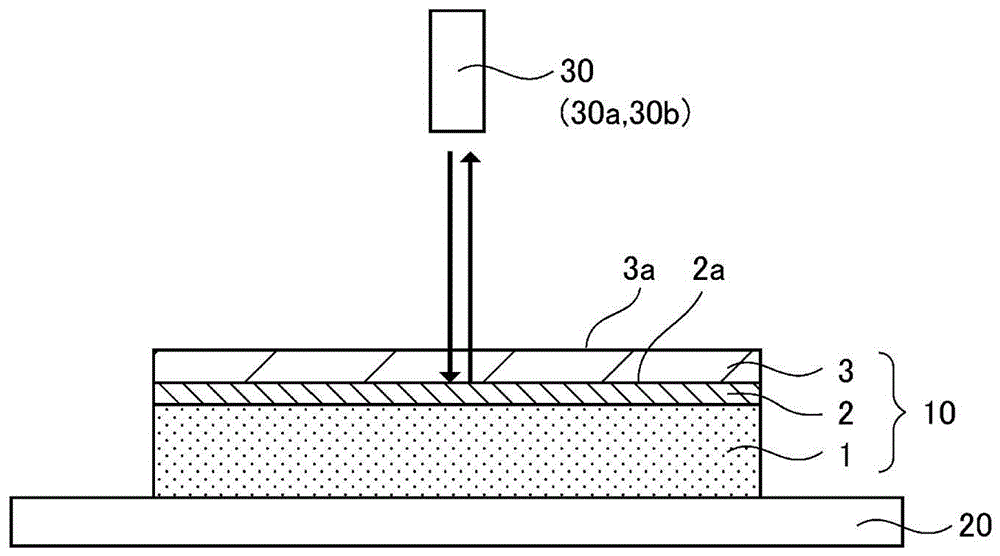
本发明涉及带压电体膜的基板、压电体膜元件及其制造方法。
背景技术:根据各种目的,压电体膜被加工成各种各样的压电体膜元件,特别是广泛用作施加电压而发生变形的执行器、反过来由元件的变形产生电压的传感器等功能性电子部件。作为用于执行器、传感器用途的压电体膜,此前广泛使用具有优异压电特性的铅系材料的电介质,特别是被称为PZT的Pb(Zr1-xTix)O3(以下记为PZT)系钙钛矿型强电介质,通常通过将包含各元素的化合物烧结(烧结法)而形成。现在,随着各种电子部件的小型化、高性能化的推进,对压电体膜元件也强烈要求小型化、高性能化。然而,使用作为传统制法的以烧结法为中心的制造方法所制造的压电材料,随着其厚度的减薄,特别是随着厚度接近于10μm左右的厚度,会接近构成材料的晶粒的大小,其影响变得不能忽视。因此,产生特性偏差、劣化变得显著等问题,为了避免这些问题,近年来一直在研究代替烧结法的应用了薄膜技术等的压电体膜形成法。最近,在硅基板上用溅射法形成的PZT薄膜,作为高速高精细的喷墨打印机头用执行器的压电薄膜已实用化。由上述PZT形成的压电烧结体、压电薄膜,由于含有60~70重量%左右的铅,因此从生态学观点和防止公害方面来说并不理想。因此,出于对环境的考虑,期望开发不含铅的压电体膜。现在,研究了各种各样的非铅压电材料,其中有由通式(K1-xNax)NbO3(0<x<1)表示的铌酸钾钠(以下也记为“KNN”)(例如,参见专利文献1、专利文献2)。该KNN是具有钙钛矿结构的材料,期待其作为非铅压电材料的有力候选。对于KNN薄膜,也尝试了通过溅射法等成膜方法在MgO基板、SrTiO3基板、Si基板等基板上成膜。现有技术文献专利文献专利文献1:日本特开2007-184513号公报专利文献2:日本特开2008-159807号公报
技术实现要素:发明要解决的问题于是,压电体膜经加工而成为压电体膜元件,而使用溅射法等作为薄膜形成的压电体膜与使用常规的烧结法形成的压电体材料相比,更多地被加工为微细器件。加工时,可进行作为制造半导体元件的方法的光刻工序、使用化学试剂·气体将材料削刻成微细形状的蚀刻工序。因此,在加工为压电体膜元件时,有对压电体膜的削刻量进行精细地控制的必要性,因而压电体膜的膜厚的信息变得重要。另外,由于压电体膜相对于外加电压的变形量随膜厚而变化,因而膜厚在获悉器件的特性方面也变得重要。因此,在压电体膜成膜后对其膜厚进行测定。这时,作为压电体膜的膜厚的测定方法,例如有以下2种方法。一种是接触法,这是通过例如将已成膜的压电体膜切割并实际测定其截面,或者预先设置未成膜的面并用探针测定其高度差,从而测定膜厚的方法。但是,在接触法中,由于通过使探针等与压电体膜接触来测定膜厚,因此存在压电体膜的破坏、污染等问题。另一种是非接触法,这是通过对压电体膜的表面照射光并测定反射的光的相位差而测定膜厚的光学式测定方法。根据光学式测定方法,由于可以使用光来非接触性地测定膜厚,因此可以非破坏性地测定膜厚。然而,上述光学式测定方法中膜厚的测定值与实际膜厚并不相同,有时难以正确地测定膜厚。即,以规定膜厚成膜时,不管实际上是不是膜厚正常的压电体膜,都存在通过测定将膜厚判定为非标准内的例子。因此,通过光学式测定方法得到的压电体膜的膜厚值可靠性不高。本发明是鉴于这样的问题而完成的,其目的是,提供压电体膜的膜厚值可靠性高的带压电体膜的基板、使用该基板的压电体膜元件及其制造方法。解决问题的方法根据本发明的第1种方式,可以提供一种带压电体膜的基板:其顺次层叠有在主面上形成的下电极和在上述下电极上形成的钙钛矿结构的压电体膜;上述压电体膜的厚度为0.3μm以上10μm以下;在表示反射率和波长关系的反射光谱,即上述压电体膜的中心部和外周部的各至少1点的上述反射光谱中,极大值和极小值分别具有至少1个,并且上述最大值中至少1个的上述反射率为0.4以上,所述反射率由对上述压电体膜的表面照射的上述波长400nm~800nm范围内的照射光在上述压电体膜的表面反射的光与上述照射光透过上述压电体膜在上述下电极的表面反射的光通过干涉而得到的反射光算出。根据本发明的第2种方式,可提供如下的第1种方式的带压电体膜的基板:上述下电极在对其表面照射波长400nm~800nm范围的照射光时的反射率,在上述波长400nm~800nm范围的一半以上的区域内为0.7以上。根据本发明的第3种方式,可提供上述压电体膜的表面粗糙度Ra为20nm以下的第1种方式或第2种方式的带压电体膜的基板。根据本发明的第4种方式,可提供如下的第1~第3种方式中任意一种的带压电体膜的基板:当将上述压电体膜中心位置与距上述压电体膜中心位置规定距离的位置的表面高度之差设为翘曲量时,上述翘曲量为60μm以下。根据本发明的第5种方式,可提供上述压电体膜为由通式(K1-xNax)NbO3(0<x<1)表示的铌酸钾钠的第1~第4种方式中任意一种的带压电体膜的基板。根据本发明的第6种方式,可提供如下的第1~第5种方式中任意一种的带压电体膜的基板:上述下电极为以Pt、Ru、Ir、Sn、In或这些物质的氧化物作为主要成分的电极层,或者包含这些电极层的层叠结构的电极层。根据本发明的第7种方式,可提供具备第1~第6种方式中任意一种的带压电体膜的基板和在上述压电体膜上形成的上电极的压电体膜元件。根据本发明的第8种方式,可提供一种压电体膜元件的制造方法,在基板上用溅射法分别形成至少下电极、钙钛矿结构的压电体膜和上电极的压电体膜元件的制造方法中,具有:在形成上述上电极之前,对上述下电极上形成的上述压电体膜的表面照射波长400nm~800nm范围的照射光的工序;对由上述照射光在上述压电体膜的表面反射的光和上述照射光透过上述压电体膜在上述下电极表面反射的光的干涉而得到的反射光进行接收的工序;得到表示由上述反射光算出的反射率和上述波长关系的反射光谱的工序;以及判断在上述压电体膜的中心部和外周部的各至少1点所得到的上述反射光谱中,极大值和极小值分别具有至少1个,并且上述极大值中至少1个的上述反射率为0.4以上的工序。发明效果根据本发明,可以得到压电体膜的膜厚值可靠性高的带压电体膜的基板及压电体膜元件。附图说明图1是表示本发明一个实施方式涉及的压电体膜元件的截面的图。图2是说明测定压电体膜膜厚的方法的图。图3是说明压电体膜表面的测定点的图。图4是对本发明实施例1的压电体膜的中心部进行测定时得到的反射光谱。图5是对本发明实施例1的压电体膜的外周部进行测定时得到的反射光谱。图6是对本发明实施例2的压电体膜的中心部进行测定时得到的反射光谱。图7是对本发明比较例1的压电体膜的中心部进行测定时得到的反射光谱。图8是对本发明比较例2的压电体膜的中心部进行测定时得到的反射光谱。图9是对本发明比较例2的压电体膜的外周部进行测定时得到的反射光谱。图10是对本发明比较例3的压电体膜的中心部进行测定时得到的反射光谱。图11是对本发明比较例3的压电体膜的外周部进行测定时得到的反射光谱。图12是对本发明实施例1的Pt膜的中心部进行测定时得到的反射光谱。图13是对本发明比较例3的Pt膜的中心部进行测定时得到的反射光谱。符号说明1基板2下电极3压电体膜4上电极10带压电体膜的基板100压电体膜元件具体实施方式如上所述,采用光学式测定方法,可以非破坏性地对压电体膜的膜厚值进行测定。在光学式的测定方法中,对压电体膜照射光,由通过反射的光的干涉而得到的反射光获得反射光谱,基于该反射光谱算出膜厚值。然而,在光学式测定方法中有测定值与实测值不同的情况,存在不能精度良好地测定膜厚值,膜厚测定值的可靠性低这样的问题。这个问题可以认为是由于成膜的压电体膜的翘曲,压电体膜被光照射的测定面与接收反射的光的受光面不平行,不能正确地测定通过干涉所得的反射光。另外,可以认为是由于成膜的压电体膜的表面粗糙度,照射的光在压电体膜的表面发生散射而不能正确地测定反射光。即,一直以来,由于反射的差异而不能正确测定反射光,从而基于得到的反射光谱来算出膜厚的测定值。于是,本发明人等着眼于光学式膜厚测定中得到的反射光谱,发现可以通过其波形来判断膜厚测定的正确性,从而完成了本发明。以下,对本发明的一个实施方式涉及的带压电体膜的基板、压电体膜元件及其制造方法进行说明。下面在对压电体膜元件的制造方法进行说明以后,再对带压电体膜的基板及压电体膜元件的构成进行说明。图1表示本发明的一个实施方式涉及的压电体膜元件的截面图。[压电体膜元件的制造方法]本实施方式的压电体膜元件100的制造方法具有如下工序:通过溅射法在基板1上形成下电极2的工序;在下电极2上形成钙钛矿结构的压电体膜3的工序;在形成上电极4之前,对下电极2上形成的压电体膜的表面3a照射400nm~800nm范围的照射光的工序;对由照射光在压电体膜的表面3a反射的光与照射光透过压电体膜3在下电极的表面2a反射的光通过干涉而得到的反射光进行接收的工序;得到表示由反射光算出的反射率与波长关系的反射光谱的工序;判断在压电体膜3的中心部和外周部各至少1点处得到的反射光谱中,极大值和极小值分别至少具有1个,并且极大值的至少1个的反射率为0.4以上的工序;以及在上述压电体膜3上形成上电极4的工序。首先,应用溅射法在基板1的主面上形成下电极2。基板1优选使用Si(硅)基板、带氧化膜的Si基板、或者SOI(绝缘体上硅,SiliconOnInsulator)基板。在Si基板中,例如有时使用Si基板表面为(100)面方向的(100)Si基板,但也可以是与(100)面不同面方向的Si基板。另外,除了Si基板外,基板1也可以使用石英玻璃基板、GaAs基板、蓝宝石基板、不锈钢等金属基板、MgO基板、SrTiO3基板等。另外,作为带氧化膜的Si基板的氧化膜,可以列举由热氧化形成的热氧化膜、或者由CVD(化学气相沉积,ChemicalVaporDeposition)法形成的Si氧化膜等。另外,当为MgO、SrTiO3、SrRuO3、石英玻璃等氧化物基板时,也可以在基板1上不形成上述氧化膜而直接形成下电极2。下电极2也是使压电体膜3成膜的基底层,形成为(001)优先取向晶体、(110)优先取向晶体和(111)优先取向晶体中至少一个共存的结构。作为下电极2,优选为以Pt、Ru、Ir、Sn、In或这些物质的氧化物为主要成分的电极层,或者包含这些电极层的层叠结构的电极层。另外,作为下电极2,优选对其表面照射波长400nm~800nm范围的照射光时的反射率,在波长400nm~800nm范围的一半以上的区域内为0.7以上。将对于下电极2的表面2a,在波长400nm~800nm范围的一半以上的区域内反射率为0.7以上时(后述实施例1)的反射光谱示于图12,在波长400nm~800nm范围的一半以上的区域内反射率不为0.7以上时(后述比较例3)的反射光谱示于图13。对图12和图13所示的反射光谱进行比较时,图13所示反射光谱中反射率为0.7以上的区域在规定的波长范围内不足一半,表示下电极的表面2a粗糙。这种情况下,透过压电体膜3在下电极的表面2a反射的光被散射,膜厚的测定值的可靠性降低。另外,可以认为在下电极2上成膜的压电体膜3的表面粗糙度恶化。另外,为了提高基板1与下电极2的密合性,也可以在基板1与下电极2之间设置密合层。作为密合层,有Ti层等。然后,在下电极2上形成钙钛矿结构的压电体膜3,得到带压电体膜的基板10。在压电体膜3的成膜中,通过溅射法,例如使用(K1-xNax)NbO3烧结体作为靶,在基板温度(基板表面的温度)为100℃以上900℃以下、导入气体为Ar等气体、导入气体氛围气气压为0.02Pa以上5Pa以下的条件下进行。压电体膜3具有钙钛矿结构,是作为晶系的准立方晶(pseudocubic)、立方晶、正方晶、斜方晶、六方晶、单斜晶、三斜晶或斜方面体的晶体结构,或者这些晶体结构中至少一种晶体结构共存的状态。压电体膜3优选含有由通式(K1-xNax)NbO3(0<x<1)表示的铌酸钾钠(以下记为“KNN”),优选组成x=Na/(K+Na)比例在0.40≤x≤0.70范围内。另外,在KNN压电体膜中,作为其他元素,还可以含有5%以下的Li、Ta、Sb、Ca、Cu、Ba、Ti等。下面,对由上述工序形成的压电体膜3的膜厚进行测定,并且判断该膜厚值是否是高可靠性的。在本实施方式中,进行如下工序:对下电极2上形成的压电体膜的表面3a照射波长400nm~800nm范围的照射光的工序;对由照射光在压电体膜表面3a反射的光与照射光透过压电体膜3在下电极2的表面2a反射的光通过干涉而得到的反射光进行接收的工序;得到表示由反射光算出的反射率与波长关系的反射光谱的工序;以及判断在压电体膜3的中心部和外周部各至少1点处得到的反射光谱中,极大值和极小值分别至少具有1个,并且极大值中至少1个的反射率为0.4以上的工序。具体地,如图2所示,将上述所得带压电体膜的基板10置于平台20上,在压电体膜的表面3a的任意位置,配置具有光源30a和受光部30b的测量头30,从光源30a照射含有波长400~800nm的照射光。作为照射光的照射位置,选择压电体膜3的中心部和外周部各至少1点。中心部表示在半径为r的基板上,例如比r/3更内侧的区域;外周部表示比2r/3更外侧的区域。也就是说,如图3所示,中心部表示的是距压电体膜的中心点(0,0)规定距离的区域(图中的A区域),外周部表示的是比中心部更外周方向的区域(图中的B区域)。通过从中心部和外周部各选择1点,可以确认压电体膜的表面3a的测定条件的差异,例如由于基板的翘曲引起的测定条件的差异。源于光源30a的照射光在压电体膜的表面3a被反射,并且透过压电体膜3而在下电极的表面2a被反射。在下电极的表面2a反射的光的相位发生偏移,与在压电体膜的表面3a反射的光干涉而相长或相消。在受光部30b接收在压电体膜3和下电极2反射的光通过干涉而得到的反射光。对接收的反射光进行分光,并且对于每个波长,由入射光的强度和反射光的强度算出比率(反射率),得到表示反射率和波长关系的反射光谱。得到的反射光谱在照射光的波长(400~800nm)范围内显示规定波形。此处,对于表示反射率和波长关系的反射光谱以及从反射光谱算出膜厚的方法,使用图4进行说明。图4表示测定反射光谱的一个例子(后述的实施例1)。在图4中,反射光谱显示为具有多个峰的周期性波形,波形具有多个极大值和极小值。当在基板1上的压电体膜3上垂直照射光时,来自压电体膜的表面3a和下表面(下电极2的表面2a)的2种反射光,根据相互之间的相位关系而发生相长或相消。相位关系由压电体膜的膜厚(d)、光学常数(n:压电体膜的折射率)、波长(λ)决定。当2nd=iλ(i:整数)时,发生相长而成为极大值。另一方面,当2nd=(i+1/2)λ时,发生相消而成为极小值。反射率R,例如在照射光对压电体膜3垂直照射时,用表示。使用该函数,以符合实际测定的反射光谱的方式进行参数拟合,分别求得常数A、B、d。最终求得的解,选择使反射率的最大值与最小值的波长偏移为最小的值。在反射光谱中,其振幅越大、极值附近的变化越陡峭,表示拟合的精度、也就是测定精度越高。另外,极大值的最大值大时,表示反射光谱的振幅在该范围内变大;反之,极大值的最大值小时,表示振幅在该范围以下(0.4以下时在其以下)。即,越是极大值的反射率尽可能接近1、在0.4以上的点多的反射光谱,表示测定的精度越高,表示算出的膜厚值的可靠性越高。另一方面,具有反射率不到0.4的极大值的反射光谱也可以算出膜厚值,但是,反射光的接收不能充分进行,使得测定精度低、算出的膜厚值可靠性低。因此,得到例如图4所示那样的反射光谱的情况下,可以判断通过光学式进行了正确的测定。与此相对,由于压电体膜3的状态而不能通过光学式正确进行膜厚测定时的反射光谱,显示例如图7或图9所示那样的波形。图7表示的是由于压电体膜的表面粗糙度大而不能正确接收反射光时(后述的比较例1)的反射光谱。图9表示的是由于压电体膜的翘曲大而不能正确接收反射光时(后述的比较例2)的反射光谱。图7表示的是压电体膜3的表面粗糙度(算术平均粗糙度Ra)超过20nm时的反射光谱。对于表面粗糙度大的压电体膜3,照射的照射光在压电体膜的表面3a发生散射。然后,由于散射使反射光的反射率降低,在受光部30b不能充分接收反射光,成为图7所示那样的反射光谱。在图7中可知,没有极大值的反射率在0.4以上的点,在全部波长范围内反射率极端小。另外,图9表示的是压电体膜的翘曲量超过60μm时的反射光谱。对于翘曲量大的带压电体膜的基板10,其外周部处于光源30a的测定面与受光部30b的受光面大大偏离平行的状态。这种状态下,反射光有一定的角度而使反射光的反射率降低,在受光部30b不能充分接收反射光,成为图9所示那样的反射光谱。在图9中可知,没有极大值的反射率在0.4以上的点,在全部波长范围内反射率极端小。其中,基板的翘曲量设定为,压电体膜的中心位置与距压电体膜的中心位置规定距离的位置的表面高度之差。随后进行如下判断:压电体膜3的中心部和外周部的各至少1点所得到的反射光谱中,极大值和极小值分别至少具有1个,并且极大值中至少1个的反射率为0.4以上。反射后发生干涉的反射光由于压电体膜3的表面粗糙度、基板1的翘曲等而未充分被接收时,在中心部分和外周部分别得到的反射光谱不显示规定的波形,因而可以判断测定的精度低。因此,本实施方式中,根据得到的反射光谱的波形,可以判断算出的压电体膜3的膜厚值的可靠性。即,根据反射光谱,可以判断测定的精度,得到可靠性高的压电体膜的膜厚值。接着,通过溅射法在上述所得压电体膜3上形成上电极4,得到本实施方式的压电体膜元件100。由于上电极4不像下电极2那样对压电体膜3的晶体结构有大的影响,因此对上电极4的材料没有特殊限制。作为上电极4,与下电极2同样地,可以是以Pt、Ru、Ir、Sn、In或这些物质的氧化物为主要成分的电极层,或者包含这些电极层的层叠结构的电极层。[带压电体膜的基板及压电体膜元件]本发明的一个实施方式涉及的带压电体膜的基板10,顺次层叠有在主面上形成的下电极2和在下电极2上形成的钙钛矿结构的压电体膜3,压电体膜3的厚度为0.3μm以上10μm以下。并且,在表示反射率和波长关系的反射光谱,即压电体膜3的中心部和外周部的各至少1点的反射光谱中,极大值和极小值分别至少具有1个,并且极大值中至少1个的反射率为0.4以上,所述反射率由对压电体膜的表面3a照射的波长400nm~800nm范围的照射光在压电体膜的表面3a反射的光与照射光透过压电体膜3在下电极的表面2a反射的光通过干涉而得到的反射光算出。另外,本发明的一个实施方式涉及的压电体膜元件100,具备带压电体膜的基板10和在压电体膜3上形成的上电极4。带压电体膜的基板10和压电体膜元件100的压电体膜3,在中心部和外周部得到的反射光谱为规定波形,反射光被充分接收。因此,压电体膜3不仅测定的膜厚值可靠性高,其表面粗糙度、翘曲也小。带压电体膜的基板10和压电体膜元件100中,压电体膜3的厚度为0.3μm以上10μm以下。不足0.3μm时,由于膜厚在照射光的波长以下,不会发生干涉,得到的反射光谱的极值消失,因此难以测定该膜厚。另一方面,超过10μm时,由于压电体膜3内部的光吸收等,来自膜下表面的反射非常小,膜厚的测定变得困难。另外,压电体膜3的表面粗糙度(算术平均粗糙度Ra)为20nm以下。并且,翘曲量为60μm以下。[本实施方式的效果]根据本实施方式,获得以下所示1种或多种效果。本实施方式中,在压电体膜的中心部和外周部得到的反射光谱显示规定的波形。根据该构成,判断出通过光的反射而发生了干涉的反射光的反射率高、测定的精度高,从而压电体膜的膜厚值的可靠性高。另外,由于反射光谱显示为规定的波形,因此压电体膜的表面粗糙度、带压电体膜的基板的翘曲小。而且,由于可使用光来非接触地测定,因此可以制成无破坏、污染(伤痕、污垢),高品质的压电体膜。另外,本实施方式中,设有从制造工序中所得的反射光谱对其测定的精度进行判断的工序。根据该构成,在正确的膜厚值的测定的同时,还可以判断表面粗糙度大的压电体膜、翘曲大的基板。另外,本实施方式中,优选下电极在对其表面照射波长400nm~800nm范围的照射光时的反射率,在波长400nm~800nm范围的一半以上的区域内为0.7以上。根据该构成,通过抑制透过压电体膜在下电极的表面反射的光的散射、提高反射光的反射率,可以提高压电体膜的膜厚测定精度,并且可以提高膜厚值的可靠性。另外,本实施方式中,压电体膜的表面粗糙度(算术平均粗糙度Ra)为20nm以下。而且,翘曲量为60μm以下。实施例通过以下方法和条件,制造本发明涉及的带压电体膜的基板。这些实施例是本发明涉及的带压电体膜的基板的一个例子,本发明不受这些实施例的限制。(实施例1)基板使用双面镜面的带热氧化膜的Si基板(厚度0.525mm,直径100mm,(100)面方位,热氧化膜的厚度200nm)。首先,以RF(射频)磁控溅射法在基板上形成Ti密合层(膜厚2nm)、Pt下电极((111)面优先取向,膜厚200nm)。Ti密合层和Pt下电极在基板温度200℃、放电功率200W、导入气体为Ar气氛、压力2.5Pa、成膜时间1~3分钟的条件下成膜。在其上以射频磁控溅射法形成0.5μm的(K1-xNax)NbO3薄膜。(K1-xNax)NbO3压电体膜使用Na/(K+Na)=0.65的(K1-xNax)NbO3靶,在基板温度500℃、放电功率2000W、导入气体为Ar气氛、压力0.3Pa的条件下成膜。KNN压电体膜的溅射成膜时间以使压电体膜的膜厚约为0.5μm的方式调节,制得实施例1的带压电体膜的基板。实施例1的制造条件如以下表1所示。表1接着,对得到的实施例1的带压电体膜的基板,通过光学式膜厚测定算出膜厚值。以下对其测定方法进行说明。(光学式膜厚测定)膜厚测定时,使用薄膜测定装置(F20、Filmetrics公司制)进行光学式的非接触膜厚测定。作为测定部位,如图3所示,选择半径为r(50mm)的压电体膜表面的中心部的中心点(0,0)、以及位于距中心点40mm的外周部的外周点(0,40)2个点。对实施例1的压电体膜表面的中心点(0,0)照射波长400nm~800nm范围的照射光,得到图4所示那样的反射光谱的波形。根据图4的反射光谱,确认到:极大值和极小值分别至少有1个,反射率为0.4以上的极大值有2个,极大值的最大反射率为0.81。从该反射光谱的波形,通过曲线拟合算出实施例1的压电体膜中心点的膜厚值。中心点的膜厚的测定值为0.53μm。另外,同样地对压电体膜表面的外周点(0,40)照射规定波长范围的光,得到图5所示那样的反射光谱的波形。根据图5的反射光谱,确认到极大值和极小值分别至少有1个,反射率为0.4以上的极大值有2个,并确认到极大值的最大反射率为0.78。然后,算出外周部的膜厚值,结果膜厚的测定值为0.51μm。根据图4和图5确认到:得到的反射光谱均为规定的波形,压电体膜的膜厚值与制造时预期的膜厚值的误差小。由此可以认为,通过光学式膜厚测定算出的膜厚值的可靠性高。在这一点上,为了证实膜厚值的可靠性高,在本实施例中,通过SEM膜厚测定测得正确的膜厚值,与通过光学式膜厚测定得到的测定值进行比较。另外,测定压电体膜的表面粗糙度和翘曲,确认到在压电体膜的中心点和外周点由测定条件的差异造成的影响小。以下,对各测定方法进行说明。(SEM膜厚测定)为了评价由反射光谱得到的利用光学式的膜厚测定值的可靠性,使用扫描电子显微镜(SEM)对压电体膜的截面进行测定(测定条件:10000倍、5kV),求得正确的膜厚值,与上述光学式测定值进行比较。实施例1的压电体膜的SEM测定结果确认到,中心点和外周点的膜厚测定值均为0.5μm,从本发明的压电体膜的反射光谱测得的中心点的测定值0.53μm、外周点的测定值0.51μm分别与使用SEM膜厚测定的测定值之间的误差小,结果大体一致。另外,本实施例中,如果在中心点和外周点,利用光学式的膜厚测定值与利用SEM的膜厚测定值的误差均不到±10%,则判断利用光学式的膜厚测定值具有可靠性。(表面粗糙度的测定)表面粗糙度测定时,用原子间力显微镜(AFM:AtomicForceMicroscopy)检查压电体膜表面的凹凸。测定是以4nm间距扫描1μm×1μm的范围而解析表面粗糙度。测定算术平均粗糙度Ra作为这里所示的表面粗糙度。对于其计算方法,使用在东阳Technica发行的《大型样品SPM观测系统操作指南》(大型サンプルSPM観測システムオペレーションガイド)(1996年)等中写明的定义式。测定实施例1的压电体膜的表面粗糙度,结果算术平均粗糙度Ra为2.8nm、反射光谱的反射率高,从而也确认到压电体膜表面的光散射少。(基板的翘曲)翘曲的测定是测定压电体膜的中心点与压电体膜的外周点的表面高度之差。测定实施例1的带压电体膜的基板的翘曲时,从基板的翘曲为12μm、反射光谱的反射率高,也可以确认压电体膜的表面较平坦、反射光处于直接被反射而被充分检测的状态。将上述压电体膜的评价结果示于以下的表2中。另外,测定实施例1的带压电体膜的基板的下电极在波长400nm~800nm范围内的反射光的反射率时,得到图12所示那样的反射光谱。根据图12可以确认在波长400nm~800nm范围的一半以上,反射率为0.7以上。表2(实施例2~4)实施例2~4中,如表1所示,变更压电体膜的成膜条件(下电极的成膜温度、KNN压电体膜的成膜温度、成膜压力),以使厚度为3μm的方式制造压电体膜。对于得到的实施例2的压电体膜,与实施例1同样地测定膜厚时,在压电体膜的中心点得到如图6所示那样的反射光谱。根据图6的反射光谱,可以确认极大值和极小值分别至少有1个,反射率为0.4以上的极大值有9个,并且确认到极大值的最大反射率为0.70。然后,算出中心点的膜厚,如表2所示,确认到膜厚的测定值为2.95μm,与通过SEM的测定值(3.0μm)的误差小。在实施例2的压电体膜的外周部,反射光谱没有图示,但得到了与图6所示反射光谱同样的反射光谱。在外周点确认到,通过光学式的膜厚测定值为2.84μm,与通过SEM的测定值(2.9μm)之间的误差小。另外,实施例2的压电体膜的算术平均粗糙度Ra为4.1nm,基板的翘曲为35μm。另外,尽管没有图示,实施例3和4也得到了与上述实施例1同样的反射光谱。对实施例3和4的压电体膜的膜厚进行测定时,如表2所示,确认到任意一个压电体膜通过光学式的测定值与通过SEM的测定值之间的误差都小,膜厚值的可靠性高。而且,确认了表面粗糙度和基板的翘曲小、反射光的反射率高、测定的可靠性高。(比较例1)在比较例1中,使压电体膜以3μm成膜,并且使成膜时的压力为0.01Pa,增加压电体膜的表面粗糙度而制造,除此以外,与实施例1同样地制造带压电体膜的基板。将比较例1的制造条件示于以下的表3。表3比较例1的压电体膜,通过肉眼观察可见整体发黑,通过光学显微镜观察表面时确认有大的凹凸。与实施例1同样地通过光学式测定评价得到的比较例1的压电体膜时,在压电体膜的中心点得到了如图7所示那样的反射光谱。根据图7的反射光谱,可知与由SEM测定的膜厚相当的图6相比,反射率极小。另外,确认了尽管存在极大值和极小值,但反射率0.4以上的极大值1个也没有,极大值的最大反射率在中心点为0.07,非常小。另外,外周点的反射光谱尽管没有图示,但显示与图7所示反射光谱同样的波形,并确定了反射率0.4以上的极大值1个也没有,极大值的最大反射率在中心点为0.02,非常小。想要从这些反射光谱的波形通过曲线拟合而算出膜厚,但拟合误差增大为一位数以上,无法算出正确的膜厚值。可以认为这是由于压电体膜的表面粗糙,因为表面散射而处于不能充分检测反射光的状态。另外,测定压电体膜的表面粗糙度时,算术平均粗糙度Ra为25nm。另外,对于基板的翘曲也与实施例1同样地进行了测定,为28μm,未确认到大的翘曲。将比较例1的评价结果示于下面的表4。其中,在表4中,“×”表示拟合误差大,无法测定膜厚值。表4(比较例2)在比较例2中,使压电体膜以3μm成膜,并且使成膜温度为650℃,使带压电体膜的基板的翘曲变大而制造,除此以外,与实施例1同样地制造带压电体膜的基板。对得到的比较例2的压电体膜,与实施例1同样地通过光学式测定进行评价时,在压电体膜的中心点和外周点分别得到图8和图9所示那样的反射光谱。根据图8所示的中心点的反射光谱,确认了极大值和极小值分别存在1个以上,反射率0.4以上的极大值有4个,并且确认了极大值的最大反射率为0.52。与此相对,根据图9所示的外周点的反射光谱,确认了虽然极大值和极小值分别存在1个以上,但是反射率0.4以上的极大值不存在,极大值的最大反射率为0.32。即,图9的反射光谱与图8的反射光谱相比时,尽管是相同的样品,但是在全部波长范围内的反射率大大降低。可以认为这是由于基板的翘曲使得外周点的光的反射与中心点不同,垂直照射的光未被直接反射,处于未被受光部充分检测的状态。另外,测定基板的翘曲时,翘曲量为65μm。另外还对压电体膜的表面粗糙度进行了测定,算术平均粗糙度Ra为6.3nm,未确认到大的凹凸。其中,基板的翘曲可以通过用平台进行真空吸附的方法等将基板矫正至平坦而测定,但是由于翘曲量过大,因此伴随着矫正有可能发生压电体膜的破裂。(比较例3)在比较例3中,使作为下电极的Pt电极层的成膜温度为400℃、将压电体膜以3μm成膜,除此以外,与实施例1同样地制造带压电体膜的基板。测定比较例3的带压电体膜的基板的下电极(Pt电极层)在波长400nm~800nm范围内的反射光的反射率时,得到图13所示那样的反射光谱。根据图13,确认了反射率为0.7以上的是波长640nm~800nm的范围,不足波长400nm~800nm范围的一半。即比较例3的Pt电极层表面粗糙。比较例3的压电体膜在上述表面粗糙的Pt电极层上成膜后呈白色浑浊,而不是透明或半透明。对得到的比较例3的压电体膜与实施例1同样地通过光学式测定进行评价时,在压电体膜的中心点和外周点分别得到图10和图11所示那样的反射光谱。根据图10和图11,确认了在中心点和外周点,虽然极大值和极小值分别存在1个以上,但是没有反射率0.4以上的极大值,极大值的最大反射率在中心点为0.31、在外周点为0.21。从反射光谱得到的膜厚的测定值,中心点为2.68μm、外周部为1.99μm,确认到与通过SEM的中心点的测定值为3.0μm、通过SEM的外周点的测定值为2.7μm分别存在大的误差。可以认为这是由于除了压电体膜上的散射以外,透过压电体膜而进入的光还在Pt电极层的表面发生散射而处于不能充分检测反射光的状态。另外,压电体膜的算术平均粗糙度Ra为16nm、基板的翘曲为30μm,未确认到大的问题。此外,上述实施例中,下电极使用的是Pt电极层,但是,使用含有Pt的合金、Ru、Ir或金属氧化物电极时,也可以获得同样的效果。另外密合层使用的是Ti层,但也可以使用Ta层,没有密合层时也可以获得同样的效果。