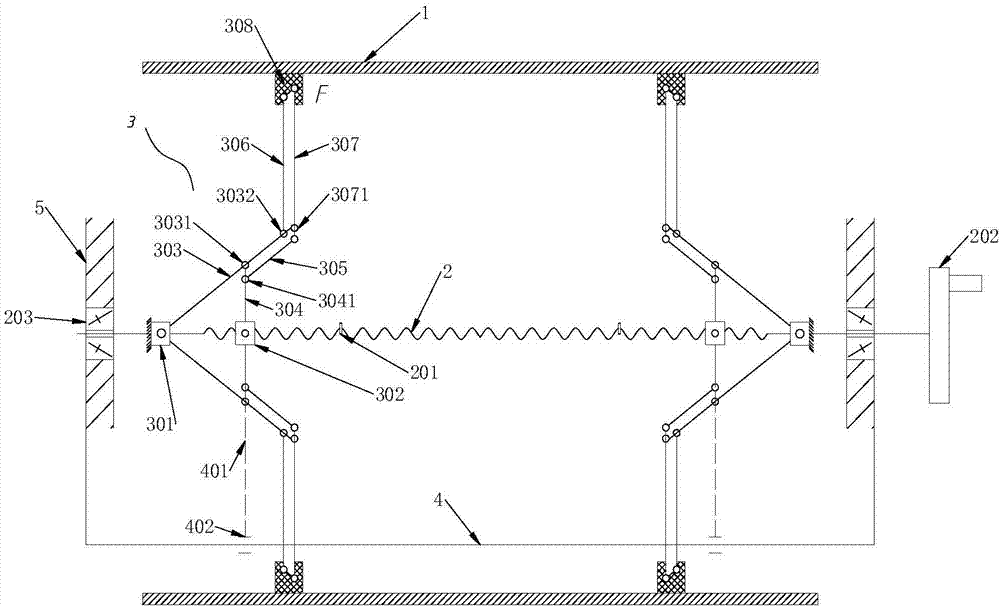
本发明涉及大型筒形件壳体焊接领域,尤其涉及一种大型筒形件壳体平焊过程中保持圆度的装置。
背景技术:
:在大型筒形件壳体平焊过程中,由于焊缝区在高温及重力的影响下,产生了变形下陷,难以保证壳体的圆度要求,降低了壳体的生产效率与生产质量。在生产实践中,需采用一定的定位压紧工装,防止变形下陷,提高壳体圆度。现有技术中常见的液压及电器撑圆工装,结构复杂,且成本较高,不能实现自锁,不能实现快速动作和锁紧。技术实现要素:本发明的目的是解决壳体焊接过程中焊缝区产生变形下陷,难以保证壳体的圆度要求的问题,提供一种大型筒形件壳体平焊过程中保持圆度的装置。为实现上述发明目的,本发明的技术方案是:一种大型筒形件壳体平焊过程中保持圆度的装置,其特征在于,包括丝杆2,丝杆2沿待焊壳体1轴线设置,丝杆2上设有多组撑杆机构3,多组撑杆机构3均以丝杠2为中心,呈辐射状布置;所述撑杆机构3包括固定座301,固定座301套装在所述丝杆2上,所述固定座301的一侧的丝杆2上螺纹连接有螺母302,丝杆2旋转,螺母302沿丝杆2轴线方向移动;所述固定座上连接有第一撑杆303,所述螺母302连接有第二撑杆304,第二撑杆304铰接在所述第一撑杆303的非端部的第一铰接点3031上,第一撑杆303靠近末端的第二铰接点3032铰接有第四撑杆306,所述第二撑杆304非端部的第三铰接点3041铰接有第三撑杆305,第三撑杆305末端铰接有第五撑杆307,所述第一撑杆303的末端铰接在第五撑杆307的非端部的第四铰接点3071上;所述第一铰接点3031、第三铰接点3041、第四铰接点3071、第三撑杆305与第五撑杆307铰接点,四点构成一平行四边形;所述第四撑杆306、第五撑杆307平行设置;所述第四撑杆306、第五撑杆307的末端设有压块308;旋转丝杆2,螺母302沿丝杆2向固定座301方向移动,第二撑杆304推动第一撑杆303,第一撑杆303推动第四撑杆306、第五撑杆307向待焊壳体1靠近,所述压块308压紧在待焊壳体1内表面,撑杆机构3在第三撑杆305作用下达到自锁状态。作为本发明的一种优选,所述压块308具体布置在待焊壳体1上的焊缝101的两侧。作为本发明的另一种优选,所述多组撑杆机构3设置于同一待焊壳体1横截面,多组撑杆机构3同时共用一个固定座301、一个螺母302,多组撑杆机构3受力相等且方向相反,丝杠2所受径向力为零。进一步的,所述丝杠2一侧设有一螺母导杆4,螺母导杆4与丝杠2平行设置,螺母导杆4上设有滑套402通过导向连杆401与所述螺母302连接,丝杠2旋转,螺母302在导向连杆401的牵引下沿丝杠2移动。进一步,所述丝杆2上设有限位挡块201,限位挡块201设于固定座301所在螺母302一侧的相对侧。进一步,所述丝杆2一端设有用于旋转丝杆2的旋转手柄202。更进一步,所述丝杆2通过圆锥轴承203安装在固定支架5上。本发明的有益效果是:1、相比于液压与电气撑圆工装,本发明结构紧凑,操作方便,减少生产成本,提高了大型筒形件壳体的生产质量。2、灵活地运用了滑动丝杆的传动与自锁功能,并结合平行四边形机构,实现了工装的快速压紧与锁紧,同时提高了丝杆及撑杆的强度。附图说明图1为本发明的结构示意图;图2为本发明实施例中五点支撑示意图;图3为本发明撑杆机构几何关系示意图。具体实施方式下面将结合附图对本发明实施例中的技术方案进行清楚、完整地描述。如图1所示,一种大型筒形件壳体平焊过程中保持圆度的装置,包括丝杆2,丝杆2沿壳体1轴线设置,丝杆2上设有十组撑杆机构3,十组撑杆机构3均以丝杠2为中心,呈辐射状布置。本实施例中,如图2所示,以盾构机壳体的平焊为例,包括盾构机的壳体1,壳体1为圆筒状,壳体1上有沿母线方向的焊缝101,壳体1上设有一条焊缝101,采取同时对壳体的两端进行压紧,一端在满足平衡与稳定前提下,采用五点支撑,此时支撑结构最优。所述撑杆机构3包括固定座301,固定座301套装在所述丝杆2上,所述固定座301的一侧的丝杆2上螺纹连接有螺母302,丝杆2旋转,螺母302沿丝杆2轴线方向移动。所述固定座上连接有第一撑杆303,所述螺母302连接有第二撑杆304,第二撑杆304铰接在所述第一撑杆303的非端部的第一铰接点3031上,第一撑杆303靠近末端的第二铰接点3032铰接有第四撑杆306,所述第二撑杆304非端部的第三铰接点3041铰接有第三撑杆305,第三撑杆305末端铰接有第五撑杆307,所述第一撑杆303的末端铰接在第五撑杆307的非端部的第四铰接点3071上;所述第一铰接点3031、第三铰接点3041、第四铰接点3071、第三撑杆305与第五撑杆307铰接点,四点构成一平行四边形;所述第四撑杆306、第五撑杆307平行设置;所述第四撑杆306、第五撑杆307的末端设有压块308;旋转丝杆2,螺母302沿丝杆2向固定座301方向移动,第二撑杆304推动第一撑杆303,第一撑杆303推动第四撑杆306、第五撑杆307向壳体1靠近,所述压块308压紧在壳体1内表面,撑杆机构3在第三撑杆305作用下达到自锁状态。为实现撑杆机构3实现压紧和自锁,需要对各撑杆长度及铰接方式进行设计,设计方法如下:由于五个支点杆结构相同,如图3所示,现取一个撑杆机构结构进行分析;步骤1:确定第一撑杆303、第二撑杆304、第三撑杆305、第四撑杆306、第五撑杆307的长度。将五根撑杆杆由铰链节点划分为l1、l2、l3、l4、l5、l6、l7、l8。(1)l1、l2、、l4、l5、l6、l7长度的确定拟取l1=1620mm,l2=1570mm,l4=450mm,l5=400mm,l6=700mm要能够实现压紧撑圆作用,由几何关系:得:l7=610mm在本实施中,两部分撑杆机构3相对设置,当撑杆机构3展开或收起时,为防止两侧撑杆在运动过程中发生干涉碰撞,保证压块308压紧壳体1内表面上,还需满足:l1+l4+l5+l6<l1+l2L0-(l1+l4+l5)cos(arcsinl2l1)<L2]]>式中:L0为两部分撑杆机构的固定座之间的丝杠长度的一半;L为盾构机壳体轴向长度。且上述杆节点长度均满足:l1+l4+l5+l6<l1+l2L0-(l1+l4+l5)cos(arcsinl2l1)<L2]]>因此取l1=1620mm,l2=1570mm,l4=450mm,l5=400mm,l6=700mm,l7=610mm(2)l3、l8长度的确定由平行四边形关系得:l3=l4+l5=850mml8=l7=610mm;]]>由此可确定第一撑杆303长度为2470mm、第二撑杆304长度为1570mm、第三撑杆305长度为850mm、第四撑杆306长度为610mm、第五撑杆307长度为1310mm。步骤2:确定螺母302的工作行程X。工作行程X需满足:0<X<L0-l1cos(arcsinl2l1)≈600mm]]>在满足工作要求的前提下,减少工作行程X,可在丝杆2上的E点安装限位挡块201,同时也可以防止螺母302过度移动,撑杆机构3与丝杠干涉。确定好点E点位置,即可确定工作行程X。因此可取X=450mm。步骤3:确定丝杆2导程S(1)确定螺母302从初始位置E到压紧状态C1所需旋转手柄202转动圈数N,取N=10,则丝杆2导程S为:S=zp=X/N=45mm式中:采用单线螺纹,则z=1。校核撑杆机构自锁条件:f=ucosβ2≈0.1035]]>ρ=arctanf≈5.9°式中:λ为螺纹升角,d2为丝杆螺纹中径值,取150mm,ρ为摩擦角,u为摩擦系数,取u=0.1,β为螺纹夹角,本发明采用梯形螺纹β=30°由上述公式求得的λ与ρ,满足自锁条件:λ<ρ因此,撑杆机构3在C1点处能够实现压紧壳体1,并自锁。在本实施例中,撑杆机构3分成两部分布置,每部分五组撑杆机构3,五组撑杆机构3设置于同一壳体1横截面,五组撑杆机构3同时共用一个固定座301、一个螺母302,五组撑杆机构3受力相等且方向相反,丝杠2所受径向力为零。每部分,第一组撑杆机构3设置于焊缝101相对的壳体1内表面上,第二组、第三组分别设置在距离焊缝101顺时针90度、逆时针90度的壳体内表面上,第四组、第五组分别设置在焊缝101两侧约8cm处。所述丝杠2一侧设有一螺母导杆4,螺母导杆4与丝杠2平行设置,螺母导杆4上设有滑套402通过导向连杆401与所述螺母302连接,丝杠2旋转,螺母302在导向连杆401的牵引下沿丝杠2移动。所述丝杆2一端设有用于旋转丝杆2的旋转手柄202。所述丝杆2通过圆锥轴承203安装在固定支架5上。通过旋转手柄202,使螺母302在工作行程X内移动,且在C1点时,撑杆机构3压紧壳体并自锁,保持焊接过程中的稳定性,同时压紧壳体,防止其变形。所描述的实施例仅仅是本发明一部分实施例,而不是全部的实施例。基于本发明中的实施例,本领域普通技术人员在没有做出创造性劳动前提下所获得的所有其他实施例,都属于本发明保护的范围。当前第1页1 2 3