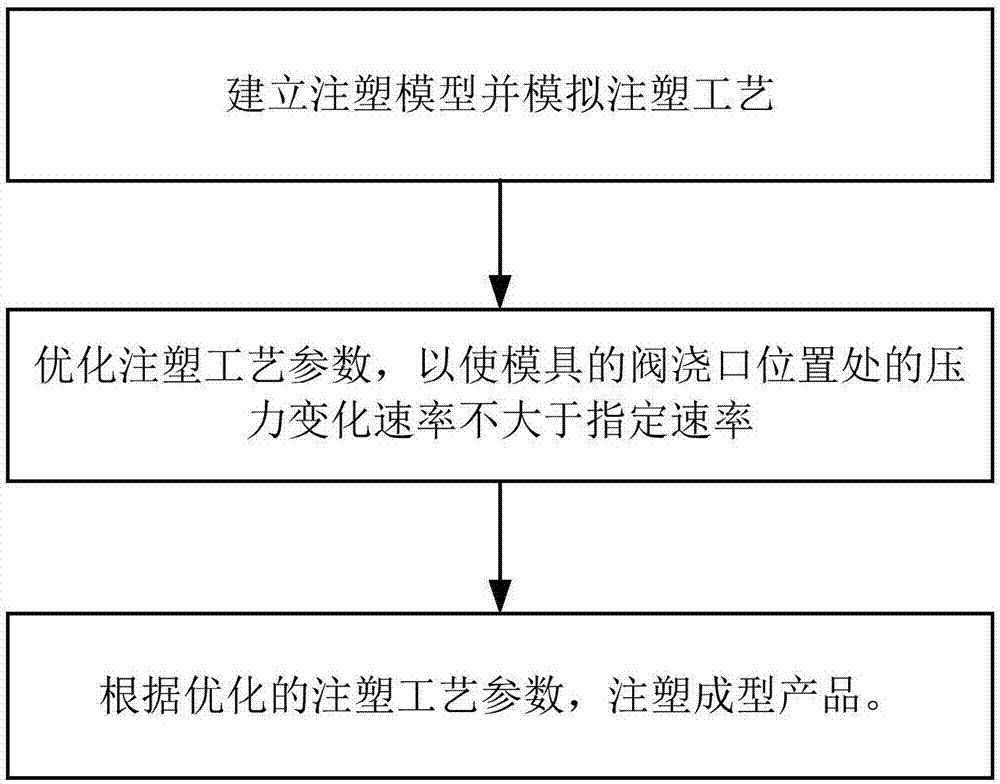
本发明涉及注塑
技术领域:
,尤其涉及一种注塑工艺。
背景技术:
由于环保和节能的需要,汽车的轻量化已成为世界汽车发展的新潮流。所谓轻量化,就是在保证汽车的强度和安全性能的前提下,尽可能地降低汽车的重量,从而提高汽车的动力性,减少材料消耗,降低排气污染。要实现轻量化的目标,势必要减小产品壁厚,进行薄壁注塑。对于薄壁零件,若采用常规的注塑方案则会导致注塑压力过大或形成熔接线等一系列问题,无法满足注塑要求。因此,为实现薄壁注塑且满足外观要求必须使用多浇口延时注塑方案。目前,延时注塑方案多采用阀浇口实时开启,该方案虽然可以满足注塑压力要求以及可以避免产生熔接线,但是当延时浇口开启时,浇口位置会形成明显的滞流,滞流会导致产品上形成波纹,影响产品外观;此外,该方案还容易导致产品翘曲变形较大以及应力集中等问题,会导致产品后续的开裂现象。因此,亟需一种注塑工艺来解决薄壁产品在注塑过程中产生的滞流问题。技术实现要素:本发明的目的在于提出一种注塑工艺,可以避免产品在注塑过程中出现滞流问题,提高产品的外观质量。为达此目的,本发明采用以下技术方案:一种注塑工艺,包括以下步骤:建立注塑模型并模拟注塑工艺,优化注塑工艺参数,以使模具的阀浇口位置处的压力变化速率不大于指定速率;根据优化的注塑工艺参数,注塑成型产品。其中,所述指定速率为15-25mpa/s。其中,所述指定速率为20mpa/s。其中,所述注塑工艺参数包括阀浇口的开启速率。其中,所述阀浇口的开启速率通过控制阀针的移动速度实现。其中,根据模拟注塑工艺过程中,多个时间点对应的阀针的位移,拟合得到所述阀针的位移与时间的关系曲线。其中,所述阀针的位移与时间的曲线为:s=63.724t3-50.326t2+13.873t+0.5854其中,s为阀针的位移,t为阀浇口的开启时间。其中,所述注塑工艺参数还包括模温、注塑材料温度、保压压力和保压时间中的至少一种。其中,所述模温为75-85℃,注塑材料温度为230-240℃,保压时间为4-6s,保压压力为60-80mpa。其中,所述模具上设置有多个所述阀浇口,每个所述阀浇口的开启速率单独控制。有益效果:本发明提供了一种注塑工艺。该注塑工艺中,在实际注塑之前通过建模模拟产品的注塑过程,通过优化注塑工艺参数,控制模具的阀浇口处的压力变化速率,使其小于指定速率,以保证阀浇口处压力平稳变化,采用优化后的注塑工艺参数进行注塑成型,能够使阀浇口位置处的压力降较小,确保产品流动等高线分布均匀,从而避免产生滞流,保证产品的外观质量。附图说明图1是本发明提供的注塑工艺的流程图一;图2是本发明提供的注塑工艺的流程图二;图3是采用常规注塑工艺时阀浇口处压力随时间变化的关系曲线;图4是采用常规注塑工艺时产品内流动等高线的分布情况;图5是采用本发明提供的注塑工艺时阀浇口处压力随时间变化的关系曲线;图6是采用本发明提供的注塑工艺时产品内流动等高线的分布情况。具体实施方式为使本发明解决的技术问题、采用的技术方案和达到的技术效果更加清楚,下面结合附图并通过具体实施方式来进一步说明本发明的技术方案。如图1所示,本实施例提供了一种注塑工艺,可以用于成型薄壁产品。为避免薄壁产品在注塑过程中出现注塑压力过大或是产生熔接线等问题,薄壁产品可以采用多阀浇口延时注塑工艺,以满足注塑压力要求,并可以避免产生熔接线。为方便介绍,本实施例中,薄壁产品以汽车中的薄壁配光镜为例介绍。薄壁配光镜一般采用聚甲基丙烯酸甲酯(polymethylmethacrylate,pmma)制成,pmma具有良好的化学稳定性和耐候性,且在破碎时不易产生尖锐的碎片,安全性能高。薄壁配光镜长度可达1000mm以上,厚度仅为2-3mm。由于薄壁配光镜厚度薄,且长度较大,因此在注塑成型时,需要设置五个以上的阀浇口。阀浇口数量较多,且阀浇口在开启时,浇口位置会瞬时产生一个较大的压力降,从而导致阀浇口位置形成明显的滞流,最终导致成型产品的表面形成波纹,产品的外观质量低。此外,阀浇口位置处压力波动大、压力梯度过大,还会导致产品流动等高线分布不均匀,从而导致产品收缩不均,产品翘曲变形和局部应力集中等问题,容易出现产品后续出现开裂。为解决上述问题,本实施例提供的注塑工艺,在注塑成型产品前,通过建立注塑模型,模拟了注塑工艺,通过保证模具的阀浇口位置处的压力变化速率不大于预设的指定速率,优化注塑工艺的参数,并将根据得到的优化后的注塑工艺参数,控制实际注塑过程,使得实际注塑过程中阀浇口位置处的压力波动小,压力平稳变化可以避免产生滞流,从而避免成型后产品表面出现波纹,提高产品的外观质量。此外,通过控制阀浇口位置处压力平稳变化,还会使产品内流动等高线分布均匀,从而保证产品收缩均匀,避免产品表面翘曲或应力集中,本实施例中,借助moldflow软件对薄壁配光镜进行模拟分析。如图2所示,建立注塑模型后,将模型导入moldflow软件,划分网格并建立浇注和冷却系统,设定注塑工艺的参数,并检测阀浇口位置处的压力变化速率是否小于指定速率,若小于指定速率,则阀浇口位置处的压力变化平稳,波动小,可以避免产生滞流,注塑工艺参数合理可用。若阀浇口位置处的压力变化速率大于指定速率,则阀浇口位置处的压力波动大,容易产生滞流,需要进一步优化注塑工艺参数,直至阀浇口位置处的压力变化速率是否小于指定速率。其中,指定速率的具体数值可以根据具体成型的产品设定,本实施例以薄壁配光镜为例,指定速率可以为15-25mpa/s,例如15mpa/s、18mpa/s、20mpa/s、23mpa/s、25mpa/s。本实施例中,指定速率选取为20mpa/s,即通过优化注塑工艺参数,使得相邻时刻内阀浇口位置处的压力变化小于20mpa。本实施例中,优化的注塑工艺参数包括阀浇口的开启速率。阀浇口包括设置在模具上的浇口以及与浇口配合的阀针,阀针可以封堵浇口。当注塑成型时,阀针向模具外侧移动,使得阀针逐渐脱离浇口,以将浇口打开。通过控制阀针的移动速度可以实现对阀浇口的开启速率的控制。在软件模拟过程中,可以得到多个时间点对应的阀针的位移,通过多组数据,可以拟合得到阀针移动曲线,即阀针的位移与时间的关系曲线,将得到的关系曲线应用至实际注塑工艺中,则可以优化产品的注塑过程,避免出现滞流、翘曲变形和开裂等问题,提高产品的注塑质量。本实施例中,优化的工艺参数还包括模温、注塑材料温度、保压压力和保压时间中的至少一个。上述工艺参数的优化方法与阀浇口的开启速率相同,模拟注塑过程中,首先选取一组工艺参数,通过检测成型过程中阀浇口位置处的压力变化,调整上述工艺参数中的一个或多个,通过多个工艺参数的配合,控制阀浇口位置处的压力变化情况。其中,模温可以为75-85℃,例如75℃、78℃、80℃、82℃、85℃;注塑材料温度可以为230-240℃,例如230℃、232℃、234℃、236℃、238℃、240℃;保压时间为4-6s,例如4s、5s、6s;保压压力可以为60-80mpa,例如60mpa、65mpa、70mpa、75mpa、80mpa。由于模具上设置有多个阀浇口,每个阀浇口位置不同,阀浇口的开启速度也可以不同。为了根据阀浇口的位置合理控制阀浇口的开启速率,每个阀浇口的开启速率可以单独控制。本实施例中,以长度为1400mm、厚度为2.5mm的薄壁配光镜为例,建立注塑模型,将其导入moldflow软件后进行模拟分析。当采用常规注塑工艺成型时,如图3所示,模具阀浇口位置处的压力梯度较大,相邻时刻内最大压力变化值为a点和b点之间的差值。其中,a点处时刻为0.9007s,压力为78.98mpa,b点处时刻为1.050s,压力为33.66mpa,压力变化值为45mpa,压力波动较大。如图4所示,产品内流动等高线分布不均,试模时存在滞流现象。采用本实施例提供的注塑工艺成型时,通过模拟得到阀浇口开启过程中多组时间增量与位移增量如表1所示。通过拟合表1中的数据,可以得到阀杆开启的时间与位移之间的关系曲线,通过多组数据拟合形成关系曲线是现有技术中比较常规的手段,本实施例中不作具体限定。表1时间增量(s)0.020.050.180.370.27位移增量(mm)10.10.9313根据表1中的数据可知阀杆移动时间与位移的五组数据,分别为(0.02,1)、(0.07,1.1)、(0.25,2)、(0.62,5)、(0.89,18),通过上述五组数据拟合可以得到阀浇口的开启曲线为:s=63.724t3-50.326t2+13.873t+0.5854其中,s为阀针的位移,t为阀浇口的开启时间。根据上述开启曲线控制实际注塑过程中阀杆的移动,得到的阀浇口处压力变化曲线以及流动等高线分布情况如图5和图6所示。如图5可知,根据本实施例提供的注塑方法注塑时,相邻时刻内最大压力变化值为c点和d点之间的差值。其中,c点处时刻为2.376s,压力为88.45mpa,d点处时刻为2.947s,压力为71.68mpa,压力变化值为17mpa,压力波动较小。如图6所示,产品内流动等高线分布均匀,试模时不存在滞流现象。采用本实施例提供的注塑工艺生产薄壁配光镜,能够消除滞流现象,使得压力分布均匀,使得产品收缩均匀,减小翘曲变形,改善产品的外观质量,消除开裂风险。优化的注塑工艺参数可以利用moldflow软件即可完成,操作简单,优化后的注塑工艺可以进一步减小产品的厚度,节约成本。以上内容仅为本发明的较佳实施例,对于本领域的普通技术人员,依据本发明的思想,在具体实施方式及应用范围上均会有改变之处,本说明书内容不应理解为对本发明的限制。当前第1页12