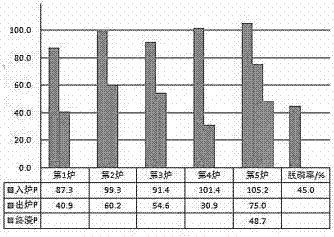
本发明属于转炉炼钢新技术及其应用领域,提供了一种充分利用气化脱磷渣循环冶炼提高转炉渣利用率、降低冶炼成本的转炉气化脱磷渣循环脱磷炼钢的方法。
背景技术:
:中国钢铁工业近20年来发展迅速,对国民经济快速增长发挥了重要作用,但在节省资源、能源和减少炉渣等固体废弃物排放等方面,目前面临着巨大的压力和挑战。以占中国产钢量90%以上氧气转炉炼钢为例,每年生产约6.2亿t粗钢,要产生6000万t以上炉渣,消耗3000万t以上石灰和700万t以上轻烧白云石,而用于生产炼钢石灰和轻烧白云石的石灰石与生白云石矿产均为重要的不可再生资源。目前应用或正在探索中转炉渣的综合利用或减少排放的方法有很多种,大致分为两类,一种是在炉渣从转炉排放为固体物以后再加以处理和利用,比较成熟的是回收金属铁,以后用于烧结矿添加剂、合成渣原料、磷肥或转炉渣水泥,即所谓“末端治理”,但是有效利用价值较低;另一种是炉渣在熔融状态,乃至在转炉内就加以循环利用,即所谓“源头治理”,这种方法是目前转炉渣的发展方向,符合无废或少废冶金的生态工业发展方向,比较成熟的有转炉溅渣护炉留渣操作等冶炼工艺。20世纪后期,深冲钢和高级别管线钢等钢种对磷含量要求苛刻,传统的单渣法炼钢脱磷率低,脱磷效果较差。90年代中期,日本各大钢厂进行了转炉铁水脱磷的试验研究,并在取得成功后迅速推广,解决了超低磷钢的生产难题。双联法是采用两座转炉联合作业,一座转炉脱磷,另一座转炉接受来自脱磷炉的低磷铁水脱碳,典型的双联法工艺流程为:高炉铁水→铁水预脱硫→转炉脱磷→转炉脱碳→二次精炼→连铸。日本各钢铁厂转炉双联法主要工艺技术参数对比,如表1所示。日本转炉采用双联法脱磷炼钢工艺的主要有jfe福山制铁所的ld-nrp法、住友金属的srp法、神户制钢的h炉法、新日铁的ld-orp法,我国宝钢、鞍钢、首钢京唐公司等也都选用了双联法炼钢工艺。表1日本钢铁厂转炉双联法主要技术工艺参数转炉双联法脱磷在大批量生产纯净钢时,转炉容量大,有充分的反应空间,反应动力学条件优越,铁水中磷可脱到0.010%以下,为少渣冶炼创造了条件;转炉双联法为生产超低磷钢、管线钢及优质宽厚板铸坯提供了有利的条件;双联法成本相对较低,转炉脱碳渣用于另一座转炉脱磷的双联法,生产1t铁水的钢铁料消耗比传统方法减少25kg,石灰消耗减少40%。但转炉双联法炼钢基建成本较高,需合理调度两座转炉设备,炉渣及钢水互相反倒,操作较复杂。新日铁室兰制铁所(两座270tld-ob转炉)和大分制铁所(3座370t复吹转炉)受设备和产品的限制,采用了murc技术,在同一转炉进行铁水脱磷预处理和脱碳吹炼,类似传统炼钢的双渣法。murc工艺操作中将转炉冶炼分为两个阶段,在第1阶段主要进行脱硅、脱磷,结束后倒出部分炉渣,然后进行第2阶段吹炼,吹炼结束后出钢但将炉渣保持在炉内,下一炉在炉内留渣情况下装入废钢、铁水,然后进行第1和第2阶段吹炼,并以此循环往复。室兰制铁所和大分制铁所全部采用murc工艺,前期脱磷渣一般倒出50%,脱碳渣直接留在炉内用于下一炉脱磷吹炼,murc工艺冶炼周期约33~35min。2001年ogawa等报道了新日铁开发的murc转炉炼钢新工艺及其在8t转炉的试验情况。近年来,新日铁陆续报道了mucr工艺相关情况,新日铁公司的大分、八幡、室兰、君津等钢厂采用了该工艺,产钢占新日铁总产钢量55%左右,转炉炼钢石灰消耗减少40%以上。20世纪50~70年代,中国一些转炉钢厂在铁水硅、磷质量分数高时,为了降低石灰消耗,减少吹炼过程喷溅,改善脱磷效果,曾采用出钢后留渣或“留渣+双渣”炼钢工艺。随着高炉生产水平的日益提高(铁水硅质量分数降低),高磷铁矿石用量减少(铁水磷质量分数降低),以及顾忌留渣造成铁水喷溅安全隐患,留渣炼钢工艺没有更大规模推广采用。近年来国内许多钢厂开始采用转炉留渣炼钢工艺,王新华等的发明专利201610012514.4“一种减少渣量的转炉炼钢方法”和201110340294.9“一种冶炼低磷钢的转炉冶炼工艺方法”,其关键技术是脱磷阶段通过采用低碱度(w(cao)/w(sio2):1.3~1.5)和低mgo质量分数(≤7.5%)渣系,形成流动性良好和适度泡沫化炉渣,解决了“留渣+双渣”炼钢工艺快速足量倒渣和渣中金属铁质量分数高这两大难题。针对转炉底吹搅拌弱的问题,在脱磷阶段采用低枪位和高强度供氧方法,利用顶吹氧气流加强金属熔池搅拌以促进脱磷,脱磷阶段结束时[p]平均降低至0.029%左右,脱碳阶段终点[p]降低至0.0096%左右,满足了绝大多数钢种对磷质量分数控制要求。经工业试验形成了sgrs工艺方法,首钢在其迁钢公司5座210t复吹转炉和首秦公司3座100t复吹转炉大规模采用此法,取得了炼钢石灰消耗减少47%以上,轻烧白云石消耗减少55%以上,渣量降低30%以上的效果。崔阳等的发明专利200910088141.2提出了“一种在溅渣护炉条件下顶底复吹转炉铁水脱磷的方法”,专利通过溅渣护炉操作有效利用前一炉次的炉渣和保护炉衬,同时提高脱磷效率。这些专利方法所基于的双渣法都需要在冶炼中期之前快速倒渣,提枪中断吹氧操作,与常规工艺相比,由于增加了炉渣固化和脱磷结束倒渣的时间,采用双渣+留渣工艺后转炉单炉生产周期比常规冶炼延长约4min,并且为了降低炉渣氧化性并固化炉渣,其溅渣护炉工艺中加入多种调质造渣料,如石灰、生白云石、轻烧白云石、镁碳球等。李建新等的发明专利200910077085.2提出了“一种使用脱磷剂的转炉冶炼工艺”,其技术方案指出利用前期低温和高氧化亚铁等良好的动力学条件,并使用含少量cacl2的cao基脱磷剂进行脱磷,后期重新造渣,脱碳渣做为下炉的脱磷渣使用。最近,赵东伟等的发明专利201610166145.8提出了“一种转炉高效脱磷的冶炼方法”,专利指出溅渣护炉后倒出残余炉渣,在转炉吹炼开始前,向炉内加入预熔渣,成分为cao:70~85%,sio2:15~30%,进行转炉吹炼操作。这些专利均优化了溅渣护炉后的炉渣,但存在的问题是未能充分对转炉渣进行改质并深入利用,磷富集问题限制了大量转炉渣在钢铁厂内部的循环利用。20世纪70年代末,日本的伊藤公久研究了ca2sio4-ca3(po4)2和cao-sio2-fe2o3液相渣间磷的平衡分配比,结果表明转炉渣中的磷绝大部分富集在初晶相ca2sio4-ca3(po4)2中,以固溶体形态存在,很难去除。morita等学者采用微波碳热还原对cao-sio2-feto系合成渣、铁水脱磷预处理渣和含cr的转炉不锈炉渣中fe、p、cr的回收进行了基础研究,验证了该方法脱磷的可行性并提出了进一步回收还原产物中p的方法。采用微波加热碳热还原转炉炉渣进行气化脱磷,是将炉渣中磷元素脱除的一条有效途径。关于经济有效地去除转炉炉渣中磷的方法,尤其是利用溅渣护炉过程中炉内气化脱除熔渣中磷的方法有很多报道,王书桓等的发明专利200610012514.4发明了一种“转炉溅渣护炉过程中气化脱除熔渣中磷的方法”,在溅渣护炉前,向熔池中加入适量脱磷剂,在溅渣过程中,高压氮气通过氧枪后产生巨大冲击力,将炉内熔渣击碎成颗粒飞溅起来挂于炉衬,此过程为固(焦炭)-气(氮气)-液(熔渣)之间的反应、以及熔渣内部的化学反应提供了良好的动力学条件,使熔渣中的磷得以通过化学反应进入气相脱除,气化脱磷剂分碳质脱磷剂和硅质脱磷剂两种,碳质更具有工业应用现实意义,经多年实验室基础实验和钢铁企业工业试验,气化脱磷率达到40%水平,留渣率80%以上,吨炉渣量平均为50~70kg/t,取得了良好的效果。王虎的发明专利201510561089.3发明了“一种用转炉煤气溅渣护炉作业的方法”,该工艺采用转炉煤气代替氮气进行转炉溅渣护炉作业,实现溅渣护炉作业时快速高效气化脱磷,降低炼钢成本。这些专利方法均能有效气化脱磷,但仍停留在转炉渣的处理上,未提出用于下炉冶炼的作用及影响,没有形成高效循环炼钢工艺。本发明基于溅渣护炉的气化脱磷渣,提出了一种转炉气化脱磷渣循环脱磷炼钢的方法,是一种所谓的“半双渣法”炼钢工艺,与新日铁murc工艺、首钢“留渣+双渣”工艺等相比,其特点是发挥气化脱磷渣在冶炼前期脱磷、转炉冶炼末期利用拉碳倒渣、热态熔渣炉内循环利用,提高了前期低温脱磷效率,减少了石灰造渣剂用量,循环高效利用转炉渣,降低了吨炉渣量,减少了铁损。技术实现要素:本发明的目的在于提供一种转炉气化脱磷渣循环脱磷炼钢的方法,该方法克服了传统工艺诸多缺陷,适用于现有钢铁厂工艺技术的改进。实现上述目的采用以下技术方案:一种转炉气化脱磷渣循环脱磷炼钢的方法,其特征在于,所述方法分为溅渣护炉气化脱磷、兑铁加料、吹氧造渣冶炼、拉碳倒渣和终点控制并出钢五个阶段,具体方法是:第一阶段溅渣护炉气化脱磷:转炉出钢结束后,根据炉渣基本状态,向转炉内热态熔渣中添加脱磷剂,在溅渣护炉过程中通过气化的方式脱除渣中的磷,保留溅渣后的气化脱磷渣;第二阶段兑铁加料:倾斜转炉兑入废钢和铁水,利用气化脱磷渣的富裕热量提高转炉废钢比,之后转炉降枪吹氧,加入头批造渣料,冶炼前期采用较低枪位,造渣原料中增加转炉石灰石用量;第三阶段吹氧造渣冶炼:转炉冶炼前期低温高效脱除钢水中磷,冶炼中后期继续吹氧造渣深脱磷;第四阶段拉碳倒渣:终点拉碳时倒出部分高磷渣;第五阶段终点控制并出钢:终点钢水成分和钢水温度合适后出钢,同时判断出钢时炉渣基本状态,进入下一个周期的转炉冶炼操作;如此循环多炉次形成转炉气化脱磷渣循环脱磷炼钢工艺;终点炉渣参数是,碱度控制为2.0~3.0,氧化性控制为feo含量15~25%,温度为1660~1680℃。进一步,所述第二阶段按照倾斜转炉内的物料重量往倾斜转炉兑入废钢的重量比值为10~35%。所述造渣原料中石灰石用量的重量比为20~40%。所述冶炼前期较低枪位,是指比不采用气化脱磷渣的操作枪位低0.1~0.3m。所述终点拉碳次数为1~3次,第1次倒出总渣量的1/5~2/5,第2次、第3次尽量少倒渣。按照所述的第五个阶段循环5~12炉次。第五个阶段循环炉次为:小型转炉为5~8炉次或更多,中大型转炉为10~12炉次或更多。与传统工艺相比,本发明具有以下优点:(1)加大溅渣前留渣比例,溅渣后不排渣,充分循环利用留渣热量和炉渣高碱度优势,提高冶炼前期低温脱磷效果,提高转炉冶炼效率。(2)可利用留渣及溅渣层热量,增加废钢比,提高废钢使用量,以石灰石替代部分石灰炼钢,降低石灰消耗;(3)炉渣铁损减少,金属收得率提高;(4)减少转炉渣向炉外排放,节能减排促进环境保护。附图说明图1为转炉气化脱磷渣循环脱磷炼钢工艺图;图2为气化脱磷量及脱磷率图3终点钢水成分图4终渣成分及加碳量图5气化脱磷量及脱磷率图6终点钢水成分图7终渣成分及加碳量图8气化脱磷量及脱磷率图9终点钢水成分图10终渣成分及加碳量图11气化脱磷量及脱磷率图12终点钢水成分图13终渣成分及加碳量图14气化脱磷量及脱磷率图15终点钢水成分图16终渣成分及加碳量图17气化脱磷率总体统计图图中标记:转炉1、氧枪2、氮气3、铁水4、铁水包5、废钢6、氧气7、炉渣8、钢水9、渣罐10、钢包11。具体实施方式下面结合附图对本发明做进一步的描述。图1为转炉气化脱磷渣循环脱磷炼钢工艺的五个阶段。第一阶段是溅渣护炉气化脱磷,第二阶段是兑铁加料,第三阶段是吹氧造渣冶炼,第四阶段是拉碳倒渣,第五阶段是终点控制并出钢。具体工艺为:装有氮气3和氧枪2的转炉1出钢结束后,根据炉渣基本状态,向转炉1内热态熔渣中添加合适的脱磷剂,在溅渣护炉过程中通过气化的方式脱除渣中的磷,保留溅渣后的气化脱磷渣;倾斜转炉1兑入废钢6和铁水包5内的铁水4,利用气化脱磷渣的富裕热量提高转炉废钢比,之后转炉降枪吹氧气7,加入头批造渣料,气化脱磷渣碱度高、流动性好,冶炼前期可采用较低枪位,造渣原料中可增加转炉石灰石用量;转炉冶炼前期低温高效脱除钢水9中磷,冶炼中后期继续吹氧造渣深脱磷,终点拉碳时倒出部分高磷渣,当终点钢水成分和钢水9温度合适后出钢至钢包11,同时判断出钢时钢包10中炉渣9的基本状态,进入下一个周期的转炉冶炼操作;如此循环一定炉次,形成了转炉气化脱磷渣循环脱磷炼钢工艺。按照上述的五个阶段,采用转炉气化脱磷渣循环脱磷炼钢方法的具体实施例:在某厂65t转炉出钢结束后,根据炉渣基本状态,在温度1660~1680℃状态下,第一阶段向转炉内热态熔渣中添加脱磷剂,在溅渣护炉过程中通过气化的方式脱除渣中的磷,保留溅渣后的气化脱磷渣;第二阶段按照倾斜转炉内的物料重量往倾斜转炉兑入废钢和铁水,成分如表1所示,第三阶段转炉降枪吹氧,加入头批造渣料,各种造渣料成分如表2所示,气化脱磷渣碱度高、流动性好,冶炼前期采用1.65~1.75m的低枪位,造渣原料中石灰石用量为1100~1500kg;第四阶段转炉冶炼前期低温高效脱除钢水中磷,冶炼中后期继续吹氧造渣深脱磷,终点一次拉碳至碳含量0.08%,第一次倒出占总渣量1/5的高磷渣,如果有渣进行第2次、第3次倒渣,尽量少倒渣。第五阶段当终点钢水成分合格和钢水温度为1660℃~1680℃时出钢,出钢时炉渣基本状态为碱度2.0,氧化性为feo含量18%,温度1680℃,之后进入下一个周期的转倾斜转炉兑入废钢炉冶炼操作,如此循环6炉次。采用气化脱磷渣循环脱磷炼钢工艺后,冶炼低合金系列钢磷含量合格率达到100%,石灰消耗降低1.5kg/t,生产成本吨钢降低3~5元。表1废钢和铁水成分铁水质量/kg废钢质量/kg废钢p含量/%铁水s含量/%铁水si含量/%铁水p含量/%7250058300.030.0250.470.113表2造渣料成分(干基%)名称caomgosio2spfeofe2o3mnoh2oco2k2ona2oal2o3石灰石47.885.022.710.050.006542.86石灰74.057.793.90.0530.00915.56轻烧36.9626.10.850.0150.005633.7除尘灰9.322.132.280.2060.13739.3539.650.710.73.951.690.1铁皮球0.2550.580.160.0850.7636.9150.361.581.40.113.8721.67矿石0.010.011.960.0480.0280.6195.470.121.13具体操作实施例实施例1按照上述原料情况实施转炉气化脱磷渣循环脱磷炼钢,循环的炉数为5炉,试验结果如图2~图4所示。结果表明,炉渣的气化脱磷率为45.0%。试验过程中,低拉碳时终点碳在0.110%以下,平均为0.076%;终点平均温度1671℃;终点feo含量大于17.1%,平均为21.5%;碱度平均为2.67;四炉试验加碳粉,平均加入量为2袋。采用低拉碳高氧化性操作,试验终渣条件较好,气化脱磷率较高。实施例2按照上述原料情况实施转炉气化脱磷渣循环脱磷炼钢,循环的炉数为5炉,试验结果如图5~图7所示。结果表明,本次循环气化脱磷率为30.9%。试验过程中,拉碳时终点碳在0.160%以下,平均为0.105%;终点平均温度1656℃;终点feo含量大于17.7%,平均为18.9%;碱度平均为2.58;三炉试验加碳粉,平均加入量为2.3袋(第一次加了5袋)。试验终渣条件明显不如第一个循环好,feo含量在20以下,碳粉加入量很少,导致气化脱磷率相对较低。实施例3按照上述原料情况实施转炉气化脱磷渣循环脱磷炼钢,炉数为6炉,试验结果如图8~图10所示。结果表明,本次循环气化脱磷率为27.5%。试验过程中,拉碳时终点碳在0.083%以下,平均为0.053%;终点平均温度1656℃;终点feo含量大于15.3%,平均为22.7%;碱度平均为2.45;三炉试验加碳粉,平均加入量为2.4袋。采用低拉碳、高氧化性操作,试验终渣条件较好,气化脱磷率相对较高。实施例4按照上述原料情况实施转炉气化脱磷渣循环脱磷炼钢,循环的炉数为5炉,试验结果如图11~图13所示。结果表明,本次循环气化脱磷率为47.9%。试验过程中,拉碳时终点碳在0.011%以下,平均为0.06%;终点平均温度1662℃;终点feo含量大于17.0%,平均为20.2%;碱度平均为2.44;三炉试验加碳粉,平均加入量为1.7袋。采用低拉碳、高氧化性操作,试验终渣条件较好,气化脱磷率相对较高。实施例5按照上述原料情况实施转炉气化脱磷渣循环脱磷炼钢,循环的炉数为6炉,试验结果如图14~图16所示。结果表明,本次循环气化脱磷率为37.3%。试验过程中,拉碳时终点碳在0.08%以上,平均为0.11%;终点平均温度1663℃;终点feo含量大于12.8%,平均为15.0%;碱度平均为2.41;五炉试验加碳粉,平均加入量为2.0袋。拉碳适中,但终渣氧化性较低,试验终渣条件一般,气化脱磷率相对较高。总之,转炉气化脱磷渣循环脱磷炼钢实施例的脱磷率总体统计图如图17所示,可见气化脱磷率为27.5%~47.9%,统计平均值为38%,炉渣脱磷效果很好,使得冶炼过程渣量小、热损低、铁损少,显著降低了冶炼成本。转炉气化脱磷渣循环脱磷炼钢实施例表明,在操作水平和参数条件控制较好时气化脱磷率完全可达到40%的水平,主要包括:多炉次气化脱磷循环冶炼终点碳平均控制在0.010%以下,终点平均温度1660℃,终点feo含量平均大于20%,碱度平均为2.45,碳粉平均加入量为2~3袋;同时配合良好的溅渣护炉过程及稳定的冶炼操作技术水平。操作实施例中所述的所加碳粉的重量,每袋碳粉重17kg。虽然,上文中已经用一般性说明及具体实施方案对本发明作了详尽的描述,但在本发明基础上,可以对之作一些修改或改进,这对本领域技术人员而言是显而易见的。因此,在不偏离本发明精神的基础上所做的这些修改或改进,均属于本发明要求保护的范围。当前第1页12