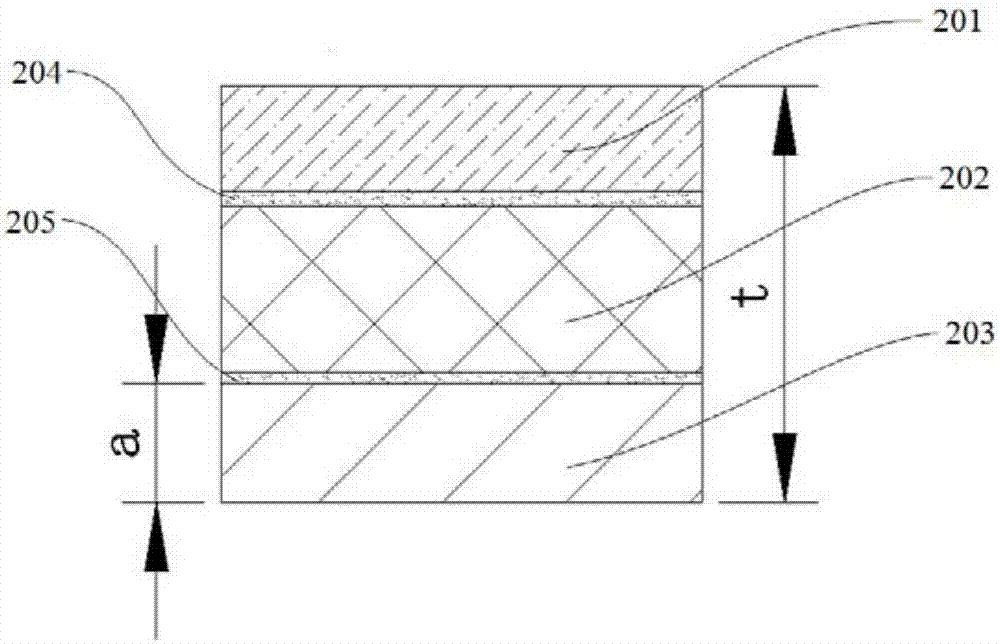
本申请涉及储能材料领域,具体讲,涉及一种二次电池及加热装置。
背景技术:
:随着便携式电子设备的快速发展,对高能量密度电池电源的要求也越来越高,而使用金属壳的外包装材料难以满足便携式电子设备对电池电源轻薄多样的需求。目前采用了软外包装膜作为电池的包装材料,如铝层压膜或者钢层压膜等多层复合膜作为电池的外包装材料。这就要求外包装材料要有长期的可靠性和一定的拉伸性能,在电池长期反复充放电过程中,依然可以保持其结构的稳定性,起到耐磨、隔绝氧气、防潮、绝缘、耐腐蚀等作用,对电池的使用安全有重要的意义。目前市场上有多种规格的铝塑复合膜和不锈钢塑复合膜,以及不同熔点的复合极耳。在复合极耳与复合包装膜封装的过程中,若封装过薄,有短路的风险,若封装过厚,强度不够,有漏液或水分渗透导致电池胀气的风险,影响电池使用安全。鉴于此,特提出本申请。技术实现要素:本申请的首要发明目的在于提出一种二次电池。本申请的第二发明目的在于提出一种加热装置。为了完成本申请的目的,采用的技术方案为:本申请涉及一种二次电池,包括电池元件、复合极耳和外包装层压膜,所述电池元件包括正极极片、负极极片、隔离膜和电解液;其特征在于,所述外包装层压膜用于包装所述电池元件和所述复合极耳,包括依次层叠设置的外部树脂层、金属层和内部树脂层;所述复合极耳包括极耳金属带,所述极耳金属带沿所述极耳金属带的长度方向设置有依次连接的头部空箔区、极耳胶覆盖区以及尾部连接区;所述极耳胶覆盖区上设置有极耳胶,所述尾部连接区用于与所述电池元件连接;所述极耳胶的最外层为熔融树脂层;所述二次电池包括用于密封所述外包装层压膜与所述复合极耳的密封部;所述密封部包括由内至外依次层叠设置的所述极耳金属带、热熔后的所述熔融树脂层、热熔后的所述内部树脂层、所述金属层以及所述外部树脂层;所述外包装层压膜的总厚度为t,所述复合极耳的总厚度为p;所述熔融树脂层的厚度为c,所述内部树脂层厚度为a;所述密封部的厚度为h,h满足以下公式:2t+p-(2c+2a)×95%<h<2t+p-(2c+2a)×5%。优选的,沿所述极耳金属带的长度方向,所述密封部的宽度为0.5~5mm。优选的,沿所述极耳金属带的长度方向,所述极耳胶的宽度大于所述密封部的宽度。优选的,沿所述极耳金属带的长度方向,所述极耳胶露出所述外包装层压膜部分的宽度大于0.1mm。优选的,所述金属层与所述极耳金属带之间任意位置的距离大于15μm。优选的,所述内部树脂层为无规聚丙烯树脂层和/或流延聚丙烯薄膜,所述金属层为铝层和/或不锈钢层,所述外部树脂层为尼龙层和/或聚对苯二甲酸乙二醇酯层。优选的,所述熔融树脂层为聚丙烯层和/或聚乙烯层。优选的,所述外部树脂层与所述金属层之间设置有第一粘合剂层,所述金属层与所述内部树脂层之间设置有第二粘合剂层。本申请还涉及一种加热装置,用于形成密封复合极耳和外包装层压膜的密封部;其特征在于,所述复合极耳包括极耳金属带,所述极耳金属带上设置有极耳胶覆盖区,所述极耳胶覆盖区上设置有最外层为熔融树脂层的极耳胶,所述外包装层压膜包括依次层叠设置的外部树脂层、金属层和内部树脂层;所述加热装置包括至少一对封头组件,一对所述封头组件上均设置有用于形成所述密封部的封头槽,所述封头槽对称设置;所述外包装层压膜的总厚度为t,所述复合极耳的总厚度为p;所述熔融树脂层的厚度为c,所述内部树脂层厚度为a;所述封头槽的深度为L,L满足以下公式:2t+p-(2c+2a)×95%<2L<2t+p-(2c+2a)×5%。优选的,所述封头槽底部的宽度大于所述复合极耳的宽度,所述封头槽口部边缘的倒角为100~160度。本申请的技术方案至少具有以下有益的效果:本申请在对极耳进行封装时,外包装层压膜中的内部树脂层、熔融树脂层之和的热压缩比例为5%~95%,从而可达到更好的熔融效果,保证密封强度高且不发生漏液或渗透。附图说明图1为二次电池的封装示意图;图2为外包装层压膜的剖面结构示意图;图3为复合极耳的正面结构示意图;图4为单层复合极耳的剖面结构示意图;图5为多层单层复合极耳的剖面结构示意图;图6为密封部的剖面结构示意图图7为密封部的正面结构示意图;图8为加热装置与外包装层压膜和复合极耳封装示意图;图9为封头槽的局部示意图;10-电池元件;20-外包装层压膜;201-外部树脂层;202-金属层;203-内部树脂层;204-第一粘合剂层;205-第二粘合剂层;30-复合极耳;301-极耳金属带;301a-头部空箔区;301b-极耳胶覆盖区;301c-尾部连接区;302-极耳胶;302a-熔融树脂层;40-密封部;50-封头组件;501-封头槽。具体实施方式下面结合具体实施例,进一步阐述本申请。应理解,这些实施例仅用于说明本申请而不用于限制本申请的范围。本申请涉及一种二次电池,包括电池元件10、外包装层压膜20和复合极耳30,其中,电池元件10包括正极极片、负极极片、隔离膜和电解液;正极极片包括正极集流体以及涂覆于该正极集流体表面的正极活性物质层,负极极片包括负极集流体以及涂覆于负极集流体表面的负极活性物质层;外包装层压膜20用于包装电池元件10和复合极耳30,即采用外包装层压膜20对电池元件10进行封装。一般工艺为:将外包装层压膜20进行冲压,冲压出电芯槽;将电芯放入电芯槽中,然后进行封装即可,具体如图1所示。在外包装层压膜20与复合极耳30的封装过程中,经热压形成一密封部40。其中,如图2所示为沿外包装层压膜20的表面垂直方向的剖面结构示意图,外包装层压膜20包括依次层叠设置的外部树脂层201、金属层202和内部树脂层203;外部树脂层与金属层202之间设置有第一粘合剂层204,金属层202与内部树脂层203之间设置有第二粘合剂层205。外包装层压膜20在外部树脂层外还可以有亚光层。进一步优选的,内部树脂层203选自无规聚丙烯树脂层和/或CPP膜,金属层202选自铝层和/或不锈钢层,外部树脂层选自尼龙层和/或聚对苯二甲酸乙二醇酯层。复合极耳30作为电连接到电池元件10上并且穿过密封部40分延伸到外部的电极端子,沿极耳金属带301的长度方向设置有依次连接的头部空箔区301a、极耳胶覆盖区301b和尾部连接区301c;极耳胶覆盖区301b上设置有极耳胶302,尾部连接区301c用于与电池元件10连接。具体如图3所示。其中,极耳金属带301的宽度为y。极耳胶302的最外层为熔融树脂层302a。极耳金属带301可选自铝、镍或铜镀镍等材料,熔融树脂层302a可选自聚丙烯层和/或聚乙烯层。具体的,复合极耳30外的树脂层为一层,其沿复合极耳30的表面垂直方向的剖面结构示意图如图4所示;复合极耳30外的树脂层为多层,最外层为熔融树脂层302a,其沿复合极耳30的表面垂直方向的剖面结构示意图如图5所示。当其为多层结构时,不同层的材料熔点有差异,最外层为具有熔融热封效果的树脂层即可。优选的,内层可采用高熔点的材料,从而增强绝缘效果,避免熔融树脂层302a过熔导致极耳金属带301和包装膜的金属层202导通形成电化学腐蚀。封装时,极耳胶302最外层的熔融树脂层302a与外包装层压膜20的内部树脂层203熔融压缩,形成密封部40保证电池的密封。密封部40包括由内至外依次层叠设置的极耳金属带301、热熔后的熔融树脂层302a、热熔后的内部树脂层203、金属层202以及外部树脂层201。在本申请中,外包装层压膜20的总厚度为t,复合极耳30的总厚度为p;外包装层压膜20中内部树脂层203厚度为a,复合极耳30中熔融树脂层302a的厚度为c;密封部40的厚度为h,h满足以下公式:2t+p-(2c+2a)×95%<h<2t+p-(2c+2a)×5%。在本申请的上述公式中,各厚度的单位相同。沿密封部40的表面垂直方向的剖面结构示意图如图6所示,其中,f=a+c。即,本申请在对极耳进行封装时,内部树脂层203与熔融树脂层302a之和的热压缩比例5%~95%,从而可达到更好的熔融效果,保证强度高且不漏液渗透。如果热压缩比例小于5%,密封部40部厚度过薄,有短路的风险;如果热压缩比例大于95%,封装过厚,热压的强度不够,有漏液或水分渗透的风险。进一步优选的,h满足以下公式:2t+p-(2c+2a)×90%<h<2t+p-(2c+2a)×10%。进一步优选的,h满足以下公式:2t+p-(2c+2a)×80%<h<2t+p-(2c+2a)×20%。进一步优选的,h满足以下公式:2t+p-(2c+2a)×70%<h<2t+p-(2c+2a)×30%。即,本申请在对极耳进行封装时,外包装层压膜20中内部树脂层203、熔融树脂层302a之和的热压缩比例10~90%;并进一步优选20~80%,更优选30~70%。在本申请实施例中,如图7所示,沿极耳金属带301的长度方向(L-L’方向),密封部40的宽度d为0.5~5mm。密封部的宽度如果过小,密封效果较差,如果密封不宽度过大,会降低电池能量密度,若封印宽度超过极耳胶片的宽度,则会有腐蚀漏液的风险。在本申请实施例中,如图7所示,沿极耳金属带301的长度方向(L-L’方向),极耳胶302的宽度大于密封部40的宽度,从而保证密封区域不超过极耳胶,避免在密封过程中将外包装层压膜20烫穿,使其中的金属层202与极耳金属带301直接相接,造成短路。进一步优选的,在本申请实施例中,如图6所示,为了避免金属层202与极耳金属带301直接相接,沿极耳金属带301的长度方向,极耳胶302露出外包装层压膜20部分e的宽度大于0.1mm。在本申请实施例中,金属层202与极耳金属带301之间任意位置的距离大于15μm。从而进一步保障了复合极耳30的极耳金属带301与外包装包装膜中的金属层202有一定的绝缘距离,从而避免电化学腐蚀和短路。在本申请实施例中,为了进一步提高密封效果,极耳胶302为至少一层,极耳胶302最外层的熔融树脂层302a的熔点为MP1,内部树脂层203的熔点为MP2,|MP1-MP2|≤15℃。若熔融树脂层302a和内部树脂层203的熔点差异过大,则热封熔融效果差,强度低,有漏液及水分渗透的风险。其中,熔融树脂层302a、内部树脂层203均选用现有已知材料,技术人员根据现有已知材料的熔点选择适宜的材料采用进行制备。进一步优选的,MP2-MP1>0,在热封过程中,外包装层压膜20中内部树脂层203先受热,因此,内部树脂层203采用比熔融树脂层302a的熔点高的材料,从而两者可同时发生软化、熔融,从而进一步提高热封熔融的效果。进一步优选的,MP2-MP1≤10℃,即内部树脂层203比熔融树脂层302a的熔点高10℃以内,进一步提高热封熔融的效果。本申请还涉及一种加热装置,如图8所示,用于形成密封复合极耳30和外包装层压膜20的密封部40。复合极耳30包括极耳金属带301,极耳金属带301上设置有极耳胶覆盖区301b,极耳胶覆盖区301b上设置有最外层为熔融树脂层302a的极耳胶302,外包装层压膜20包括依次层叠设置的外部树脂层201、金属层202和内部树脂层203;加热装置包括至少一对封头组件50,一对封头组件50上均设置有用于形成密封部40的封头槽501,封头槽501对称设置;外包装层压膜20的总厚度为t,复合极耳30的总厚度为p;熔融树脂层302a的厚度为c,内部树脂层203厚度为a;封头槽501的深度为L,L满足以下公式:2t+p-(2c+2a)×95%<2L<2t+p-(2c+2a)×5%。进一步优选的,L满足以下公式:2t+p-(2c+2a)×90%<2L<2t+p-(2c+2a)×10%。进一步优选的,L满足以下公式:2t+p-(2c+2a)×80%<2L<2t+p-(2c+2a)×20%。进一步优选的,L满足以下公式:2t+p-(2c+2a)×70%<2L<2t+p-(2c+2a)×30%。在本申请的加热装置中,图9为图8的局部放大图,封头槽501底部的宽度g大于复合极耳30的宽度y,封头槽501口部的宽度为I;封头槽501口部边缘的倒角r为100~160度。采用该角度的可使热封熔融的树脂可以很好的填充槽位空间,提高封装密封性。在本申请实施例中,正极活性物质层中含有正极活性材料,正极活性材料可选自钴酸锂、锰酸锂、镍钴铝三元材料(NCA)或镍钴锰三元材料(NCM)等;负极活性物质层中含有负极活性材料,负极活性材料可选自石墨或含Si元素的材料。电解液可选用固态、液态、凝胶态电解液。当采用液态电解液或凝胶态电解液时,电池元件10还隔离膜,隔离膜选自聚烯烃隔离膜。实施例正极极片的制备:正极极片包括正极集流体和涂覆在集流体表面的正极活性材料层。正极集流体采用金属箔材,常用的有铝箔。正极活性材料层包括正极活性物质,粘结剂和导电剂。正极活性物质可以是钴酸锂,磷酸铁锂,镍钴锰或镍钴铝,锰酸锂等过渡金属组成的复合氧化物。导电剂可以是炭黑、碳纳米管、碳纤维、石墨烯、导电石墨等导电材料。粘结剂可以使用聚四氟乙烯或者聚(偏二氟乙烯)。溶剂可以采用N-甲基吡咯烷酮(NMP)。以下举例某个配比的正极材料,不限于此混合配比。配制97%的钴酸锂:1.8%的导电炭黑:1.2%的粘结剂聚偏二氟乙烯的正极浆料。将钴酸锂和导电剂先混合均匀,加入溶剂NMP进行均匀分散并加入粘结剂进行调粘制得正极浆料。将正极浆料均匀涂布在集流体表面,接着在高温下干燥除去溶剂,并通过滚压形成一定压实的正极极片。负极极片的制备:负极极片包括负极集流体和涂覆在集流体表面的负极活性材料层。负极集流体采用金属箔材,常用的有铜箔。负极活性材料层包括负极活性物质,粘结剂和导电剂。正极活性物质可以是石墨或含碳的复合物或者是金属机材料,如人造石墨、天然石墨、中间相碳微球、碳纤维、硬碳,硅碳负极,锂负极等。导电剂可以是炭黑、碳纳米管、碳纤维、石墨烯、导电石墨等导电材料。粘结剂可以使用丁苯橡胶或者聚(偏二氟乙烯)。必要时需加增稠剂如羧甲基纤维素钠(CMC)使负极浆料更加稳定,溶剂可以采用N-甲基吡咯烷酮(NMP)或去离子水。以下举例某个配比的负极材料,不限于此混合配比,溶剂为去离子水。配制96.5%的人造石墨:1%的导电炭黑:1.5%的丁苯橡胶:1%的CMC的负极浆料。将石墨和导电炭黑先混合均匀,加入溶剂去离子水作为溶剂和CMC进行均匀分散并加入粘结剂丁苯橡胶进行调粘制得负极浆料。将负极浆料均匀涂布在集流体表面,接着在高温下干燥除去溶剂,并通过滚压形成一定压实的负极极片。电解液的制备:电解液包括电解质盐和有机溶剂,并且另外凝胶电解质也可以使用。作为电解液的有机溶剂例如碳酸二乙酯,碳酸二甲酯,碳酸甲乙酯,碳酸二丙酯,碳酸乙丙酯,碳酸亚丙酯,碳酸亚乙酯,碳酸丙烯酯,丙酸乙酯,丙酸丙酯,亚硫酸丙烯酯等。电解质盐例如LiPF6、LiBF4等。本实施例采用了电解液溶剂配比为50%的丙酸丙酯,25%的碳酸乙烯酯,16%碳酸丙烯酯,6%的乙二腈,碳酸亚乙酯3%,LiPF6锂盐浓度为1.1mol/L。隔膜:采用厚度为8μm孔隙率为30%的多孔聚乙烯薄膜。电池制备:将正负极片进行裁切,负极比正极片宽2mm,在负极片空集流体处引出负极极耳,在正极片空集流体处引出正极极耳,隔离膜宽度比负极宽2.5mm,保证正负极之间有隔离膜绝缘,正极活性材料层对面保证有负极活性材料层包裹,隔膜超出负极两端,将正负极片和隔膜进行卷绕得到电池元件10。如图1将电池元件放入包装袋中进行顶侧封后注入电解液封装完成,化成后抽气封口,形成电池。二次电池的封装:采用t=61μm的铝塑膜作为外包装层压膜,内部树脂层为无规聚丙烯树脂层,金属层为铝层,外部树脂层为尼龙层,铝塑膜的内部树脂层厚度a=24μm;极耳总厚度p=210μm,熔融树脂层c=80μm,为单层CPP层,极耳胶熔融层的总厚度2c=160μm;其中实施例1~5以及对比例1-1~1-4采用铝塑膜与单层极耳胶极耳热封,DSC测试极耳熔融树脂层的最外层的熔点MP1比内部树脂层的熔点MP2均小10℃;使用以上铝塑膜和极耳制作电池进行封装。当没有热封压缩时,即-(2c+2a)=0;hmax=2t+p=61×2+210=332μm;当热封挤压后所有失去所有热封熔融树脂层时,即-(2c+2a)×100%;hmin=2t+p-(2c+2a)=61×2+210-(80×2+24×2)=124μm。通过改变封装封头的温度和压力以及封头槽的深度L,以达到实验对比的目的。制备得到实施例及对比例的密封部厚度如表1所示:表1:以上每个实施例及对比例都形成如上所述的测试电池。检测方法:(1)检测短路:测定正负极之间的电阻,以及正负极耳与铝塑膜金属层的电阻刚封装之后的电池具有足够高的串联电阻,且发生短路时,电阻减少到毫欧级水平。(2)检测漏液和胀气目检电池是否漏液或胀气,并将经过长期循环实验(500次)以后的漏液或胀气情况一并统计在内。(3)循环性能在25℃下,将上述电池,以1C恒流充电至4.4V,然后恒压充电至电流为0.05C,再用0.7C恒流放电至3.0V,此时为首次循环,按照上述条件进行多次循环计算得出锂离子电池循环500次后的容量保持率。循环性能的公式:容量保持=100×(第500次循环的放电容量)/(第一次循环的放电容量)(%)同时测量循环后的厚度膨胀:循环厚度膨胀=100×(第500次循环的满充电池厚度)/(第一次循环的满充电池厚度)(%)相关测试数据参见表2。表2从表2可以看出,实施例1到实施例5在合适封装范围内的不同封装厚度的电池无短路漏液胀气,循环性能优异,容量保持在80%以上,循环膨胀小于10%。对比例1-1由于过热封,封装厚度125μm小于合适范围导致电池短路。短路的原因例如极耳金属带与铝塑膜的金属层发生了接触导致短路。对比例1-2由于热封树脂层熔融不充分,封印区域会有气体和水分通道,封装厚度320μm,大部分电池出现了漏液和胀气现象,其余做长期循环性能不合格,容量保持低,循环膨胀大。当热封熔融的树脂层由于厚度下降到合适范围之外或者热封熔融不完全存在电池内部与外界空气的孔隙通道时,会有空气和水分渗入电池内部,导致电池胀气。对比例1-3由于封装宽度较窄,密封部存在电池内部与外界的水分或者气体的大小毛细通道。对比例中有4个电池在循环前已漏液胀气,其他的在长期循环过程中也出现了循环容量保持低,循环膨胀大的问题。对比例1-4由于封装后极耳胶超出铝塑膜距离小于0.1mm,其中有8支电池出现了短路,原因是极耳金属带和铝塑膜的金属层接触短路。对比例:采用上述二次电池包装材料(外包装层压膜厚度t、铝塑膜的内部树脂层厚度a、极耳总厚度p、熔融树脂层c均与实施例1相同),区别在于对比例2-1~2-5中DSC测试MP2-MP1=20℃,制备得到的密封部厚度如表3所示。并测试其封装后的循环性能,如表4所示。表3表4对比例2-1至2-5中,MP2-MP1=20℃由于熔点差异,导致熔融程度有差异,在封装后熔融界面会有一些熔融不完全导致的孔隙通道。导致初始就有电池漏液和胀气,其他电池在长期循环中也会暴露截面问题,导致漏液胀气。另一实施例:铝塑膜与三层极耳胶极耳热封,DSC测试极耳熔融树脂层的最外层的熔点MP1比内部树脂层的熔点MP2均小10℃;实施例为在封装合格范围内的封装效果,对比例为封装在合格范围之外的电池。采用t=88μm的铝塑膜作为外包装层压膜,内部树脂层为无规聚丙烯树脂层,金属层为铝层,外部树脂层为尼龙层,铝塑膜的内部树脂层厚度a=35μm;极耳总厚度p=270μm,极耳金属带厚度为80μm,极耳胶厚度100μm,熔融树脂层c=35μm,为三层极耳胶结构,极耳胶中间骨架层为熔点较高的树脂层,厚度为25μm,极耳胶熔融层的总厚度2c=70μm。使用以上铝塑膜和极耳制作电池进行封装。当没有热封压缩时,即-(2c+2a)=0;hmax=2t+p=88×2+270=446μm;当热封挤压后所有失去所有热封熔融树脂层时,即-(2c+2a)×100%;hmin=2t+p-(2c+2a)=88×2+270-(35×2+35×2)=306μm。通过改变封装封头的温度和压力以及封头槽的深度L,以达到实验对比的目的。制备得到的密封部厚度如表5所示。并测试其封装后的循环性能,如表6所示。表5编号h(μm)d(mm)e(mm)实施例2-13102>0.1实施例2-23402>0.1实施例2-33702>0.1实施例2-44002>0.1实施例2-54302>0.1对比例3-12802>0.1对比例3-24402>0.1对比例3-33400.5>0.1对比例3-43402<0.1表6从表6可以看出,实施例2-1到实施例2-5在合适封装范围内的不同封装厚度的电池无短路漏液胀气,循环性能优异,容量保持在80%以上,循环膨胀小于10%。对比例3-1由于过热封,封装厚度310μm小于合适范围导致电池漏液。漏液的原因例如极耳金属带与铝塑膜的PP熔融层过热封,骨架层和PP层间产发生了空隙,导致了漏液现象。对比例3-2由于热封树脂层熔融不充分,封印区域会有气体和水分通道,封装厚度440μm,大部分电池出现了漏液和胀气现象,其余做长期循环性能不合格,容量保持低,循环膨胀大。当热封熔融的树脂层由于厚度下降到合适范围之外或者热封熔融不完全存在电池内部与外界空气的孔隙通道时,会有空气和水分渗入电池内部,导致电池胀气。对比例3-3由于封装宽度较窄,密封部存在电池内部与外界的水分或者气体的大小毛细通道。对比例中有3个电池在循环前已漏液胀气,其他的在长期循环过程中也出现了循环容量保持低,循环膨胀大的问题。对比例3-4由于封装后极耳胶超出铝塑膜距离小于0.1mm,其中有5支电池出现了短路,原因是极耳金属带和铝塑膜的金属层接触短路。本申请虽然以较佳实施例公开如上,但并不是用来限定权利要求,任何本领域技术人员在不脱离本申请构思的前提下,都可以做出若干可能的变动和修改,因此本申请的保护范围应当以本申请权利要求所界定的范围为准。当前第1页1 2 3