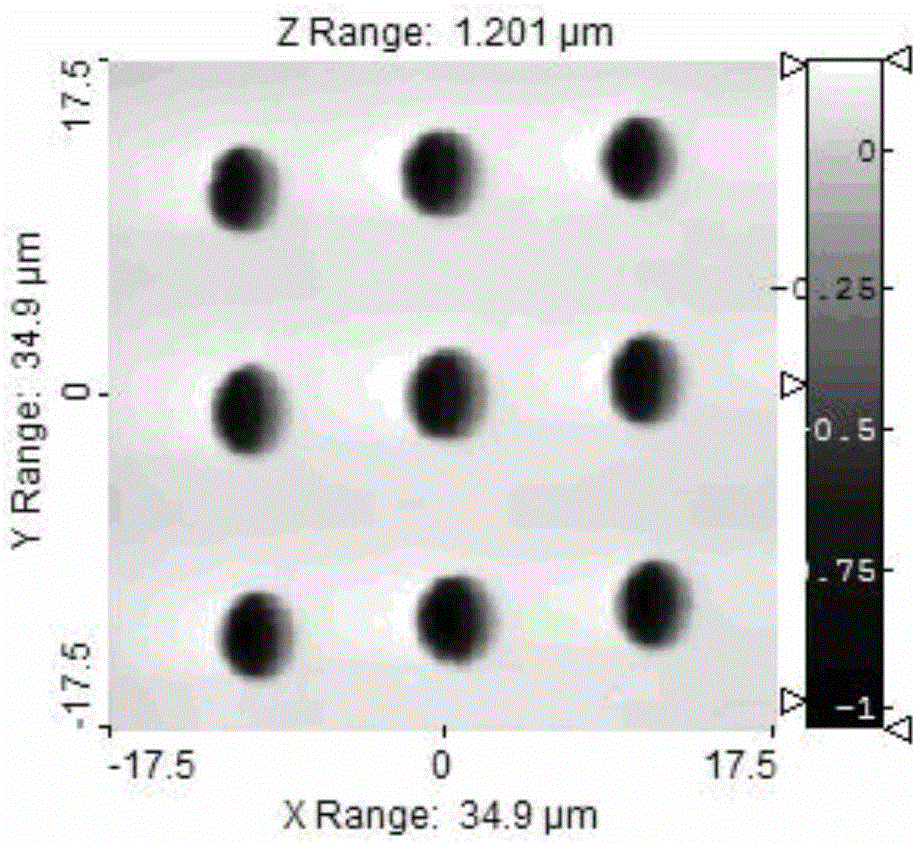
本发明涉及软物质的微纳米加工技术,具体涉及一种利用表面氧化控制转移印刷法进行PDMS表面图案化的工艺方法。
背景技术:聚二甲基硅氧烷(PDMS)是一种最广泛使用的硅基有机聚合物材料。PDMS作为一种有机硅橡胶,在户外绝缘材料、填缝剂、润滑剂、人体整形植入等方面有着很多用途,更为重要的是其在微纳制造中有着独特的应用前景。在微纳尺度上,PDMS厚/薄膜广泛应用于软刻蚀技术、微/纳流体控制、微/纳电子机械系统、生物传感等诸多领域。这些应用都依赖于PDMS的表面微结构化。然而目前PDMS弹性体的微纳米加工技术却十分有限,且受限于加工形式、难以制备复杂精细表面图案结构。与此同时,印刷法作为一种简单、便捷、适用性广泛的图案化技术越来越受到学术界的重视。
技术实现要素:针对上述现有技术,本发明提供一种基于表面氧化控制的微转移印刷法,制备PDMS微纳米结构图案。本发明选用平面PDMS片(厚度范围从纳米级到毫米级)为基底,以复制模铸法制备的表面带有简单微结构图案的PDMS为转移印刷印章,通过对PDMS印章和基底表面氧化处理条件的不同引入内聚能“软/硬”差异,转移“墨水”来自印章或基底中较“软”的一方,从而实现平面PDMS基底表面的可控图案化。本发明制备方法避免了昂贵仪器的使用以及繁琐复杂的操作步骤,是一种通用的PDMS微纳加工方法。为了解决上述技术问题,本发明提出的一种基于表面氧化控制转移印刷的PDMS弹性体微纳加工方法,包括以下步骤:步骤一、利用浇筑法或旋涂法制备厚度可调的PDMS膜,作为转移印刷的基底;步骤二、利用复制模铸法制备带有表面微结构的PDMS膜,作为转移印刷的印章;步骤三、对步骤一制备得到的基底或对步骤二制备得到的印章进行表面氧化处理,从而获得一组硬印章/软基底组合或是一组软印章/硬基底组合;步骤四、将经过步骤三获得的一组硬印章/软基底组合或是一组软印章/硬基底组合中的印章和基底同时进行表面活化处理;然后立即将处理后的印章和基底贴合并在鼓风干燥箱中加热保温一定时间;随炉冷却至室温,取下印章,得到表面具有凹陷或凸起图案的PDMS膜。进一步讲,步骤一中,浇筑法制备具有微米到毫米级厚度PDMS膜的过程是:首先,将PDMS预聚体和交联剂按质量比为10:1混合,用玻璃棒充分搅拌形成均匀的预聚合物;将上述预聚合物在循环水式多用真空泵中脱气1小时后,浇筑到表面皿中;在70℃下加热4h进行固化;获得厚度可调的PDMS膜。步骤一中,旋涂法制备具有纳米级厚度且膜厚可调的PDMS膜的过程是:首先,将PDMS预聚体和交联剂按质量比为10:1混合,然后,加入一定量的正己烷溶液,其中,正己烷与PDMS的质量比从80:1到10:1之间可调(其对应旋涂膜厚从约70nm到800nm),震荡摇匀;用移液器取50μl混合液,滴到洁净的盖玻片上旋涂成膜,旋涂的转速6000r/min、时间150s;在95℃下加热1h进行固化。步骤二中,复制模铸法制备带有表面微结构的PDMS膜的过程是:首先,将PDMS预聚体和交联剂按质量比为10:1混合,用玻璃棒充分搅拌形成均匀的预聚合物;将上述预聚合物在循环水式多用真空泵中脱气1小时后,浇筑到母模板上,浇筑厚度为1mm;在70℃下加热4h进行固化。步骤三中,表面氧化处理是氧等离子体处理1min–50min或是紫外臭氧处理5min–50min。步骤四中,表面活化处理是氧等离子体处理0.5min或是紫外臭氧处理2min。步骤四中,若制备具有微米级到毫米级厚度的表面具有凹陷或凸起图案的PDMS膜,则设定加热温度为100℃,其保温时间为1h;若制备具有纳米级到微米级厚度的表面具有凹陷或凸起图案的PDMS膜,则设定加热温度为70℃,其保温时间为10min。与现有技术相比,本发明的有益效果是:本发明制备方法中,通过对PDMS印章或基底进行不同时间的表面氧化处理来调控PDMS“墨水”转移方向,从而达到对PDMS平面基底的可控图案化。本发明的方法具有简单,便捷,适用范围广的特点。尤其是可以简单地通过表面氧化处理条件的选择实现PDMS表面图案的精细调控,这是目前其他技术难以达到的。附图说明图1为本发明实施例1得到的PDMS印章的扫描电子显微镜图片;图2为本发明实施例1得到的表面图案化PDMS厚基底的原子力显微镜图片;图3为本发明实施例2得到的表面图案化PDMS厚基底的原子力显微镜图片;图4为本发明实施例3得到的表面图案化PDMS薄基底的原子力显微镜图片;图5为本发明实施例4得到的表面图案化PDMS薄基底的原子力显微镜图片。具体实施方式下面结合附图和具体实施例对本发明技术方案作进一步详细描述,所描述的具体实施例仅对本发明进行解释说明,并不用以限制本发明。实施例1、表面微纳米级图案化的PDMS膜的制备,步骤如下:步骤一、利用浇筑法制备厚度约为1mm的PDMS厚膜作为转移印刷的基底;具体内容是:首先,将PDMS预聚体和交联剂Sylgard184(购自美国道康宁公司)按质量比为10:1混合,用玻璃棒充分搅拌形成均匀的预聚合物;将上述预聚合物在循环水式多用真空泵中脱气1小时后,浇筑到表面皿中,浇筑厚度约为1mm;在70℃下加热4h进行固化;获得PDMS厚膜基底;步骤二、利用复制模铸法制备带有表面微结构的PDMS作为转移印刷的印章;首先,将PDMS预聚体和交联剂按质量比为10:1混合,用玻璃棒充分搅拌形成均匀的预聚合物;将上述预聚合物在循环水式多用真空泵中脱气1小时后,浇筑到带有圆柱阵列的硅模板上,浇筑厚度约1mm;在70℃下加热4h进行固化;小心地揭掉模板获得PDMS印章,该PDMS印章的表面结构如图1所示。步骤三、对上述步骤二获得的PDMS印章进行氧等离子体(OP)处理30min,而对步骤一获得的PDMS厚膜基底不进行表面氧化(OP)处理,将该步骤的氧化处理参数记为OP30min/OP0min。步骤四、将步骤三处理后的PDMS印章和步骤一获得的PDMS厚膜基底同时进行OP处理0.5min;然后立即将二者贴合并在鼓风干燥箱中100℃下加热1h;随炉冷却至室温,取下印章,得到表面图案化的PDMS膜。通过原子力显微镜测量,该PDMS膜表面带有规则凹陷圆点图案。本实施例1所得图案化PDMS膜如图2的原子力图所示。实施例2:表面微纳米级图案化的PDMS膜的制备,其制备过程与实施例1基本相同,不同仅在于,步骤三中改为:对步骤二获得的PDMS印章不进行表面氧化处理,对步骤一获得的PDMS厚膜基底进行OP处理30min,将该步骤的氧化处理参数记为OP0min/OP30min,最终得到的表面带有规则圆点凸起图案的PDMS厚膜基底如图3的原子力图所示。实施例3:表面微纳米级图案化的PDMS膜的制备,其制备过程如下:步骤一、利用旋涂法制备厚度约为70nm的PDMS薄膜作为转移印刷的基底,具体内容是:首先,将PDMS预聚体和交联剂按质量比为10:1混合,然后,按照正己烷与PDMS的质量比为80:1加入正己烷溶液,震荡摇匀;用移液器取50μl混合液,滴到洁净的盖玻片上旋涂成膜,转速6000r/min、时间150s;在95℃下加热1h进行固化;获得PDMS薄膜基底。步骤二同实施例1;步骤三、对PDMS印章进行OP处理10min,PDMS基底不处理,氧化处理参数记为OP10min/OP0min。步骤四与实施例1基本相同,只是将OP处理后的PDMS印章和PDMS薄膜立即贴合并在鼓风干燥箱中70℃下加热10min;随炉冷却至室温,取下印章,得到的表面带有规则圆坑图案的PDMS薄膜基底如图4的原子力图所示。实施例4:表面微纳米级图案化的PDMS膜的制备,其制备过程与上述实施例3基本相同,不同仅在于,步骤三改为:对PDMS印章不进行OP处理,PDMS薄膜基底进行OP处理10min,该氧化处理参数记为OP0min/OP10min,最终得到的表面带有规则圆点凸起图案的PDMS薄膜基底如图5的原子力图所示。综上,本发明方法主要是利用表面氧化处理条件的不同引入PDMS印章与平面PDMS基底间内聚能(即所谓的“软硬”)差异,并通过表面活化和加热处理提高印章与基底间的接触粘附作用,使二者分离时“软方”发生内聚能断裂提供PDMS“墨水”并通过接触转移到“硬方”,从而实现平面PDMS基底的可控精细图案化,即通过印章和基底的不同“软/硬”组合以及多次印刷可以得到复杂精细的PDMS表面微结构。本方法不但避免了其他相关技术适用范围有限、加工图案简单的缺点,而且还避免了复杂昂贵仪器的使用,其适用范围广、操作简便、成本低,可作为一种通用的PDMS微纳米加工技术。尽管上面结合图对本发明进行了描述,但本发明并不局限于上述的具体实施方案,上述的具体实施方式仅仅是示意性的,而不是限制性的,本领域的普通技术人员在本发明的启示下,在不脱离本发明宗旨的情况下,还可以作出很多变形,这些均属于本发明的保护之内。