绕层和玻璃纤维反绕层的合计厚度;(5)覆盖缝编毡:完成步骤(4)后,通过包裹装置用缝编毡完全包裹在玻璃拉维纱外部,同时,通过牵拉装置对玻璃纤维直拉层、玻璃纤维正绕层、玻璃纤维反绕层和缝编毡施加一定张力,使其与内模具外围紧贴,一边顺着内模具轴向拉动,一边包裹覆盖;(6)加热固化:将完成步骤(5)后的玻璃纤维纱和缝编毡由牵引装置拉入外模具中,所述外模具中设有加热装置,在温度为110-140℃、时间为1-4min的条件下加热固化成形,通过牵拉装置将固化成形后的玻璃钢管连续牵拉出外模具出口端;(7)切割成品:将玻璃钢管固化冷却后,通过切割机切割为成品。上述技术方案中,2~4步骤为主要工艺,即通过走底纱形成玻璃纤维直拉层;正向缠绕在玻璃纤维直拉层上缠绕覆盖玻璃纤维正绕层;反向缠绕在玻璃纤维正绕层上按与缠绕玻璃纤维正绕层相反的方向旋转缠绕玻璃纤维反绕层。通过直拉层、正绕层、反绕层所形成复合结构能够有效提高玻璃钢管的抗冲击性,适宜烟花炮筒的工作特性。然而,在生产实践中上述生产方法的实现较为困难。其原因在于,直拉层粘附在内模具外表面,形成较大的拉动阻力;在经过正绕层和反绕层的缠绕紧束后拉动阻力更大;而且,直拉层、正绕层、反绕层施胶复合之后要通过内、外模具之间的间隙辅以加热胶水固化才能成型,在该间隙中复合层受到挤压、而且增加了复合层外表面与外模具内表面的粘附力,进一步增大了拉动阻力。上述技术方案中,直拉层、正绕层、反绕层分别施胶,到进入所述间隙时,各层的胶水已经存在粘稠度增高和不同程度的固化现象,导致如下弊端:其一,拉动非常困难,阻力极大,必须施加较大的拉力。不但导致生产成本大幅上升;而且,拉动的拉力来源于生产线后端对已固化成型管体的拉动,已经固化成型的后端管体和尚未固化成型的前端管体的结合部难以承受过大的拉力负荷。其二,在所述间隙中的挤压的目的在于:使得所有玻璃纤维之间的胶水适量,胶水能够充分浸润粘合而不存在冗余量;同时排挤气泡;从而使得所述复合层构成结构强度大而均匀的整体化的筒体,并保证所形成的筒体内外壁光滑。但是,各层已分别出现粘稠固化的情况下,上述目的很难得到充分实现,导致管体质量下降。其三,复合层进入所述缝隙时,外模的端口对玻璃纤维纱形成较强的阻滞作用,玻璃纤维可能在端口处形成堆积,造成产品失败。技术实现要素:为了解决上述弊端,本发明所要解决的技术问题是,提供一种直拉缠绕复合式玻璃钢管的生产设备,能够确保生产的顺利完成和产品的质量。为了解决上述技术问题,本发明采用的技术方案是,直拉缠绕复合式玻璃钢管的生产装置,包括沿内模具前后依序分布的直拉层单元、正绕层单元、反绕层单元,反绕层单元的后方设置套装在内模具上的外模具,外模具设有加热机构,外模具的后方依序分布牵引单元和切割单元,其特征在于,所述直拉层单元包括支架上的若干直拉层纱卷,直拉层纱卷上的直拉层玻璃纤维纱在若干分纱环的约束下均匀分布在内模具外周,直拉层玻璃纤维纱在牵引单元的作用下,沿内模具轴向依序穿过正绕层单元、反绕层单元、外模具而固化成型为玻璃钢管的组成部分;供胶机构在直拉施胶点向直拉层玻璃纤维纱施胶;所述正绕层单元包括环绕内模具装置的环状的正绕滚筒,正绕滚筒后端固接直行导引件,直行导引件后端固接缠绕导引件,正绕滚筒、直行导引件、缠绕导引件以内模具为中轴线进行旋转运动;正绕滚筒上沿圆周均匀分布若干正绕层纱轮;正绕层纱轮上的正绕层玻璃纤维纱依序通过直行导引件、缠绕导引件的导引,在第一缠绕点缠绕覆盖在直拉层玻璃纤维纱上;供胶机构在第一缠绕点向正绕层玻璃纤维纱施胶;所述反绕层单元包括环绕内模具装置的环状的反绕滚筒,所述正绕层单元的直行导引架穿过反绕滚筒的环状中空区;反绕滚筒后端固接第二缠绕导引件,反绕滚筒、第二缠绕导引件以内模具为中轴线进行旋转运动,旋转方向与正绕滚筒相反;反绕滚筒上沿圆周均匀分布若干反绕层纱轮;反绕层纱轮上的反绕层玻璃纤维纱通过第二缠绕导引件的导引,在第二缠绕点缠绕覆盖在正绕层玻璃纤维纱上;供胶机构在第二缠绕点向反绕层玻璃纤维纱施胶;所述直拉施胶点、第一缠绕点和第二缠绕点都集中设置在反绕滚筒和外模具进口之间的区域内,该区域称之为处理工段;直拉施胶点、第一缠绕点和第二缠绕点依序在处理工段内前后靠近分布;第二缠绕点靠近外模具进口。采用上述技术方案,各个单元的机构设置协同实现了直拉施胶点、第一缠绕点和第二缠绕点在所述处理工段的集中设置,使得直拉层、正绕层、反绕层的施胶时间趋于接近并在胶水尚未粘稠固化时就进入外模具进口:1.胶水起到了润滑作用,使得各层玻璃纤维丝都能够顺畅进入内外模具之间的缝隙,杜绝了玻璃纤维纱在缝隙进口的阻滞堆积现象;2.能够在进入缝隙的过程中挤出冗余的胶水并排除空气;3.在缝隙内的挤压中,各层玻璃纤维丝作为一个整体得到胶水的充分浸润;4.尚未粘稠固化的胶水在受热至固化的过程中,在一定的时间段内胶水有一个受热粘稠度下降的过程,也使得拉动阻力变小;5.提高玻璃钢管的结构强度和结构均匀性,提高玻璃钢管内外壁的光滑度。值得注意的是,覆盖缝编毡的作用主要在于使得玻璃钢管的外表面光洁,本发明的玻璃钢管的生产中也可以不覆盖缝编毡。5.正绕层、反绕层的玻璃纤维纱越粗约有利于管体结构强度的提高,但现有技术难以使用较粗的玻璃纤维纱。本发明的技术方案能够实现较粗玻璃纤维纱的适用,同时也便于缠绕中的纱体有序排布。如在现有技术中,直拉层、正绕层、反绕层都只适用800#或更细的玻璃纤维纱;本发明中正绕层、反绕层能够适用800#~4800#的玻璃纤维纱。综上所述,本发明的有益效果在于,采用本发明的生产装置,玻璃钢管的复合质量大幅提高;同时大幅减少了复合层的拉动阻力,有利于生产顺利完成并减少功耗。优选地,所述直拉施胶点采用施胶套对向直拉层玻璃纤维纱施胶;所述直拉施胶点采用施胶套对向直拉层玻璃纤维纱施胶;所述施胶套呈环形体,环状体具有贮存胶水的内腔,所述内腔的内侧壁开放,环形体外壁设有进胶口,环形体套装在直拉层玻璃纤维纱上。供胶机构通过进胶口向环状体内腔送入胶水,环状体内腔动态贮存胶水,对直拉层玻璃纤维纱进行均匀施胶和胶水浸润。优选地,供胶机构的供胶管依序穿过正绕滚筒、反绕滚筒的中空区,向直拉施胶点供应胶水。避免胶水对环境及设备的污染,减少胶水浪费。优选地,所述第一缠绕点设有作用于正绕层玻璃纤维纱的第一胶水刷,第一胶水刷随缠绕导引件同步旋转。对正绕层玻璃纤维纱进行均匀施胶和胶水浸润。优选地,所述第二缠绕点设有作用于反绕层玻璃纤维纱的第二胶水刷,第二胶水刷随第二缠绕导引件同步旋转。对反绕层玻璃纤维纱进行均匀施胶和胶水浸润。优选地,所述直拉施胶点、第一缠绕点和第二缠绕点依序在处理工段内前后衔接;直拉施胶点采用施胶套对向直拉层玻璃纤维纱施胶;所述施胶套为环形体,环形体内侧壁开放,环形体外壁设有进胶口,环形体套装在内模具和直拉层玻璃纤维纱上,供胶机构的供胶管依序穿过正绕滚筒、反绕滚筒的中空区,向施胶套供应胶水;所述第一缠绕点设有作用于正绕层玻璃纤维纱的第一胶水刷,第一胶水刷随缠绕导引件同步旋转;所述第二缠绕点设有作用于反绕层玻璃纤维纱的第二胶水刷,第二胶水刷随第二缠绕导引件同步旋转,供胶机构向第二胶水刷供应胶水。该方案合理设置供胶、刷胶节奏,使得各层玻璃纤维纱得到充分的胶水浸润,并有利于胶合结构的均匀化整体成型。实践证明,能够大幅改善复合层整体穿过所述缝隙的通过性,大幅提高玻璃钢管的质量。为使本发明的上述目的、特征和优点能够更加明显易懂,下面结合附图对本发明的具体实施方式做详细的说明。在下面的描述中阐述了很多具体细节以便于充分理解本发明。但是本发明能够以很多不同于在此描述的其它方式来实施,本领域技术人员可以在不违背本发明内涵的情况下做类似改进,因此本发明不受下面公开的具体实施例的限制。附图说明图1为生产装置整体结构原理示意图(没有在设备上穿入玻璃纤维纱);图2为图1部分放大图(去除了牵引单元5和切割单元6);图3为图2中b部分放大机构图(椭圆形取图框内的部分);图4为图2所示a-a面剖视结构图;图5为施胶套结构示意图;图6为施胶套内部结构示意图;图7为内模和外模配合结构示意图;图8为分纱环结构示意图;图9为生产装置整体结构原理示意图(已在设备上穿入玻璃纤维纱)。附图标注说明:1直拉层单元11直拉层玻璃纤维纱104直拉供胶桶202直行导引件2正绕层单元12正绕层玻璃纤维纱105直拉供胶管203缠绕导引件3反绕层单元13反绕层玻璃纤维纱106施胶套204第一胶水刷4外模具14缝编毡1061进胶口301反绕滚筒5牵引单元15固化成型管体201正绕滚筒302反绕供胶桶6切割单元16复合层2011正绕层纱轮303反绕供胶管7内模具101支架2012正绕层纱轮转轴304第二缠绕导引件8缝编毡卷102直拉层纱卷2013正绕滚筒中空区305第二胶水刷9回收胶盘103分纱环2014滚筒基台401外模具锥形进口具体实施方式参见附图,反映本发明的一种具体结构。所述直拉缠绕复合式玻璃钢管的生产装置,包括沿内模具7前后依序分布的直拉层单元1、正绕层单元2、反绕层单元3,反绕层单元3的后方设置套装在内模具7上的外模具4,外模具4设有加热机构,外模具4的后方依序分布牵引单元5和切割单元6。内模具7和外模具4都固定不动。牵引单元5夹持拉动后端的固化成型管体15,从而带动前端的各层玻璃纤维纱向后运动。切割单元6对固化成型管体15进行定长切割。所述直拉层单元1包括支架101上的若干直拉层纱卷102,直拉层纱卷102上的直拉层玻璃纤维纱11在若干分纱环103的约束下均匀分布在内模具7外周,直拉层玻璃纤维纱11在牵引单元5的作用下,沿内模具7轴向依序穿过正绕层单元1、反绕层单元2、外模具4而固化成型为玻璃钢管的组成部分。供胶机构在直拉施胶点向直拉层玻璃纤维纱11施胶:所述直拉施胶点采用施胶套106对直拉层玻璃纤维纱11施胶;所述施胶套106为环形体,环形体内侧壁开放,环形体外壁设有进胶口1061,环形体套装在内模具7和直拉层玻璃纤维纱11上。直拉供胶桶104的供胶管105依序穿过正绕滚筒201的中空区2013、反绕滚筒301的中空区,通过进胶口1061向环状体施胶套106的内腔送入胶水,环状体内腔动态贮存胶水,对直拉层玻璃纤维纱11进行均匀施胶和胶水浸润。如图5、6所示,玻璃纤维纱11和施胶套106出口处的间隙大小决定了玻璃纤维纱11外表面上的留存胶水的厚度,留存胶水用于正绕层玻璃纤维纱12的施胶。所述正绕层单元2包括环绕内模具7装置的环状的正绕滚筒201,正绕滚筒201后端固接直行导引件202,直行导引件202后端固接缠绕导引件203,正绕滚筒201、直行导引件202、缠绕导引件203以内模具7为中轴线进行旋转运动。正绕滚筒201上沿圆周均匀分布若干正绕层纱轮2011;正绕层纱轮2011上的正绕层玻璃纤维纱12依序通过直行导引件202、缠绕导引件203的导引,在第一缠绕点缠绕覆盖在直拉层玻璃纤维纱11上。所述直拉施胶点和第一缠绕点前后衔接;所述第一缠绕点设有作用于正绕层玻璃纤维纱12的第一胶水刷204,第一胶水刷204随缠绕导引件203同步旋转。利用直拉施胶点的所述留存胶水对正绕层玻璃纤维纱12进行均匀施胶和胶水浸润。所述反绕层单元包括环绕内模具7装置的环状的反绕滚筒301(正绕滚筒201和反绕滚筒301结构相同,如图4所示)。正绕层单元2的直行导引架202穿过反绕滚筒301的环状中空区;反绕滚筒301后端固接第二缠绕导引件304,反绕滚筒301、第二缠绕导引件304以内模具7为中轴线进行旋转运动,旋转方向与正绕滚筒201相反。反绕滚筒301上沿圆周均匀分布若干反绕层纱轮;反绕层纱轮上的反绕层玻璃纤维纱13通过第二缠绕导引件304的导引,在第二缠绕点缠绕覆盖在正绕层玻璃纤维纱12上。供胶机构在第二缠绕点向反绕层玻璃纤维纱13施胶:所述第二缠绕点设有作用于反绕层玻璃纤维纱13的第二胶水刷305,第二胶水刷305随第二缠绕导引件304同步旋转,反绕供胶桶302通过反绕供胶管303向第二胶水刷305供应胶水。对反绕层玻璃纤维纱13进行均匀施胶和胶水浸润。所述直拉施胶点、第一缠绕点和第二缠绕点都集中设置在反绕滚筒301和外模具锥形进口401之间的区域内,该区域称之为处理工段;直拉施胶点、第一缠绕点和第二缠绕点依序在处理工段内前后衔接分布;第二缠绕点靠近外模具锥形进口401。上述的实现方式仅是为了清楚的说明本发明的技术方案,而不能理解为对本发明做出任何限制。本发明在本
技术领域:
具有公知的多种替代或者变形,在不脱离本发明实质意义的前提下,均落入本发明的保护范围。当前第1页12