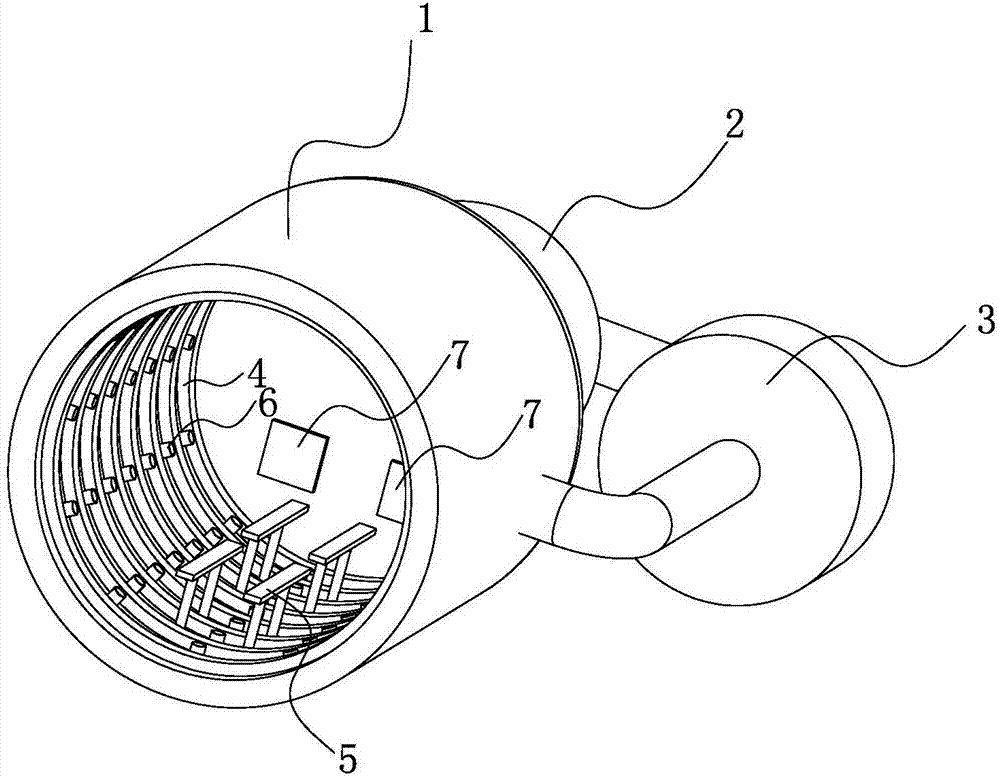
本实用新型涉及一种烧结装置,尤其涉及一种烧结钕铁硼磁体的烧结装置。
背景技术:
:在烧结钕铁硼的生产过程中,经常会遇到较大块产品(1kg以上)烧结,对于较大块产品的烧结在烧结过程中经常出现产品开裂的现象,其原因主要是因为在冷却过程中充入的冷却气体和产品之间冷热差距大,产品受到冷却时热胀冷缩时收缩力很大,但是产品本身受重力和料盒之间存在摩擦阻力作用,摩擦力和收缩力相互作用太大,导致磁体开裂。现有技术中在向产品吹冷却气体时,采用直吹方式,如图1所示,在烧结炉1’上设置带有直吹喷嘴的进气管6’,即产品和冷却气体直接做热交换,若在烧结温度对产品直吹冷却气体,巨大的温差导致产品开裂。为了避免较大损失,冷却方式采用先不充入冷却气体,让产品自然冷却,当降低到中间温度后,再充入冷却气体鼓风冷却,而自然冷却耗时长,大大降低了烧结装置的生产效率,而且钕铁硼的冷却需要快淬,自然冷却在降低冷却速度的同时还降低了此题的磁性能指标,影响产品的质量。技术实现要素:本实用新型所要解决的技术问题是减少现有技术的不足,提供一种能保证产品质量且缩短冷却时间的一种烧结钕铁硼的烧结装置本实用新型解决上述技术问题所采用的技术方案为:一种烧结钕铁硼磁体的烧结装置,包括两两连通的烧结炉、冷却系统和鼓风系统,所述烧结炉的内壁上覆盖有加热层,内壁上还设有用于放置产品的支架,所述烧结炉内壁上安装有进气管,所述烧结炉的内壁和外壁之间设有绝热层,所述进气管的进气端通过总管道贯穿绝热层外壁与鼓风系统在烧结炉外部连通,所述进气管贯穿加热层设置,其特征在于:所述进气管的出气端露出于所述加热层,并且出气端上设有向相反方向的两侧出气的喷嘴,使冷却气体沿内壁周向吹出,所述进气管的出气端与放置在支架上的产品间隔设置,所述进气管的进气端还与外部冷却气体源连通。进一步地,所述加热层包括至少两条环绕烧结炉内壁周向的钼带,所述至少两条钼带之间等间距间隔设置,每条钼带上贯穿的进气管的出气端呈等间距分布。进一步地,所述烧结炉的两端均设有用于将冷却气体排出烧结炉并进入冷却系统的出气口。进一步地,所述烧结炉的炉内真空度为小于10-2Pa,所述进气管的进气端压强范围为100kPa~150kPa。进一步地,所述冷却系统为用于对烧结炉内升温后的冷却气体进行热交换的水冷机构。与现有技术相比,本实用新型的优点在于:本实用新型烧结装置改变进气管的吹气方向,避免冷却气体直接接触产品,本发明的进气管向烧结炉的周向吹气,冷却气体先对加热层冷却,同时冷却气体升温,冷却气体和产品直接形成气体过渡区,减小了冷却气体和产品之间的温度差,有效避免了产品因为温度差距较大而开裂的现象。附图说明图1为现有技术中冷却气体对产品作用的简单结构示意图。图2为本实用新型实施例的烧结钕铁硼磁体的烧结装置的结构示意图。图3为本实用新型烧结钕铁硼磁体的烧结装置中烧结炉的剖视图(含进气管风向示意)。图4为本发明烧结钕铁硼磁体的烧结装置中进气管的出气端示意图(含风向示意)。具体实施方式以下结合附图实施例对本实用新型作进一步详细描述。实施例1:如图2-4所示,本实施例提供一种烧结钕铁硼磁体的烧结装置,包括两两连通的烧结炉1、冷却系统2和鼓风系统3,烧结炉1的内壁上覆盖有加热层4,加热层4包括至少两条环绕烧结炉1内壁周向的钼带,每两条钼带之间等间距间隔设置,每条钼带上贯穿的进气管6的出气端呈等间距分布,内壁上还设有用于放置产品的支架5,烧结炉1内壁安装有进气管6,烧结炉1的内壁和外壁之间为绝热层,进气管6贯穿加热层4设置且在加热层4上呈等间距分布,进气管6的进气端通过总管道贯穿绝热层与鼓风系统3在烧结炉1外部连通,进气管6的出气端露出于加热层4,并且出气端上设有向相反方向的两侧出气的喷嘴,使冷却气体沿内壁周向吹出,进气管6的出气端与放置在支架5上的产品间隔设置,进气管6的进气端还与外部冷却气体源连通。当冷却气体从外部充入烧结炉1内,冷却气体向加热层4吹冷气,冷却气体和产品之间形成了气体过渡区,冷却气体由于先和加热层4进行了热传导,导致气体过渡区的冷却气体升温,降低了冷却气体和产品的温度差,避免出现冷却气体直吹导致产品与冷却气体温差巨大而产生破裂的现象。烧结炉1的炉门和炉底两端均设有出气口7,升温后的冷却气体在鼓风系统的排风作用下通过出去口7进入冷却系统2,通过冷却系统2的水冷机构降温,降低被升温后的冷却气体,通过冷却系统2后的冷却气体进入鼓风系统3,再通过鼓风系统3重新进入烧结炉1用于冷却产品。烧结炉1的在烧结前需要保持真空度,炉内真空度为小于10-2Pa,且对于冷却气体进入进气管的压强范围为100kPa~150kPa。实施例2:一种应用实施例1中的烧结炉烧结钕铁硼磁体的方法,包括步骤如下:将装有5.07kg的产品放入料盒,再将料盒放置在支架上,在产品和料盒之间铺洒氧化铝粉末并且将烧结炉内抽真空至10-2Pa;控制烧结炉内的加热层进行第一阶段升温,升温至250℃并保温2.5h,此阶段对产品进行去油脂处理;控制第二阶段升温,升温至550℃,保温2h,此阶段对产品进行脱气并排出废气;控制第三阶段升温,升温至850℃,保温2.5h;控制第四阶段升温,升温至烧结温度1050℃,保温6h;从外部通过进气管向烧结炉内充入冷却气体,冷却气体的压强为125kPa,同时通过冷却系统的气体热交换和鼓风系统的循环鼓风配合,将产品冷却至500℃;进行一级回火,升温至930℃;再次充入冷却气体,再次冷却至500℃。如表1所示,为实施例2烧结出的产品在冷却过程中的用时以及产品的外观。表1:实施例3:将装有5.07kg的产品放入料盒,再将料盒放置在支架上,在产品和料盒之间铺洒氧化铝粉末并且将烧结炉内抽真空至10-2Pa;控制烧结炉内的加热层进行第一阶段升温,升温至250℃并保温2.5h,此阶段对产品进行去油脂处理;控制第二阶段升温,升温至550℃,保温2h,此阶段对产品进行脱气并排出废气;控制第三阶段升温,升温至850℃,保温2.5h;控制第四阶段升温,升温至烧结温度1100℃,保温6h;从外部通过进气管向烧结炉内充入冷却气体,冷却气体的压强为125kPa,同时通过冷却系统的气体热交换和鼓风系统的循环鼓风配合,将产品冷却至550℃;进行一级回火,升温至930℃;再次充入冷却气体,再次冷却至550℃。如表2所示,为实施例3烧结出的产品在冷却过程中的用时以及产品的外观。表2:实施例4将装有5.07kg的产品放入料盒,再将料盒放置在支架上,在产品和料盒之间铺洒氧化铝粉末并且将烧结炉内抽真空至10-2Pa;控制烧结炉内的加热层进行第一阶段升温,升温至250℃并保温2.5h,此阶段对产品进行去油脂处理;控制第二阶段升温,升温至550℃,保温2h,此阶段对产品进行脱气并排出废气;控制第三阶段升温,升温至850℃,保温2.5h;控制第四阶段升温,升温至烧结温度1070℃,保温6h;从外部通过进气管向烧结炉内充入冷却气体,冷却气体的压强为125kPa,同时通过冷却系统的气体热交换和鼓风系统的循环鼓风配合,将产品冷却至550℃;进行一级回火,升温至900℃;再次充入冷却气体,再次冷却至550℃。如表3所示,为实施例4烧结出的产品在冷却过程中的用时以及产品的外观。表3:以实施例四的实验数据对比采用自然冷却的数据,所需的冷却时间对比如表4所示表4:对自然冷却和实施例4中冷却的产品进行高温热损失对比,将两种产品分别加工成磁化方向相同的方片,在120℃干燥箱内保温,产品到保温之后开始计时,烘烤5h。冷却到室温,测量磁通热损失产品的磁性能对比如表5所示:表5:剩磁Br(kGs)矫顽力Hcj(kOe)方形度HK/Hcj磁通减率自然冷却12.91-13.0617.73-18.260.931-0.9754.81%-7.46%实施例4冷却12.94-13.0718.03-18.650.980-0.9923.57%-4.12%根据表5所示,磁体的剩磁(Br)变化不大,矫顽力(Hcj)提高了0.3-0.39kOe,方形度(HK/Hcj)提高了0.49,从数据分析,采用实施例4的冷却速度有所加快,磁体得到了快淬,磁体内部没有析出杂质相,减少了不必要的结晶,磁体的一致性大大改善。尽管以上详细地描述了本发明的优选实施例,但是应该清楚地理解,对于本领域的技术人员来说,本实用新型可以有各种更改和变化。凡在本实用新型的精神和原则之内所作的任何修改、等同替换、改进等,均应包含在本实用新型的保护范围之内。尽管以上详细地描述了本实用新型的优选实施例,但是应该清楚地理解,对于本领域的技术人员来说,本实用新型可以有各种更改和变化。凡在本实用新型的精神和原则之内所作的任何修改、等同替换、改进等,均应包含在本实用新型的保护范围之内。当前第1页1 2 3