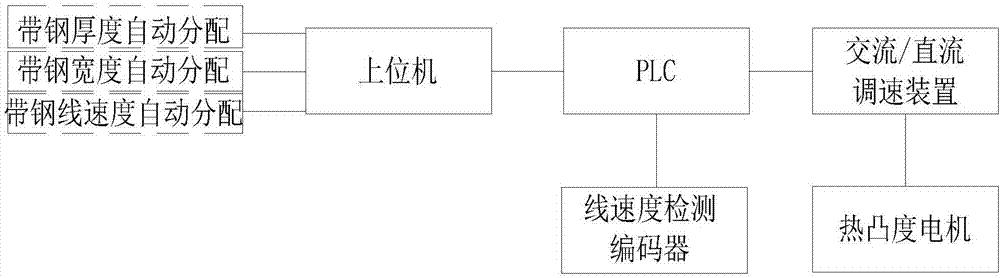
本发明涉及冷轧热处理
技术领域:
,特别涉及一种冷轧连退炉加热段导向辊热凸度电机转速设定方法。
背景技术:
:连续退火机组是冷轧带钢生产的重要环节,具有流程短、产量高和产品质量好等一系列优点。其中,连续退火炉是连续退火机组重要的组成部分。研究发现,带钢应力分布与带钢跑偏和瓢曲变形有着直接关系。然而,连退炉内,导向辊辊形并不是固定不变的,由于受热不均,导向辊会产生热凸度,使其形状发生改变,最终导致带钢应力分布的改变。本发明为了解决现有技术问题,提供了一种冷轧连退炉加热段导向辊热凸度电机转速设定方法,能够改善带钢的应力分布,进而避免带钢跑偏和瓢曲。技术实现要素:为了克服现有技术的不足,本发明提供一种冷轧连退炉加热段导向辊热凸度电机转速设定方法,解决了冷轧连退炉内加热段导向辊由于受热不均产生的热凸度带来辊形形状的改变,使得带钢的应力分布发生变化,导致带钢跑偏和瓢曲变形的问题。为了达到上述目的,本发明采用以下技术方案实现:一种冷轧连退炉加热段导向辊热凸度电机转速设定方法,该方法应用于采用热凸度电机驱动冷却风机喷吹连退炉加热段导向辊边部;该方法包括以下步骤:(1)确定带钢宽度分类;(2)确定带钢厚度分类;(3)确定带钢线速度分类;(4)确定热凸度电机转速设定值。步骤(1)中的宽度分类为[1000-1100)、[1100-1200)、[1200-1450)、[1450-1700)、[1700-1800)、[1800-1980],单位为毫米。步骤(2)中带钢的厚度分类为[0.300-0.500)、[0.500-0.750)、[0.750-1.100)、[1.100-1.600)、[1.600-2.000],单位为毫米。步骤(3)中带钢的线速度分类为[0.00-70.00)、[70.00-140.00)、[140.00-210.00)、[210.00-280.00)、[280.00-480.00],单位为米/分钟。步骤(4)中热凸度电机转速采用百分比的形式进行设定,即额定转速的百分比,具体方法如下:当带钢的厚度、宽度、线速度分别对应到[0.750-1.100)、[1000-1100)、[140.00-210.00)时,热凸度电机转速设定值为22%;当带钢的厚度、宽度、线速度分别对应到[0.750-1.100)、[1000-1100)、[210.00-280.00)时,热凸度电机转速设定值为36%;当带钢的厚度、宽度、线速度分别对应到[0.750-1.100)、[1000-1100)、[280.00-480.00]时,热凸度电机转速设定值为67%;当带钢的厚度、宽度、线速度分别对应到[0.750-1.100)、[1100-1200)、[140.00-210.00)时,热凸度电机转速设定值为18%;当带钢的厚度、宽度、线速度分别对应到[0.750-1.100)、[1100-1200)、[210.00-280.00)时,热凸度电机转速设定值为30%;当带钢的厚度、宽度、线速度分别对应到[0.750-1.100)、[1100-1200)、[280.00-480.00]时,热凸度电机转速设定值为60%;当带钢的厚度、宽度、线速度分别对应到[1.100-1.600)、[1000-1100)、[70.00-140.00)时,热凸度电机转速设定值为24%;当带钢的厚度、宽度、线速度分别对应到[1.100-1.600)、[1000-1100)、[140.00-210.00)时,热凸度电机转速设定值为38%;当带钢的厚度、宽度、线速度分别对应到[1.100-1.600)、[1000-1100)、[210.00-280.00)时,热凸度电机转速设定值为68%;当带钢的厚度、宽度、线速度分别对应到[1.100-1.600)、[1000-1100)、[280.00-480.00]时,热凸度电机转速设定值为90%;当带钢的厚度、宽度、线速度分别对应到[1.100-1.600)、[1100-1200)、[70.00-140.00)时,热凸度电机转速设定值为20%;当带钢的厚度、宽度、线速度分别对应到[1.100-1.600)、[1100-1200)、[140.00-210.00)时,热凸度电机转速设定值为32%;当带钢的厚度、宽度、线速度分别对应到[1.100-1.600)、[1100-1200)、[210.00-280.00)时,热凸度电机转速设定值为62%;当带钢的厚度、宽度、线速度分别对应到[1.100-1.600)、[1100-1200)、[280.00-480.00]时,热凸度电机转速设定值为80%;当带钢的厚度、宽度、线速度分别对应到[1.100-1.600)、[1200-1450)、[140.00-210.00)时,热凸度电机转速设定值为20%;当带钢的厚度、宽度、线速度分别对应到[1.100-1.600)、[1200-1450)、[210.00-280.00)时,热凸度电机转速设定值为35%;当带钢的厚度、宽度、线速度分别对应到[1.100-1.600)、[1200-1450)、[280.00-480.00]时,热凸度电机转速设定值为60%;当带钢的厚度、宽度、线速度分别对应到[1.600-2.000]、[1000-1100)、[70.00-140.00)时,热凸度电机转速设定值为26%;当带钢的厚度、宽度、线速度分别对应到[1.600-2.000]、[1000-1100)、[140.00-210.00)时,热凸度电机转速设定值为40%;当带钢的厚度、宽度、线速度分别对应到[1.600-2.000]、[1000-1100)、[210.00-280.00)时,热凸度电机转速设定值为70%;当带钢的厚度、宽度、线速度分别对应到[1.600-2.000]、[1000-1100)、[280.00-480.00]时,热凸度电机转速设定值为100%;当带钢的厚度、宽度、线速度分别对应到[1.600-2.000]、[1100-1200)、[70.00-140.00)时,热凸度电机转速设定值为24%;当带钢的厚度、宽度、线速度分别对应到[1.600-2.000]、[1100-1200)、[140.00-210.00)时,热凸度电机转速设定值为30%;当带钢的厚度、宽度、线速度分别对应到[1.600-2.000]、[1100-1200)、[210.00-280.00)时,热凸度电机转速设定值为64%;当带钢的厚度、宽度、线速度分别对应到[1.600-2.000]、[1100-1200)、[280.00-480.00]时,热凸度电机转速设定值为90%;当带钢的厚度、宽度、线速度分别对应到[1.600-2.000]、[1200-1450)、[140.00-210.00)时,热凸度电机转速设定值为25%;当带钢的厚度、宽度、线速度分别对应到[1.600-2.000]、[1200-1450)、[210.00-280.00)时,热凸度电机转速设定值为40%;当带钢的厚度、宽度、线速度分别对应到[1.600-2.000]、[1200-1450)、[280.00-480.00]时,热凸度电机转速设定值为70%;上述未提及的情况,热凸度电机不投入使用,不进行转速设定。本发明方法所述的热凸度电机转速参数为1500rpm,所述的冷却风机参数全压为1000pa+/-20pa,流量为2200m3/h+/-35m3/h,在所述的热凸度电机驱动的冷却风机风量和风压不变的情况下,本方法中的电机转速设定值还适用于与所述冷却风机配套的任何转速的热凸度电机。转速自动设定方法为:(1)首先在上位机软件程序中对带钢宽度、厚度和线速度进行分类;(2)上位机软件按带钢宽度、厚度和线速度进行分类并存储在上位机数据库、文件或软件中,按上述转速设定方法中的转速百分比设定值存储于上位机数据库、文件或软件中;(3)带钢宽度、厚度数据存储在数据库中,通过带钢号进行索引,带钢号通过plc的跟踪系统发送给上位机软件程序;线速度值由测速编码器检测,plc负责将采集到的线速度值发送给上位机软件程序;(4)上位机软件根据带钢号和线速度值自动选择带钢的宽度、厚度和线速度分类;(5)上位机软件按选择的分类自动查询并设定热凸度电机的转速值;(6)上位机将配置好的热凸度电机转速值发送至现场的plc控制器;(7)plc控制器根据接收到的转速设定值通过交流变频器或直流调速装置对热凸度电机转速进行开环调节;(8)交流变频器或直流调速装置将输出的转速值反馈给plc,并通过plc最终将转速输出值反馈至上位机界面进行显示;(9)布置于现场设备上的用于检测带钢线速度的编码器将现场实际的线速度值实时通过plc反馈至上位机,用于进行线速度分类和供操作人员进行查看。与现有技术相比,本发明的有益效果是:1、本发明提出的一种冷轧连退炉加热段导向辊热凸度电机转速设定方法,冷轧连退炉加热段导向辊热凸度电机转速设定方法应用后,能够有效地控制连退炉加热段导向辊产生热凸度,改善带钢跑偏和瓢曲变形。2、本发明提出的一种冷轧连退炉加热段导向辊热凸度电机转速设定方法,转速设定过程为全自动控制,由现场的plc系统和上位机结合,能够根据钢号自动配置钢带的厚度、宽度,根据现场的编码器自动检测线速度,实现热凸度电机的转速自动设定。附图说明图1为本发明的冷轧连退炉加热段导向辊热凸度电机转速设定方法的流程图;图2本发明实施例中的实现本发明方法的装置结构图。具体实施方式以下本发明提供的具体实施方式进行详细说明。如图1所示,一种冷轧连退炉加热段导向辊热凸度电机转速设定方法,该方法应用于采用热凸度电机驱动冷却风机喷吹连退炉加热段导向辊边部;该方法包括以下步骤:(1)确定带钢宽度分类;(2)确定带钢厚度分类;(3)确定带钢线速度分类;(4)确定热凸度电机转速设定值。步骤(1)中的宽度分类为[1000-1100)、[1100-1200)、[1200-1450)、[1450-1700)、[1700-1800)、[1800-1980],单位为毫米。步骤(2)中带钢的厚度分类为[0.300-0.500)、[0.500-0.750)、[0.750-1.100)、[1.100-1.600)、[1.600-2.000],单位为毫米。步骤(3)中带钢的线速度分类为[0.00-70.00)、[70.00-140.00)、[140.00-210.00)、[210.00-280.00)、[280.00-480.00],单位为米/分钟。步骤(4)中热凸度电机转速采用百分比的形式进行设定,即额定转速的百分比,具体方法如下:当带钢的厚度、宽度、线速度分别对应到[0.750-1.100)、[1000-1100)、[140.00-210.00)时,热凸度电机转速设定值为22%;当带钢的厚度、宽度、线速度分别对应到[0.750-1.100)、[1000-1100)、[210.00-280.00)时,热凸度电机转速设定值为36%;当带钢的厚度、宽度、线速度分别对应到[0.750-1.100)、[1000-1100)、[280.00-480.00]时,热凸度电机转速设定值为67%;当带钢的厚度、宽度、线速度分别对应到[0.750-1.100)、[1100-1200)、[140.00-210.00)时,热凸度电机转速设定值为18%;当带钢的厚度、宽度、线速度分别对应到[0.750-1.100)、[1100-1200)、[210.00-280.00)时,热凸度电机转速设定值为30%;当带钢的厚度、宽度、线速度分别对应到[0.750-1.100)、[1100-1200)、[280.00-480.00]时,热凸度电机转速设定值为60%;当带钢的厚度、宽度、线速度分别对应到[1.100-1.600)、[1000-1100)、[70.00-140.00)时,热凸度电机转速设定值为24%;当带钢的厚度、宽度、线速度分别对应到[1.100-1.600)、[1000-1100)、[140.00-210.00)时,热凸度电机转速设定值为38%;当带钢的厚度、宽度、线速度分别对应到[1.100-1.600)、[1000-1100)、[210.00-280.00)时,热凸度电机转速设定值为68%;当带钢的厚度、宽度、线速度分别对应到[1.100-1.600)、[1000-1100)、[280.00-480.00]时,热凸度电机转速设定值为90%;当带钢的厚度、宽度、线速度分别对应到[1.100-1.600)、[1100-1200)、[70.00-140.00)时,热凸度电机转速设定值为20%;当带钢的厚度、宽度、线速度分别对应到[1.100-1.600)、[1100-1200)、[140.00-210.00)时,热凸度电机转速设定值为32%;当带钢的厚度、宽度、线速度分别对应到[1.100-1.600)、[1100-1200)、[210.00-280.00)时,热凸度电机转速设定值为62%;当带钢的厚度、宽度、线速度分别对应到[1.100-1.600)、[1100-1200)、[280.00-480.00]时,热凸度电机转速设定值为80%;当带钢的厚度、宽度、线速度分别对应到[1.100-1.600)、[1200-1450)、[140.00-210.00)时,热凸度电机转速设定值为20%;当带钢的厚度、宽度、线速度分别对应到[1.100-1.600)、[1200-1450)、[210.00-280.00)时,热凸度电机转速设定值为35%;当带钢的厚度、宽度、线速度分别对应到[1.100-1.600)、[1200-1450)、[280.00-480.00]时,热凸度电机转速设定值为60%;当带钢的厚度、宽度、线速度分别对应到[1.600-2.000]、[1000-1100)、[70.00-140.00)时,热凸度电机转速设定值为26%;当带钢的厚度、宽度、线速度分别对应到[1.600-2.000]、[1000-1100)、[140.00-210.00)时,热凸度电机转速设定值为40%;当带钢的厚度、宽度、线速度分别对应到[1.600-2.000]、[1000-1100)、[210.00-280.00)时,热凸度电机转速设定值为70%;当带钢的厚度、宽度、线速度分别对应到[1.600-2.000]、[1000-1100)、[280.00-480.00]时,热凸度电机转速设定值为100%;当带钢的厚度、宽度、线速度分别对应到[1.600-2.000]、[1100-1200)、[70.00-140.00)时,热凸度电机转速设定值为24%;当带钢的厚度、宽度、线速度分别对应到[1.600-2.000]、[1100-1200)、[140.00-210.00)时,热凸度电机转速设定值为30%;当带钢的厚度、宽度、线速度分别对应到[1.600-2.000]、[1100-1200)、[210.00-280.00)时,热凸度电机转速设定值为64%;当带钢的厚度、宽度、线速度分别对应到[1.600-2.000]、[1100-1200)、[280.00-480.00]时,热凸度电机转速设定值为90%;当带钢的厚度、宽度、线速度分别对应到[1.600-2.000]、[1200-1450)、[140.00-210.00)时,热凸度电机转速设定值为25%;当带钢的厚度、宽度、线速度分别对应到[1.600-2.000]、[1200-1450)、[210.00-280.00)时,热凸度电机转速设定值为40%;当带钢的厚度、宽度、线速度分别对应到[1.600-2.000]、[1200-1450)、[280.00-480.00]时,热凸度电机转速设定值为70%;上述未提及的情况,热凸度电机不投入使用,不进行转速设定。本发明方法所述的热凸度电机转速参数为1500rpm,所述的冷却风机参数全压为1000pa+/-20pa,流量为2200m3/h+/-35m3/h,在所述的热凸度电机驱动的冷却风机风量和风压不变的情况下,本方法中的电机转速设定值还适用于与所述冷却风机配套的任何转速的热凸度电机。表1当厚度为[0.750-1.100)时,热凸度电机转速为:宽度\线速度[140.00-210.00)[210.00-280.00)[280.00-480.00][1000-1100)22%36%67%[1100-1200)18%30%60%表2当厚度为[1.100-1.600)时,热凸度电机转速为:表3当厚度为[1.600-2.000]时,热凸度电机转速为:宽度\线速度[70.00-140.00)[140.00-210.00)[210.00-280.00)[280.00-480.00][1000-1100)26%40%70%100%[1100-1200)24%34%64%90%[1200-1450)25%40%70%上述方法中,关于带钢厚度、宽度好线速度范围中的“[”和“]”表示闭区间符号,表示范围中含有端点,“(”“)”表示开区间符号,表示范围中不含有端点,例如:[70.00-140.00)表示范围中包含70.00,不包含140.00,即70.00≤x<140.00。具体实施例:以热凸度电机转速参数为1500rpm、风机参数全压为1000pa(+/-20pa),流量为2200m3/h(+/-35m3/h)为例,以现场实际生产的带钢为例,带钢厚度和宽度分别为1.5mm、1200mm,厚度1.5mm,对应到[1.100-1.600)类别,宽度1200mm对应到[1200-1450)类别。当带钢从预热段运行到加热段时,带钢的运行速度为200m/min,对应到速度[140.00-210.00)类别,那么可以得到热凸度电机转速设定值为20%,即热凸度电机采用额定转速1500rpm的20%,300rpm的转速驱动风机,喷吹连退炉加热段导向辊边部,减小导向辊边部和中部的温度差,避免热凸度的产生,进而改善带钢跑偏和瓢曲变形。如图2所示,为实现本发明方法应用的装置结构示意图,热凸度电机转速自动设定方法为:(1)首先在上位机软件程序中对带钢宽度、厚度和线速度进行分类;(2)上位机软件按带钢宽度、厚度和线速度进行分类并存储在上位机数据库、文件或软件中,按上述转速设定方法中的转速百分比设定值存储于上位机数据库、文件或软件中;(3)带钢宽度、厚度数据存储在数据库中,通过带钢号进行索引,带钢号通过plc的跟踪系统发送给上位机软件程序;线速度值由测速编码器检测,plc负责将采集到的线速度值发送给上位机软件程序;(4)上位机软件根据带钢号和线速度值自动选择带钢的宽度、厚度和线速度分类;(5)上位机软件按选择的分类自动查询并设定热凸度电机的转速值;(6)上位机将配置好的热凸度电机转速值发送至现场的plc控制器;(7)plc控制器根据接收到的转速设定值通过交流变频器或直流调速装置对热凸度电机转速进行开环调节;(8)交流变频器或直流调速装置将输出的转速值反馈给plc,并通过plc最终将转速输出值反馈至上位机界面进行显示;(9)布置于现场设备上的用于检测带钢线速度的编码器将现场实际的线速度值实时通过plc反馈至上位机,用于进行线速度分类和供操作人员进行查看。如果热凸度电机配置为交流电机,则采用变频调速方法进行调速,如果热凸度电机配置为直流电机,则采用直流调速驱动装置进行调速。以上实施例在以本发明技术方案为前提下进行实施,给出了详细的实施方式和具体的操作过程,但本发明的保护范围不限于上述的实施例。上述实施例中所用方法如无特别说明均为常规方法。当前第1页12