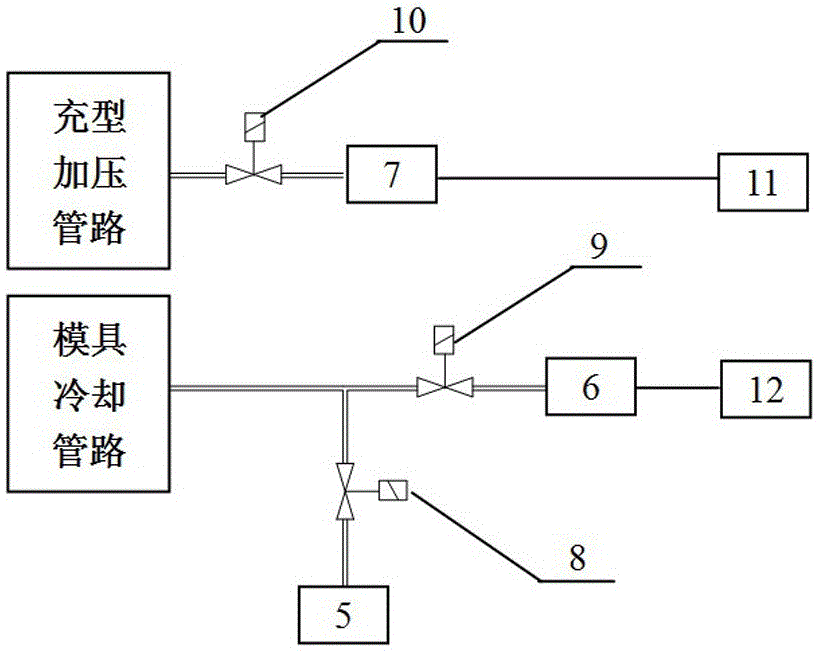
本实用新型涉及一种铝合金铸造设备,具体涉及一种用于铝合金低压或差压铸造工艺的介质传输管路系统。
背景技术:
:在铝合金低压或差压铸造工艺中,一方面,需要采用气体介质进行炉内加压,从而实现对模具型腔充型及作为铸件补缩的介质;另一方面,在充型结束后,需要对模具进行冷却,通常,模具的冷却包括气体冷却和冷却水冷却。现有技术中,如附图1所示,介质管路系统包括一气体输入端1和一冷却水输入端2,所述冷却水输入端2经1#电磁阀3连通至模具冷却管路,所述气体输入端1由三通分为两路,一路经2#电磁阀4连通至模具冷却管路,另一路连通至充型加压管路。因此,在该介质管路系统中,充型加压气体和冷却气体采用同一气体输入端进入管路系统,采用压缩空气进行炉内加压,实现对模具型腔充型及作为铸件补缩的介质。这种方式,会导致铸造过程中铝合金中的活性金属(如:镁、铝)与氧气反应形成氧化渣。形成的氧化渣会粘附在承载铝液的坩埚的内壁,造成坩埚使用寿命缩短;上述氧化渣可能在随后的铸造充型过程中进入到模具型腔内,导致铸件内有氧化夹渣缺陷;同时由于氧化渣的形成会损耗铝液,增加成本。另一方面,由于充型加压管路和模具冷却管路间通过2#电磁阀连接,当气体压力小于冷却水压力,且隔绝气体与冷却水的2#电磁阀发生泄漏时,水管中的水就会窜入充型气体输送管道中,导致管路中的水含量超标,进而造成充型过程中铝合金的氧化形成夹渣。因此,有必要对该介质传输管路系统进行改进,以解决上述问题。技术实现要素:本实用新型的发明目的是提供一种用于铝合金低压或差压铸造的介质管路系统,解决现有技术中压缩空气充型造成的氧化渣问题以及设备故障时易产生水泄漏造成产品夹渣的问题。为达到上述发明目的,本实用新型采用的技术方案是:一种用于铝合金低压或差压铸造的介质管路系统,包括充型加压管路、模具冷却管路、冷却水输入端口,所述冷却水输入端口经第一电磁阀连通所述模具冷却管路,设有第一气体输入端口和第二气体输入端口,所述第一气体输入端口经第二电磁阀连通所述模具冷却管路,所述第二气体输入端口经第三电磁阀连通所述充型气体管路。上述技术方案中,设置第一气体输入端口作为冷却气体入口,设置第二气体输入端口作为充型气体入口,两者之间不存在连通结构,因此可以使用不同的气源,也不会发生冷却水泄漏的问题。进一步的技术方案,分别设有氮气气源和压缩空气气源,所述第一气体输入端口连接压缩空气气源,所述第二气体输入端口连接氮气气源。采用氮气作为充型加压介质,解决了坩埚内壁表面粘附氧化渣的问题,也避免了铸件夹渣的风险。由于上述技术方案运用,本实用新型与现有技术相比具有下列优点:1、本实用新型通过设置两个气体输入端口,使得充型加压气体和模具冷却气体可以使用不同的气源,从而解决了现有技术中使用压缩空气进行充型加压导致的增加铸造产品夹渣缺陷的风险问题;2、本实用新型将充型加压气体管路和模具冷却管路分离,避免了电磁阀泄漏导致的冷却水窜入充型气体的输送管道的可能性。附图说明图1是现有技术的介质管路系统的连接示意图;图2是本实用新型实施例的介质管路系统的连接示意图。其中:1、气体输入端;2、冷却水输入端;3、1#电磁阀;4、2#电磁阀;5、冷却水输入端口;6、第一气体输入端口;7、第二气体输入端口;8、第一电磁阀;9、第二电磁阀;10、第三电磁阀;11、氮气气源;12、压缩空气气源。具体实施方式下面结合附图及实施例对本实用新型作进一步描述:实施例一:一种用于铝合金低压或差压铸造的介质管路系统,参见图2所示,包括充型加压管路、模具冷却管路、冷却水输入端口5、第一气体输入端口6、第二气体输入端口7、氮气气源11和压缩空气气源12。所述冷却水输入端口5经第一电磁阀8连通所述模具冷却管路,所述第一气体输入端口6经第二电磁阀9连通所述模具冷却管路,所述第二气体输入端口7经第三电磁阀10连通所述充型气体管路。所述第一气体输入端口6连接压缩空气气源12,所述第二气体输入端口7连接氮气气源11。进行充型加压时,打开第三电磁阀10,氮气气源11连通充型加压管路。本实施例中使用高纯氮气,高纯氮气的要求如下表所示:项目要求氮气纯度≥99.9%氮气露点温度≤-50℃氮气中的氧气含量<0.1%氮气出口压力0.60-0.65Mpa使用冷却气体冷却时,打开第二电磁阀9,保持第一电磁阀8关闭,压缩空气进入模具冷却管路。使用冷却水冷却时,关闭第二电磁阀9,打开第一电磁阀8,冷却水进入模具冷却管路。当前第1页1 2 3