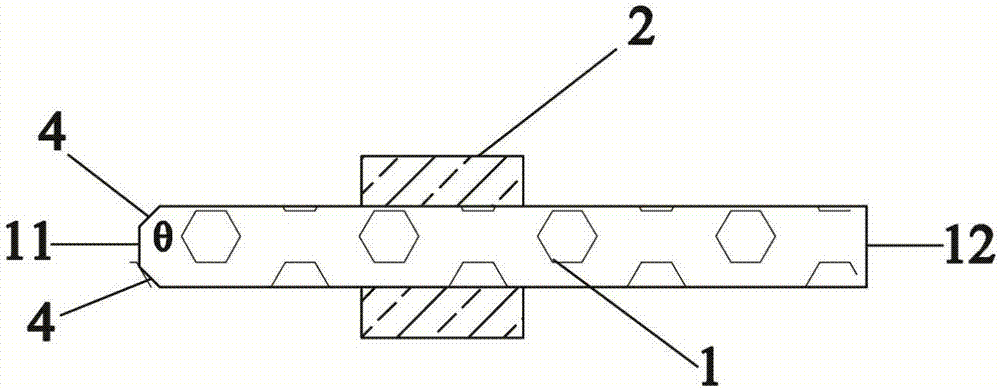
本实用新型属于锂离子电池
技术领域:
,尤其涉及一种极耳。
背景技术:
:锂离子电池具有能量密度大、输出功率高、充放电寿命长、无污染、工作温度范围宽和自放电小等诸多优点,被广泛应用于各类便携式电子设备中。随着时代进步,人们对便携式电子设备的要求越来越高,而首当其冲的是便携式电子设备的重量,这对锂离子电池的重量体积密度和容量体积密度的要求越来越高,因而越来越多的锂离子电池采用铝塑包装壳体。采用铝塑软包装的电池,由于其壳体不导电,因而需要采用极耳将电池内部的正极、负极和外界连接。目前,铝塑膜一般由尼龙层、铝箔层和流延聚丙烯层组成,极耳则是由极耳胶和金属带热压复合而成的。现有技术中,极耳的金属带平面和端面都具有棱角,这些棱角具有一定的尖锐度,一方面,平面棱角容易刺穿极耳胶和铝塑膜的CPP层后与铝塑膜中间的铝箔接触,将导致电池腐蚀、极耳处漏液;另一方面,端面上的毛刺容易刺破隔离膜,将导致电池短路甚至起火等安全问题。专利CN205543013U中公开了一种极耳,其在金属带平面个边缘接连处设置了弧形倒角,虽然其降低了金属带平面棱角的尖锐度,避免金属带刺穿铝塑膜,一定程度上提高了锂离子电池的安全性;但是金属带端面存在的毛刺容易刺穿隔离膜这一缺陷并没有得以克服。技术实现要素:本实用新型的目的在于:针对现有技术的不足,而提供一种极耳,以避免金属带刺破铝塑膜和隔离膜,进而提高锂离子电池的安全性。为了实现上述目的,本实用新型采用以下技术方案:一种极耳,包括金属带和粘接于所述金属带两面的极耳胶,所述金属带设置为方形,所述金属带的四个角设置有第一倒角,所述金属带的第一端面或/和第二端面设置有第二倒角,所述第一倒角为弧形倒角,所述第二倒角为倾斜倒角。作为本实用新型所述的极耳的一种改进,所述第一倒角的半径为1~10mm。作为本实用新型所述的极耳的一种改进,所述第一倒角的半径为1~4mm。作为本实用新型所述的极耳的一种改进,所述第二倒角的倾斜角度θ为90<θ<180°。作为本实用新型所述的极耳的一种改进,所述第二倒角的倾斜角度θ为120≤θ≤160°。作为本实用新型所述的极耳的一种改进,所述金属带的宽度为3~150mm。作为本实用新型所述的极耳的一种改进,所述金属带的厚度为0.08~1mm。作为本实用新型所述的极耳的一种改进,所述金属带设置为铝带、镍带、铜镀镍带或铜带。相对于现有技术,本实用新型的有益效果在于:本实用新型提供一种极耳,包括金属带和粘接于所述金属带两面的极耳胶,所述金属带设置为方形,所述金属带的四个角设置有第一倒角,所述金属带的第一端面或/和第二端面设置有第二倒角,所述第一倒角为弧形倒角,所述第二倒角为倾斜倒角。一方面,第一倒角可以防止金属带刺穿极耳胶和铝塑膜的CPP层后与铝塑膜中间的铝箔接触,避免发生电池腐蚀;另一方面,第二倒角可以防止端面上的毛刺刺破隔离膜,避免电池短路甚至起火等安全问题。附图说明图1是本实用新型的平面图。图2是本实用新型中实施例1的截面图。图3是本实用新型中实施例2的截面图。图4是本实用新型中实施例3的截面图。其中:1-金属带,2-极耳胶,3-第一倒角,4-第二倒角,11-第一端面,12-第二端面。具体实施方式下面结合具体实施方式和说明书附图,对本实用新型作进一步详细的描述,但本实用新型的实施方式并不限于此。实施例1如图1~2所示,一种极耳,包括金属带1和粘接于金属带1两面的极耳胶2,金属带1设置为方形,金属带1的四个角设置有第一倒角3,金属带1的第一端面11设置有第二倒角4,第一倒角3为弧形倒角,第二倒角4为倾斜倒角。第一倒角3的半径为1mm。第二倒角4的角度θ为120°。金属带1的宽度为3mm。金属带1的厚度为0.08mm。金属带1设置为铝带。实施例2如图3所示,与实施例1不同的是,本实施例中金属带1的第二端面12设置有第二倒角4。第一倒角3的半径为4mm。第二倒角4的倾斜角度θ为135°。金属带1的宽度为50mm。金属带1的厚度为0.5mm。金属带设置为镍带。其它的与实施例1相同,这里不再赘述。实施例3如图4所示,与实施例1不同的是,本实施例中金属带1的第一端面11和第二端面12均设置有第二倒角4。第一倒角3的半径为10mm。第二倒角4的角度θ为160°。金属带1的宽度为150mm。金属带1的厚度为1mm。金属带设置为铜镀镍带或铜带。其它的与实施例1相同,这里不再赘述。对比例1~3与实施例1~3不同的是,本对比例中金属带1的四个角没有设置第一倒角3,金属带1的第一端面11或/和第二端面12也没有设置第二倒角4。其它的与实施例1~3相同,这里不再赘述。对比例4~6与实施例1~3不同的是,本对比例中金属带1的四个角设置有第一倒角3,金属带1的第一端面11或/和第二端面12没有设置第二倒角4。其它的与实施例1~3相同,这里不再赘述。测试结果分别对上述实施1~3和对比例1~6的极耳进行测试,测试方法如下:测试一:将实施例1~3和对比例1~6的极耳制作成锂离子电池,再将制得的锂离子电池充电至3.85V,使用万用表打到电流档,正极接通电池铝塑壳中的铝层,负极接通到金属带1,读取万用表的电流大小。测试结果如表1所示。测试二:将实施例1~3和对比例1~6的极耳制作成锂离子电池,对电池进行充电,测试其是否发生膨胀、起火、爆炸等现象,以判断电池是否发生短路。表1测试结果电池数量边电流<1μA边电流≥1μA实施例11001000实施例21001000实施例31001000对比例11009010对比例2100928对比例31008812对比例41001000对比例5100982对比例6100991表2测试结果二由表1可以看出,实施1~3中极耳所制得的锂离子电池测得边电流≥1μA的电池数均为0,由此可见,该锂离子电池的安全性能较好,第一倒角3的设置能有效防止金属带与铝塑膜中的铝层接触。由表2可以看出,实施例1~3中极耳制得的锂离子电池发生膨胀、着火或爆炸等的几率较对比例1~6小,也就是说,实施例1~3中极耳制得的锂离子电池内部发生短路的几率胶对比例1~6小,这是因为实施例1~3中的极耳在金属带1的第一端面11或/和第二端面12设置了第二倒角4,其防止了金属带侧破隔离膜,进而避免了正极极片与负极极片的接触而造成的内部短路的发生。根据上述说明书的揭示和教导,本实用新型所属领域的技术人员还能够对上述实施方式进行变更和修改。因此,本实用新型并不局限于上述的具体实施方式,凡是本领域技术人员在本实用新型的基础上所作出的任何显而易见的改进、替换或变型均属于本实用新型的保护范围。此外,尽管本说明书中使用了一些特定的术语,但这些术语只是为了方便说明,并不对本实用新型构成任何限制。当前第1页1 2 3