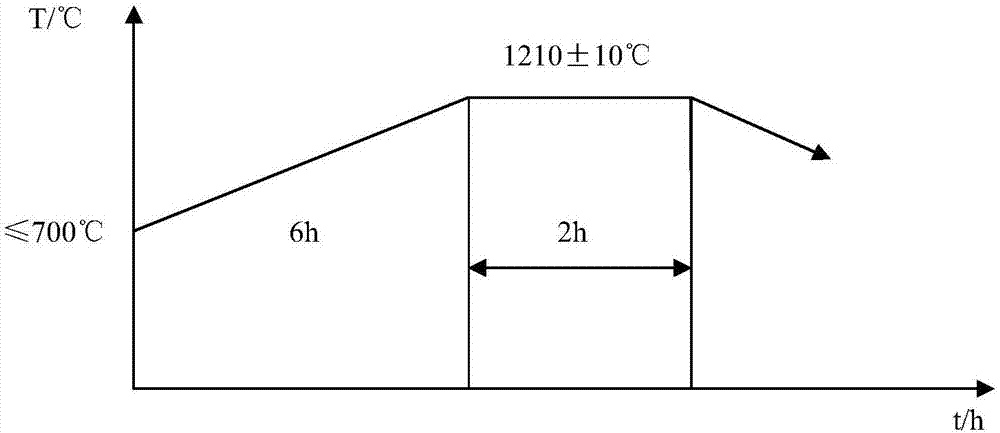
本发明涉及冶金领域,且特别涉及一种高镧含量的难变形钴基高温合金板材及其制备方法。
背景技术:
:随着航空发动机性能的不断提高,燃烧室进口温度、压力和出口温升逐步上升,高温燃气向火焰筒壁面的热辐射强度也随之增强,因而火焰筒所使用的高温合金板材是航空发动机的关键用材。同时针对航空发动机火焰筒等的结构特点:壁薄、尺寸精度要求高、结构复杂,因此,航空发动机的用材的使用条件苛刻。钴基高温合金是指钴含量为40%~65%的奥氏体高温合金。该合金在730~1100℃条件下具有一定的高温强度、良好的抗热腐蚀和抗氧化能力,适于制作航空喷气发动机、工业燃气轮机、舰船燃气轮机的导向叶片和喷嘴导叶以及柴油机喷嘴等。因此,针对航空发动机火焰筒等特殊的用材要求,生产出合格的冷轧薄板具有很强的现实意义,能为国防建设做出贡献,社会效益显著。技术实现要素:本发明的目的在于提供一种高镧含量的难变形钴基高温合金板材,其表面、尺寸、性能满足标准和用户使用要求,可用于制作航空发动机火焰筒。本发明的另一目的在于提供一种高镧含量的难变形钴基高温合金板材的制备方法,采用真空感应、电渣重熔冶炼工艺路线,生产出合格的高镧含量的难变形高温合金冷轧薄板产品,提高产品质量,为企业创造更多的经济效益。本发明解决其技术问题是采用以下技术方案来实现的。本发明提出一种高镧含量的难变形钴基高温合金板材,按重量百分数计,其主要由以下合金元素成分组成:C:0.05%~0.15%;Cr:19%~24%;Ni:9%~24%;W:13%~16%;Fe:≤3%;Mn:1%~2%;Si:0.2%~0.4%;P:≤0.04%;S:≤0.015%;B:≤0.015%;La:0.03%~0.12%;余量为Co。进一步地,在本发明较佳实施例中,其合金密度为9~9.5g/cm3,熔化温度范围为1330~1410℃。一种上述的高镧含量的难变形钴基高温合金板材的制备方法,其包括以下步骤:将合金原材料采用真空感应、电渣重熔冶炼工艺路线进行冶炼,获得钢锭;将钢锭经锻造、轧制、固溶热处理、酸洗获得冷轧薄板。进一步地,在本发明较佳实施例中,合金原材料包括:1#Ni、J-Cr、J-W、J-Mn、J-Co、C块、工业硅、金属镧、硼铁。进一步地,在本发明较佳实施例中,将合金原材料装入真空感应炉进行冶炼,具体是将合金原材料Ni、Cr、W、Co及部分的C装入坩埚,梯度加大功率;料平,加剩余部分的C;全熔,1470~1480℃;降低功率至150kw,1520~1530℃;充Ar200,加入J-Mn、工业硅、硼铁、金属镧;真空度<1.0Pa方可给电熔炼,浇注成初锭。进一步地,在本发明较佳实施例中,冶炼条件为:水压>0.3MPa,风压>0.6MPa,不得中断;炉子冷态真空度<0.13Pa,漏气度<0.13Pa/min;电极:Φ115mm×6支。进一步地,在本发明较佳实施例中,将初锭在结晶器中、并在电极棒作用下采用交换电极方式重熔,重熔条件为:重熔电压50±2V,重熔电流4700±300A;电渣CaF2:Al2O3:CaO:MgO=50%~60%:20%~30%:8%~12%:8%~12%;充填≥15min,炉冷≥30min,出炉后空冷;水温控制42~58℃,使用脱氧剂脱氧,得到钢锭。进一步地,在本发明较佳实施例中,锻造的方法为:将钢锭在灶式炉中加热,在5~6h内,由600~700℃升温至1200~1250℃,保温2h,逐渐冷却;将冷却后的钢锭在电液锤上进行锻造开坯,锻成方坯,开锻温度≥1100℃,终锻温度≥950℃,回炉再烧时间1小时;将方坯进行轧制,轧制条件为:装炉温度:≤700℃;加热温度:1170~1210℃,加热时间:≥2h,保温时间>1小时;开轧温度≥1100℃,终轧温度≥950℃,得到板材。进一步地,在本发明较佳实施例中,轧制的方法为:热轧:荒轧温度1170~1200±10℃,精轧温度1130~1170±10℃,终轧温度≥920℃,加热时间按1.5min/mm+3~5min计算,热轧道次变形量≤20%,最后一火次变形量≥25%;冷轧:半成品总变形量30%~35%,成品总变形量25%~30%,最大道次变形量≤10%;退火:在辊底炉中进行,加热温度至1175~1205℃,按照1.5min/mm±10~12min,然后空冷或水冷。进一步地,在本发明较佳实施例中,退火的具体方法为:半成品:加热温度1180±10℃,加热时间1.5min/mm+3~5min,空冷;成品:加热温度1150~1250℃,加热时间1.5min/mm+3~5min,空冷。本发明实施例的高镧含量的难变形钴基高温合金板材及其制备方法的有益效果是:高镧含量的难变形钴基高温合金板材按重量百分数计主要由以下合金元素成分组成:C:0.05%~0.15%;Cr:19%~24%;Ni:9%~24%;W:13%~16%;Fe:≤3%;Mn:1%~2%;Si:0.2%~0.4%;P:≤0.04%;S:≤0.015%;B:≤0.015%;La:0.03%~0.12%;余量为Co,该高镧含量的难变形钴基高温合金板材的表面、尺寸、性能满足标准和用户使用要求,可用于制作航空发动机火焰筒;该高镧含量的难变形钴基高温合金板材的制备方法是将合金原材料采用真空感应、电渣重熔冶炼工艺路线进行冶炼,获得钢锭;将钢锭经锻造、轧制、固溶热处理、酸洗获得冷轧薄板,采用真空感应、电渣重熔冶炼工艺路线,生产出合格的高镧含量的难变形高温合金冷轧薄板产品,提高产品质量,为企业创造更多的经济效益。附图说明为了更清楚地说明本发明实施例的技术方案,下面将对实施例中所需要使用的附图作简单地介绍,应当理解,以下附图仅示出了本发明的某些实施例,因此不应被看作是对范围的限定,对于本领域普通技术人员来讲,在不付出创造性劳动的前提下,还可以根据这些附图获得其他相关的附图。图1为本发明实施例采用真空感应熔炼高镧含量的难变形钴基高温合金母材熔炼功率曲线;图2为本发明实施例中锻造过程中的钢锭加热制度。具体实施方式为使本发明实施例的目的、技术方案和优点更加清楚,下面将对本发明实施例中的技术方案进行清楚、完整地描述。实施例中未注明具体条件者,按照常规条件或制造商建议的条件进行。所用试剂或仪器未注明生产厂商者,均为可以通过市售购买获得的常规产品。下面对本发明实施例的高镧含量的难变形钴基高温合金板材及其制备方法进行具体说明。本发明实施例提供一种高镧含量的难变形钴基高温合金板材,按重量百分数计,其主要由以下合金元素成分组成:C:0.05%~0.15%;Cr:19%~24%;Ni:9%~24%;W:13%~16%;Fe:≤3%;Mn:1%~2%;Si:0.2%~0.4%;P:≤0.04%;S:≤0.015%;B:≤0.015%;La:0.03%~0.12%;余量为Co。高镧含量的难变形钴基高温合金是以Ni、Cr、W、Mn固溶强化的钴基合金,该合金具有较好的综合机械性能,耐磨、抗腐蚀、抗氧化、焊接性能较好,还具有较好的工艺塑性,可热加工成棒材、板材、丝材、锻件等。该高镧含量的难变形钴基高温合金板材的合金密度为9~9.5g/cm3,熔化温度范围为1330~1410℃。本发明实施例提供一种上述的高镧含量的难变形钴基高温合金板材的制备方法,其包括以下步骤:将合金原材料采用真空感应、电渣重熔冶炼工艺路线进行冶炼,获得钢锭;将所述钢锭经锻造、轧制、固溶热处理、酸洗获得冷轧薄板。原材料主要成分和杂质含量应满足相应技术要求,合金进厂后必须按原材料进厂检验规程进行验收,合格后方可使用;原材料的表面、尺寸、块度要求符合基本规程。所述合金原材料包括:1#Ni、J-Cr、J-W、J-Mn、J-Co、C块、工业硅、金属镧、硼铁。高镧含量的难变形钴基高温合金板材的制备方法的具体过程如下:S1、将合金原材料装入真空感应炉进行冶炼,具体是将合金原材料Ni、Cr、W、Co及部分的C一次装入坩埚,梯度加大功率,0~15min,100kW;15~30min,150kW;30~40min,300kW;料平,加剩余部分的C;全熔,1470~1480℃;降低功率至150kW,1520~1530℃;充Ar200,加入J-Mn、工业硅、硼铁、金属镧;真空度<1.0Pa方可给电熔炼,浇注成初锭。冶炼条件为:新坩埚需Fe洗一炉,Co洗一炉;中间冶炼需Co洗一炉,方可冶炼本合金;如果前炉钢种不影响本钢成分且装入量大于本钢,可不洗炉。设备正常,风、水、电、天燃气供应正常,)其中水压>0.3MPa,风压>0.6MPa,不得中断;炉子冷态真空度<0.13Pa,漏气度<0.13Pa/min;电极:Φ115mm×6支。S2、将初锭在结晶器中并在电极棒作用下,采用交换电极方式重熔,重熔条件为:重熔电压50±2V,重熔电流4700±300A;电渣CaF2:Al2O3:CaO:MgO=50%~60%:20%~30%:8%~12%:8%~12%;充填≥15min,炉冷≥30min,出炉后空冷;水温控制42~58℃,使用脱氧剂脱氧,得到钢锭。S3、锻造:将钢锭在灶式炉中加热,在5~6h内,由600~700℃升温至1200~1250℃,保温2h,逐渐冷却;将冷却后的钢锭在电液锤上进行锻造开坯,锻成方坯,开锻温度≥1100℃,终锻温度≥950℃,回炉再烧时间1小时;将方坯进行轧制,轧制条件为:装炉温度:≤700℃;加热温度:1170~1210℃,加热时间:≥2h,保温时间>1小时;开轧温度≥1100℃,终轧温度≥950℃,得到板材。S4、轧制:热轧:荒轧温度1170~1200±10℃,精轧温度1130~1170±10℃,终轧温度≥920℃,加热时间按1.5min/mm+3~5min计算。热轧道次变形量≤20%,最后一火次变形量≥25%;冷轧:半成品总变形量30%~35%,成品总变形量25%~30%,最大道次变形量≤10%;退火:在辊底炉中进行,加热温度至1175~1205℃,按照1.5min/mm±10~12min,然后空冷或水冷。本实施例中,退火的方法为:半成品:加热温度1180±10℃,加热时间1.5min/mm+3~5min,空冷;成品:加热温度1150-1250℃,加热时间1.5min/mm+3~5min,空冷。S5、酸洗步骤。本发明实施例通过调整、优化和改进冷轧薄板制备工艺,采用真空感应+电渣重熔冶炼工艺路线,生产的高镧含量的难变形高温合金板材的表面、尺寸、性能满足标准和用户使用要求,生产出合格的高镧含量的难变形高温合金冷轧薄板产品,提高产品质量,为企业创造更多的经济效益,尤其是GH5188高温合金的表面、尺寸、性能等进行控制,生产出成分合格的GH5188合金冷轧薄板。该制备工艺适用于高镧含量的难变形钴基高温合金在炼钢总厂真空感应炉/电渣炉冶炼、锻造厂电液锤开坯、连轧厂轧钢作业区轧制、扁钢作业区开坯、锻造厂薄板作业区成材的整个生产工艺过程。以下结合实施例对本发明的特征和性能作进一步的详细描述。实施例1本实施例提供一种高镧含量的难变形钴基高温合金板材,其按照以下制备方法制得:(1)3000P真空感应炉冶炼工艺1.1、冶炼条件(关键过程)新坩埚需Fe洗一炉,Co洗一炉。中间冶炼需Co洗一炉,方可冶炼本合金;如果前炉钢种不影响本钢成分且装入量大于本钢,可不洗炉。设备正常,风、水、电、天燃气供应正常,其中水压>0.3MPa,风压>0.6MPa,不得中断。炉子冷态真空度<0.13Pa,漏气度<0.13Pa/min。1.2、装入量及电极规格装入量:900kg,电极:Φ115mm×6支。1.3、配入成分,具体见表1(%)表1熔炼分析表元素CCrNiCoWFe质量分数0.05~0.1519~249~24余13~16≤3配入0.0920.510.2余15.5---元素MnSiPSBLa质量分数1~20.2~0.4≤0.04≤0.015≤0.0150.03~0.12配入1.650.32-------0.00611.4、原材料要求原材料主要成分和杂质含量应满足相应技术要求,合金进厂后必须按原材料进厂检验规程进行验收,合格后方可使用;原材料的表面、尺寸、块度要求符合基本规程。所用原材料有:1#Ni、J-Cr、J-W、J-Mn、J-Co、C块、工业硅、金属镧、硼铁。1.5、装炉所有入炉原材料经当班人员按配料单检查、称重,确认品种、数量无误并签字认可方可入炉。按图1所示的熔炼功率曲线进行加料和熔炼,Ni、Cr、W、Co及2/3C一次装入坩埚。1/3C、J-Mn、工业硅、硼铁、金属镧按工艺曲线加入。冶炼按工艺曲线按图1进行,真空度<1.0Pa方可给电熔炼。1.7、浇注(1)浇注在真空下进行,控制浇注速度及填充质量。(2)钢锭模必须用钢水烫过,清洁无锈,方可使用。(3)浇注后模冷时间大于1h。1.8、真空感应炉冶炼质量控制点(1)装料盘皮重应标在盘子上,每次装料要先过皮重。(2)合金装炉前过称必须准确。(3)调节出钢温度、浇注速度和填充质量。(2)电渣重熔工艺(关键过程)2.1、电极和结晶器:Φ115mm电极棒,采用交换电极方式在Φ230mm的结晶器中重熔。2.2、电制度:重熔电压50±2V,重熔电流4700±300A。2.3、渣制度:CaF2:Al2O3:CaO:MgO=55:25:10:10(%),渣量14kg。2.4、充填及缓冷制度:充填≥15min,炉冷≥30min,出炉后空冷。2.5、水温控制42~58℃,使用本钢底垫,使用Al粒/粉等脱氧剂脱氧。(3)锻造3.1、加热曲线锻造开坯在电液锤上进行,钢锭在灶式炉中加热。加热曲线如图2所示的钢锭加热制度。3.2、开坯(1)钢锭锻成方坯供锻造厂、404轧制,锻坯尺寸由下工序提供。(2)开锻温度≥1100℃,终锻温度≥950℃,回炉再烧时间1小时。(3)锻坯经表面清理后,转下工序。3.3、轧制关键过程(1)装炉温度:≤700℃。(2)加热温度:1200±10℃,加热时间:≥2h,保温时间:1小时。(3)开轧温度≥1100℃,终轧温度≥950℃。(4)板材轧制4.1、热轧荒轧温度1200±10℃,精轧温度1170±10℃,终轧温度≥920℃,1.5min/mm+3~5min。热轧道次变形量≤20%,最后一火次变形量≥25%。4.2、冷轧(关键过程)半成品总变形量30~35%,成品总变形量25~30%,最大道次变形量≤10%,得到0.8mm厚板。4.3、退火(关键过程)退火在辊底炉中进行,退火温度见表2:表2退火温度表(5)酸碱洗。(6)成品经平整、矫直、剪切、取样、检验、探伤合格后,包装入库。将本实施例的成品对以下项目进行检测。A、板材表面质量:冷轧薄板按GBn180-82规定执行,热轧板按GBn179-82规定执行。B、横低倍:在相当于钢锭头部和尾部的热轧板坯上切取试样,横低倍不应有缩孔痕迹、夹渣、裂纹、空洞和针孔、C、显微组织检查。a晶粒度:按NFA04-102测定晶粒度,晶粒度均匀,≤4mm的冷轧板平均晶粒直径为≤0.15mm(相当2.5级)允许各别0.25mm(相当1级);>4.0~10.5mm热轧板晶粒度报实测结果,积累数据,晶粒应力争细小。b评定夹杂物级别:可参照GBn187.5-82。D、机械性能:在交货状态下测定,取样方向为横向。a室温拉伸性能应符合表3的规定。表3室温拉伸性能表b持久性能符合表4的规定。表4持久性能表c维氏硬度HV≤290。d弯曲试验:E、对于厚度≤3mm的板材,在每炉批板材上进行弯曲试验,一个试样平行于轧制方向切取,一个试样垂直于轧制方向切取,试验条件如表5规定。表5试验条件表r为弯曲后试样褶子的内部半径弯曲的试样在抛光掉皱纹后,不应有用8倍放大镜或其他检验方法可见的任何裂纹。成品探伤:板材应逐张进行超声波探伤,板材不允许有裂纹、分层、夹渣。检测结果如下表6所示:表6成品检测结果实施例2本实施例提供一种高镧含量的难变形钴基高温合金板材,其制备方法与实施例1的制备方法制得,不同之处在于:本实施例制得1.1mm厚板的成品。将本实施例的成品进行相同的项目检测,检测结果如下表7所示:表7成品检测结果实施例3本实施例提供一种高镧含量的难变形钴基高温合金板材,其制备方法与实施例1的制备方法制得,不同之处在于:本实施例制得2.0mm厚板的成品。将本实施例的成品进行相同的项目检测,检测结果如下表8所示:表8成品检测结果实施例4本实施例提供一种高镧含量的难变形钴基高温合金板材,其制备方法与实施例1的制备方法制得,不同之处在于:本实施例制得7.0mm厚板的成品。将本实施例的成品进行相同的项目检测,检测结果如下表9所示:表9成品检测结果实施例5本实施例提供一种高镧含量的难变形钴基高温合金板材,其制备方法与实施例1的制备方法制得,不同之处在于:本实施例制得8.0mm厚板的成品。将本实施例的成品进行相同的项目检测,检测结果如下表10所示:表10成品检测结果实施例6本实施例提供一种高镧含量的难变形钴基高温合金板材,其制备方法与实施例1的制备方法制得,不同之处在于:本实施例制得10.5mm厚板的成品。将本实施例的成品进行相同的项目检测,检测结果如下表11所示:表11成品检测结果综上所述,本发明实施例的高镧含量的难变形钴基高温合金板材的表面、尺寸、性能满足标准和用户使用要求,可用于制作航空发动机火焰筒;该高镧含量的难变形钴基高温合金板材的制备方法是采用真空感应、电渣重熔冶炼工艺路线,生产出合格的高镧含量的难变形高温合金冷轧薄板产品,提高产品质量,为企业创造更多的经济效益。以上所描述的实施例是本发明一部分实施例,而不是全部的实施例。本发明的实施例的详细描述并非旨在限制要求保护的本发明的范围,而是仅仅表示本发明的选定实施例。基于本发明中的实施例,本领域普通技术人员在没有作出创造性劳动前提下所获得的所有其他实施例,都属于本发明保护的范围。当前第1页1 2 3