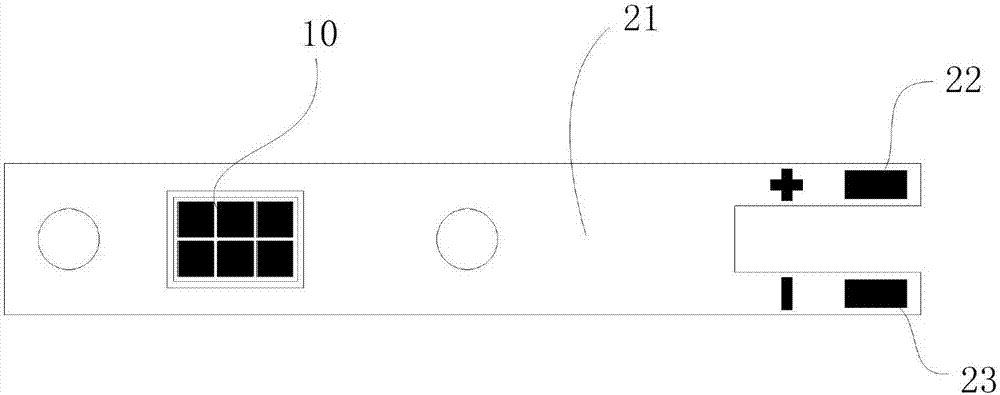
本实用新型涉及汽车照明领域,尤其涉及一种应用于汽车的LED光源模组及结构。
背景技术:
:CSP无金线芯片级封装,基于倒装焊技术,在传统LED芯片封装的基础上,减少了金线封装工艺,省掉导线架、打线,仅留下芯片搭配支架预留空间使用。作为新封装技术,其封装密度增加,封装体积缩小,灯具设计空间更大。倒装无金线芯片凭借更稳定的性能、更好的散热性、更均匀的光色分布、更小的体积,受到越来越多汽车企业使用LED灯具和终端产品应用企业的使用。在现有技术上研究高亮度、低衰减、导热高、高稳定性的光源结构是需要解决的问题。技术实现要素:为了克服现有技术的不足,本实用新型提出一种应用于汽车的LED光源模组及结构,提供了高亮度、低衰减、导热高、高稳定性的光源结构。为了解决上述的技术问题,本实用新型提出的基本技术方案为:一方面,本实用新型提供一种应用于汽车的LED光源模组,包括设置在基板上的固晶区和通过固晶胶固定于所述固晶区的若干LED晶片,所述若干LED晶片之间及周边设置有用于提高亮度的白胶。其中,所述LED晶片为CSP晶片。其中,所述CSP晶片底面的焊接面积不小于所述CSP晶片下底面面积的1/3。其中,所述应用于汽车的LED光源模组还包括用于固定所述CSP晶片的固晶锡膏,当所述CSP晶片的底部完全粘上所述固晶锡膏时,所述CSP晶片的电极间隙处的固晶锡膏不能横向冒出超过20μm,所述CSP晶片四周的固晶锡膏的高度不能超过所述CSP晶片高度的1/3。其中,所述应用于汽车的LED光源模组还包括用于焊接所述CSP晶片的焊盘,所述CSP晶片的电极通过固晶锡膏与所述焊盘焊接。优选的,所述应用于汽车的LED光源模组还包括用于焊接所述CSP晶片的焊盘,以所述CSP晶片上的喷锡层为焊接焊料,在助焊膏的作用下,将所述CSP晶片的电极上的焊料层与所述焊盘焊接。其中,所述助焊膏点涂时满足所述CSP晶片安装后所述助焊膏的膏量在所述CSP晶片高度的1/4到1/3位置。其中,所述焊盘的表面包括喷层。另一方面,本实用新型提供一种包括以上所述的应用于汽车的LED光源模组的光源结构,还包括底板,所述LED光源模组焊接于所述底板上。其中,所述底板成长条形,在所述底板的一端设置有正电极和负电极。本实用新型的有益效果是:本实用新型提供一种应用于汽车的LED光源模组及结构。该模LED光源模组包括设置在基板上的固晶区和通过固晶胶固定于所述固晶区的若干LED晶片,所述若干LED晶片之间及周边设置有用于提高亮度的白胶。在相邻晶片的缝隙之间和四周设置白胶,有效的提升了光源的亮度,使得光源的效率更高,使用体验更佳。附图说明为了更清楚地说明本实用新型实施例中的技术方案,下面将对本实用新型实施例描述中所需要使用的附图作简单的介绍,显而易见地,下面描述中的附图仅仅是本实用新型的一些实施例,对于本领域普通技术人员来讲,在不付出创造性劳动的前提下,还可以根据本实用新型实施例的内容和这些附图获得其他的附图。图1为本实用新型实施例提供的一种应用于汽车的LED光源模组的结构示意图。图2为本实用新型实施例提供的一种应用于汽车的LED光源结构的结构示意图。附图标号说明:标号名称标号名称10LED光源模组11基板12LED晶片13白胶21底板22正电极23负电极具体实施方式下面将结合附图1和图2对本实用新型实施例中的技术方案进行清楚、完整地描述,显然,所描述的实施例仅仅是本实用新型的一部分实施例,而不是全部的实施例。基于本实用新型中的实施例,本领域普通技术人员在没有作出创造性劳动前提下所获得的所有其他实施例,都属于本实用新型保护的范围。需要说明,若本实用新型实施例中有涉及方向性指示(诸如上、下、左、右、前、后……),则该方向性指示仅用于解释在某一特定姿态(如附图所示)下各部件之间的相对位置关系、运动情况等,如果该特定姿态发生改变时,则该方向性指示也相应地随之改变。参照图1,本实施例提供一种应用于汽车的LED光源模组10,包括设置在基板11上的固晶区和通过固晶胶固定于所述固晶区的若干LED晶片12,所述若干LED晶片12之间及周边设置有用于提高亮度的白胶13。本实施例中,所述白胶13为乳白色的单组份有机硅橡胶材料,易于成型,触变性高;白胶13具有高反射、耐黄变、密封性好的作用,在LED晶片12的四周都设置白胶13,挡住LED晶片12四周的发光,使得LED晶片12只能从上表面发光,起到了聚光的作用,有效的提升了光源的亮度,使得光源的效率更高。本实施例中,所述LED晶片12为CSP晶片,CSP为白光芯片,颜色一致性好,简化了点粉工艺。使用CSP晶片在固晶时使用锡膏直接固定芯片,使得光源结构的导热更快,减小了衰减,提高了效率。本实施例中,所述CSP晶片底面的焊接面积不小于所述CSP晶片下底面面积的1/3。本实施例中,所述LED光源模组还包括用于固定所述CSP晶片的固晶锡膏,当所述CSP晶片的底部完全粘上所述固晶锡膏时,所述CSP晶片的电极间隙处的固晶锡膏不能横向冒出超过20μm,所述CSP晶片四周的固晶锡膏的高度不能超过所述CSP晶片高度的1/3。本实施例中,在点涂固晶膏时,因为涂布不均或是膏量没控制好会导致涂布好的固晶膏中有气体产生空洞,为了保证更好的固晶效果,所述固晶膏中的空洞面积应小于8%;且为了防止短路,在点涂固晶胶的时候,应避开LED晶片的电极,使得LED晶片的电极间隙处的固晶膏不能相连,保持20μm的距离。本实施例中,所述LED光源模组还包括用于焊接所述CSP晶片的焊盘,所述CSP晶片的电极通过固晶锡膏与所述焊盘焊接。另一优选的,所述LED光源模组还包括用于焊接所述CSP晶片的焊盘,以所述CSP晶片上的喷锡层为焊接焊料,在助焊膏的作用下,将所述CSP晶片的电极上的焊料层与所述焊盘焊接。本实施例中,所述助焊膏点涂时满足所述CSP晶片安装后所述助焊膏的膏量在所述CSP晶片高度的1/4到1/3位置。本实施例中,所述焊盘的表面包括喷层,所述喷层包括金、银、镍、锡等金属材料。本实施例可以在真空环境或惰性气体保护环境或自然条件下回流焊接,为防止回流过程中晶片电极焊料因长时间高温熔融脱落,倒装时的焊接峰值温度高出回流焊料的15℃-25℃为宜,超出固晶锡膏的共晶熔点的共晶时间应在30-60秒,要定时对各段温度进行检测;晶线路板共晶后晶片的焊接偏移应小于电极焊接面积的5%。参照图2,另一实施例提供一种包括以上实施例所述的应用于汽车的LED光源模组10的光源结构,还包括底板21,所述LED光源模组10焊接于所述底板21上。本实施例中,所述底板21成长条形,在所述底板21的一端设置有正电极22和负电极23。该光源结构还包括设置于所述基板上光源模组10两侧的两个开孔,所述开孔用于安装时固定所述光源结构于汽车上。本实施例提供一种应用于汽车的LED光源模组及结构。该模LED光源模组包括设置在基板上的固晶区和通过固晶胶固定于所述固晶区的若干LED晶片,所述若干LED晶片之间及周边设置有用于提高亮度的白胶。在相邻晶片的缝隙之间和四周设置白胶,有效的提升了光源的亮度,使得光源的效率更高,使用体验更佳。本实施例中,CSP只有两道工艺,固晶点胶,没有传统的焊线工艺,会大比例节省成本,同时提高产品可靠性;颜色一致性提升,由于CSP采用覆晶封装技术封装,光源一致性、集中度、色差范围都会有大提升、优化;散热性能提升,可靠性大幅度提升,整灯散热不在需要以前那么大的散热器,节省成本,增加整灯安全性,舒适性。本实施例中涉及的CSP芯片的固晶焊料,其导热系数在40(W/m.K)-70W(W/m.K)。本实施例中,倒装晶片后不需金线的电路连接,极大程度提高了LED的可靠性能,使LED死灯闪灯降低到20%以下;缩短了LED产品的制造周期,LED倒装制造方法不但减少了LED的金线焊接、减少焊线工时,也同时减少点粉工时,使LED的制造周期缩短到LED封装制造的1/4以内。总之,本实用新型使LED封装与组装的中下游制造成本降低5%-10%;大幅提升了LED的使用寿命;使LED的工作结温降低10-15度;使LED死灯闪灯降低到20%以下;使LED的制造周期缩短2/5。根据上述说明书的揭示和教导,本实用新型所属领域的技术人员还可以对上述实施方式进行变更和修改。因此,本实用新型并不局限于上面揭示和描述的具体实施方式,对本实用新型的一些修改和变更也应当落入本实用新型的权利要求的保护范围内。此外,尽管本说明书中使用了一些特定的术语,但这些术语只是为了方便说明,并不对本实用新型构成任何限制。当前第1页1 2 3