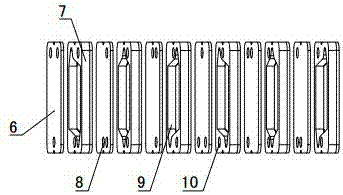
一种三介质编织式金属丝网材料换热器及制作方法,属于换热设备技术领域。
背景技术:换热器是工业生产重要的能量交换设备,在石油化工、核能、航空航天等领域占有重要地位。目前主要以管壳式换热器为主,体积大、换热效率低,不符合科学发展的要求。不少人针对换热器的优化设计方法提出了方案,但由于优化设计目标的不明确性及换热器种类的多样性,换热器的优化设计目前还不完善。随着科学技术的发展和现实工艺的需要,三介质复合换热器的应用也越来越受到了重视。现有的三介质换热器主要是在管壳式换热器的基础进行改进,具有承载压力小、占地空间大、传热不均匀、传热效率低等缺点,因此有待于探索一种新型的三介质换热器。管壳式换热器是石油工业领域应用较为广泛的一种换热器,而以板翅结构作为基本散热单元,制造的板翅式换热器,与传统管壳式换热器相比,换热效率提高10倍左右,而重量降低5-10倍,被认为是新一代能源系统的使能技术,如高温气冷堆、新一代航空发动机、微型燃气轮机以及核动力潜艇等高端装备均以回热系统作为提高效率的关键。核反应堆,操作温度达到850℃,冷却介质的压力达到9MPa,这需要换热器除了具有高效的换热效率之外,还应具有较高的强度,可以在高压情况下正常工作。我国相关技术发展缓慢,加上西方国家的封锁,尚未掌握核心制造技术和设计理论。板式换热器由于其结构紧凑、传热系数高、清洗或维修方便、节省投资等优点,被广泛地应用于石油工业生产领域中。因此以板式换热器为基础,开发紧凑、节能高效的三介质换热技术与设备,对换热器的工业应用具有重要意义。但目前应用广泛的板式换热器,在实际使用时仍存在几个缺陷:其换热板片是由具有一定波纹形状的金属片叠装而成的,刚度较低,承载能力差;工作压力在2.5MPa以下的板式换热器是靠垫片进行密封的,密封周边较长,而且角孔的两道密封处支承情况较差,垫片得不到足够的压紧力,容易引起泄漏;另外板式换热器受到换热面积的限制,使得其换热效率并不高。中国发明专利ZL201110309135.2公开了一种点阵材料换热器,相比常规板式换热器,该换热器的承载能力和换热效率有所提高,但制作工艺较为复杂,需经过多次焊接工艺才能最终成型,上下面板与扩流板之间、上下面板与封条之间、扩流板与封条之间,均需焊接连接,可能会引起泄漏问题,密封性能并不能得到有效地保障;其次,点阵材料金属网芯体在冲压成型时,尤其对于大多数航材,容易产生回弹现象,使得金属网芯体尺寸发生变化或金属网芯体内部存在较大的残余应力,并不能满足使用要求,难以应用在对尺寸精度要求较高的领域。综上所述,该点阵材料换热器在工程应用时具有一定的局限性。
技术实现要素:本发明要解决的技术问题是:克服现有技术的不足,提供一种空隙大、传热面积大、换热效率高而且承载能力好的三介质编织式金属丝网材料换热器及制作方法。本发明解决其技术问题所采用的技术方案是:该三介质编织式金属丝网材料换热器,包括压紧板、导杆以及接管,其特征在于:在两压紧板之间设有多片金属网换热单元,多片金属网换热单元叠加并由导杆和压紧板压紧固定;所述的金属网换热单元包括换热板、换热板两侧的密封板以及金属网芯体,换热板中部设有换热腔体,金属网芯体设置在换热腔体内,并通过两侧的密封板密封;所述金属网换热单元的换热腔体外侧设有三个介质流道,一个介质流道与换热腔体连通,另外两个介质流道分别与沿介质流向相邻的两金属网换热单元的换热腔体连通。优选的,所述的金属网芯体包括加强板以及金属网,所述加强板有间隔设置的多片,每相邻的两加强板之间设有金属网;加强板上间隔设有多个引流孔。一种上述三介质编织式金属丝网材料换热器的制作方法,其特征在于:包括如下步骤:a、将退火后的金属丝进行拉直处理,将部分金属丝制成波浪状的预弯金属丝,并进行表面处理;b、将直金属丝从预弯金属丝中间穿过,然后在预弯金属丝和直金属丝的连接处涂抹氮化硼,完成金属网的装配;c、将金属网和加强板放入焊接成形装置中,且相邻两加强板之间放入金属网,进行扩散焊焊接,再向焊接成形装置中充入气体超塑成形,形成金属网芯体;d、将金属网芯体进行深冷处理和反淬火处理;e、切割金属网芯体,并在金属网芯体上设置引流孔和导流板;f、将金属网芯体放入换热板的换热腔体内,并在换热板两侧焊接密封板,形成金属网换热单元;g、对金属网换热单元检验,并对多片金属网换热单元进行组装。优选的,步骤b中所述的金属网的金属丝半径与金属丝间距之间满足如下关系:;其中:为编织结构的相对密度,其值为0.07~0.1;d为相邻金属丝的间距;r为金属丝的半径。优选的,步骤c中所述的焊接成形装置包括承载板、承载板上方的上盖板、两侧的侧支撑板以及定位板,两侧支撑板间隔设置,承载板和上盖板分别位于两侧支撑板的下方和上方,并分别与两侧支撑板的两端固定连接,形成两侧开口的方形筒状,定位板有两块,分别可滑动的安装在两侧开口处并将开口封闭,从而形成一个容积可变的封闭内腔;两侧的侧支撑板上分别连接有进气管和排气管。优选的,步骤c中所述的扩散焊焊接的温度为880~930℃,扩散焊保温时间为120min。优选的,步骤c中所述的气体为氮气,所述超塑成形的压力源为氮气。优选的,步骤d中所述的金属网芯体在-196℃的液氮中并处理180min,完成深冷处理。优选的,步骤d中所述的金属网芯体在175℃的有机介质中保温120min后空冷至室温,完成反淬火处理。与现有技术相比,本发明的三介质编织式金属丝网材料换热器及制作方法所具有的有益效果是:1、本三介质编织式金属丝网材料换热器的金属网换热单元通过金属网芯体实现换热,增大了孔隙率,增大了传热面积,使得换热效率大大提高,金属网换热单元可以作为板式换热器波纹板的替代材料;金属网换热单元对流体扰动形成涡流,提高了传热效率,金属网相比目前已有的蜂窝结构、泡沫结构,具有质量轻、强度高的优点;金属网芯体还对两侧的密封板起到连接作用,大大提高了本换热器的承载能力;金属网换热单元上设有三个介质流道,可实现三种介质的逆流换热,也能对两种介质进行换热,应用范围广,有效地提高了传热效率。2、加强板提高了金属网芯体的承载能力,进而提高了本三介质编织式金属丝网材料换热器的承载能力,提高本换热器的使用范围,也大大提高了本换热器的使用寿命;加强板上设有引流孔,能够避免加强板阻碍流体流动的问题,保证了流体的流动,从而保证了本换热器的换热效率。3、加强板上设有导流板,导流板能够对金属网换热单元内的流体进行导流,使流体能够更顺畅的流入金属网芯体内,并能更顺畅的从金属网芯体内流出。4、本三介质编织式金属丝网材料换热器的制作方法工艺简单,金属网通过金属丝编织而成,相比于目前应用较为前沿的点阵结构,编织式金属网结构具有制作工艺简单、强度高、传热效率高的优点;且在制作编织式金属丝网时,通过制作一部分的预弯金属丝,并夹持固定,让直金属丝从中间穿过,简化了常规经纬编织法中繁琐的挑压工序,操作简单、方法可靠,缩短了制造周期。5、编织结构的相对密度限定在0.07-0.1之间,各方面的性能表现为最优,通过金属丝的半径和金属丝间距来调整编织结构的相对密度,能够极大的提高换热器的性能。6、成形焊接装置既能够进行扩散焊焊接,还能够进行超塑成形,装置结构简单,操作方便,而且效果好。7、应用超塑成形扩散焊制作的编织结构,具有无回弹、无残余应力、成形精度高、强度高等优点,作为换热器的芯体,可以承受更大的载荷,提高了结构的承载能力,另外,结构的整体性好,抗弯刚度大,编织结构在扩散连接后的界面完全消失,使整个结构成为一个整体,极大地提高了结构的抗疲劳和抗腐蚀特性;金属网芯体的超塑成形以氮气为压力源,一方面氮气的价格低,降低了生产成本,另一方面可以促使金属丝表面渗氮,提高金属丝的硬度、耐蚀性、疲劳强度及耐高温性能。8、深冷处理降低了编织结构的热应力,同时组织晶粒细化,提高了金属网硬度、强度和抗冲击性能,使用寿命和尺寸稳定性也得以提高。9、反淬火处理能够防止金属网芯体发生变形,提高了金属网芯体的精度,而且大大提高了金属网芯体的使用寿命。附图说明图1为三介质编织式金属丝网材料换热器的爆炸示意图。图2为三介质编织式金属丝网材料换热器换热单元的爆炸示意图。图3为换热单元的立体结构示意图。图4为安装金属网芯体后的换热板的主视示意图。图5为金属网芯体的立体结构示意图。图6为金属网的立体结构示意图。图7为三介质流向示意图。图8为金属网芯体扩散焊的主视结构示意图。图9为金属网芯体扩散焊的左视结构示意图。图10为金属网芯体超塑成形主视剖视示意图。图中:1、压紧板2、导杆孔3、接管4、螺栓孔5、法兰6、密封板7、换热板8、密封板流道9、换热腔体10、换热板流道11、金属网芯体12、金属网13、导流板14、加强板15、引流孔16、定位板17、进气管18、排气管19、上盖板20、承载板21、侧支撑板。具体实施方式图1~10是本发明的最佳实施例,下面结合附图1~10对本发明做进一步说明。一种三介质编织式金属丝网材料换热器,包括压紧板1、导杆以及接管3,在两压紧板1之间设有多片金属网换热单元,多片金属网换热单元叠加并由导杆和压紧板1压紧固定;金属网换热单元包括换热板7、换热板7两侧的密封板6以及金属网芯体11,换热板7中部设有换热腔体9,金属网芯体11设置在换热腔体9内,并通过两侧的密封板6密封;金属网换热单元的换热腔体9外侧设有三个介质流道,一个介质流道与换热腔体9连通,另外两个介质流道分别与沿介质流向相邻的两金属网换热单元的换热腔体9连通。本三介质编织式金属丝网材料换热器的金属网换热单元通过金属网芯体11实现换热,增大了孔隙率,增大了传热面积,使得换热效率大大提高,金属网换热单元可以作为板式换热器波纹板的替代材料;金属网换热单元对流体扰动形成涡流,提高了传热效率,金属网12相比目前已有的蜂窝结构、泡沫结构,具有质量轻、强度高的优点;金属网芯体11还对两侧的密封板6起到连接作用,大大提高了本换热器的承载能力;金属网换热单元上设有三个介质流道,可实现三种介质的逆流换热,也能对两种介质进行换热,应用范围广,有效地提高了传热效率。具体的:如图1~2所示:压紧板1有两块,两块压紧板1均为长方形板,两压紧板1的下方均设有用于支撑的支撑脚。金属网换热单元有多个,金属网换热单元为长方形,且金属网换热单元的长和宽均小于压紧板1的长和宽,多块金属网换热单元均设置在两块压紧板1之间。压紧板1上设有三个接管3,接管3上设有法兰5,接管3用于换热器与流体管道连接,法兰5方便与流体管道的固定。金属网换热单元上设有三个介质流道,且每相邻的两个金属网换热单元的介质流道相连通,与两个压紧板1的金属网换热单元的三个介质流道分别与接管3连通,该换热器可以在三种介质或两种介质之间进行换热,使用方便。两块压紧板1的外沿均设有螺栓孔4,两块压紧板1通过螺栓固定连接,两压紧板1的上下两侧分别设有一个导杆孔2,且每个金属网换热单元的上下两侧均设有与导杆孔2相配合的导杆槽,金属网换热单元通过两压紧板1和导杆压紧固定。换热板7和密封板6均为长方形板,换热板7的厚度大于密封板6的厚度,换热腔体9设置在换热板7的中部,金属网芯体11安装在换热板7的换热腔体9内。换热板7和两侧的密封板6密封连接,金属网芯体11分别与换热板7和密封板6相连,增大了金属网换热单元的承载能力,进而提高了该换热器的承载能力,使该换热器的适用范围大大增加。每个密封板6上设有三个密封板流道8,每个换热板7上设有两个换热板流道10,密封板6上的两个密封板流道8与换热板7上的换热板流道10连通,密封板6上的第三个密封板流道8与换热板7上的换热腔体9连通,从而使两两介质之间形成逆流换热,有效地提高了换热效率。如图3~4所示:金属网芯体11包括加强板14以及金属网12。加强板14有间隔设置的多块,多块加强板14均竖直设置。加强板14的宽度与换热板7厚度相等,加强板14的长度小于换热板7的长度。每相邻的两加强板14之间设有金属网12,金属网12与加强板14固定连接,从而形成金属网芯体11。金属网芯体11具有大孔隙率,增大了传热面积,使得换热效率大大提高,而且又有良好的承载能力,可以作为板式换热器波纹板的替代材料;而且金属网12结构相比目前已有的蜂窝结构、泡沫结构,具有轻质、高强等优点,而相比目前应用较为前沿的点阵结构,金属网12的结构具有制作工艺简单,强度高,传热效率高等优点。如图5所示:加强板14的两端分别设有导流板13,导流板13的宽度与加强板14的宽度相等,导流板13一端与加强板14固定连接,另一端向与密封板6连通的密封板流道8倾斜,导流板13对进入换热腔体9的流体和流出换热腔体9的流体进行导向,从而使流体更好的流入和流出换热腔体9。加强板14上间隔设有多个引流孔15,引流孔15能够使整个换热腔体9连通,方便流体在换热腔体9内的流动,进而提高了流体的换热效率。如图6所示:金属网12为采用类似经纬编织的方法编织而成,且每相邻的两金属丝间的间距相等。在制作编织式金属丝网时,通过制作一部分的预弯金属丝,并夹持固定,让直金属丝从中间穿过,简化了常规经纬编织法中繁琐的挑压工序,操作简单、方法可靠,缩短了制造周期。如图7所示:每个金属网换热单元上的三个介质流道中,有一个与该金属网换热单元的换热腔体9连通,另两个分别与沿介质流向相邻的两个金属网换热单元的换热腔体9连通,使得每个介质流道均是回流型,增大了介质的流速和湍流程度,从而提高了传热效率。同时,每相邻的两金属网换热单元内介质流动方向相反,实现了三介质相互之间的逆流换热,换热效率高。上述三介质编织式金属丝网材料换热器的制作方法,包括如下步骤:1、将退火后的金属丝进行拉直处理,将部分金属丝制成波浪状的预弯金属丝,并进行表面处理。金属网12的金属丝半径与金属丝间距之间满足如下关系:;其中:为编织结构的相对密度,其值为0.07~0.1;d为相邻金属丝的间距;r为金属丝的半径。编织结构相对密度值越小时,特征表现为越细长,越容易发生屈曲变形,理论上相对密度最低值应在0.07左右。另外,实验表明相关密度在0.1-0.3时,表现为高的摩擦因素,介质从其中穿过时可能引起动能的大量损失。而相对密度超过0.3时,编织结构孔隙率非常低,不利于介质在编织结构中的流动。因此,将编织结构的相对密度限定在0.07-0.1之间,各方面的性能表现为最优。结构紧凑型板式换热器,一般板间距为4-6mm。另外,考虑到金属丝的制作成本,其直径不应该过小,而且金属丝直径过小时,相应的金属丝间距减小,介质通过时容易引起堵塞问题。综合上述编织结构的相对密度、板间距以及金属丝的制作成本等因素,将金属丝直径优化为0.25mm,金属丝间距为2mm,板间距为6mm,相对密度为0.098。根据金属丝的直径以及金属丝的间距,制作预弯金属丝模具。对金属丝进行退火处理,并将退火处理后的金属丝进行拉直处理,然后通过液压机和模具将部分金属丝制成预弯金属丝,预弯金属丝上间隔设有多个向同一侧凸出的弧形,并根据需要对预弯金属丝进行切割以及对切割面的打磨处理,预弯金属丝两端面的粗糙度达到3.2um,预弯金属丝的曲率半径为0.125mm。2、将直金属丝从预弯金属丝中间穿过,然后在预弯金属丝和直金属丝的连接处涂抹氮化硼,完成金属网12的装配。在制作编织式金属丝网时,并夹持固定预弯金属丝,让直金属丝从中间穿过,简化了常规经纬编织法中繁琐的挑压工序,操作简单、方法可靠,缩短了制造周期。3、将金属网12和加强板14放入焊接成形装置中,且相邻两加强板14之间放入金属网12,进行扩散焊焊接,再向焊接成形装置中充入气体超塑成形,形成金属网芯体11。如图8~9所示:焊接成形装置包括承载板20、承载板20上方的上盖板19、两侧的侧支撑板21以及定位板16,两侧支撑板21间隔设置,承载板20和上盖板19分别位于两侧支撑板21的下方和上方,并分别与两侧支撑板21的两端固定连接,形成两侧开口的方形筒状,定位板16有两块,分别可滑动的安装在两侧开口处并将开口封闭,从而形成一个容积可变的封闭内腔。两侧的侧支撑板21上分别连接有进气管17和排气管18,且进气管17和排气管18可以单独控制通断。将装配好的金属网12放置在承载板20上,预弯金属丝长度方向与水平面垂直,然后放置加强板14,并在金属网12和加强板14的连接处涂抹氮化硼,注意保持连接处表面的清洁度。准确的在两侧的加强板14外侧放置定位板16并加以固定,且两侧的加强板14与定位板16间隔设置,进气管17和排气管18均设有两组,两组进气管17分别连接两侧的加强板14与定位板16间的空腔以及焊接成形装置的内腔,两组排气管18也分别连接两侧的加强板14与定位板16间的空腔以及焊接成形装置的内腔。通过对上盖板19以及两侧支撑板21施加压力实现整个装配件的固定,继而在扩散焊加热炉中进行焊接。两侧的加强板14的厚度为中部加强板14厚度的一半。焊接过程为:首先将焊接成形装置的内腔抽真空,然后以20℃/min的速度加热到880~930℃。打开进气管17向两侧的加强板14与定位板16之间充入氮气,使得2MPa的压力作用在两侧加强板14的外侧,并保温120min,完成扩散焊焊接过程。如图10所示:焊接完成后继续保持温度不变,进行超塑成形处理。打开进气管17,向相邻加强板14之间的空腔内充入氮气,两侧的加强板14在压力作用下向定位板16移动,金属网12在加强板14的带动下拉伸,完成超塑成形,最终形成金属网芯体11。应用超塑成形扩散焊制作的编织结构,具有无回弹、无残余应力、成形精度高、强度高等优点,作为换热器的芯体,可以承受更大的载荷,提高了结构的承载能力。另外,结构的整体性好,抗弯刚度大,编织结构在扩散连接后的界面完全消失,使整个结构成为一个整体,极大地提高了结构的抗疲劳和抗腐蚀特性。金属网芯体11的超塑成形以氮气为压力源,一方面氮气的价格低,降低了生产成本,另一方面可以促使金属丝表面渗氮,提高金属丝的硬度、耐蚀性、疲劳强度及耐高温性能。4、将金属网芯体11进行深冷处理和反淬火处理。将金属网芯体11从焊接成形装置内取出,采用深冷处理工艺进行深冷处理。首先,放入深冷箱的液氮中,深冷处理温度为-196℃,保温180min后迅速取出并转移到QCW-01型高温有机介质中,进行反淬火处理,升温至175℃,并保温120min,然后空冷至室温。进行深冷处理的目的是为了降低连接处的残余应力,细化晶粒,并提高硬度、强度和抗冲击性能。深冷处理是为了降低编织结构的热应力,同时组织晶粒细化,提高了金属网12的硬度、强度和抗冲击性能,使用寿命和尺寸稳定性也得以提高。反淬火处理能够防止金属网芯体11发生变形,提高了金属网芯体11的精度,而且大大提高了金属网芯体11的使用寿命。5、切割金属网芯体11,并在金属网芯体11上设置引流孔15和导流板13。通过线切割方式,对金属网芯体11进行分割,并在加强板14上开设引流孔15,引流孔15的直径为0.8mm。然后采用脉冲激光焊将导流板13焊接在加强板14上,并进行除油、除锈处理。6、将金属网芯体11放入换热板7的换热腔体9内,并在换热板7两侧焊接密封板6,形成金属网换热单元。在密封板6与换热板7上分别开设密封板流道8和换热板流道10,同时需对换热板7和密封板6进行表面处理,达到平整且光滑,再用丙酮清洗去除表面油污。将金属网芯体11放置在换热板7的换热腔体9内,分别在两侧的密封板6、金属网芯体11和换热板7的连接处涂抹一层氮化硼,完成金属网换热单元的装配,再用与上述扩散焊相同的工艺,实现密封板6、金属网芯体11以及换热板7的固定连接,形成金属网换热单元。可能泄漏的部位仅在换热板7与密封板6之间的连接处,换热板7和密封板6通过扩散焊焊接,保证了该部位的密封,提高了整体的密封性能,有效的降低了泄漏的可能,金属网芯体11也与密封板6和换热板7焊接,提高了承载能力。7、对金属网换热单元检验,并对多片金属网换热单元进行组装。采用X射线探伤检测密封板6与换热板7连接处的内部缺陷,并进行气密性实验,确保扩散焊的质量。然后将多个金属网换热单元通过压紧板1固定,完成换热器的制作。打开连接相邻加强板14之间空腔的进气管17,向其中充入氮气作为超塑成形的压力源。由于相邻加强板14之间的空腔内压力不同于加强板14与定位板16之间的空腔内压力,因此两侧的加强板14在压力作用下向定位板16移动,金属网12在加强板14的带动下,逐渐超塑成形。其中,采用微机控制超塑成形的压力,保证超塑成形在最佳应变速率下进行。超塑成形处理一般采用氩气作为压力源,本实施例中的超塑成形采用氮气的原因是一方面氮气成本低,另一方面可以促使金属丝表面渗氮,提高金属丝的硬度、耐蚀性、疲劳强度及耐高温性能。以上所述,仅是本发明的较佳实施例而已,并非是对本发明作其它形式的限制,任何熟悉本专业的技术人员可能利用上述揭示的技术内容加以变更或改型为等同变化的等效实施例。但是凡是未脱离本发明技术方案内容,依据本发明的技术实质对以上实施例所作的任何简单修改、等同变化与改型,仍属于本发明技术方案的保护范围。