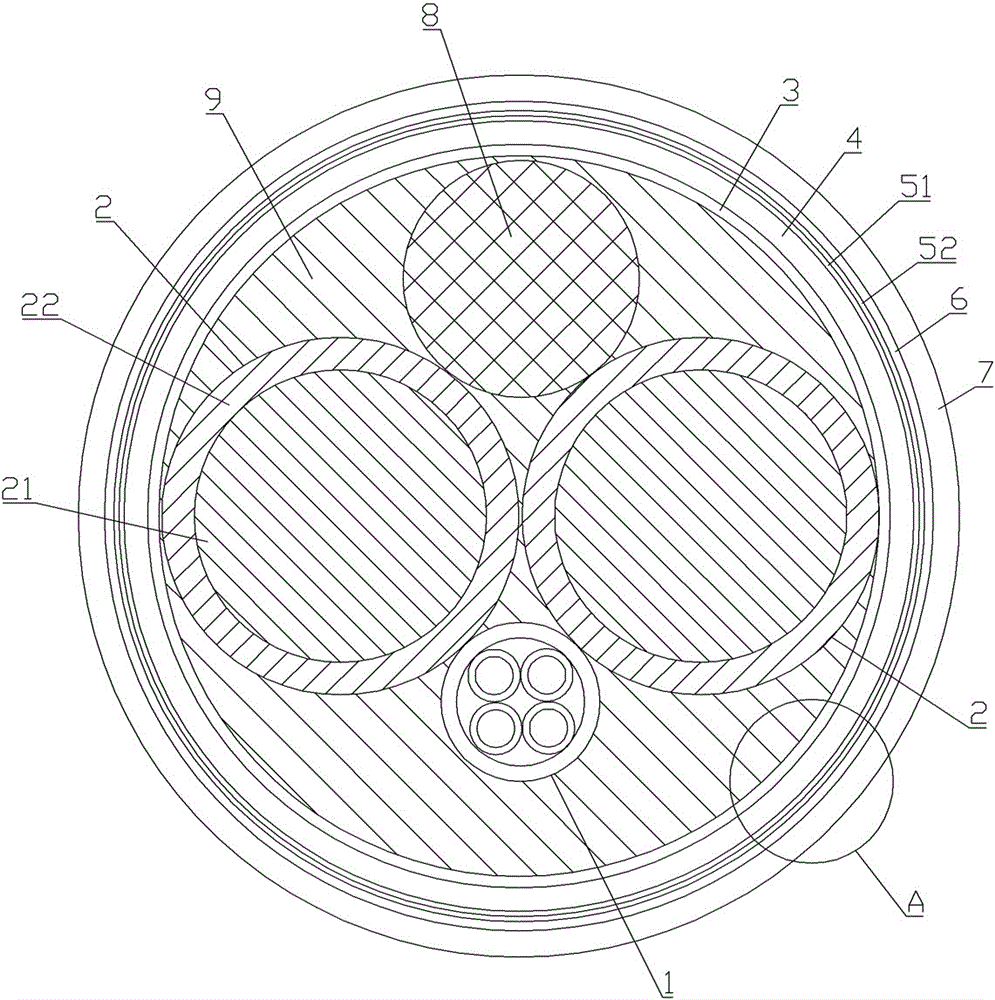
本发明涉及一种电缆,特别是一种电动汽车传导充电系统用电缆。
背景技术:
:电动汽车传导充电系统用电缆是随着电动汽车而出现的一种新型的电缆形式,它用于电动汽车与电源的充电连接,是电动汽车传导充电系统的关键设备之一,该类产品的性能优劣对电动汽车的安全可靠运行将产生直接的影响。该类电缆可在室内或室外使用,在室外使用时应满足高寒、日光、雨水及汽车用油类物质的侵蚀,这就要求电缆具备适用于使用场合的抗紫外线、臭氧、耐高低温和化学侵蚀等特殊性能。其在使用过程中会被频繁的拉伸弯曲或被电动汽车碾压,所以该类电缆也应该满足特殊的机械性能要求,如曲绕、弯曲及车辆碾压试验等。现有的电动汽车传导充电系统用电缆的结构如图1所示,包括由多根绝缘线芯10绞合而成的缆芯、信号线11、将缆芯与信号线一同包覆在内的无纺布层12和包覆在无纺布层12外的护套层13。在无纺布层12与绝缘线芯10之间的间隙中填充有填充材料14。绝缘线芯10包括多束股线绞合而成的导体101和包覆在导体101外的绝缘层102。股线采用分层绞合的结构形成导体101,最内层为单根股线,其余层均由多束股线分别绞合而成,由最内层向外,每一层均将上一层紧密包围在内。除最内层,相邻层之间绞向相反。但该结构的电缆存在以下不足之处:1、绝缘线芯的导体由股线分层绞合而成,其中最外层节径比为14~16倍,除最外层和最内层之外的其它层的节径比为16~19倍,绝缘线芯绞合成缆芯的节径比为16~18倍。节径比较大,导致导体和缆芯的弯曲半径小,导体和缆芯的柔软度不能满足电缆频繁移动、弯曲及耐扭转的要求。2、无纺布层采用重叠式绕包将缆芯和信号线一同包覆在内,该结构缆芯与护套层不能接触,电缆在频繁弯曲及扭转时,缆芯与护套层各自发生位置移动,造成电缆起包,导体断裂,护套层损坏,缩短了电缆的使用寿命。3、绝缘线芯的横截面一般为圆形,那么绝缘线芯之间的间隙较大,现有的填充材料为聚乙烯绳,不能保证电缆的圆整度。技术实现要素:本发明的目的是克服现有技术的不足,而提供一种电动汽车传导充电系统用电缆。它具有较高的柔软性、优秀的抗外载压力、良好的耐油性、极佳的低温韧性和抗电磁干扰性。解决了现有的电动汽车传导充电系统用电缆弯曲半径小、柔软度不够,使用过程中缆芯与护套层容易各自发生位移,造成电缆起包,导体断裂,护套层损坏,及圆整度达不到要求的问题。本发明的技术方案是:一种电动汽车传导充电系统用电缆,包括缆芯和信号线,缆芯由多根绝缘线芯绞合而成,还包括将缆芯与信号线一同包覆在内的聚酯薄膜带层;依次包覆在在聚酯薄膜带层外的内护套层、电磁屏蔽层、无纺布层及外护套层;及填充在内护套层与绝缘线芯之间间隙中的填充物;无纺布层采用间隙式绕包,间隙率为20%~30%;聚酯薄膜带层采用重叠式绕包,重叠率不小于25%。本发明进一步的技术方案是:填充物包括芳纶纱。本发明再进一步的技术方案是:填充物还包括填充条。本发明进一步的技术方案是:绝缘线芯包括多束股线绞合而成的导体和包覆在导体外的绝缘层;股线采用分层绞合的结构形成导体,最内层为单根股线,其余层均由多束股线分别绞合而成,由最内层向外,每一层均将上一层紧密包围在内,除最内层外的其余各层绞向相同,除最内层外的其余各层绞合的节径比为8~10倍。本发明进一步的技术方案是:电磁屏蔽层包括铝塑带层和绕包在其上的编织铜丝层。本发明再进一步的技术方案是:绝缘线芯绞合成缆芯的节径比为12~14倍本发明与现有技术相比具有如下优点:1、填充物中加入填充条绞合成一个密实的整体,极大提高了电缆的耐弯曲,抗扭转性能,使电缆整体具有优秀的抗外载压力及热应力,良好的耐油性和极佳的低温韧性。2、填充物包括填充条和芳纶纱,填充条的直径与绝缘线芯的直径相等,并采用密度和硬度大于芳纶纱的TPE材质,可增加电缆结构的稳定性,保证电缆的圆整性。3、相比于现有的电缆,增加了电磁屏蔽层,其包括铝塑带层和绕包在其上的编织铜丝层,增强了电缆的抗电磁干扰性。铜丝编织层网格中心产生的电容被铝塑带大部分消除,表面转移阻抗小于10(CQC标准小于250),两者产生的磁场相互抵消。4、采用聚酯薄膜带将缆芯与信号线一同包覆在内,并采用重叠式绕包,便于把缆芯扎紧,保证了电缆的圆整性,还便于后工序中缆芯与内护套层紧密结合,方便充电桩电缆端子的接头。5、绝缘线芯的导体是由股线分层绞合而成,除最内层外的其余各层绞向相同,柔软性得到提升,弯曲半径达5D(D为成品电缆直径),除最内层外的其余各层绞合的节径比为8~10倍,绝缘线芯绞合成缆芯的节径比为12~14倍,与现有的电缆相比,节径比缩小,弯曲半径进一步缩小。以下结合图和实施例对本发明作进一步描述。附图说明图1为现有的电动汽车传导充电系统用电缆的结构示意图;图2为本发明实施例1的结构示意图;图3为本发明实施例2的结构示意图;图4为本发明实施例3的结构示意图;图5为图2的A部放大图。注明:为使结构显示得更清楚,部分剖面线未填充。具体实施方式实施例1:如图2、5所示:一种电动汽车传导充电系统用电缆,包括:缆芯;信号线1;将缆芯与信号线一同包覆在内的聚酯薄膜带层3;依次包覆在在聚酯薄膜带层3外的内护套层4、电磁屏蔽层、无纺布层6及外护套层7;及填充在内护套层4与绝缘线芯2之间间隙中的填充物。缆芯由多根绝缘线芯2绞合而成。绝缘线芯2包括多束股线绞合而成的导体21和包覆在导体21外的绝缘层22;股线采用分层绞合的结构形成导体21,最内层为单根股线,其余层均由多束股线分别绞合而成,由最内层向外,每一层均将上一层紧密包围在内,除最内层外的其余各层绞向相同,除最内层外的其余各层绞合的节径比为8~10倍。绝缘线芯2绞合成缆芯的节径比为12~14倍。聚酯薄膜带层3采用重叠式绕包,重叠率不小于25%。电磁屏蔽层包括铝塑带层51和绕包在其上的编织铜丝层52。编织铜丝层52的编织密度不低于80%。无纺布层6采用间隙式绕包,间隙率为20%~30%。本实施例中,绝缘线芯有两根,填充物包括填充条8和芳纶纱9。实施例2:如图3所示,本实施例与实施例1相比,区别仅在于:绝缘线芯有四根,填充物为芳纶纱9。实施例3:如图4所示,本实施例与实施例1相比,区别仅在于:绝缘线芯有五根,填充物包括填充条8和芳纶纱9。关于技术效果的说明:本发明的电缆与现有的电动汽车传导充电系统用电缆分别在相同的试验条件下做成品电缆直流耐压试验、电磁屏蔽层表面转移阻抗试验、成品电缆高温压力试验、成品电缆低温卷绕试验、成品电缆曲挠试验、成品电缆车辆碾压试验及成品电缆扭摆试验。上述的试验中选用本发明的成品电缆外径为11.5~14.8(mm),对比例(即现有电缆)的成品电缆外径也选用11.5~14.8(mm)。试验结果分别如表1~7所示。表1:成品电缆直流耐压试验表2:电磁屏蔽层表面转移阻抗试验实验参数技术要求试验结果本发明30MHz≤2504~8现有电缆30MHz≤25065~82表3:成品电缆高温压力试验表4:成品电缆低温卷绕试验表5:成品电缆曲挠试验表6:成品电缆车辆碾压试验表7:成品电缆扭摆试验(40N)结合表1~7可以看出,本发明的电动汽车传导充电系统用电缆与现有的电动汽车传导充电系统用电缆相比,具有优良的电性能,耐弯曲性能,抗扭转性能,低温韧性及抗外载压力性能。当前第1页1 2 3