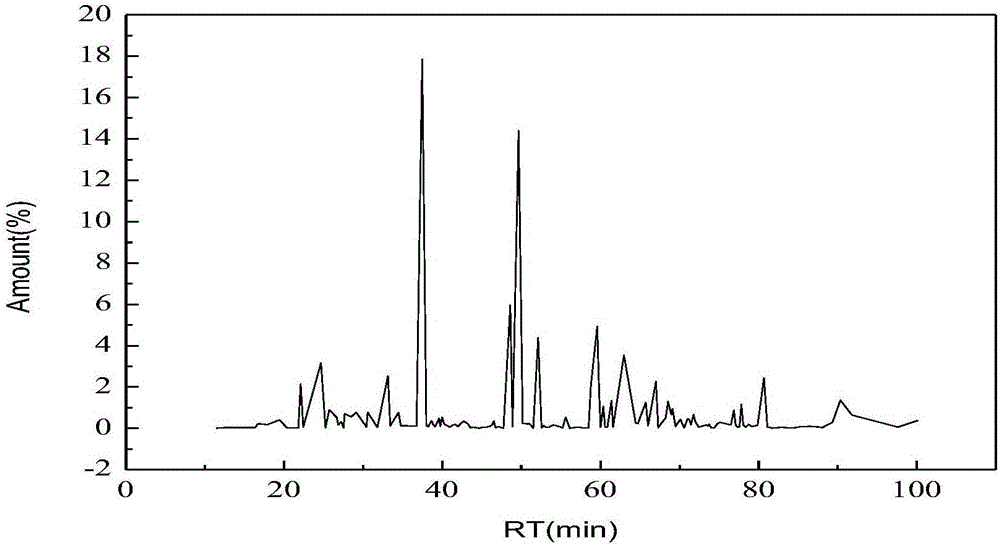
本发明属于化工领域,涉及一种全馏分中低温煤焦油加氢制取单环芳烃的方法及装置,尤其涉及一种中低温煤焦油全馏分为原料经过分馏,轻相进行裂化精制,重相进行两次裂化后再精制裂化的工艺路线来制取苯、甲苯、二甲苯等单环芳烃的方法及装置。
背景技术:
:随着世界经济的飞速发展,对各种各样化工原料的需求也不断增加,其中苯、甲苯、二甲苯等轻质芳烃作为重要的化工原料,一度成为全球市场长期旺盛需求的产品。一直以来,我国是一个富煤、少气、缺油的国家,煤炭储量远远大于石油、天然气储量。据统计预测,我国煤炭资源远景总量为50000×108t以上,随着煤热解工艺技术的逐渐增多,煤焦油的产量愈来愈多。从目前的生产现状来看,BTX芳烃主要来自石脑油馏分催化重整和裂解汽油,少部分来自煤焦油,未能充分利用我国富煤的能源特点,故综合高效利用煤焦油资源生产轻质芳烃将具有长期稳定的效益。目前,对煤焦油加工的方法有蒸馏、加氢处理等,然而煤焦油加氢工艺大多是分馏程对煤焦油轻馏分进行加氢精制-加氢裂化,煤焦油并未得到完全充分的利用,因此充分利用煤焦油进行催化加氢并且制取附加值高的化工产品是一项重要的研究课题。公告号是CN103121895B的发明专利公开了一种稠环芳烃制取单环芳烃方法,该工艺通过自制催化剂使含稠环芳烃的混合物原料与催化剂接触,生成含苯、甲苯和二甲苯的单环芳烃物流。与本发明所得单环芳烃收率相比,其不足之处在于此工艺过程产物中单环芳烃的收率最高不超过40%,发展前景尤为不佳。公告号是CN101712889B的发明专利公开了一种煤焦油制取轻质芳烃的方法,该工艺是通过分馏将小于200℃的轻油馏分进行两段选择性加氢处理得到所需产品,但是对于大于200℃的重质馏分未充分利用进行制取轻质芳烃,而且所制轻质芳烃收率较低。制取BTX单环芳烃的论文很多,例如裂解汽油重质馏分轻质化增产BTX芳烃技术展望、菲加氢裂化制BTX的催化反应研究、催化裂化轻循环油生产轻质芳烃的分子水平研究等都能够制取出一定量的单环芳烃,但是没有针对我国富煤、少气、缺油的能源特点做出很好的利用,从长远的利益与未来的发展前景来看,本发明所研究的课题非常具有研究意义。此外,煤焦油中含有大量较难转化的沥青质,分子量相当高且结构复杂,沥青质进入加氢系统,不仅会堵塞并腐蚀设备,影响装置长期安全稳定的运行,还容易引起加氢催化剂的结焦和中毒失活。故一般煤焦油加氢工艺要进行大部分的沥青焦分离,但分离势必会浪费一部分沥青焦资源,对煤焦油的利用率变低。因此一方面需要探索出一种充分利用煤焦油的方法,对煤焦油全馏分进行加氢,来制取单环芳烃。另一方面探究出使沥青质在加氢过程中发生环烷环开环断裂和芳香核外侧芳香环加氢饱和反应,且对含有5-6个环的沥青分子转化为只含有1-2个环的小分子,H/C原子比显著增加,沥青质轻质化和杂原子脱除效果明显的方法就尤为重要。综上所述,中低温全馏分煤焦油制取单环芳烃中整个工艺流程的设计与其催化剂的配套选择是该发明
技术领域:
亟待解决的难题。技术实现要素:针对现有技术的不足,本发明的目的在于提供一种以中低温煤焦油全馏分为原料经过分馏,轻相进行裂化精制,重相进行两次裂化后再精制裂化的全馏分中低温煤焦油加氢制取单环芳烃的方法及装置,以实现全馏分煤焦油加氢制取苯、甲苯、二甲苯等单环芳烃。为实现上述目的,本发明采用如下技术方案:一种全馏分中低温煤焦油加氢制取单环芳烃的方法,其特征在于:所述全馏分中低温煤焦油加氢制取单环芳烃的方法包括以下步骤:1)全馏分中低温煤焦油进入分馏塔进行分馏,从分馏塔底部分馏得到物流Ⅱ以及从分馏塔顶部分馏得到的物流Ⅰ;所述物流Ⅰ直接进入步骤2);所述物流Ⅱ直接进入步骤3);所述物流Ⅰ是轻质馏分;所述物流Ⅱ是重质馏分;2)将步骤1)所得到的物流Ⅰ根据常规工艺制备得到单环芳烃;3)将步骤1)得到的物流Ⅱ进行加氢裂化,并将加氢裂化后的物流输送至步骤2)根据常规工艺制备单环芳烃。上述步骤3)的具体实现方式是:3.1)将分馏塔底产生的物流Ⅱ经过加热炉,进入反应器Ⅲ,在温度380-450℃、反应压力12-15MPa、液时空速0.3-0.6h-1、氢油比1200:1-1600:1条件下,物流Ⅱ中高分子稠环芳烃化合物与反应器Ⅲ中的裂化催化剂Ⅱ接触,反应后生成物流Ⅴ;3.2)将步骤3.1)得到的物流Ⅴ经高分器Ⅲ分理出循环氢后,进入闪蒸塔;3.3)物流Ⅴ在闪蒸塔内进行闪蒸,从闪蒸塔的顶部闪蒸得到轻相物流Ⅵ以及从闪蒸塔的底部闪蒸得到塔底物流Ⅶ;所述轻相物流Ⅵ输送至步骤2)根据常规工艺制备单环芳烃;所述塔底物流Ⅶ执行步骤3.4)3.4)塔底物流Ⅶ经过反应器Ⅳ进行沥青质、胶质的加氢裂化,生成物流Ⅷ,反应器Ⅳ中采用的工艺条件和催化剂均与步骤3.1)中的反应器Ⅲ所采用的工艺条件以及催化剂相同;所述物流Ⅷ执行步骤3.5);3.5)物流Ⅷ经过高分器Ⅳ后输送至步骤2)根据常规工艺制备单环芳烃。上述步骤3.1)中的裂化催化剂Ⅱ满足以下条件:a)裂化催化剂Ⅱ的载体:超稳Y型分子筛与无定型硅铝组合的载体;b)裂化催化剂Ⅱ的加氢活性成分:Mo-Ni-Zn作为催化剂的加氢活性组分;c)裂化催化剂Ⅱ的孔径:孔径分布在小于10nm之间所占比例1-5%;10-20nm所占比例10-15%;20-50nm所占比例20-30%;>50nm所占比例50%;d)裂化催化剂Ⅱ的孔容是0.55-0.65cm3/g。上述加氢活性成分中包括质量百分比是2%-8%的MoO3、2%-4%的NiO以及4%-6%的Zn。上述步骤2)的具体实现方式是:2.1)将从分馏塔顶部分馏得到的物流Ⅰ经过加热炉,进入反应器Ⅰ,在反应温度为320-380℃、压力为6-8MPa、液时空速0.8-1h-1、氢油比600:1-800:1的条件下,与精制催化剂充分接触进行馏分油的精制,制得硫含量在10ppm以下、氮含量小于20ppm的物流Ⅲ;2.2)所述物流Ⅲ经高分器Ⅰ分离出循环氢后,进入反应器Ⅱ;在反应器Ⅱ中,在反应温度360-400℃、压力6-8MPa、液时空速1.5-2h-1、氢油比600:1-800:1的条件下,与选择性加氢裂化催化剂Ⅰ接触,发生裂化反应和异构化反应生成物流Ⅳ;2.3)物流Ⅳ经高分器Ⅱ分离出循环氢后,得到单环芳烃。上述步骤2.1)中所采用的精制催化剂满足以下条件:a)精制催化剂的载体:γ-Al2O3;b)精制催化剂的加氢活性组分:Ni-Mo-W作为催化剂的加氢活性组分;c)精制催化剂的孔径分布2-5nm占20-25%,5-10nm占30-60%,>10nm占10-15%;d)精制催化剂的孔容0.34-0.44cm3/g。上述精制催化剂的加氢活性组分包括质量百分比是16%-22%的WO3、6%-8%的MoO3以及3%-5%的NiO。上述步骤2.2)中所采用的选择性加氢裂化催化剂Ⅰ满足以下条件:所述选择性加氢裂化催化剂主要组分:a)选择性加氢裂化催化剂Ⅰ的载体:HY+γ-Al2O3;b)选择性加氢裂化催化剂Ⅰ的加氢活性金属组分:采用Ni-W-F作为加氢活性金属组分;c)选择性加氢裂化催化剂Ⅰ的孔径分布处于2-5nm占15-25%,5-10nm占35-65%,>10nm占5-15%;d)选择性加氢裂化催化剂Ⅰ的孔容0.39-0.49cm3/g。上述选择性加氢裂化催化剂Ⅰ的加氢活性金属组分包括质量百分比是10%-16%的WO3、3%-7%的NiO以及0.25%-0.95%的F。一种用于如前所述的全馏分中低温煤焦油加氢制取单环芳烃的方法的装置,其特征在于:所述装置包括分馏塔、反应器Ⅲ、高分器Ⅰ、反应器Ⅰ、高分器Ⅱ、反应器Ⅱ、高分器Ⅲ、闪蒸塔、反应器Ⅳ以及高分器Ⅳ;所述分馏塔包括设置在顶部的顶部出口以及设置在底部的底部出口;所述分馏塔的顶部出口依次通过反应器Ⅰ、高分器Ⅰ以及反应器Ⅱ与高分器Ⅱ相贯通;所述闪蒸塔包括顶部出口以及底部出口;所述分馏塔的底部出口依次通过反应器Ⅲ、高分器Ⅲ、闪蒸塔的底部出口以及反应器Ⅳ与高分器Ⅳ相贯通;所述闪蒸塔的顶部出口以及高分器Ⅳ分别与反应器Ⅰ相贯通;所述反应器Ⅰ是加氢精制反应器;所述反应器Ⅱ是加氢裂化反应器;所述反应器Ⅲ为加氢裂化反应器;所述反应器Ⅳ为加氢裂化反应器。与现有技术相比,本发明所具有的有益效果如下:1、本发明采用的工艺方法,充分利用了煤焦油的全馏分,且为了达到理想的工艺效果,对重质馏分沥青质、胶质等大分子通过两段裂化将原本含有5-6个芳香环的稠环芳烃依次逐步脱除1-2个环,最终将其裂化为1-2个芳香环分子,更深层次的进行目标产物的制取,使得所制苯、甲苯、二甲苯等单环芳烃比一般工艺收率高出35%-40%左右,说明本工艺取得了非常好的技术效果。2、本发明所采用的工艺方法、工艺参数的使用和催化剂体系密切的配合,不仅很大程度上使沥青质等重馏分转化成轻质馏分油,原料得到了充分的利用,而且经闪蒸塔的物流Ⅵ与反应器Ⅲ的物流Ⅷ循环至物流Ⅰ进行硫氮的脱除与目标产物的制备时,所配套使用的催化剂使得每个阶段反应器反应情况都处于最佳状态,整套系统设备运行十分稳定,后期转化率高达65%-70%,其中单环芳烃的选择性可高达75%左右,保证了非常好的产品收率效果。因此,本发明具有一定的发展前景与不错的经济效益。本发明对中低温全馏分煤焦油实现了充分利用,并且得到了一定附加值高的产品。此设计工艺不仅增加了目标产物的收率,得到了一系列附加值不错的产品。还合理充分的利用了全馏分煤焦油,显现出相当大的发展前景。附图说明图1是沥青质、胶质的平均分子结构模型;图2是实施例1产品的详细组成谱图;图3是实施例2产品的详细组成谱图;图4是本发明在制取全馏分煤焦油制取轻质芳烃时所采用的装置的结构示意图。具体实施方式本发明提供了一种全馏分中低温煤焦油加氢制取单环芳烃的方法,该方法包括以下步骤:1)全馏分中低温煤焦油首先进入分馏塔进行分馏,塔顶物流Ⅰ经过加热炉,进入反应器Ⅰ,在反应温度为320-380℃、压力为6-8MPa、液时空速0.8-1h-1、氢油比600:1-800:1的条件下,与精制催化剂充分接触进行馏分油的精制,成功制得硫含量在10ppm以下、氮含量小于20ppm的物流Ⅲ。其催化剂是以γ-Al2O3为载体,Ni-Mo-W作为催化剂的加氢活性组分,16%-22%的WO3,6%-8%的MoO3,3%-5%的NiO,孔径分布2-5nm占20-25%,5-10nm占30-60%,>10nm占10-15%;孔容0.34-0.44cm3/g。2)物流Ⅲ经高分器分离出循环氢后,进入反应器Ⅱ;3)在反应器Ⅱ中,在反应温度360-400℃、压力6-8MPa、液时空速1.5-2h-1、氢油比600:1-800:1条件下,与选择性加氢裂化催化剂Ⅰ接触,发生裂化反应和异构化反应生成物流Ⅳ,即所得产品苯、甲苯、二甲苯。此过程中所用催化剂主要组分:a)以HY+γ-Al2O3为载体,b)采用Ni-W-F作为加氢活性金属组分,重量百分比是10%-16%的WO3、3%-7%的NiO以及0.25%-0.95%的F;c)孔径分布处于2-5nm占15-25%,5-10nm占35-65%,>10nm占5-15%;d)孔容0.39-0.49cm3/g。4)物流Ⅳ经高分器分离出循环氢后,进而得到所需要的苯、甲苯、二甲苯等单环芳烃;5)分馏塔底产生的物流Ⅱ经过加热炉,进入反应器Ⅲ,在温度380-450℃、反应压力12-15MPa、液时空速0.3-0.6h-1、氢油比1200:1-1600:1条件下,煤焦油中高分子稠环芳烃化合物(沥青质)与反应器Ⅲ中的催化剂Ⅱ接触,反应后生成物流Ⅴ,其中所用裂化催化剂Ⅱ主要目的可以将沥青质、胶质等大分子开环裂化,其催化剂主要包含以下组分:a)超稳Y型分子筛与无定型硅铝组合的载体,利用分子筛与二氧化硅配比来进行酸性保护;b)Mo-Ni-Zn作为催化剂的加氢活性组分,重量百分比是2%-8%的MoO3、2%-4%的NiO以及4%-6%的Zn;c)孔径分布在小于10nm之间所占比例1-5%;10-20nm所占比例10-15%;20-50nm所占比例20-30%;>50nm所占比例50%;d)孔容0.55-0.65cm3/g。6)物流Ⅴ经高分器分理出循环氢后,进入闪蒸塔;7)物流Ⅴ在闪蒸塔内进行闪蒸,塔底物流Ⅶ经过反应器Ⅳ进行沥青质、胶质的加氢裂化,生成物流Ⅷ,反应器Ⅳ中工艺条件和催化剂的使用都与反应器Ⅲ的相同;塔顶的轻相物流Ⅵ与经过高分器的物流Ⅷ一起循环至物流Ⅰ进行深层次硫、氮的脱除以及单环芳烃的制备。本发明所采用的工艺路线是为了将全馏分中低温煤焦油中沥青质得到充分利用,原料经过分馏塔进行分馏,使得轻质馏分进行精制裂化得到一定量的单环芳烃,与此同时对重质馏分沥青质、胶质进行裂化开环,其主要过程在于保证沥青1-2个环的缓慢脱除,然后将裂化后的1-2个环的分子再次进行精制裂化,深层次脱除硫氮并获取所需的单环芳烃,显著提高整个工艺流程中单环芳烃的收率。其中,步骤1)对全馏分煤焦油进行分馏,所得轻质馏分进入加氢精制反应器,加氢精制反应器中所用催化剂采用以γ-Al2O3为载体,WO3,MoO3,NiO作为催化剂的加氢活性组分,具有非常高的加氢活性,能有效的使油品中硫、氮等非烃类化合物含量降低在本发明规定的标准之下,减少了后续裂化反应中催化剂的中毒与失效。在步骤3)中经精制后的轻质馏分进行加氢裂化与异构化反应,其催化剂通过改变基质和沸石分子筛的不同搭配来改变催化剂的选择性,以HY+γ-Al2O3为载体,Ni-W-F作为加氢活性金属组分,不仅增加了催化剂的活性组分的分散度与分散性,而且增加催化剂的酸性位,减少了二次裂化的发生,使得反应朝着目标产物的方向发展。在步骤5)中,重质馏分经裂化反应器Ⅲ,使芳环数为5-6的沥青质、胶质进行1-2个芳环的脱除,催化剂所选用的超稳Y型分子筛具有高的稳定性和选择性,提高对重质组分烃的转化能力,加快了反应物和产物的扩散速度。无定型硅铝的比表面积大、酸性高、孔径分布宽对裂化全馏分煤焦油是有利的。Mo-Ni-Zn金属组分不仅增加了催化剂的酸性位,而且还具有一定断侧链和轻微的脱硫、氮能力。在步骤7)中再次进行加氢裂化,将芳香环数为3-4个环的沥青质、胶质大分子裂化为1-2个芳香环的分子,然后使其全部进入加氢精制反应器中深层次的进行硫氮的脱除,此法不仅降低沥青质引起的催化剂结焦而且还提高加氢催化剂的抗失活能力,最终经裂化制得所需苯、甲苯、二甲苯等单环芳烃。参见图4,本发明还提供了一种用于如前的全馏分中低温煤焦油加氢制取单环芳烃的方法的装置,包括分馏塔、反应器Ⅲ、高分器Ⅰ、反应器Ⅰ、高分器Ⅱ、反应器Ⅱ、高分器Ⅲ、闪蒸塔、反应器Ⅳ以及高分器Ⅳ;分馏塔包括设置在顶部的顶部出口以及设置在底部的底部出口;分馏塔的顶部出口依次通过反应器Ⅰ、高分器Ⅰ以及反应器Ⅱ与高分器Ⅱ相贯通;闪蒸塔包括顶部出口以及底部出口;分馏塔的底部出口依次通过反应器Ⅲ、高分器Ⅲ、闪蒸塔的底部出口以及反应器Ⅳ与高分器Ⅳ相贯通;闪蒸塔的顶部出口以及高分器Ⅳ分别与反应器Ⅰ相贯通;反应器Ⅰ是加氢精制反应器;反应器Ⅱ是加氢裂化反应器;反应器Ⅲ为加氢裂化反应器;反应器Ⅳ为加氢裂化反应器。本发明以低温全馏分煤焦油为原料,原料性质见表1,重质馏分油里沥青质、胶质的平均分子结构模型见图1。实施例1-2的加氢反应条件见表2,同时配以相应催化剂见表3。以煤焦油进料10t/h计,反应过程中各物流的流量及相关性质见表4,实施例所得产品的详细性质见表5、表6、图2以及图3。表1低温煤焦油的性质表2各反应器的加氢反应条件表3各反应器的催化剂表4各物流的相关性质(煤焦油进料10t/h)表5实施例1中所得产品中烃类的详细性质(PONA)表6实施例2中所得产品中烃类性质(PONA)CNumnPiPONACSum6.000.000.000.000.003.173.177.000.004.160.100.6514.7522.568.002.114.410.001.5616.7427.729.001.362.700.000.9217.7322.2110.000.261.400.000.2511.5213.4311.000.000.060.000.190.590.8412.000.000.680.000.000.000.78total03.7313.4100.1003.5664.585.3通过本发明的实施,从全馏分中低温煤焦油中成功制取了单环芳烃,充分利用了煤焦油的全馏分,达到了理想的工艺效果。表4可以看出实施例1所得产品中单环芳烃的收率达到69.5%,其中物流Ⅱ至物流Ⅴ中三环芳烃含量与双环芳烃含量的增多体现了对含有5-6个芳香环沥青、胶质分子的1-2个环的一次裂化,物流Ⅴ至物流Ⅷ中三环芳烃含量的减少与双环芳烃含量的增多体现了对物流再次进行1-2个环的二次裂化。实施例2在实施例1催化剂组成不改变的情况下,对活性组分含量、孔容、孔径进行改变,所得产品收率为64.5%,对比可得,实施例1所使用的催化剂及其各组分含量使得各阶段反应器反应情况都处于最佳状态,整套系统设备运行十分稳定,显现出了相当大的发展前景。对比例1以中低温全馏分煤焦油为原料,改变反应器Ⅰ中催化剂的使用见表7,其余反应器内催化剂与实施例1相同,且反应温度、压力、空速、氢油比条件与实施例1相同。对比例2以中低温全馏分煤焦油为原料,改变反应器Ⅰ中催化剂的使用见表7,其余反应器内催化剂与实施例2相同,且反应温度、压力、空速、氢油比条件与实施例2相同。表7改变反应器Ⅰ中的催化剂对比例3以中低温全馏分煤焦油为原料,改变反应器Ⅱ中催化剂的使用见表8,其余反应器内催化剂与实施例1相同,且反应温度、压力、空速、氢油比条件与实施例1相同。对比例4以中低温全馏分煤焦油为原料,改变反应器Ⅱ中催化剂的使用见表8,其余反应器内催化剂与实施例2相同,且反应温度、压力、空速、氢油比条件与实施例2相同。表8改变反应器Ⅱ中的催化剂对比例5以中低温全馏分煤焦油为原料,改变反应器Ⅲ和Ⅳ中催化剂的使用见表9,其余反应器内催化剂与实施例1相同,且反应温度、压力、空速、氢油比条件与实施例1相同。对比例6以中低温全馏分煤焦油为原料,改变反应器Ⅲ和Ⅳ中催化剂的使用见表9,其余反应器内催化剂与实施例2相同,且反应温度、压力、空速、氢油比条件与实施例2相同。表9改变反应器Ⅲ和Ⅳ中的催化剂表10实施例1、例2与对比例1-6在改变反应催化剂后所得物流Ⅳ(产品)的分析结果项目实施例1实施例2对比例1对比例2对比例3对比例4对比例5对比例6产品收率/%9797939189868782氮含量/%0.00150.00160.230.480.00160.00170.00160.0017硫含量/%0.00080.00090.170.290.00070.00110.00080.0010饱和烃含量/%21.220.821.922.323.325.723.926.1三环芳烃含量/%4.14.86.47.57.88.29.813.4双环芳烃含量/%5.26.17.48.29.110.514.417.3单环芳烃含量/%69.564.557.654.351.749.245.643.9胶质/%00000000沥青质含量/%00000000从表10可知全馏分中低温煤焦油加氢反应在温度、压力、空速、氢油比不变的情况下,因实施例中所用催化剂不仅具有很好的加氢活性、高稳定性和选择性,能使油品中硫、氮等非烃类化合物含量降低在本发明规定的标准之下,减少了后续裂化反应中催化剂的中毒与失效,而且一定程度上增加了催化剂的酸性位,减少了二次裂化的发生,使得反应朝着目标产物的方向发展。改变了各反应器催化剂后,催化效果不佳,使得整个工艺过程中所得单环芳烃含量远不如实施例1、例2。综上,本发明在
技术领域:
亟待解决的问题,工艺流程的设计与其催化剂的配套选择,显现出很好的研究进展。对比例7以中低温全馏分煤焦油为原料,改变工艺过程中的温度、压力、液体空速、氢油比等参数的使用见表11,各反应器催化剂与实施例1相同。对比例8以中低温全馏分煤焦油为原料,改变工艺过程中的温度、压力、液体空速、氢油比等参数的使用见表11,各反应器催化剂与实施例2相同。表11改变温度、压力、液体空速、氢油比等参数的使用表12改变各工艺参数后所得物流Ⅳ(产品)的分析结果项目实施例1实施例2对比例7对比例8产品收率/%97978173氮含量/%0.00150.00160.0370.054硫含量/%0.00080.00090.0240.031饱和烃含量/%21.220.834.738.9三环芳烃含量/%4.14.87.310.7双环芳烃含量/%5.26.16.89.2单环芳烃含量/%69.564.547.336.9胶质/%0001.7沥青质含量/%0002.4从表12可以看出,在本发明所规定的工艺参数范围之内,单环芳烃的收率效果最佳。超出所规定的范围后,单环芳烃的收率远不如本发明高,说明本发明所用工艺参数与配套使用的催化剂使得各反应器的情况都处于最佳状态,对中低温全馏分煤焦油实现了充分利用,具有很好的发展前景与不错的经济效益。当前第1页1 2 3