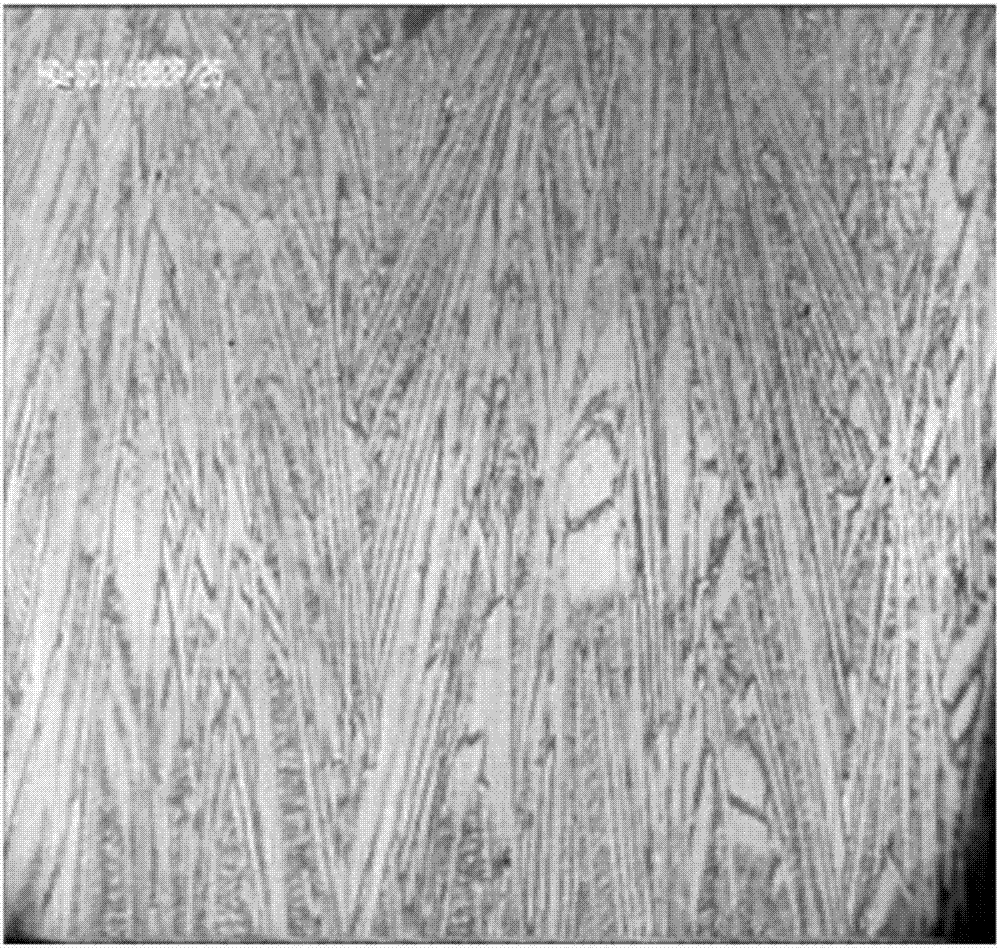
本发明属于钕铁硼磁体领域,尤其涉及到一种耐腐蚀钕铁硼磁体的制备方法。
背景技术:
:钕铁硼永磁材料按制备方法分为烧结、粘结永磁体,前者约占总产量的85%,据主导地位。烧结NdFeB是一种能量密度很高的贮能器,能够满足高矫顽力、高磁能积的要求,特别适用于高性能、小型化、轻型化器件的制备。烧结NdFeB广泛应用于军工设备、电声器件、电动机、发电机、计算机硬盘驱动器(HDD)、音圈电机(VCM)、人体核磁共振成像仪(MRI)、微波通讯技术、控制器、仪表、磁分离设备、磁卡盘及其他需用永久磁场的装置和设备中。随着时代飞速发展,烧结NdFeB在科技发展中扮演的角色愈加重要,社会需求量也逐年增加。烧结NdFeB基本上由Nd2Fe14B主相、富Nd晶界相构成,两相具有不同的物化性质,后者非常活泼,在含有腐蚀介质、湿热等环境中易于腐蚀。另外由于主相和晶界相之间的电极电位差大,易发生晶间腐蚀。烧结钕铁硼磁体耐蚀性差,严重限制其在重要领域的应用。技术实现要素:本发明的一个目的是解决至少上述问题,并提供至少后面将说明的优点。本发明通过提高氧含量,减小粉末粒度,改善了晶界相组织和理化特性,抑制和消弱了晶界相与主相间的电化学反应,减缓了晶界相的氧化腐蚀和氢化腐蚀,提供一种耐腐蚀钕铁硼磁体的制备方法。本发明是通过以下技术方案实现的:耐腐蚀钕铁硼磁体的制备方法,其包括以下步骤:步骤一将钕铁硼磁体烧结原材料制备成钕铁硼氢爆粉;步骤二将步骤一制得的所述钕铁硼氢爆粉进行气流磨处理得到磁粉,并将所述磁粉制得钕铁硼磁体,其中,所述气流磨处理时气流中的氧含量为800-900ppm,所述钕铁硼氢爆粉的粒径为2.9-3.1μm。优选的是,所述的耐腐蚀钕铁硼磁体的制备方法中,所述气流的气压为0.45MPa±0.05MPa,分级轮转速为4900rpm±100rpm。优选的是,所述的耐腐蚀钕铁硼磁体的制备方法中,所述钕铁硼磁体烧结原材料包括按重量份计的镨钕合金28-31份、纯铁31-33份、镝铁合金3-4份、纯铜0-0.1份、纯铝0.5-1份和硼铁合金0.95-1.05份,其中,所述镨钕合金中钕含量为25%,镝铁合金中镝含量为78%,硼铁合金中硼含量为18.3~20.4%。优选的是,所述的耐腐蚀钕铁硼磁体的制备方法,所述步骤一中,将所述钕铁硼磁体烧结原材料混合后经过熔炼、浇铸、冷却得到钕铁硼合金铸片,熔炼温度为1460℃±5℃,浇铸温度1460℃±5℃,真空度<4Pa,冷却时间>5h;所述钕铁硼合金铸片经过吸氢后形成氢化物使得所述钕铁硼合金铸片爆裂得到苏搜钕铁硼氢爆粉,氢气压力为0.15-0.18MPa,吸氢时间为1.5-2h,脱氢温度为580℃±4℃,脱氢时间为5h±20min。优选的是,所述的耐腐蚀钕铁硼磁体的制备方法,所述步骤二中,将所述磁粉在取向磁场≥1.5T条件下进行压制2-5s,成型后完全浸没在油液中进行冷等静压制得钕铁硼磁体压坯,等静压压力为200MPa,其中,压制过程采用氮气保护;将所述钕铁硼磁体压坯进行烧结制得钕铁硼磁体,烧结温度为1030℃-1039℃,保温时间为5h,一次回火温度为900℃,一次回火保温时间为4.5h,二级回火温度为480℃-600℃,二级回火保温时间为4h。优选的是,所述的耐腐蚀钕铁硼磁体的制备方法中,对所述钕铁硼磁体进行端面抛光或六面抛光。优选的是,所述的耐腐蚀钕铁硼磁体的制备方法中,对所述钕铁硼磁体进行酸洗。优选的是,所述的耐腐蚀钕铁硼磁体的制备方法中,还包括以下步骤:将所述钕铁硼磁体氢爆粉经蒸馏水清洗后放入除油液中在超声的作用下除油,除油时的温度在40-85℃,除油时间1-5min,溶液pH值8-11,之后用蒸馏水清洗干净,置于酸洗液中酸洗,酸洗温度20-30℃,酸洗时间6-8s,之后用蒸馏水洗净加5-30g·L-1的柠檬酸进行活化;活化时的温度10-40℃,活化时间10-60s;将气流磨后的磁粉加入到NiSO4、Na3C6H5O7、Nd2(SO4)3和KI的混合溶液中,在搅拌的条件下化学镀镍,镀镍时温度40-85℃,镀镍时间5-20min,化学镀镍过程中维持溶液pH值5-9;之后蒸馏水洗净,在真空或Ar气保护气氛中烘干后进行压制和烧结,干燥温度不超过120℃;其中,所述NiSO4、Na3C6H5O7、Nd2(SO4)3和KI的混合溶液中各组分的浓度为,20-30g/L的NiSO4,18-30g/L的Na3C6H5O7,50-70g·L-1的Nd2(SO4)3,3mg·L-1的KI;所述除油液为NaOH、Na2CO3、Na3PO4组成的混合液,其中,NaOH的浓度为8-10g/L,Na2CO3的浓度为40-60g/L,Na3PO4的浓度为60-80g/L;所述酸洗液为HCl或HNO3与硫脲的混合液,混合液中各组分的浓度为1-5%的HCl和1g/L的硫脲。本发明的有益效果:气流磨制备出粒径越细小、尺寸更分布均匀的粉末,钕铁硼合金粉末的烧结活性越大,更易烧结致密化,这样可降低磁体致密化所需烧结温度。故实验35SH的烧结温度(1030℃-1039℃)较量产35K(1039℃)低。粒径更细小的粉末所制作的烧结钕铁硼磁体主相晶粒更细,磁体Hcj就越高;粒径更细小、尺寸分布更均匀的粉末使得在烧结过程中液态的富钕相有更多的毛细通道自由流动,使得分布于主相晶粒边界的富钕相更加细薄、均匀,这不仅可提高磁体的各项磁性能指标,同时可显著改善磁体的耐腐蚀性;由于氧含量的增加,使得磁体合金成分中的稀土总量减少,这进一步的提高了磁体的耐腐蚀性;采用本发明提供的方法制得的烧结钕铁硼磁体的腐蚀失重为1.77-2.04mg/cm2,相比于现有技术的51.56mg/cm2有显著的降低。本发明的其它优点、目标和特征将部分通过下面的说明体现,部分还将通过对本发明的研究和实践而为本领域的技术人员所理解。附图说明图1为烧结钕铁硼磁体的单胞空间结构图;图2为烧结钕铁硼磁体的腐蚀过程图;图3为钕铁硼合金铸片的工艺流程图;图4为本发明的一个实施例中的对比例的钕铁硼合金铸片平行于冷却方向的截面的SEM背散射电子扫描图;图5为本发明提供的一个实施例中的对比例的钕铁硼合金铸片的一个金相图;图6为本发明提供的一个实施例中的对比例的钕铁硼合金铸片的另一个金相图;图7为本发明提供的一个实施例中的对比例的钕铁硼合金铸片的又一个金相图;图8为本发明提供的一个实施例中的对比例的钕铁硼合金铸片的再一个金相图;图9为本发明提供的一个实施例中的对比例的钕铁硼合金铸片厚度测试结果的过程能力直方分布图;图10为本发明提供的耐腐蚀钕铁硼磁体的制备方法的一个实施例的对撞式可控气流磨制粉的机理图;图11为本发明的一个实施例的磁粉的粒度分布图;图12为本发明的一个对比例的磁粉粒度分布图;图13为本发明的另一个实施例的混料后的磁粉的电子扫描图;图14为本发明的一个实施例的磁粉的1000倍的电子扫描图;图15为本发明的一个对比例的磁粉的1000倍的电子扫描图;图16为本发明的一个实施例的磁粉的2000倍的电子扫描图;图17为本发明的一个对比例的磁粉的2000倍的电子扫描图;图18为本发明的一个实施例的磁粉的4000倍的电子扫描图;图19为本发明的一个对比例的磁粉的4000倍的电子扫描图;图20为本发明的一个实施例的磁粉的8000倍的电子扫描图;图21为本发明的一个对比例的磁粉的8000倍的电子扫描图;图22为本发明提供的一个实施例压坯时模具方向的收缩比的I-MR控制图;图23为本发明提供的一个对比例压坯时模具方向的收缩比的I-MR控制图;图24为本发明提供的一个实施例压坯时压制方向的收缩比的I-MR控制图;图25为本发明提供的一个对比例压坯时压制方向的收缩比的I-MR控制图;图26为本发明提供的一个实施例压坯时取向方向的收缩比的I-MR控制图;图27为本发明提供的一个对比例压坯时取向方向的收缩比的I-MR控制图;图28为本发明提供的耐腐蚀钕铁硼磁体的制备方法的一个实施例的烧结流程图;图29为本发明提供的一个对比例在不同烧结温度下的烧结态Br箱线图;图30为本发明提供的一个对比例在不同烧结温度下的烧结态(BH)m的箱线图;图31为本发明提供的一个对比例在不同烧结温度和回火温度下烧结态Hcj的箱线图;图32为本发明提供的一个实施例的烧结钕铁硼磁体的金相图;图33为本发明提供的一个实施例的烧结钕铁硼磁体的另一个金相图;图34为本发明提供的一个实施例的烧结钕铁硼磁体的又一个金相图;图35为本发明提供的一个对比例的烧结钕铁硼磁体的金相图;图36为本发明提供的一个实施例的烧结钕铁硼磁体的断面电子扫描图;图37为本发明提供的一个实施例的烧结钕铁硼磁体的机加工后的一个断面电子扫描图;图38为本发明提供的一个实施例的烧结钕铁硼磁体的机加工后的另一个断面电子扫描图;图39为本发明提供的一个实施例的烧结钕铁硼磁体的机加工后的表面电子扫描图;图40为本发明提供的一个实施例的烧结钕铁硼磁体的机加工后的另一个表面电子扫描图;图41为本发明提供的一个实施例的烧结钕铁硼磁体的机加工后的又一个表面电子扫描图;图42为本发明提供的一个实施例的烧结钕铁硼磁体的机加工后的再一个表面电子扫描图;图43为本发明提供的一个实施例的烧结钕铁硼磁体的经过酸洗后的一个表面电子扫描图;图44为本发明提供的一个实施例的烧结钕铁硼磁体的经过酸洗后的另一个表面电子扫描图;图45为本发明的一个实施例的实验报告图;图46为本发明的一个实施例的实验报告图;图47为本发明的一个实施例的实验报告图;图48为本发明的一个实施例的实验报告图;图49为本发明的一个实施例的实验报告图;图50为本发明的一个实施例的实验报告图;图51为本发明的一个实施例的实验报告图;图52为本发明的一个实施例的实验报告图;图53为本发明的一个实施例的实验报告图;图54为本发明的一个实施例的实验报告图;图55为本发明的一个实施例的实验报告图。具体实施方式下面结合附图对本发明做进一步的详细说明,以令本领域技术人员参照说明书文字能够据以实施。应当理解,本文所使用的诸如“具有”、“包含”以及“包括”术语并不配出一个或多个其它元件或其组合的存在或添加。烧结NdFeB磁体的强磁性来源于Nd2Fe14B相。Nd2Fe14B具有四方结构,单胞空间结构如图1所示。烧结NdFeB属于多晶复相材料,主要由Nd2Fe14B主相、富Nd晶界相构成,还可能存在少量的富B相、Nd2O3、Nd2Fe17或a-Fe软磁相;此外,在合金化磁体的晶界区域可能出现Nd6Fe13Cu、Nd6Fe13Ga、NdCu等合金相。富Nd相是非磁性相,沿Nd2Fe14B晶粒边界分布或者呈块状存在于晶界接隅处,也可能呈颗粒状分布在主相晶粒内。富Nd相通常含有一定量的氧,因为氧在制备中是不能完全排除的。烧结磁体中,富Nd相起着重要作用:(1)促进烧结,起着助烧结作用,使磁体致密;(2)沿晶界分布,起去磁交换祸合作用,保证磁体高矫顽力。富Nd相的形态和分布显著地影响着磁体的磁性能。烧结NdFeB的Br、Hcj、(BH)max和Tc取决于材料的内部性能和显微组织,提高磁体磁性能的途径包括改变材料成分和改进制备工艺。在烧结NdFeB永磁体生产中,成分设计是基础,制备工艺是关键。烧结NdFeB的磁性能受制备工艺(熔铸或熔甩、制粉、取向压制、烧结、热处理)和制备环境(氧含量)影响。烧结NdFeB永磁材料制备方法包括单合金法和双合金法。目前,生产中多采用单合金法,其工艺流程为:原材料准备→冶炼→铸锭→破碎与制粉→磁场取向与压型→烧结→回火→机加工与表面处理→检测。制备流程中前7个环节的工艺参数均对烧结磁体的磁性能有影响。制备高性能磁体必须做到以下6点:①熔炼中合金液要“清、准、均、净”,避免夹杂、污染,保证成分准确;②铸锭组织应柱状晶生长良好,尺寸细小,富Nd相沿晶分布均匀,不存在a-Fe;③磁粉颗粒尺寸要小(2.5-3.5μm),分布要窄,颗粒要呈球状或近似球状,表面吸附杂质和气体要少,尤其是氧含量要小;④取向压制时做到压坯密度均匀,易磁化C轴取向一致;⑤烧结确保磁体致密,晶粒尺寸(~6μm)分布均匀;⑥回火处理保证富Nd相沿晶界均匀分布,晶界光滑、平直。烧结NdFeB基本上由Nd2Fe14B主相、富Nd晶界相构成,两相具有不同的物化性质,后者非常活泼,在含有腐蚀介质、湿热等环境中易于腐蚀,烧结NdFeB腐蚀具有典型的晶间腐蚀特征。烧结NdFeB腐蚀机理主要分为电化学机理和化学机理,一般情况下,这两种腐蚀机理很难截然分开,经常一起对烧结NdFeB的腐蚀起作用。烧结NdFeB中富Nd相的腐蚀电位远小于Nd2Fe14B主相的电位,热力学上讲磁体在酸、碱、盐等腐蚀介质中发生电化学腐蚀,其中富Nd主相作为阳极区域优先溶解或腐蚀,腐蚀过程如图2所示。在干燥纯氧的环境下,烧结NdFeB氧化腐蚀过程与环境温度有关。研究发现,在190℃富Nd相与氧反应生成Nd2O3;230℃主相与氧反应生成Nd2O3、Fe、B;生成的Fe在400℃又与氧反应,形成Fe2O3。反应过程可用下列公式表示。氧蚀始于磁体表面,后向内部扩展,腐蚀过程中氧沿晶界扩散,受富Nd晶界相的分布形态影响。在湿热环境下,烧结NdFeB的富Nd晶界相与H2O反应,有H生成并沿晶界相向磁体内部扩散(在高温或高压的条件下,H向主相中扩散),生成的H与富Nd相反应,生成NdH3,晶界区域体积膨胀产生晶界应力,导致晶界相破坏,使Nd2Fe14B主相颗粒从磁体中剥离、脱落下来,严重时晶界发生断裂,使磁体粉化。烧结NdFeB氢蚀与磁体中稀土含量及分布状况有关,磁体中Nd含量增加,腐蚀速度升高,在晶粒磁化取向垂直的外表面腐蚀最快。环境湿度也是影响NdFeB磁体腐蚀行为的重要因素,在干燥的氧化环境中,磁体表面可形成较致密的腐蚀产物薄膜,一定程度上将磁体与环境分隔开,能阻止磁体内部的腐蚀;但是在潮湿的环境中,磁体表面可能生成氢氧化物或其它含氢化合物,这些腐蚀产物不具备隔离保护作用,随着环境湿度增大,尤其是磁体表面有液态水存在时,可能引发电化学腐蚀。烧结NdFeB抗蚀性能的影响因素如下:1.富Nd相的影响富Nd相网状分布在烧结NdFeB的晶界和晶界接隅处,起到磁隔离作用,保证磁体具有良好的永磁性能。但是根据腐蚀机理,活泼的富Nd却易导致磁体发生晶间腐蚀。在介质环境中,富Nd相与NdFeB主相之间形成电偶效应,加速磁体腐蚀速度,因此富Nd相的数量和分布决定了磁体本征抗蚀能力。研究表明,Nd含量越少,磁体腐蚀速度越小,抗蚀性能越好;富Nd相均匀分布在三角晶界处,能有效抑制磁体发生晶界腐蚀。2.微观结构的影响烧结NdFeB的微观结构也是影响磁体本征抗蚀性的重要因素,磁体具有多相结构,各相的化学稳定性不同,富Nd晶界相易于腐蚀。如果磁体不致密,孔隙率大,磁体内部会吸收大量的氢,导致富Nd相吸氢腐蚀,晶界变得疏松,使NdFeB的表面难于形成保护膜,这会加速晶界区域中富Nd相的氧化,同时会引起连锁反应,可能会加速相邻富Nd相的氧化。烧结NdFeB中主相的体积分数一般在85%以上,使磁体形成腐蚀原电池时,具有小阳极大阴极的特点。因此,富Nd相的腐蚀电流密度较大,会加速烧结磁体发生晶间腐蚀。另外,磁体主相颗粒尺寸也对抗蚀性能有明显的影响,磁体晶粒尺寸增大,烧结钦铁硼磁体抗腐蚀性降低,磁体晶粒尺寸减小,烧结钦铁硼磁体抗腐蚀性提高。3.环境介质的影响烧结NdFeB磁体的腐蚀行为与使用环境密切相关,受环境中酸、碱、盐、高温、高湿介质的影响显著。烧结NdFeB中富Nd晶界活泼、电极电位低的特点,决定了磁体易晶间腐蚀,因此只有提高晶界相的化学稳定性,改善晶界相的分布,才能提高磁体的抗蚀性。根据合金腐蚀理论,向烧结NdFeB中掺合金元素能降低晶界相的活性,提高富Nd相的腐蚀电位,缩小晶界相与主相间的电位差,减小磁体腐蚀的动力。合金化是提高烧结钦铁硼抗蚀性的重要途径,其中元素掺杂有两种方式:一则是磁体组元熔炼时添加(熔炼添加);二则是混粉添加合金元素(晶界添加)。本发明采用晶界添加,即在气流磨制作细粉时,提高氧含量,在钕铁硼磁粉表面起到一定的钝化作用。基于以上对腐蚀机理和影响因素的了解,针对R14客户的低失重要求:≤1.2mg/cm2,设计了35SH低失重实验。35SH低失重实验的配方同量产35K,实验工艺参数与量产35K的主要区别为:一、气流磨时提高了氧含量(由200-400ppm提高到800-900ppm);二、提高分级轮转速(由4200rpm到4900rpm),即减小粉末粒度。制备出符合目标要求的磁体,磁体密度7.57g/cm3,通过控制和完善制粉工艺,烧结温度,时间等工艺参数,从而提高磁体样片的Hcj,以期达到Hcj≥23kOe的要求,从而开发研究出满足预期目标的35SH磁体。具体参数对比见下表:表1:量产35K和实验35SH过程工艺参数对比所采用的的原材料为金属PrNd、纯铁、镝铁(Dy含量约78%)、纯铜、纯铝和硼铁合金(含硼约18%)。采用真空熔炼工艺制成钕铁硼合金铸片。钕铁硼合金铸片在室温下饱和吸氢,并在580℃脱氢制成氢爆粉,通过气流磨工艺制成平均粒度为3.2μm的磁粉。磁粉在1.8T磁场中垂直取向压制成型后,放入高真空烧结炉内1030~1039℃烧结5h,经一次回火900℃保温4.5h,二级回火480-600℃保温4h,制得钕铁硼磁体。磁体采用NIM-10000磁性材料测量系统测试磁性能,磁体氧含量测定采用了IRO-I红外氧含量测定仪。磁体密度用阿基米德排水法测试。采用金相显微镜和电子扫描镜分析磁体显微组织。高压加速腐蚀实验又称失重实验,能有效地测试材料在湿热环境中的抗蚀性能,是判定材料抗蚀性强弱的重要方法。磁体腐蚀状况用腐蚀一段时间后,单位面积的质量损失来表示,Mloss=(M前-M后)/S。实验采用了PCT高压加速寿命实验机,实验前用电子天平(精度0.1mg)称出试样的质量,然后把待测样品放进实验机中,保证样品对准测试槽的圆形孔,减少实验误差,样品放置完毕,设置实验参数(温度130℃、相对湿度95%、压力2.6atm)并启动程序,腐蚀168h后取出腐蚀样品放入干燥箱内进行烘干处理,清理掉腐蚀产物,并称腐蚀后样品的质量。根据公式计算出腐蚀后磁体单位面积的质量损失。从理论上讲,永磁体的剩磁(Br)和磁能积(BH)max由下式决定式中A是正向畴体积分数;β是非磁性相体积分数;(1-β)是主相的体积分数;d是烧结磁体实际密度;d0是磁体的理论密度;cosθ是Nd2Fe14B晶粒c轴沿取向轴的取向因子或取向度;Js是Nd2Fe14B化合物单晶饱和磁极化强度;μrec为永磁体的回复导磁率。显然,要得到高磁能积的永磁体,首先必须围绕如何提高烧结磁体的取向度、主相Nd2Fe14B的体积分数以及磁体的致密度等环节来设计合理的合金成分和制作工艺。但为了得到具有足够高矫顽力的烧结Nd-Fe-B永磁体,磁体必须含有一定比例的富Nd相。因为在烧结磁体中,富Nd相分布在主相晶粒边界周围,起着对主相晶粒的去磁耦合作用;另外,富Nd相在烧结过程中呈液态,对于磁体的致密化和显微组织的均匀化起着重要作用。烧结Nd-Fe-B磁体中除主相和富Nd相外,还有富B相、氧化物相、气孔以及其它杂质相。由于通常的烧结Nd-Fe-B磁体中含有0.1%量级(质量分数)的氧,而氧又对磁体的磁性能有着重大影响,因此完全有必要将其当成Nd-Fe-B中的一个重要的合金元素来考虑。为制造高磁能积烧结Nd-Fe-B系永磁材料,应注意如下几个关键技术:(l)成分设计时,应尽量接近四方相(主相)的化学计量成分。为使磁体具有一定Hcj值,应使其净Nd含量大于或等于28%(质量分数)。(2)晶粒取向度应大于96%。(3)相对密度应达0.995。(4)由于高磁能积烧结永磁体的成分已接近Nd2Fe14B成分,随主相体积分数增加,烧结磁体矫顽力将会降低。为使在主相体积分数高的情况下,矫顽力不降低,务必使有限的富Nd相充分地分散,使每一个Nd2Fe14B晶粒被一层厚度约2nm富Nd相层包围,尽量减少第Ⅱ种类型边界。要做到这一点,首先应从细化铸锭组织开始。我们知道,Nd-Fe-B铸锭晶以片状晶形式生长,在片状晶边界上有富Nd相分布,片状晶尺寸越小,富Nd相越分散,这样就为制造高磁能积Nd-Fe-B烧结磁体打下基础。烧结NdFeB永磁材料的技术参量可分为非结构敏感参量(即内禀磁参量,如饱和磁化强度Ms、居里温度Tc等),和结构敏感参量(如剩磁Br、矫顽力Hcb或Hcj、磁能积(BH)m等)。前者主要由材料的化学成分和晶体结构所决定;后者除了与内禀参量有关外,还与晶粒尺寸、磁畴取向、晶体缺陷、掺杂物等因素有关。本设计的基本合金成分为:(PrNd)29.28Fe65.16M4.53B1.03,M=Dy、Cu、Al等。实验35SH配方与量产35K配方相同,配方如表2所示:表2:35K和35SH配方∑REPrNdBAlCuDyCo35K及35SH配方相同31-3328-310.95-1.050.5-10-0.13-40.2-0.8溶炼的目的是将纯金属料(Fe、Nd、B-Fe、Dy、Al、Co、Cu等)熔化,并确保合金液"清、准、均、净"。熔炼的原材料要有较高的纯度,防止杂质在熔炼过程中造成大量的烟气和炉渣。熔炼过程中要控制好熔炼功率和真空度,以减少元素的挥发,避免炉料氧化,从而提高熔炼的回收率。目前,生产中常用的铸锭技术为速凝鳞片铸锭技术。它是将熔炼的溶液以一定流速和流量饶注到具有一定转速的水冷铜辊上,这种方法可以将铸锭的厚度大大降低。在成分相同的情况下,片铸技术较传统的铸锭技术有很大优势。铸片可完全不含a-Fe,具有明显的柱状晶,并且柱状晶均匀细小,富Nd相分布更均匀,氧含量低,对以后的制粉、取向和烧结都有重要的意义。在铸片贴近辊面附近存在细小等轴晶会影响磁体的性能,所以应尽可能减少贴辊面细小等轴晶所占比例。最佳铸片组织的获得和熔体温度、熔体流速、流嘴与辊面的间距、辊子的结构和材质、冷却水的温度和流量、辊子的转速等因素有关。在本实验中,以国内生产烧结钕铁硼磁体通用的Pr-Nd、Dy-Fe、Fe、Nb-Fe、Co、Al、Cu和B-Fe为原材料,其中,Pr-Nd纯度大于99%,Pr含量为25%,Dy-Fe中Dy含量为78%,B-Fe中B含量为18.3~20.4%。应用额定装炉数量为600kg的FMI-Ⅱ-600R-C型真空速凝炉制备钕铁硼合金铸片,浇铸温度1460℃±5℃,铜辊转速44rpm。生产钕铁硼合金铸片的工艺过程如图3所示。图4是35SH钕铁硼合金铸片平行于冷却方向截面的SEM背散射电子像,图中灰色部分为Nd2Fe14B主相,白色部分为富Nd相。对于厚度为0.15~0.45mm的钕铁硼合金铸片(图4),其主相以片状晶方式沿冷却方向生长,富Nd相呈薄层状较为均匀地分布在主相内部及晶界处,薄层间距约为3~5μm,并且显微组织中无a-Fe相存在,整个钕铁硼合金铸片显微组织比较均匀。图5、图6、图7、图8为35SH钕铁硼合金铸片的金相照片,平均柱状晶尺寸为4.54μm、4.59μm、4.42μm、4.39μm。35SH钕铁硼合金铸片厚度测试结果的过程能力直方分布图如图9所示,公司所定甩片标准:(0.15-0.45)mm的数量比例≥95%;大于0.45mm的数量比例≤2.0%;小于0.15mm的数量比例≤2.0%。35SH合金甩片厚度测试结果合格,符合标准要求。当钕铁硼合金铸片厚度大于0.45mm时,靠近自由面处会有黑色的a-Fe枝晶存在。a-Fe枝晶的存在是因为当冷却速度较低时,Nd2Fe14B主相主要通过包品反应生成。当温度低于液相线温度,首先从液相中析出γ-Fe,当温度到达包晶反应温度时,发生γ-Fe+L>T1+L'包晶反应,其中部分主相以γ-Fe枝晶为基底形核,并将γ-Fe包围,使液相与γ-Fe相脱离,之后包晶反应只能靠原子扩散完成。由于扩散反应速度很慢,所以一旦形成γ-Fe,很难在随后的凝固过程中消除,当温度继续降低,γ-Fe相转变为a-Fe相。厚度为0.15~0.45mm的样品,由于厚度薄,冷却速度快,组织中未观察到有a-Fe相出现。这是由于当冷却速度较快时,溶液温度迅速降低到包晶反应线以下,来不及形成γ-Fe,包晶反应也被抑制,直接从合金液中结晶出主相,所以没有a-Fe相生成。铸片的厚度直接影响着其显微组织。当厚度过大时,铸片显微组织中会出现枝状a-Fe相,a-Fe相是软磁相,它的析出导致了主相的减少和富Nd相的增加,使硬磁性能降低;另外a-Fe相具有较高的初性,在气流磨制粉时会影响粉末的可破碎性,使粉末粒度分布恶化,并且影响随后的取向过程,使最终磁体的取向度下降。铸片越薄,冷却速度也越快,被富Nd相隔开的片状晶粒越小,同时避免了a-Fe相的产生,但如果过薄,片状晶粒尺寸将小于磨粉时的粉末粒度,将影响磁体的晶粒取向。当铸片厚度在0.15~0.45mm之间,组织中无a-Fe相出现,主相晶粒被富Nd相薄层均匀分隔成3~5μm的片状晶,制粉时可以获得单晶粉末颗粒,有利于优化取向度,提高Br,是比较理想的显微组织结构。烧结钕铁硼磁体铸锭吸氢后会形成氢化物使铸锭爆裂,我们称其为氢碎。氢碎处理时,富稀土相首先氢化,然后是基体相氢化,前者引起晶界断裂,后者引起晶间断裂。氢破碎处理可将钕铁硼铸锭破碎成45~355μm大小的颗粒,其中大部分是125μm左右的颗粒。图7所示为XZHD-1000氢破碎炉,与传统的机械破碎法相比,由于富钕相首先氢化,因此氢破碎过程中的断裂大部分是晶界断裂,这样可以提高单晶颗粒的比例,有利于磁场取向和富Nd相在晶界的分布,从而有效提高了烧结钕铁硼磁体的性能。氢碎粉是十分脆的氢化物,经过简单粗破就可直接进入气流磨,提高气流磨制备合金粉末的效率。另外,氢碎粉降低了制造过程中各阶段的氧含量,而且在真空炉中烧结时,炉中产生的氢气还可减少坯体氧化。氢碎能否实现,受合金表面状态、氢气量的多少、氢气的扩散速度、充入的氢气压力、温度等诸多因素的影响。气流磨制粉原理是利用高压气流将粉末颗粒加速到超声速,使之相互碰撞而粉碎,已破碎的颗粒随上升气流通过分选机进行分离,大于规定尺寸的颗粒返回破碎区继续破碎,小于规定尺寸的粉末送到高速旋风分离器进行分离,尺寸过小的颗粒被分离掉,在合格范围内的粉末从出料口排出。图10为对撞式可控气流磨制粉机理图。制备出的磁粉的颗粒形状、颗粒大小、粒度分布、松装密度和流动性等因素对烧结铁硼磁体粉末的磁场取向与成型、烧结过程以及最终的磁体性能都有显著的影响。形状规则的粉末颗粒在磁场取向过程中造成的机械阻力较小,磁场取向度高,而且其流动性好,对提高压坯的密度有利。形状比较复杂的粉末,其流动性不如球形粉末好,但对提高制品的压坯强度有利。粉末的粒度越小,则烧结驱动力越大,有助于获得致密的组织,同时粉末粒度分布越窄,越容易在烧结时获得均匀一致的晶粒组织,从而获得高性能磁体。气流磨制粉时要根据每台气流磨的特点,按照生产工艺的要求,通过控制分选轮转速来控制粉末粒度及其分布。本实验中量产35K的分级轮转速控制在4200rpm,实验35SH的分级轮转速控制在4900rpm,气流磨所得35K粉末粒度及其分布图如图11所示,气流磨所得35SH粉末粒度及其分布图如图12所示。从气流磨出来的粉料是不均匀的,有三个不均匀性:第一是成分不均匀,先出来的粉料成分和后出来的粉料有所不同。第二是粉末颗粒尺寸不均匀,先出来的粉料颗粒尺寸偏小,后出来的粉料尺寸偏大。第三是粉末颗粒形状不均匀。这三种不均匀性对后续工艺和磁体产品质量的均匀一致性有重要的影响。因此,要对JM出来的粉料进行混料处理,使粉末体的成分、尺寸、颗粒外形从总体上达到均匀一致。35K混粉后的粉末SEM照片如图13所示。从图中可以看出,细粉颗粒形状不规则,粉末颗粒大小分布不均匀,有突出的棱角,标注出来的颗粒直径分别为2.33μm、2.75μm、4.31μm、5.35μm。图14、图15、图16、图17、图18、图19、图20、图21分别为35K和35SH细粉颗粒在1000倍、2000倍、4000倍、8000倍的倍率下的对比SEM照片,从图14、图15、图16、图17、图18、图19、图20、图21可以看出,35K粉末比35SH粉末颗粒粗大,颗粒棱角明显,颗粒表面超细粉颗粒附着较少,而35SH粉末颗粒较细,颗粒表面突出棱角较少,颗粒表面附着的超细粉较多。生产中常使用模压加冷等静压方式进行粉末成型。磁场取向应尽可能使每个颗粒易磁化轴沿磁场方向保持一致,提高取向度,使磁体达到最佳性能。粉末颗粒的取向度与取向磁场强度,粉末颗粒形状与尺寸,取向粉末初始密度,成型方式等因素有关。通常细小磁粉颗粒为单晶多畴,颗粒间相互作用易形成二次粉末颗粒,使流动性变差,为打破粉末团聚,使其沿磁场方向取向,取向磁场应大于单畴粒表面场1.5T。为了提高粉末的取向度添加0.3%的JC1添加剂,用三维立体混料机混料2小时后进行压制,压制称粉过程采用氮气保护,压机为SKH45V1530/16/A自动压机,取向磁场≥1.5T,保压2-5s,成型后进行冷等静压,等静压压力为200MPa,然后进行剪料入炉。等静压时,压坯完全浸没在油液中,压坯各个方向受到液体压力相等,且无外摩擦作用,可以保持较好的取向度。表3:量产35K和实验35SH压坯收缩比对比图22、23、24、25、26、27为量产35K和实验35SH压坯不同方向收缩比的I-MR控制图,从图上可以看出,35SH模具方向和压制方向收缩比较35K略微变小,35K取向方向收缩比较35SH略微变大,收缩比的变化在正常波动范围之内。烧结是将压坯加热到粉末基体相熔点以下的某一温度,进行一段时间的热处理的工艺过程。其过程中包括了粉末颗粒表面吸附气体的排除,有机物的挥发,应力的消除,粉末颗粒表面氧化物的还原,变形粉末颗粒的回复和再结晶,接着是原子的扩散和物质的迁移,颗粒间由机械接触转化为物理化学接触,形成金属键或共价键,晶粒的长大,密度提高等一系列物理化学变化。烧结是制造钕铁硼磁体的关键技术之一,烧结时的升温速度,烧结温度,保温时间及冷却速度等工艺参数对最终磁体的性能有重要的影响。不同成分设计和不同铸锭组织及粉末粒度分布的压坯具有不同的烧结工艺参数。在烧结过程中应选择合理的烧结温度和保温时间,以确保烧结钕铁硼磁体的显微组织的均匀致密,晶粒无异常长大显现象,使磁体具备最佳的性能。烧结钕铁硼磁体烧结并快冷后磁性能较低,通过回火处理可显著提高其磁性能,尤其是矫顽力。回火处理通常有一级回火和二级回火两种,合理的回火温度和回火时间可以改善富Nd相在晶界的分布状态,更好的去除晶粒间的磁交换耦合作用,提高磁体的内部矫顽力,并且使其退磁曲线方形度也得到改善。压坯是许多粉末颗粒的机械堆积体,它的相对密度仅有60-70%,其中内部的空隙很大,强度低。事实证明粉末的压结体的磁性能很低。经过烧结后,磁体的密度可增加94-98%。烧结时,由于原子的扩散,使不同的粉末颗粒彼此融合在一起,而形成一个整体。烧结后的磁体不仅致密度增加,它的机械强度、剩磁Br、矫顽力Hcj和磁能积(BH)max等都大大的提高。所以烧结是十分重要的工序。采用真空气淬烧结炉烧结,先抽真空至10-2Pa时开始加热,待真空度重新达到10-2Pa后再充氩气烧结。烧结工艺路线如图28所示。实验35SH找温度结果如下图所示:图29为35SH在不同烧结温度下烧结态Br箱线图,从图29的Br的箱线图可以看出,35SH磁体的最佳烧结温度为1039℃。理应再往上找烧结温度,找到性能下降的点方可。图30为35SH在不同烧结温度下烧结态(BH)m的箱线图,从图30中(BH)m的箱线图可以看出,35SH磁体的最佳烧结温度为1030℃-1039℃。图31为35SH在不同烧结温度和回火温度下烧结态Hcj的箱线图,从图31中可以看出,当烧结温度为1039℃,回火温度为560℃时的Hcj最佳。35SH最佳磁性能数据如下表4所示,可以看出粒度变小,Br减小,Hcj增大;35SH磁体比重为7.57g/cm3,C含量为0.053%,O:4195ppm;35K磁体比重为7.54g/cm3,C含量为0.083%,O:3506ppm。以上分析可知,35SH的最佳烧结温度为1030℃-1039℃+900℃+560℃,量产35K的烧结回火温度为1039℃+900℃+560℃。表4:最佳烧结温度下35SH的磁性能数据及量产35K磁性能数据从图32、33、34和35的金相照片可以看出,晶粒尺寸在6.0μm-6.53μm之间,晶粒尺寸分布均匀,无晶粒长大现象发生。这点也可以从磁体的SEM照片看出,如图36所示。本实验的目标是降低35SH的失重,以下是失重情况对比表:表5:35K及35SH失重对比的分析失重分析小结:一、本次实验客户要求失重≤1.2mg/cm2,相对于量产产品,实验35SH已有很大改善;二、从以上数据可以看出,实验35SH基体加工为不同的规格,做不同的处理时,所得失重不同:a、当规格为D10*10mm时,酸洗样品失重效果(1.77mg/cm2)略优于未酸洗样品(2.04mg/cm2),主要原因是D10*10柱子的圆柱面是经过无心磨加工,机加工过程中在磁体的表面会形成疏松层,如图37、38、39、40、41、42所示,微观比表面积较大,在酸洗的过程中,硝酸会腐蚀掉部分疏松层,使得圆柱的微观比表面积减小,这样有利于降低失重率;b、当规格为10*10*10时,恰好相反,未酸洗的样品失重为0mg/cm2,失重优于酸洗方块0.61mg/cm2,远远优于圆柱样品的失重。分析认为,产生这种现象的主要原因是,未酸洗方块是经过六面抛光的样品,它的微观比表面积已经得到最大程度的减小,样品表面平整、光滑。而酸洗方块是把六面抛光的样品又酸洗了一下,相当于把样品表面又腐蚀了一下,使其表面因为酸洗凹凸不平,又增大了其微观比表面积。如图43、44所示,酸洗可以使磁体表面形成凹凸不平的小丘峦,因为优先腐蚀晶界相。综上所述,在材料相同的条件下,样品失重与样品的微观比表面积直接相关,半成品基体表面越光滑,越平整,比表面积越小,则失重率越低。抛光是物理的办法使得磁体表面更光滑;在存在机加工疏松层的情况下,酸洗洗掉部分表层疏松层,用化学的方法使得基体表面更光滑。建议:在材料条件无法改变的情况下,①.做失重的样品,要想失重率低,若是经过机加工的样品,建议酸洗以降低其失重率;②.若是六面抛光的样品,不必酸洗,直接做失重,效果最佳。通过对现有量产35K工艺参数的调整,即提高氧含量和减小粉末粒度,达到了显著降低磁体失重的目的,磁体质量损失由的51.56mg/cm2降低至1.77-2.04mg/cm2。通过对不同制样方法的摸索,使得磁体失重趋于0mg/cm2(原理分析参见失重分析小结),完全达到客户的失重目标≤1.2mg/cm2。本次实验目标完成。从显微组织照片可以看出,35K粉末比35SH粉末颗粒粗大,颗粒棱角明显,颗粒表面超细粉颗粒附着较少,而35SH粉末颗粒较细,颗粒表面突出棱角较少,颗粒表面附着的超细粉较多。这与实际情况相符,35SH的SMD为3.21μm,35K粉末的SMD为3.43μm。35SH压制后,模具方向和压制方向的收缩比较35K略微较小,取向方向的收缩比较35K略微增大,对模具稍作调整即可达到正常要求尺寸。对35SH找温度后发现,35SH的最佳烧结温度为1030℃-1039℃,最佳回火温度为900℃+560℃,量产35K的烧结回火温度为1039℃+900℃+560℃。气流磨制备出粒径越细小、尺寸更分布均匀的粉末,钕铁硼合金粉末的烧结活性越大,更易烧结致密化,这样可降低磁体致密化所需烧结温度。故实验35SH的烧结温度(1030℃-1039℃)较量产35K(1039℃)低。粒径更细小的粉末所制作的烧结钕铁硼磁体主相晶粒更细,磁体Hcj就越高;粒径更细小、尺寸分布更均匀的粉末使得在烧结过程中液态的富钕相有更多的毛细通道自由流动,使得分布于主相晶粒边界的富钕相更加细薄、均匀,这不仅可提高磁体的各项磁性能指标,同时可显著改善磁体的耐腐蚀性,本实验进行了有力的验证。同时由于氧含量的增加,使得磁体合金成分中的稀土总量减少,这进一步的提高了磁体的耐腐蚀性。但是我认为用提高氧含量的方法来提高磁体的耐腐蚀性这一途径不可取,治标不治本,这样制备的磁体在后加工时比较脆,有可能是氧脆导致的,类似于氢脆原理。钕铁硼的腐蚀性与富钕相的分布最紧密,因为优先腐蚀富钕相,故可以减小富钕相快速腐蚀的方法均可有效提高磁体的抗腐蚀性。尽管本发明的实施方案已公开如上,但其并不仅仅限于说明书和实施方式中所列运用,它完全可以被适用于各种适合本发明的领域,对于熟悉本领域的人员而言,可容易地实现另外的修改,因此在不背离权利要求及等同范围所限定的一般概念下,本发明并不限于特定的细节和这里示出与描述的图例。当前第1页1 2 3