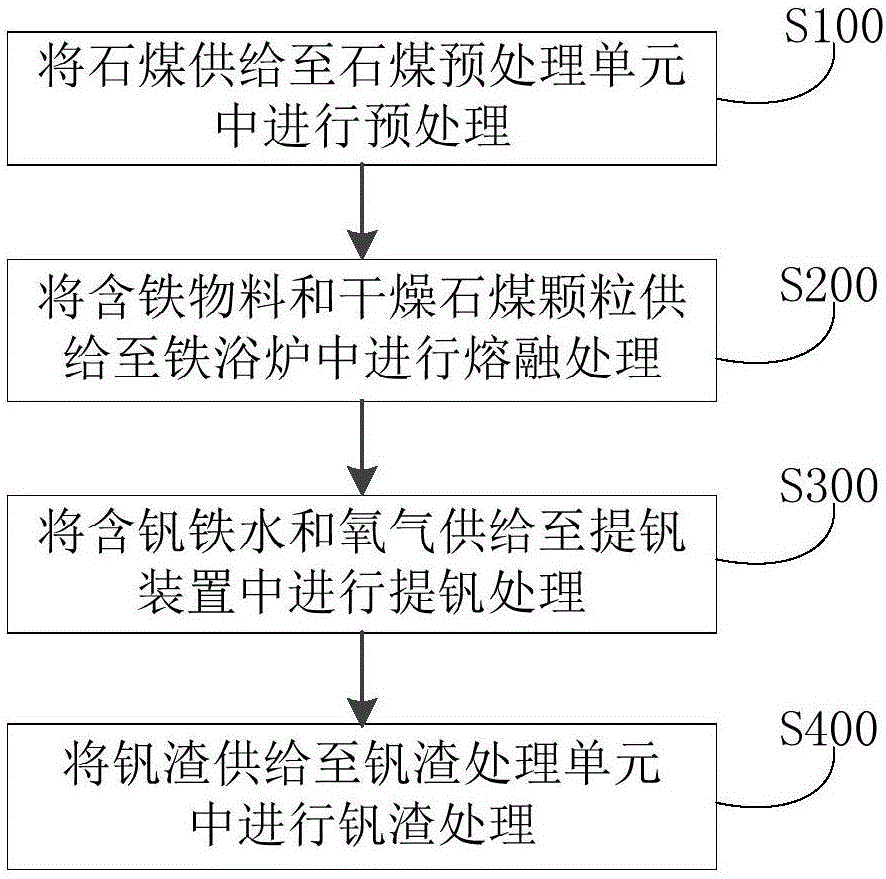
本发明属于冶金领域,具体而言,本发明涉及石煤提钒的系统和方法。
背景技术:
:石煤是一种含碳少、发热值低的劣质无烟煤,又是一种低品位多金属共生矿,石煤资源中已发现的伴生元素多达60多种,其中可形成工业矿床的主要是钒,其次是钼、铀、磷、银等等。我国的石煤资源非常丰富,总储藏量居世界第一位。我国从20世纪60年代开始对石煤提钒进行研究,70年代开始工业生产,所使用的工艺主要分为两大工艺路线,即火法焙烧湿法提钒工艺和全湿法提钒工艺。火法工艺钠化焙烧-水浸或酸浸工艺均为钠化焙烧(NaCl)-水浸或酸浸工艺。这种工艺存在两个严重缺陷,一是为得到较高V2O5浸出率,不得不消耗大量H2SO4,生产中H2SO4用量一般为矿石质量的25%~40%,钒回收率普遍为45%-55%,使50%左右的钒矿资源得不到有效利用而浪费;二是酸性浸出液的净化除杂、Fe(III)还原和pH值调整等工序需要消耗大量药剂,特别是氨水,从而导致氨氮废水的产生及处理问题。尽管攀钢在石煤提钒技术上取得了突破,远远高于国内同行业通常的40%~50%的指标,钒的总收率平均达到60.70%,仍有40%的钒资源浪费。全湿法提钒工艺是将石煤在常压或加温加压及氧化剂存在下酸浸,将酸浸得到的含钒溶液利用萃取、离子交换等工艺进行提钒,因石煤中钒含量低、处理量大,使得酸耗大、污染物排放高、钒产品生产成本高。因此现有石煤提钒的技术有待进一步改进。技术实现要素:本发明旨在至少在一定程度上解决相关技术中的技术问题之一。为此,本发明的一个目的在于提出一种石煤提钒的系统和方法,该系统采用石煤中的碳作为燃料和还原剂加热还原石煤中铁、钒氧化物,综合回收铁、钒有价金属,所得钒渣中五氧化二钒的含量是石煤中五氧化二钒含量的十倍以上,碱耗降低75%以上,且石煤铁氧化物、钒氧化物还原母液可以循环使用,降低石煤提钒生产成本及能源消耗10%以上。在本发明的一个发明,本发明提出了一种石煤提钒的系统。根据本发明的实施例,所述系统包括:石煤预处理单元,所述石煤预处理单元具有石煤入口、烟气出口和干燥石煤颗粒出口;铁浴炉,所述铁浴炉具有含铁物料入口、干燥石煤颗粒入口、含钒铁水出口和高温烟气出口,所述干燥石煤颗粒入口与所述干燥石煤颗粒出口相连,所述高温烟气出口与所述石煤预处理单元相连;提钒装置,所述提钒装置具有含钒铁水入口、氧气入口、半钢出口和钒渣出口,所述含钒铁水入口与所述含钒铁水出口相连,所述半钢出口与所述含铁物料入口相连;钒渣处理单元,所述钒渣处理单元具有钒渣入口和五氧化二钒出口,所述钒渣入口与所述钒渣出口相连。由此,根据本发明实施例的石煤提钒的系统通过将石煤进行预处理,可将石煤中的结晶水、自由水及其他易挥发杂质去掉,得到干燥石煤颗粒,如此,有利于提高后续钒渣中五氧化二钒的含量;在铁浴炉中,干燥石煤颗粒在高温下迅速熔化,期间干燥石煤颗粒中的碳与自身中的铁氧化物和钒氧化物发生还原反应,将三氧化二铁还原为氧化亚铁、氧化亚铁还原为铁、五氧化二钒还原为三氧化二钒,同时干燥石煤颗粒中的碳与熔融后的含铁物料发生渗碳反应,生成饱和碳,该饱和碳释放到熔融后的含铁物料和干燥石煤颗粒的混合熔液中,与其中的铁氧化物、钒氧化物发生还原反应,被充分还原后的钒进入混合熔液中得到含钒铁水。从铁浴炉得到的高温烟气可用于石煤预处理单元中对石煤进行干燥和预热处理,有利于降低石煤预处理单元的能耗,提高系统的经济性;在提钒装置中,含钒铁水在氧气的作用下可得到含五氧化二钒15wt%以上的钒渣,是石煤中五氧化二钒含量的10以上,达到富集钒的目的,所得的半钢可返回至铁浴炉中熔化,用作干燥石煤颗粒熔化时其内的铁氧化物和钒氧化物熔融还原的母液,如此,有利于循环利用提钒装置所得的半钢,且可显著减少铁浴炉中含铁物料的加入量,减少铁浴炉的能耗,进一步提高系统的经济性;在钒渣处理单元中,可将钒渣中的五氧化二钒提出,同时碱耗降低75%以上。整个石煤提钒系统的生产成本及能源消耗降低10%以上。另外,根据本发明上述实施例的石煤提钒的系统,还可以具有如下附加的技术特征:在本发明的一些实施例中,所述石煤预处理单元包括依次相连的破碎装置、干燥装置和预热装置。由此,有利于去除石煤中的水分和杂质,同时加快后续铁浴炉中干燥石煤颗粒的熔化速度,从而提高铁浴炉中的反应速度。在本发明的一些实施例中,所述钒渣处理单元包括依次相连的第一焙烧装置、水浸装置和第二焙烧装置。由此,有利于得到五氧化二钒。在本发明的再一个方面,本发明提出了一种采用上述石煤提钒的系统实施石煤提钒的方法,根据本发明的实施例,该方法包括:(1)将石煤供给至所述石煤预处理单元中进行预处理,以便除去结晶水和自由水,得到干燥石煤颗粒;(2)将含铁物料和所述干燥石煤颗粒供给至所述铁浴炉中进行熔融处理,以便得到含钒铁水和高温烟气,并将所述高温烟气返回步骤(1)中的所述石煤预处理单元;(3)将所述含钒铁水和氧气供给至所述提钒装置中进行提钒处理,以便得到钒渣和半钢,并将所述半钢返回步骤(2)中的所述铁浴炉;(4)将所述钒渣供给至所述钒渣处理单元中进行钒渣处理,以便得到五氧化二钒。由此,根据本发明实施例的石煤提钒的方法通过将石煤进行预处理,可将石煤中的结晶水、自由水及其他易挥发杂质去掉,得到干燥石煤颗粒,如此,有利于提高后续钒渣中五氧化二钒的含量;在铁浴炉中,干燥石煤颗粒在高温下迅速熔化,期间干燥石煤颗粒中的碳与自身中的铁氧化物和钒氧化物发生还原反应,将三氧化二铁还原为氧化亚铁、氧化亚铁还原为铁、五氧化二钒还原为三氧化二钒,同时干燥石煤颗粒中的碳与熔融后的含铁物料发生渗碳反应,生成饱和碳,该饱和碳释放到熔融后的含铁物料和干燥石煤颗粒的混合熔液中,与其中的铁氧化物、钒氧化物发生还原反应,被充分还原后的钒进入混合熔液中得到含钒铁水。从铁浴炉得到的高温烟气可用于石煤预处理单元中对石煤进行干燥和预热处理,有利于降低石煤预处理单元的能耗,提高整体的经济性;在提钒装置中,含钒铁水在氧气的作用下可得到含五氧化二钒15wt%以上的钒渣,是石煤中五氧化二钒含量的十倍以上,达到富集钒渣的目的,所得的半钢可返回至铁浴炉中熔化,用作干燥石煤颗粒熔化时其内的铁氧化物和钒氧化物熔融还原的母液,如此,有利于循环利用提钒装置所得的半钢,且可显著减少铁浴炉中含铁物料的加入量,减少铁浴炉的能耗,进一步提高整体的经济性;在钒渣处理单元中,可将钒渣中的五氧化二钒提出,同时碱耗降低75%以上。整个石煤提钒的方法的生产成本及能源消耗降低10%以上。在本发明的一些实施例中,在步骤(1)中,所述预处理依次包括破碎、干燥和预热处理。由此,有利于去除石煤中的水分和杂质,同时加快后续铁浴炉中干燥石煤颗粒的熔化速度,从而提高铁浴炉中的反应速度。在本发明的一些实施例中,在步骤(1)中,所述干燥石煤颗粒中的粒径为5~15mm的占比80%以上。由此,可进一步加快后续铁浴炉中干燥石煤颗粒的熔化速度,从而提高铁浴炉中的反应速度。在本发明的一些实施例中,在步骤(2)中,所述干燥石煤颗粒与所述含铁物料的质量比为1:(1~2)。由此,可将干燥石煤颗粒中的碳与熔融后的含铁物料充分发生渗碳反应,从而将干燥石煤颗粒中的铁氧化物和钒氧化物充分还原,达到富集钒的目的。在本发明的一些实施例中,在步骤(3)中,所述提钒处理的温度为1350~1420摄氏度。由此,可提高提钒处理的效率。在本发明的一些实施例中,在步骤(4)中,所述钒渣处理依次包括第一焙烧处理、水浸处理和第二焙烧处理。由此,有利于得到五氧化二钒。本发明的附加方面和优点将在下面的描述中部分给出,部分将从下面的描述中变得明显,或通过本发明的实践了解到。附图说明本发明的上述和/或附加的方面和优点从结合下面附图对实施例的描述中将变得明显和容易理解,其中:图1是根据本发明一个实施例的石煤提钒的系统结构示意图;图2是根据本发明一个实施例的石煤提钒的方法流程示意图;图3是根据本发明再一个实施例的石煤提钒的系统结构示意图。具体实施方式下面详细描述本发明的实施例,所述实施例的示例在附图中示出,其中自始至终相同或类似的标号表示相同或类似的元件或具有相同或类似功能的元件。下面通过参考附图描述的实施例是示例性的,旨在用于解释本发明,而不能理解为对本发明的限制。在本发明中,除非另有明确的规定和限定,术语“安装”、“相连”、“连接”、“固定”等术语应做广义理解,例如,可以是固定连接,也可以是可拆卸连接,或成一体;可以是机械连接,也可以是电连接;可以是直接相连,也可以通过中间媒介间接相连,可以是两个元件内部的连通或两个元件的相互作用关系,除非另有明确的限定。对于本领域的普通技术人员而言,可以根据具体情况理解上述术语在本发明中的具体含义。在本发明的一个方面,本发明提出了一种石煤提钒的系统。根据本发明的实施例,参考图1,该系统包括:石煤预处理单元100、铁浴炉200、提钒装置300和钒渣处理单元400。根据本发明的实施例,石煤预处理单元100具有石煤入口101、烟气出口102和干燥石煤颗粒出口103,且适于将石煤进行预处理,以便除去结晶水和自由水,得到烟气和干燥石煤颗粒。发明人发现,通过将石煤进行预处理,可将石煤中的结晶水、自由水及其他易挥发杂质去掉,得到干燥石煤颗粒,如此,有利于提高后续钒渣中五氧化二钒的含量。根据本发明的一个实施例,石煤预处理单元包括依次相连的破碎装置、干燥装置和预热装置。发明人发现,将石煤进行破碎有利于提高后续对石煤进行干燥和预热处理的效率,同时加快干燥石煤颗粒在铁浴炉中的熔化速率;石煤经干燥和预热后,可以除去石煤中的结晶水、自由水和其他亦挥发杂质,得到温度较高的干燥石煤颗粒,如此,有利于减少向铁浴炉中带入杂质的量,从而提高后续所得钒渣中五氧化二钒的含量,同时因干燥石煤颗粒经预热后有一定温度,可减少铁浴炉的能耗,从而提高整个系统的经济性。根据本发明的再一个实施例,干燥石煤颗粒的粒径并不受特别限制,本领域技术人员可以根据实际需要进行选择,根据本发明的一个具体实施例,干燥石煤颗粒中的粒径可以为5~15mm的占比80%以上。发明人发现,若颗粒太细,影响生产透气性,传热慢;而若颗粒太粗,热量从外传入颗粒内部的速度慢,生产效率低。由此,采用本申请粒径范围的颗粒可以显著提高生产率,缩短冶炼时间,降低能耗。根据本发明的实施例,铁浴炉200具有含铁物料入口201、干燥石煤颗粒入口202、含钒铁水出口203和高温烟气出口204,干燥石煤颗粒入口202与干燥石煤颗粒出口103相连,高温烟气出口204与石煤预处理单元100相连,且适于将含铁物料和干燥石煤颗粒进行熔融处理,以便得到含钒铁水和高温烟气,并将高温烟气返回至上述石煤预处理单元。具体的,在铁浴炉中,待含铁物料熔化升温到不小于1500摄氏度时,将干燥石煤颗粒加入铁浴炉内,干燥石煤颗粒在高温下迅速熔化,期间干燥石煤颗粒中的碳与自身中的铁氧化物和钒氧化物发生还原反应,将三氧化二铁还原为氧化亚铁、氧化亚铁还原为铁、五氧化二钒还原为三氧化二钒,同时干燥石煤颗粒中的碳与熔融后的含铁物料发生渗碳反应,生成饱和碳,该饱和碳释放到熔融后的含铁物料和干燥石煤颗粒的混合熔液中,与其中的铁氧化物、钒氧化物发生还原反应,被充分还原后的钒进入混合熔液中得到含钒铁水。当干燥石煤颗粒在1550-1650摄氏度下完全熔清后,保温45-75min。从铁浴炉得到的高温烟气可用于石煤预处理单元中对石煤进行干燥和预热处理,有利于降低石煤预处理单元的能耗,提高系统的经济性。干燥石煤颗粒中的碳与自身中的铁氧化物和钒氧化物发生还原反应的反应式主要有:C+Fe2O3=FeO+CO(1)C+FeO=Fe+CO(2)C+V2O5=V2O3+CO(3)干燥石煤颗粒中的碳与熔融后的含铁物料发生渗碳反应,生成饱和碳,该饱和碳释放到熔融后的含铁物料和干燥石煤颗粒的混合熔液中,与其中的铁氧化物、钒氧化物发生还原反应的反应式主要有:[C]+[Fe]=[Fe3C](4)[C]+(FeO)=[Fe]+CO(5)[C]+(V2O3)=(VO)+CO(6)C+[VO]=[V]+CO(7)[C]+(SiO2)=[Si]+CO(8)根据本发明的一个实施例,干燥石煤颗粒与含铁物料的质量比并不受特别限制,本领域技术人员可以根据实际需要进行选择,根据本发明的一个具体实施例,干燥石煤颗粒与含铁物料的质量比可以为1:(1~2)。发明人发现,若干燥石煤颗粒配比太低,含铁物料配比过高,则含钒铁水钒含量低,提钒成本增加;而若干燥石煤颗粒配比过高,则造成碳资源浪费,且干燥石煤颗粒熔化速度降低,钒氧化物反应速度降低,从而导致生产效率降低。根据本发明的实施例,提钒装置300具有含钒铁水入口301、氧气入口302、半钢出口303和钒渣出口304,含钒铁水入口301与含钒铁水出口203相连,半钢出口303与含铁物料入口201相连,且适于将含钒铁水和氧气进行提钒处理,以便得到钒渣和半钢,并将半钢返回上述铁浴炉中。具体的,在提钒装置中,含钒铁水在氧气的作用下可得到含五氧化二钒15wt%以上的钒渣,是石煤中五氧化二钒含量的十倍以上,达到富集钒的目的,所得的半钢可返回至铁浴炉中熔化,用作干燥石煤颗粒熔化时其内的铁氧化物和钒氧化物熔融还原的母液,如此,有利于循环利用提钒装置所得的半钢,且可显著减少铁浴炉中含铁物料的加入量,减少铁浴炉的能耗,进一步提高系统的经济性。含钒铁水与氧气反应的反应式主要有:[V]+[O]=V2O3(9)[Fe]+[O]=(FeO)(10)[O]+[Si]=(SiO2)(11)[C]+[O]=CO(12)根据本发明的一个实施例,提钒处理的条件并不受特别限制,本领域技术人员可以根据实际需要进行选择,根据本发明的一个具体实施例,提钒温度可以控制在1350-1420摄氏度,吹氧5-8min。发明人发现,当提钒温度过高,炉渣变稀,不利于渣铁分离;但提钒温度过低,反应速度慢,满足不了生产要求,生产效率低。当吹氧时间过短,钒还原不完全,会导致钒资源浪费;而吹氧时间过长,金属铁氧化成氧化亚铁量增加,铁进入钒渣的量增加,会导致铁资源浪费,降低钒渣中五氧化二钒的含量,导致钒渣生产单位五氧化二钒的成本增加。根据本发明的实施例,钒渣处理单元400具有钒渣入口401和五氧化二钒出口402,钒渣入口401与钒渣出口304相连,且适于将钒渣进行钒渣处理,以便得到五氧化二钒。发明人发现,在钒渣处理单元中,可将钒渣中的五氧化二钒提出,同时碱耗降低75%以上。根据本发明的一个实施例,钒渣处理单元并不受特别限制,本领域技术人员可以根据实际需要进行选择,根据本发明的一个具体实施例,钒渣处理单元可以包括依次相连的第一焙烧装置、水浸装置和第二焙烧装置。具体的,焙烧温度750-900摄氏度,时间1-2h,焙烧温度过高或时间过长时,部分钒易生成不能浸出的复杂物相,同时增加能源消耗;而焙烧温度过低或时间过短时,五氧化二钒转化成钒酸钠不完全,导致钒回收率低;焙烧后将钒渣细磨到60-100目,粒度过粗,钒难以浸出,过细,则细磨成本增加,难以经济的生产。将细磨后的钒渣与水混合,固液比1:(2-5),加热至70-95摄氏度搅拌浸出,钒以不溶于水的水合物形式存在,过滤得到固体水合钒。钒渣与会混合时,若固液比过低,钒进液体速度低,浸出率低,导致钒回收率低;而若固液比过大,水耗增加,导致水资源浪费。水浸时,若温度过高,水会以水蒸气的形式挥发,造成水耗增加,而若温度过低,则水浸反应热力学条件差,钒水浸率低,钒回收率低。上述所得的水合钒在焙烧炉去水获得产品五氧化二钒。根据本发明实施例的石煤提钒的系统通过将石煤进行预处理,可将石煤中的结晶水、自由水及其他易挥发杂质去掉,得到干燥石煤颗粒,如此,有利于提高后续钒渣中五氧化二钒的含量;在铁浴炉中,干燥石煤颗粒在高温下迅速熔化,期间干燥石煤颗粒中的碳与自身中的铁氧化物和钒氧化物发生还原反应,将三氧化二铁还原为氧化亚铁、氧化亚铁还原为铁、五氧化二钒还原为三氧化二钒,同时干燥石煤颗粒中的碳与熔融后的含铁物料发生渗碳反应,生成饱和碳,该饱和碳释放到熔融后的含铁物料和干燥石煤颗粒的混合熔液中,与其中的铁氧化物、钒氧化物发生还原反应,被充分还原后的钒进入混合熔液中得到含钒铁水。从铁浴炉得到的高温烟气可用于石煤预处理单元中对石煤进行干燥和预热处理,有利于降低石煤预处理单元的能耗,提高系统的经济性;在提钒装置中,含钒铁水在氧气的作用下可得到含五氧化二钒15wt%以上的钒渣,是石煤中五氧化二钒含量的十倍以上,达到富集钒的目的,所得的半钢可返回至铁浴炉中熔化,用作干燥石煤颗粒熔化时其内的铁氧化物和钒氧化物熔融还原的母液,如此,有利于循环利用提钒装置所得的半钢,且可显著减少铁浴炉中含铁物料的加入量,减少铁浴炉的能耗,进一步提高系统的经济性;在钒渣处理单元中,可将钒渣中的五氧化二钒提出,同时碱耗降低75%以上。整个石煤提钒系统的生产成本及能源消耗降低10%以上。在本发明的再一个方面,本发明提出了一种利用上述石煤提钒的系统实施石煤提钒的方法。根据本发明的实施例,参考图2,该方法包括:S100:将石煤供给至石煤预处理单元中进行预处理该步骤中,将石煤供给至石煤预处理单元中进行预处理,以便除去结晶水和自由水,得到烟气和干燥石煤颗粒。发明人发现,通过将石煤进行预处理,可将石煤中的结晶水、自由水及其他易挥发杂质去掉,得到干燥石煤颗粒,如此,有利于提高后续钒渣中五氧化二钒的含量。根据本发明的一个实施例,预处理依次包括破碎、干燥和预热处理。发明人发现,将石煤进行破碎有利于提高后续对石煤进行干燥和预热处理的效率,同时加快干燥石煤颗粒在铁浴炉中的熔化速率;石煤经来自铁浴炉中的高温烟气干燥和预热后,可以除去石煤中的结晶水、自由水和其他亦挥发杂质,得到温度较高的干燥石煤颗粒,如此,有利于减少向铁浴炉中带入杂质的量,从而提高后续所得钒渣中五氧化二钒的含量,同时因干燥石煤颗粒经预热后有一定温度,可减少铁浴炉的能耗,从而提高整个系统的经济性。根据本发明的再一个实施例,干燥石煤颗粒的粒径并不受特别限制,本领域技术人员可以根据实际需要进行选择,根据本发明的一个具体实施例,干燥石煤颗粒中的粒径可以为5~15mm的占比80%以上。发明人发现,若颗粒太细,影响生产透气性,传热慢;而若颗粒太粗,热量从外传入颗粒内部的速度慢,生产效率低。由此,采用本申请粒径范围的颗粒可以显著提高生产率,缩短冶炼时间,降低能耗。S200:将含铁物料和干燥石煤颗粒供给至铁浴炉中进行熔融处理该步骤中,将含铁物料和干燥石煤颗粒供给至铁浴炉中进行熔融处理,以便得到含钒铁水和高温烟气,并将高温烟气返回S100中的石煤预处理单元。具体的,在铁浴炉中,待含铁物料熔化升温到不小于1500摄氏度时,将干燥石煤颗粒加入铁浴炉内,干燥石煤颗粒在高温下迅速熔化,期间干燥石煤颗粒中的碳与自身中的铁氧化物和钒氧化物发生还原反应,将三氧化二铁还原为氧化亚铁、氧化亚铁还原为铁、五氧化二钒还原为三氧化二钒,同时干燥石煤颗粒中的碳与熔融后的含铁物料发生渗碳反应,生成饱和碳,该饱和碳释放到熔融后的含铁物料和干燥石煤颗粒的混合熔液中,与其中的铁氧化物、钒氧化物发生还原反应,被充分还原后的钒进入混合熔液中得到含钒铁水。当干燥石煤颗粒在1550-1650摄氏度下完全熔清后,保温45-75min。从铁浴炉得到的高温烟气可用于石煤预处理单元中对石煤进行干燥和预热处理,有利于降低石煤预处理单元的能耗,提高系统的经济性。干燥石煤颗粒中的碳与自身中的铁氧化物和钒氧化物发生还原反应的反应式主要有:C+Fe2O3=FeO+CO(1)C+FeO=Fe+CO(2)C+V2O5=V2O3+CO(3)干燥石煤颗粒中的碳与熔融后的含铁物料发生渗碳反应,生成饱和碳,该饱和碳释放到熔融后的含铁物料和干燥石煤颗粒的混合熔液中,与其中的铁氧化物、钒氧化物发生还原反应的反应式主要有:[C]+[Fe]=[Fe3C](4)[C]+(FeO)=[Fe]+CO(5)[C]+(V2O3)=(VO)+CO(6)C+[VO]=[V]+CO(7)[C]+(SiO2)=[Si]+CO(8)根据本发明的一个实施例,干燥石煤颗粒与含铁物料的质量比并不受特别限制,本领域技术人员可以根据实际需要进行选择,根据本发明的一个具体实施例,干燥石煤颗粒与含铁物料的质量比可以为1:(1~2)。发明人发现,若干燥石煤颗粒配比太低,含铁物料配比过高,则含钒铁水钒含量低,提钒成本增加;而若干燥石煤颗粒配比过高,则造成碳资源浪费,且干燥石煤颗粒熔化速度降低,钒氧化物反应速度降低,从而导致生产效率降低。S300:将含钒铁水和氧气供给至提钒装置中进行提钒处理该步骤中,将含钒铁水和氧气供给至提钒装置中进行提钒处理,以便得到钒渣和半钢,并将半钢返回S200中的铁浴炉。具体的,在提钒装置中,含钒铁水在氧气的作用下可得到含五氧化二钒15wt%以上的钒渣,是石煤中五氧化二钒含量的十倍以上,达到富集钒的目的,所得的半钢可返回至铁浴炉中熔化,用作干燥石煤颗粒熔化时其内的铁氧化物和钒氧化物熔融还原的母液,如此,有利于循环利用提钒装置所得的半钢,且可显著减少铁浴炉中含铁物料的加入量,减少铁浴炉的能耗,进一步提高系统的经济性。含钒铁水与氧气反应的反应式主要有:[V]+[O]=V2O3(9)[Fe]+[O]=(FeO)(10)[O]+[Si]=(SiO2)(11)[C]+[O]=CO(12)根据本发明的一个实施例,提钒处理的条件并不受特别限制,本领域技术人员可以根据实际需要进行选择,根据本发明的一个具体实施例,提钒温度可以控制在1350-1420摄氏度,吹氧5-8min。发明人发现,当提钒温度过高,炉渣变稀,不利于渣铁分离;但提钒温度过低,反应速度慢,满足不了生产要求,生产效率低。当吹氧时间过短,钒还原不完全,会导致钒资源浪费;而吹氧时间过长,金属铁氧化成氧化亚铁量增加,铁进入钒渣的量增加,会导致铁资源浪费,降低钒渣中五氧化二钒的含量,导致钒渣生产单位五氧化二钒的成本增加。S400:将钒渣供给至钒渣处理单元中进行钒渣处理该步骤中,将钒渣供给至钒渣处理单元中进行钒渣处理,以便得到五氧化二钒。发明人发现,在钒渣处理单元中,可将钒渣中的五氧化二钒提出,同时碱耗降低75%以上。根据本发明的一个实施例,钒渣处理并不受特别限制,本领域技术人员可以根据实际需要进行选择,根据本发明的一个具体实施例,钒渣处理可以依次包括第一焙烧处理、水浸处理和第二焙烧处理。具体的,焙烧温度750-900摄氏度,时间1-2h,焙烧温度过高或时间过长时,部分钒易生成不能浸出的复杂物相,同时增加能源消耗;而焙烧温度过低或时间过短时,五氧化二钒转化成钒酸钠不完全,导致钒回收率低;焙烧后将钒渣细磨到60-100目,粒度过粗,钒难以浸出,过细,则细磨成本增加,难以经济的生产。将细磨后的钒渣与水混合,固液比1:(2-5),加热至70-95摄氏度搅拌浸出,钒以不溶于水的水合物形式存在,过滤得到固体水合钒。钒渣与会混合时,若固液比过低,钒进液体速度低,浸出率低,导致钒回收率低;而若固液比过大,水耗增加,导致水资源浪费。水浸时,若温度过高,水会以水蒸气的形式挥发,造成水耗增加,而若温度过低,则水浸反应热力学条件差,钒水浸率低,钒回收率低。上述所得的水合钒在焙烧炉去水获得产品五氧化二钒。根据本发明实施例的石煤提钒的方法通过将石煤进行预处理,可将石煤中的结晶水、自由水及其他易挥发杂质去掉,得到干燥石煤颗粒,如此,有利于提高后续钒渣中五氧化二钒的含量;在铁浴炉中,干燥石煤颗粒在高温下迅速熔化,期间干燥石煤颗粒中的碳与自身中的铁氧化物和钒氧化物发生还原反应,将三氧化二铁还原为氧化亚铁、氧化亚铁还原为铁、五氧化二钒还原为三氧化二钒,同时干燥石煤颗粒中的碳与熔融后的含铁物料发生渗碳反应,生成饱和碳,该饱和碳释放到熔融后的含铁物料和干燥石煤颗粒的混合熔液中,与其中的铁氧化物、钒氧化物发生还原反应,被充分还原后的钒进入混合熔液中得到含钒铁水。从铁浴炉得到的高温烟气可用于石煤预处理单元中对石煤进行干燥和预热处理,有利于降低石煤预处理单元的能耗,提高整体的经济性;在提钒装置中,含钒铁水在氧气的作用下可得到含五氧化二钒15wt%以上的钒渣,是石煤中五氧化二钒含量的十倍以上,达到富集钒渣的目的,所得的半钢可返回至铁浴炉中熔化,用作干燥石煤颗粒熔化时其内的铁氧化物和钒氧化物熔融还原的母液,如此,有利于循环利用提钒装置所得的半钢,且可显著减少铁浴炉中含铁物料的加入量,减少铁浴炉的能耗,进一步提高整体的经济性;在钒渣处理单元中,可将钒渣中的五氧化二钒提出,同时碱耗降低75%以上。整个石煤提钒的方法的生产成本及能源消耗降低10%以上。下面参考具体实施例,对本发明进行描述,需要说明的是,这些实施例仅仅是描述性的,而不以任何方式限制本发明。实施例1参考图3,石煤破碎至粒径5-15mm占80%以上(石煤组成成分及个成分的含量见表1),经干燥和预热后送至铁浴炉,预热后干燥石煤颗粒的温度为500摄氏度,预热热源来自铁浴炉的高温烟气,待铁浴炉内的含铁物料(生铁或废钢)熔化升温到1500摄氏度时,将预热后的干燥石煤颗粒经过下料仓和下料管均匀加入铁浴炉膛内,干燥石煤颗粒与含铁物料的加料比例为1:2,干燥石煤颗粒在铁浴炉内迅速熔化,且在干燥石煤颗粒熔化升温过程中,干燥石煤颗粒中的碳与自身中的铁氧化物和钒氧化物发生还原反应,反应式为:C+Fe2O3=FeO+CO(1)C+FeO=Fe+CO(2)C+V2O5=V2O3+CO(3)同时,干燥石煤颗粒中的碳与熔融后的含铁物料发生渗碳反应,生成饱和碳,该饱和碳释放到熔融后的含铁物料和干燥石煤颗粒的混合熔液中,与其中的铁氧化物、钒氧化物发生还原反应,反应式为:[C]+[Fe]=[Fe3C](4)[C]+(FeO)=[Fe]+CO(5)[C]+(V2O3)=(VO)+CO(6)C+[VO]=[V]+CO(7)[C]+(SiO2)=[Si]+CO(8)还原后的钒进入反应后的混合熔液中,得到含钒铁水,含钒铁水的主要组成成分及各成分的含量见表2。当干燥石煤颗粒在1550摄氏度下完全熔清后,保温60min。从铁浴炉得到的高温烟气可用于石煤预处理单元中对石煤进行干燥和预热处理。含钒铁水出炉入铁水包,铁水包倒运至提钒装置(提钒炉),提钒温度控制在1380摄氏度,吹氧时间7min,含钒铁水在氧气的作用下可得到含五氧化二钒的钒渣,吹氧过程主要发生如下反应:[V]+[O]=V2O3(9)[Fe]+[O]=(FeO)(10)[O]+[Si]=(SiO2)(11)[C]+[O]=CO(12)吹氧结束,得到半钢和钒渣,半钢出炉,所得的半钢可返回至铁浴炉中熔化,用作干燥石煤颗粒熔化时其内的铁氧化物和钒氧化物熔融还原的母液,钒渣残留在提钒装置(提钒炉)内,两炉出一次钒渣。钒渣的主要成分及各成分的含量见表3;所出的钒渣送入钒渣处理单元,依次进行焙烧-水浸-焙烧,获得片状V2O5。所得钒渣中五氧化二钒的含量是石煤中五氧化二钒含量的13倍,且碱耗降低75%,整个石煤提钒的能耗降低10%。表1石煤主要成分及各成分含量(wt%)V2O5FeMgOSiO2SiO2CaOAl2O3C∑1.2475.8046.7647.41.7688.3411.6512-25100表2含钒铁水主要成分及各成分含量(wt%)VSiCS0.3150.444.151.22表3钒渣主要成分及各成分含量(wt%)V2O5SiO2TFeCaO16.8632.5538.125.28实施例2参考图3,石煤破碎至粒径5-10mm占80%以上(石煤组成成分及个成分的含量见表1),经干燥和预热后送至铁浴炉,预热后干燥石煤颗粒的温度为500摄氏度,预热热源来自铁浴炉的高温烟气,待铁浴炉内的含铁物料(生铁或废钢)熔化升温到1550摄氏度时,将预热后的干燥石煤颗粒经过下料仓和下料管均匀加入铁浴炉膛内,干燥石煤颗粒与含铁物料的加料比例为1:1,干燥石煤颗粒在铁浴炉内迅速熔化,且在干燥石煤颗粒熔化升温过程中,干燥石煤颗粒中的碳与自身中的铁氧化物和钒氧化物发生还原反应,反应式为:C+Fe2O3=FeO+CO(1)C+FeO=Fe+CO(2)C+V2O5=V2O3+CO(3)同时,干燥石煤颗粒中的碳与熔融后的含铁物料发生渗碳反应,生成饱和碳,该饱和碳释放到熔融后的含铁物料和干燥石煤颗粒的混合熔液中,与其中的铁氧化物、钒氧化物发生还原反应,反应式为:[C]+[Fe]=[Fe3C](4)[C]+(FeO)=[Fe]+CO(5)[C]+(V2O3)=(VO)+CO(6)C+[VO]=[V]+CO(7)[C]+(SiO2)=[Si]+CO(8)还原后的钒进入反应后的混合熔液中,得到含钒铁水,含钒铁水的主要组成成分及各成分的含量见表4。当干燥石煤颗粒在1600摄氏度下完全熔清后,保温60min。从铁浴炉得到的高温烟气可用于石煤预处理单元中对石煤进行干燥和预热处理。含钒铁水出炉入铁水包,铁水包倒运至提钒装置(提钒炉),提钒温度控制在1420摄氏度,吹氧时间5min,含钒铁水在氧气的作用下可得到含五氧化二钒的钒渣,吹氧过程主要发生如下反应:[V]+[O]=V2O3(9)[Fe]+[O]=(FeO)(10)[O]+[Si]=(SiO2)(11)[C]+[O]=CO(12)吹氧结束,得到半钢和钒渣,半钢出炉,所得的半钢可返回至铁浴炉中熔化,用作干燥石煤颗粒熔化时其内的铁氧化物和钒氧化物熔融还原的母液,钒渣残留在提钒装置(提钒炉)内,两炉出一次钒渣。钒渣的主要成分及各成分的含量见表5;所出的钒渣送入钒渣处理单元,依次进行焙烧-水浸-焙烧,获得片状V2O5。所得钒渣中五氧化二钒的含量是石煤中五氧化二钒含量的18倍,且碱耗降低82%,整个石煤提钒的能耗降低13%。表4含钒铁水主要成分及各成分含量(wt%)VSiCS0.5990.493.970.20表5钒渣主要成分及各成分含量(wt%)V2O5SiO2TFeCaO21.8628.7235.694.66在本说明书的描述中,参考术语“一个实施例”、“一些实施例”、“示例”、“具体示例”、或“一些示例”等的描述意指结合该实施例或示例描述的具体特征、结构、材料或者特点包含于本发明的至少一个实施例或示例中。在本说明书中,对上述术语的示意性表述不必须针对的是相同的实施例或示例。而且,描述的具体特征、结构、材料或者特点可以在任一个或多个实施例或示例中以合适的方式结合。此外,在不相互矛盾的情况下,本领域的技术人员可以将本说明书中描述的不同实施例或示例以及不同实施例或示例的特征进行结合和组合。尽管上面已经示出和描述了本发明的实施例,可以理解的是,上述实施例是示例性的,不能理解为对本发明的限制,本领域的普通技术人员在本发明的范围内可以对上述实施例进行变化、修改、替换和变型。当前第1页1 2 3