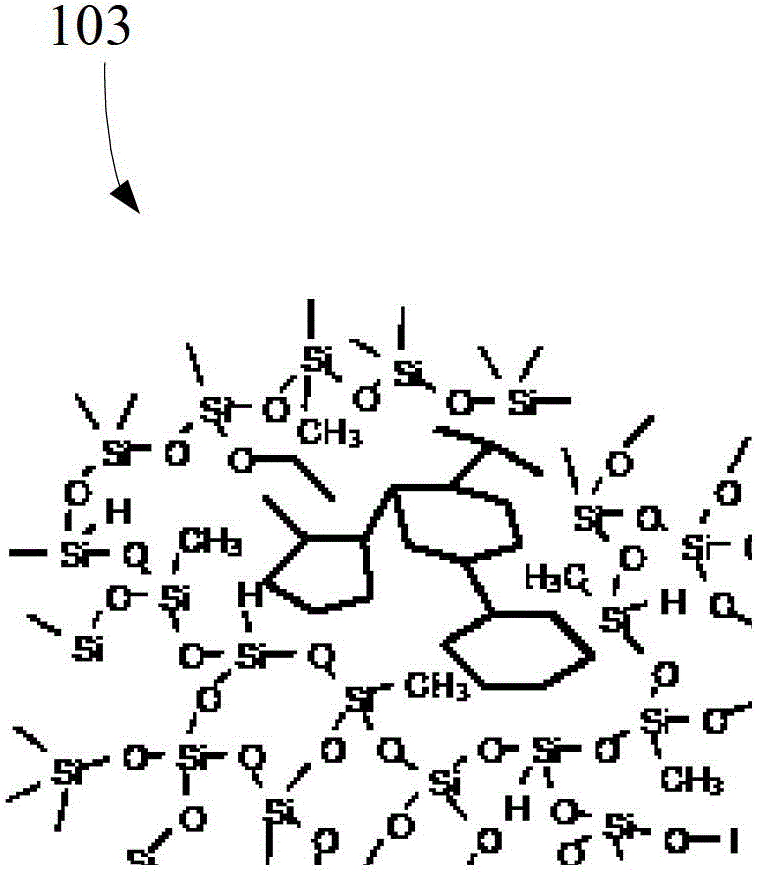
本发明涉及半导体制造领域,尤其涉及一种多孔低k介质层的形成方法及多孔低k介质层。
背景技术:在超大规模集成电路工艺中,有着热稳定性、抗湿性的二氧化硅一直是金属互连线路间使用的主要介质材料,金属铝则是芯片中电路互连线路的主要材料。然而,相对于元件的微型化及集成度的增加,电路中互连线路数目不断的增多,使得互连结构中的电阻(R)及电容(C)所产生的寄生效应,造成了严重的传输延迟(RCDelay)。因此,在降低导线电阻方面,由于金属铜具有高熔点,低电阻系数及高抗电子迁移的能力,已被广泛的应用在互连结构中来取代金属铝作为互连线路的材料。在降低寄生电容方面,采用低介电常数常数(lowk)的材料来降低寄生电容值。公开号为US7279427B2,公开日为2007年10月9日的美国专利文献中还能发现更多的采用低k介质层来制造互连结构的信息。现有技术中,多孔低k介质层的形成方法如下:参考图1,提供基底100,将基底100放入反应腔室(图未示)中,向反应腔室通入甲基二乙氧基硅烷(DEMS)101和松油烯(ATRP)102两种主反应气体,将反应腔室的温度设定在300℃,反应一段时间后,在基底表面形成介质层103,然后,结合图3和图4,对介质层103进行紫外线104处理,形成多孔低k介质层105。但是,利用现有技术形成多孔低k介质层的工艺复杂,生产效率低下。
技术实现要素:本发明解决的问题是利用现有技术形成多孔低k介质层的工艺复杂,生产效率低下。为解决上述问题,本发明提出了一种多孔低k介质层的形成方法,包括:提供基底,在所述基底上形成介质层,形成所述介质层的反应气体包括主反应气体,所述主反应气体的化学结构式包括环状基团、硅原子、碳原子和氢原子,所述环状基团包括碳原子和氢原子;利用紫外线对所述介质进行处理,形成多孔低k介质层。可选的,所述主反应气体的化学结构式还包括氧原子。可选的,所述环状基团包括碳碳双键或碳碳三键。可选的,所述环状基团还包括碳氧键。可选的,所述环状基团中碳原子与氧原子的个数总和为3~10。可选的,所述环状基团为环烷基。可选的,所述环烷基中碳原子的个数为3~10。可选的,所述主反应气体的化学结构式包括一个环状基团和一个硅原子。可选的,所述主反应气体为环丙基(三甲硅基)乙炔或/和1-乙氧基-1-三甲基硅基环丙烷。可选的,形成所述介质层的反应气体还包括辅反应气体,所述辅反应气体包括氦气。可选的,所述辅反应气体还包括氧气。可选的,在所述基底上形成介质层包括:在所述基底上形成介质层是在反应腔室中进行的,主反应气体的流量为0.05g/min~10g/min;氦气的流量为100sccm~5000sccm;氧气的流量为50sccm~1000sccm;反应腔室的温度为100℃~400℃,反应腔室的压力为0.1torr~10torr。可选的,所述利用紫外线对所述介质层进行处理包括:利用紫外线照射所述介质层,所述紫外线的波长范围为10nm~400nm,所述紫外线的照射的功率为50w~100w,照射时间为63s~77s。本发明还提供了一种由上述方法形成的多孔低k介质层。可选的,所述多孔低k介质层的平均孔径小于等于9A。与现有技术相比,本发明的技术方案具有以下优点:本发明中,形成介质层的反应气体包括主反应气体,该主反应气体的化学结构式中既包括后续形成多孔低k介质层的骨架结构的前驱体部分,又包括孔的前驱体部分。其中,主反应气体的化学结构式中的硅原子和碳原子是后续形成的多孔低k介质层骨架结构的必要组成部分。主反应气体的化学结构式中的环状基团为后续形成的多孔低k介质层中的孔做准备。本发明形成介质层的反应气体包括该主反应气体,在形成介质层的过程中不需要像现有技术那样调整不同主反应气体间的配比,更不用对不同主反应气体间的配比进行实时监测,因此本发明节省了工艺步骤,降低了工艺复杂度,提高了形成介质层的工艺效率。附图说明图1是现有技术中的形成介质层的剖面结构示意图;图2是现有技术中的部分介质层的分子结构示意图;图3和图4是现有技术中的形成多孔低k介质层的剖面结构示意图;图5是现有技术中的部分多孔低k介质层的分子结构示意图;图6是本发明的多孔低k介质层的形成方法的流程示意图;图7是本发明一实施例的形成介质层的剖面结构示意图;图8是本发明一实施例的采用1-乙氧基-1-三甲硅基环丙烷气体形成的部分介质层的分子结构示意图;图9和图10是本发明一实施例的形成多孔低k介质层的剖面结构示意图;图11是本发明一实施例的采用1-乙氧基-1-三甲硅基环丙烷气体形成的部分多孔低k介质层的分子结构示意图。具体实施方式发明人发现和分析,利用现有技术形成多孔低k介质层的工艺复杂,生产效率低下的原因为:现有技术中,参考图1,将基底100放入反应腔室(图未示)中,向反应腔室通入甲基二乙氧基硅烷(DEMS)101和松油烯(ATRP)102两种主反应气体,其中,甲基二乙氧基硅烷的化学结构式为:松油烯的化学结构式为:结合参考图2和图5,甲基二乙氧基硅烷101为后续形成的多孔低k介质层105骨架结构的前驱体(Structureformerprecursor),松油烯102为后续形成的多孔低k介质层105中的孔106的前驱体(Porogenprecursor),因此,松油烯是成孔剂。结合参考图3和图4,在反应腔室中通入两种主反应气体的过程中,甲基二乙氧基硅烷气体与松油烯气体会在基底表面发生聚合反应形成介质层103,该介质层103为无孔介质层。其中,甲基二乙氧基硅烷聚合形成介质层的骨架结构,松油烯聚合形成的聚合物经后续的紫外线照射会分解挥发,松油烯聚合形成的聚合物分解挥发后在介质层的内部形成孔106。因此,紫外线104对介质层103处理后,无孔介质层103变成多孔低k介质层105,再结合参考图2和图5,松油烯聚合物的位置就是多孔低k介质层105中孔106的位置。现有工艺中,向反应腔室中通入上述两种主反应气体形成多孔低k介质层105的工艺操作过程中,需要获取这两种主反应气体的反应配比值,如果甲基二乙氧基硅烷101在主反应气体中所占的比例太大时,松油烯102的比例相对会小,则后续形成的多孔低k介质层中的孔106会比较少,该多孔低k介质层的介电常数较大,仍然会造成较严重的传输延迟;如果甲基二乙氧基硅烷101在主反应气体中所占的比例太小时,松油烯102的比例相对会大,虽然后续形成的多孔低k介质层的介电常数比较小,但是,后续形成的多孔低k介质层中的孔会比较多,相应的,后续形成的多孔低k介质层的机械强度不符合要求。若想形成机械强度和介电常数都符合要求的多孔低k介质层时,需要在工艺开始之前摸索配比值,并且在工艺过程中严格控制这两种主反应气体的配比并进行实时监测,因此现有技术中形成多孔低k介质层的工艺复杂,从而造成生产效率低下。发明人还发现,参考图4和图5,采用现有技术的方法形成多孔低k介质层105中的孔106的平均孔径太大,并且孔106的分布不均匀,从而使得多孔低k介质层105的机械强度变小。发明人进一步分析现有技术的方法形成的多孔低k介质层105中的孔106的平均孔径太大,并且孔106的分布不均匀的原因如下:向反应腔室通入甲基二乙氧基硅烷101和松油烯102两种主反应气体时,松油烯分子除了与甲基二乙氧基硅烷分子容易发生聚合反应外,还很容易发生松油烯分子之间的相互聚合,这样一个甲基二乙氧基硅烷分子会同时与多个松油烯聚合,其中,与甲基二乙氧基硅烷分子发生聚合的松油烯分子有的是直接连接在甲基二乙氧基硅烷分子上,有的是连接在与甲基二乙氧基硅烷分子连接的松油烯分子上的,因此,参考图2和图5,形成的松油烯聚合物中的松油烯分子个数比较多,形成的松油烯聚合物的分子量和面积比较大,从而使得后续形成的多孔低k介质层105中的孔106的平均孔径D1会很大(至少大于15A)。另外,向反应腔室通入甲基二乙氧基硅烷和松油烯两种主反应气体时,除了发生松油烯分子与甲基二乙氧基硅烷分子的聚合反应、松油烯分子之间的相互聚合反应外,还会发生甲基二乙氧基硅烷分子之间的相互聚合反应,形成多孔低k介质层105的骨架部分。当松油烯分子与甲基二乙氧基硅烷分子发生聚合时,松油烯分子与甲基二乙氧基硅烷分子聚合时比较随机。具体为,松油烯分子和甲基二乙氧基硅烷单个分子发生聚合时形成的多孔低k介质层中的孔距会小;松油烯分子和甲基二乙氧基硅烷聚合物发生聚合时形成的多孔低k介质层中的孔距会大,因此,后续形成的多孔低k介质层中的孔距大小不等,后续形成的多孔低k介质层中的孔的分布不均匀。多孔低k介质层中的平均孔径太大、孔的分布不均匀都会使多孔低k介质层的机械强度变小。相应地,发明人提供了一种多孔低k介质层的形成方法,图6是本发明的多孔低k介质层的形成方法的流程示意图。图7是本发明一实施例的形成介质层的剖面结构示意图。图8是本发明一实施例的采用1-乙氧基-1-三甲硅基环丙烷气体形成的部分介质层的分子结构示意图。图9和图10是本发明一实施例的形成多孔低k介质层的剖面结构示意图。图11是本发明一实施例的采用1-乙氧基-1-三甲硅基环丙烷气体形成的部分多孔低k介质层的分子结构示意图。下面将图7至图11与图6结合起来对本发明多孔低k介质层的形成方法进行详细说明。首先参考图7和图8,执行图6中的步骤S11,提供基底200,在所述基底200上形成介质层202,形成所述介质层202的反应气体包括主反应气体201,所述主反应气体201的化学结构式包括环状基团、硅原子、碳原子和氢原子,所述环状基团包括碳原子和氢原子。本实施例中,所述基底200包括:形成有晶体管等半导体元件的衬底层(图未示),形成于衬底层上的互连结构,所述互连结构内具有金属互连线路(图未示),形成于金属互连线路上的阻挡层(图未示)。其中所述金属互连线路实现衬底层中的半导体元件与后续形成的其他半导体元件进行电性连接。此处所述阻挡层用于防止金属互连线路中的金属扩散。在其他实施例中,基底200也可以只是指形成有晶体管半导体元件的衬底层。具体地,金属互连线路的材料为铜或铝。所述阻挡层的材料为掺氮的碳化硅(NitrogenDopedSiliconCarbon,NDC),它能更好的防止金属互连线路中的金属扩散。但是本发明对金属互连线路和阻挡层的材料不作限制。参考图7,将基底200放入反应腔室(图未示)中,向反应腔室内通入主反应气体201,该主反应气体201的化学结构包括环状基团、硅原子、碳原子和氢原子,所述环状基团包括碳原子和氢原子。其中,主反应气体201分为后续形成多孔低k介质层的骨架结构的前驱体部分和孔的前驱体部分。主反应气体201的化学结构式中的硅原子和碳原子是后续形成的多孔低k介质层骨架结构的必要组成部分。主反应气体201的化学结构式中的环状基团为后续形成的多孔低k介质层中的孔做准备,原因如下:参考图7和图8,当向反应腔室通入主反应气体201后,基底200表面会形成介质层202,聚合的环状基团具有一定的三维空间结构。当后续用紫外线照射介质层202时,聚合的环状基团分解挥发,介质层202中原有的聚合的环状基团的位置处会形成孔。其中,主反应气体201的环状基团包括碳原子和氢原子,至少有三种情况:(1)主反应气体201的环状基团只包括碳原子和氢原子,为环烷基,例如,环丙烷基、环丁烷基、环戊烷基等。(2)主反应气体201的环状基团除了包括碳原子和氢原子这个必备的条件外,还可以包括碳碳双键或碳碳三键,例如,环戊烯基、环戊二烯基、环壬炔基等。(3)主反应气体的环状基团除了包括碳原子和氢原子这个必备的条件外,该环状基团还可以为环氧烷基,具体为,该环状基团除了具有碳原子和氢原子外,还可以具有氧原子,也就是说,所述环状基团还可以包括碳氧键,例如环氧丙烷基、环氧丁烷基等。向反应腔室中通入主反应气体201的同时,还可以向腔室中通入辅反应气体,辅反应气体可以包括氦气,或者,可以包括氦气和氧气。其中,氦气的作用为载气,具有运输主反应气体的作用。当主反应气体201的分子中的骨架前驱体部分不具有氧原子时,辅反应气体可以包括氦气,不包括氧气;辅反应气体也可以包括氦气和氧气,氧气的作用为和主反应气体一起参与形成介质层202。当主反应气体的分子中的骨架前躯体部分具有氧原子时,氧气可以增加后续形成的介质层202中氧原子的数量,从而增加后续形成的介质层202的机械强度。当然,主反应气体201的分子中骨架前驱体部分具有氧原子时,辅反应气体可以不包括氧气,也能实施本发明,只是形成的介质层的机械强度不如前者大。另外,如果向反应腔室中通入主反应气体的过程中不通入辅反应气体也能实施本发明,只是后续形成的多孔低k介质层的机械强度比通入辅反应气体的情况差些。当辅反应气体为氦气和氧气时,在基底200的表面形成介质层202的具体工艺为:主反应气体201的流量为0.05g/min~10g/min;氦气的流量为100sccm~5000sccm;氧气的流量为50sccm~1000sccm;反应腔室的温度为100℃~400℃,反应腔室的压力为0.1torr~10torr。本实施例中,主反应气体201的化学结构式中除了环状基团可以具有氧原子外,其骨架前驱体部分还可以包括氧原子。例如,本实施例的主反应气体201为1-乙氧基-1-三甲硅基环丙烷。它的化学结构式如下:当向反应腔室通入1-乙氧基-1-三甲硅基环丙烷气体时,形成的介质层202的部分结构请参考图8。1-乙氧基-1-三甲硅基环丙烷中的1-乙氧基-1-三甲硅基为骨架结构前驱体部分,1-乙氧基-1-三甲硅基相互聚合形成介质层202的骨架结构。1-乙氧基-1-三甲硅基环丙烷气体中的环丙烷基为孔的前驱体部分,环丙烷为后续形成多孔低k介质层的孔做准备。本实施例中,参考图8,两个1-乙氧基-1-三甲硅基环丙烷分子中的环丙烷基相互聚合形成环状聚合物,该环状聚合物经后续的紫外线照射后会分解挥发,参考图11,在介质层202的环状聚合物的位置形成孔205,在介质层202的内部形成孔205后,介质层202成为多孔低k介质层204。多孔低k介质层204中的孔205的孔径D2小于等于9A。向反应腔室通入1-乙氧基-1-三甲硅基环丙烷主反应气体,并且通入氦气和氧气辅反应气体,在基底上形成介质层202的工艺步骤具体为:1-乙氧基-1-三甲硅基环丙烷气体的流量为0.05g/min~10g/min;氦气的流量为100sccm~5000sccm;氧气的流量为50sccm~1000sccm;反应腔室的温度为100℃~400℃,反应腔室的压力为0.1torr~10torr。在其他实施例中,主反应气体的化学结构式中可以不包括氧原子。例如,主反应气体为环丙基(三甲硅基)乙炔。它的化学结构式如下:当向反应腔室通入环丙基(三甲硅基)乙炔气体时,环丙基(三甲硅基)乙炔中的(三甲硅基)乙炔基相互聚合形成介质层的骨架结构。环丙基(三甲硅基)乙炔气体中的环丙烷基为后续形成多孔低k介质层的孔做准备。本实施例中,两个环丙基(三甲硅基)乙炔分子中的环丙烷基相互聚合形成环状聚合物,该环状聚合物经后续的紫外线照射后会分解挥发,在介质层的环状聚合物的位置形成孔,在介质层成孔后,介质层成为多孔低k介质层。向反应腔室通入环丙基(三甲硅基)乙炔气体主反应气体,并且通入氦气和氧气辅反应气体,在基底上形成介质层的工艺步骤具体为:环丙基(三甲硅基)乙炔气体的流量为0.05g/min~10g/min;氦气的流量为100sccm~5000sccm;氧气的流量为50sccm~1000sccm;反应腔室的温度为100℃~400℃,反应腔室的压力为0.1torr~10torr。本发明中,主反应气体201的化学结构式中既包括后续形成多孔低k介质层的骨架结构的前驱体部分,又包括孔的前驱体部分。其中,主反应气体201的化学结构式中的硅原子和碳原子是后续形成的多孔低k介质层骨架结构的必要组成部分。主反应气体201的化学结构式中的环状基团为后续形成的多孔低k介质层中的孔做准备。一方面,在形成介质层的过程中不需要像现有技术那样调整不同主反应气体间的配比,更不用对不同主反应气体的配比进行实时监测,因此本实施例节省了工艺步骤,降低了工艺复杂度,提高了形成介质层202的工艺效率。另一方面,在形成介质层202的过程中只需要提供一种主反应气体的设备就可以,不需要像现有技术那样还需要提供其他种类的主反应气体的设备,因此,本实施例节省了工艺成本。接着,结合参考图9至图11,执行图5中的步骤S12,利用紫外线203对所述介质层202进行处理,形成多孔低k介质层204。其中,具体工艺为:参考图9,利用紫外线203照射所述介质层202,所述紫外线203的波长范围为10nm~400nm,所述紫外线203的照射的功率为50w~100w,照射时间为63s~77s。紫外线203产生的热量使得环状基团的聚合物分解并且挥发(参考图8和图9),使得在介质层202中的环状基团的聚合物位置处形成孔205(参考图10和图11),介质层202的介电常数也有所下降,从而使得介质层202形成多孔低k介质层204。参考图8,本实施例中,当主反应气体的分子式为1-乙氧基-1-三甲硅基环丙烷时,两个1-乙氧基-1-三甲硅基环丙烷分子中的环丙烷基相互聚合形成环状聚合物,参考图9,该环状聚合物经后续的紫外线203照射后分解挥发,结合参考图9至图11,在介质层202的环状聚合物的位置形成孔205,此时,介质层202变成多孔低k介质层204。本实施例中的主反应气体的化学结构式中包括一个硅原子和一个环状基团。向反应腔室中通入该主反应气体后,主要发生该主反应气体分子之间的聚合反应,硅原子与环状基团之间的聚合反应相对于现有技术的两种主反应气体来说,没有骨架前驱体之间的聚合反应和孔的前驱体之间的聚合反应,因此,主反应气体分子之间的聚合反应为有规律的聚合反应,即,基本上都是含硅原子的主链带有一个环状基团之间的聚合反应,而不会发生含硅原子主链之间的相互聚合反应和环状基团之间的相互聚合反应,因此后续形成的多孔低k介质层中的孔距大小基本相等,后续形成的多孔低k介质层中的孔的分布会比较均匀。孔的分布均匀的多孔低k介质层要比孔的分布不均匀的多孔低k介质层的机械强度高。后续形成的多孔低k介质层中的孔的平均孔径的大小也直接影响后续形成的多孔低k介质层的机械强度。当平均孔径越小,后续形成的多孔低k介质层的机械强度越强。因此为了形成平均孔径较小的孔,本实施例中的环状基团中碳原子数不能太多。当所述环状基团为环烷基时,该环烷基中碳原子的个数为3~10,即,该环烷基为环丙烷基~环辛烷基。如果环烷基中碳原子的个数大于10,则后续形成的多孔低k介质层中的孔的平均孔径会较大,例如,在本实施例中,多孔低k介质层204的平均孔径D2会大于9A,影响形成的多孔低k介质层的机械强度;环烷基中碳原子的总个数至少等于3,如果小于3,则形成不了环烷基,从而形成不了孔,进一步的,形成不了多孔低k介质层204。当所述环状基团为环氧烷基时,该环烷基中碳原子和氧原子的总个数为3~10。如果环氧烷基中碳原子与氧原子的总个数大于10,则后续形成的多孔低k介质层204中的孔205的平均孔径会较大,例如在本实施例中,多孔低k介质层的平均孔径也会大于9A;环氧烷基中碳原子的总个数至少等于3,如果小于3,则后续形成不了多孔低k介质层。本实施例中,环烷基较佳为环丙烷或环氧丙烷,因为环丙烷或环氧丙烷中的环状结构中的原子数最小,后续形成的环状结构的聚合物的分子量也会最小,在介质层中形成的孔的平均孔径会最小,从而使得后续形成的多孔低k介质层中机械强度较高。上述实施例中,向反应腔室通入的主反应气体201只有一种。在其他实施例中,主反应气体201也可以为两种或多种,也能实施本发明。但是这两种或多种主反应气体的化学结构式都包括环状基团、硅原子、碳原子和氢原子,所述环状基团包括碳原子和氢原子。例如,可以向反应腔室中同时通入1-乙氧基-1-三甲硅基环丙烷气体和环丙基(三甲硅基)乙炔气体,也能实施本发明。当主反应气体201为两种或多种时,也可以向反应腔室通入辅反应气体。该辅反应气体可以包括氦气,或者,也可以包括氦气和氧气。当辅反应气体为氧气和氦气时,具体工艺参数为:1-乙氧基-1-三甲硅基环丙烷气体和环丙基(三甲硅基)乙炔气体的总流量为0.05g/min~10g/min;氦气的流量为100sccm~5000sccm;氧气的流量为50sccm~1000sccm;反应腔室的温度为100℃~400℃,反应腔室的压力为0.1torr~10torr。当主反应气体201为两种或多种时,每一种主反应气体的化学结构式中既包括后续形成多孔低k介质层的骨架结构的前驱体部分,又包括孔的前驱体部分,同样可以节省工艺步骤,降低工艺复杂度,提高形成介质层202的工艺效率。需要说明的是,主反应气体是两种以上时,形成的多孔低k介质层的孔的分布不如主反应气体是一种时的均匀。本发明还提供一种多孔低k介质层,所述多孔低k介质层为上述方法形成的多孔低k介质层。所述多孔低k介质层的平均孔径小于等于9A。以上所述,仅是本发明的较佳实施例而已,并非对本发明作任何形式上的限制。任何熟悉本领域的技术人员,在不脱离本发明技术方案范围情况下,都可利用上述揭示的技术内容对本发明技术方案作出许多可能的变动和修饰,或修改为等同变化的等效实施例。因此,凡是未脱离本发明技术方案的内容,依据本发明的技术实质对以上实施例所做的任何简单修改、等同变化及修饰,均仍属于本发明技术方案保护的范围内。