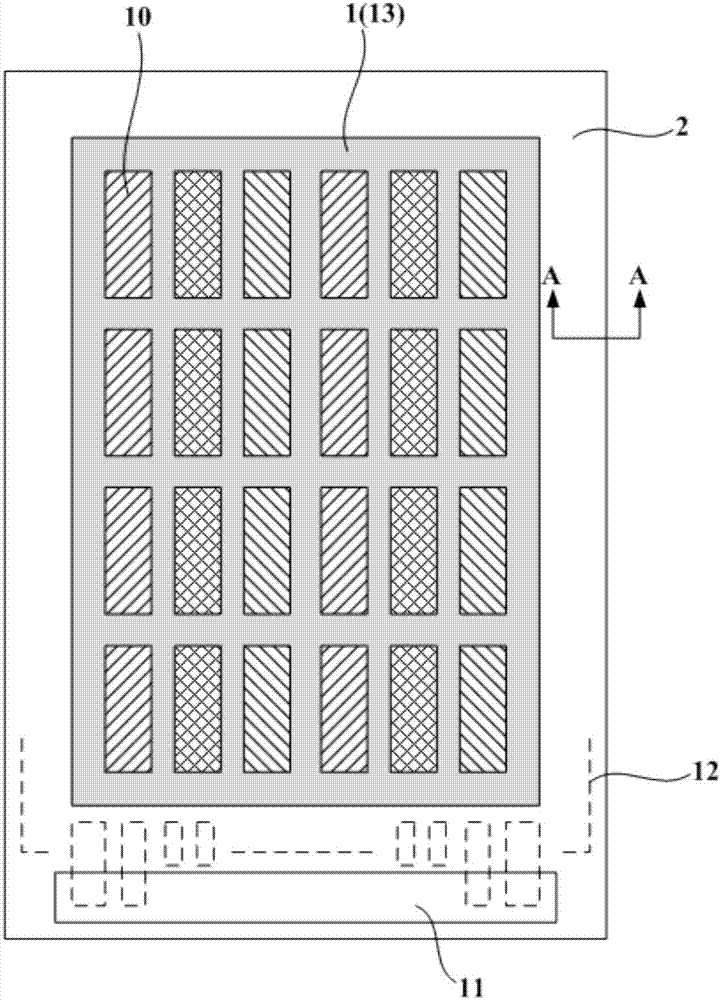
本发明涉及显示
技术领域:
,特别是涉及一种oled(organiclight-emittingdiode,有机发光二极管,简称oled)显示基板及其制作方法、oled显示装置。
背景技术:
:oled显示装置,由于具有薄、轻、宽视角、主动发光、发光颜色连续可调、成本低、响应速度快、能耗小、驱动电压低、工作温度范围宽、生产工艺简单、发光效率高及可柔性显示等优点,已被列为极具发展前景的下一代显示技术。研究表明,空气中的水汽和氧气等成分对oled显示装置中oled器件的寿命影响很大,这是因为:oled器件工作时需要从阴极注入电子,这就要求阴极功函数越低越好,但阴极通常采用铝、镁、钙等金属材质,化学性质比较活波,极易与渗透进来的水汽和氧气发生反应。另外,水汽和氧气还会与oled器件的空穴传输层以及电子传输层发生化学反应,这些反应都会引起oled器件的失效。因此对oled器件进行有效的封装,使oled器件的各功能层与大气中的水汽、氧气等成分充分隔开,就可以大大延长oled器件的寿命,从而延长oled显示装置的使用寿命。目前,oled显示装置的显示基板(截面结构如图1所示)在制作时,普遍采用tfe(thinfilmencapsulation,薄膜封装,简称tfe)技术。具体工艺步骤如下:在形成有oled器件阵列01的基板周边形成两道挡墙02;在两道挡墙02和oled器件阵列01之上形成封装结构层。该封装结构层包括:形成于两道挡墙02和oled器件阵列01之上的第一无机封装层03,形成于第一无机封装层03之上的有机封装层04,形成于有机封装层04之上的第二无机封装层05,其中,有机封装层04一般采用ijp(ink-jetprinting,喷墨打印,ijp)工艺形成于两道挡墙02的内侧,两道挡墙02的预先形成对有机封装层04具有阻隔作用。本申请的发明人在实现本申请过程中发现,当oled显示基板应用于柔性oled显示装置或者曲面oled显示装置时,挡墙02和封装结构层之间在弯曲处存在较大的弯曲应力,极易产生层断裂或剥离,从而使水汽和氧气沿着缝隙进入oled器件,造成oled器件失效。因此,如何提高oled显示装置的弯曲可靠性,延长oled显示装置的使用寿命是目前亟待解决的技术问题。技术实现要素:本发明实施例的目的是提供一种oled显示基板及其制作方法、oled显示装置,以提高oled显示装置的弯曲可靠性,延长oled显示装置的使用寿命。本发明实施例所提供的oled显示基板,包括显示区域和围绕所述显示区域的非显示区域,所述oled显示基板包括设置于所述非显示区域的挡墙,以及覆盖所述显示区域并延伸至覆盖所述挡墙的封装结构层,所述oled显示基板还包括位于所述挡墙和所述封装结构层之间且至少覆盖所述挡墙的金属卤化物层。在挡墙和封装结构层之间增加金属卤化物层,金属卤化物层与挡墙之间,以及与封装结构层之间均具有较好的界面结合力,从而减少了oled显示基板边缘的断裂或剥层,进而能够有效防止水汽和氧气进入oled显示基板内部侵蚀oled器件。相比现有技术,采用本发明实施例技术方案,提高了oled显示装置的弯曲可靠性,延长oled显示装置的使用寿命。可选的,所述金属卤化物层的材质包括mgf2、alf3、naf和lif中的至少一种。优选的,所述金属卤化物层远离所述显示区域的边缘超出所述封装结构层的边缘。采用该设计,封装结构层的边缘只与金属卤化物层结合且结合紧密,从而进一步保障了封装效果。较佳的,所述金属卤化物层远离所述显示区域的边缘超出所述封装结构层边缘10~50微米。这样,不但保障了封装效果,而且金属卤化物层和封装结构层的制作工艺也比较容易管控。较佳的,所述金属卤化物层包括覆盖所述显示区域的第一部分,以及位于所述非显示区域的第二部分,所述第二部分环绕所述第一部分并与所述第一部分间隔设置。金属卤化物层包括不连续的第一部分和第二部分,相当于设置了两道屏障,即使第一部分与封装结构层之间产生间隙导致水汽和氧气进入,但由于第一部分和第二部分不连续,因此,水汽和氧气会止步于第一部分,而无法进一步进入显示区域侵蚀oled器件。此外,第一部分和第二部分不连续,还可以减小oled显示基板的弯曲应力,从而进一步提高oled显示基板的弯曲可靠性。可选的,所述oled显示基板在所述非显示区域还包括依次设置的第一金属走线层、绝缘层、第二金属走线层和第三金属走线层,其中:所述绝缘层具有通向所述第一金属走线层的第一过孔;所述第二金属走线层通过所述第一过孔与所述第一金属走线层电连接;所述挡墙设置于所述第二金属走线层远离所述绝缘层的一侧;所述第三金属走线层位于所述挡墙靠近所述显示区域一侧,并与所述第二金属走线层电连接;所述金属卤化物层还覆盖所述第三金属走线层,以及所述第二金属走线层被所述第三金属走线层和所述挡墙暴露出的部分。较佳的,所述oled显示基板包括设置于所述显示区域的多个oled器件,以及每个所述oled器件所对应电连接的薄膜晶体管;所述第一金属走线层与所述薄膜晶体管的源漏极同层制作;所述第二金属走线层与所述oled器件的阳极同层制作;所述第三金属走线层与所述oled器件的阴极同层制作。较佳的,所述绝缘层为有机绝缘层,所述第二金属走线层具有通向所述有机绝缘层的至少一个第二过孔,所述显示基板还包括与所述挡墙同层制作且填充所述至少一个第二过孔的填充结构。有机绝缘层制作后通常需要将其中的溶剂挥发完毕,否则可能导致基板出现气泡、分层或剥离,采用该技术方案,有机绝缘层中的溶剂可以在第二金属走线层制作过程中通过第二过孔挥发,有机绝缘层与第二金属走线层可以先后连续制作,从而简化了基板的制程,提高了制作产能。填充结构填充第二过孔,可以减少第二金属走线层在制作第三金属走线层之前被氧化,从而提高了产品品质。具体的,所述oled显示基板在所述非显示区域还包括依次设置的柔性衬底基板、缓冲层、栅绝缘层和层间绝缘层;所述第一金属走线层、所述绝缘层、所述第二金属走线层、所述挡墙、所述第三金属走线层、所述金属卤化物层和所述封装结构层依次形成于所述层间绝缘层之上。本发明实施例还提供一种oled显示装置,包括前述任一技术方案所述的oled显示基板。该oled显示装置的弯曲可靠性较佳,使用寿命较长。本发明实施例还提供一种oled显示基板的制作方法,包括:形成位于非显示区域的挡墙;形成至少覆盖所述挡墙的金属卤化物层;在所述金属卤化物层远离所述挡墙的一侧形成覆盖显示区域并延伸至覆盖所述挡墙的封装结构层。具体的,所述方法包括:在基板上形成位于非显示区域的第一金属走线层;在所述第一金属走线层之上形成绝缘层,所述绝缘层具有通向所述第一金属走线层的第一过孔;在所述绝缘层之上形成位于非显示区域的第二金属走线层,所述第二金属走线层通过所述第一过孔与所述第一金属走线层电连接;在所述第二金属走线层之上形成位于非显示区域的挡墙;在所述挡墙的层结构之上形成位于非显示区域的第三金属走线层,所述第三金属走线层位于所述挡墙靠近显示区域的一侧并与所述第二金属走线层电连接;在所述第三金属层之上形金属卤化物层,所述金属卤化物层覆盖所述挡墙、所述第三金属走线层,以及所述第二金属走线层被所述第三金属走线层和所述挡墙暴露出的部分;在所述金属卤化物层之上形成覆盖显示区域并延伸至覆盖所述挡墙的封装结构层。采用上述实施例方法制作的oled显示基板,金属卤化物层与挡墙之间,以及与封装结构层之间均具有较好的界面结合力,从而减少了oled显示基板边缘的断裂或剥层,进而能够有效防止水汽和氧气进入oled显示基板内部侵蚀oled器件。因此,采用该制作方法,提高了oled显示装置的弯曲可靠性,延长oled显示装置的使用寿命。附图说明图1为现有技术oled显示基板截面示意图;图2为本发明一实施例oled显示基板俯视图;图3为图2的a-a处截面示意图;图4为本发明一实施例中金属卤化物层俯视图;图5为本发明一实施例oled显示基板制作方法流程图。附图标记:现有技术部分:01-oled器件阵列;02-挡墙;03-第一无机封装层;04-有机封装层;05-第二无机封装层。本发明实施例部分:1-显示区域;2-非显示区域;281-挡墙;31-封装结构层;30-金属卤化物层;301-第一部分;302-第二部分;25-第一金属走线层;26-绝缘层;23-栅绝缘层;27-第二金属走线层;29-第三金属走线层;282-填充结构;21-柔性衬底基板;22-缓冲层;24-层间绝缘层;311-第一无机封装层;312-有机封装层;12-走线结构;313-第二无机封装层;10-oled器件;11-绑定连接结构;13-像素定义层;32-有机覆盖层。具体实施方式为了提高oled显示装置的弯曲可靠性,延长oled显示装置的使用寿命,本发明实施例提供了一种oled显示基板及其制作方法、oled显示装置。为使本发明的目的、技术方案和优点更加清楚,以下举实施例对本发明作进一步详细说明。如图2和图3所示,本发明实施例提供了一种oled显示基板,包括显示区域1和围绕显示区域1的非显示区域2,oled显示基板包括设置于非显示区域2的挡墙281,以及覆盖显示区域1并延伸至覆盖挡墙281的封装结构层31,此外,oled显示基板还包括位于挡墙281和封装结构层31之间且至少覆盖挡墙281的金属卤化物层30。oled显示基板在显示区域1设置有呈阵列排布的多个oled器件10以及对应控制每个oled器件10工作状态的薄膜晶体管(图中未示出),oled显示基板在非显示区域2设置有绑定连接结构11以及走线结构12。挡墙281、金属卤化物层30和封装结构层31等用于对显示区域1的oled器件10和非显示区域2的走线结构12等进行有效封装。oled器件10的主要结构包括阳极、阴极以及位于阳极和阴极之间的有机发光层,各个oled器件10的阳极和有机发光层通过像素定义层13相互间隔,各个oled器件10的阴极或若干个oled器件10的阴极连为一体结构。通常,挡墙281采用有机材质,例如聚酰亚胺等。封装结构层31包括沿远离柔性衬底基板21方向依次设置的第一无机封装层311、有机封装层312和第二无机封装层313,第一无机封装层311和第二无机封装层313覆盖了挡墙281,有机封装层312位于挡墙281靠近显示区域的内侧。在本发明实施例中,金属卤化物层30的具体材质不限,例如可以包括mgf2、alf3、naf和lif中的至少一种。金属卤化物层30的具体成膜方式不限,优选通过蒸镀工艺形成在基板上。蒸镀工艺是指在一定的真空条件下加热蒸镀材料,使蒸镀材料熔化(或升华)成原子、分子或原子团组成的蒸气,然后凝结在基板表面成膜。在挡墙281和封装结构层31之间增加金属卤化物层30,金属卤化物层30能够与有机材质的挡墙281和无机材质的第一无机封装层311紧密结合,因此,金属卤化物层30与挡墙281之间,以及与封装结构层31之间均具有较好的界面结合力,从而减少了oled显示基板边缘的断裂或剥层,进而能够有效防止水汽和氧气进入oled显示基板内部侵蚀oled器件10。相比现有技术,采用本发明实施例技术方案,提高了oled显示装置的弯曲可靠性,延长oled显示装置的使用寿命。请参照图3所示,该实施例oled显示基板在非显示区域2具体包括以下结构:依次设置的柔性衬底基板21、缓冲层22、栅绝缘层23、层间绝缘层24、第一金属走线层25、绝缘层26、第二金属走线层27、挡墙281、第三金属走线层29、金属卤化物层30和封装结构层31,其中:绝缘层26具有通向第一金属走线层25的第一过孔;第二金属走线层27通过第一过孔与第一金属走线层25电连接;挡墙281设置于第二金属走线层27远离绝缘层26的一侧;第三金属走线层29位于挡墙281靠近显示区域一侧,并与第二金属走线层29电连接;金属卤化物层30还覆盖第三金属走线层29,以及第二金属走线层27被第三金属走线层29和挡墙281暴露出的部分;封装结构层31包括沿远离柔性衬底基板21方向依次设置的第一无机封装层311、有机封装层312和第二无机封装层313,第一无机封装层311和第二无机封装层313覆盖了挡墙281,有机封装层312位于挡墙281靠近显示区域的内侧。在本发明实施例中,优选的,第一金属走线层25与薄膜晶体管的源漏极同层制作;第二金属走线层27与oled器件的阳极同层制作;第三金属走线29层与oled器件的阴极同层制作。第二金属走线层29可以采用ito等材质,第三金属走线层29可以采用mg、ag、ca、al、mno3或ito等材质。第一金属走线层25、第二金属走线层27和第三金属走线层29作为走线结构,用于在显示区域内设置的电子器件与周边区域设置的控制芯片之间传输电信号。采用本发明上述实施例方案,第一金属走线层25、第二金属走线层27和第三金属走线层27无需另外采用构图工艺制作,从而简化了制作工艺,节约了制作成本。较佳的,绝缘层26为有机绝缘层,第二金属走线层27具有通向有机绝缘层的至少一个第二过孔,显示基板还包括与挡墙281同层制作且填充至少一个第二过孔的填充结构282。有机绝缘层制作后通常需要将其中的溶剂挥发完毕,否则可能导致基板出现气泡、分层或剥离,采用该技术方案,有机绝缘层中的溶剂可以在第二金属走线层27制作过程中通过第二过孔挥发,有机绝缘层与第二金属走线层27可以先后连续制作,从而简化了基板的制程,提高了制作产能。填充结构282填充第二过孔,可以减少第二金属走线层27在制作第三金属走线层27之前被氧化,从而提高了产品品质。填充结构282、挡墙281与显示区域的像素定义层可以采用相同材质同层制作,例如,采用聚酰亚胺等有机材质同层制作而成。如图3所示,金属卤化物层30远离显示区域的边缘超出封装结构层31的边缘。采用该设计,金属卤化物层30的边缘部分与层间绝缘层24紧密结合,封装结构层31的边缘部分与金属卤化物层30紧密结合,封装结构层31的边缘部分与层间绝缘层24无直接结合界面,因此有效减少了两者之间剥离的可能,进一步保障了封装效果。较佳的,金属卤化物层30远离显示区域的边缘超出封装结构层31边缘10~50微米。这样,不但保障了封装效果,而且金属卤化物层30和封装结构层31的制作工艺也比较容易管控。较佳的,如图4所示,金属卤化物层30包括覆盖显示区域的第一部分301,以及位于非显示区域的第二部分302,第二部分302环绕第一部分301并与第一部分301间隔设置。金属卤化物层30包括不连续的第一部分301和第二部分302,相当于设置了两道屏障,即使第一部分301与封装结构层31之间产生间隙导致水汽和氧气进入,但由于第一部分301和第二部分302不连续,因此,水汽和氧气会止步于第一部分301,而无法进一步进入显示区域侵蚀oled器件。此外,第一部分301和第二部分302不连续,还可以减小oled显示基板的弯曲应力,从而进一步提高oled显示基板的弯曲可靠性。如图3所示,非显示区域的第三金属走线层29的上表面以及显示区域的oled器件的阴极上表面(该部分图中未示出)还设置有用于提高光取出效率的有机覆盖层32(也称为cpl)。为验证本发明实施例效果,本申请的发明人先后进行了三次界面剥离试验,分别为:试验一、有机覆盖层cpl与sinx无机封装层的界面剥离试验;试验二、有机覆盖层cpl与sionx无机封装层的界面剥离试验;试验三、lif层与sinx无机封装层的界面剥离试验。试验结果如下表一所示:2.0gf/25mm剥离试验2.0gf/25mm百格试验试验一剥离剥离试验二剥离剥离试验三无剥离5b表一界面剥离试验结果对比表可见,金属卤化物层与无机封装层之间具有较好的界面结合力,两者之间不易产生剥离,因此,应用到oled显示基板中,可以有效减少oled显示基板边缘的断裂或剥层。本发明实施例还提供一种oled显示装置,包括前述任一技术方案的oled显示基板。该oled显示装置的弯曲可靠性较佳,使用寿命较长。oled显示装置的具体类型不限,包括但不限于具有曲屏或可弯曲屏的手机、平板电脑、显示器,等等。如图5所示,本发明实施例还提供一种oled显示基板的制作方法,包括:步骤101、形成位于非显示区域的挡墙;步骤102、形成至少覆盖挡墙的金属卤化物层;步骤103、在金属卤化物层远离挡墙的一侧形成覆盖显示区域并延伸至覆盖挡墙的封装结构层。在本发明的一个实施例中,上述方法可具体包括:在基板上形成位于非显示区域的第一金属走线层;在第一金属走线层之上形成绝缘层,绝缘层具有通向第一金属走线层的第一过孔;在绝缘层之上形成位于非显示区域的第二金属走线层,第二金属走线层通过第一过孔与第一金属走线层电连接;在第二金属走线层之上形成位于非显示区域的挡墙;在挡墙的层结构之上形成位于非显示区域的第三金属走线层,第三金属走线层位于挡墙靠近显示区域的一侧并与第二金属走线层电连接;在第三金属层之上形金属卤化物层,金属卤化物层覆盖挡墙、第三金属走线层,以及第二金属走线层被第三金属走线层和挡墙暴露出的部分;在金属卤化物层之上形成覆盖显示区域并延伸至覆盖挡墙的封装结构层。其中,在形成第一金属走线层之前,上述方法还可包括:在柔性衬底基板上形成覆盖非显示区域的缓冲层;在缓冲层之上形成覆盖非显示区域的栅绝缘层;在栅绝缘层之上形成覆盖非显示区域的层间绝缘层。第一金属走线层、绝缘层、第二金属走线层、挡墙、第三金属走线层、金属卤化物层和封装结构层依次形成于层间绝缘层之上。其中,金属卤化物层可采用蒸镀工艺形成。采用上述实施例方法制作的oled显示基板,金属卤化物层与挡墙之间,以及与封装结构层之间均具有较好的界面结合力,从而减少了oled显示基板边缘的断裂或剥层,进而能够有效防止水汽和氧气进入oled显示基板内部侵蚀oled器件。因此,采用该制作方法,提高了oled显示装置的弯曲可靠性,延长oled显示装置的使用寿命。显然,本领域的技术人员可以对本发明进行各种改动和变型而不脱离本发明的精神和范围。这样,倘若本发明的这些修改和变型属于本发明权利要求及其等同技术的范围之内,则本发明也意图包含这些改动和变型在内。当前第1页12