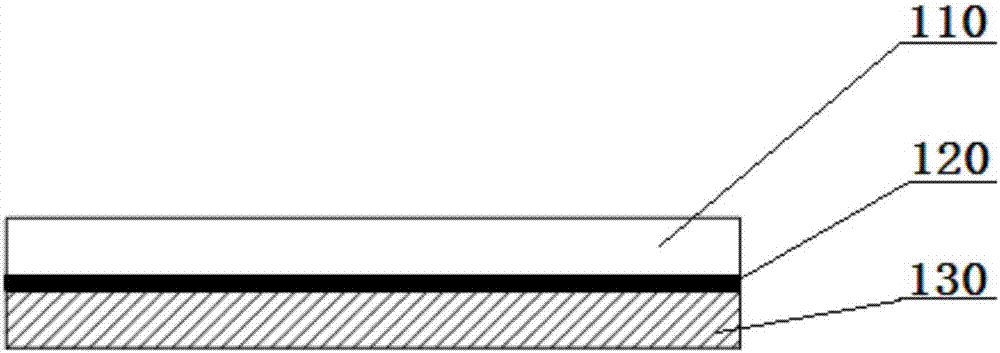
本发明涉及一种预胶接固化粘铆工艺,属于粘铆复合连接工艺领域。
背景技术:
:汽车、轮船、飞机与航天飞船等运输设备的自身重量对其运输性能与成本等指标因素有重要的影响。因此汽车、船舶、飞机、航天等行业需要新型的连接工艺技术,在保证整体刚度与耐撞等性能前提下,用轻质材料替代传统高强度钢等材料,减少自身总重量,实现车身轻量化,降低能源消耗,提高运输效率,减少生产成本。粘铆复合连接技术是实现轻量化的有效途径之一。粘铆复合连接技术是对已胶接的板材进行铆接。粘铆复合连接工艺通过胶层作为绝缘性材料将板材分开,具有良好的抗腐蚀性与连接固定的作用,铆接可以防止胶接突然失效,起到失效缓冲的作用。粘铆复合连接接头的疲劳强度与静力强度比单一接铆接接头或胶接接头高。粘铆复合连接工艺不仅仅应用于金属与非金属连接,还可以应用于非金属于金属连接,非金属与非金属连接。以钢*-铝材料为例,现如今粘铆复合连接的工艺路线是以下两种:1.钢铝板胶接表面预处理——钢铝板胶接——钢铝板粘接接头固化——钢铝板铆接;2.钢铝板胶接表面预处理——钢铝板胶接——钢铝板铆接——钢铝板粘铆接头固化。在上述工艺路线中,钢铝胶接板胶接后的固化度比较低,固化速率与温度有关,在常温下,固化速率低,因此需要添加固化剂在适当的固化温度下进行多次固化,从而提升固化度。胶粘剂的固化温度是有一定的范围的,选择不同的固化温度所对应的固化时间不同。在粘铆复合连接的工艺路线中,铆接与胶接固化的工序是分离的,钢铝板的铆接都是在胶接固化结束,或者在胶接固化之前,上述工艺没有充分考虑胶接固化参数对铆接的影响,没有对铆接最优固化范围进行研究,没有在胶接固化连续时进行铆接。因此,本发明设计了一种在胶接固化进行时铆接的新型连接工艺。技术实现要素:本发明设计开发了一种预胶接固化粘铆工艺,能够克服现有粘铆工艺中胶层固化与铆接工艺分离,在固化达到一定固化度时候进行铆接,铆接完成后进行剩余固化,充分考虑胶接固化参数对铆接工艺所带来的影响的问题。本发明提供的技术方案为:一种预胶接固化粘铆工艺,包括以下步骤:步骤1、将上、下层板料进行除杂预处理,将高分子胶粘剂均匀的涂抹一块板料的一面进行胶接,胶层厚度为0.1~0.3mm,去除板料周围多余的胶粘剂,开始固化,当固化度在0.18~0.45时,停止进行固化,得到胶接板;步骤2、将胶接板放在铆接平台上,压边圈向下运动将被铆接板料进行预压紧,准备进行铆接;步骤3、上、下层板料和胶层受到冲头压力发生变形,上、下层板料相互咬合,在固化度达到1时,胶层固化结束,完成粘铆连接工艺。优选的是,在步骤1中,胶层厚度为0.1mm,并在固化度为0.45时,停止固化。优选的是,所述上、下层板料和胶层在冲头压力及凹模的作用下,相互咬合成燕尾槽状,形成自锁结构。优选的是,进行胶接的两块板材的材质包括:金属和金属板材、金属和非金属板材、非金属和非金属板材。优选的是,所述两块板材的材质分别为低碳钢钢板和铜板。优选的是,所述高分子胶粘剂为环氧树脂胶。优选的是,所述铆接连接工艺进行时的温度与固化温度相同,为80~200℃。本发明所述的有益效果:1、采用预胶接固化粘铆工艺,能够充分缩短整个粘铆复合连接的过程,节省能源,减少工序,还提高粘铆复合连接接头的静态强度和疲劳强度,最终提高接头的完整性、可靠性与耐久性。2、避免对固化度比较低的胶层进行铆接,对固化度比较低的胶层进行铆接,防止板材的铆接位置出现没有胶层形成的问题,无法起到连接固定与绝缘防腐等作用。3、避免对固化度非常高的胶层进行铆接,固化度非常高的胶层进行铆接,胶层连接板材,抵抗板材的变形,使铆接困难,固化度高的粘接剂具有一定的脆性,冲头的冲击会破坏胶层,无法起到板材连接的作用。4、在固化温度下铆接,使粘接剂的自身的物理属性变化,防止出现断裂,更容易承接冲头的冲力,易于胶层参与铆接头的形成。在胶层固化温度下进行铆接,完成胶接固化目的同时使板材在胶接固化温度下塑性变形能力与延展性提高,硬度降低,变形抗力降低,使板料在铆接条件下更加容易成型,从而提高粘铆复合接头质量。附图说明图1为本发明所述的粘铆连接工艺的流程图。图2为本发明所述的已经完成胶接的板材示意图。图3为本发明所述的铆接预压紧示意图。图4为本发明所述的铆接成形示意图。图5为本发明所述的铆接保压示意图。图6为本发明所述的铆接退模示意图。图7为本发明所述的板材完成粘铆复合连接工艺示意图。图8为本发明所述的在固化度过低时进行铆接时的示意图。具体实施方式下面结合附图对本发明做进一步的详细说明,以令本领域技术人员参照说明书文字能够据以实施。如图1所示,本发明提供一种预胶接固化粘铆工艺,包括:实施例1步骤1、在室温下,将上、下层板料进行除杂预处理,将高分子胶粘剂均匀的涂抹在一块板料的一面进行胶接,胶层厚度为0.1~0.3mm,去除板材周围多余的胶粘剂,开始固化;控制固化温度在80~200℃,当固化度在0.18时,停止进行固化,得到胶接板;在该步骤中,上、下层板料的材质可选用金属和金属板料,金属和非金属板料,非金属和非金属板料,作为一种优选,在本发明中,上、下层板料的材质分别为低碳钢钢板和铜板。作为一种优选,本发明中胶层厚度为0.1mm,此厚度的胶层力学性能最佳,因为随着胶层厚度的增加,力学性能逐渐下降。作为一种优选,本发明中固化温度为120℃。作为一种优选,本发明中板料的裁剪尺寸为:板长为100mm,板宽为36mm,板厚为1mm,上、下层板料的搭接长度为35mm。作为一种优选,本发明中高分子胶粘剂选择环氧树脂胶粘剂。步骤2、将胶接板放在铆接平台上,对胶接板材进行定位,将要铆接的位置与凹模和冲头的轴心线在一条直线上,压边圈首先向下运动将被铆接板料进行预压紧,准备进行铆接。步骤3、随着冲头的向下运动,上、下层板料和胶层受到冲头与凹模的联合作用。冲头的端面及圆角、凹模内侧面、凹模端面的特殊形状,促使上、下板料与胶层形成燕尾状自锁的结构;保持固化温度,当冲头运行到下止点位置后,上、下板料将完全填充在冲头与凹模之中,此时将冲头继续保持在下止点位置不动,防止板料发生回弹现象;进行铆接退模,在固化温度下,控制固化时间,当胶层固化度达到1时,胶层固化结束,完成粘铆复合连接工艺。对完成粘铆复合连接工艺的板材进行拉伸试验和剥离试验,得到拉伸最大负载为4.33kn,剥离最大负载为0.71kn。实施例2步骤1、在室温下,将上、下层板料进行除杂预处理,将高分子胶粘剂均匀的涂抹在一块板料的一面进行胶接,胶层厚度为0.1~0.3mm,去除板材周围多余的胶粘剂,开始固化;控制固化温度在80~200℃,当固化度在0.37时,停止进行固化,得到胶接板;在该步骤中,上、下层板料的材质可选用金属和金属板料,金属和非金属板料,非金属和非金属板料,作为一种优选,在本发明中,上、下层板料的材质分别为低碳钢钢板和铜板。作为一种优选,本发明中胶层厚度为0.1mm,此厚度的胶层力学性能最佳,因为随着胶层厚度的增加,力学性能逐渐下降。作为一种优选,本发明中固化温度为120℃。作为一种优选,本发明中板料的裁剪尺寸为:板长为100mm,板宽为36mm,板厚为1mm,上、下层板料的搭接长度为35mm。作为一种优选,本发明中高分子胶粘剂选择环氧树脂胶粘剂。步骤2、将胶接板放在铆接平台上,对胶接板材进行定位,将要铆接的位置与凹模和冲头的轴心线在一条直线上,压边圈首先向下运动将被铆接板料进行预压紧,准备进行铆接。步骤3、随着冲头的向下运动,上、下层板料和胶层受到冲头与凹模的联合作用。冲头的端面及圆角、凹模内侧面、凹模端面的特殊形状,促使上、下板料与胶层形成燕尾状自锁的结构;保持固化温度,当冲头运行到下止点位置后,上、下板料将完全填充在冲头与凹模之中,此时将冲头继续保持在下止点位置不动,防止板料发生回弹现象;进行铆接退模,在固化温度下,控制固化时间,当胶层固化度达到1时,胶层固化结束,完成粘铆复合连接工艺。对完成粘铆复合连接工艺的板材进行拉伸试验和剥离试验,得到拉伸最大负载为4.39kn,剥离最大负载为0.73kn。实施例3步骤1、在室温下,将上、下层板料进行除杂预处理,将高分子胶粘剂均匀的涂抹在一块板料的一面进行胶接,胶层厚度为0.1~0.3mm,去除板材周围多余的胶粘剂,开始固化;控制固化温度为80~200℃,当固化度在0.45时,停止进行固化,得到胶接板;在该步骤中,上、下层板料的材质可选用金属和金属板料,金属和非金属板料,非金属和非金属板料,作为一种优选,在本发明中,上、下层板料的材质分别为低碳钢钢板和铜板。作为一种优选,本发明中胶层厚度为0.1mm,此厚度的胶层力学性能最佳,因为随着胶层厚度的增加,力学性能逐渐下降。作为一种优选,本发明中固化温度为120℃。作为一种优选,本发明中板料的裁剪尺寸为:板长为100mm,板宽为36mm,板厚为1mm,上、下层板料的搭接长度为35mm。作为一种优选,本发明中高分子胶粘剂选择环氧树脂胶粘剂。步骤2、将胶接板放在铆接平台上,对胶接板材进行定位,将要铆接的位置与凹模和冲头的轴心线在一条直线上,压边圈首先向下运动将被铆接板料进行预压紧,准备进行铆接。步骤3、随着冲头的向下运动,上、下层板料和胶层受到冲头与凹模的联合作用。冲头的端面及圆角、凹模内侧面、凹模端面的特殊形状,促使上、下板料与胶层形成燕尾状自锁的结构;保持固化温度,当冲头运行到下止点位置后,上、下板料将完全填充在冲头与凹模之中,此时将冲头继续保持在下止点位置不动,防止板料发生回弹现象;进行铆接退模,在固化温度下,控制固化时间,当胶层固化度达到1时,胶层固化结束,完成粘铆复合连接工艺。对完成粘铆复合连接工艺的板材进行拉伸试验和剥离试验,得到拉伸最大负载为4.51kn,剥离最大负载为0.75kn。对比例1步骤1、在室温下,将上、下层板料进行除杂预处理,将高分子胶粘剂均匀的涂抹一块板料的一面进行胶接,胶层厚度为0.1~0.3mm,去除板材周围多余的胶粘剂,开始固化;控制固化温度为80~200℃,当固化度在0.14时,停止进行固化,得到胶接板;在该步骤中,上、下层板料的材质可选用金属和金属板料,金属和非金属板料,非金属和非金属板料,作为一种优选,在本发明中,上、下层板料的材质分别为低碳钢钢板和铜板。作为一种优选,本发明中胶层厚度为0.1mm,此厚度的胶层力学性能最佳,因为随着胶层厚度的增加,力学性能逐渐下降。作为一种优选,本发明中固化温度为120℃。作为一种优选,本发明中板料的裁剪尺寸为:板长为100mm,板宽为36mm,板厚为1mm,上、下层板料的搭接长度为35mm。作为一种优选,本发明中高分子胶粘剂选择环氧树脂胶粘剂。步骤2、将胶接板放在铆接平台上,对胶接板材进行定位,将要铆接的位置与凹模和冲头的轴心线在一条直线上,压边圈首先向下运动将被铆接板料进行预压紧,准备进行铆接。步骤3、随着冲头的向下运动,上、下层板料和胶层受到冲头与凹模的联合作用。冲头的端面及圆角、凹模内侧面、凹模端面的特殊形状,促使上、下板料与胶层形成燕尾状自锁的结构;保持固化温度,当冲头运行到下止点位置后,上、下板料将完全填充在冲头与凹模之中,此时将冲头继续保持在下止点位置不动,防止板料发生回弹现象;进行铆接退模,在固化温度下,控制固化时间,当胶层固化度达到1时,胶层固化结束,完成粘铆复合连接工艺。对完成粘铆复合连接工艺的板材进行拉伸试验和剥离试验,得到拉伸最大负载为4.23kn,剥离最大负载为0.64kn。对比例2步骤1、在室温下,将上、下层板料进行除杂预处理,将高分子胶粘剂均匀的涂抹一块板料的一面进行胶接,胶层厚度为0.1~0.3mm,去除板材周围多余的胶粘剂,开始固化;控制固化温度为80~200℃,当固化度在0.89时,停止进行固化,得到胶接板;在该步骤中,上、下层板料的材质可选用金属和金属板料,金属和非金属板料,非金属和非金属板料,作为一种优选,在本发明中,上、下层板料的材质分别为低碳钢钢板和铜板。作为一种优选,本发明中胶层厚度为0.1mm,此厚度的胶层力学性能最佳,因为随着胶层厚度的增加,力学性能逐渐下降。作为一种优选,本发明中固化温度为120℃。作为一种优选,本发明中板料的裁剪尺寸为:板长为100mm,板宽为36mm,板厚为1mm,上、下层板料的搭接长度为35mm。作为一种优选,本发明中高分子胶粘剂选择环氧树脂胶粘剂。步骤2、将胶接板放在铆接平台上,对胶接板材进行定位,将要铆接的位置与凹模和冲头的轴心线在一条直线上,压边圈首先向下运动将被铆接板料进行预压紧,准备进行铆接。步骤3、随着冲头的向下运动,上、下层板料和胶层受到冲头与凹模的联合作用。冲头的端面及圆角、凹模内侧面、凹模端面的特殊形状,促使上、下板料与胶层形成燕尾状自锁的结构;保持固化温度,当冲头运行到下止点位置后,上、下板料将完全填充在冲头与凹模之中,此时将冲头继续保持在下止点位置不动,防止板料发生回弹现象;进行铆接退模,在固化温度下,控制固化时间,当胶层固化度达到1时,胶层固化结束,完成粘铆复合连接工艺。对完成粘铆复合连接工艺的板材进行拉伸试验和剥离试验,得到拉伸最大负载为4.21kn,剥离最大负载为0.61kn。对比例3步骤1、在室温下,将上、下层板料进行除杂预处理,将高分子胶粘剂均匀的涂抹一块板料的一面进行胶接,胶层厚度为0.1~0.3mm,去除板材周围多余的胶粘剂,开始固化;控制固化温度为80~200℃,当固化度在0.96时,停止进行固化,得到胶接板;在该步骤中,上、下层板料的材质可选用金属和金属板料,金属和非金属板料,非金属和非金属板料,作为一种优选,在本发明中,上、下层板料的材质分别为低碳钢钢板和铜板。作为一种优选,本发明中胶层厚度为0.1mm,此厚度的胶层力学性能最佳,因为随着胶层厚度的增加,力学性能逐渐下降。作为一种优选,本发明中固化温度为120℃。作为一种优选,板料的裁剪尺寸为:板长为100mm,板宽为36mm,板厚为1mm,上、下层板料的搭接长度为35。作为一种优选,本发明中高分子胶粘剂选择环氧树脂胶粘剂。步骤2、将胶接板放在铆接平台上,对胶接板材进行定位,将要铆接的位置与凹模和冲头的轴心线在一条直线上,压边圈首先向下运动将被铆接板料进行预压紧,准备进行铆接。步骤3、随着冲头的向下运动,上、下层板料和胶层受到冲头与凹模的联合作用。冲头的端面及圆角、凹模内侧面、凹模端面的特殊形状,促使上、下板料与胶层形成燕尾状自锁的结构;保持固化温度,当冲头运行到下止点位置后,上、下板料将完全填充在冲头与凹模之中,此时将冲头继续保持在下止点位置不动,防止板料发生回弹现象;进行铆接退模,在固化温度下,控制固化时间,当胶层固化度达到1时,胶层固化结束,完成粘铆复合连接工艺。对完成粘铆复合连接工艺的板材进行拉伸试验和剥离试验,得到拉伸最大负载为4.22kn,剥离最大负载为0.63kn。表1项目固化度拉伸最大负载p(kn)剥离最大负载p(kn)实施例10.184.330.71实施例20.374.390.73实施例30.454.510.75对比例10.144.230.64对比例20.894.210.61对比例30.964.220.63通过表1可以看出,在板料、胶粘剂、胶层厚度、铆接时的温度等条件相同的情况下,在固化度为0.45时,拉伸最大负载值和剥离最大负载值均大于在其他固化度时所进行的粘铆复合工艺;同时,当固化度在0.18-0.45范围内,拉伸最大负载值和剥离最大负载值大于在其他固化度情况。尽管本发明的实施方案已公开如上,但其并不仅仅限于说明书和实施方式中所列运用,它完全可以被适用于各种适合本发明的领域,对于熟悉本领域的人员而言,可容易地实现另外的修改,因此在不背离权利要求及等同范围所限定的一般概念下,本发明并不限于特定的细节和这里示出与描述的图例。当前第1页12