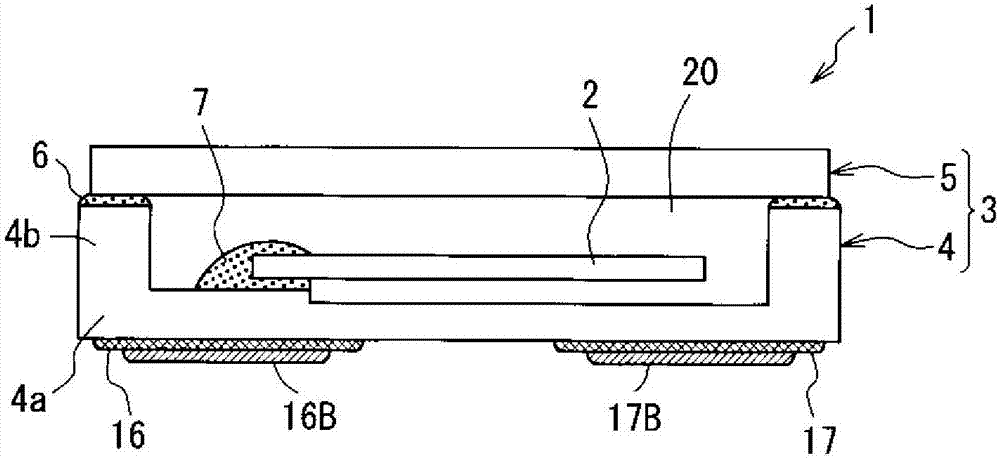
本发明涉及一种表面安装型电子部件用封装件及具备该电子部件用封装件的压电器件。
背景技术:
:表面安装型电子部件用封装件用于电子设备等,具体而言,用于石英振子或石英过滤器、石英振荡器等表面安装型压电器件。在压电器件中,在压电振动片的表面形成有金属薄膜电极,并且为了隔绝外部空气以保护该金属薄膜电极,压电振动片被电子部件用封装件气密密封。从容易加工和成本优势角度来看,在供压电器件安装的电路基板中,广泛使用使环氧树脂材料浸渍在网眼状的玻璃纤维中的、所谓玻璃环氧基板。另外,在该电路基板的电极图案上部,通过丝网印刷等方法涂布有焊料膏。并且,搭载成使上述压电器件的封装件的端子电极与该电路基板的电极图案重叠的状态,并利用熔化炉(加热炉等)使焊料膏熔化而将压电器件焊接接合在电路基板上。但是,由于封装件与电路基板的热膨胀系数之差,对接合这些封装件和电路基板的焊料产生应力,并且有时产生裂纹。特别是,对于使用氧化铝等陶瓷材料来作为封装件,并使用玻璃环氧基板来作为电路基板的组合来说,进一步面向高温环境下使用该封装件和电路基板的车载用等耐热用途的情况下,相对于封装件的热膨胀系数,电路基板的热膨胀系数较大,焊料易于产生疲劳破坏。如此,在通常温度环境下没有多大问题的焊料裂纹在高温环境下显著出现,进而在对该封装件和电路基板施加冲击的情况下,存在从焊料裂纹部分起产生剥离的问题。本申请人已提出了用于解决上述问题的技术(例如,参照专利文件1)。专利文件1:特开2006-32645号公报但是,在上述专利文件1中,相对于封装件底面的面积,将封装件的端子电极的面积规定为特定比例,由此促进焊料的角焊缝的形成,并提高与电路基板的接合强度。因此,由于相对于封装件的底面的面积,封装件的端子电极的面积被限制为特定比例,从而当实现封装件的小型化时,存在不得不缩小端子电极的面积,并且与电路基板的接合面积变小的问题。技术实现要素:本发明是为了解决上述问题而提出的,目的在于在相对于封装件的底面的面积,封装件的端子电极的面积未被规定为特定比例的情况下,抑制焊料裂纹并提高电子部件用封装件与电路基板的接合可靠性。本发明人为了达到上述目的,进行了深入研究,其结果,着眼于保持电子部件元件的基座的底面的端子电极的、与所述基座的底面的角部相对的倒角部,发现了可通过将该倒角部的倒角角度设在特定角度范围内,来有效地抑制焊料裂纹,并完成了本发明。即,本发明的电子部件用封装件至少具有用于保持电子部件元件的基座,基座底面具有被电连接到外部电路基板的端子电极,所述端子电极具有与所述基座底面的角部相对的倒角部,所述倒角部和基准线所成的倒角角度在±10°以内,所述基准线为与直线垂直且通过所述倒角部的垂线,其中,所述直线连结所述基座底面的所述角部和所述端子电极的、与所述基座底面的中心点接近的一侧的一边中央部。本发明的电子部件用封装件至少具有基座即可,可不具有盖。在本发明中,用于将电子部件用封装件电连接到外部电路基板的基座底面的端子电极具有与基座底面的角部相对的倒角部,将所述倒角部和基准线所成的倒角角度设为±10°以内。由此,当接合所述电路基板和所述端子电极的焊料等导电性接合材料的裂纹从基座底面的外周角部附近的受到最大应力的部位起产生,并向基座底面的中心部的应力最小的最小应力部位发展和行进时,能够通过形成于其中途的端子电极的倒角部,来有效地分散应力,并且能够使裂纹的行进方向弯曲,从而能够有效地抑制裂纹的发展和行进。在本发明优选的实施方式中,在所述端子电极上层压并一体形成有由金属膜构造的凸起,所述凸起具有与所述基座底面的角部相对的倒角部,所述凸起的倒角部和凸起用基准线所成的倒角角度在±10°以内,所述凸起用基准线为与直线垂直且通过所述凸起的倒角部的垂线,其中,所述直线连结所述基座底面的所述角部和所述端子电极的、与所述基座底面的中心点接近的一侧的一边中央部。在该实施方式中,在端子电极上层压形成有凸起,所述凸起具有与基座底面的角部相对的倒角部,并将所述倒角部和凸起用基准线所成的倒角角度设在±10°以内。由此,当接合电路基板和端子电极的焊料等导电性接合材料中所产生的裂纹从基座底面的外周角部附近的最大应力部位起向基座底面的中心部的最小应力部位发展和行进时,也能通过端子电极上的凸起的倒角部与端子电极的倒角部相结合,来有效地分散应力,并且能够使裂纹的行进方向弯曲,从而能够更有效地抑制裂纹的发展和行进。在本发明的其它实施方式中,所述端子电极的所述倒角部和所述凸起的所述倒角部为平面状的倒角部,所述端子电极的所述倒角部的所述倒角角度和所述凸起的所述倒角部的所述倒角角度相等。根据该实施方式,由于将端子电极的倒角部的倒角角度和凸起的倒角部的倒角角度设为相等,因此能够更有效地抑制裂纹的发展和行进。在本发明的其它实施方式中,所述倒角角度在±5°以内。根据该实施方式,能够更有效地抑制裂纹的发展和行进。在本发明的又一实施方式中,所述端子电极分别具有与所述基座底面的一边两端的各角部分别相对的各倒角部,在与所述基座底面的所述一边对应的所述基座的侧面形成有沿上下延伸的堞形结构,在所述堞形结构中形成有与所述端子电极相连的侧面电极,所述堞形结构以其开口宽度控制在沿所述端子电极的所述各倒角部的各倒角方向的各延长线与所述基座底面的所述一边分别交叉的两交点之间的方式形成。在该实施方式中,被形成在与基座底面的一边对应的基座侧面的堞形结构以其开口宽度控制在沿所述各倒角部的倒角方向的各延长线与基座底面的所述一边分别交叉的两交点之间的方式形成。由此,能够避免如下的情况:由于开口宽度较大的堞形结构达到端子电极的倒角部而该倒角部无法有效地分散应力,因此应力集中而无法有效地抑制裂纹的发展和行进。另外,由于在所述堞形结构中形成有与所述端子电极相连的侧面电极,因此通过焊料等导电性接合材料将端子电极连接到电路基板时,焊料的一部分爬到堞形结构的侧面电极并形成角焊缝,从而能够提高接合强度,并且容易进行角焊缝形状的光学检查等。在本发明的其它实施方式中,所述基座底面俯视呈矩形,并具备一对彼此相对的所述基座底面的所述一边,沿所述基座底面的一对所述一边,配置有一对所述端子电极,在与所述基座底面的一对所述一边分别对应的所述基座的两侧面分别形成有沿上下延伸的所述堞形结构,在各个所述堞形结构中分别形成有与各个所述端子电极分别相连的所述侧面电极。根据该实施方式,通过形成一对与俯视呈矩形的所述基座底面上的相对的各一边分别对应,并且分别具有与所述各一边的两端的各角部相对的各倒角部的端子电极,从而能够抑制从俯视呈矩形的基座底面的四个角部的最大应力部位起向基座底面的中心部的最小应力部位发展和行进的裂纹。在本发明的优选的实施方式中,具备用于气密密封所述基座的上部开口的盖,所述基座为在上下方向上层压有多个层的层压构造,所述堞形结构在所述基座的所述多个层中的至少最上层上的开口尺寸小于剩余层上的开口尺寸。根据该实施方式,当利用盖密封作为最上层的基座上部时,可通过扩大密封面积来提高密封强度,另一方面,可在作为剩余层的基座下部的侧面形成与侧面电极相连的开口尺寸较大的堞形结构,从而能够切实且牢固地进行采用焊料等导电性接合材料的电连接。本发明的压电器件具备:本发明的电子部件用封装件或上述各实施方式的电子部件用封装件;和作为所述电子部件元件的压电振动元件。根据本发明,能够提高压电器件的封装件与电路基板的接合可靠性。根据本发明,当接合电路基板和所述端子电极的焊料等导电性接合材料的裂纹从基座底面的外周角部附近的最大应力部位起向基座底面的中心部的最小应力部位发展和行进时,能够通过具有与基座底面的角部相对的特定倒角角度的倒角部来有效地分散应力,并且能够使裂纹的行进方向弯曲。由此,能有效地抑制裂纹的发展和行进,并能够提高电子部件用封装件与电路基板的接合可靠性。附图说明图1是作为本发明一实施方式的压电器件的石英振子的剖视图。图2是图1的石英振子的仰视图。图3是从图1的石英振子的底面侧观察的立体图。图4是用于说明与应力分布有关的焊料裂纹的行进和发展方向的图。图5是用于说明倒角部的倒角角度的仰视图。图6是表示用模拟评价的各倒角角度的图。图7是表示模拟模型整体的立体图。图8是表示用于模拟的1/4模拟模型的立体图。图9是焊料部分的最大主应变的等高线图(contourmap)。图10是沿X坐标方向的主应变的等高线图。图11是沿Y坐标方向的主应变的等高线图。图12是表示在每个倒角角度θ下的沿X坐标方向的主应变的变化的图。图13是表示在每个倒角角度θ下的沿Y坐标方向的主应变的变化的图。图14是表示在每个倒角角度θ下的A点附近和B点附近的主应变的平均值的图。图15是对图14的A点附近的主应变平均值和B点附近的主应变平均值中的、较大的主应变的平均值进行绘制的图。图16是表示用模拟评价的其它倒角部的图。图17是用于说明堞形结构的开口宽度的基座的仰视图。图18是表示用模拟评价的开口宽度不同的堞形结构的图。图19是图18的开口宽度不同的堞形结构的焊料部分的最大主应变的等高线图(contourmap)。图20是图18的开口宽度不同的堞形结构的焊料部分的沿Y坐标方向的主应变的等高线图。图21是表示图20的AB之间的主应变的变化。图22是从本发明的其它实施方式的石英振子的底面侧观察的立体图。具体实施方式下面,基于附图对本发明的实施方式进行详细说明。在本实施方式中,作为表面安装型压电器件,应用石英振子来进行说明。图1是表示本发明一实施方式的石英振子的剖视图,图2是其仰视图,图3是从底面侧观察的立体图。如图1所示,该实施方式的石英振子1具备:作为电子部件元件的晶振片2,其由AT切割石英形成;和封装件3,用于保持该晶振片2,并对晶振片2进行气密密封。封装件3具备:基座4,具有上部开口的凹部,并收纳保持晶振片2;和盖5,对保持于基座4的晶振片2进行气密密封。盖5通过密封材料6而被接合在基座4的开口部,从而形成被气密密封的内部空间20。在该内部空间20中,通过使用导电性粘接剂7等而晶振片2被机电接合在基座4的电极焊盘(未图示)上。基座4由氧化铝等陶瓷材料形成,并且如图1所示,被成型为由底部4a和沿底部4a的外周向上方延伸的堤部4b形成的箱状。该基座4通过层压多层陶瓷后一体烧成为上部开口的凹状而成。另外,如图2和图3所示,在俯视呈矩形的基座4外周的四个角部,形成有从基座4的底面至上表面向内方凹陷的堞形结构8~11。另外,在所述堞形结构8与所述堞形结构11之间的基座4的侧面以及所述堞形结构9与所述堞形结构10之间的基座4的侧面,形成有向内方凹陷且沿上下方向延伸的堞形结构12、13。该堞形结构12、13被形成在俯视呈大致矩形的基座4上的彼此相对的短边的中央部分。如图3所示,在沿上下延伸的堞形结构12、13的下部即靠近基座4的底面的部分,分别形成有侧面电极14、15(未图示侧面电极15)。该侧面电极14、15被分别电连接到形成于基座4的底面的一对端子电极16、17,该端子电极16、17通过使用作为导电性接合材料的例如焊料而被连接到外部电路基板。此时,可通过焊料爬到形成有侧面电极14、15的堞形结构12、13来确认连接状态。基座4的底面的各端子电极16、17为沿一对相对的各短边以彼此相对的方式对称形成的、所谓相对的两端子。一侧端子电极16具有与一侧短边的两侧的两个角部相对的两个倒角部161、162,另一侧端子电极17具有与另一侧短边的两侧的两个角部相对的两个倒角部171、172。各倒角部161、162、171、172为用倾斜面对各端子电极16、17的角部进行倒角的平面状的倒角部161、162、171、172。除与上述侧面电极14、15相连的堞形结构部分和所述倒角部161、162、171、172以外,各端子电极16、17俯视呈矩形。各端子电极16、17的矩形的各短边与同样俯视呈矩形的基座4的底面的长边相对,各端子电极16、17的矩形的各长边与基座4的底面的短边相对。在各端子电极16、17上分别形成有与各端子电极16、17的平面面积相比稍小的大致相同形状即俯视呈相似形状的凸起16B、17B。与各端子电极16、17相同,在各凸起16B、17B中,分别形成有与基座4的矩形底面的四个角部分别相对的倒角部161B、162B、171B、172B。与端子电极16、17的各倒角部161、162、171、172相同,凸起16B、17B的各倒角部161B、162B、171B、172B为平面状。这些凸起16B、17B通过在端子电极16、17的金属镀膜上部以几乎相同的形状层压相同材质的金属镀膜(钨、钼等)而被一体形成。另外,这些端子电极16、17和凸起16B、17B以如下方式形成:将这些金属镀膜材料与基座4一体烧成,并在该金属镀膜上部形成镀镍层,从而在其上部形成镀金层。各端子电极16、17经由形成于堞形结构12、13的侧面电极14、15被电连接到基座4的图1所示的内部空间20的上述电极焊盘(未图示)上。对于该电极焊盘,晶振片2的引出电极(未图示)例如被导电性粘接剂7导电接合,并且晶振片2被保持于基座4。在该晶振片2的正面和背面形成有未图示的一对激励电极和上述引出电极。用于对基座4进行气密密封的盖5由板状的氧化铝等陶瓷材料形成,并且使用玻璃等密封材料6来密封。与基座4相同,盖5俯视呈矩形,但为稍小的形状。在具有上述结构的基座4的内部空间20中收纳保持晶振片2,并用盖5密封晶振片2,并且通过由加热炉进行的熔融接合等方法进行晶振片2的气密密封,从而完成使用石英振子即电子部件用封装件的压电器件。作为成品的石英振子经由焊料等导电性接合材料被接合在例如由玻璃环氧材料形成的电路基板的电极图案的上部。在该实施方式中,为了抑制焊料裂纹的发展和行进并提高电子部件用封装件与电路基板的搭载接合的可靠性,采取如下措施。在因电子部件用封装件与电路基板的热膨胀系数之差而对作为用于接合封装件与电路基板的导电性接合材料的焊料产生应力的情况下,如图4所示,从作为与基座4的底面的外周角部接近的区域的最大应力部位Smax起产生焊料裂纹的情况较多,通过继续受到由相同的应力引起的影响而产生的焊料裂纹向基座4的底面的中心部的最小应力部位Smin发展和行进。并且,最终焊料裂纹行进到端子电极16、17整体,从而导致由焊料进行的封装件与电路基板的接合被剥离。为了抑制该裂纹的发展和行进,本发明人进行了深入研究,其结果着眼于以与基座4的角部相对的方式形成的端子电极16、17的倒角部161、162、171、172,发现了将这些倒角部161、162、171、172的倒角角度设在特定角度范围内是有效的。在该实施方式中,在俯视形状与端子电极16、17大致相似的凸起16B、17B中也同样形成有倒角部161B、162B、171B、172B。为了在抑制焊料裂纹的基础上,形成有效的倒角部,本发明人进行作为使用了有限元法的结构解析的、焊料裂纹模拟,来验证由背面的端子电极16、17的形状不同引起的焊料应变差,并求出倒角部的优选形状。图5是用于说明焊料裂纹模拟的基座4的仰视图,在该图5中,通过代表性地表示一侧端子电极16的凸起16B的一个倒角部161B来进行说明。在该焊料裂纹模拟中,通过变更凸起16B的倒角部161B的倒角角度θ来实施。该凸起16B的倒角部161B的倒角角度θ以如下方式规定。即,将与直线L1垂直且通过凸起16B的倒角部161B的垂线设为凸起用基准线L2,其中,该直线L1连结端子电极16的内侧端部的中心O1和基座4的底面的角部顶点V1。端子电极16的内侧端部的中心O1为俯视呈大致矩形的端子电极16的相对的长边中的、与基座4的底面的中心O接近的一侧的长边的中央点。将该凸起用基准线L2和沿对凸起16B的倒角部161B进行倒角后的平面的直线L3所成的角度θ设为凸起16B的倒角部161B的倒角角度。此外,图5是用于说明倒角角度θ的图,图5的凸起16B的倒角部161B的实际倒角角度θ为θ=0°,即沿进行倒角后的平面的所述直线L3与所述凸起用基准线L2一致,但为了明确表示倒角角度θ,特意将直线L3作为相对于进行倒角后的平面倾斜的直线来表示。在焊料裂纹模拟中,变更了凸起16B的倒角部161B的倒角角度θ,并且与凸起16B的倒角部161B相同地,对端子电极16的倒角部161也变更了倒角角度θ。关于端子电极16的倒角部161的倒角角度θ,将与直线L1垂直且通过端子电极的倒角部161的垂线设为基准线L8,其中,该直线L1连结端子电极16的内侧端部的中心O1和基座4的底面的角部顶点V1,将该基准线L8和沿对端子电极的倒角部161进行倒角后的平面的直线所成的角度θ设为端子电极的倒角部161的倒角角度。基准线L8和基准线L2均为与直线L1垂直且彼此平行并分别通过端子电极16的倒角部161和凸起16B的倒角部161B的垂线,其中,该基准线L8规定端子电极的倒角部161的倒角角度θ,该基准线L2规定凸起16B的倒角部161B的倒角角度θ,该直线L1连结端子电极16的内侧端部的中心O1和基座4的底面的角部顶点V1。各垂线L2、L8通过所述直线L1与沿对各倒角部161、161B进行倒角后的平面的各直线的交点。如图5所示,在本实施方式中,对端子电极16的倒角部161和凸起16B的倒角部161B,以进行倒角后的平面平行的方式变更倒角角度θ。因此,端子电极16的倒角部161和凸起16B的倒角部161B的倒角角度θ彼此相等。具体而言,如图6的(a)~(f)所示,对于该焊料裂纹模拟中的倒角角度θ的变更来说,将端子电极16的倒角部161和凸起16B的倒角部161B的上述倒角角度θ沿顺时针方向和逆时针方向分别变更5°,直至最大15°为止,并实施了模拟。图7中示出用于模拟的模型整体。该模拟模型为通过使用焊料18而电子部件用封装件被安装在玻璃环氧基板19上的模拟模型,其中,该电子部件用封装件在由陶瓷形成的基座4上接合有由陶瓷形成的盖5。关于该模拟模型的尺寸,基座4的底面尺寸为3.2mm×2.5mm,端子电极16、17的尺寸为1.2mm×2.3mm,玻璃环氧基板19的尺寸为6.0mm×5.0mm×1.6mm。在使用有限元法的结构计算中,使用了图7所示的模拟模型整体的1/4即用图7的虚线表示那样包含一个角部的1/4对称部分。在图7的例中,一个角部与上述图2的形成有堞形结构11的角部对应。对模型整体均匀地施加+100℃的载荷,在以+25℃为基准的情况下,计算+125℃时的条件。即,在该裂纹模拟中,关于热载荷条件,将室温(25℃)作为应力出发点(无应力),施加热载荷直至125℃为止,并实施了线性解析。关于作为1/4模拟模型的放大图的图8所示的各结构材料,即作为端子电极16的钨(W)、作为基座4和盖5的陶瓷(Ceramics)、作为密封材料6的密封玻璃(FlintGlass,火石玻璃)、作为导电性粘接剂的焊料(solder)18和作为玻璃环氧基板19的FR-4的物理参数,使用了下述表1的值。[表1]杨氏模量[GPa]浦松氏比线膨胀率[ppm]钨4070.174.5陶瓷3160.247.2火石玻璃80.10.278.5焊料38.50.3821.7FR-4270.1514下面,对模拟结果进行说明。由于在施加到焊料部的应变变化时焊料裂纹受到较大的影响,因此注意了焊料的最大主应变。最大主应变为通过对在膨胀方向上最大的张量的六个分量坐标进行旋转而合成的值。图9是焊料部分的最大主应变的等高线图(contourmap)。该图9仅示出上述图7、8的1/4模拟模型的焊料部分,该焊料部分具有与端子电极16和凸起16B分别对应的形状部分16’、16B’,并且与堞形结构12的部分对应地焊料角焊缝12’向上方延伸。可知在焊料的与端子电极16的倒角部162对应的周边部分162’产生较大的主应变。以如下方式对如上述那样变更倒角角度θ时的主应变进行了评价。即,如图10所示,将焊料的所述短边方向的角部A点设为基准X坐标“0”,并如线条L4所示,按上述的每个倒角角度θ,对包含A点的其两侧的多个点计算出沿作为端子电极16的短边方向的X坐标方向的主应变。同样,如图11所示,将焊料的所述长边方向的角部B点设为基准Y坐标“0”,并如线条L5所示,按上述的每个倒角角度θ,对包含B点的其两侧的多个点计算沿作为端子电极16的长边方向的Y坐标方向的主应变。图12中示出倒角角度θ=0°(基准)、+10°、+15°、-10°、-15°的各情况下的、沿X坐标方向的主应变变化。在该图12中,横轴(X坐标)表示以图10的A点为基准X坐标“0”且沿线条L4的位置,纵轴表示沿X坐标方向的主应变。另外,图13中示出倒角角度θ=0(基准)、+10°、+15°、-10°、-15°的各情况下的、沿Y坐标方向的主应变变化。在该图13中,横轴(X坐标)表示以图11的B点为基准Y坐标“0”且沿线条L5的位置,纵轴表示沿Y坐标方向的主应变。如图12所示,沿X坐标方向的主应变在作为基准X坐标的A点附近比较大,并且,如图13所示,沿Y坐标方向的主应变在作为基准Y坐标的B点附近比较大。因此,按上述的每个倒角角度θ,分别计算出基准A点和B点附近即-0.05~+0.05的范围内的沿X坐标方向和Y坐标方向的主应变的各平均值。图14中示出在各倒角角度θ=-15°、-10°、-5°、0°、5°、10°、15°下的角部A点附近的沿X坐标方向的主应变的平均值和角部B点附近的沿Y坐标方向的主应变的平均值。在该图14的各倒角角度θ中,抽取沿角部A点附近的X坐标方向的主应变的平均值和沿角部B点附近的Y坐标方向的主应变的平均值中的、主应变较大的倒角角度来绘制的图为图15。如图15所示,可知随着靠近倒角角度θ=0°而主应变的平均值减小。为了缩小主应变并抑制焊料裂纹,倒角角度θ优选为±10°以内,更优选地,倒角角度θ为±5°以内。此外,对于作为以与基座4的角部相对的方式形成的端子电极16、17和凸起16B、17B的倒角部,除如上所述的平面状的倒角部以外的、如图16的(a)、(b)所示那样向外方膨胀的倒圆面(R形状)的倒角部161-R、161B-R或向内方凹陷的内倒圆面(倒R形状)的倒角部161-R’、161B-R’也进行了模拟,并确认出与上述平面状的倒角部相比,主应变均变大。如此,在本实施方式中,将基座4的底面的端子电极16、17和凸起16B、17B的倒角部161~164、171~174、161B~164B的倒角角度设为±10°以内,优选将该倒角角度设为±5°以内。由此,当用于接合电路基板和端子电极16、17的焊料等导电性接合材料的裂纹从基座底面的外周角部的最大应力部位起产生,并向基座底面的中心部的最小应力部位发展和行进时,能通过所述倒角部161~164、171~174、161B~164B有效地分散应力,并且能够使裂纹的行进方向弯曲,从而抑制裂纹的发展和行进。以上,对基座4的底面的端子电极16、17和凸起16B、17B的倒角部161、162、171、172、161B、162B、171B、172B的倒角角度θ进行了说明,但在本实施方式中,进一步以如下方式规定形成于基座4的侧面的堞形结构12、13的开口尺寸,由此更有效地抑制焊料裂纹。图17是用于说明形成于基座4的两侧面的堞形结构12、13的尺寸的基座4的仰视图。在此,应用一侧堞形结构12来进行说明,但另一侧堞形结构13也相同。在该实施方式中,在将延长线L6、L7与所述短边分别交叉的各交点设为C1、C2时,形成于所述短边的中央部分的堞形结构12的开口宽度W、即基座4的侧面中的堞形结构12的宽度W控制在两交点C1、C2之间内,其中,该延长线L6、L7为沿与基座4的底面的一个短边的两端角部分别相对的端子电极16的倒角部161、162的倒角方向的直线。上述延长线L6、L7为沿对倒角部161、162进行倒角后的各平面的直线。如此,通过以将宽度W控制在沿端子电极16的倒角部161、162的倒角平面的延长线L5、L6与所述短边的两交点C1、C2之间的方式形成堞形结构12,从而如以下说明那样,能够更有效地抑制焊料裂纹。即,如图18的(a)~(c)所示,本发明人对具有将堞形结构12的开口宽度W设为不同的W1、W2、W3的三种堞形结构12a~12c的模拟模型,进行了与上述相同的焊料裂纹模拟。此外,倒角部161、162、161B、162B的倒角角度θ均设为基准“0°”。关于开口宽度W1、W2、W3,开口宽度W1较小(小),开口宽度W2为中等程度(中),开口宽度W3较大(大)。对于图18的(a)、(b)所示的开口宽度W1、W2的堞形结构12a、12b来说,其开口宽度W1、W2均位于上述的两交点C1、C2之间,但对于图18的(c)所示的开口宽度W3的堞形结构12c来说,其开口宽度W3大于上述的两交点C1、C2之间。图19中示出针对各开口宽度W1、W2、W3的堞形结构12a~12c的模拟结果。图19的(a)~(c)是针对具有图18的(a)~(c)所示的三种堞形结构12a~12c的模拟模型的焊料部分的最大主应变的等高线图(contourmap)。如图19的(c)的圆形框所示,由于堞形结构12c的开口宽度较大,因此沿端子电极16的倒角角度θ的倒角部较小,无法充分地分散应力,从而主应变较大。图20是沿作为端子电极16的长边方向的Y坐标方向的焊料的主应变的等高线图,将端子电极16的短边方向(X坐标方向)的角部设为A点,将所述长边方向(Y坐标方向)的角部设为B点。当对该AB之间的主应变的值进行绘制时,如图21所示。如图21所示,可知与开口宽度W1、W2位于两交点C1、C2之间的堞形结构12a、b相比,开口宽度W3大于上述的两交点C1、C2之间的堞形结构12c的主应变随着从AB之间的中间点接近B点而大幅变大。如上述图17所示,在本实施方式中,由于以将堞形结构12、13的开口宽度W分别控制在沿端子电极16、17的倒角部161、162、171、172的倒角方向的延长线与基座4的底面的短边分别交叉的两交点之间内的方式形成基座4的两侧面的堞形结构12、13,因此端子电极16、17的倒角部161、162、171、172不会阻碍抑制裂纹的发展和行进,可形成堞形结构12、13。另外,也不会对与端子电极16、17的倒角部161、162、171、172一同抑制裂纹的发展和行进的凸起16B、17B的各倒角部161B、162B、171B、172B带来不良影响。另一方面,由于以开口宽度控制在所述两交点之间内的方式形成的基座4的侧面的堞形结构12、13形成有与端子电极16、17相连的侧面电极14、15,因此在通过焊料等导电性接合材料将端子电极16、17连接到电路基板时,由于焊料的一部分爬到堞形结构12、13的侧面电极14、15并形成角焊缝,因此能够提高接合强度,并且容易进行角焊缝形状的光学检查等。在上述实施方式中,虽然形成于基座4的侧面的堞形结构12、13的开口尺寸在上下方向上相同,但作为本发明的其它实施方式,也可以使堞形结构12、13的开口尺寸在上下方向上不同。图22的(a)、(b)是将堞形结构12、13的上部开口尺寸设为与下部开口尺寸相比较小的实施方式的基座底面的立体图及堞形结构12的局部放大图。此外,在图22中,仅示出一侧堞形结构12,但另一侧堞形结构13也相同。如图22的(b)所示,关于堞形结构12,与形成有侧面电极14的下部121相比,上部122的开口尺寸较小。在该实施方式中,堞形结构12的上部122与下部121相比,堞形结构12的上部122的开口宽度和开口深度均小。此外,也可以仅使开口宽度或开口深度中的任一个减小。如上述,基座4通过层压多层陶瓷层而构造,堞形结构12的开口尺寸较小的上部122至少包括所述多层的最上层,下部121为剩余的层。如图1所示,因在基座4的上部接合有盖5而被气密密封,但在该实施方式中,由于形成于基座4的侧面的堞形结构12、13的上部的开口尺寸较小,因此相应地密封面积较大,从而能够提高密封强度。另一方面,由于对形成于基座4的侧面的堞形结构12、13的下部、即形成有侧面电极14、15的部分来说,堞形结构12、13的开口尺寸较大,因此能够切实且牢固地进行采用作为导电性接合材料的焊料的电连接。在上述实施方式中,虽然端子电极16、17的倒角部161~164、171~174的倒角角度θ和凸起16B、17B的倒角部161B、162B、171B、172B的倒角角度θ彼此相等,但也可以使倒角角度θ彼此不同。另外,也可以省略端子电极16、17上的凸起16B、17B。在上述实施方式中,虽然应用石英振子来进行了说明,但本发明并不限于石英振子,例如还可以应用石英过滤器或石英振荡器等其它表面安装型电子部件。在上述实施方式中,虽然封装件3具备盖5,但在本发明中,也可以省略盖5。附图标记说明1石英振子2晶振片3封装件4基座5盖8~11堞形结构12、13堞形结构16、17端子电极161~164倒角部171~174倒角部16B、17B凸起161B~164B倒角部171B~174B倒角部18焊料19玻璃环氧基板当前第1页1 2 3