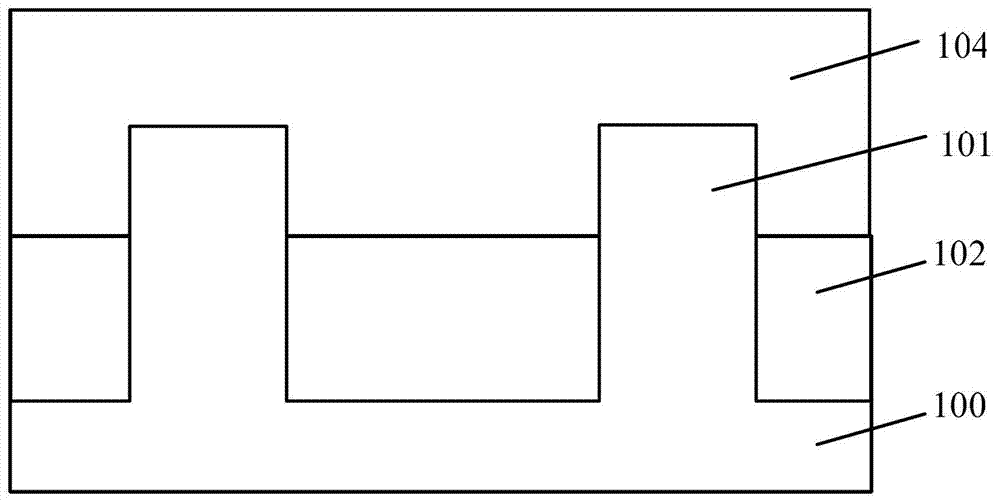
本发明涉及半导体制造领域,特别涉及一种鳍式场效应管的形成方法。
背景技术:MOS晶体管通过在栅极施加电压,调节通过沟道区域的电流来产生开关信号。但当半导体技术进入30纳米以下节点时,传统的平面式MOS晶体管对沟道电流的控制能力变弱,造成严重的漏电流。鳍式场效应晶体管(FinFET)是一种新兴的多栅器件,它一般包括凸出于半导体衬底表面的半导体鳍部,覆盖部分所述鳍部的顶部和侧壁的栅极结构,位于所述栅极结构两侧的鳍部内的源区和漏区。为了降低鳍式场效应晶体管栅极的寄生电容,提高器件速度,高K栅介电层与金属栅极的栅极叠层结构被引入到鳍式场效应晶体管中。现有金属栅极与高K栅介电层的栅极叠层结构通常采用“后栅(gatelast)”工艺制作。图1~图2示出了现有技术的一种鳍式场效应晶体管的形成过程的剖面结构示意图。首先,请参考图1,提供半导体衬底100,所述半导体衬底100上具有若干凸起的鳍部101;然后,在相邻鳍部101之间的半导体衬底100上形成隔离结构102,所述隔离结构102的顶部表面低于所述鳍部101的顶部表面;接着,形成覆盖所述鳍部101和隔离结构102上的牺牲层103。在后栅(Gate-last)工艺中,所述的牺牲层103后续用于形成伪栅。由于所述隔离结构102的顶表面低于所述鳍部101的顶表面,相邻鳍部101之间具有凹槽,在形成牺牲层103时,会使得隔离结构102上方的牺牲层的表面低于鳍部101上方的牺牲层的表面,造成牺牲层103表面凹凸不平,栅牺牲层103的厚度均匀性较差,不利于光刻中对焦深的控制,影响后续制造工艺。而为了解决该问题,现有通常会对形成的牺牲层103进行平坦化工艺,参考图2,采用化学机械研磨(CMP)工艺抛光所述牺牲层103(如图1所示),形成伪栅材料层104,形成的伪栅材料层104的表面比较平整,厚度的均匀性较好。后续通过刻蚀伪栅材料层104,形成横跨鳍部101的侧壁和顶部表面的伪栅。但是,现有化学机械研磨所述牺牲层103的过程中,难以控制抛光后的形成伪栅材料层104的厚度,使得伪栅材料层104的厚度具有不确定性,通过刻蚀伪栅材料层104形成的伪栅的厚度也具有不确定性,造成后续伪栅的去除深度和金属栅的填充深度具有不确定性。其他有关鳍式场效应晶体管的形成方法,还可以参考公开号为US2011/0147812A1的美国专利申请。
技术实现要素:本发明解决的问题是精确控制鳍式场效应晶体管的伪栅的高度。为解决上述问题,本发明技术方案提供了一种鳍式场效应晶体管的形成方法,包括:提供半导体衬底,所述半导体衬底上具有若干分立的鳍部,相邻鳍部之间具有隔离结构,所述隔离结构的表面低于鳍部的顶部表面;形成覆盖所述鳍部以及隔离结构的牺牲层;对所述牺牲层进行离子注入,在所述牺牲层中形成离子掺杂层;采用化学机械研磨工艺平坦化所述牺牲层,以离子掺杂层作为停止层;刻蚀剩余的牺牲层,形成横跨所述鳍部顶部和侧壁表面的伪栅。可选的,所述牺牲层的材料为多晶硅或无定形硅。可选的,所述牺牲层的厚度大于等于600纳米。可选的,所述牺牲层的材料为多晶硅时,所述离子注入的杂质离子为锗离子、硅离子和碳离子中的一种,形成的离子掺杂层为非晶层,化学机械研磨所述牺牲层时,当检测到研磨的速率发生变化时,停止研磨的进行。可选的,化学机械研磨所述牺牲层时,当检测到研磨速率从一定的速率逐渐增大,达到最大值后再逐渐减小时,停止研磨的进行。可选的,所述牺牲层的材料为多晶硅或无定形硅时,所述离子注入的杂质离子为氧离子、氮离子、砷离子、硼离子和锑离子中的一种,化学机械研磨所述牺牲层时,当检测到研磨液中杂质离子的浓度变化时,停止研磨的进行。可选的,化学机械研磨所述牺牲层时,当检测到研磨液中的杂质离子的浓度先逐渐增大,达到最大值后再逐渐减小时,停止研磨的进行。可选的,所述离子注入的能量为1~20Kev,剂量大于等于1E15/cm2可选的,在所述牺牲层表面形成填充材料层,以填充牺牲层表面形成的凹陷,对所述牺牲层和填充材料层进行离子注入,在牺牲层中形成离子掺杂层。可选的,所述牺牲层的厚度为30~200纳米。可选的,所述离子注入的杂质离子为锗离子、硅离子、碳离子、氧离子、氮离子、砷离子、硼离子或锑离子,所述离子注入的能量为1~20Kev,剂量大于等于1E15/cm2。可选的,所述填充材料层为无定形碳。可选的,所述填充材料层的厚度为200~400纳米。可选的,所述填充材料层的形成工艺为可流动性化学气相沉积。可选的,所述化学机械研磨工艺采用的研磨液的主体成分为胶体氧化硅,稀释剂为氢氧化钠,胶体氧化硅的质量百分含量为10%~20%,研磨液的PH值为10~13。可选的,还包括:形成覆盖所述鳍部和伪栅的介质层;平坦化所述介质层,暴露出伪栅的顶部表面;去除所述伪栅,形成凹槽;在凹槽中填充满金属,形成金属栅极。可选的,在凹槽中填充金属之前,在凹槽的侧壁和底部表面形成高K栅介质层,在高K栅介质层上形成功能层。可选的,在所述金属栅极两侧的鳍部内形成鳍式场效应管的源/漏区。可选的,所述源/漏区为嵌入式源漏区。与现有技术相比,本发明技术方案具有以下优点:在形成覆盖所述鳍部以及隔离结构的牺牲层后,对所述牺牲层进行离子注入,在所述牺牲层中形成离子掺杂层,当采用化学机械研磨工艺平坦化所述牺牲层时,以离子掺杂层作为停止层,然后刻蚀剩余的牺牲层,形成横跨所述鳍部顶部和侧壁表面的伪栅。由于离子掺杂层是通过注入工艺形成的,注入工艺可以较为精确的控制在牺牲层中形成的离子掺杂层的位置,当以牺牲层中的离子掺杂层作为研磨的停止层时,在研磨牺牲层的过程中,即使研磨速率会发生变化,剩余的牺牲层的厚度也能较精确的控制,使得刻蚀剩余的牺牲层形成的伪栅的高度也比较精确。进一步,所述牺牲层的材料为多晶硅,进行离子注入时注入的杂质离子为锗离子、硅离子或碳离子,使得注入离子位置对应的多晶硅非晶化,形成的离子掺杂层为非晶层,多晶硅被非晶化后形成的非晶层的熔点、密度和硬度都会明显低于多晶硅,由于非晶层与多晶硅层不同的物理特性,在进行化学机械研磨时,多晶硅的研磨速率会小于非晶层的研磨速率,由于形成的非晶层是位于牺牲层中,当从牺牲层表面向下研磨时,研磨到非晶层时的研磨速率会发生明显变化,因此通过检测研磨过程中研磨的速率变化,即可判断是否研磨到非晶层,从而停止研磨的进行,以便较为精确的控制剩余的牺牲层的厚度。进一步,当所述牺牲层的材料为多晶硅或无定形硅时,所述离子注入的杂质离子为氧离子、氮离子、砷离子、硼离子或锑离子一种,并且所述掺杂离子与研磨液的成分和牺牲层的材料成分不相同,形成的离子掺杂区中含有其中某一种掺杂离子(比如:硼离子),离子掺杂层是位于牺牲层中,从牺牲层表面向下研磨,当研磨到离子掺杂层时,研磨液中某种杂质离子(比如:硼离子)的浓度会从无到有,并逐渐增大,因此当检测到研磨液中杂质离子的浓度变化时,停止研磨的进行。进一步,所述化学机械研磨工艺采用的研磨液的主体成分为胶体氧化硅,稀释剂为氢氧化钠,胶体氧化硅的质量百分含量为10%~20%,研磨液的PH值为10~13,减小对研磨过程中研磨速率的影响或者研磨液中杂质离子浓度的影响,有利于通过研磨速率的变化或杂质离子浓度的变化来判定研磨终点,提高研磨的效率和研磨终点判断的准确性。附图说明图1~图2是现有技术鳍式场效应晶体管的形成过程的剖面结构示意图;图3~图6为本发明第一实施例鳍式场效应晶体管的形成过程的剖面结构示意图;图7~图10为本发明第二实施例鳍式场效应晶体管的形成过程的剖面结构示意图。具体实施方式发明人在采用现有技术在制作鳍式场效应晶体管过程中发现,当采用化学机械研磨工艺平坦化牺牲层,由于牺牲层表面凹凸不平,会使得研磨过程中,化学机械研磨的研磨速率不一样,并且研磨过程中不存在研磨停止层,当通过控制研磨时间终止研磨进行时,使得剩余的牺牲层(或伪栅材料层)的厚度具有不确定性,剩余的牺牲层的厚度与目标值的偏差较大,当刻蚀剩余的牺牲层形成伪栅时,使得伪栅的高度的精度大幅减低,最终使得在去除伪栅形成凹槽,并在凹槽中形成的金属栅极的高度的精度也大幅降低,不利于器件稳定性的提高和工艺的管控。基于上述研究,发明人提出一种鳍式场效应晶体管的形成方法,在形成覆盖所述鳍部以及隔离结构的牺牲层后,对所述牺牲层进行离子注入,在所述牺牲层中形成离子掺杂层,当采用化学机械研磨工艺平坦化所述牺牲层时,以离子掺杂层作为停止层,然后刻蚀剩余的牺牲层,形成横跨所述鳍部顶部和侧壁表面的伪栅。由于离子掺杂层是通过注入工艺形成的,注入工艺可以较为精确的控制在牺牲层中形成的离子掺杂层的位置,当以牺牲层中的离子掺杂层作为研磨的停止层时,若研磨牺牲层的过程中,即使研磨速率会发生变化,剩余的牺牲层的厚度也能较精确的控制,使得刻蚀剩余的牺牲层形成的伪栅的高度也比较精确。为使本发明的上述目的、特征和优点能够更加明显易懂,下面结合附图对本发明的具体实施方式做详细的说明。在详述本发明实施例时,为便于说明,示意图会不依一般比例作局部放大,而且所述示意图只是示例,其在此不应限制本发明的保护范围。此外,在实际制作中应包含长度、宽度及深度的三维空间尺寸。第一实施例图3~图6为本发明第一实施例鳍式场效应晶体管的形成过程的剖面结构示意图。首先,参考图3,提供半导体衬底300,所述半导体衬底300上具有若干分立的鳍部301,相邻鳍部301之间的半导体衬底301上具有隔离结构302,所述隔离结构302的表面低于鳍部301的顶部表面。所述半导体衬底300可以是硅或者绝缘体上硅(SOI),所述半导体衬底300也可以是锗、锗硅、砷化镓或者绝缘体上锗。本实施例中,所述鳍部301通过刻蚀半导体衬底300形成,在本发明的其他实施例中,所述鳍部301通过外延工艺形成。所述隔离结构302用于电学隔离相邻的鳍部301,所述隔离结构302的材料为氧化硅、氮化硅或氮氧化硅。隔离结构302形成的具体过程为:首先形成覆盖所述半导体衬底300和鳍部301的隔离材料层;然后采用化学机械研磨工艺平坦化所述隔离材料层,以鳍部301的顶部表面为停止层;接着刻蚀所述剩余的隔离材料层,形成隔离结构302,所述隔离结构302的表面低于鳍部301的顶部表面。在形成隔离结构302,相连鳍部301之间会具有一个凹槽,以便后续形成横跨所述鳍部301的顶部表面和暴露的侧壁的伪栅或栅极结构。接着,请参考图4,形成覆盖所述鳍部301以及隔离结构302的牺牲层303。所述牺牲层303后续用于形成鳍式场效应管的伪栅,所述牺牲层303的形成工艺为化学气相沉积(CVD),由于隔离结构302表面低于鳍部301顶部表面,相邻的鳍部301之间具有凹槽,因此在沉积形成牺牲层303时,鳍部301上方形成的牺牲层303表面会高于隔离结构302上方形成的牺牲层303的表面,使最终形成牺牲层303的表面会凹凸不平,牺牲层303表面的平整度较差。在本实施例中,所述牺牲层303的厚度大于等于600纳米,通过形成较厚的牺牲层303,以减小隔离结构302表面和鳍部301顶部表面之间的高度差异对形成的牺牲层303表面平整度的影响,减小隔离结构302上方的牺牲层303的表面高度与鳍部301上方的牺牲层303表面的高度之间的差异,后续对牺牲层303进行离子注入,在牺牲层303中形成离子掺杂层时,使得离子掺杂层在牺牲层303中的分布的均匀性受到牺牲层303表面的平整度的影响最小,以使离子掺杂层能较准确的作为平坦化牺牲层303时的停止层。需要说明的是,本是实施例中,所述牺牲层303的厚度是指鳍部301顶部表面上方的牺牲层303的厚度。所述牺牲层303的材料为多晶硅或无定形硅,本实施例中,所述牺牲层303的材料为多晶硅。接着,请参考图5,对所述牺牲层303进行离子注入,在所述牺牲层303中形成离子掺杂层304。本实施例中所述牺牲层303的材料为多晶硅,进行离子注入时注入的杂质离子为锗离子、硅离子或碳离子,使得注入离子位置对应的多晶硅非晶化,形成的离子掺杂层304为非晶层,多晶硅被非晶化后形成的非晶层的熔点、密度和硬度都会明显低于多晶硅,由于非晶层与多晶硅层不同的物理特性,在进行化学机械研磨时,多晶硅的研磨速率会小于非晶层的研磨速率,本实施例中,由于形成的非晶层(离子掺杂层304)是位于牺牲层303中,当从牺牲层303表面向下研磨时,研磨到非晶层时的研磨速率会发生明显变化,因此通过检测研磨过程中研磨的速率变化,即可判断是否研磨到非晶层(离子掺杂层304),从而停止研磨的进行,以便较为精确的控制剩余的牺牲层303的厚度。在本发明的其他实施例中,当所述牺牲层303的材料为多晶硅或无定形硅时,所述离子注入的杂质离子为氧离子、氮离子、砷离子、硼离子或锑离子一种,并且所述掺杂离子与研磨液的成分和牺牲层的材料成分要不相同,形成的离子掺杂区304中含有其中某一种掺杂离子(比如:硼离子),离子掺杂层304是位于牺牲层303中,从牺牲层303表面向下研磨,当研磨到离子掺杂层304时,研磨液中某种杂质离子(比如:硼离子)的浓度会从无到有,并逐渐增大,因此当检测到研磨液中杂质离子的浓度变化时,停止研磨的进行。所述离子注入的能量为1~20Kev,剂量大于等于1E15/cm2,通过控制离子注入的能量,能较为准确的牺牲层303中形成的控制离子掺杂层304的深度,当离子掺杂层304的深度确定后,对牺牲层303进行平坦化时,剩余的牺牲层的厚度也就确定了,通过控制离子注入的剂量,使得离子掺杂层304中杂质离子的浓度大于等于10E18/cm3,以提高非晶化的程度或者研磨时剩余的研磨液中的待检测杂质离子的浓度,当研磨到离子掺杂层304时,从而提高检测研磨速率变化或者研磨液中杂质离子的浓度变化的灵敏度,提高检测的研磨终点判断的精度。在具体的实施例中,所述离子注入的能量和剂量根据不同的待注入杂质离子作出选择,使不同的杂质离子注入后形成的离子掺杂层304均能达到作为研磨停止层的效果,并且利于离子掺杂层304的深度控制,当注入的杂质离子为锗离子、硅离子或碳离子时,离子注入的能量为5~20Kev,剂量大于等于1E15/cm2,当注入的杂质离子为氧离子、氮离子、砷离子、硼离子或锑离子时,离子注入的能量为1~20Kev,剂量大于等于1E15/cm2。接着,参考图6,采用化学机械研磨工艺平坦化所述牺牲层303,以离子掺杂层304作为停止层。本实施例中,所述离子掺杂层304为非晶层,采用化学机械研磨工艺平坦化所述牺牲层303时,当检测到研磨速率从一定的速率逐渐增大,达到最大值后再逐渐减小时,停止研磨的进行,即相对于化学机械研磨时,以离子掺杂层304作为停止层。本实施例中进行化学机械研磨所采用的研磨设备能实时检测研磨测速率,并将检测结果实时反馈给研磨设备的主控制单元,主控制单元能根据研磨速率的变化发出停止研磨的信号,从而停止研磨的进行。在本发明的其他实施例中,所述离子掺杂层304为掺杂有杂质离子的多晶硅或无定形硅时,采用化学机械研磨工艺平坦化所述牺牲层303时,当检测到研磨液中的某一杂质离子的浓度先逐渐增大,达到最大值后再逐渐减小时,停止研磨的进行,即相对于化学机械研磨时,以离子掺杂层304作为停止层。本实施例中进行化学机械研磨所采用的研磨设备具有光谱检测单元,光谱检测单元通过检测研磨液中某一杂质离子的反射光谱的变化来确定研磨液中某一杂质离子浓度。所述化学机械研磨工艺采用的研磨液的主体成分为胶体氧化硅,稀释剂为氢氧化钠,胶体氧化硅的质量百分含量为10%~20%,研磨液的PH值为10~13,减小对研磨过程中研磨速率的影响或者研磨液中杂质离子浓度的影响,有利于通过研磨速率的变化或杂质离子浓度的变化来判定研磨终点,提高研磨的效率和研磨终点判断的准确性。在进行研磨时,所述离子掺杂层304能被全部研磨或部分剩余。最后,在平坦化所述牺牲层303后,刻蚀剩余的牺牲层303,形成横跨所述鳍部顶部和侧壁表面的伪栅(图中未示出);还包括:形成覆盖所述鳍部301和伪栅的介质层(图中未示出);平坦化所述介质层,暴露出伪栅的顶部表面;去除所述伪栅,形成凹槽(图中未示出);在凹槽中填充满金属,形成金属栅极(图中未示出);在所述金属栅极两侧的鳍部内形成鳍式场效应管的源/漏区。在凹槽中填充金属之前,在凹槽的侧壁和底部表面形成高K栅介质层,在高K栅介质层上形成功能层,调节鳍式场效应管的功函数。所述源/漏区为嵌入式源漏区,以提高鳍式场效应管的性能。第二实施例请参考图7,提供半导体衬底300,所述半导体衬底300上具有若干分立的鳍部301,相邻鳍部301之间的半导体衬底301上具有隔离结构302,所述隔离结构302的表面低于鳍部301的顶部表面;形成覆盖所述鳍部301以及隔离结构302的牺牲层303。本实施例中,所述牺牲层303的厚度为30~200纳米,由于形成的牺牲层303的厚度较薄,采用化学气相沉积工艺形成牺牲层303时,隔离结构302表面和鳍部301顶部表面之间的高度差异对形成的牺牲层303表面平整度的影响较大,使得隔离结构302上方的牺牲层的表面高度与鳍部301上方的牺牲层表面的高度之间的差异较大,牺牲层303的表面的凹凸不平(凹陷)比较明显,后续对牺牲层303进行离子注入,在牺牲层303中形成离子掺杂层时,使得离子掺杂层在牺牲层303中的分布的受到牺牲层303表面的平整度的影响较大,后续进行化学机械研磨时,不利于研磨停止时机的判断。接着,请参考图8,在所述牺牲层303表面形成填充材料层307,以填充牺牲层303表面形成的凹陷。所述填充材料层307为无定形碳,填充材料层303的形成工艺为可流动性化学气相沉积(FCVD),当形成晶粒较小的无定形碳时,无定形碳具有较好的填充凹陷的能力,并使得形成的填充材料层307具有较平坦的表面。所述填充材料层307的厚度为200~400纳米,后续进行离子注入时,填充材料层307对离子注入的影响较小,使牺牲层303中形成的离子掺杂层的分布较为均匀。然后,请参考图9,对所述牺牲层303和填充材料层307进行离子注入,在牺牲层303中形成离子掺杂层404。所述离子注入的杂质离子为锗离子、硅离子、碳离子、氧离子、氮离子、砷离子、硼离子和锑离子中的一种。由于存在填充材料层307,本实施例中,离子注入的能量要大于第一实施例中离子注入的能量,以在牺牲层303中形成离子掺杂层404,所述离子注入的能量为1~40Kev,剂量大于等于1E15/cm2。本实施例中,当所述牺牲层303的材料为多晶硅,进行离子注入时注入的杂质离子为锗离子、硅离子或碳离子,使得注入离子位置对应的多晶硅非晶化,形成的离子掺杂层304为非晶层,后续研磨填充材料层307和牺牲层303时,当研磨速率发生变化时,即可停止研磨的进行。在本发明的其他实施例中,当所述牺牲层303的材料为多晶硅或无定形硅时,所述离子注入的杂质离子为氧离子、氮离子、砷离子、硼离子或锑离子一种,并且所述掺杂离子与研磨液的成分和牺牲层303和填充材料层307的材料成分均不相同,形成的离子掺杂区304中含有其中某一种掺杂离子(比如:硼离子),离子掺杂层304是位于牺牲层303中,从填充材料层307表面向下研磨,当研磨到离子掺杂层304时,研磨液中某种杂质离子(比如:硼离子)的浓度会从无到有,并逐渐增大,因此当检测到研磨液中杂质离子的浓度变化时,即可停止研磨的进行。在具体的实施例中,所述离子注入的能量和剂量根据不同的待注入杂质离子作出选择,使不同的杂质离子注入后形成的离子掺杂层304均能达到作为研磨停止层的效果,并且利于离子掺杂层304的深度控制,当注入的杂质离子为锗离子、硅离子或碳离子时,离子注入的能量为5~40Kev,剂量大于等于1E15/cm2,当注入的杂质离子为氧离子、氮离子、砷离子、硼离子或锑离子时,离子注入的能量为1~40Kev,剂量大于等于1E15/cm2。参考图10,采用化学机械研磨工艺平坦化所述填充材料层307(如图9所示)和牺牲层303,以离子掺杂层304作为停止层。当离子掺杂层304为非晶层,由于本实施例的牺牲层303表面会具有填充材料层307,因此对填充材料层307和牺牲层303堆叠结构进行研磨时,研磨速度首先保持一定的速度,当研磨到填充材料层307和牺牲层303交接处时,研磨速率会逐渐减小,当研磨到离子掺杂层304区时,研磨速率会逐渐增大并且变化速率的变化幅度较大,当研磨速率达到最大值后再逐渐减小时,停止研磨的进行。当所述离子掺杂层304为掺杂有杂质离子的多晶硅或无定形硅时,其研磨过程请参考第一实施例。在平坦化所述牺牲层303后,刻蚀剩余的牺牲层303,形成横跨所述鳍部顶部和侧壁表面的伪栅(图中未示出);还包括:形成覆盖所述鳍部301和伪栅的介质层(图中未示出);平坦化所述介质层,暴露出伪栅的顶部表面;去除所述伪栅,形成凹槽(图中未示出);在凹槽中填充满金属,形成金属栅极(图中未示出);在所述金属栅极两侧的鳍部内形成鳍式场效应管的源/漏区。综上,本发明实施例鳍式场效应管的形成方法,离子掺杂层是通过注入工艺形成的,注入工艺可以较为精确的控制在牺牲层中形成的离子掺杂层的位置,当以牺牲层中的离子掺杂层作为研磨的停止层时,若研磨牺牲层的过程中,即使研磨速率会发生变化,剩余的牺牲层的厚度也能较精确的控制,使得刻蚀剩余的牺牲层形成的伪栅的高度也比较精确。本发明虽然已以较佳实施例公开如上,但其并不是用来限定本发明,任何本领域技术人员在不脱离本发明的精神和范围内,都可以利用上述揭示的方法和技术内容对本发明技术方案做出可能的变动和修改,因此,凡是未脱离本发明技术方案的内容,依据本发明的技术实质对以上实施例所作的任何简单修改、等同变化及修饰,均属于本发明技术方案的保护范围。