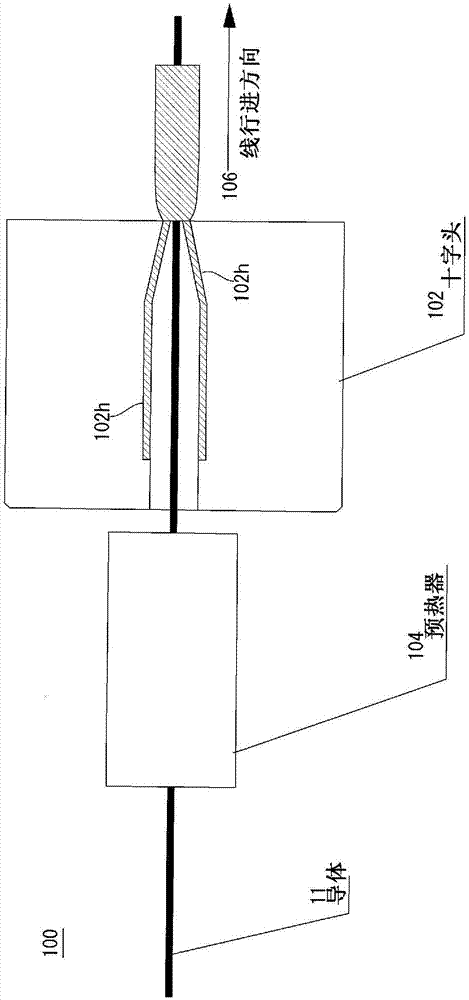
本发明涉及例如在医疗设备等中使用的发泡同轴电缆等传输电缆和构成该传输电缆的电缆芯。
背景技术:
:在通信用电线中使用的同轴电缆中,对于由发泡体构成在中心导体的周围设置的电介体而得到的发泡同轴电缆,电介体的介电常数小、能够高速传输信号,因此,被用作信号传输电缆。例如,在专利文献1记载的现有例中,发泡绝缘电缆被用作通信用电线。另一方面,对于在医疗设备等中使用的同轴电缆,近年来,随着医疗设备等的小型轻量化和省电化,要求同轴电缆的细径化。例如,在医用超声波探头电缆、内视镜电缆等芯数多的传输电缆中已使用了发泡同轴电缆,从操作性的观点考虑,特别要求电缆的细径化和柔软性。现有技术文献专利文献专利文献1:日本特开2011-162721号公报技术实现要素:发明欲解决的技术问题例如,专利文献1记载的现有例的目的在于解决发泡成核剂凝聚的问题,并且形成低介电常数的发泡绝缘体,通过将不同种类的高分子材料混炼在基体树脂中,在其界面产生气泡,成形发泡成形体,从而能够得到气泡径小、发泡度高且均匀、低介电常数、低延迟差的发泡绝缘电缆。然而,在专利文献1记载的现有例中,对于电缆的细径化而言,气泡径太大,而且,关于用于在进行细径化的同时维持电气特性的技术,没有给出任何技术启示。另外,一般在现有的发泡同轴电缆中,关于同时实现维持电气特性和细径化的技术,事实上几乎没有有效的提案。为了在对发泡同轴电缆进行细径化的同时维持电气特性,需要降低构成发泡同轴电缆的电缆芯的电介体的介电常数。对于降低电介体的介电常数,存在提高构成电介体的发泡电介体的发泡率的方法。另外,伴随着细径化,发泡电介体的壁厚也变薄,因此,需要进一步减小发泡泡孔直径。随着发泡率变高,将导致发泡电介体的发泡泡孔的增大、合并,发泡泡孔直径的不均变得显著。发泡泡孔直径变得不均,从而对电缆特性的影响大,另外,发泡泡孔直接成为外观的凹凸,在电缆的耐久性、绝缘性等方面产生问题。本发明是鉴于上述问题而完成的,其目的在于提供一种能够在对电缆芯进行细径化的同时维持电气特性的技术。用于解决问题的技术手段本发明人针对将发泡同轴电缆细径化所需要的构成反复进行了深入研究,结果发现,通过以构成同轴电缆的电缆芯的发泡电介体的发泡率为80%以上,所述发泡电介体的平均发泡泡孔直径为10μm以下,发泡泡孔直径的标准偏差为2.5以下的方式构成,从而能够在将电缆芯细径化的同时维持电气特性。即,为了实现上述目的,本发明的构成发泡同轴电缆的电缆芯的特征在于,所述电缆芯由内部导体、发泡电介体和表层构成,其中,所述发泡电介体在所述内部导体上利用挤出成形而形成,并且,由氟树脂构成,所述表层包覆所述发泡电介体,其中,所述发泡电介体的发泡率为80%以上,所述发泡电介体的平均发泡泡孔直径为10μm以下,所述发泡电介体的发泡泡孔直径的标准偏差为2.5以下。根据本发明,能够提供一种电气特性优异的awg40以上的极细发泡同轴电缆。此处,本发明的电缆芯的电介体由发泡电介体和包覆发泡电介体的表层构成。发泡电介体由发泡树脂构成,与此相对,表层由实心树脂构成。表层具有将内部导体与外部导体绝缘的功能,也有助于发泡电介体的表面的平滑化。发泡电介体能够用现有公知的物理发泡和化学发泡的手法进行发泡。例如,可以列举以下方法:向在氟树脂中加入发泡成核剂而得到的发泡性组合物导入氮气等气体作为发泡剂,同时进行挤出成形,并且将通过加热进行热分解而产生气体的发泡性物质等混合在发泡性组合物中。作为成为发泡电介体的基体(base)的氟树脂,可以列举:四氟乙烯-六氟丙烯共聚物(fep)、四氟乙烯-全氟烷基乙烯基醚共聚物(pfa)、乙烯-四氟乙烯共聚物、乙烯-三氟氯乙烯共聚物、聚偏二氟乙烯、聚氟乙烯等热塑性氟树脂。这些可以单独使用,也可以多种组合使用。作为发泡成核剂,优选不影响电气特性的电气绝缘性的成核剂。具体而言,可以列举:从氮化硼、硼酸铝、硼酸镁、钛酸钾、氮化硅等中选出的成核剂。表层由实心树脂形成,因此,为了提高发泡层整体的发泡率,需要将表层变薄,具体而言,有时也需要使表层薄壁化到0.01mm以下。表层由于薄壁化而容易受到发泡电介体的发泡泡孔成长导致的应力的影响和成形时下拉的伸长应力的影响,因此,难以在取得与发泡电介体的平衡的同时稳定地成形均匀的表层。作为表层中使用的树脂,可以列举:四氟乙烯-六氟丙烯共聚物(fep)、四氟乙烯-全氟烷基乙烯基醚共聚物(pfa)、乙烯-四氟乙烯共聚物、乙烯-三氟氯乙烯共聚物、聚偏二氟乙烯、聚氟乙烯等热塑性氟树脂。为了稳定地成型薄壁的表层,形成表层的树脂的熔化张力与mfr的平衡是重要的,为了成为适合表层的特性,可以单独使用这些树脂,也可以将多种组合。在发泡电介体12和表层13中使用的树脂也可以不同。将发泡电介体的发泡率设定为80%以上是因为,为了在进行细径化的同时维持电缆芯的电气特性,需要将电介体的介电常数抑制得较低。例如在构成电介体的树脂为pfa的情况下,通过使发泡率为80%以上,从而电介体的介电常数达到1.3以下。为了提高发泡电介体的发泡率,不优选构成发泡电介体的树脂的粘度过高。如果粘度过高,则妨碍发泡泡孔的产生和成长,难以提高发泡率。另一方面,如果粘度过小,则已出现的发泡泡孔的增大和合并容易进一步恶化,特别是,发泡电介体的发泡率越高,越容易引起泡孔的合并。一旦电缆芯细径化,发泡电介体的壁厚也变薄,因此,在发泡电介体的厚度方向能够排列的发泡泡孔的个数变少。经研究获知,为了保持发泡电介体的机械强度,需要减小每个发泡泡孔的直径,使得在发泡电介体内尽可能多地存在发泡泡孔的壁。如果所述发泡体的平均发泡泡孔直径为10μm以下,则即使是电缆芯的中心导体为awg40以上的极细线,也能得到充分的发泡电介体的机械强度,即使在使电缆弯曲时,也能够防止传导特性因电介体的压碎而下降。另外,电缆芯的直径越细,发泡电介体的壁厚越薄,发泡泡孔直径与发泡电介体的壁厚的比变得越大,因此,发泡泡孔直径对电缆芯的特性有很大影响。为了得到作为信号传输电缆而良好的传输特性,需要发泡泡孔直径尽可能均匀。如果出现发泡泡孔的增大、合并,则发泡泡孔直径不均,电介体的均匀性被损坏,无法得到充分的性能。通过使所述发泡电介体的平均发泡泡孔直径为10μm以下,同时使发泡泡孔直径的标准偏差为2.5以下,从而能够兼顾电缆芯的细径化和电气特性的维持。进一步地,通过使发泡泡孔直径为10μm以下,从而电缆芯外径稳定。如果发泡泡孔直径大,则发泡电介体表面的凹凸变大,发泡电介体的壁厚的尺寸稳定性被损坏。如果发泡电介体的壁厚不稳定,则在作为传输电缆时,其特性阻抗改变,发生信号反射,因此不优选。另外,对于发泡电介体的壁厚变薄的部分,电缆芯外径变细,外力引起的负荷集中在外径细的部分,电缆芯的机械强度降低,此外,凹凸导致外观也变差。通过使所述发泡电介体的平均发泡泡孔直径为10μm以下的同时,将电缆芯外径mm的标准偏差设定为0.012以下,从而能够得到电气特性特别稳定的传输电缆。本发明的电缆芯的所述电缆芯的中心导体为awg40以上的极细线是合适的。例如,利用awg44、46、48的极细线,能够得到优异的效果。附图说明图1是示出以本发明的实施方式的电缆芯作为主要的构成要素的发泡同轴电缆的构成的图,(a)是从其轴方向观察到的图,(b)是从与其轴正交的方向观察到的图。图2是用于说明本发明的实施方式的电缆芯的挤出成形方法的图。图3是示出本发明的实施方式的构成电缆芯的表层(skinlayer)的树脂的、熔体粘度与mfr的优选范围的相关图。图4(a)是本发明的实施方式的电缆芯的截面的模式图,(b)是作为比较例的现有的电缆芯的截面的模式图。图5是使用了电缆芯外径mm的标准偏差超过0.012的电缆芯的同轴电缆的tdr曲线。图6是使用了电缆芯外径mm的标准偏差为0.012以下的电缆芯的同轴电缆的tdr曲线。符号说明1发泡同轴电缆、11内部导体、11a导线、12发泡电介体、13表层、14外部导体、15护套具体实施方式以下说明的实施方式并不用于限定权利要求所涉及保护范围,另外,实施方式中说明的特征的所有组合对本发明的成立并不是必不可少的。图1是示出以本发明的实施方式的电缆芯作为主要的构成要素的发泡同轴电缆的构成的图,(a)是其截面图,(b)是示出电缆的构造的图。在本实施方式的发泡同轴电缆1中,主要是,在由内部导体11、在内部导体11上利用挤出成形而形成的由氟树脂构成的发泡电介体12和包覆发泡电介体12的表层13构成的电缆芯的外周,配置外部导体14而构成。被构成为:发泡电介体12的发泡率为80%以上,所述发泡电介体的平均发泡泡孔直径为10μm以下,发泡泡孔直径的标准偏差为2.5以下。需要说明的是,在外部导体14的外周形成有护套15(jacket)。作为本发明的特征部分的发泡电介体12由使含有上述发泡成核剂的发泡性组合物发泡而得到的发泡树脂形成。如上构成的发泡同轴电缆1按照以下次序形成。首先,在内部导体11的外周使用挤出机(后述的),通过混合挤压,形成发泡电介体12和表层13,制作电缆芯。在发泡电介体12的挤出机内,在已熔化的发泡性组合物中注入氮气等发泡气体,形成由发泡树脂构成的发泡电介体12,同时以包覆该发泡电介体12的外周的方式形成表层13。发泡电介体12由发泡树脂形成,与此相对,表层13由固体树脂形成。为了实现本发明的发泡同轴电缆的构成,为了使发泡电介体12均匀地发泡,优选尽可能地减小发泡电介体整体的温度差。其理由是因为,由于树脂的温度不同,发泡泡孔的产生、成长速度也不同,通过使发泡电介体的温度均匀,从而发泡泡孔的产生和成长在整体上同时推进,其结果是,得到发泡泡孔直径小、均匀的发泡电介体。为了能够尽可能地减小发泡电介体的温度最高的外表面附近与温度最低的内部导体附近的温度差,优选在内部导体上挤出包覆发泡电介体时,同时进行从挤出树脂外侧加热和内部导体加热等手段。现有的电缆芯的发泡电介体的发泡可以认为是按照以下机理发生的。在挤出发泡性组合物的情况下,例如,在已使发泡性组合物溶解后的挤出机内,填充发泡气体,使发泡气体溶解于发泡性组合物。已溶解于发泡性组合物的发泡气体被发泡性组合物中的发泡成核剂吸附,发泡成核剂周围的发泡气体浓度变高。如果发泡性组合物从挤出机的模具流出,树脂的压力下降,则在发泡成核剂周围开始发泡。此时,树脂压力下降的速度在发泡电介体整体上不均匀。一般情况下,对于树脂,应力在熔化状态下在与挤出机的挤出方向正交的方向起作用,因此,压力先从发泡电介体外表面开始下降,相反地,内部导体侧的压力开始下降得晚。开始发泡时的树脂压力不均,因此,照这样的话,发泡泡孔的产生、成长偏向在发泡电介体外表面,成为发泡泡孔增大、合并的主要原因。相反地,发泡电介体的内部导体侧无法充分地发泡。此处,表层13具有抑制发泡电介体12的发泡泡孔的增大、合并,并且将发泡泡孔直径细微化的效果。通过在挤出发泡电介体的同时挤出表层,从而有从外侧控制住发泡电介体、减缓发泡电介体的外表面的树脂压力下降的速度、减小发泡电介体层整体的压力差的效果。此时,构成表层的树脂的熔化张力需要调整在既抑制发泡电介体外表面的急剧减压又不妨碍发泡的张力的范围。另外,同时,为了提高电介体整体的发泡率,需要将表层13构成为非常薄壁,因此,需要提高形成表层13的树脂的mfr。对于形成表层13的树脂来说,熔化张力与mfr的平衡是重要的。通过减小在发泡电介体发泡时的树脂温度、树脂压力的偏差,从而能够实现高发泡率、发泡泡孔直径的细微化、发泡泡孔直径均匀的发泡电介体。因此,能够实现在细径化的同时维持了电气特性的电缆芯。上述这样得到的发泡电介体的发泡泡孔直径是10μm以下,发泡泡孔直径的标准偏差为2.5以下。接着,在该电缆芯的外周形成外部导体14。外部导体14是通过将多根导体裸线14a以预定角度(螺旋状)相对于长轴方向横卷或编织,或者卷绕金属箔,或者用金属微粒的蒸镀等任意方法形成。最后,在该外部导体14的外周以预定角度(螺旋状)相对于长轴方向卷绕树脂带,或者使用挤出机挤出树脂进行包覆,形成护套15,从而发泡同轴电缆1完成。导线11a包含双绞线或单线。作为材质,包含铜线、银线、铝线、各种合金线等。一般情况下,使用在表面用银、锡等的镀层包覆后的线。例如,使用镀银的铜合金线等。作为导体裸线14a或金属箔的材质,例如,能够使用铜合金、镀银的软铜等任意材质。作为护套15的材质,除了氟树脂之外,可以使用一般的树脂,例如聚烯烃、聚氯乙烯、聚酯等。关于本实施方式的电缆芯的制造方法,进行详细说明。图2是用于说明本实施方式的电缆芯的挤出成形方法的图,示出挤出成形机的概略构成。为了实现本发明的电缆芯的构成,需要使发泡电介体均匀地发泡,因此,优选尽可能地减小使发泡电介体整体的树脂温度的差。优选将温度最高的部分与温度最低部分的温度差设定在10℃以内。在本实施方式中,在对内部导体11上挤出包覆发泡电介体12时,采用在从挤出树脂外侧加热的同时,先对内部导体11一边加热一边包覆的方法(预加热)。图2所示的挤出成形机100包括:预热器104和用于将发泡层和表层混合挤压的十字头102。11示出电缆芯的内部导体,箭头106表示线的行进方向。102h表示对十字头102中的树脂进行加热的加热器的配置部分。被设置为:除了利用该挤出成形机100的加热构造从挤出树脂外侧加热之外,还利用预热器104,先对内部导体11进行加热(预加热)。基于此,利用从已加热的内部导体11传递的热,也对发泡电介体12的导体侧进行加热,因此,能够有效地防止在发泡电介体12中在外侧与导体侧产生温度差。另外,对于与发泡电介体混合挤压的表层,考虑构成表层的树脂的熔化张力与mfr的平衡、与发泡电介体发泡时的应力的平衡,来调整树脂的选择、挤出条件等。虽然熔化张力与mfr因电缆芯的尺寸、表层的壁厚等的不同而不同,但对于本发明的电缆芯的尺寸,只要在380℃时进行测定的情况下的熔化张力约为0.03n~0.08n,并且,将mfr设定为约15~40g/min即可。在图3中,用虚线的矩形示出上述的熔化张力与mfr的合适范围。熔化张力与mfr彼此的平衡是重要的,因此,即使在上述范围中,也特别优选设定为由图3的四边形围成的范围。以下示出本实施方式的电缆芯的制造方法的要点。实施例1将含有四氟乙烯-全氟烷基乙烯基醚共聚物(三井·杜邦氟化学制pfa420hp-j)99.5质量%和硼酸铝晶须(四国化成制アルボレックスy)0.5质量%的发泡性组合物在挤出机中以模具的温度400℃进行挤出成形。向挤出机注入0.7mpa的氮气,在已预加热到405℃的0.05mm的镀银的软铜线上利用发泡成形形成外径0.15mm的发泡电介体。在包覆发泡电介体的同时,从另一台连接着的挤出机挤出调整成熔化张力0.04n、mfr30的以pfa420hp-j为基体的pfa,在发泡电介体的外表面形成了表层。对得到的发泡电介体的静电容量进行测定,利用以下的数学式1求出介电常数ε,根据得到的介电常数,进一步利用以下的数学式2求出气孔率v(%)。[数1]ε=(c×log(d/d))/24.16此处,c:每1m的静电容量(pf)d:电介体外径(mm)d:导体的直径(mm)[数2]v=(1-logε/logεf)×100此处,εf:构成发泡体电介体的组合物的发泡前的介电常数图4(a)是以与轴方向垂直的面切断本实施方式的电缆芯,并且用光学显微镜(hirox制kh-2700)观察截面而得到的显微镜照片的模式图。发泡泡孔直径的算出是根据截面的显微镜照片的图像算出。发泡泡孔也包含椭圆形状的泡孔,因此,用以下的数学式3换算成圆形。[数3]发泡泡孔直径=(最长泡孔直径+最短泡孔直径)/2针对任意50个或者在截面图像中能够确认的全部发泡泡孔,算出发泡泡孔直径,将其平均值作为平均发泡泡孔直径。根据以与轴方向垂直的面切断电缆芯而得到的截面的光学显微镜照片的图像,算出电缆芯的外径。对每个截面,在4个方向测定外径,将其平均值作为电缆芯外径。在任意50处测定电缆芯外径,求出电缆芯外径的标准偏差。比较例1对在实施例1中使用的发泡性组合物,除了不进行导体预加热,并将构成表层的树脂的熔化张力设定为0.018n、将mfr设定为35以外,与实施例1同样地制作电缆芯,与实施例1同样地,测定静电容量。另外,将得到的电缆芯以与轴方向垂直的面切断,用光学显微镜照片观察截面。图4(b)是其截面的显微镜照片的模式图。根据显微镜照片的图像,与实施例1同样地,求出平均发泡泡孔直径和发泡泡孔直径的标准偏差。对于图4(a)实施例1的电缆芯,与图4(b)比较例1的电缆芯相比,电介体的发泡率提高。即,与比较例1的电缆芯相比,第一、发泡电介体12的发泡率升高,第二、表层13被薄壁化。另外,对于比较例1的电缆芯,发泡电介体外表面附近的发泡泡孔增大、合并,发泡电介体的发泡泡孔直径不均变得显著。与此相对,实施例1的电缆芯的发泡电介体抑制了发泡泡孔的增大、合并,与比较例1相比,泡孔直径变得均匀。因此,能够防止发泡泡孔直径不均所导致的、对电缆的电气特性的不良影响,也减少外观的凹凸,能够有效地防止在电缆的耐久性、绝缘性等方面产生问题。关于第二点,即使在将发泡层与表层混合挤压的情况下,也能够将表层薄壁化,成形均匀的表层。试制了本发明的发泡同轴电缆的实施例,结果通过使发泡电介体的发泡率为80~90%、使表层厚为0.006~0.008μm,从而能够在维持静电容量:60pf/m的状态下,成形电介体外径φ0.15mm以下的电缆。将本发明的发泡电缆的实施例与比较例的发泡电缆的主要尺寸、发泡率、静电容量、平均发泡泡孔直径等示于表1。[表1]实施例1比较例1导体尺寸awg46awg46导体直径(mm)0.050.05介电体外径(mm)0.150.17介电发泡体层厚(mm)0.0420.05表层厚(mm)0.0080.01发泡层的发泡率(%)9065介电体发泡率(%)6245静电容量(pf/m)61±2.561±2.5泡孔直径平均值(μm)8.1419.2泡孔直径平均标准偏差2.15.7如表1所示,实施例1的发泡电缆在维持了电气特性的状态下,与比较例1相比,分别得到了显著改善,芯外径(mm)从0.17细径化至0.15,表层厚(mm)从0.01改善至0.00g,发泡电介体的发泡率从65%改善至90%。实施例2导体使用0.09mm镀银的软铜线,在导体上形成发泡电介体,同时在发泡电介体的外表面形成表层。除了将构成表层的树脂的熔化张力设定为0.0gn、将mfr设定为15以外,与实施例1同样地,制作外径0.33mm的电缆芯。比较例2除了导体使用0.09mm镀银的软铜线、将构成表层的树脂的熔化张力设定为0.05n、将mfr设定为10以外,与比较例1同样地,制作外径0.35mm的电缆芯。实施例3导体使用0.06mm镀银的软铜线,在导体上形成发泡电介体,同时在发泡电介体的外表面形成表层。除了将构成表层的树脂的熔化张力设定为0.07n、将mfr设定为27以外,与实施例1同样地,制作外径0.19mm的电缆芯。实施例4导体使用0.05mm的镀银的软铜线,向挤出机注入0.8mpa的氮气,在导体上形成发泡电介体。在包覆发泡电介体的同时,在发泡电介体的外表面形成表层。除了将构成表层的树脂调整为熔化张力0.03n、mfr25以外,与实施例1同样地,制作外径0.14mm的电缆芯。实施例5导体使用0.039mm的镀银的软铜线,在导体上形成发泡电介体,同时在发泡电介体的外表面形成表层。除了将构成表层的树脂的熔化张力设定为0.03n、将mfr设定为35以外,与实施例1同样地,制作外径0.133mm的电缆芯。针对各实施例、比较例,与实施例1同样地,求出平均发泡泡孔直径和发泡泡孔直径的标准偏差。将本发明的发泡电缆的实施例和比较例的发泡电缆的主要尺寸、发泡率、静电容量、平均发泡泡孔直径等示于表2。[表2]实施例2比较例2实施例3实施例4实施例5导体尺寸awg40awg40awg44awg46awg48导体直径(mm)0.090.090.060.050.039芯外径(mm)0.330.350.190.140.133泡体层厚(mm)0.1130.1230.0580.0390.041表层厚(mm)0.0070.0070.0070.0060.006发泡层的发泡率(%)8469859582整体的发泡率(%)7959646761静中容量(pf/m)51±2.551±2.551±2.561±2.554泡孔直径平均值(μm)8.715.39.85.87.7泡孔直径平均标准偏差2.24.92.51.82.3如表2所示,实施例2的发泡电缆与具有与实施例2相同静电容量的比较例2相比,芯外径(mm)从0.35细径化到0.33。即使对于实施例3~5,通过使发泡率为80%以上,使平均发泡泡孔直径为10μm以下,抑制发泡泡孔的合并,并且使发泡泡孔直径的标准偏差为2.5以下,从而即使对电缆芯进行细径化,也能够维持电气特性。针对各实施例、比较例,与实施例1同样地,求出电缆芯外径的标准偏差。将本发明的电缆芯的实施例和比较例的电缆芯外径标准偏差等示于表3。另外,针对使用实施例1的电缆芯制成的同轴电缆,将进行timedomainreflectmetry(tdr)测定的结果的tdr曲线示于图5。同样地,针对使用实施例2的电缆芯制成的同轴电缆,将进行tdr测定的结果的tdr曲线示于图6。[表3]实施例1比较例1实施例2比较例2实施例3实施例4实施例5电缆芯外径平均值(mm)0.150.170.330.350.190.140.133电缆芯外径标准偏差(mm)0.0150.0220.0120.0260.0200.0040.003泡孔直径平均值(μm)8.1419.28.715.39.85.87.7泡孔直径平均标准偏差(μm)2.15.72.24.92.51.82.3可以知道,对于实施例1的电缆芯,芯外径的标准偏差大于0.012mm,图5的示出特性阻抗的tdr曲线的波形中出现了干扰,并且,特性阻抗因电缆位置而变动。对于实施例2的电缆芯,芯外径的标准偏差为0.012mm以下,图6示出的tdr曲线的波形稳定,得到电气特性特别稳定的传输电缆。如上所述,根据本发明的电缆芯,尽管发泡电介体的发泡率高,也能够抑制发泡泡孔的增大、合并。能够得到发泡电介体的发泡率高、发泡泡孔直径小、发泡电介体整体的发泡泡孔直径均匀的电缆芯,从而在以电缆芯作为主要的构成要素的发泡同轴电缆中,在实现细径化的同时,能够维持与电缆直径大时同等的电气特性。产业实用性对于以本发明的电缆芯作为构成要素的发泡同轴电缆,当然可以用在医疗设备、通信设备、计算机等电子设备中,也可以适当用在汽车、飞机等需要将控制设备搭载于狭小部的设备的控制电路。当前第1页12