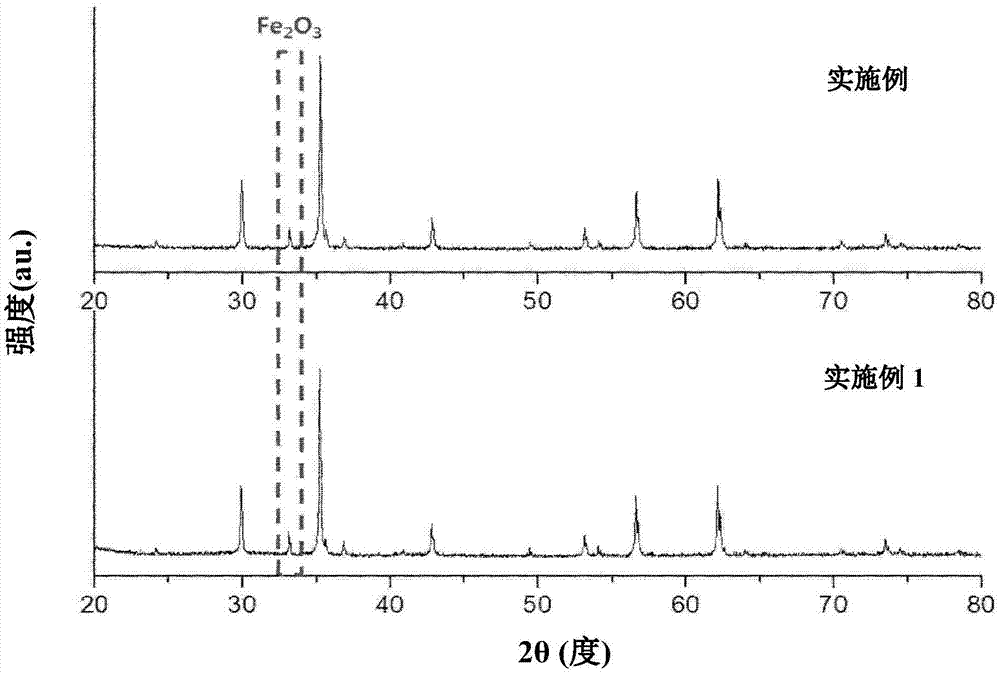
[相关申请的交叉引用]本申请要求于2017年05月04日在韩国知识产权局提交的韩国专利申请no.10-2017-0056741和基于该专利的优先权于2018年04月25日在韩国知识产权局再次提交的韩国专利申请no.10-2018-0047836的优先权,这两项申请的公开内容通过引用并入本说明书中。本发明涉及一种用于氧化脱氢的催化剂的制备方法和使用所述催化剂进行氧化脱氢的方法。根据所述用于氧化脱氢的催化剂的制备方法,当制备用于氧化脱氢的催化剂时,非活性α-fe2o3晶体结构的比例降低,使得制备的催化剂可以具有高活性。此外,当制备的催化剂用于制备丁二烯时,可以减少副反应,并且可以提高丁二烯的选择性,从而提高丁二烯的生产率。
背景技术:
:1,3-丁二烯是石油馏分的主要基础产物,是用于制备合成橡胶的代表性原料,并且其价格随着石化工业的供需迅速波动。1,3-丁二烯的制备方法的实例包括石脑油裂化、正丁烯的直接脱氢、正丁烯的氧化脱氢等。根据通过正丁烯的氧化脱氢制备1,3-丁二烯的方法,在金属氧化物催化剂的存在下丁烯与氧气反应生成1,3-丁二烯和水。在这种情况下,由于反应而生成的水是稳定的。因此,所述制备方法在热力学上非常有利。此外,与直接脱氢不同,由于正丁烯的氧化脱氢是放热反应,因此,反应可以在低温下进行。因此,可以在减少能量消耗的同时以高产率得到1,3-丁二烯。此外,在氧化脱氢的情况下,由于添加氧化剂,因此,通过使催化剂中毒而缩短催化剂寿命的碳沉积物的产生减少。此外,由于氧化剂容易除去,因此,使用氧化脱氢制备1,3-丁二烯的方法非常适合商业化。通常,公知的作为用于丁烯的氧化脱氢的催化剂的铁酸盐催化剂由共沉淀法合成。由共沉淀法合成的催化剂在氧化脱氢过程中以活性晶体结构和非活性fe2o3晶体结构存在。因此,需要一种降低催化剂合成过程中非活性fe2o3晶体结构的比例的技术,或者即使非活性晶体结构以一定量以上存在,也仍然制备具有优异的活性的催化剂的技术。另外,当使用共沉淀法制备催化剂时,由于技术和空间限制,在单一制备过程中制备的催化剂的量少。因此,为了得到所需的量的催化剂,必须重复数次相同的制备过程。这使得难以提高生产率。为了克服这个问题,已经采用在催化剂合成过程中浓缩催化剂的方法。然而,在这种情况下,非活性晶体结构的比例增加,并且制备的催化剂的活性和稳定性会降低。[现有技术文献][专利文献]kr10-0847206b1kr10-1071230b1技术实现要素:技术问题因此,鉴于上述问题而做出本发明,本发明的一个目的是提供一种用于氧化脱氢的催化剂的制备方法。根据所述用于氧化脱氢的催化剂的制备方法,可以提供即使非活性fe2o3晶体结构以一定水平存在也在氧化脱氢中表现出优异的活性的催化剂。此外,即使在使用共沉淀法的制备过程中,也可以降低非活性fe2o3晶体结构的比例。本发明的另一目的是提供一种使用采用所述用于氧化脱氢的催化剂的制备方法制备的催化剂来进行氧化脱氢的方法。根据使用所述催化剂进行氧化脱氢的方法,当进行氧化脱氢时,可以减少副反应,并且可以显著提高丁二烯的产率或丁二烯的选择性。上述目的和其它目的可以通过下面描述的本公开实现。技术方案根据本发明的一个方面,提供一种用于氧化脱氢的催化剂的制备方法,包括:通过向水中添加三价阳离子铁(fe)前体和二价阳离子金属(a)前体制备金属前体水溶液的步骤;通过将所述金属前体水溶液和碱性水溶液添加到含有ph为6以上的水溶液或水的共沉淀浴中使铁和金属(a)共沉淀的步骤;以及对共沉淀后的共沉淀物进行灼烧的步骤,其中,在共沉淀步骤过程中、在完成共沉淀步骤之后、或从共沉淀步骤过程中直至完成共沉淀步骤之后进行向共沉淀浴中供应惰性气体或空气的过程。根据本发明的另一方面,提供一种进行氧化脱氢的方法,包括如下步骤:通过使包含氧气和含有正丁烯的c4混合物的反应物通过填充有根据上述制备方法的用于氧化脱氢的催化剂的反应器来进行氧化脱氢。有益效果从上面的描述显而易见的是,本发明有利地提供一种用于氧化脱氢的催化剂的制备方法和使用所述催化剂进行氧化脱氢的方法。根据本发明,当使用共沉淀法制备用于氧化脱氢的催化剂时,进行在特定时间点向共沉淀浴中注入惰性气体或空气的过程以提高催化剂的活性。任选地,当通过共沉淀浴的下部供应金属前体水溶液时,催化剂中非活性fe2o3晶体结构的比例降低,进一步提高催化活性。此外,当使用制备的催化剂进行丁烯的氧化脱氢时,可以减少副反应,并且可以提高丁二烯的选择性和丁二烯的产率。因此,本发明可以以高生产率提供高质量的丁二烯。附图说明图1是示出根据实施例1(空气供应)和比较例1(常规合成方法)制备的铁酸锌催化剂的晶体结构的xrd数据;图2是示出根据实施例2(n2供应+通过下部供应金属前体水溶液)、实施例3(空气供应+通过下部供应金属前体水溶液)和比较例1(常规合成方法)制备的铁酸锌催化剂的晶体结构的xrd数据;图3是示出根据实施例1至3和比较例1制备的共沉淀浆料的粒度的图。具体实施方式下文中,将详细描述根据本发明的用于氧化脱氢的催化剂的制备方法。本发明人证实,当使用共沉淀法合成铁酸盐催化剂时,生成能够影响用于氧化脱氢的催化剂的活性的非活性fe2o3晶体结构。本发明人研究了一种即使当存在一定量以上的非活性fe2o3晶体结构时也能够提高氧化脱氢过程中的催化活性的方法,以及一种能够降低非活性晶体结构的比例的方法。结果,本发明人证实,当在催化剂合成过程中在特定的时间点进行向共沉淀溶液中供应氮气(n2)或空气的步骤时,以及任选地,当在共沉淀步骤中通过共沉淀浴的下部供应金属前体水溶液时,对应于铁酸盐催化剂前体的共沉淀物的分散程度最大化,并且铁酸盐催化剂中非活性fe2o3晶体结构的比例降低。因此,本发明人证实,当使用本发明的制备方法时,上述问题得以解决,并且基于此而完成本发明。例如,根据本发明的用于氧化脱氢的催化剂的制备方法包括:通过向水中添加三价阳离子铁(fe)前体和二价阳离子金属(a)前体制备金属前体水溶液的步骤;通过将所述金属前体水溶液和碱性水溶液添加到含有ph为6以上的水溶液或水的共沉淀浴中使铁和金属(a)共沉淀的步骤;以及对共沉淀后的共沉淀物进行灼烧的步骤,其中,在共沉淀步骤过程中、在完成共沉淀步骤之后、或从共沉淀步骤过程中直至完成共沉淀步骤之后进行向共沉淀浴中供应惰性气体或空气的过程。例如,向共沉淀浴中供应惰性气体或空气的过程可以是:在使用诸如叶轮的搅拌方式搅拌共沉淀浴中的溶液的同时将惰性气体或空气供应至共沉淀浴中的过程;将管道(pipe)连接至共沉淀浴的下部,并通过该管道将惰性气体或空气供应至共沉淀浴中的过程;或在共沉淀浴中提供管路(tube),例如,特氟隆管路,并通过该管路将惰性气体或空气供应至溶液中的过程。此外,管道和管路的内径可以为,例如,1/8"至1/2"或1/6"至1/2",对它们的位置没有特别地限制,只要管道和管路位于共沉淀浴的下部,即,在共沉淀浴中的溶液表面下方即可。例如,管道和管路可以位于共沉淀浴的下部,具体地位于从共沉淀浴的底部至溶液的表面的距离的一半以内。下文中,将逐步地详细描述用于氧化脱氢的催化剂的制备方法。例如,在金属前体水溶液的制备步骤中,三价阳离子铁(fe)前体和二价阳离子金属(a)前体可以独立地是选自硝酸盐、铵盐、硫酸盐和氯化物中的一种或多种。优选地,考虑到大规模生产所需的制造成本和容易购买性,前体可以独立地是硝酸盐或氯化物。例如,二价阳离子金属(a)可以是选自铜(cu)、镭(ra)、钡(ba)、锶(sr)、钙(ca)、铍(be)、锌(zn)、镁(mg)、锰(mn)和钴(co)中的一种或多种,优选地为在丁烯的氧化脱氢中表现出高活性的锌(zn)或锰(mn),在丁二烯的产率或丁二烯的选择性方面,最优选地为锌(zn)。将三价阳离子铁(fe)前体和二价阳离子金属(a)前体在水中混合以制备水溶液。当金属前体溶解在水中并且以液相存在时,铁与二价阳离子金属之间的离子交换容易,使得可以容易地得到所需的共沉淀物。例如,水可以是蒸馏水。通常,金属前体水溶液中的三价阳离子铁(fe)前体和二价阳离子金属(a)前体的混合比优选地为1.5摩尔至10摩尔、1.5摩尔至4摩尔或1.5摩尔至2.5摩尔的三价阳离子铁(fe)前体比1摩尔的二价阳离子金属(a)前体。在所述范围内,促进氧化脱氢中活性晶体结构的形成,并且可以提高催化活性。另外,金属前体水溶液的ph可以为,例如,0至4、1至3或1至2。在所述范围内,可以稳定地形成所需的活性成分。在制备金属前体水溶液之后,制备用于使铁和金属(a)共沉淀的含有ph为6以上的水溶液或水的共沉淀浴,并且将金属前体水溶液添加到共沉淀浴中以使铁和金属(a)共沉淀。例如,在共沉淀步骤中,ph为6以上的水溶液可以是选自氢氧化钠水溶液和氨水中的一种或多种。当在将金属前体水溶液逐滴添加至共沉淀浴中之前将共沉淀浴的ph调节至6以上、6至10或7至8时,由于添加金属前体水溶液而引起的初始ph变化的宽度减少,因此,可以稳定地形成具有均匀的组成的催化剂。例如,在本发明的催化剂的制备方法中,可以在共沉淀步骤的过程中进行将惰性气体或空气注入到共沉淀浴中的过程。通过进行所述过程,氧气和金属前体可以均匀地结合,提高混合效果,从而提高氧化脱氢的反应活性。例如,当根据本发明制备的催化剂用于进行丁烯的氧化脱氢时,可以提高丁烯的转化率、丁二烯的选择性和丁二烯的产率,并且可以减少副反应产物的生成。此外,具有在相对低的热点温度下表现出优异的反应活性的优点。在本发明中,热点指在反应过程中装载在反应器中的催化剂床中具有最高温度的部分。对将惰性气体或空气注入到共沉淀浴中的条件没有特别地限制。例如,基于共沉淀浴中的溶液的体积,惰性气体或空气可以以0.1l/分钟至2l/分钟或0.5l/分钟至1l/分钟的速度经1分钟至300分钟、10分钟至200分钟、30分钟至100分钟或40分钟至90分钟注入到共沉淀浴中。在所述范围内,可以制备具有小的粒度和均匀的粒度分布的催化剂,并且可以增加活性晶体结构的比例。例如,在共沉淀步骤中,共沉淀溶液的ph优选保持在7至10或7至8。在所述范围内,催化剂的活性或稳定性会优异。因此,在共沉淀步骤中,优选同时添加碱性水溶液和金属前体水溶液,以将ph保持在7至10。例如,在共沉淀步骤中,可以将金属前体水溶液和碱性水溶液一起逐滴添加至共沉淀浴中以使铁和金属(a)共沉淀。例如,碱性水溶液可以是选自氢氧化钠和氨水中的一种或多种。在本发明中,“逐滴添加”指将两种以上的溶液逐滴添加至相同的点或容器中。“相同的点”包括:从滴落点开始至滴落的溶液溅落在现有溶液的表面上的点的范围,或者从滴落点开始至滴落的溶液降落到现有溶液的表面同时保持其性能而不与现有溶液混合的点的范围。作为另一实例,在共沉淀步骤中,可以通过共沉淀浴的下部供应金属前体水溶液,并且可以将碱性水溶液逐滴添加至共沉淀浴中以使铁和金属(a)共沉淀。当将金属前体水溶液与碱性水溶液分别地直接加入到共沉淀浴中时,金属前体向设置在共沉淀浴中的溶液中扩散的速度增加。因此,可以形成均匀的晶体结构,并且可以降低非活性晶体结构的比例,使得可以提供表现出高活性的催化剂。在本发明中,对将金属前体水溶液供应至共沉淀浴中的方法没有特别地限制,只要将金属前体水溶液直接引入至共沉淀浴中的溶液的表面的下方而不引入至共沉淀浴中的溶液的表面即可。例如,金属前体水溶液可以通过连接至共沉淀浴的下部的管道供应,或者通过设置为其一端浸入共沉淀浴中的溶液中的管路供应。在这种情况下,由于通过共沉淀浴的下部供应金属前体水溶液,因此,可以提高金属前体向溶液中扩散的速度。例如,共沉淀物在共沉淀浴中为浆料状态。浆料粒子的中值粒度(mediansize)可以为7μm以下或1μm至7μm,众数粒度(modesize)可以为7μm以下或1μm至7μm。在所述范围内,与常规的铁酸锌催化剂相比,可以以高产率得到丁二烯。在本发明中,使用激光粒度仪-960(horiba,co.,ltd.)测量浆料粒子的中值粒度和众数粒度。测量所需要的折射率基于浆料状态下最丰富的铁(fe)来设定。在对共沉淀步骤中制备的由共沉淀溶液得到的共沉淀物进行灼烧之前,可以对共沉淀溶液进行搅拌、老化、或者搅拌并老化的步骤。在这种情况下,可以得到足够量的共沉淀物。例如,在根据本发明的催化剂的制备方法中,在完成共沉淀步骤之后,可以进行在搅拌共沉淀溶液的同时供应惰性气体或空气的过程。在这种情况下,制备的催化剂可以在氧化脱氢中表现出优异的活性。例如,当催化剂用于进行丁烯的氧化脱氢时,可以提高丁烯的转化率和丁二烯的选择性,并且可以减少副反应产物的生成。此外,具有在相对低的热点温度下表现出优异的反应活性的优点。作为另一实例,在根据本发明的催化剂的制备方法中,在使所添加的金属前体水溶液和碱性水溶液共沉淀的步骤中,可以进行将惰性气体或空气注入到共沉淀浴中的过程。在完成共沉淀步骤之后,可以进行在搅拌共沉淀溶液的同时向共沉淀浴中另外注入惰性气体或空气的过程。在这种情况下,催化剂可以在氧化脱氢中表现出优异的活性。作为另一实例,在根据本发明的催化剂的制备方法中,可以进行从将金属前体水溶液和碱性水溶液添加到共沉淀浴中并共沉淀的共沉淀步骤至完成共沉淀步骤之后搅拌共沉淀溶液的步骤为止,向共沉淀浴中连续注入惰性气体或空气的过程。换言之,可以在从共沉淀步骤至完成共沉淀步骤为止进行向共沉淀浴中连续注入惰性气体或空气的过程。在这种情况下,催化剂可以在氧化脱氢中表现出优异的活性。例如,惰性气体可以是氮气(n2)。例如,搅拌并老化可以独立地进行30分钟至3小时或30分钟至2小时,但是不限于此。可以通过对共沉淀溶液进行干燥、过滤、或者干燥并过滤来得到共沉淀物。包含afe2o4晶体结构的催化剂可以通过灼烧共沉淀物来得到。对干燥方法和过滤方法没有特别地限制,只要这些方法是本领域中通常使用的即可。例如,可以采用真空过滤进行过滤过程。根据需要,在完成过滤过程之后,可以进行洗涤过程。例如,干燥过程可以使用常规烘干机在60℃至100℃、70℃至100℃或80℃至100℃下进行12小时至20小时、14小时至20小时或14小时至18小时。例如,灼烧过程可以使用常规的灼烧炉在400℃至800℃、500℃至800℃或550℃至750℃下进行1小时至10小时、3小时至8小时或5小时至7小时,但是不限于此。通过灼烧过程得到的催化剂可以包含afe2o4晶体结构。作为一个具体的实例,催化剂可以表现出包含afe2o4晶体结构和α-fe2o3晶体结构的混合相。例如,根据本发明的一个实施方案得到的催化剂可以包含93.7重量%以上、94.0重量%以上、94.5重量%以上、94.8重量%以上或94.8重量%至96.0重量%的afe2o4晶体结构;以及6.3重量%以下、6.0重量%以下、5.5%重量%以下、5.2重量%以下或4.0重量%至5.2重量%的α-fe2o3晶体结构。在本发明中,afe2o4与α-fe2o3的重量比可以由xrd衍射分析中afe2o4峰(2θ:29.5°至30.5°,34.5°至35.5°,42°至43°,52.5°至53.5°,56.5°至57.5°,62°至63°)的强度和α-fe2o3峰(2θ:33°至34°)的强度计算。另外,在xrd衍射分析中,作为各个峰存在的平面上的衍射峰,afe2o4峰存在于(220)、(311)、(222)、(400)、(422)、(511)和(440)位置,α-fe2o3峰存在于(104)位置。作为一个具体的实例,根据本发明的催化剂的制备方法包括:1)通过向水中添加三价阳离子铁(fe)前体和二价阳离子金属(a)前体制备金属前体水溶液的步骤;2)通过将所述金属前体水溶液和碱性水溶液逐滴添加到含有ph为6至10的水溶液或水的共沉淀浴中使铁和金属(a)共沉淀的步骤;以及3)对在共沉淀步骤中得到的共沉淀溶液进行搅拌、或者搅拌并老化,并对共沉淀后的共沉淀物进行灼烧的步骤,其中,在共沉淀步骤和搅拌步骤的过程中进行向共沉淀浴中注入氮气或空气的过程。作为另一具体的实例,根据本发明的催化剂的制备方法包括:1)通过向水中添加三价阳离子铁(fe)前体和二价阳离子金属(a)前体制备金属前体水溶液的步骤;2)在向共沉淀浴中逐滴添加碱性水溶液的同时,通过含有ph为6至10的水溶液或水的共沉淀浴的下部供应所述金属前体水溶液,以使铁和金属(a)共沉淀的步骤;以及3)对在共沉淀步骤中得到的共沉淀溶液进行搅拌、或者搅拌并老化,并对共沉淀后的共沉淀物进行灼烧的步骤,其中,在共沉淀步骤和搅拌步骤的过程中进行向共沉淀浴中注入氮气或空气的过程。另外,根据本发明的制备方法制备的催化剂满足下面的等式1:[等式1]0≤t2/t1≤0.80,其中,t2表示基于100重量%的催化剂的总量,根据本发明的催化剂的制备方法制备的催化剂中包含的α-fe2o3晶体结构的含量,所述制备方法包括将金属前体水溶液供应至共沉淀浴的下部并注入惰性气体或空气的步骤;t1表示基于100重量%的催化剂的总量,以如下制备方法制备的催化剂中包含的α-fe2o3晶体结构的含量,该制备方法除了将金属前体水溶液和碱性水溶液逐滴添加至共沉淀浴中,并且省略注入惰性气体或空气的过程之外,与上述催化剂的制备方法相同;并且α-fe2o3晶体结构的含量通过测量在催化剂的xrd衍射分析中对应于α-fe2o3晶体结构的峰(2θ:33°至34°)的强度来确定。更优选地,t2/t1可以为0至0.75、0至0.70或0至0.68。在所述范围内,催化剂可以具有优异的活性。此外,当催化剂用于进行氧化脱氢时,可以提高丁二烯的产率或丁二烯的选择性,可以以高生产率提供高质量的丁二烯,并且催化剂可以在相对低的热点温度下表现出优异的反应活性。根据本发明制备的用于氧化脱氢的催化剂可以用于进行丁烯的氧化脱氢以得到丁二烯。下文中,将描述根据本发明的进行氧化脱氢的方法。例如,根据本发明的进行氧化脱氢的方法可以包括如下步骤:通过使包含氧气和含有正丁烯的c4混合物的反应物通过填充有根据所述制备方法的用于氧化脱氢的催化剂的反应器来进行氧化脱氢。例如,进行氧化脱氢的方法可以是制备丁二烯的方法。作为一个具体的实例,根据本发明的丁二烯的制备方法可以包括:i)用用于氧化脱氢的催化剂填充反应器的步骤;以及ii)通过使包含氧气和含有正丁烯的c4混合物的反应物连续通过填充有所述催化剂的反应器的催化剂层来进行氧化脱氢的步骤。例如,c4混合物包含选自包括2-丁烯(反式-2-丁烯和顺式-2-丁烯)和1-丁烯的正丁烯异构体中的一种或多种,还可以任选地包含正丁烷或c4萃余液-3。反应物还可以包含选自空气、氮气、蒸汽和二氧化碳中的一种或多种。作为一个具体的实例,反应物可以包含摩尔比为1:0.01至1.5:1至15:1至10或1:0.5至1.2:5至15:1至10的c4混合物、氧气、蒸汽和氮气。在所述范围内,可以容易地控制反应热,并且可以提高丁二烯的产率。例如,氧化脱氢反应可以在250℃至430℃、300℃至425℃或350℃至425℃的反应温度下进行。在所述范围内,可以提高反应效率而不显著增加能量消耗,由此,可以提高丁二烯的生产率并且可以提高催化剂的活性和安全性。例如,氧化脱氢反应可以在基于正丁烯的气时空速(ghsv)为50h-1至2,000h-1、50h-1至1,500h-1或50h-1至1,000h-1下进行。在所述范围内,反应效率优异,因此,转化率、选择性和产率会优异。下文中,将参照下面的优选实施例更详细地描述本发明。然而,提供这些实施例仅用于说明的目的并且不应理解为限制本发明的范围和精神。此外,对本领域技术人员显而易见的是,在不脱离本发明的精神和范围的情况下,可以进行各种改变和修改,并且这些改变和修改也在所附权利要求书的范围之内。[实施例]实施例1将0.122摩尔的氯化锌(zncl2)和0.243摩尔的氯化铁(fecl36h2o)溶解在12.778摩尔的水中以制备金属前体水溶液。在这种情况下,作为金属前体水溶液中含有的金属组分,fe与zn的摩尔比为2:1。然后,在供应氮气的同时,将金属前体水溶液与9重量%至10重量%的氨水逐滴添加到含有蒸馏水的共沉淀浴中以使铁和锌共沉淀。在这种情况下,基于1升的蒸馏水,以1l/分钟的注入速率供应氮气80分钟至90分钟。在共沉淀完成之后,将共沉淀溶液搅拌1小时,使得可以实现充分的共沉淀。在这种情况下,基于1升的蒸馏水,以0.5l/分钟的注入速率供应氮气。之后,停止搅拌,并将共沉淀溶液在室温下静置1小时以使所有的沉淀物沉淀。换言之,进行用于制备共沉淀物的老化过程。使用真空过滤器对搅拌并老化后的共沉淀溶液进行真空过滤,以得到共沉淀物。洗涤得到的共沉淀物,接着在90℃下干燥24小时。将干燥后的共沉淀物放入灼烧炉中,并在650℃下热处理5小时以制备铁酸锌催化剂。比较例1除了省略向共沉淀浴中注入氮气的过程之外,进行与实施例1中相同的过程。[试验例]使用根据实施例1和比较例1制备的铁酸锌催化剂进行下面的试验分析。试验例1:xrd分析进行xrd分析以确认根据实施例1和比较例1制备的催化剂的晶体结构以及晶体结构的比例。分析结果示于图1和下面的表1中。[表1]类别实施例1比较例1znfe2o4晶体结构(重量%)96.092.4α-fe2o3晶体结构(重量%)4.07.6参照图1和表1,根据实施例1和比较例1制备的铁酸锌催化剂表现出包含znfe2o4晶体结构和α-fe2o3晶体结构的混合相。在根据实施例1的催化剂的情况下,α-fe2o3晶体结构的比例非常低。基于这些结果,可以看出,在共沉淀浴中供应氮气对铁酸盐类催化剂的晶体结构具有有利的影响。试验例2:氧化脱氢使用根据实施例1和比较例1制备的铁酸锌催化剂进行氧化脱氢以制备丁二烯。实施例1a至实施例1c和比较例1a至比较例1d的结果示于下面的表2中。将根据实施例1或比较例1制备的催化剂在直径为1.8cm的金属管式反应器中以30cc的体积固定在催化剂床上,并将作为反应物的含有40重量%的顺式-2-丁烯和60%重量的反式-2-丁烯的2-丁烯混合物与氧气引入到反应器中,然后将氮气和蒸汽引入到反应器中。在反应物中,氧气/丁烯、蒸汽/丁烯和氮气/丁烯的摩尔比分别设定为1、8和1。将在340℃下通过蒸发器中的水的蒸发产生的蒸汽与反应物一起引入到反应器中。使用用于液体的质量流量控制器将丁烯混合物的进料速率设定为0.625cc/分钟,使用用于气体的质量流量控制器来控制氧气和氮气的进料速率,并使用液体泵控制蒸汽的进料速率。在气时空速(ghsv)设定为66h-1的反应器中,反应在大气压力(压力表为0)和下面的表2中所示的温度条件下进行。完成反应之后,使用气相色谱(gc)分析产物。在混合物中,丁烯的转化率(be_conv.)、1,3-丁二烯的选择性(s_bd)、1,3-丁二烯的产率(y)、cox的选择性(s_cox)、重组分的选择性(s_heavy)以及o2的转化率(o2_conv.)分别根据下面的等式2至等式4计算。为了测量热点温度,将热电偶(thermo-couple;tc)连接至传动装置,并且在进行扫描的同时以恒定速度从反应器顶部移动至反应器底部。[等式2]转化率(%)=(反应的丁烯或氧气的摩尔数/供应的丁烯或氧气的摩尔数)×100[等式3]选择性(%)=(生成的1,3-丁二烯、cox或重组分的摩尔数/反应的丁烯的摩尔数)×100[等式4]丁二烯的产率(%)=(生成的1,3-丁二烯的摩尔数/供应的丁烯的摩尔数)×100[表2]参照表2,在实施例1和比较例1中,在富氧条件下观察到最高活性。与省略氮气供应步骤的比较例1相比,在根据包括在特定时间点供应氮气的步骤的方法制备催化剂的实施例1的情况下,丁烯的转化率、丁二烯的选择性和丁二烯的产率增加,同时副反应产物cox的选择性减少。此外,与根据比较例1的催化剂相比,根据实施例1的催化剂在氧化脱氢过程中在低的热点温度下表现出优异的活性。换言之,可以看出,当在铁酸锌催化剂的合成过程中引入供应氮气的过程时,非活性α-fe2o3晶体结构的比例降低并且反应活性增加。实施例2除了通过共沉淀浴的下部供应金属前体水溶液,并且逐滴添加氨水以使铁和锌共沉淀之外,根据与实施例1中相同的条件制备金属前体水溶液,然后进行与实施例1中相同的过程。实施例3除了供应空气而不是氮气(n2)之外,进行与实施例2中相同的过程。试验例3:xrd分析进行xrd分析以确认根据实施例1至实施例3制备的催化剂的晶体结构以及晶体结构的比例。此外,进行比较例1的xrd分析。xrd分析结果示于图2和下面的表3中。[表3]参照图2和表3,根据实施例2和实施例3制备的铁酸锌催化剂表现出包含znfe2o4晶体结构和α-fe2o3晶体结构的混合相。与不遵循实施例2和实施例3的方法的比较例1相比,在通过包括通过共沉淀浴的下部供应金属前体水溶液的步骤和向共沉淀浴中供应氮气或氧气的步骤的方法来制备催化剂的实施例2或实施例3的情况下,作为非活性晶体结构的α-fe2o3晶体结构的比例减少。换言之,当在使用共沉淀法合成铁酸锌的过程中进行通过共沉淀浴的下部供应金属前体水溶液的步骤和供应氮气或空气的步骤时,制得具有低比例的非活性晶体结构的铁酸锌催化剂。试验例4:粒度分析分析根据实施例1至实施例3和比较例1制备的铁酸盐催化剂前体浆料的粒度,结果示于下面的表4和图3中。使用激光粒度仪-960(horiba,co.,ltd.)进行粒度分析。此时,基于在浆料中作为主要成分的fe来设定要求分析的折射率。[表4]类别实施例1实施例2实施例3比较例1中值粒度(μm)6.95.86.08.4众数粒度(μm)7.26.26.38.3*中值粒度:分布在中间的粒子的直径*众数粒度:分布最多的粒子的直径如表4和图3中所示,与比较例1相比,在实施例1至实施例3的情况下,浆料粒子相对较小并且具有均匀的粒度。此外,与实施例1相比,在实施例2和实施例3的情况下,浆料粒子相对小并且具有更均匀的粒度。从这些结果可以看出,氮气的供应有效地使催化剂前体能够具有小且均匀的粒度。此外,可以看出,空气的供应以及金属前体水溶液的供应的重新设置能够有效地使催化剂前体具有更小且更均匀的粒度。试验例5:氧化脱氢以与上面描述的相同的方式在相同的条件下使用根据实施例2和实施例3制备的铁酸锌催化剂进行氧化脱氢,以制备丁二烯。实施例2a至实施例2d和实施例3a至实施例3c的结果示于表5中,为了进行比较,重新描述比较例1a至比较例1d的结果。[表5]参照表5,在实施例2和实施例3以及比较例1中,可以看出,当进行氧化脱氢时,在高耗氧量的条件下观察到高的催化活性。与不遵循实施例2和实施例3的方法的比较例1相比,在实施例2和实施例3的情况下,其中使用通过包括通过共沉淀浴的下部供应金属前体水溶液的步骤和在特定时间点供应氮气或空气的步骤的方法制备的铁酸锌催化剂进行氧化脱氢,丁烯的转化率、丁二烯的选择性和丁二烯的产率增加,同时作为副反应产物的cox的选择性降低。此外,与比较例1相比,当使用根据本发明的实施例2和实施例3的铁酸锌催化剂时,即使在低的热点温度下反应活性也优异。换言之,在使用共沉淀法合成铁酸锌催化剂的情况下,当通过共沉淀浴的下部供应金属前体水溶液并且在特定时间点供应氮气或空气时,铁酸锌催化剂中非活性晶体结构的比例降低,并且催化剂的活性也增加。当前第1页12